三现五原则手法讲解
合集下载
三现五原则培训讲义

五原则
1.
◎现状把握的目的 1.真对问题全面调查事实. 2.掌握变异. 3.归纳可疑方向
查明要因 真因追查
5W分析 特性要因图 再现试验 NG再现试验 OK再现实验
2.
问题 要因 真因 查明真因
不良原因 流出原因
≈
何谓三现五原则
≈
适当对策
*已留入市场处理
临时对策
*库存成品处理 *半成品处理 *在库物料处理
标准化
S.O.P修正
*试验规范 *限度样品
三现五原则对策注意事项 1.无科学根据DATA之解析对策
2.以偏盖全之解析对策
3.增加不必要成本之解析对策
4.以变更设计改善制程变异之改善对策 5.变化点分析不明确之解析对策 6.无回馈标准之解析对策 7.无再现之解析对策
8.无三现之解析对策
9.无制程面、流出面检讨之解析对策 10.五层分析内容不连续解析对策
一.没有科学根据DATA 问题点:常发生的直觉判断 焊接强度不足 对策:加锡 正确吗? 焊接器件不粘锡 对策:焊接温度提升10度 没问题吗?
思 考:加锡/提高烙铁温度10度如何得来的? 直觉+经验≠事实 100个直觉或经验不如1个数据
分析方法:科学的根据=实验数据 有实验的数据才能决定新的标准. 要去试验出加锡及温度提高10度是最好的作业条件.
三现五原则讲义
前
一.背景
言
1.品质是企业生存的基本条件. 2.品质经常发生异常.成本损失大. 3.品质不良,操作人员总是认为是品管部门的责任. 4.不良解析经常找不到真因.
二.基本想法
1.籍由提高三现五原则解析能力.真正改善重要的品质问题点. 2.解决问题 持续有效的解决问题 不再是问题
三现五原则-品保部
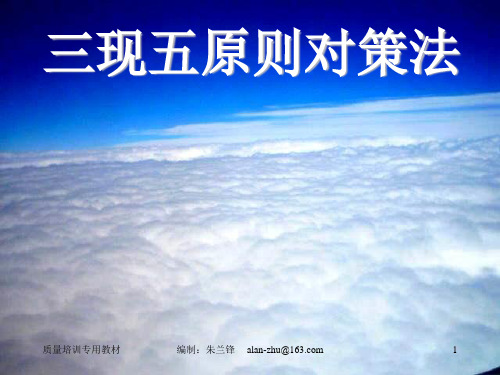
三现五原则对策法
质量培训专用教材
编制:朱兰锋
alan-zhu@
1
何 谓 三 现 五 原 则
三现 现物 现场 现状 事实把握 1. *机种、零件名称/号码 机种、零件名称 号码 机种 *发生场所 环境 使用条件 发生场所/环境 发生场所 环境/使用条件 *发生现象 问题 发生现象/问题 发生现象 *发生日期 发生日期 *引擎号码 引擎号码 *发生件数 严重性 发生件数/严重性 发生件数 *行驶里程 耐久性 行驶里程/耐久性 行驶里程 *制造日期 批量性 制造日期/批量性 制造日期 *出车日期 库存性 出车日期/库存性 出车日期 *不良现物品质确认 不良现物品质确认 *量产中品质水准确认 量产中品质水准确认 *开发阶段品质水准比对 开发阶段品质水准比对 *设计变更履历 设计变更履历 *其它异常履历 其它异常履历 *标准确认 图面、作业、QC工程检验 标准确认(图面 工程检验…) 标准确认 图面、作业、 工程检验 查明要因 2. 真因追查 4M分析 5W分析法 特性要因图 再现试验 NG再现 再现 OK再现 再现
质量培训专用教材 编制:朱兰锋 alan-zhu@ 4
一、解析对策应有科学的数据依据
疑问点: 疑问点:常发生的直觉判断 1.焊接强度不足 对策:焊道加长2mm 正确吗? 焊接强度不足→ 2mm, 1.焊接强度不足→对策:焊道加长2mm,正确吗? 2.模温不足变形 对策:模温提高10℃ 没问题吗? 模温不足变形→ 10℃, 2.模温不足变形→对策:模温提高10℃,没问题吗? 思考:加长2mm、提高10℃如何得到的? 2mm、 10℃如何得到的 思考:加长2mm 提高10℃如何得到的? 直觉+经验≠ 直觉+经验≠事实 100个直觉或经验不如 100个直觉或经验不如1个数据 个直觉或经验不如1 分析方法: 分析方法: 1.科学的根据 1.科学的根据=实验数据 科学的根据= 2.有实验的数据才能决定新的标准 2.有实验的数据才能决定新的标准 3.要去试验出焊道加长2mm及模温提高10℃是最好的条 3.要去试验出焊道加长2mm及模温提高10℃是最好的条 要去试验出焊道加长2mm及模温提高10℃ 件作业。 件作业。
质量培训专用教材
编制:朱兰锋
alan-zhu@
1
何 谓 三 现 五 原 则
