装置检修无损检测施工方案
无损检测施工方案(高效)
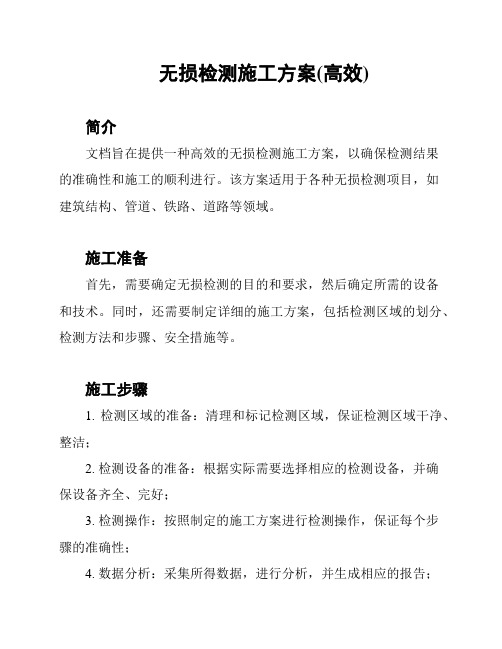
无损检测施工方案(高效)
简介
文档旨在提供一种高效的无损检测施工方案,以确保检测结果
的准确性和施工的顺利进行。
该方案适用于各种无损检测项目,如
建筑结构、管道、铁路、道路等领域。
施工准备
首先,需要确定无损检测的目的和要求,然后确定所需的设备
和技术。
同时,还需要制定详细的施工方案,包括检测区域的划分、检测方法和步骤、安全措施等。
施工步骤
1. 检测区域的准备:清理和标记检测区域,保证检测区域干净、整洁;
2. 检测设备的准备:根据实际需要选择相应的检测设备,并确
保设备齐全、完好;
3. 检测操作:按照制定的施工方案进行检测操作,保证每个步
骤的准确性;
4. 数据分析:采集所得数据,进行分析,并生成相应的报告;
5. 结果确认:针对检测结果进行确认,并在必要时进行重复检测;
6. 报告编制:根据检测结果编制详细的报告,报告中应包含检测目的、方法、结果等内容。
安全措施
在无损检测施工中,需要采取一系列安全措施,以确保施工过程中的安全性。
这些措施包括:
- 严格遵守安全操作规程;
- 设立安全防护措施,保证施工地点的安全性;
- 做好防腐、防火等工作,确保施工地点的安全性。
结论
该高效的无损检测施工方案,提供了详细的施工步骤和安全措施,以确保检测结果准确、施工过程安全。
在实际应用中,需要结合具体的项目和实际情况进行调整,以达到最佳的检测效果。
无损检测施工方案
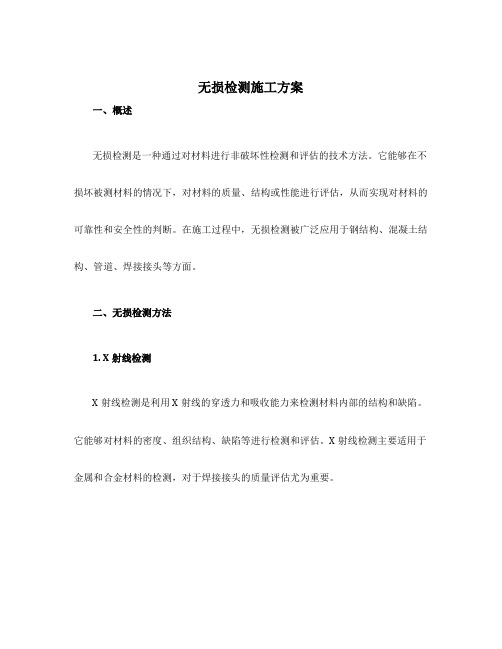
无损检测施工方案一、概述无损检测是一种通过对材料进行非破坏性检测和评估的技术方法。
它能够在不损坏被测材料的情况下,对材料的质量、结构或性能进行评估,从而实现对材料的可靠性和安全性的判断。
在施工过程中,无损检测被广泛应用于钢结构、混凝土结构、管道、焊接接头等方面。
二、无损检测方法1. X射线检测X射线检测是利用X射线的穿透力和吸收能力来检测材料内部的结构和缺陷。
它能够对材料的密度、组织结构、缺陷等进行检测和评估。
X射线检测主要适用于金属和合金材料的检测,对于焊接接头的质量评估尤为重要。
2. 超声波检测超声波检测是利用超声波在材料中的传播和反射特性来检测材料内部的结构和缺陷。
它能够对材料的厚度、波速、声阻抗等进行检测和评估,并能够定位和测量缺陷的尺寸。
超声波检测主要适用于金属和非金属材料的检测,对于混凝土结构和管道的检测具有重要意义。
3. 磁粉检测磁粉检测是利用外加磁场和磁粉的磁化作用来检测材料表面和近表层的结构和缺陷。
它能够对材料的表面裂纹、缺陷和疲劳裂纹进行检测和评估,并能够定位和测量缺陷的尺寸和形态。
磁粉检测主要适用于金属材料的表面检测,对于焊接接头和表面裂纹的检测具有重要意义。
4. 热红外检测热红外检测是利用物体的热辐射特性来检测物体的缺陷和异常情况。
它能够通过红外相机对物体的温度分布进行测量和分析,从而判断物体内部的结构和材料的性能状况。
热红外检测主要适用于建筑物、电力设备和输电线路等方面的检测,对于温度异常、能量损失等问题具有重要意义。
三、无损检测施工流程无损检测施工包括前期准备、检测方案制定、实施检测和结果分析报告等环节。
1. 前期准备在进行无损检测之前,需要对被测物体进行准备工作。
