水平连铸机定尺切割系统的分析与改进方法研究
连铸切割机返回系统的改进-文档
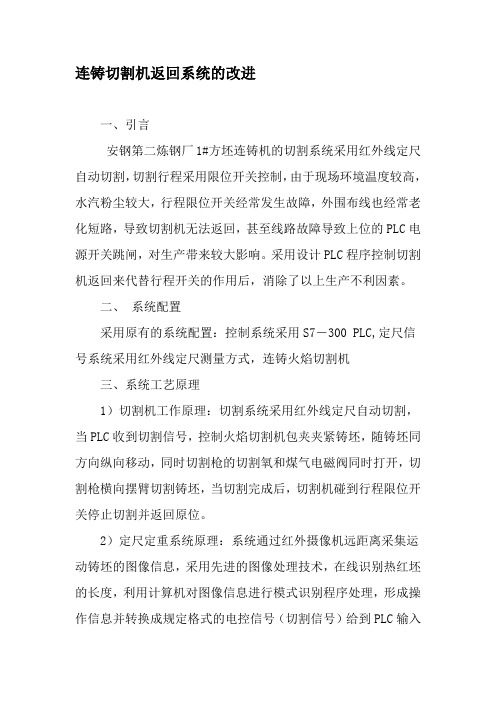
连铸切割机返回系统的改进一、引言安钢第二炼钢厂1#方坯连铸机的切割系统采用红外线定尺自动切割,切割行程采用限位开关控制,由于现场环境温度较高,水汽粉尘较大,行程限位开关经常发生故障,外围布线也经常老化短路,导致切割机无法返回,甚至线路故障导致上位的PLC电源开关跳闸,对生产带来较大影响。
采用设计PLC程序控制切割机返回来代替行程开关的作用后,消除了以上生产不利因素。
二、系统配置采用原有的系统配置:控制系统采用S7―300 PLC,定尺信号系统采用红外线定尺测量方式,连铸火焰切割机三、系统工艺原理1)切割机工作原理:切割系统采用红外线定尺自动切割,当PLC收到切割信号,控制火焰切割机包夹夹紧铸坯,随铸坯同方向纵向移动,同时切割枪的切割氧和煤气电磁阀同时打开,切割枪横向摆臂切割铸坯,当切割完成后,切割机碰到行程限位开关停止切割并返回原位。
2)定尺定重系统原理:系统通过红外摄像机远距离采集运动铸坯的图像信息,采用先进的图像处理技术,在线识别热红坯的长度,利用计算机对图像信息进行模式识别程序处理,形成操作信息并转换成规定格式的电控信号(切割信号)给到PLC输入端,PLC根据切割信号控制切割机完成切割。
3)切割枪返回设计原理:由于连铸机切割系统对定尺切割的尺寸要求比较精确,但对切割完成后切割机的返回行程要求则相对较宽(切割机切割行程在1.1m到1.5m之间),因此给设计带来了可行。
当切割信号给到PLC,并控制切割机开始切割时,设计PLC程序对铸坯的拉速信号进行采集并累加,当累加的拉距值接近原有限位开关的位置距离值时,使PLC程序断开切割机包夹信号,松开包夹,切割机由配重装置牵引回到原位,等待下一次切割。
四、 PLC程序设计由于连铸机生产系统中的PLC程序已经满足当前控制的需要,改进的切割机返回系统只需在原有PLC主程序中加入设计的切割机返回的功能模块FC,当切割机开始定尺切割铸坯时调用此FC模块即可。
因此对PLC主程序不再赘述,只对拉速采集程序以及设计的功能模块FC简单叙述一下,以阐明工作原理。
连铸切割系统在炼钢企业中的应用及优化
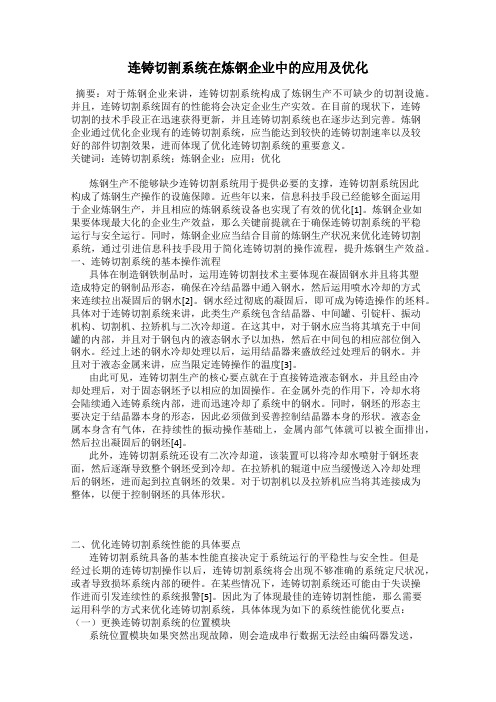
连铸切割系统在炼钢企业中的应用及优化摘要:对于炼钢企业来讲,连铸切割系统构成了炼钢生产不可缺少的切割设施。
并且,连铸切割系统固有的性能将会决定企业生产实效。
在目前的现状下,连铸切割的技术手段正在迅速获得更新,并且连铸切割系统也在逐步达到完善。
炼钢企业通过优化企业现有的连铸切割系统,应当能达到较快的连铸切割速率以及较好的部件切割效果,进而体现了优化连铸切割系统的重要意义。
关键词:连铸切割系统;炼钢企业;应用;优化炼钢生产不能够缺少连铸切割系统用于提供必要的支撑,连铸切割系统因此构成了炼钢生产操作的设施保障。
近些年以来,信息科技手段已经能够全面运用于企业炼钢生产,并且相应的炼钢系统设备也实现了有效的优化[1]。
炼钢企业如果要体现最大化的企业生产效益,那么关键前提就在于确保连铸切割系统的平稳运行与安全运行。
