教材-三现五原则
三现五原则培训讲义

五原则
1.
◎现状把握的目的 1.真对问题全面调查事实. 2.掌握变异. 3.归纳可疑方向
查明要因 真因追查
5W分析 特性要因图 再现试验 NG再现试验 OK再现实验
2.
问题 要因 真因 查明真因
不良原因 流出原因
≈
何谓三现五原则
≈
适当对策
*已留入市场处理
临时对策
*库存成品处理 *半成品处理 *在库物料处理
标准化
S.O.P修正
*试验规范 *限度样品
三现五原则对策注意事项 1.无科学根据DATA之解析对策
2.以偏盖全之解析对策
3.增加不必要成本之解析对策
4.以变更设计改善制程变异之改善对策 5.变化点分析不明确之解析对策 6.无回馈标准之解析对策 7.无再现之解析对策
8.无三现之解析对策
9.无制程面、流出面检讨之解析对策 10.五层分析内容不连续解析对策
一.没有科学根据DATA 问题点:常发生的直觉判断 焊接强度不足 对策:加锡 正确吗? 焊接器件不粘锡 对策:焊接温度提升10度 没问题吗?
思 考:加锡/提高烙铁温度10度如何得来的? 直觉+经验≠事实 100个直觉或经验不如1个数据
分析方法:科学的根据=实验数据 有实验的数据才能决定新的标准. 要去试验出加锡及温度提高10度是最好的作业条件.
三现五原则讲义
前
一.背景
言
1.品质是企业生存的基本条件. 2.品质经常发生异常.成本损失大. 3.品质不良,操作人员总是认为是品管部门的责任. 4.不良解析经常找不到真因.
二.基本想法
1.籍由提高三现五原则解析能力.真正改善重要的品质问题点. 2.解决问题 持续有效的解决问题 不再是问题
三现五原则-最终版

要点二
详细描述
为了确保三现五原则的有效实施,企业应重视员工的培训 与参与。这可以通过开展定期培训、提供学习资源、鼓励 员工参与决策等方式实现。此外,企业应建立良好的激励 机制,表彰在原则实施过程中表现优秀的员工,以提高员 工的积极性和参与度。通过提高员工素质和参与度,企业 可以进一步推动三现五原则的落实,实现更好的发展成果 。
持续改进与优化的实施与效果
总结词
持续改进与优化是五原则的核心目标之一,它有助于组 织不断适应变化、提高竞争力和可持续发展。
详细描述
组织需要鼓励员工不断寻求改进和优化的机会,并为其 提供必要的资源和支持。这包括制定改进计划、设立改 进团队、引入创新技术和方法等。同时,组织还需要建 立有效的绩效评估体系,以衡量改进与优化的成果并持 续改进。持续改进与优化能够提高生产效率、降低成本 、增强创新能力、提升客户满意度和增强组织竞争力。
现状反思
定期对当前的工作情况进行反思和总结,找出可以改 进的地方。
现行措施调整
根据实际情况和反馈,及时调整现行措施,以实现持 续改进的目标。
04
五原则的实施与效果
管理层的决心和承诺的实施与效果
总结词
管理层对实施五原则的决心和承诺是至关重 要的,它决定了整个组织对五原则的重视程 度和执行力。