首先,要清理被测物体的表面,确保无杂质和污染物。
其次,要研究被测物体的结构和材料特性,了解其内部结构和缺陷的可能性。
2. 检测方案制定根据被测物体的特点和检测要求,制定适合的检测方案。
选择合适的无损检测方法,并确定检测仪器和设备的使用参数。
无损检测施工方案
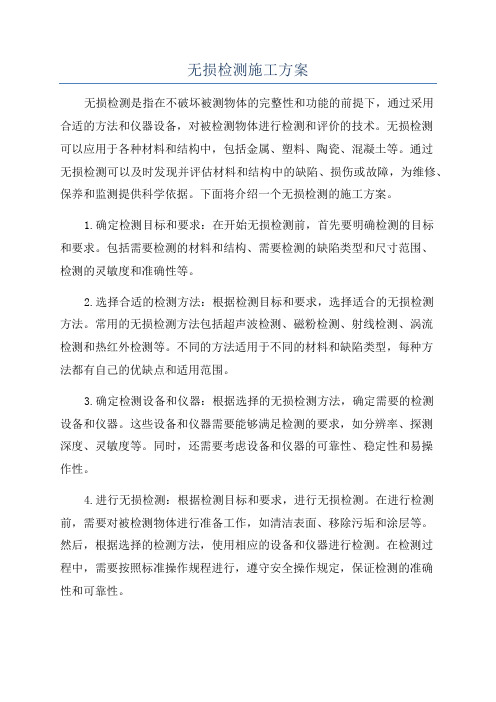
无损检测施工方案无损检测是指在不破坏被测物体的完整性和功能的前提下,通过采用合适的方法和仪器设备,对被检测物体进行检测和评价的技术。
无损检测可以应用于各种材料和结构中,包括金属、塑料、陶瓷、混凝土等。
通过无损检测可以及时发现并评估材料和结构中的缺陷、损伤或故障,为维修、保养和监测提供科学依据。
下面将介绍一个无损检测的施工方案。
1.确定检测目标和要求:在开始无损检测前,首先要明确检测的目标和要求。
包括需要检测的材料和结构、需要检测的缺陷类型和尺寸范围、检测的灵敏度和准确性等。
2.选择合适的检测方法:根据检测目标和要求,选择适合的无损检测方法。
常用的无损检测方法包括超声波检测、磁粉检测、射线检测、涡流检测和热红外检测等。
不同的方法适用于不同的材料和缺陷类型,每种方法都有自己的优缺点和适用范围。
3.确定检测设备和仪器:根据选择的无损检测方法,确定需要的检测设备和仪器。
这些设备和仪器需要能够满足检测的要求,如分辨率、探测深度、灵敏度等。
同时,还需要考虑设备和仪器的可靠性、稳定性和易操作性。
4.进行无损检测:根据检测目标和要求,进行无损检测。
在进行检测前,需要对被检测物体进行准备工作,如清洁表面、移除污垢和涂层等。
然后,根据选择的检测方法,使用相应的设备和仪器进行检测。
在检测过程中,需要按照标准操作规程进行,遵守安全操作规定,保证检测的准确性和可靠性。
5.数据分析和评价:对检测得到的数据进行分析和评价。
根据不同的无损检测方法,可以得到不同的检测结果,如声波图像、磁粉图像、射线图像等。
通过对这些图像进行分析,可以判断材料和结构中是否存在缺陷、损伤或故障,并评估其大小、深度和影响程度。
6.缺陷管理和维修建议:根据检测结果,进行缺陷管理和维修建议。
对于检测到的缺陷,需要根据其大小、深度和影响程度,评估其对结构强度和安全性的影响,制定相应的管理和维修方案。
对于无法修复的缺陷,还需进行监测和评估,以及制定相应的风险控制措施。
无损检测施工方案
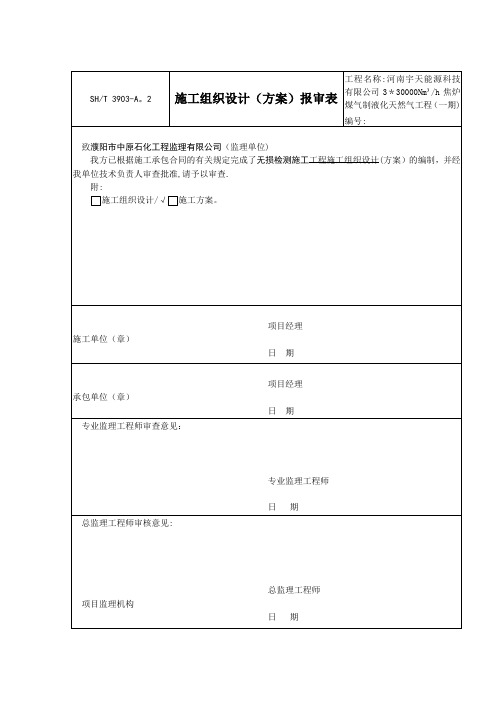
河南宇天能源科技有限公司3*30000Nm³/h焦炉煤气制液化天然气工程(一期)无损检测施工方案批准:审核:编制:河北省安装工程有限公司2016年5月1 工程概况工程名称:河南宇天能源科技有限公司3*30000Nm³/h焦炉煤气制液化天然气工程(一期)无损检测施工建设单位:河南宇天能源科技有限公司总承包单位:西安华江环保科技股份有限公司设计单位:新地能源工程技术有限公司监理单位:濮阳市中原石化工程监理有限公司建设地点:河南省安阳市安阳县铜冶镇工程范围:本方案规定了本工程第二、三标段净化、液化、提氢、脱盐水站、气体供应站及冷水站、循环水泵房、LNG装车区、全厂供排水、全厂外管等工段内工艺管道无损检测工作的要求、操作程序及操作方法。
本方案与有关标准、规范,施工技术文件有抵触时,应以有关标准、规范。
