位置度超差五原则表
位置度超差五原则表

W2011021602
编 号:
标题 零件图号 发起人 签发日期
前轮辋装不上制动盘
54111H05712 谭晓武
零件名称 审批人
前轮辋 潘小平
2011-02-17
请于2011-03-14前返回
五原则表
责任单位
金华今飞
年月日
制作
确认
徐申
批准
确认/日期 批准/日期 接受 报告
得分
发生状况(发生件数、发生现象、处置情况等)
一
不良品的确认结果
1.现象说明:位置度超差是导致碟刹盘无法装配的直接原因。
2.不良品与正常品的外观差异:
不良品
不良品
正常品
正常品:四个螺纹孔中心距尺寸无偏差; 不良品:四个螺纹孔中心距尺寸明显存在偏差。 3.与作业指导书的对比:
产品 序号
类型 模具号
生产日期
合格证 日期
1
尺寸33mm
2
3
4
示意图
1
L
2
1
5
L
2010.12.30 1.3 31.92 33.12 34.04 32.94
6 7
不良品
L L
8
L
9
L
2010.12.30 2010.12.30 2010.12.30 2010.12.30
1.3 1.3 1.3 1.3
31.96 31.72 32.02 32.02
33.12 33.22 33.3 33.2
内 发生 容 流出
1
位置度超差 位置度超差
2
刀具中心与工装中心不同心 检验员没有检查
三 、
序号
问题点
标准
让你更容易理解的位置度公差
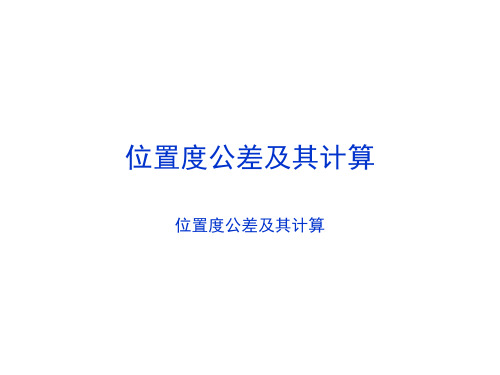
③复合位置度公差注 法:图6-13。
• 四个孔的实际轴线应同时位 于孔组位置度公差带和各孔 位置度公差带内,即四个孔 的实际轴线应位于两个公差 带的重叠部分,但各孔位置 度公差带中心不必位于孔组 位置度公差带内,则满足设 计要求。
三、位置度公差的计算
• 1. 孔组内各孔位置度公差的计算 • 孔组内各孔的位置度公差带计算公式由紧固件与被连接零 件的连接方式决定。 • 通孔连接方式:用螺栓、销钉等紧固件穿过两个或几个被 连接零件上的通孔; • 螺孔连接方式:把双头螺柱、螺钉等紧固件拧入一个被连 接零件的螺孔中,且穿过其余的被连接零件上的通孔。 • (1)通孔连接方式的位置度公差计算(图6-14) t=DM-dM=Xmin • 上式中,紧固件采用包容要求
二、位置度公差的标注
孔组的两种设计要求 • (1)第一种设计要求。装配时不仅要求被连接的两个零件上对应孔组内各孔的位
置分别对准,是孔组内部的孔的位置要对准,而且要求这两个零件上的某些其他要素 也应分别对准。(对孔组的位置和各孔的位置变动量都应规定较严格的位置度公差。) • • 换句话说就是既要保证孔组的位置度公差还要保证各孔的位置度公差,孔组的位置度 公差可以保证零件的边是不是对齐的。 (2)第二种设计要求。装配时仅要求被连接的两个零件上对应孔组内各孔的位置分别 对准,而不要求这两个零件上的某些其他要素也分别对准。(对各孔的位置变动量应 规定较严格的位置度公差,而对孔组位置度公差或定位尺寸公差则应规定的较松。) 孔组位置度公差与各孔位置度公差的关系是孔组的位置度公差一定要大于或等于各个 孔的位置度公差。
孔组位置度公差
பைடு நூலகம்
各孔位置度公差
二、位置度公差的标注
• ②位置度公差与定位尺寸公差组合注法:图6-4和6-8。
(优选)位置度影响因素及调整步骤注意事项
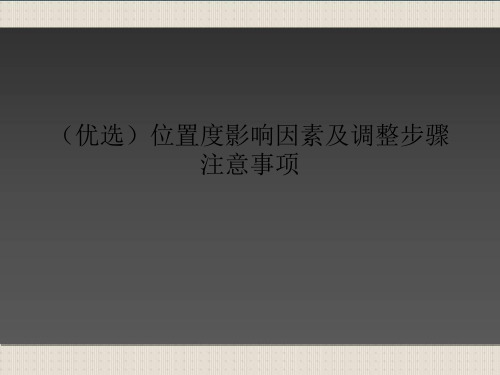
位置度定义
如下图, φ3孔的位置度要求
位置度
• 位置度是关联实际要素对基准在位置上允 许的变动全量.包括点的位置度公差,线的位 置度公差,和平面或中心平面的位置度公差.
