原因分析五原则表格(根本原因版)
5原则表
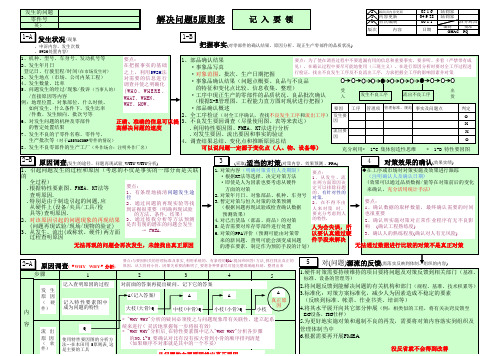
发生状况(现象、申诉内容、发生次数、5W2H处置内容)(使用反面)1、机种、型号、车身号、发动机号等2、发生年月日登记日、行驶里程/时间(在市场发生时)3、发生地点(市场、公司内某工程)4、发生数量、比率5、问题发生的经过/现象/投诉(当事人的)/直接原因等内容例:地理位置、对象部位、什么时候、如何发生、什么条件下、发生比率/件数、发生倾向、批次号等6、对发生问题的机种及零部件的暂定处置结果7、发生不良的子零件名称、零件号、生产批次等(对于ASSY&COMP 零件的情况)8、发生不良零部件的生产工厂(外作场合:注明外作厂名)内容记入要领要点:在把握事实的基础之上,利用5W2H 法对需要的信息进行调查并使之明确化(WHO 、WHERE 、WHAT 、WHEN 、WHY 、HOW 、1、部品确认结果·事象品写真·对象范围、批次、生产日期把握·事象品确认结果(问题点概要、良品与不良品的特征和变化点比较、信息收集、整理)·工序中现正生产的零部件的品质状况、良品批次确认(根据X-R 管理图、工程能力直方图对现状进行把握)·部品确认概述2、全工序检证(对全工序确认,查找不良发生工序和流出工序)3、不良发生要因调查(尽量使用图、表等来表达).利用特性要因图、FMEA 、KT 法进行分析.对发生要因、流出要因和事实的验证4、调查结果总结、变化点和推断原因总结使用特性要因图的分析方法…在本田用5原则表,这是主要的工具充分利用*1-C 集体创造性思维*1-D 特性要因图1-B12345记入查明原因的过程记入特性要素图中成为问题的特性发生原因(硬件)流出原因(软件)对前面的答案再提出疑问、记下它的答案A(记入答案)AA A 大枝(大骨)Q Q中枝(中骨)Q小枝小枝(小骨)Q真正原1、引起问题发生的过程和原因(考虑的不仅是事实的一部分而是关联的全过程).根据特性要素图、FMEA 、KT 法等查明原因..特别是由于制造引起的问题,应从硬件上(设备/夹具/工具/检具等)查明原因.2、对该原因引起的问题现象的再现结果(问题再现试验/现场/现物的验证)3、从发生、流出(或称软、硬件)两方面过程查明原因2-B 1-A 2-A原因,从大骨到小骨,因果关系要清晰明了,要将各种要素尽可能完整准确地归纳、整理出来34要点:为了使在调查过程中不要遗漏有用的信息和重要事实,要多听、多看(严禁带有成见),在确认过程中要尽可能地使用(三现主义)。
5why分析法表单

实施整改措施,
防止问题再次发生
跟踪并审查结果
¾⅛Q因所住端
Ip#为什么?】第空除因翳为什么?2
:^W
M∖么?3
原崛
为什么?4
朦因
为什么?
J
根本原因
J
整改措籁J
褥到的经验教训
识别/确认直接原因
问“5个为什么〃,以找出与问题相关的
Y
'J具体的根本原因
问“5个为什么〃,弄清为什么
问题没有被发现,问题到了客户那里
问“5个为什么〃,弄清为什么
“系统〃出了问题
5个为什么工具分析表
参考编号:
日期:
客户:
零件号/零件名:
公司名称
问题描述:
改正措施
E其?$37
为什么?
使用该路径分为什么该特定问题会发生?
根本原因
A
.k
为什么?
为什么?
