配料仓设计说明
360配料室料仓施工方案要点

宣钢3#360m2烧结机工程配料室料仓制安方案编制:审核:批准:河北宣化钢盛建安公司2014-4-18目录一、工程概况--------------------------------------------------------------1二、施工依据----------------------------------------------------------------1三、施工准备----------------------------------------------------------------1四、施工工艺要求---------------------------------------------------1-5五、具体制作安装施工------------------------------------------------5-14六、运输方案------------------------------------------------------------14-15七、劳动力计划----------------------------------------------------------15-16八、施工机具--------------------------------------------------------------16九、工程质量保证措施-------------------------------------------------17-18十、安全保证措施-------------------------------------------------------18-23 十一、工期保证措施----------------------------------------------------23-24 十二、现场文明施工措施-----------------------------------------------24一、工程概况配料仓18个,共六种规格,料仓外形尺寸基本一致。
配料仓的设计与计算
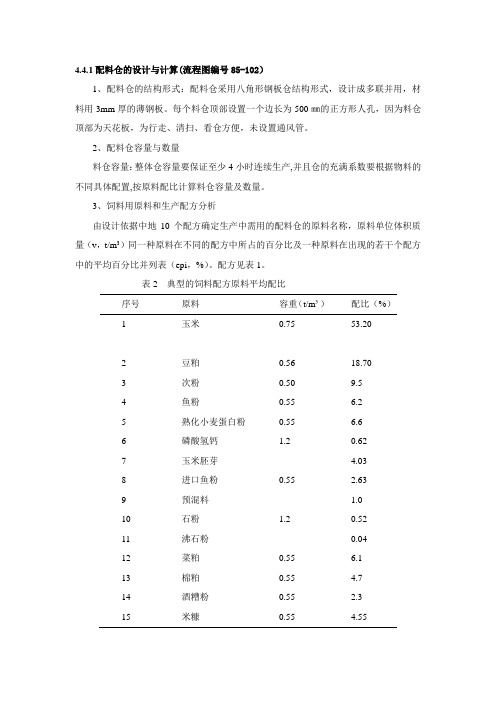
4.4.1配料仓的设计与计算(流程图编号85-102)1、配料仓的结构形式:配料仓采用八角形钢板仓结构形式,设计成多联并用,材料用3mm厚的薄钢板。
每个料仓顶部设置一个边长为500㎜的正方形人孔,因为料仓顶部为天花板,为行走、清扫、看仓方便,未设置通风管。
2、配料仓容量与数量料仓容量:整体仓容量要保证至少4小时连续生产,并且仓的充满系数要根据物料的不同具体配置,按原料配比计算料仓容量及数量。
3、饲料用原料和生产配方分析由设计依据中地10个配方确定生产中需用的配料仓的原料名称,原料单位体积质量(v,t/m3)同一种原料在不同的配方中所占的百分比及一种原料在出现的若干个配方中的平均百分比并列表(epi,%)。
配方见表1。