• 对于我们公司来说,位置度的要求大多是 对于孔,所以我们这篇文章的重点也在于 孔和外圆,我们的以下内容都是基于对于 孔来讲述的。
始与此 6、液压气动系统---夹具的动力源 7、冷却系统---刀具的保护神
影响位置度的因素
• 那现在我们就可以来说位置度的影响因素了。简 单的说,设备的各组成部分都会对位置度有一定 的影响,只不过是重不重要的问题,但值得注意 的是,有的时候看似次要的部位有可能反而是问 题的关键。
• 位置度的影响因素有:(排名分前后☺) 1、夹具2、主轴箱3、导向机构4、液压气动系统5、 刀辅具6、冷却系统7、床身8、其它
二、夹具夹紧后检查各夹紧点是否与工件压紧,若 没有压紧就需要检查夹紧机构有无问题;
三、夹具夹紧后检查各定位块、辅助支撑与工件是 否贴死,这样可以针对具体的情况得出响应的判 断;
四、在以上都 没有问题的情况下开始试切工件,但 需在此状态下感受工件是否有移动或者震动;
夹具对位置度的影响
五、若发生了第四项的情况,则需要对系统 的夹紧力来进行检查;
(优选)位置度影响因素及调整步骤 注意事项
加工零件位置度超差调整前的检查步 骤及注意事项,位置度变化影响因素
编稿:李军
位置度定义
• 位置公差(俗称位置度)——位置度公差是指各实 际要素相互之间或它们相对一个或多个基准位置 所允许的变动全量,也就是加工后实际存在的位置 相对设计上规定的理想位置所允许偏离的极限范 围。换成我们的话讲,就是目标(孔、外圆等)相 对于某一规定基点或者面的实测坐标值与要求坐 标值间的误差,这个误差在要求范围内既位置度 合格,超过范围既位置度超差,这时就需要调整 位置度了。
位置度影响因素及调整步骤、注意事项
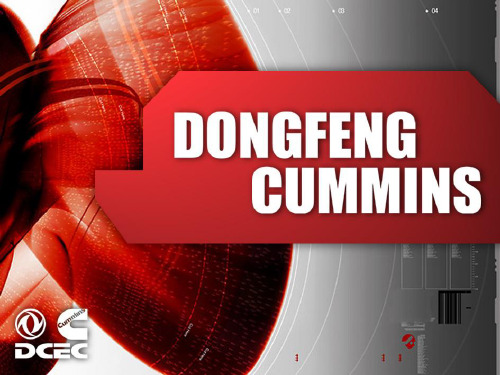
刀辅具对于位置度的影响
• 这是一个比较常见的问题,刀具的磨损程 度直接决定了加工质量的一切参数,包括 对位置度产生影响,比如刀具直径磨损就 会导致钻套起不到很好的导向作用而导致 位置度不稳定;刀具切削刃磨损就会导致 刀具跳动加工孔变大位置度不稳定等。
冷却系统对位置度的影响
在高速主轴设备中就会突出的表现冷却液的 作用,冷却液的流量和压力不够就会导致 刀具过热,被加工孔变大或者椭圆,这样 位置度当然就会变差。这个时候就相应的 对于冷却系统进行检查和修理,确保冷却液 的流量.