使用该路径分析为什么该问题没有被检测到?
为什么
A
B
一
为什么?
为什么?
为什么?
使用该路径分析为什么管理体系会允许该问题发生?
为什么?
根本原因
整改推MI$
得到的经验教训
摸清目前状况
活动(步骤)
他们知道了什么?
他们做了什么?
识别出问题
厂
验明问题
分解问题
定出原因点
(图象定位)
摸清问题的倾向
(你问了哪些问题?)
原因调查
活动(步出来的问题
(大的,柳胃的,翅杂的)7
验明的MS8
M;.,Jj∙⅝fJ,AJJJJ⅛WσΓuTH<
B
为什么?
安全事故五原则模板

安全事故五原则模板
安全事故五原则模板是一种常用于分析安全事故的方法,包括以下五个原则:
1. 事故根源原则:分析事故的根本原因,找出引发事故的基本原因,这是分析事故的关键步骤。
常见的基本原因包括人为因素、设备故障、环境因素等。
通过找出根本原因,可以采取相应的
措施来防止类似的事故再次发生。
2. 多重原因原则:事故往往是由多个原因共同作用导致的,不能简单地归咎于单一原因。
分析
事故时,需要考虑各种因素,包括人的不安全行为、设备问题、管理漏洞等。
对于每个原因都
要进行仔细的分析,以便了解它们是如何相互作用的。
3. 预防为主原则:事故分析的目的之一是为了预防类似事故的再次发生。
因此,在分析事故时,需要关注事故预防措施的有效性。
要针对发现的问题制定相关的预防措施,并确保这些措施能
够防范类似事故的发生。
4. 透明原则:分析事故时要保持透明度,及时和相关人员共享发现的信息和结论。
这对于组织
内部的学习和改进非常重要,也有助于其他类似行业的组织从中吸取教训。
5. 持续改进原则:安全事故分析应该是一个持续的过程,组织应该不断总结经验教训,改进和
优化安全管理体系。
只有这样,才能够有效地减少安全事故的发生,提高组织的整体安全水平。
以上是安全事故五原则模板的基本内容,根据具体情况可以进行适当调整和扩充。
这一模板有
助于组织对安全事故进行科学分析,以促进安全问题的解决和预防。
五WHY分析法

02 5WHY的实施步骤
正确案例分析
正确案例分析
02 5WHY的实施步骤
案例1-杰弗逊纪念馆
杰弗逊纪念馆墙面破 损情况很严重
why
经常用化学性质很强烈 的清洗液对其进行清洗
why why
为了清除大量的鸟粪
被黄昏的灯光所吸引 why
3-why 为什么不知道手册规定?
依据上一年的报告为模板来写的
4-why 为什么模板与手册不符? 模板中没有手册依据和控制项
5-why 为什么没有手册依据和控制项?
模板的管理没有相应的规范
04 5WHY演示
步骤3、制定对策
短期措施: 修订2014年福州机务部安全质量分析“事件汇报材料,增加手册中的相关 要求内容。 长期措施: 制定模板管理规范,包括在模板中必须有填写手册依据及符合性的页面。
系统为什么 没防住?
为什么?
教训:
根源
为什么? 为什么? 为什么?
为什么? 为什么? 为什么?
为什么? 为什么? 为什么?