表2 典型的饲料配方原料平均配比序号原料容重(t/m³)配比(%)1 玉米0.75 53.202 豆粕0.56 18.703 次粉0.50 9.54 鱼粉0.55 6.25 熟化小麦蛋白粉0.55 6.66 磷酸氢钙 1.2 0.627 玉米胚芽 4.038 进口鱼粉0.55 2.639 预混料 1.010 石粉 1.2 0.5211 沸石粉0.0412 菜粕0.55 6.113 棉粕0.55 4.714 酒糟粉0.55 2.315 米糠0.55 4.554、典型单体仓几何仓容计算 根据公式Vi=iktepi Q γ⨯⨯选定5%≤epi ≤10%的几种原料计算典型单体仓仓容式中: epi ——几种原料出现在若干个配方中的平均百分数(%);Vi ——原料的单位体积质量(t/m 3); Q ——配合饲料厂的设计生产能力(t/h ); t ——原料在料仓中的存放时间,取t=3h ; k ——单体仓的有效仓容系数,取k=0.80。
通过计算10种典型的配方,可知次粉的平均配比为9.5% 则有: V 次粉 =80.050.03%5.920⨯⨯⨯=14.25 m 35、基本仓仓容的确定由5%≤epi ≤10%原料所在单体仓的仓容大小得:V 基本仓=14.25 m 3 单体仓数量的配置:epi >10%,有2种原料;6个基本仓,其中2个存放玉米的基本料仓尺寸加大。
污泥配料仓设计说明书技术质询

四、搅拌轴动力
1、搅拌主轴 1)、空心主轴尺寸:φ108*δ10*3000mm 2)、实心主轴见图纸 3)、搅拌页片:见图纸 2、密 封:参见螺旋密封 3、轴 承 座:UCF316 4、减速电机: GRA77-63.03-Y3参数: 转速23r/min 输出转矩:1027N.M =2.47kw; 许用径向载荷10KN 使用系数:1.15 ; 孔端直径60H7。
叶片厚度 (δmm) 2~4mm 4~5mm 7~8mm
四、螺旋输送量
双螺旋输送量 Q=12.42m³
5、螺旋输送量的验算 Q=47D²ψCSpN Q:输送量T/H D:叶片直径 D=0.258m ψ水平输送时物料的填充系数: ψ=0.3 C 倾斜输送系数,C=1 p物料堆积比重:p=1.3T/M³ S螺距 S=0.206m N螺旋转速 n=33r/min 代入公式Q=47*0.0665*0.3*1*0.206*1.3*33*1.5(双螺旋输送系
四、螺旋动力
螺旋主动轴最小轴径 D=60mm
6、螺旋轴的最小轴径: 根据轴的计算公式: d> =A*3√P/n 或 3√5T/[t] d:计算截面处轴的直径 (mm)。 T:轴传递的额定转矩(N.mm) T=1010Nm= 9.55E6P/n P:轴传递的额定功率。(kw) 3.49kw N:轴的转速。 (r/min) 33r/min [t]:轴的许用切应力(MPa) 20MPa A:按[t]定的系数。 135 d> A*3√P/n=135*3√3.49/33 =135*0.525=59.11mm 螺旋主动轴最小轴径选d=60mm
四、螺动力
联轴器、轴端密封
7、螺旋联轴器: 选用凸缘联轴器,具体型号见标准件样本。 8、轴端密封 动密封分为以下几种密封形式: 填料密封 骨架密封 机械密封 迷宫密封。 我们选用填料密封,采用斜开口石墨圈3层密封。 形式见下图,尺寸75*95*10mm。
食品仓库设计要求

食品仓库设计选址布局设计设施仓库设计相关标准是《(单层)通用仓库及库区规划设计参数》〔GB/T28581〕。
通用仓库,是指除冷藏冷冻、危险品等具有特殊要求的货物外,能满足货物一般储存要求的仓库。
·作业区,是指库区内进行货物储存、装卸、搬运、加工等作业的区域。
·辅助作业区,是指库区内进行作业设备充电、保养、维修及安装的区域。
·装卸作业区,是指用于停靠车辆并进行货物装卸的作业区域。