详细描述
VS
详细描述
随着企业内外部环境的变化,三现五原则 的实施方案也应不断调整和完善。企业应 定期评估原则的执行情况,总结经验教训 ,并根据实际情况调整实施方案。此外, 企业应关注行业动态和最佳实践,不断引 入新的理念和方法,以保持原则的先进性 和有效性。
原则五:员工培训与参与
要点一
总结词
员工培训与参与是三现五原则的重要支撑,需要提高员工 素质和参与度。
三现五原则-现场管理
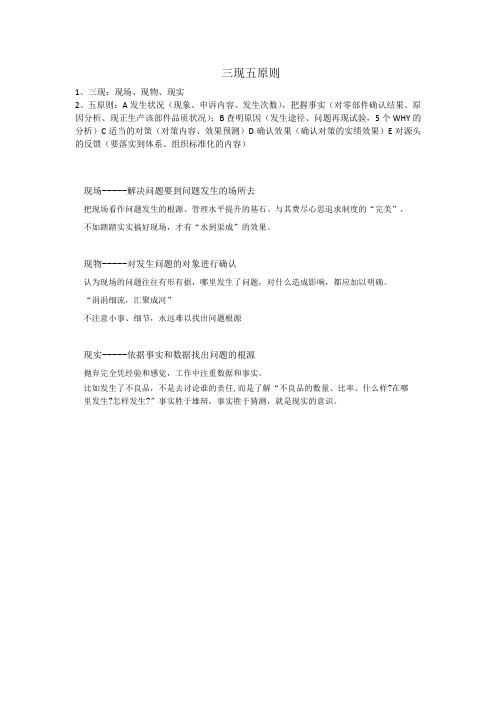
三现五原则
1、三现:现场、现物、现实
2、五原则:A发生状况(现象、申诉内容、发生次数),把握事实(对零部件确认结果、原因分析、现正生产该部件品质状况);B查明原因(发生途径、问题再现试验,5个WHY的分析)C适当的对策(对策内容、效果预测)D确认效果(确认对策的实绩效果)E对源头的反馈(要落实到体系、组织标准化的内容)
现场-----解决问题要到问题发生的场所去
把现场看作问题发生的根源、管理水平提升的基石。
与其费尽心思追求制度的“完美”,不如踏踏实实搞好现场,才有“水到渠成”的效果。
现物-----对发生问题的对象进行确认
认为现场的问题往往有形有据,哪里发生了问题,对什么造成影响,都应加以明确。
“涓涓细流,汇聚成河”
不注意小事、细节,永远难以找出问题根源
现实-----依据事实和数据找出问题的根源
抛弃完全凭经验和感觉,工作中注重数据和事实。
比如发生了不良品,不是去讨论谁的责任,而是了解“不良品的数量、比率、什么样?在哪里发生?怎样发生?”事实胜于雄辩,事实胜于猜测,就是现实的意识。
三现五原则
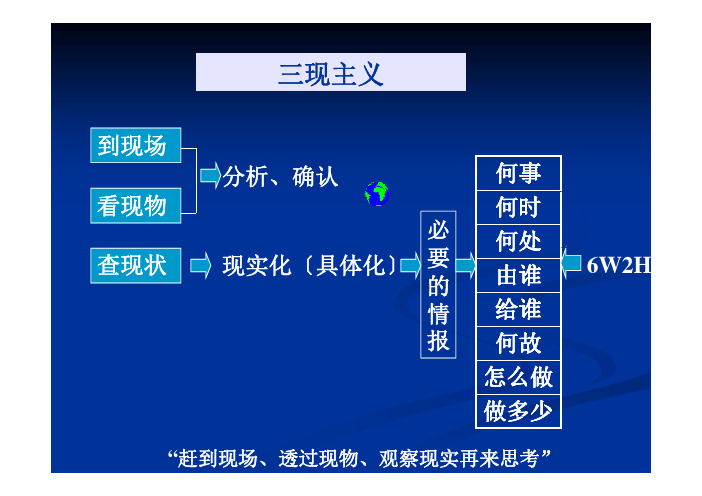
到 场 到现场 分析、确认 看现物 查现状 必 现实化〔具体化〕 要 的 情 报 何事 何时 何处 由谁 给谁 何故 怎么做 做多少
6W2H
“赶到现场、透过现物、观察现实再来思考”
三现五原则法: 三现五原则法 *三现:现场、现物、现状 *三现: 现场、现物、现状 发生状况 *五原则: *五原则 把握现状: 把握现状:时间、地点、现象、总生产量、不良 时间、地点、现象、总生产量、不良 数、不良率 不良率 。 查明原因: 制造不良原因:潜在因素、流出因素 制造不良要因 数据 不良简图 制造不良要因:数据、不良简图 对策追踪: 暂时对策 永久对策 永久 对策 确定所采措施 效果评估: 效果评估:改善后数据收集、左证成效 改善后数据收集、左证成效 回馈源流: 回馈源流 水平展开,引用于类似产品之设计开发 回馈源流:水平展开,引用于类似产品之设计开发 水平展开 引用于类似产品之设计开发 输入及制程规划之标准化
三现五原则表
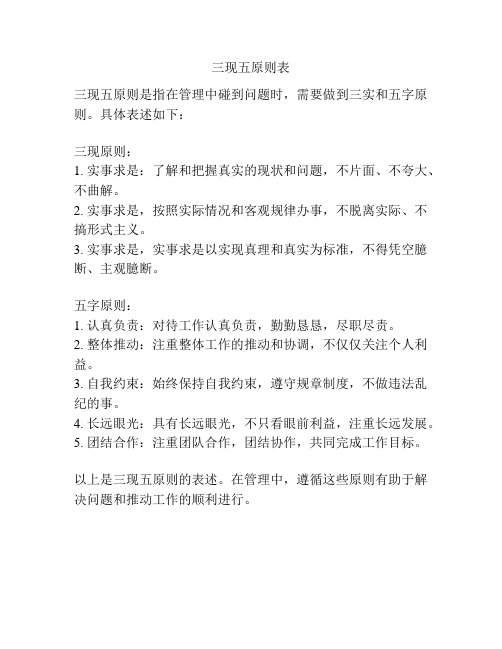
三现五原则表
三现五原则是指在管理中碰到问题时,需要做到三实和五字原则。