同时,炼钢企业应当结合目前的炼钢生产状况来优化连铸切割系统,通过引进信息科技手段用于简化连铸切割的操作流程,提升炼钢生产效益。
一、连铸切割系统的基本操作流程具体在制造钢铁制品时,运用连铸切割技术主要体现在凝固钢水并且将其塑造成特定的钢制品形态,确保在冷结晶器中通入钢水,然后运用喷水冷却的方式来连续拉出凝固后的钢水[2]。
钢水经过彻底的凝固后,即可成为铸造操作的坯料。
具体对于连铸切割系统来讲,此类生产系统包含结晶器、中间罐、引锭杆、振动机构、切割机、拉矫机与二次冷却道。
在这其中,对于钢水应当将其填充于中间罐的内部,并且对于钢包内的液态钢水予以加热,然后在中间包的相应部位倒入钢水。
经过上述的钢水冷却处理以后,运用结晶器来盛放经过处理后的钢水。
并且对于液态金属来讲,应当限定连铸操作的温度[3]。
由此可见,连铸切割生产的核心要点就在于直接铸造液态钢水,并且经由冷却处理后,对于固态钢坯予以相应的加固操作。
在金属外壳的作用下,冷却水将会陆续通入连铸系统内部,进而迅速冷却了系统中的钢水。
同时,钢坯的形态主要决定于结晶器本身的形态,因此必须做到妥善控制结晶器本身的形状。
连铸机火切机技改效益分析报告

关于山东广富集团有限公司炼钢厂连铸坯火切机技改效益分析及技改方案的报告尊敬的广富集团公司领导:根据“国家发改委2012年第10号公告”(请点击查阅)的“万家企业节能低碳行动”企业名单及节能量目标(请点击查阅),广富集团的“十二五”节能量目标已锁定为85740吨标准煤(125页第68项)。
为积极响应国家节能减排降耗的号召,我司工程技术人员于去年11月底对贵司的炼钢厂相关设备及工艺流程做了初步的研究分析,现就贵司炼钢厂的当前切割工艺和我公司的高效节能减排降耗切割工艺,并就贵司炼钢厂的方坯生产线做出详细分析如下:一、方坯:1.按年产50万吨六机六流方坯生产线计算:设“120”组:尺寸为120×120×5200、中期割缝平均6mm、年产50万吨。
设“150”组:尺寸为150×150×7000、中期割缝平均6mm、年产50万吨。
设“120”组:尺寸为200×200×9000、中期割缝平均6mm、年产50万吨。
2. 方坯单支重量:“120”组:方坯单支重量:0.12×0.12×5.2×7.85=0.59吨“150”组:方坯单支重量:0.15×0.15×7×7.85=1.24吨“200”组:方坯单支重量:0.20×0.20×9×7.85=2.83吨3. 方坯支数(切割刀数):“120”组:500000÷0.59≈847457支“150”组:500000÷1.24≈403225支“200”组:500000÷2.83≈176678支4. 金属收得率:(即钢材节省率)我公司中期割缝平均为3.5mm,割缝节省分别为:“120”组:6-3.5=2.5mm;单支:0.12×0.12×0.0025×7.85≈0.000283吨“150”组:6-3.5=2.5mm;单支:0.15×0.15×0.0025×7.85≈0.000442吨“200”组:6-3.5=2.5mm;单支:0.20×0.20×0.0025×7.85≈0.000785吨钢材节省总量:“120” 组:847457支×0.000283≈239.83吨“150” 组:403225支×0.000442≈178.23吨“200” 组:176678支×0.000785≈138.69吨5.燃气消耗:按设定的贵司方坯尺寸,我司每切割1支方坯消耗丙烷约0.015m3(0.03kg)。