纠正措施
日期
A
A
B
B
CC
02 5WHY的实施步骤
第2步的要点
怎么问问题很重要! 原则:导向可控的解决方案
02 5WHY的实施步骤
错误案例分析
02 5WHY的实施步骤
案例:由一个人摔跤引出的故事
五WHY分析法
目录
: contents sub title : contents sub title
01 / 5WHY简介 02 / 实施步骤 03 / 5WHY练习 04 / 5WHY演示 05 / 5WHY注意事项
五原则表(pdf 3页)

原本保存期限:
年
月
பைடு நூலகம்
~2. 问题件、制造年月日
… 等、按工艺顺序和时间顺序整理。
~3. 问题件、发生个数、发生率
4. 预测发生件数及批次。
5. 确认重点。
~1. 与没出现问题的比较其特征及变化。
~2. 确认出现不良的日期和时间。
6. 工艺调查结果的归纳方法 … 按工艺流程和时间系列以变化为主填写。
7. 变化点和推断原因。
【目的】
1. 下次行动时锁定目标。 2. 真实填写发生的原因和状况,以便使不良零部件、部位更清晰
【填写内容】
1. 机种、机型等
2. 车身号码、发动机号码、批号等。
3. 发身地点。
4. 发生年月日。
5. (发生后在销售店)登记年月日。
6. 行使路程/时间。
7. 发生内容/原因
~1. 地理位置。
~2. 对象件的何部位。
~3. 何时。
~4. 发生方式。
~5. 什么条件下。
~6. 发生比例。
~7. 发生倾向。
8. 该车、该机的处置方法和程序。
9. 出货件的确认结果。
掌握事实 (零件确认结果・主要原因分析・产品质量状况)
【目的】
1. 事情发生的情况(最初原因)和再现试验 … 决定不良零件、部位。
2. 明确零件、部位的不良原因。
- 无法再现的问题会再次发生 -
【目标】
1.证明品质、成本、日程都是最合适的, 以防止出现的情况再次发生。
【填写内容】
1.引起问题零件/部位的硬件(设备、夹工具等)的临时对策、不能消 除真正原因时的适当对策、针对真正原因的纠正对策日程和责任人。
2.防止问题零件/部位流出的硬件(QA机、防出错装置等)的临时对策、 不能消除真正原因时的对策、消除真正原因的纠正对策推进日程和 责任人。
品质知识五个为什么分析培训(ppt 24页)

为什么顾客需要解决供应商问题?
– 因为供应商偶尔出现的质量问题会影响顾客对生意的运作并且也会影响终端顾客的 满意度
为什么供应商会偶尔出现质量问题?
2020/12/14
6
问题的解决 5个为什么的优点
满足顾客的需求
– 对已确定的问题根源做清晰的沟通 – 对缺乏的能力作出说明以便发现问题 – 重视潜在的系统性问题
2020/12/14
15
新的需求 DE WI 914.01.01
请参考实
定义问题 为什么?
对正在被调查的特 殊的不和谐性使用
这条路径
参考号 ____________
(Spill, PR/R…) 日期: ____________
为什么?
使用这条路径来调 查为什么问题没有
为什么中心被引爆? 绝缘被烧坏
为什么绝缘被烧坏?
在前导系统测试过程中氧气舱过热
为什么氧气舱过热? 氧气舱中的加热器通常会维持舱内的 压力,但在舱内被清空后(也就是测
试结束后)没有被关掉
为什么加热器没有被关掉?
2020/12/14
5个为什么分析 阿波罗13氧气舱爆炸
为什么加热器没有被关掉? 切断电源的开关可以在舱过热时自动
– 为什么问题会发生?(各部分) – 为什么问题会触及到顾客?(保护顾客) – 为什么“体系”会失败?(过程)
2020/12/14
5
为什么要学习和使用5个为什么分析?
为什么要学习和使用5个为什么分析?
– 程序DE914.01(纠正和预防措施程序)已被更新并且会详细解释5个为什么分析的 用法?
– 中国最大的资料库下载
想法、原因、纠正措施或教训在避免的过程中有没有大的漏洞呢? 有没有由顾客来承担而不是供应商去承担的更多的纠正措施呢? 分析会说明整个事件吗?