具体表述如下:
三现原则:
1. 实事求是:了解和把握真实的现状和问题,不片面、不夸大、不曲解。
2. 实事求是,按照实际情况和客观规律办事,不脱离实际、不搞形式主义。
3. 实事求是,实事求是以实现真理和真实为标准,不得凭空臆断、主观臆断。
五字原则:
1. 认真负责:对待工作认真负责,勤勤恳恳,尽职尽责。
2. 整体推动:注重整体工作的推动和协调,不仅仅关注个人利益。
3. 自我约束:始终保持自我约束,遵守规章制度,不做违法乱纪的事。
4. 长远眼光:具有长远眼光,不只看眼前利益,注重长远发展。
5. 团结合作:注重团队合作,团结协作,共同完成工作目标。
以上是三现五原则的表述。
在管理中,遵循这些原则有助于解决问题和推动工作的顺利进行。
三现五原则over[1]1
![三现五原则over[1]1](https://img.taocdn.com/s3/m/698f88d076eeaeaad1f33070.png)
对策:首末件检查→全检
10.要因:焊接后H方向尺寸NG
对策:焊接治具H方向调整
质量培训专用教材
16
核准
对策单位 复核
承办
1.发生状况 机种
零件编号
零件名称
发生时间
发生地点
数量
不良现象/抱怨内容
反应单位
生产日期
责任单位
临时措施:
3.问题点五层分析
问题 ①
WHY ②
发 生 源
WHY ③
WHY ④
流 出 面
实例:不良现象:踩剎车时BrakePedal有上、下作动感觉
1
2
3
4
5
為什
目視檢查時
麼之 Drum 內徑黑 未檢查
五層 皮產生
Drum 內徑
分析
尺寸 NG
無檢查基準 鑄造時 Drum 加熱變形 模具與 Drum 間隙過大
溫度過高加熱不 無溫度控制
均勻(500℃↑ ) (180℃~200℃)
模具磨損
無標準規定
分析方法: 1.制造面:分析4M的变化点→真因对策。 2.流出面: a.分析制造中的流程→作业环境、作业检验工程标准; b.分析检验的流出面:检验标准、限度样品、自动检测、 防呆装置。
质量培训专用教材
13
十、解析对策应五层分析内容连贯
意义:五层分析是一个形容词,代表追根究底的意思,其目 的在寻找真正的原因,并不是一次要作五次为什么分 析,可以比五次少,也可以比五次多。
担当 期限
效果确认
判定
7.效果确认(收集改善后一段时间的数据判断改善的效果) 确认者
单责 位任 主单 管位 核接 准单 后后 回应 复立 品即 保采 部取 ;临 品时 保措 部施 将消 稽除 核顾 对客 策/ 的下 实工 施程 状的 况抱 和怨 实; 施对 的策 效报 果告 。原
三现五原则与8D
5W分析法
特性要因圖
再現試驗
~
※ 問題
要因
真因
查明真因
NG再現
OK再現 不良再現 不良原因 製造面 流出原因 流出面
何謂三現五原則2/2
適當對策
3
查明要因 永久對策
對策情報傳達
效果確認
4
源流回饋
5
查明要因 永久對策