提高定尺剪切系统剪切精度的方法与应用
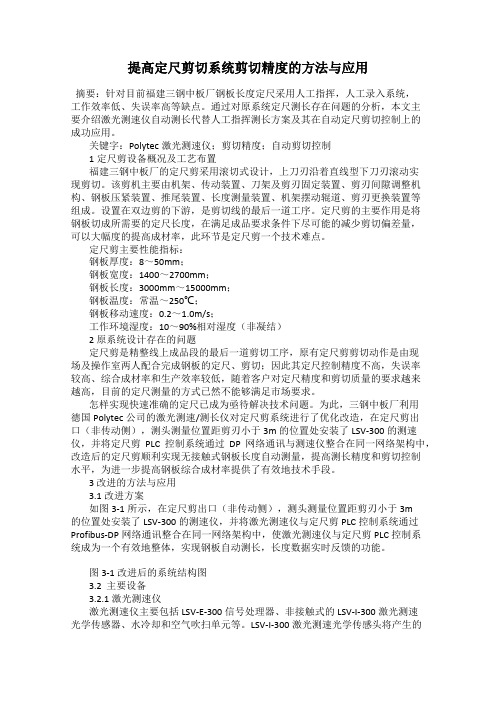
提高定尺剪切系统剪切精度的方法与应用摘要:针对目前福建三钢中板厂钢板长度定尺采用人工指挥,人工录入系统,工作效率低、失误率高等缺点。
通过对原系统定尺测长存在问题的分析,本文主要介绍激光测速仪自动测长代替人工指挥测长方案及其在自动定尺剪切控制上的成功应用。
关键字:Polytec激光测速仪;剪切精度;自动剪切控制1定尺剪设备概况及工艺布置福建三钢中板厂的定尺剪采用滚切式设计,上刀刃沿着直线型下刀刃滚动实现剪切。
该剪机主要由机架、传动装置、刀架及剪刃固定装置、剪刃间隙调整机构、钢板压紧装置、推尾装置、长度测量装置、机架摆动辊道、剪刃更换装置等组成。
设置在双边剪的下游,是剪切线的最后一道工序。
定尺剪的主要作用是将钢板切成所需要的定尺长度,在满足成品要求条件下尽可能的减少剪切偏差量,可以大幅度的提高成材率,此环节是定尺剪一个技术难点。
定尺剪主要性能指标:钢板厚度:8~50mm;钢板宽度:1400~2700mm;钢板长度:3000mm~15000mm;钢板温度:常温~250℃;钢板移动速度:0.2~1.0m/s;工作环境湿度:10~90%相对湿度(非凝结)2 原系统设计存在的问题定尺剪是精整线上成品段的最后一道剪切工序,原有定尺剪剪切动作是由现场及操作室两人配合完成钢板的定尺、剪切;因此其定尺控制精度不高,失误率较高、综合成材率和生产效率较低,随着客户对定尺精度和剪切质量的要求越来越高,目前的定尺测量的方式已然不能够满足市场要求。
怎样实现快速准确的定尺已成为亟待解决技术问题。
为此,三钢中板厂利用德国Polytec公司的激光测速/测长仪对定尺剪系统进行了优化改造,在定尺剪出口(非传动侧),测头测量位置距剪刃小于3m的位置处安装了LSV-300的测速仪,并将定尺剪PLC控制系统通过DP网络通讯与测速仪整合在同一网络架构中,改造后的定尺剪顺利实现无接触式钢板长度自动测量,提高测长精度和剪切控制水平,为进一步提高钢板综合成材率提供了有效地技术手段。
连铸机精度提高方法的研究
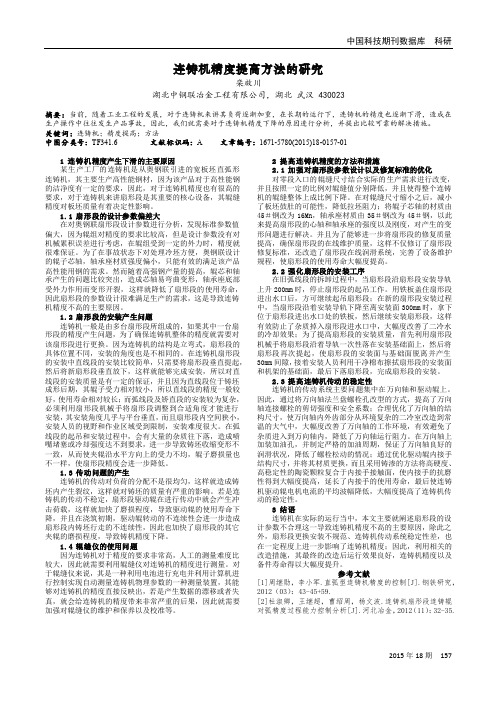
中国科技期刊数据库 科研2015年18期 157连铸机精度提高方法的研究栾啟川湖北中钢联冶金工程有限公司,湖北 武汉 430023摘要:当前,随着工业工程的发展,对于连铸机来讲其负荷逐渐加重,在长期的运行下,连铸机的精度也逐渐下滑,造成在生产操作中往往发生产品事故,因此,我们就需要对于连铸机精度下降的原因进行分析,并提出比较可靠的解决措施。
关键词:连铸机;精度提高;方法 中图分类号:TF341.6 文献标识码:A 文章编号:1671-5780(2015)18-0157-011 连铸机精度产生下滑的主要原因某生产工厂的连铸机是从奥钢联引进的宽板坯直弧形连铸机,其主要生产高性能钢材,因为该产品对于高性能钢的洁净度有一定的要求,因此,对于连铸机精度也有很高的要求,对于连铸机来讲扇形段是其重要的核心设备,其辊缝精度对板坯质量有着决定性影响。