施工技术文件要求为准。
2 编制依据本方案编制依据招标图纸,招标文件及以下规范.2.1《工业管道工程施工及验收规范》(金属管道篇) GB502352。
2《现场设备、工业管道焊接工程施工施工及验收规范》GB502362。
3《金属熔化焊焊接接头射线照相》GB/T33232.4《承压设备无损检测》JB/T47302.5《射线卫生防护基本标准》GB47922.6《工业Y射线探伤卫生防护标准》GBZ1322。
7新地能源工程技术有限公司提供的相关图纸及资料3 施工方法、技术措施3.1人员资格31.1无损检测责任工程师负责现场无损检测质量控制工作,无损检测责任工程师应具有无损检测Ⅱ级或Ⅲ级资格。
3.1.2无损检测工作应由按《特种设备无损检测人员考核与监督管理规则》考试合格,并取得相应检测方法和技术等级的检测人员担任。
3.13Ⅰ级人员应在Ⅱ级或Ⅲ级人员的指导下进行相应的探伤操作和记录。
Ⅱ级或Ⅲ级人员有权对检测结果进行评定并签发检测报告。
3.1。
4探伤人员视力应符合JB/T4730。
2—2005第3。
1.2条的规定.3。
无损检测施工方案
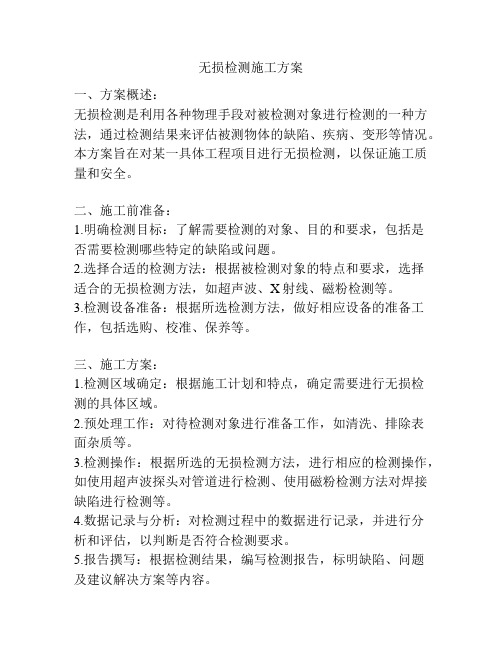
无损检测施工方案一、方案概述:无损检测是利用各种物理手段对被检测对象进行检测的一种方法,通过检测结果来评估被测物体的缺陷、疾病、变形等情况。
本方案旨在对某一具体工程项目进行无损检测,以保证施工质量和安全。
二、施工前准备:1.明确检测目标:了解需要检测的对象、目的和要求,包括是否需要检测哪些特定的缺陷或问题。
2.选择合适的检测方法:根据被检测对象的特点和要求,选择适合的无损检测方法,如超声波、X射线、磁粉检测等。
3.检测设备准备:根据所选检测方法,做好相应设备的准备工作,包括选购、校准、保养等。
三、施工方案:1.检测区域确定:根据施工计划和特点,确定需要进行无损检测的具体区域。
2.预处理工作:对待检测对象进行准备工作,如清洗、排除表面杂质等。
3.检测操作:根据所选的无损检测方法,进行相应的检测操作,如使用超声波探头对管道进行检测、使用磁粉检测方法对焊接缺陷进行检测等。
4.数据记录与分析:对检测过程中的数据进行记录,并进行分析和评估,以判断是否符合检测要求。
5.报告撰写:根据检测结果,编写检测报告,标明缺陷、问题及建议解决方案等内容。
四、施工要求:1.施工人员:由经过专业培训的无损检测人员进行,确保操作规范、准确性和安全性。
2.操作环境:提供适合的操作环境,如保持室温、降低干扰等,以确保检测过程的准确性。
3.保养维护:保养和维护无损检测设备,确保设备的正常运行。
4.安全防护:在无损检测过程中,使用符合要求的个人防护设备,确保施工人员的安全。
五、质量控制:1.制定质量控制计划:在施工前制定无损检测质量控制计划,包括检测要求、检测方法、操作标准等内容。
2.质量检查:在施工过程中进行质量检查,确保操作符合要求,并及时纠正不合格操作。
3.重要数据备份:对重要数据进行备份,以防止数据丢失造成损失。
六、施工管理:1.组织施工人员:组织好无损检测人员的工作安排和任务分配,确保施工进度和质量。
2.施工进度控制:配合工程进度安排,合理安排无损检测施工时间,确保无损检测工作的顺利进行。
无损检测施工技术方案