5why分析法模板
5why分析法模板5why分析法是一种系统性的问题分析方法,通过反复追问“为什么”,找出问题的根本原因,从而解决问题。
这种方法被广泛应用于质量管理、生产管理、故障分析等领域。
下面将为大家介绍一份5why分析法的模板,希望对大家在实际工作中有所帮助。
1. 问题描述。
首先,需要明确问题的描述,这是进行5why分析的前提。
问题描述应该尽量客观、清晰,避免主观臆断。
比如,产品出现了质量问题,或者生产线频繁停机等。
2. 第一问,为什么会出现这个问题?在这一步,需要深入分析问题的表面原因。
可能是因为设备故障、操作不当、材料质量问题等。
需要对问题进行细致的分解,找出可能的原因。
3. 第二问,为什么会出现这个原因?接下来,需要进一步追问为什么会出现这个原因。
可能是因为设备没有进行定期维护、操作人员没有接受专业培训、供应商提供的材料质量不稳定等。
需要找出导致这个原因的更深层次的原因。
4. 第三问,为什么会出现这个更深层次的原因?继续深入追问,找出更深层次的原因。
可能是因为管理不到位、人员流动频繁、市场需求变化等。
需要找出根本原因,而不是停留在表面现象上。
5. 第四问,为什么会出现这个根本原因?再次追问,找出根本原因背后的原因。
可能是因为企业文化问题、管理体系不完善、技术水平不够等。
需要找出问题的根源所在。
6. 第五问,为什么会出现这个根源所在?最后一步,继续深入追问,找出问题的根本所在。
可能是因为企业发展战略不清晰、组织架构不合理、人才储备不足等。
这是问题的最根本的原因。
通过5why分析法,我们可以清晰地找出问题的根本原因,而不是仅仅停留在表面现象上。
这种方法可以帮助我们在解决问题时,不断追问,直至找到问题的根源所在,从而有针对性地解决问题。
当然,在实际应用中,可能会遇到多个原因交织在一起的情况,这时候需要综合考虑,找出主要原因。
同时,还需要注意在追问过程中,避免陷入主观臆断的误区,要以客观事实为依据。
总之,5why分析法是一个简单而又实用的问题分析方法,可以帮助我们更深入地了解问题,并找出解决问题的方法。
5Why分析表(案例)
XX电子有限公司5Why分析表(案例)产品名称A型针车型问题描述针变形分析日期2018.3.9 不良数量55000PCS/180PCS/4PCS 不良率 2.2000% 发生场所进料检验生产批号2018.3.2a.过程工艺、检验、零部件状况追踪检查说明1、是否遵循SOP的工艺条件、作业流程?☐是□否 4、是否使用了经验证合格的零件?☐是□否2、是否使用正确的设备(含条件)及工具?☐是□否 5、技术规范是否符合、验证且培训?☐是□否3、人员是否培训并鉴定?□是☐否6、生产期间的环境状况是否有区别?□是☐否7、运输包装是否符合标准书要求?☐是□否 8、其它,说明:说明:进行5WHY分析时,参与人员应尽量全面,如设计开发、工程(生产技术)、生产、品保、采购、业务、班组长、作业人员;过程中应采取开放式的以事实为原则,并结合采用脑力激荡法等方式进行。
b、根本原因分析(5个为什么):发生原因:第1个为什么?直接原因①为什么会发生电镀变形答:电镀卡槽内卡住撞击变形流出原因:第1个为什么?直接原因①为什么OQC没有管控到答:未尽职责第2个为什么?直接原因②为什么品质监控没有终止不良发生答:已发现不良实行全检,未能追踪第2个为什么?直接原因②为什么全检员工没有管控到答:技术培训不达标第3个为什么?直接原因③为什么电镀之后发现问题不能完全解决答全检过程中QC没能对全检之后的产品进行仔细抽检第3个为什么?直接原因③为什么发现不良没有严格管控答:监督不足第4个为什么?直接原因④为什么决定全检还不能控制不良答:控制不到位,OQC没能管控到第4个为什么?直接原因④为什么新进员工对产品认知不够规范答:经验不足第5个为什么?根本原因⑤为什么QC未跟踪追查不良答:不够细心第5个为什么?根本原因⑤为什么发现问题对策不够彻底答:包装人员不够认真负责c、问题点无法再现,根本原因查找1、现品分析(可采用环境试验、老化验证、模拟试验、客户或供应商场所验证、对手件上试验、实车验证等):机器运行正常,生产模具一次成型下落不会发生变形,电镀之后发现不良变形。