標準類反應 S.O.P修訂
.已流入市場處理 .庫存品處理
.半成品處理
.不良品處理
製造面、流出面之治本對策 水平展開對策 工程作業者 進料檢驗者
與滑板 ASSY 寬鬆
之析
搭配間隙大
回 檢驗標準增.修訂
饋
製程管理標準增.修訂 作業標準增.修訂
不良原因 人員
機械
會
品質檢查課(材料)檢驗員:
方法
材料
該工程作業員:
5
識別記號 責任單位 組立日期
設計 V
引擎號碼
- 蔡 正欽
-
-
3/28
已修訂 果 確
5.確認本案所費工時:
說
明: 1.設計者之原理念不詳,不能更改設計。
2.原設計時,經過耐久的驗證及市場之考驗
,其可靠度甚高。
3.未依圖裂作及未依原設計製作而產生之問題
(市怨、廠異…)
4.依圖製面程設變計異製應作之從保製障程。面去改善
五:變化點分析不清楚
疑 問 點:以前為何不會發生不良,現在才發生? 一定是那裡有變更,變化點在那裡?
原因分析 解析退回品椅背晃動量判定:合格 (附件一) 依品安表履歷查閱,” 05 年 3 月 15 日曾對策此項問題點止 鬆 Nut 未明訂扭力值,故 SY/全興所有成車及庫存均以扭力 板手(扭力設定 250 ㎏.㎝)全數確認 (附件二) 單件尺寸調查於” 05 年 3 月 24 日完成,因前/後升降連桿總 城與滑板總成約有 0.3~1.3mm 間隙,故於” 05 年 3 月 28 日 追加 t1.0mm 塑膠墊片 2PCS 以退回品座椅比較晃動量(追加墊片) 1 ㎏ 0.92mm0.39mm 5 ㎏ 5.99mm2.71mm 10 ㎏ 14.88mm6.60mm
三现五原则--现场管理PPT幻灯片
2020/4/1
23
质量●创新●服务
解决问题5原则表
记入要领
1-B 对事实的把握(对零部件的确认结果、原因分析、现在正在生产的该零部件的品质状况)
1、在确认事故发生时,也发现了
同样汽缸倒下来的情况,作业 人 人员每一次都是同样地用手把
它扶起来(还了解到一般9个 疲劳
设备
没有反馈 不知道方法
(利用特性要素图或FEMA, 析时,要最大限度使用“特性要素图”
KT法进行分析,对原因和事
实的验证)
在使用特性要素图时…在GSK版5原则表中这是主要
4、现在正在生产的零部件的品 的工具(使用另页)从大骨到小骨,因果关系要清
质状况(根据X-R管理图
晰明了,要将各种要素尽可能完整准确地归纳、整
工程能力表直方图现状进行 把握)
样数量可参考实际问题发生 率,数据方面可以灵活使用 统计手法。
2020/4/1
19
质量●创新●服务
5、源流回馈
标准类反应 源流回馈
•图面 •零件检验标准 •QC工程表 •作业标准 •试验规范 •限度样品
S.O.P修订
2020/4/1
20
质量●创新●服务
1、无科学根据数据
疑 问 点:常发生的直觉判断 ~ 焊接强度不足对策:焊道加长2mm.正确吗? ~ 模温不足变形对策:模温提高10℃.没问题吗?