钻模板对位置度的影响
钻模板对位置度的影响
主轴箱对位置度的影响
• 在主轴箱出现异常的情况下,也会造成位 置度不稳定的情况出现,所以也相应需要 对主轴箱来做针对性检查。 1、检查主轴箱内部有无异响,有无震动,可 判断主轴箱传动机构是否有问题,震动较 大则会造成孔干大或位置度波动。
主轴箱对位置度的影响
加工零件位置度超差调整前的检查步 骤及注意事项,位置度变化影响因素
编稿:李军
位置度定义
• 位置公差(俗称位置度)——位置度公差是指各实 际要素相互之间或它们相对一个或多个基准位置 所允许的变动全量,也就是加工后实际存在的位置 相对设计上规定的理想位置所允许偏离的极限范 围。换成我们的话讲,就是目标(孔、外圆等)相 对于某一规定基点或者面的实测坐标值与要求坐 标值间的误差,这个误差在要求范围内既位置度 合格,超过范围既位置度超差,这时就需要调整 位置度了。
钻模板对位置度的影响
三、对于活动钻模板要检查模板是否贴死定 位面,模板定位销、定位块是否磨损,定 位销是否松动等异常;这里检查可以通过 气检压力读数、用塞尺等办法,夹具定位 面检查类似。
钻模板对位置度的影响
检测位置度误差

线的圆柱面内,图b所示。
位置度误差的检测
(1)准备的检具 坐标测量装置、心轴。 (2)检测步骤 如图所示。
步骤l:按基准调整被测零件,使其与测量装置的
坐标方向一致。 步骤2:将心轴放置在孔中,在靠近被测零件的板
面处,测量x1,x2,y1,y2。
步骤3:按下式分别计算出坐标尺寸x,y: x=(x1+x2)/2;y=(y1+y2)/2 步骤4:将x,y分别与相应的理论正确尺寸比较,得出fx和fy 步骤5:然后把被测件翻转,对其背面按上述方法重复测量,取其中的误 差较大值,作为该零件的位置度误差。 (3)评定检测结果 如果测得的最大误差值≤0.1 nlnl,该零件的位置度 符合要求;如果测得的最大误差值>0.1mm
检测位置度误差
☞ 知识点
(1)位置度公差;
(2)位置度公差的检测。
位置度公差
定位公差是关联实际要素对基准在位置上允许的变动量。 根据被测要素和基准要素之间的功能关系,定位公差分为位置度、同 轴度和对称度3个项目;
位置度公差
(1)位置度公差的标注和公差带 如图所示。
位置度公差
(2)识读位置度的标注 图a所示被测孔φ28mm轴线相对于基准面A, 基准面B和基准面C组成的基面体系的位置度公差为φ0.1 mm。 (3)解释位置度公差带的含义 被测轴线必须位于直径为公差值0.1 mm,且以相对于A,B,C基准表面(基准平面)所确定的理想位置为轴
利用Excel制作各类品质图表
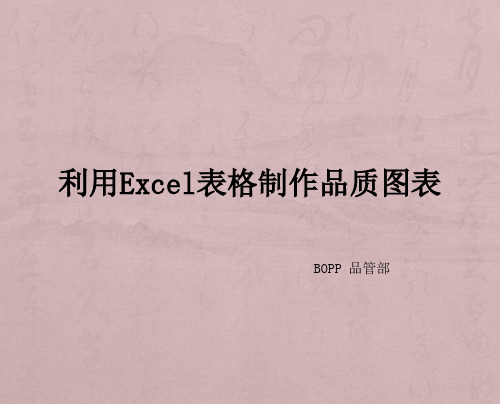
所涉及的函数:
1. 逻辑函数:
AND
执行真假值判断,根据逻辑计算的真假值,返回不同结果。可以使 用函数 IF 对数值和公式进行条件检测。
OR
在其参数组中,任何一个参数逻辑值为 TRUE,即返回 TRUE;任
何一个参数的逻辑值为 FALSE,即返回 FALSE。
步骤1: 计算人与人交叉(A*B,B*C,A*C)
步骤1:计算数据中的最大最小值 步骤2:计算全距(最大值-最小值) 步骤3:计算组数K
温馨提示:右图为组数的参考值 步骤4:计算组距(全距/组数K )
數據數 50~100 100~250 250以上
組數 6~10 7~12 10~20