1.1 扇形段的设计参数偏差大在对奥钢联扇形段设计参数进行分析,发现标准参数值偏大,因为辊组对精度的要求比较高,但是设计参数没有对机械累积误差进行考虑,在辊组受到一定的外力时,精度就很难保证。
为了在事故状态下对处理冷坯方便,奥钢联设计的辊子芯轴,轴承座材质强度偏小,只能有效的满足该产品高性能用钢的需求。
然而随着高强钢产量的提高,辊芯和轴承产生的问题比较突出,造成芯轴易弯曲变形,轴承座底部受外力作用而变形开裂,这样就降低了扇形段的使用寿命,因此扇形段的参数设计很难满足生产的需求,这是导致连铸机精度不高的主要原因。
1.2 扇形段的安装产生问题连铸机一般是由多台扇形段所组成的,如果其中一台扇形段的精度产生问题,为了确保连铸机整体的精度就需要对该扇形段进行更换。
因为连铸机的结构是立弯式,扇形段的具体位置不同,安装的角度也是不相同的。
在连铸机扇形段的安装中直线段的安装比较简单,只需要将扇形段垂直提起,然后将新扇形段垂直放下,这样就能够完成安装,所以对直线段的安装质量是有一定的保证,并且因为直线段位于铸坯成形后期,其辊子受力相对较小,所以直线段的精度一般较好,使用寿命相对较长;而弧线段及矫直段的安装较为复杂,必须利用扇形段机械手将扇形段调整到合适角度才能进行安装,其安装角度几乎与平台垂直,而且扇形段内空间狭小,安装人员的视野和作业区域受到限制,安装难度很大。
连铸坯坯长定尺精度分析与调整

炼钢厂冶炼的钢水经连铸机连续浇铸为钢坯 ,
钢坯 根 据下 工序 的需 要切 割 为一 定长 度 的铸 坯 , 铸
坯定尺精度对下工序 的影响相当大 , 定尺过长将造 成浪费, 定 尺过 短将 影 响成材 或成 品 , 甚 至报 废 。 钢 坯的长度与钢水成分和钢坯温度密切相关 , 将影响 切割后 的铸坯定尺长度。 铸坯长度定尺检测对铸坯 定 尺精 度最 为关 键 , 检测 方法 不 当将 造成 定 尺 长度 波动 , 影 响 定尺 精度 。 应 针对 设备 的实 际情况 , 合 理 应用检测方法 , 达到满足完全 同步的时 间) , 当此 时 间一 定 或 波 动较 小 时 , 影 响 定 尺较 小 , 当此 时间 波 动较 大 时 , 影 响 定 尺较 大 。 切 割 装 置原 位 主 要取决于检测信号 , 当原位检测信号误差范围较小 或一定时 , 影响定 尺较小 , 当原位检测信号误差波 动时 , 影 响定尺较 大 。 4 铸坯 长 度定 尺检测 铸 坯 长度定 尺 检测方 法 较多 , 主 要有将 连 铸机 拉 速检 测信 号作 为铸 坯长 度 检测信 号 、 连铸 坯 上安 装同步装置测量铸坯长度 、 铸坯定尺长度位置安装 检测开关测量长度 、铸坯摄像定尺检测长度等 。 连 铸机 拉矫 系统 电机 安装 有许 多编 码器 , 用 于检 测铸 机 的拉坯 速度 和浇 铸长 度 。 利用 拉矫 机 编码器 检 测 信号作为铸坯定尺长度检测是最简单 的方法。 此检 测方法 的优点是不增加任何设备 , 节约投资 , 缺点 是拉矫编码器信号波动较大 , 对铸坯长度定尺影响 相 当大 , 定 尺精 度 非 常低 。 