5why分析表(案例)
XX电子有限公司5Why分析表(案例)产品名称A型针车型问题描写针变形分析日期202X.3.9 不良数量55000PCS/180PCS/4PCS 不良率 2.2000% 产生场所进料检验生产批号202X.3.2a.进程工艺、检验、零部件状态追踪检查说明1、是否遵守SOP的工艺条件、作业流程?☐是□否 4、是否使用了体会证合格的零件?☐是□否2、是否使用正确的设备(含条件)及工具?☐是□否 5、技术规范是否符合、验证且培训?☐是□否3、人员是否培训并鉴定?□是☐否6、生产期间的环境状态是否有区分?□是☐否7、运输包装是否符合标准书要求?☐是□否 8、其它,说明:说明:进行5WHY分析时,参与人员应尽量全面,如设计开发、工程(生产技术)、生产、品保、采购、业务、班组长、作业人员;进程中应采取开放式的以事实为原则,并结合采取脑力激荡法等方式进行。
b、根本原因分析(5个为何):产生原因:第1个为何?直接原因①为何会产生电镀变形答:电镀卡槽内卡住撞击变形流出原因:第1个为何?直接原因①为何OQC没有管控到答:未尽职责第2个为何?直接原因②为何品质监控没有终止不良产生答:已发觉不良实行全检,未能追踪第2个为何?直接原因②为何全检员工没有管控到答:技术培训不达标第3个为何?直接原因③为何电镀之后发觉问题不能完全解决答全检进程中QC没能对全检之后的产品进行仔细抽检第3个为何?直接原因③为何发觉不良没有严格管控答:监督不足第4个为何?直接原因④为何决定全检还不能控制不良答:控制不到位,OQC没能管控到第4个为何?直接原因④为何新进员工对产品认知不够规范答:体会不足第5个为何?根本原因⑤为何QC未跟踪追查不良答:不够仔细第5个为何?根本原因⑤为何发觉问题计策不够彻底答:包装人员不够认真负责c、问题点没法再现,根本原因查找1、现品分析(可采取环境实验、老化验证、模拟实验、客户或供应商场所验证、对手件上实验、实车验证等):机器运行正常,生产模具一次成型着落不会产生变形,电镀之后发觉不良变形。
【精品】5个为什么分析
实际问题解决方式
问题的解决 5个为什么漏斗
鉴别出的问题 (大的,含糊不清的,复杂的)
阐明的问题
已定位的理由区
理由点 (简称PoC)
基本因果调查
问题发生在这个过程中的 哪一步?
“去看”问题
为什么? 1 理由 为什么? 2 理由 为什么? 3 理由 为什么? 4 理由 为什么? 5
根源
想法、原因、纠正措施或教训在避免的过程中有没有大的漏洞呢? 有没有由顾客来承担而不是供应商去承担的更多的纠正措施呢? 分析会说明整个事件吗?
感
5 – 为什么?
(测量特点在物理 和技术上的限制)
但是,顾客仍然不满意……
2023/10/15
12
问题的解决 例(4)
顾客想要知道为什么问题没有早一点被发现:
配件A2的物理特 性在顾客的组装 工厂里突然失效
1 – 为什么缺点 没有在到达顾客
前被发现?
生产零部件A2时的测 试程序不会和顾客的
测试一模一样
– 一些顾客已经发现5个为什么分析是解决供应商问题的一项有效工具
为什么顾客需要解决供应商问题?
– 因为供应商偶尔出现的质量问题会影响顾客对生意的运作并且也会影响终端顾客的 满意度
为什么供应商会偶尔出现质量问题?
2023/10/15
6
问题的解决 5个为什么的优点
满足顾客的需求
– 对已确定的问题根源做清晰的沟通 – 对缺乏的能力作出说明以便发现问题 – 重视潜在的系统性问题
2023/10/15
20
对5个为什么的评价 纠正措施
每一个纠正措施都会显示某条路径的根源吗? 每个根源都有一项独立的纠正措施吗?如果没有,那么一项纠正 措施应用于多个根源有意义吗? 每一项纠正措施都是可行的吗? 有没有哪些纠正措施会影响到顾客?如何对顾客解释它们? 有没有什么证据和文件来证明因果的有效性? 有无法撤回的纠正措施吗?如果没有,那有适当的可用作牵制政 策的纠正措施吗?