无损检测施工技术方案一、引言无损检测是一种在不破坏被测件和试件完整性的情况下,通过对被测件内部、表面以及材料性能进行测量和评估的技术方法。
无损检测技术广泛应用于各个领域,如航空航天、核能、石油化工、汽车制造等。
本文将对无损检测施工技术方案进行详细介绍。
二、技术方案(一)检测方法的选择根据被测件的材料和缺陷类型,选择合适的无损检测方法。
常见的无损检测方法包括超声波检测、磁粉检测、涡流检测、X射线检测等。
对于复杂的结构或大型设备,可以采用多种无损检测方法相结合的方式进行综合检测。
(二)仪器设备的选型根据具体的检测要求,选择适用的无损检测设备。
一般情况下,无损检测设备包括信号发射和接收系统、控制系统、显示系统等。
在选型过程中,需要考虑被测物体的尺寸、形态和材料等因素,并确保设备的灵敏度和精度满足检测要求。
(三)检测参数的确定在进行无损检测时,需要确定一系列检测参数,如检测位置、检测速度、探头角度、探头频率等。
这些参数的选取将直接影响到检测的准确性和可靠性。
在确定参数时,需要根据被测物体的材料特性、缺陷类型以及检测的目的进行综合考虑。
(四)预处理和数据分析在无损检测之前,需要对被测材料进行预处理,如除锈、清洁等。
同时,还需要对检测数据进行分析和评估,以判断材料的完整性和缺陷情况。
在数据分析过程中,可以利用专业的软件工具进行图像处理、信号处理等操作,以提高数据的可视化和可靠性。
(五)质量控制和验收无损检测施工过程中,需要进行质量控制和验收。
质量控制包括设备校准、试件标准化、工艺规范化等;验收包括检测结果的评估和判定。
质量控制和验收的目的是确保检测结果的准确性和可靠性,以满足相关技术规范和标准的要求。
三、施工步骤(一)准备工作在进行无损检测之前,需要进行准备工作,包括检查设备和试剂的状态、检查设备是否与电源、工控机等连接正常、检查探头和探头连接线是否有损坏以及防护措施是否到位等。
(二)试验方案的制订根据被测件的要求和检测要求,制订具体的试验方案。
无损检测施工方案及质量保证措施

附件15 无损检测施工方案及质量保证措施1 无损检测施工方案1.1 主要工程量大庆炼化公司30万吨/年聚丙烯工程第三标段主要包括料仓11台,工艺管线25公里。
焊口检测比例按施工图和规范标准具体要求执行。
1.2 无损检测程序1.2.1 射线检测程序见图3.15-1图3.15-11.2.2 渗透检测程序见图3.15-2图3.15-21.3 无损检测方案为了保证施工的顺利进行及确保优质高效的工程质量,我公司对本工程无损检测给予高度重视。
初步预计设立6个检测小组,配备先进的检测设备及经验丰富的检测人员,并根据工程的进度及要求随时增加检测力量,编制如下无损检测方案。
1.3.1 设备物资准备⑴每小组配备日本理学定向射线探伤机一台,确保仪器在施工前进行计量检定合格,性能良好。
⑵为了防止设备故障等外力干扰因素,备用检测设备1套。
⑶射线胶片采用柯达或性能相近的其它品牌。
⑷根据工程进度需要及时运送渗透检测所需试剂及用品。
⑸为了及时准确地出具检测结果,在现场配备无损检测专用车(带自动洗片机及活动暗室)一辆。
⑹主要设备机具及辅助材料需要量一览表。
表3.15-11.3.2 人员配备⑴所有检测人员都有与其检测项目及级别相应的锅炉压力容器、压力管道无损检测资质证书,每个检测组现场必须有不少于二名Ⅱ级及Ⅱ级以上资格的人员。