解决问题5原则表1b对事实的把握对零部件的确认结果原因分析现在正在生产的该零部件的品质状况记入要领右手腕受伤材料方法设备注意不够疲劳睡眠不足没有反馈不知道方法作业标准不完善汽缸倒了用手扶起来手被夹住支架位置离作业人员太近支架材料刚性作业标准不完善没有关于汽缸倒下来的内容作业人员不知道反馈方法作业标准没有关于汽缸倒下来的情报未建立反馈体系汽缸倒下来这一情况未反馈202042925与特性要因图鱼刺图利用系统的有条理的qa提问和回答方法抓住找出真正的原因2a查明原因whywhy分析它扶起手腕被夹在传送带的横支架和汽缸之支架的位置离作业员太近由于作业人员注意不足扶起汽缸时机把握不当太支架和汽缸之间的间隙太小
质量管理三现五原则
2-B 查明原因(发生的途径、问题再现试验WHY WHY分析)
3 采取)适当的对策 (对策内容、效果预测PPA) 4确认(对策)效果(效果实绩) 5对(问题)源头的反馈(需落实到体制、组织的内容)
15、案例
右腕受伤
1- A 发生状况(现象、申诉内容、发生次数、5W1H处置内容)
1、发生场所:汽缸压铸NO.2生产线。 2、 发生状况:请参照右手腕受伤素描图
检验: 为何会检测不出来。
10、五层分析
意义:为什么之五层分析是一个形容 词,代表追根究底的意思,其目 的在寻求真正的原因,并不是一 次要作五次为什么分析,可以比 五次少,也可以比五次多,只要 能寻求出真正的原因。
10、五层分析
实例说明: 不良现象:踩刹车时有上、下作动感觉。
1
2
3
4
5
目视检查
为什 Drum内 未检查
3、五层分析是三现五原则单之中 心思想及布局。
11、要因 对策案例练习
1.要因:人为疏忽 对策:教育训练加强
2.要因:XX治具磨损 对策:更换新治具
3.要因:遗漏焊接 对策:后工程实施全检以确保
4.要因:半成品因台车太小不慎流入后工程 对策:台车修改加大
5.要因:修护车辆,等待时间长 对策:等待时间提供杂志阅读
1、把握现况 - 5W2H
WHERE 何地 – 记入问题发生的场所。 WHY 为什么 – 具体的内容 HOW 怎么样 – 问题是怎样发生的 HOW MANY 什么程度 – 问题发生量,
程度。
1、把握现况的填写方法
1、问题点的概要(信息的收集、整 理)。例:针对部品或工程。
2、问题再现试验的结果 3、现行品(现在生产)的品质状况 4、发生的对象范围
三现五原则
Drum内 未检验 为何 径黑皮
铸造时
热不均匀 (500↑℃)
之五 产生 层分 析
Drum内径 Drum加热 尺寸NG 变形
模具与
模具磨损
Drum间隙
过大
6
无温度 控制 (180200℃)
无原则 要求
10、五层分析
1、五层分析是三现五原则原因解 析之浓缩要点内容。
2、五层分析是同说故事一样,故 事必须连贯。
11、要因 对策案例练习
6. 要因:涂装后之成品受落尘污染 对策:将成品以防尘套保护
7. 要因:锁付之螺丝易松动 对策:螺丝追加LOCKTITE涂布
8. 要因:宿舍被单送洗频度高易破损 对策:送洗频度由15天/1次→30天/1次
9. 要因:检验疏忽 对策:首末件检验→全检
10.要因:焊接后H方向尺寸NG 对策:焊接治具H方向调整
3、五层分析是三现五原则单之中 心思想及布局。
11、要因 对策案例练习
1.要因:人为疏忽 对策:教育训练加强
2.要因:XX治具磨损 对策:更换新治具
3.要因:漏掉焊接 对策:后工程实施全检以确保
4.要因:半成品因台车太小不慎流入后工程 对策:台车修改加大
5.要因:修护车辆,等待时间长 对策:等待时间提供杂志阅读
制程变异应从制程面去改善
5、变化点分析不清楚
疑 问 点:此前为何不会发生不良,目前才发生? 一定是哪里有变更,变化点在哪里?