·站台登车桥,是指当货车底板平面与装卸货站台平面有高度差时,可使手推车、叉车无障碍地进入车厢内的装置。
一、库区选址应从地区产业布局、企业发展战略、客户分布、库区定位、存储货物类别、包装、存储量及波动系数、环境与消防要求、交通条件、地质条件、城市规划、供排水、供电等方面进行综合评价,确定仓库建设具体地点及库区规模。
二、库区布局1、平面布局根据库址的地理形状、气候条件和客户类别、仓库功能、存储特性、拣选模式及作业流程、防火要求等因素,合理规划库区内的作业区、装卸作业区、辅助作业区、办公区、停车场、库区出入口与通道、排水系统的位置与设计参数,做到布局合理、安全、高效,并能充分提高土地利用率。
2、仓库布局应根据库区地形地貌、占地面积、气候条件和服务功能定位、物流动线、运输车辆类型等因素,确定仓库布局。
(1)库区功能区。
作业区、辅助作业区、办公区与停车场应分区布置。
办公区宜设于库区主入口处,辅助作业区应充分利用库区的边角用地。
装卸作业区的宽度及地面承重应根据运输车辆类型、作业方式等进行规划,应满足12.192m(40英尺,下同)集装箱卡车作业需要。
单侧装卸作业时宽度(含车辆通道)宜不小于30m;相向作业时,宽度(含车辆通道)宜不小于45m。
应根据当地气候条件,采取必要的防雨、防雪措施。
(2)通道布局。
库区通道的宽度、承重、转弯半径应满足12.192m集装箱卡车通行的要求,并结合消防通道要求对库区主通道与库区车流走向进行规划。
混凝土配料系统设计与优化

混凝土配料系统设计与优化一、引言混凝土是建筑工程中常用的材料之一,混凝土配料系统的设计与优化是混凝土施工中关键的环节之一。
合理的混凝土配料系统设计与优化可以提高混凝土的强度、耐久性、抗裂性等性能,从而增强混凝土的使用寿命和安全性。
本文将着重介绍混凝土配料系统的设计与优化,包括混凝土配料系统的组成、混凝土配料系统设计的原则、混凝土配料系统优化的方法等内容。
二、混凝土配料系统的组成混凝土配料系统主要由以下几个组成部分组成:1. 水泥仓:储存水泥的设备,通常采用钢板制成,具有防潮、防漏、防火等功能。
2. 骨料仓:储存石子、沙子等骨料的设备,骨料仓的大小和数量根据混凝土的配比和生产能力确定。
3. 混凝土搅拌机:混合水泥、骨料、水等原材料的设备,通常采用双卧轴强制式混合机,具有搅拌均匀、产量大、操作简单等特点。
4. 控制系统:包括计量系统、控制系统、自动化系统等,用于控制混凝土配料系统的生产过程,保证混凝土质量的稳定性和生产效率的高效性。
5. 输送系统:包括输送带、螺旋输送机、气动输送系统等,用于将混凝土从搅拌机输送到施工现场。
三、混凝土配料系统设计的原则混凝土配料系统的设计应遵循以下原则:1. 合理的配比:根据混凝土的强度等要求,合理确定水泥、骨料、水等原材料的配比,保证混凝土的性能稳定。
2. 安全可靠:混凝土配料系统的设计应具有安全性和可靠性,防止设备故障和意外事故的发生,保障工人的人身安全。
3. 经济合理:混凝土配料系统的设计应具有经济合理性,既要保证混凝土的质量,又要尽可能减少生产成本。
4. 可维护性:混凝土配料系统的设计应具有可维护性,易于设备维修和保养,延长设备的使用寿命。
5. 环保节能:混凝土配料系统的设计应具有环保节能性,采用低噪音、低能耗、低排放的设备,减少环境污染。