底片评定人员必须具有Ⅱ级及Ⅱ级以上资格证书,校正视力不低于1.0并且能辨别距离400mm远的一组高为0.5mm,间距为0.5mm的印刷字母。
从事渗透检测人员不得有色盲、色弱。
⑵设无损检测责任工程师一名,由无损检测Ⅲ级人员但任。
⑶所有人员都要具有团队精神,爱岗敬业,并具有较高的职业道德,不弄虚作假。
做到使探伤比例执行率、扩探比例执行率、评片准确率达到100%。
⑷劳动力需求表表3.15-2⑸无损检测人员名单及资质表3.15-31.3.3 作业前准备⑴无损检测责任工程师在检测前须了解和熟悉有关监察规程、验收标准、技术文件要求,熟悉被检焊缝的规格、材质及其焊接工艺、检测工艺,并编制检测工艺卡,对无损检测人员进行技术交底和检测要点、注意事项的培训。
无损检测工程施工方案
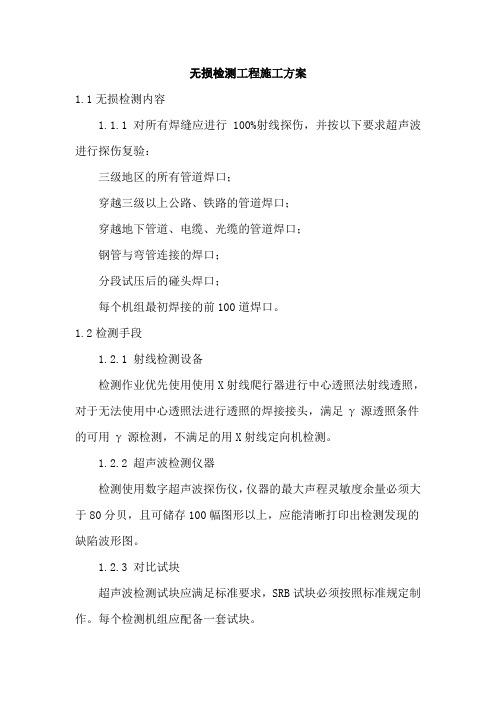
无损检测工程施工方案
1.1无损检测内容
1.1.1 对所有焊缝应进行100%射线探伤,并按以下要求超声波进行探伤复验:
三级地区的所有管道焊口;
穿越三级以上公路、铁路的管道焊口;
穿越地下管道、电缆、光缆的管道焊口;
钢管与弯管连接的焊口;
分段试压后的碰头焊口;
每个机组最初焊接的前100道焊口。
1.2检测手段
1.2.1 射线检测设备
检测作业优先使用使用X射线爬行器进行中心透照法射线透照,对于无法使用中心透照法进行透照的焊接接头,满足γ源透照条件的可用γ源检测,不满足的用X射线定向机检测。
1.2.2 超声波检测仪器
检测使用数字超声波探伤仪,仪器的最大声程灵敏度余量必须大于80分贝,且可储存100幅图形以上,应能清晰打印出检测发现的缺陷波形图。
1.2.3 对比试块
超声波检测试块应满足标准要求,SRB试块必须按照标准规定制作。
每个检测机组应配备一套试块。
1.2.4使用人工方法冲洗底片。
1.2.5 射线检测胶片
为保证射线检测质量,在本项目中完全使用爱克发(AGFA) C7型胶片。
胶片宽度不得小于80mm。
1.2.6 所有检测设备(仪器)均应经计量检定(或校准)合格。
1.2.7 按照检测标准规范和业主的要求自行采购无损检测材料,所有材料必须具有相关质量证明文件。
1.3人员资质
1.3.1 参加本工程无损检测人员必须持有国家质量监督检验检疫总局核发的相应项目的无损检测资格证书。
- 1、下载文档前请自行甄别文档内容的完整性,平台不提供额外的编辑、内容补充、找答案等附加服务。
- 2、"仅部分预览"的文档,不可在线预览部分如存在完整性等问题,可反馈申请退款(可完整预览的文档不适用该条件!)。
- 3、如文档侵犯您的权益,请联系客服反馈,我们会尽快为您处理(人工客服工作时间:9:00-18:30)。
文件编号:DQLH-ARGG-JSCS-10-2010 xx公司180万吨/年ARGG装置检修工程无损检测技术方案xx公司xx项目经理部2010年7月14日版次:第A1版目录1.无损检测技术要求 (3)2.主要检测方案 (3)3. 检测部位表面质量要求 (3)4.检测时机 (3)5.检测工艺流程 (4)6.射线检测(RT)工艺 (6)7.渗透检测(PT)工艺 (12)8.磁粉检测(MT)工艺 (13)9.无损检测人员资格要求 (15)10、质量保证措施 (16)11风险识别及预防措施 (16)12、安全措施 (17)1.无损检测技术要求(1)检测比例要求:A、本工程无损检测主要是工艺管线焊缝的检测、再生斜管固定口的探伤、进口烟道焊缝的探伤等,检测比例要符合设计或规范规定。