思 考:不良隐藏於变化点中。
分析措施:4M1D里寻找真因 人[Man]:人员有否更换,有否依原则作业、人员之 士气等。 机[Machine]:机器设备、镆、治、检、工具有否调 整、变更等。 料[Material]:材料有否变化、前工程流入件不良事 等。 措施[Method]: 原则有否要求?原则是否明确? 设计[Design]: 是否设计变更等。
- 1、下载文档前请自行甄别文档内容的完整性,平台不提供额外的编辑、内容补充、找答案等附加服务。
- 2、"仅部分预览"的文档,不可在线预览部分如存在完整性等问题,可反馈申请退款(可完整预览的文档不适用该条件!)。
- 3、如文档侵犯您的权益,请联系客服反馈,我们会尽快为您处理(人工客服工作时间:9:00-18:30)。
2.查明原因
三現五原則
1. 利用要因分析、FMEA等手法,寻求造成不良零件质量特性的原因。 引起 不良零件质量特性 何种制程上的因素(设备、工夹治检 具) 2. 内容 2.1发生要因 ●使用特性要因图、FMEA等QC手法查明原因 ●制造原因:设备、治具、工具、检具等原因追查 2.2原因未明,问题现象再现性 ●现场确认 ●现物确认 ●再现TE???
特性要因圖 •何谓特性要因图: • 一个问题的特性受到一些要因的影响时,我们将这些要因 •加以整理成为有相互关系而且有 条理的图形。这个图形称为 •特性要因图。 问题的特性是由许多要因造成的!
要 因
要 因
要 因
問 題 特 性
要 因
要 因
要 因
将这些要因分成为大、中、小要因可绘制成特性要因图, 因其像鱼骨故又称鱼骨图。
三現五原則
为什么之五层分析的实例说明一:
为 什 么 之 五 层 分 析 1 2 目视检查时 未全检 煞车环内径 黑皮产生 煞车内径尺寸 NG 3 无目视 检查基准 温度过高加热不 铸造时煞车环加 均匀 热变形 500℃↑ 模具与煞车环间 隙过大 磨损 无温度控制 180~200℃ 4 5
无标准规定
何谓三现~ 三现主义
到现场 分析、确认 看现物 必 要 的 情 报
何事
何时 何处 由谁
查现状
现实化〔具体化〕
6W2H
如何
给谁 怎么做
“赶到现场、透过现物、观察现状再来思考” 做多少
三 現 五 原 則
例:汽车轮圈 1.现场 2.现物 3.现状
现场:北投区防波堤
现物:南阳汽车保养厂撞毁汽车 现状:轮圈断裂分离,车头及右车辆 侧面严重擦伤
三現五原則
为什么之五层分析说明及实例 为什么之五层分析的意义 为什么之五层分析是一个形容词,代表追根究底的意思,其目的在 寻求真正的原因,并不是一次要作五次为什么分析,可以比5次少,可以 比5次多,只要能寻出真正的原因。
图示说明
零件品質特性不良 結果 零件质量特性不良流出原因 原因 产生零件质量特性不良原因 原因
表格
三現五原則
實例說明二:
XX零件不良 無檢驗標準 XX治具磨損 無治具堪用標準
實例說明三:
XX零件不良
作業者未依標準檢驗
作業者不了解
XX治具磨損
作業者未依規定 更換
作業者不了解
三現五原則
3.对策拟定、实施 对策拟定 1.临时对策及对策效果预测。 (依据再现测试或质量DATA效果预测) 2.已流入市场零件处理对策。 3.库存品、半成品处理对策。 4.对策时考虑是否有潜在问题。 对策拟定注意事项 1.对策时需记录对策年、月、日,对策对象零件、型式、 尺寸(可作为对策确认的依据) 。 2.对策部品需管制,直到??攘
大 要 因
大 要 因
小要 因
中 要 因
小要 因
中 要 因
特 性
中 要 因
中 要 因 大 要 因 大 要 因
特性要因图制作的五个步骤
步骤一:决定问题或质量的特性
为 什 么 延 迟 交 货 ?
特 性
步驟二:決定大要因
制 造
人
为 什 么 延 迟 交 货 ?