四、混凝土配料系统优化的方法混凝土配料系统的优化主要包括以下几个方面:1. 混凝土配比优化:根据混凝土使用的环境和要求,进行混凝土配比的优化,使混凝土具有更好的强度、耐久性、抗裂性等性能。
配料仓设计

配料仓的设计目录摘要:一、配料仓的功能特性二、配料仓的结构、形状1.仓的组成2.仓体的形式3.斗仓的形式(优缺点)4.卸料口的位置、形状和尺寸5. 料仓的壁厚确定三、配料仓的设计1.基本设计原则:2.设计举例——20t/h饲料厂设计举例①饲料配方收集②典型单体仓仓容的计算③基本仓仓容的确定④单体仓数量的配置⑤配料仓体积的计算⑥设计注意事项四、配料仓的物料结拱及消除措施1.形成原因2.危害3.破拱原理4.具体方法五、料仓要求及物料流动(一)整体流动(二)中心流动六、配料生产工艺配料仓的设计一、配料仓的功能特性:配料仓是清理粉碎工段至混合工段中间仓,其功能是储存各种原料,按照配方要求在指定时间内向配料秤内准确供料。
二、配料仓的结构、形状1.仓的组成:仓体和斗2.仓体的形式(按结构形式分):①矩形:可以联壁,当群体仓使用时可以使整个空间利用率增大。
②圆形:单体仓使用时空间利用率高。
③多边形:结构复杂,应用较少。
注:中间仓体的横截面积相关原则:max边长≤2.5,min边长≥1.2;4在同一工程中为了制作安装方便,料仓的便常规个不宜过多,一般两种规格。
(参考书籍——《饲料工厂设计原理》P117)注:料仓配置原则——根据物料特征定仓型,而且应保证你料仓内物料“全进全出,先进先出”,尽量避免结拱产生;4.卸料口的位置、形状和尺寸①.卸料口位置:居中、侧边(偏心)、角部(偏心)三种(侧边及角部卸料可以在一定程度上破坏料流对称性,有利于防结拱);②.卸料口形状:矩形、方形、圆形(卸料性能:矩形>方形>圆形)③.出口尺寸——其是保证物料顺利卸出的重要参数,物料的顺利卸出还与斗仓倾角α以及出仓设备有关;注:斗仓倾角α:斗壁与水平面夹角或者斗仓壁曲线各点切线与水平面的夹角;我国斗仓倾角α的经验数据:粉料≥45°、粒料≥65°;对于矩形或者方形仓,斗仓倾角α应以斗仓邻壁的倾角值为准。
④.出口尺寸的最小允许值确定:在饲料厂中、麸皮、秸秆、米糠和鱼粉等内摩擦系数很高,卸料口最短边尺寸a或者最小直径均采用较大值≥200mm,长边≥仓体相应边的1/4;注1:物料内摩擦系数tanφ与初始剪切阻力τ0数据见参考资料《饲料加工工艺与设备》P14 表1-6;注2:当长边a/短边b=1(即为方形口)时,由实验证明,圆形卸料口的卸料性能类似于同宽度的的方形口;5. 料仓的壁厚确定:因为计算太过复杂,此处给出实际常用经验值,在实际应用时,常选用仓壁厚度为3-4mm钢板焊接,焊后去毛刺。
高水分原料配料仓的设计

对 称 方 仓 ,为仓 壁 与垂 直方 向 的 最 大 夹 角 ,以 保 证物料卸除 ( 出 口长 / 宽 ≥3)。d :适用 于对 称 筒 仓 ,为 防止 起 拱 的最 小 直 径 ,mm,d> ( 1 0×物 料 最 大 颗粒 尺 寸 );b :适 用 于对 称 方 仓 ,为 防止
了确保物料依靠 自 身重力实现卸料通畅 ,我们选择 了方形 仓 ,以减 少生 产 中清堵 的成本 。
2 . 3 导流板 的设 计
物 料 进 入 板 喂 机 时 ,导 流 板 不 采用 上 下 宽 度
一
致 的设计 ,而是前宽后窄 ( 见图2 )。物料运行
过程 中这 种设计 不会 出现 卡料 现象 ,物料 卸 出更加