步骤5:计算上下组列
用CONCATENATE函数合并上下界 数值文本,计算如下:
了解制程变异手法特点与作用会在?spc与excel的结合运用?部分细说柏拉图与excel的结合运用09第四季度散热片不良状况5032184310706986219138948396551000020406080100螺纹不良位置度超差导通不良表面赃物来错物料变形其它不良类别0102030405060708090100不良数量累积不良率首先让我们来看以下一个关于某款产品进行季度的质量分析
CONCATENATE
计算区域中满足给定条件的单元格的个数。 返回一组值中的最大值。 返回一组值中的最小值。 将几个文本字符串合并为一个文本字符串。
2. 数学与三角函数:
LOG 3.文本函数:
FIXED
按所指定的底数,返回一个数的对数。
将数字按指定的小数位数进行取整,利用句号和逗号,以小 数格式对该数进行格式设置,并以文本形式返回结果。
品质七大手法与EXCEL的结合运用
位置度
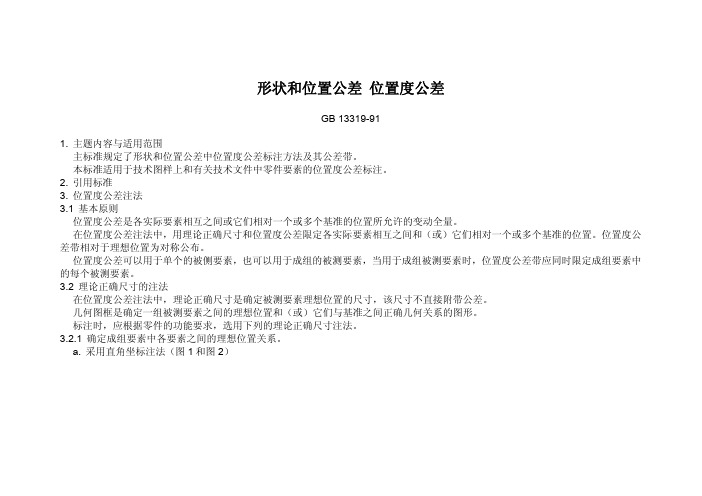
形状和位置公差位置度公差GB 13319-911. 主题内容与适用范围主标准规定了形状和位置公差中位置度公差标注方法及其公差带。
本标准适用于技术图样上和有关技术文件中零件要素的位置度公差标注。
2. 引用标准3. 位置度公差注法3.1 基本原则位置度公差是各实际要素相互之间或它们相对一个或多个基准的位置所允许的变动全量。
在位置度公差注法中,用理论正确尺寸和位置度公差限定各实际要素相互之间和(或)它们相对一个或多个基准的位置。
位置度公差带相对于理想位置为对称公布。
位置度公差可以用于单个的被侧要素,也可以用于成组的被测要素,当用于成组被测要素时,位置度公差带应同时限定成组要素中的每个被测要素。
3.2 理论正确尺寸的注法在位置度公差注法中,理论正确尺寸是确定被测要素理想位置的尺寸,该尺寸不直接附带公差。
几何图框是确定一组被测要素之间的理想位置和(或)它们与基准之间正确几何关系的图形。
标注时,应根据零件的功能要求,选用下列的理论正确尺寸注法。
3.2.1 确定成组要素中各要素之间的理想位置关系。
a. 采用直角坐标注法(图1和图2)b. 采用极坐标注法(图3和图4)若成组要素中的各要素在圆周上均匀分布时,各要素间的理论正确角度允许省略不注,在公差框格上方加注“均布”两字(图4)。
此时,各要素间的角向位置关系为圆周理想等分的角度关系。
c. 采用混合法(图5)。
d. 采用表格注法(图6)。
图1至图6中各理论正确尺寸仅确定成组要素组内各要素(孔的轴线)相互间的理想位置关系,在图中分别用相应的几何图框表示。
3.2.2 确定各要素之间及相对基准的理想位置关系a. 采用直角坐标法(图7至图9)图7中基准线A作为确定各条被测线理想位置的尺寸起始线。
图8中基准平面A、B构成的互相垂直的基准体系作为确定各孔理想位置的坐标尺寸起始面。
有对中心基准要求的要素,其理论正确尺寸应从基准中心平面注起(图9)。
图9中基准中心平面A确定了孔组的定位和定向要求。
位置公差与误差

四、 跳动公差
跳动公差为关联实际被测要素绕基准轴线回转一周 或连续回转时所允许的最大变动量。可用来综合控制被 测要素的形状误差和位置误差。
跳动公差是针对特定的测量方式而规定的公差项目。 跳动误差就是指示表指针在给定方向上指示的最大与最 小读数之差。