B、抽检时以每一种管线号为基准对每名焊工所施焊的不同材质,不同规格的焊接接头按设计要求进行抽检。
C、对管道焊缝返工扩检应执行GB50235-97中的下列规定:当抽样检验未发现需要返修的焊缝缺陷时,则该次抽样所代表的一批焊缝应认为全部合格;当抽样检验发现需要返修的焊缝缺陷时,除返修该焊缝外,还应采用原规定方法按下列规定进一步检验:a每出现一道不合格焊缝应再检验两道该焊工所焊的同一批焊缝。
b当这两道焊缝均合格时,应认为检验所代表的这一批焊缝合格。
c当这两道焊缝又出现不合格时,每道不合格焊缝应再检验两道该焊工的同一批焊缝。
2.主要检测方案(1)对于本装置中工艺管道对接焊缝射线检测一般采用常规χ射线检测为主的检测方法。
(2)工艺管道检测有困难的固定焊口、容器类焊缝等可采用γ射线进行双壁单影或双壁双影透照。
(3)对于大壁厚(单壁≥25mm)工艺管道对接焊缝可采用下列检测方法:A、周向χ射线或γ射线周向一次曝光。
B、γ射线双壁单影透照。
3. 检测部位表面质量要求(1)进行检测作业前,必须对被检焊缝的表面质量进行确认,符合标准要求后方可进行检验。
(2)射线检测部位表面的不规则状态以不掩盖或不影响内部缺陷显示作为是否修磨处理的限度。
4.检测时机(1)检测对象应经形状尺寸和外观质量检查合格后,方可进行检测。
(2)设计文件有要求的,按规定的时机进行无损检测。
(3)对于返修部位应在返修后及时复探。
(4)材质为合金钢的对接焊缝必须焊接完成24h后,才能进行检测。
5.检测工艺流程(1)射线检测工艺流程(2)渗透检测工艺流程图6.射线检测(RT)工艺(1)射线照相质量等级:选用AB级(2)检测设备与器材检测设备:250/300kV定向、250kV/300kV周向X射线机机胶片类型:柯达胶片AA400象质计灵敏度:按JB/T4730-2005中要求进行选择。
增感屏:铅箔增感屏(χ射线前后屏为0.02~0.2mm,根据不同的电压kV值进行选择)。
(3)透照方式、象质计的选用和摆放位置(见表23)(4)训机要求:必须按照设备使用说明书进行规范训机,严禁违章操作,每次训机必须达到满幅的80%以上。
(5)曝光参数的选择:依照JB4730—2005中的要求,当焦距为700mm时,曝光量不得低于15mA·min。
当焦距改变时可按平方反比定律对曝光量的推荐值进行换算。
(6)透照方法的选择A、对于管径≤100mm以下的管道焊缝,且T≤8mm,b(焊缝宽度≤D0/4)时采用双壁双影法透照,分两次相互垂直方向透照,椭圆间距应在1倍焊缝宽度左右为宜;椭圆成像方法:采用位移法,其位移计算公式:L=()qbLL+ 21式中:L——位移距离L1——焦点到工件表面距离L2——工件表面到胶片距离b——焊缝宽度(b≤D0/4)q——椭圆开口宽度B、对于管径≤100mm以下的管道焊缝,若T>8mm,b(焊缝宽度>D0/4)时,采用垂直透照方式重叠成像,此时一般应相隔120°或60°透照3次;C、对于100mm<Φ≤711mm的管道焊缝和Φ>711mm的固定焊口,采用双壁单投影法透照。