增加人工岗位 、工人 劳动强度 和中控 的调整难度 。创新设计的新流程 ,不仅节约投资 、减少工作班次 ,还较
好地实现了 自动化控制 。 关键词 脱硫石膏 粘堵 流程 创新设计
0 引 言
造 成选粉 机 内导流 叶片 、风 道 内部极 易积料结 皮 ,
脱 硫 石 膏 又 称 排 烟 脱 硫 石 膏 ,主 要 成 分 和 天 然 石 膏 一 样 ,为 C a S O ・ 2 H, 0。 脱 硫 石 膏 是 火 电 厂 、炼 油 厂 等 工 厂 处 理 烟 气 中 的 S 0, 后 得
是 确保 物料 具有 最佳 的流 动性 。我 们从 实验 和受 力 两个 方 面开 展论证 工 作 。
( 1 )实 验 。
方形仓物料只有 向下的重力 ,其余方 向没有受力 ( 沿着 板 喂机 出料 方 向 );圆形 仓物 料重 力 分 力
有 垂 直于仓 壁 的压 力 。根据 受力 情况 分析 得知 方
用脱硫石膏替代天然石膏的水泥粉磨系统的创新设计
石料原料料仓设计手册

石料原料料仓设计手册一、前言石料原料料仓是矿山、石料加工厂等行业的重要设备,主要用于储存、加工、输送石料原料,为生产线提供原料供应。
设计合理的石料原料料仓可以提高生产效率、保障生产安全,并且节约空间、降低成本。
本手册旨在介绍石料原料料仓的设计原则、注意事项和工程实践,为相关从业人员提供参考。
二、设计原则1. 结构稳固:石料原料料仓的结构设计应考虑到原料的重量和流动性,确保料仓能够承受原料的重量,并保持在生产运作中不会发生倾斜或震动。
2. 储料能力:根据生产需求确定石料原料料仓的储料容量,确保能够满足一定周期内的生产需求,同时避免过度储料导致原料积压、老化、变质等问题。
3. 流通畅通:料仓内应设计合理的原料流动结构,确保原料能够顺畅地进出料仓,避免出现原料积压、卡料等情况。
4. 安全可靠:料仓的设计应考虑到生产操作人员的安全,如安装防护栏杆、紧急停车装置等安全设备,确保生产过程中的安全生产。
5. 维护便捷:考虑到料仓设备的日常维护和检修,设计中应留出足够的空间和通道,方便人员进行设备的维护和检修。
三、设计注意事项1. 材料选择:根据原料类型和储存环境选择适合的材料,如耐磨钢板、防腐蚀材料等,以保证料仓的耐用性和稳定性。
2. 原料流动设计:根据原料的流动特性和料仓的结构特点,设计合理的原料进出口、流通通道和导流装置,避免原料积压和卡料情况。
3. 环境气氛控制:考虑到料仓的储存环境,应考虑通风、降温、防潮等措施,以保护原料不受湿气、高温等影响。
4. 安全设施配置:根据料仓的尺寸、高度等情况配置安全扶梯、防护栏杆、紧急停车装置等安全设施,确保生产操作人员的安全。
5. 设备配套:设计料仓时需考虑与输送设备、破碎设备、筛分设备等的配套,以保证生产线的连续运作。
四、工程实践1. 设计方案确定:根据生产工艺、原料类型和生产能力等确定石料原料料仓的设计方案,包括结构形式、尺寸容量、布局等。
2. 材料采购:根据设计方案选择适合的材料,保证料仓的质量和稳定性。
- 1、下载文档前请自行甄别文档内容的完整性,平台不提供额外的编辑、内容补充、找答案等附加服务。
- 2、"仅部分预览"的文档,不可在线预览部分如存在完整性等问题,可反馈申请退款(可完整预览的文档不适用该条件!)。
- 3、如文档侵犯您的权益,请联系客服反馈,我们会尽快为您处理(人工客服工作时间:9:00-18:30)。