连铸 坯 上 安 装 同步 测 量 轮 检测 定 尺 长 度 , 检 测 装 置相 对 简单 , 投 资设 备 较 少, 但 因铸坯温度较高 , 对测量装置造成易变形 、 故 障高及测量精度低 。 铸坯长度定尺位置安装检测开 关测量长度方法 , 是根据定尺长度距切割装置原位 的距离处安装检测开关 ( 主要为光电开关 ) , 当铸坯 头到达此位置时 , 检测开关发送信号 , 切割装置 同 步切割。 此检测方法的优点是设备简单 , 投资较小 , 检 测精 度 较 高 , 缺 点 是 只 能检 测 一 种定 尺 , 当定 尺 变化时必须移动检测开关 。铸坯摄像定尺检测方 法, 是安 装摄 像装 置 和计算 机 程序来 实 现铸 坯长 度 的检 测 。此 检 测 方法 的优 点 是解 决 了环境 因素 影 响, 提高了自动化程度 , 检测灵活及精度较高 , 缺点 是投资较高。 铸 坯长 度定 尺检 测与 切 割装置 原 位密 切相 关 , 切 割装 置原 位检测 方 法主要 有 原位 开关 检测 、 开 关
连铸机扇形段存在的问题及改善途径分析

连铸机扇形段存在的问题及改善途径分析[摘要]扇形段是连铸系统工艺中的重要设备之一,扇形段工作性能直接影响后续板坯轧制厚度的均匀性,对钢坯质量起着关键性作用。
通过对莱钢型钢炼钢连铸机扇形段存在的问题进行分析,进行相应的技术方案改进,对提高产品质量、降低耗能、减轻工人劳动量取得了良好的经济效益。
[关键词]扇形段;连铸机;轴承中图分类号:文献标识码:A 文章编号:1009-914X(2014)04-0321-011 前言扇形段是连铸机重要组成部分,是集机械、干油润滑、水冷系统系统于一体的关键重要设备。
每个扇形段由辊子及其轴承座、上下框架、辊缝调整装置、辊子压下装置、冷却水配管、给油脂配管等构成。
扇形段传动辊由直流机、齿接手、行齿轮减速机、万向接手等构成。
驱动装置通过万向接手穿过二冷室壁与驱动辊的中间法兰相连接。
扇形段的上下框架都是钢板焊接的结构,在上下框架上分别安装着内弧和外弧侧的辊子及轴承座。
辊子的对中则在机外方对中台上通过调整轴承座下面的垫片来达到。
放轴承座的位置是经过机加工的。
此外,在上下框架上,还安装着各种冷却水配管、压缩空气和给油脂配管。
在上下框架上安装有一对可升降的传动辊液压缸。
下框架的下部装有4个销缸,通过双楔和销子固定在大香蕉底座或基础框架上,同时还装有与水连接板相结合的装置。
随着生产节奏的加快,连铸浇筑速度的提升,型钢炼钢厂2#连铸机扇形段设备投入多年,加上扇形段工况环境恶劣,受受高温、粉尘、潮湿等因素的影响,扇形段框架锈蚀严重,已严重影响了产品质量。
2 连铸扇形段存在问题分析型钢异型坯连铸机自投产以来,由于连铸机扇形段最初设计存在一定的缺陷,加上设备结构复杂,工况条件差,扇形段运行状况不甚理想,经常出现各种各样的故障,严重影响了连铸生产节奏,对连铸铸坯质量存在不同程度的影响,造成严重经济损失。
通过总结扇形段长出现的故障,对现有问题进行综合分析,主要存在以下几个方面的问题::扇形段辊子扇形段辊子组成的流道是铸坯的通道,主要用来支承、导向、拉矫铸坯。
连铸机模拟定尺自动控制系统的研究与应用

连 铸 机 模 拟 定 尺 自动 控 制 系 统 的 研 究与 应 用
赵 春 佳