liuq1217@
二、 定向公差
2.垂直度公差 1)一个方向
d
0.1 A 基准平面
A
liuq1217@
2)任意方向
d
0.05 A
A
liuq1217@
d 基准平面
二、 定向公差
3.倾斜度公差 倾斜度公差用来控制面对线、线对线、面对面和线对
面的倾斜度误差,只是将理论正确角度从0°或90°变为 0°~90°的任意角。
1)径向圆跳动和圆度的公差带都为半径差为公差 值 t的两个同心圆之间的区域,即公差带形状相 同。
2)径向圆跳动:两个同心圆的圆心与基准同轴 (圆心固定)。 圆度:两个同心圆的圆心随着被测实际圆的位 置而变动(圆心浮动)。
3)径向圆跳动:位置公差项目,关联要素(有基 准)。 圆度:形状公差项目,单一要素(无基准)。
图样标注时应将角度值用理论正确角度标出。
liuq1217@
二、 定向公差
0.06 B
α
60°
t
B
基准线
liuq1217@
二、 定向公差
定向公差带特点: 1. 定向公差用来控制被测要素相对于基准保持一定的 方向(夹角为0°、90°或任意理论正确角度)。
2.定向公差带具有综合控制定向误差和形状误差的能力。 因此,在保证功能要求的前提下,对同一被测要素给出 定向公差后,不需再给出形状公差,除非对它的形状精 度提出进一步要求。
- 1、下载文档前请自行甄别文档内容的完整性,平台不提供额外的编辑、内容补充、找答案等附加服务。
- 2、"仅部分预览"的文档,不可在线预览部分如存在完整性等问题,可反馈申请退款(可完整预览的文档不适用该条件!)。
- 3、如文档侵犯您的权益,请联系客服反馈,我们会尽快为您处理(人工客服工作时间:9:00-18:30)。
大长江纳 入时间
纳入数量
2010.12.28 240只 2010.12.31 120只 2011.1.8 170只 2011.1.10 160只
2011.1.12 190只 2011.1.14 170只
2011.1.16 180只 2011.1.16 60只
54111H05712 10.12.24 134只
1.车(机)型:
2133
型号
q72
2.发生时间: 2011-02-16 3.发生地点: 过程
4.发生数量: 12
5.不良比例:
6.批 次 号: H10200044 7.到货时间: 2011-01-29
8. 发 前轮辋4-M8-7H螺纹孔位置度超差要求ф0.15,实测不良件均 不过检具,三坐标检测1只数据为1.540,装不上制动盘。 9.处置情况:1、生产现场跟线挑选;2、库存退回厂家挑选
攻丝所有工序由原来的涂装车间加工完成改为机加车间
完成,在没交接完毕情况下,机加车间安排了1个气试
人员进行上机操作,其余没变化 。
3.生产过程同类问题发生情况调查:
通过调查,发现以往无类似情况发 生。
● ● ● ● ● ●
车削加工
☆发生工序 螺纹孔加工
巡检
☆流出工序
前处理
● ● ● ● ● ●
发送
要因
五、横向展开、反馈到源头(系统、体制等)
1.分批对机加工以及检验员就整车装配和异常处理进行培训
。
责任人:陈巧华/朱海贵
完成时间:11.02.26
2.分批对机加操作工就所有工序的工艺工装标准进行培训。
责任人:徐旭阳
完成时间:11.02.28
3.对车间管理人员的执行力进行培训。
责任人:朱丹华
完成时间:11.02.28
2010.12.30 1.3