特 性
物 品
交 货
步骤三:决定中、小要因:可利用亲和图法来将决定中、小要因区分出来。 步骤四:讨论影响问题点的主要原因。 步骤五:填上制作目的,日期及制作者等数据。
三现五原则法:
*三现:现场、现物、现状 发生状况 *五原则: 把握现状:时间、地点、现象、总生产量、不良数、不 良率 。 查明原因:制造不良原因:潜在因素、流出因素制造不 良要因:数据、不良简图 对策追踪:暂时对策 永久对策 确定所采措施 效果评估:改善后数据收集、左证成效 回馈源流:水平展开,引用于类似产品之设计开发 输入及制程规划之标准化 (表格)
三現五原則
发生状况 1.1数据来源 1.2发生地点
1.3发生日期 1.4发生批号 1.5发生件数
掌握发生状况 2.1数据来源 对书面资料所反 应的状况有所依据 2.2发生地点 对书面资料所反 应的状况有所不了 解,可直接到现场了解 2.3发生日期 可作为问题处理 时效的评估 2.4发生批号 可了解发生问题 的对象方便追查 2.5发生件数 可了解事???
所谓5W1H就是: Why(为何必要)、What(目的为何)、Where(在何处做) When(何时做)、Who(谁来做)、How( 如何做)。
绘制特性要因图掌握原则
•大、小要因要确实可行。
•由大Байду номын сангаас因到小要因进行讨论,之后再由小要因往 • 大要因追溯,以确认其相关性
•在找小要因时,原则上不考虑其可能性的大小, • 一一列出。之后圈选可能原因时,再搭配查检表 • 做数量收集。
5.回馈标准
1.把握现状
2.1目的 掌握顾客所反应的不良现象,然后针对所退回的不良实物,测定其质 量特性并从事下列二项工作。 a.何种零件之质量特性不良引起不良结果。 b.了解引起不良现象之不良零件质量特性的量产水帄,并了解该零件 所分布的状况。 2.2内容 a.问题部品依质量特性测定结果 b.问题再现确认结果(不良品质量特性再现) c.要因分析:特性要因图,FMEA手法等分析,要因事实追查确认 d??迨
发生状况的数据越完整,对问题的解析越有有帮助, 如市场不良统计层别分析方式,如果数据完整,甚至可使 用状况、天候…… 等各种方式来层别,当然层别的目的 是要找出问题所在,不是每种层别都要作,只要掌握这个 原则,假以时日,对你解决问题的能力相信有莫大的帮助
何谓五原则?
1.把握现状
2.查明原因
3.对策实施 4.效果确认
三現五原則
4.对策后效果确认 效果确认的方式可分为下列3种 1.零件质量特性的确认-------可于制程中确认 2.初期样品质量的确认-------可于最终检查单位或厂 内确认 3.性能强度测试的确认-------可由工程课协助确认
三现五原则
5.回馈 1.使对策效果继续维持,将对策项目反应于标准类 ~1. QC工程表修订 ~2. 检验基准书修订 ~3. 图面修订 ~4. 作业标准书修订 2.对于造成原因之项目所做的解决方案(横、直向)给予反应 ~1.制程相关单位:厂商、资材、品管、生管等。 ~2.相关基准单位:厂商、资材、品管、研发。 ~3.技术累积 ???
大 要 因 大 要 因
小 要 因
中要因 如 何 做 ? 中要因 大 要 因 小 要 因 中要因
小 要 因
中要因
大 要 因
绘制特性要因图掌握原则
•绘制特性要因图要把握脑力激荡法的原则,让所有的成员表达心声。 •列出的要因应给予层别化。 •绘制特性要因图时,重点应放在“为何会有这种原因”并且依5W1H的方法逐一 • 列出。 •如果您是指导人员,切记不可凭个人好恶去决定或交办给他人的方式而影响讨论 • 人员的热忱。
製 造
人
生产计划不相吻合 不良率高 没有危机感
情报错误
库存量低
会议目的: 会议日期: 与会者:
物 品
存放位置不佳
交期过短
为 什 么 延 迟 交 货 ?
特 性
交 货
特性要因图的使用时机
•问题的整理,及原因探索。 •追查真正的原因。 •寻找对策:特性要因图也可用来做对策整理用,这时鱼头的方向会刚好相反过来, • 又称为反转。