( 钢 集 团 自动 化 部 山 东 莱 芜 2 1 o 莱 7 1 4)
[ 摘 要 ]在 现 代 化 连 铸 工 艺 生 产 过 程 中 ,铸 坯 需 按 一 定 长 度 精 度 进 行 切 割 ,本 文 提 出 的 模 拟 定 尺 切 割 系 统 ,利 用 铸 机 自带 的 西 门 子 S7 ~ 4 L 控 制 系 统 编 程 , 实 j 铸 坯 高 精 度 定 长 切 割 , 与 传 统 的 红 外 定 尺 系 统 相 比 , 具 有 投 资 少 、 故 障 率 低 、 运 行 稳 定 等 优 点 ,在 冶 金 行 oP 0 C 见了 业具 有广 泛 的应 用 前景 。 [ 关键 词 ]自动 控 制 模 拟 定 尺 连 铸 中 图 分 类 号 :T P 文 献 标 识 码 :A 文 章 编 号 :1 0 - 1 X( 0 ) 6 0 4 - 1 9 9 2 1 0 - 0 9 0 0 4 0
备 。其 工 作 原 理 如 下 : ( ) 据 采 集 1数
! ±
2
其 中 :
S :铸坯 的行程 ;S :铸坯每 个 8 m n 0 S的行程 ;V:铸坯每个 8 m 0s 的 平均速 度 ;V :每 个 8 I . 0l l S开始 时 的瞬 时拉速 ;V, :每个 8 m 0 S结 时的瞬 时 拉速 ;Sl .在 监控 操 作画面 上 设定 的定尺 长度 ;q:根 _ 据 实 际工 况 设定 的补 偿 系数 。
1、 前 言
=
20 0 5年 7月莱 钢炼钢厂新 二区 5 替连铸红 外切割定尺 系统正式投 产 以来,频繁 出现不 检测或切 长短尺 的现象 ,在此条件下 ,通过对定 尺系统的改造 ,利用编程算 出切割尺 寸并发 出切割信 号,避免 了原有 红外定尺系统依靠摄 像头检 测铸坯 度 ,容 易受外界环境 的影响 ,故 障率较高等缺点 。木 系统 的成 功应用 ,不仪 降低 了生产成 本,减少 了 劳动 强度 , 而 且还 大 大 提 高 了钢 坯 成 坯 合 格 率 , 提 高 了 生 产 膏 。 夏 2、模拟 切 割 系 统 的 自 动控 制 2 1模拟切 割定尺 自动控制系统 的硬件 . 本系统涉及 到的连铸机 设备有 铸流 西门子 S — 0 7 4 0控 t 系 统 、 液 i 9 面 自控 系 统 、 执 行 设 备 ( 括 火 焰 切 割 机 、 加 紧 汽 缸 、 返 回 汽 缸 )等 , 包 需 要 通 汛模 块 与 变 频 器 建 立 通 讯连 接 ,通 过 A I和 D I采 集 的 数 据 送 到 CU P ,经 过 数 据 处 理 ,通 过 D 0模 板 发 出命 令 , 敛 使 继 电器 和 接 触 器 吸 合 ,使 汽 缶 、 火 切 机 完 成 切 割 动 作 。 丁 2. 拟 定 尺 切 割 系 统 的 软 件 实 现 2模 模 拟定尺切 割系统直接 利用连 铸机铸 流西 门子 s — 0 7 4 0控 制系统 采 集 的 铸 坯 瞬 时 拉述 V,进 行 数 学 运 算 得 到 铸 坯 行 程 ,并 根 据 铸 坯 行 程 控 制 火 焰 切 割 机 、加 紧 汽 缸 、返 回 汽 缸 完 成 铸 坯 切 割 。 整 个 过 程 在 连铸机铸 流西 门予 S — 0 4 0控 制 系 统 中 完 成 , 编 程 语 言 使 用 S P 7 TE 7, 操 作 及 监 控 画 面 在 铸 机 工控 机 ( 用 W N C . 使 IC 6 0)上 完 成 ,无 需额 外 设