32 32.7 34.18 33.26
2
L
2010.12.30 1.3 32.02 33.1 34.04 33.4
3 4
L
2010.12.30 1.3 32.02 32.82 33.08 33.1
L
2010.12.30 1.3 31.76 32.97 34.28 32.8
10.12.27 50只 10.12.28 84只
库存:12只
11.01.05 164只
2011.1.7 164只 库存:133只
2011.1.26 110只
54111H05712 10.12.27 60只
10.12.31 60只 库存:20只
11.01.06 52只
库存:23只 2011.1.8 52只
4.编制《巡检记录表》,检验员在巡检过程中及时记录检查
结果,并对检验员进行培训。
责任人:朱海贵
完成时间:11.02.20
A2版
2
1
5
L
2010.12.30 1.3 31.92 33.12 34.04 32.94
6 7
不良品
L L
8
L
9
L
2010.12.30 2010.12.30 2010.12.30 2010.12.30
1.3 1.3 1.3 1.3
31.96 31.72 32.02 32.02
33.12 33.22 33.3 33.2
一
不良品的确认结果
1.现象说明:位置度超差是导致碟刹盘无法装配的直接原因。
2.不良品与正常品的外观差异:
不良品
不良品
正常品
正常品:四个螺纹孔中心距尺寸无偏差; 不良品:四个螺纹孔中心距尺寸明显存在偏差。 3.与作业指导书的对比:
产品 序号
类型 模具号
生产日期
合格证 日期
1
尺寸33mm
2
3
4
示意图
1
L
○
业指导书 判定方法
涂装车间与机
新员工在上岗 加车间在没交
前需要经过培 接完毕情况
员工技能不足 训和考核,合 下,机加车间
×
格后才能上岗 安排了1个气
操作 试人员进行上
机操作。
检验员没有巡 要求检验员进 当班检验员没
检
行巡检 有进行巡检
×
○:排除在要因外 ×:致命要因
要因分析概括: 1.操作工属于无证上岗。 2.当班检验员没有进行巡检。
规定
事实
判定
抽查库存,轮
轮辋跳动不良
轮辋跳动≤ 0.5
辋跳动 进行测算,
○
Cpk=1.55
机床精度不良 Cpk≥1.33 Cpk=1.38
○
四个方向的等 等高块尺寸一
工装不良 高块尺寸相等
样
○
定芯跳动≤ 定芯跳动为
0.02mm
0.02mm
○
要求各道工序 该工序有明确
工艺文件无 都有完善的作 的检验标准及
2011.02.16 2.20
33 33.14 33.04 33.06
5
L
2011.02.16 2.20 33.08 33.02 33
33
平均
33.04 33.06 33.04 33.01
判定
OK
4.确认结果的总结: 4个螺纹孔中心距圆心往第3个螺纹孔方向偏移了1mm,造成位置 度超差,直接导致碟刹盘无法装配。
置架,便于和正常品区分 品全部归放到不良品放置
架上 1.建立 《异常品处理流
5
没有异常品处理规定
/
程》 2.对现场检验员以及操作
工进行培训与考核
1.制作首末检产品放置
6
现场无首末检产品放置架
/
架,并放在该道工序的现
场
调机完成后检验员进行首
7
检验员没有进行首检
调机完成后检验员进行首检 检,首检合格的产品放到
2011.1.29 240只
11.01.08 72只