其每次透照长度计算见下式:L3=πD0 /N式中:D0 ——环焊缝外径N——每道焊口透照底片张数(既可查表又可计算)D、对于Φ>711mm的活动焊口,可利用周向X射线机,采用中心透照方式周向曝光;(7)射线照相质量等级及透照厚度比:JB4730—2005规定,射线照相质量等级为AB级,管径为100到400之间时,透照厚度比K为1.2,管径大于400时,透照厚度比K为1.1。
(8)焊缝透照底片张数的计算方法:ADN≧500 执行SH3501-2002规范,抽查比例和检验长度按每条焊缝的长度计算。
B500>DN≥100,每道焊缝的透照次数N的计算方法及过程如下:依据JB4730-2005规定和上图,其计算公式见下式: N=1800 /a = 1800 /η+θ η=Sin-1(D0Sin θ/F-D0) θ=Cos-1〔1+(K-1)T/ D0〕/K a=η+θ式中:N ——透照底片张数 η——射线束半辐射角 θ——横向裂纹检出角 K ——透照厚度比 F ——焦点到胶片距离(mm )D0——环焊缝外径(mm ) T ——壁厚(mm ) 当D/T ≧1/30时可使公式θ=Cos-1〔1+(K-1)T/ D0〕/K 简化为: θ= Cos-11/K透照方式和透照焦距如表24:C 工艺管道各注:以上数值为采用双壁单影法透照时计算出的透照张数和有效长度,采用垂直透照方式重叠成像时一般应相隔120°或60°透照3次,采用单壁单影法周向曝光时,此时K =1,底片有效长度可依片长而定。
(9)RT 编号方法如图20、图21、图22所示:注:1.底片示意图中各字母的含义:A:区号 B :管号 D:焊口号E:片位号 R X :返工标记X:返工次数H:检测日期 K Y:扩探标记 Y:扩探次数W:焊工号中心标记(小管径用):2.识别标记包括区号、管号、焊口号、片位号、返工标记、扩探标记、返工次数、扩探次数和检测日期。
定位标记包括定位中心标记、搭接标记。
3.标记摆放要求齐全、规范,距离焊缝边缘5mm以上,紧贴于工件表面与胶片之间。
若业主对此有特殊要求,则另行约定、执行。
4.检测状态的标识符号○——合格×——返工Ä——复验合格位置:距焊缝边缘100mm范围内。
方法:有色记号笔标注。
(10)暗室处理暗室处理采用自动洗片机为主,手洗为辅。
手洗操作方法见下面的操作程序。
A、显影显影方法:手工槽洗;显影温度20±2℃;显影时间4~6 min。
注意事项:显影前,测量显影液温度;充分搅动显影液;显影中,应不时作垂直方向的抖动。
B、停显或漂洗停影液(水)停影时间2~3min 强力抖动C、定影定影温度16~24℃;定影时间10~15min;注意事顶:a定影前,测量定影液温度;充分搅拌定影液。
定影刚开始,要多次抖动,之后,每隔一定时间抖动一次;b使用的定影液与新液相比,当定影时间为新液所需时间的两倍,视为失效,更换新液。
D、水洗水洗温度:16℃~22℃;水洗时间:15~30 min;水质要求:流动、清洁;水洗程序:后水洗的底片放在流动水的后面。
E、干燥干燥方法:视环境温度选用自然干燥;干燥程序:润湿—→滴离—→干燥;润湿液:洗洁精水溶液;润湿时间:1 min;注意事项:底片之间保持一定的间距。
(11)底片评定A、设备环境条件:评片室单独设置,室内光线暗淡。
室内照明不在底片上产生反射光。
冷光源强光观片灯应有足够亮度(观察黑度>4.0),且亮度可调;B、底片质量要求:a灵敏度检查:象质计影象、型号、规格、摆放位置。