- 1、下载文档前请自行甄别文档内容的完整性,平台不提供额外的编辑、内容补充、找答案等附加服务。
- 2、"仅部分预览"的文档,不可在线预览部分如存在完整性等问题,可反馈申请退款(可完整预览的文档不适用该条件!)。
- 3、如文档侵犯您的权益,请联系客服反馈,我们会尽快为您处理(人工客服工作时间:9:00-18:30)。
水平连铸机定尺切割系统的分析与改进方法研究
摘要:火焰切割机的控制精度是水平连铸机生产的一个重要指标,直接影响钢坯的定尺精度和合格率。
红外摄像定尺系统因具有易于调整,系统轻便和控制精度相对较高等优点而在企业中得到广泛应用,但随着生产要求的不断提高,现有开环的非接触式控制系统因主要误差都是不可控的而很难再提高定尺精度,在对现有非接触式定尺控制系统进行详细的误差分析后,找到定尺误差主要是由钢坯的运动所导致的。
在此基础上,对现有控制系统进行改进,使之成为一闭环控制系统,大大减小因钢坯运动引入的误差,从而提高定尺精度。
关键词:连铸机,定尺切割,红外摄像,闭环控制
1 引言
在水平连铸机生产过程中,火焰切割机将钢坯切割成一定尺长度,以满足轧钢机的要求。
由于火焰切割机是在高温下长时间持续运行的,所以要求其具有极高的可靠性和良好的可维修性。
常用的火焰切割机由定尺控制系统,切割系统和冷却系统组成,钢坯切割能否达到定尺要求关系到连铸机能否向下一道工序提供合格的产品问题。
钢坯定尺大于设定尺寸,则浪费坯料,小则造成废品。
因此,钢坯定尺精度和合格率就成了连铸机生产的一项重要指标,故对火焰切割机定尺控制是非常有必要的[1]。
常用到的定尺切割系统有人工目测,机械挡板,碰球定尺和非接触式红外摄像定尺系统等。
红外摄像自动定尺系统通过红外摄像机远距离采集运动高温铸坯的图像信息,计算机对图像信息进行模式识别程序处理,形成操作信息并转换为规定格式的电信号,用以控制火焰切割机对高温铸坯进行定尺切割[2]。
相对于其它集中定尺控制系统,非接触式定尺系统具有易于调整,系统轻便,可以使用计算机控制和控制精度相对较高的等优点,现已在许多企业得到了广泛使用。
但由于现有的控制系统多为开环的,存在定尺尺寸浮动较大,铸坯定尺合格率仍难以达到企业对铸坯成本最小化的要求,因此有必要对现有控制系统进行改进。
2现有非接触式定尺系统分析
红外摄像定尺切割系统是通过两个红外线端口来检测高温钢坯的位置,先设定好定尺尺寸,当高温钢坯到第一个检测位置后,系统开始做准备工作,当到了第二个检测位置后,控制系统给切割小车一个信号,切割小车的两支夹脚夹住钢坯并与钢坯一起运动并切割。
切割完成后小车复位,等待下一个信号,完成一次定尺切割,其主要的误差来源有以下几点。
①红外线检测误差,大概为5mm。
②红外线测量装置的位置误差,该误差较小,并可以控制。
③由于钢坯是运动的,当高温钢坯到达测量位置时可能以比较快的速度运动,从检测到计算机图像拟合完成并发出控制指令,继电器响应完成的时间内,钢坯可能已偏离定尺长度一段距离,该误差属于随机误差,无法控制,是定尺误差的主要来源之一。