2011.1.11 72只
54111H05712 10.12.30 274只
11.01.02 130只 11.01.03 144只
11.01.10 36只
2011.1.12 36只 2011.1.13 108只
库存:222
11.01.11 108只
2.变化点调查: 54111H05712 11.01.04 205只 54111H05712 11.01.06 150只
11.01.08 105只 11.01.09 100只 11.01.10 96只
库存:703只
针对上述不良批次从11人.01库.1存1:145只4只、机、料、法、环、测量进行变
化点调查,发现人员状况有变化,2010年12月份我司将
11.02.19
11.02.19 11.02.27
已完成 11.02.27
已完成 11.02.20 11.03.10
3
4
5
调机时未对中心用杠杆百分表进 行校正
员工上岗未经过培训
管理人员没有按制度执行
/
检验员没有按照制度执行
/
/
/
四、检查对策效果(量化的实际效果)
1.今飞外租库库存品1100只进行全检,有13只不良品。 2.今飞库存品1290只进行全检,未发现类似不良产品。 3.对策实施后对该产品的位置度进行CPK测试,测试结果 为:1.3595>1.33 OK
库存:12只 10.12.22 22只 10.12.23 38只 10.12.25 86只
库存:42只
发货时间 发货数量 10.12.30 380只 11.01.03 116只
今飞外租 库接收时
间
今飞外租 库数量
截止12月25日外租 库库存量为763只
库存:73只
2011.1.1 380只
库存:93只 2011.1.5 116只
问题点
1.新员工上岗 不具备调机能 力,造成调机 不良 2.新员工不了 解该道工序的 送检频次 检验员没有巡 检造成不良品 流出
二 、
再现试验:
发生机理: 新员工调机
刀具中心与
四个螺纹孔
发生原因:
1.刀具和工装定芯没有同心。
流出原因: 1.操作工没有自检和送检。 2.调机后检验员未进行巡检。
分析为什么、为什么 阶段
装的中心不同心。
操作
3.该道工序的操作工实行
每月考核一次,合格后上
岗
3
操作工不了解该尺寸的重要性 操作工掌握本道工序的作业 对操作工在工艺方面的知
没有自检和送检
指导书上的全部内容
识进行系统的培训
在攻丝工序机床旁边划分 各道工序现场都应该划分一 不良品放置区和不良品放
4
现场无异常品放置区域
个不良品放置区和不良品放 置架,生产过程中的不良
库存:78
54111H05712 11.01.01 203只
11.01.04 90只
库存:51只
11.01.05 113只
2011.2.14 180只
54111H05712 11.01.02 210只
11.01.06 100只
11.01.07 110只
11.01.17 832只
2011.1.19 832只
大长江编 号:
W2011021602
编 号:
标题 零件图号 发起人 签发日期
前轮辋装不上制动盘
54111H05712 谭晓武
零件名称 审批人
前轮辋 潘小平
2011-02-17
请于2011-03-14前返回
五原则表
责任单位
金华今飞
年月日
制作
确认
徐申
批准
确认/日期 批准/日期 接受 报告
得分
发生状况(发生件数、发生现象、处置情况等)