象质指数(Z)达到JB4730—94的表5-3规定的要求。
b黑度(D)检查:c标记检查:齐全、规范,位置适当,距焊缝边缘大于5mm;d伪缺陷检查:有效评定区域不允许有伪缺陷影象;e背散射的检查:较黑背景上,不得出现较淡的“B”的影象。
C、底片评定:严格按照 JB/T4730—2005标准对底片进行正确质量等级评定。
D、检测信息反馈:以返工通知单形式及时、准确地与委托单位、相关部门反馈检测结果,以委托形式按规定进行扩探、复验。
E、资料整理底片整理:先排序后装袋。
同一焊口的底片,按检测位号由小到大的顺序;同管号的底片,按焊口号由小到大的顺序;同区的底片,按管号由小到大的顺序;依次排序、填袋、装袋、捆扎、归箱。
报告签发:按容器编号、管号、规格、分区域出具报告;报告摆放次序:射线探伤一览表→射线探伤综合报告→射线探伤报告资料审核:对照底片袋上记录的内容,审核底片的质量;审核焊缝质量等级评定。
依据检测委托单要求,审核检测比例、扩探比例执行情况;返工复验片与一次片位置的一致性;报告、底片的符合性;资料内容的准确性;签字人员资质的符合性。
报告发放必须及时准确,真实可靠,字体清晰,专业术语规范,报告内容符合JB/T4730—2005中的规定。
7.渗透检测(PT)工艺(1)渗透检测方法:采用溶剂去除型着色渗透剂—快干湿式显像剂。
(VC—S)(2)检测设备:A检测剂:渗透剂(DH-RS) 清洗剂/丙酮 (HD-BS) 显像剂 (HD-EV)B对比试块:镀铬试块(3)检测环境:当被检部位温度低于15℃时,应先做对比试验;检测剂易燃、易爆,严禁明火;检测剂有毒,采取必要的通风措施;观察迹痕在被检表面可见光照度大于500lx条件下,应有充足的光线和照明。
(4)操作工艺(5)PT编号方法:区号——容器编号、管号——焊口号(6)检测状态标识:○——合格×——返工Ä——复验合格(7)缺陷显示迹痕的判别A、缺陷显示迹痕:除确认外界因素或操作不当造成的显示迹痕之外,其它任何大于等于0.5mm的显示迹痕;B、线性缺陷:长宽比大于3的缺陷显示迹痕;C、圆形缺陷:长宽比小于等于3的缺陷显示迹痕;D、横向缺陷:缺陷显示迹痕长轴方向与被检件轴线或母线的夹角大于等于30°;E、纵向缺陷:缺陷显示迹痕长轴方向与被检件轴线或母线的夹角小于30°;F、一条缺陷:同一直线、间距≤2mm、至少2条缺陷显示迹痕视为一条缺陷,长度为各条缺陷之和加间距。
(8)缺陷显示迹痕等级评定A、不允许存在的缺陷:任何裂纹、白点;B、不允许超标的缺陷:单位 mmC、执行标准 JB/T4730.5—2005 ;D、合格级别Ⅰ级;E、检测记录:依据检测批次,分区按管号填写,在管段图上标注检测位置,草图示意缺陷位置。
(9)检测报告的签发依据检测委托单、记录,按管号分区出具检测报告,一式四份,交甲方2份原件、施工部和QA/QC部1份复印件,检测自留1份复印件。
由PT-Ⅱ、Ⅲ级人员签发、审核渗透检测报告。
摆放次序:PT 委托单——PT综合报告——渗透报告8.磁粉检测(MT)工艺(1)检测对象:容器、管道焊缝表面或其它需要做磁粉检测的部位(2)探伤仪:磁轭式磁粉探伤仪(MP—A3)(3)灵敏度试片:A1-30/100(4)磁化方法:交流电磁轭式纵向磁化(5)通电方式:连续法(6)通电时间:1~3s(7)磁化方向:每一检测区域独立磁化次数≥2次,磁化方向相互垂直。