④从继电器闭合到切割小车夹脚动作,需要比较长的时间,再加之切割小车质量较大,具有相当大的惯性,在夹脚加紧之前会产生滑移,这就相当于拿静止的东西来夹持运动的物体,会引入很大的误差,该误差也是随机误差,无法控制。
⑤开环系统,主要误差都是不可控的,精度很难再得到提高。
3 定尺切割系统的改进方案
从前面的分析可知,定尺误差主要是由高温钢坯的运动所导致的。
利用计算机处理速度快、软件控制灵活的特点,可以在原有红外摄像定尺控制系统的基础上进行改进,使之成为一个闭环控制系统。
其系统框图如图1所示。
图中是设定尺寸,是夹钳加紧后的钢坯测量尺寸,从图中可以看出只需对原控制软件稍加改进并添加一火焰喷嘴移动机构即可。
其改进后的工作示意图如图2所示。
该系统式在切割行走小车前端连接一固定臂,固定臂下方安装一耐高温滚珠丝杠和一根滑杆,滚珠丝杠由步进电机驱动。
在滚珠丝杠和滑杆上安装与切割喷嘴相连的滑动块。
由于红外线检测装置的检测范围较宽,相当于一个检测窗,利用计算机设定定尺长度,工作时,当高温钢坯运动到定尺标线时,发出控制指令,夹脚动作,夹紧钢坯。
在夹脚加紧钢坯,行走小车开始脱离定位挡块的同时,用红外线检测装置读出此时高温钢坯的实际长度,实际长度和定尺长度之间的差值就是该次动作的误差,此时行走小车与管坯相对静止,计算机计算出该误差后判断该误差是否大于零且小于允许偏差,若成立,则直接切割,若不成立,则控制步进电机转动,使滑动块移动相应的距离后停止,喷嘴开始喷火切割钢坯。
当切割完成后,停止喷火,夹脚松开,行走小车回退到与定位挡块解出,与此同时,步进电机带动滑动块移动到初始位置,完成一次切割动作。
4 结语
在水平连铸机生产过程中,为了得到跟高的定尺合格率,进一步提高定尺测控精度,降低企业生产时浪费的坯料和废品率,从而降低生产成本,提高生产效率,现有的定尺控制系统已不能满足企业的生产要求,改进后的准闭环控制系统克服了因高温钢坯运动而导致的误差,定尺测控精度得到了大幅度提升,能极大的满足轧钢对钢坯切割精度的要求,能有效地避免铸坯的浪费,提高金属的收得率。
参考文献:
[1]程加堂,向凤红,付浩伟.基于PLC的连铸火切机应用设计[J].冶金丛刊,2008,(1).
[2] 田汉蒲.新技术在衡钢3#水平连铸机上的应用[J].金属材料与冶金工程,2008,(2).
[3] 陈厚田.PLC控制水平连铸机的原理和设计[J].制造业自动化,2001,(1).
[4]宋志刚,蔚小玲.非接触式定尺切割系统在连铸机上的应用[J].连铸,2006,(2).
[5]王进,徐小雷.非接触式方坯自动定尺切割系统[J].冶金自动化,2000,(5).
[6]于家涌,马秋波,徐维利,等.非接触方坯自动定尺切割系统的应用[J].黑龙江冶金,2004,(3).
[7] 张治国,王付令,郭建党,等.红外摄像定尺技术在板坯连铸机中的应用[J].冶金丛刊,2006,(4).
[8]贾志富,于长江.连铸火焰切割机自动控制系统的开发[J]黑龙江冶金,2002,(3).
[9]赵良,李世文.连铸自动定尺火焰切割方法[J].设备管理与维修,2007,(8).
[10]郭军林,王三忠.摄像定尺技术在板坯连铸机铸坯定尺切割上的应用[J].河南冶金,2008,(1).。