配料仓的设计目录摘要:一、配料仓的功能特性二、配料仓的结构、形状1.仓的组成2.仓体的形式3.斗仓的形式(优缺点)4.卸料口的位置、形状和尺寸5. 料仓的壁厚确定三、配料仓的设计1.基本设计原则:2.设计举例——20t/h饲料厂设计举例①饲料配方收集②典型单体仓仓容的计算③基本仓仓容的确定④单体仓数量的配置⑤配料仓体积的计算⑥设计注意事项四、配料仓的物料结拱及消除措施1.形成原因2.危害3.破拱原理4.具体方法五、料仓要求及物料流动(一)整体流动(二)中心流动六、配料生产工艺配料仓的设计一、配料仓的功能特性:配料仓是清理粉碎工段至混合工段中间仓,其功能是储存各种原料,按照配方要求在指定时间向配料秤准确供料。
二、配料仓的结构、形状1.仓的组成:仓体和斗2.仓体的形式(按结构形式分):①矩形:可以联壁,当群体仓使用时可以使整个空间利用率增大。
②圆形:单体仓使用时空间利用率高。
③多边形:结构复杂,应用较少。
注:中间仓体的横截面积相关原则:max边长≤2.5,min边长≥1.2;4在同一工程中为了制作安装方便,料仓的便常规个不宜过多,一般两种规格。
(参考书籍——《饲料工厂设计原理》P117)3.斗仓的形式(优缺点)注:料仓配置原则——根据物料特征定仓型,而且应保证你料仓物料“全进全出,先进先出”,尽量避免结拱产生;4.卸料口的位置、形状和尺寸①.卸料口位置:居中、侧边(偏心)、角部(偏心)三种(侧边及角部卸料可以在一定程度上破坏料流对称性,有利于防结拱);②.卸料口形状:矩形、方形、圆形(卸料性能:矩形>方形>圆形)③.出口尺寸——其是保证物料顺利卸出的重要参数,物料的顺利卸出还与斗仓倾角α以及出仓设备有关;注:斗仓倾角α:斗壁与水平面夹角或者斗仓壁曲线各点切线与水平面的夹角;我国斗仓倾角α的经验数据:粉料≥45°、粒料≥65°;对于矩形或者方形仓,斗仓倾角α应以斗仓邻壁的倾角值为准。
④.出口尺寸的最小允许值确定:在饲料厂中、麸皮、秸秆、米糠和鱼粉等摩擦系数很高,卸料口最短边尺寸a或者最小直径均采用较大值≥200mm,长边≥仓体相应边的1/4;注1:物料摩擦系数tan φ与初始剪切阻力τ0数据见参考资料《饲料加工工艺与设备》P14 表1-6; 注2:当长边a/短边b=1(即为方形口)时,由实验证明,圆形卸料口的卸料性能类似于同宽度的的方形口;5. 料仓的壁厚确定:因为计算太过复杂,此处给出实际常用经验值,在实际应用时,常选用仓壁厚度为3-4mm 钢板焊接,焊后去毛刺。
(数据来源——《饲料工厂设计原理》P120)三、配料仓的设计 1.基本设计原则:①按照设计生产能力及饲料配方中各种粉、粒料原料使用的平均百分数及种类来计算仓容和数量;②配料仓的总容积应保证4h 连续生产; ③仓容计算公式:Vi=ikt epi Q γ⨯⨯式中:Vi ——原料的单位体积质量(t/m 3); Q ——配合饲料厂的设计生产能力(t/h );epi ——几种原料出现在若干个配方中的平均百分数(%);t ——原料在料仓中的存放时间,取t=2h ;γi ——物料容重;k ——单体仓的有效仓容系数,取k=0.85。
④由公式得基本设计步骤:a.生产配方的收集(了解物料的种类数量以及质量百分数);b.计算各原料在个配方中平均质量分数epi ;c.设定基本储存时间t(t=3)和有效仓容系数k(k=0.85);d.确定典型原料的配比来计算典型单体仓仓容以此确定基本仓仓容;e.确定单体仓数量相应规格;f.计算总体积验算是否可行;2.设计实例——20t/h 饲料厂设计实例①饲料配方收集:该饲料配方为畜禽饲料配方,来源:.feed2008./;②典型单体仓仓容的计算:依据配方中各原料配比,由表可知:e pi>20%的原料有2种;10%≤e pi≤20%的原料有4种;1%<e pi<10%的原料有6种;e pi≤1%的原料有5种;易知10%≤e pi≤10%的配比较为密集,具有高度的典型性,故据仓容计算公式:Vi=ik tepi Qγ⨯⨯式中:Vi——原料的单位体积质量(t/m3);Q——配合饲料厂的设计生产能力(t/h);epi——几种原料出现在若干个配方中的平均百分数(%);t——原料在料仓中的存放时间,取t=3h;γi——物料容重;k——单体仓的有效仓容系数,取k=0.85。
通过计算10种典型的配方,可知次粉的平均配比为9.5%则有: V菜籽粕 =10.69 m³、V稻草粉=28.24m³、V米糠=14.71 、V次粉 =9.41m³;③基本仓仓容的确定由5%≤epi≤10%原料所在单体仓的仓容大小得:V基本仓=1/4(V菜籽粕+ V稻草粉+ V米糠+ V次粉)=13.42m3④单体仓数量的配置:针对已知的生产配方,计算出各种原料在各个配方中平均质量分数e pi,并据此将所涉及的原料分为 I 、Ⅱ、Ⅲ 3 类 (I 类>20%;5%<Ⅱ类<10%;Ⅲ类< 5% ),确定基本仓的规格和数目。
将配料仓群的单体仓设定为一个基本仓仓容和半个基本仓仓容的两种规格形式。
单体仓的数量原则上以生产配方中所涉及的原料数为基础,I 类每种原料各配置 2 个基本仓;Ⅲ类原料各配给1个1/2基本仓仓容的单体仓;而Ⅱ类原料各配给 1 个基本仓。
另外,还需考虑配给 1~2 个基本仓作为备用仓。
根据以上设定的单体仓的规格和数量计算配料仓群的总仓容。
具体配置如下:epi>20%, 2种原料:4个基本仓;5%≤epi≤10%, 4种原料:4个基本仓;1%≤epi≤5% ,6种原料:6个1/2基本仓,设计为小料仓;epi≤1%, 5种原料:2个1/2基本仓即可满足装料要求。
另配备2个1/2基本仓做回机料用仓。
有8个基本仓,10个1/2基本仓,一共18个配料仓。
⑤配料仓体积的计算配料仓由上下两部分组成,上部为四面柱体、下部分为截头方锥体;注:配料仓总高度一般占据生产车间一层楼高最好H=5.4m根据公式:A——四面体计算公式:V四面体=a1⨯b1⨯h式中,V四面体——四面体体积;a1 b1——分别表示仓体的上部矩形的两个边长;h——仓体的高度(m)。
B——配料仓截头方锥体计算公式:式中,V方锥体——中心对称截头方锥体体积(m3);a1b1——分别表示中心对称截头方锥体上部矩形的两个边长(m);a2b2——分别表示中心对称截头方锥体下部矩形的两个边长;h——中心对称截头方锥体的高度(m)所以Ⅰ.基本仓体积计算:确定——a1=2.1m 、b1=1.4 m 、 a2=b2=0.4m、四面体高度h0=4.6、中心对称截头方锥体h1=0.9;依据A和B给出的公式可以分别计算得:V四面体=a1⨯b1⨯h0= V基本仓=13.42m3;V方锥体=[a1b1+(a1+a2)(b1+b2)+a2b2]=1.14 m3V总1= V四面体 + V方锥体 =14.56 m3Ⅱ.(同理) 1/2基本仓总体积:确定——a3=1.6 、 b3=1.05、 a4=b4=0.4、中心对称截头方锥体h2=0.9 ;依据A和B给出的公式可以分别计算得:V四面体 =7.73 m3;V方锥体=0.71 m3 ;V总2=8.44 m3 Ⅲ.综合Ⅰ和Ⅱ得:配料仓总体积: V总= 8×V总1 + 10×V总2=8×14.56+10×8.44=200.88 m3因为整体仓容理论上要满足4h 连续生产,设计为20t/h,故存料会有80t;取平均容重0.5t/ m3 , k=0.85, 所以 V理论=80/0.5×0.85=188.23 m3 ;因为V总> V理论;所以设计满足要求.⑥设计注意事项:a.为保证料仓料斗倾角大于70°以避免粉状物料在料仓结拱,料斗采用大卸料口偏心卸料,卸料口位置依照需要而定,同时每个料仓斗都配备气锤以备不时之需。
,但其采用大卸料口偏心卸料可在一定程度上缓解结拱问题,同时料仓斗配备气锤,在结拱时可以气动强行破拱,因此可以保证生产的顺利进行。
b.中间仓的仓顶应设置进入孔和排气装置,入孔尺寸为500×500mm即可;排气装置的设置应便于排湿、防尘。
排气装置可以使通风除尘装置,仓群组可以共用一套排气装置,并在仓壁上端开设互通通道;c.为满足料仓的刚度要求,应在仓外设置加强筋。
四、配料仓的物料结拱及消除措施1.形成原因:主要因素有三点——物料储存时间的过长,水分增加导致物料结块;物料与仓壁的黏着作用;料仓的结构造型,导致物料无法顺利流通,局部会因为压力过大而结拱。
2.危害:破坏料仓工作的可靠性,导致物料流动中断,而且在破拱时物料塌下的瞬间还会对仓壁产生很大压力,可能会造成仓壁破坏;3.破拱原理:消除或者削弱料拱垂直截面的压力,减少物料之间、物料与仓壁之间的摩擦力上4.具体方法:a.增大斗仓卸料口尺寸,尽可能采用条形卸料口;b.增大斗仓壁倾角,是斗仓壁尽可能陡峭而光滑;c.采用非对称斗仓或者偏心卸料口;d.改善仓壁材料或者壁涂刷环氧树脂等光滑材料,以增强粉体流动性;e.减小仓体高度,采用浅仓以降低粉体压力;f.配料仓嵌入改流体改善物料流动性;g.安装振动、气力或者螺旋搅拌等强制性破拱设施。
五、料仓要求及物料流动料仓设计时应满足以下三方面的要求:⑴能储存规定数量的仓料;⑵有足够的强度来承受料仓物料所产生的压力以及外届自然环境可能施加在料仓上的力;⑶在从料仓卸料时,物料能够顺畅而均衡地从料仓出口流出,且出料速度均匀可控。
物料在料仓中的流动性,是料仓性能的一个重要指标。
据目前归类总结,我们可以把料仓物体的流动形式主要分为两种:整体流动和中心流动。
(一)整体流动所谓的整体流动就是指:卸料时所有物料均向卸料口流动,不存在“死区”,料位均匀下降,卸料流动稳定均匀。
理想的料流形态应为整体流动,这样保证了物料以先进先出的顺序均匀卸出,而且具有卸料速率稳定,卸料密度均匀,仓料储存时间基本一致等优点。
(二)中心流动中心流动即卸料开始时,只有位于库顶的物料处于运动状态,位于四周的物料向中心滑动、下降,形成中心通道,只有中心部位的物料向卸料口流动,在该“流动区”以外的部分为流动“死区”。
1.中心流动主要特点:①先进后出的流动顺序。
因为仓壁附近的物料可能静止不流动,所以先进仓的物料有可能后出来。
②产生鼠洞。
由于出现漏斗流,如果物料有足够的黏性,仓壁附近的物料就不会流出。
③不均衡流动。
漏斗流料仓中,四周的物料是靠超过物体本身的休止角而塌落下来的,所以卸料时是不均衡的,此外塌落料的冲击力会进一步压实料仓出料口的物料并使之结拱。