三现 现物 现场 现状 事实把握 1. *机种、零件名称/号码 机种、零件名称 号码 机种 *发生场所 环境 使用条件 发生场所/环境 发生场所 环境/使用条件 *发生现象 问题 发生现象/问题 发生现象 *发生日期 发生日期 *引擎号码 引擎号码 *发生件数 严重性 发生件数/严重性 发生件数 *行驶里程 耐久性 行驶里程/耐久性 行驶里程 *制造日期 批量性 制造日期/批量性 制造日期 *出车日期 库存性 出车日期/库存性 出车日期 *不良现物品质确认 不良现物品质确认 *量产中品质水准确认 量产中品质水准确认 *开发阶段品质水准比对 开发阶段品质水准比对 *设计变更履历 设计变更履历 *其它异常履历 其它异常履历 *标准确认 图面、作业、QC工程检验 标准确认(图面 工程检验…) 标准确认 图面、作业、 工程检验 查明要因 2. 真因追查 4M分析 5W分析法 特性要因图 再现试验 NG再现 再现 OK再现 再现
质量培训专用教材 编制:朱兰锋 alan-zhu@ 4
一、解析对策应有科学的数据依据
疑问点: 疑问点:常发生的直觉判断 1.焊接强度不足 对策:焊道加长2mm 正确吗? 焊接强度不足→ 2mm, 1.焊接强度不足→对策:焊道加长2mm,正确吗? 2.模温不足变形 对策:模温提高10℃ 没问题吗? 模温不足变形→ 10℃, 2.模温不足变形→对策:模温提高10℃,没问题吗? 思考:加长2mm、提高10℃如何得到的? 2mm、 10℃如何得到的 思考:加长2mm 提高10℃如何得到的? 直觉+经验≠ 直觉+经验≠事实 100个直觉或经验不如 100个直觉或经验不如1个数据 个直觉或经验不如1 分析方法: 分析方法: 1.科学的根据 1.科学的根据=实验数据 科学的根据= 2.有实验的数据才能决定新的标准 2.有实验的数据才能决定新的标准 3.要去试验出焊道加长2mm及模温提高10℃是最好的条 3.要去试验出焊道加长2mm及模温提高10℃是最好的条 要去试验出焊道加长2mm及模温提高10℃ 件作业。 件作业。
三现五原则教材

为了使在调查过程中不要遗漏有用的信息和重要事实,要 多听、多看(严禁带有成见)在确认过程中尽可能地使用(3 现实主义),在进行原因分析时,要最大限度使用“特性要素 图”
现状把握举例:
1、 3、 4、 6、 机种、型号 2、 发生状况:(市场、公司内) 问题发生时的现象或(当事人的)申诉 发生年月日 5、 发生件数 对发生问题机种或是零部件的处置结果。
五原则三----对策实施
临 时 对 策 适 当 对 策 (防止恶化扩大) 永 久 对 策 (避免再发) •已流入市场处理 •库存成品处理 •半成品处理 •不良品处理 •制造面、流出 面之治本对策 •水平展开对策 •工程作业者 •进料检验者 •市场服务者 (品质通报)
对策情报传达
适当的对策(对策内容、效果预测PPA)
為什 麼之 飾條素材 五層 產生縮水 分析
2
目視檢查時 未檢查
3
無檢查基準
4
加熱不均 勻 模具損壞
5
溫度控 制損壞 未按規 定檢查
射出時素材加熱 飾條素材表 變形 面NG 模具與飾條間隙 過大
1、五層分析是三現五原則原因解析之濃縮重點內容。 2、五層分析是同說故事一樣,故事必須連貫。 3、五層分析是三現五原則單之中心思想及佈局。
不良实物
不良发生的状况, 包括使用状况 不良品发生的原 地、环境因素
五原则一--------现状把握
现状把握目的 针对问题,全盘调查事实掌握变异(机遇/非机遇原因)归纳可 疑方向 对事实的把握(现在生产的该零部件的品质状况、现象、问题 内容、发生次数、5W2H处置内容)
现状把握内容
1、问题点的概要(信息的收集、整理)例,针对部品或工程。 2、问题再现试验的结果 3、现行品的品质状况 4、发生的对象范围 5、利用绘图、图表、柱状图使问题明确化。 6、将可能想到的原因、内容,详尽的进行整理,在记录上明 确的记载。
三现五原则-文档资料
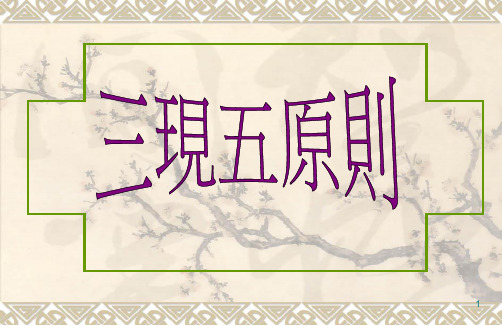
21
三现五原则
5.回馈 1.使对策效果继续维持,将对策项目反应于标准类 ~1. QC工程表修订 ~2. 检验基准书修订 ~3. 图面修订 ~4. 作业标准书修订 2.对于造成原因之项目所做的解决方案(横、直向)给予反应 ~1.制程相关单位:厂商、资材、品管、生管等。 ~2.相关基准单位:厂商、资材、品管、研发。 ~3.技术累积 ???
1
何谓三现~ 三现主义
到现场 看现物 查现状
分析、确认
必 要 现实化〔具体化〕 的 情 报
何事 何时 何处 由谁 如何 怎么做
“赶到现场、透过现物、观察现状再来思考”
5W1H
2
三現五原則
例:汽车轮圈
1.现场 2.现物 3.现状
现场:北投区防波堤
现物:南阳汽车保养厂撞毁汽车
现状:轮圈断裂分离,车头及右车辆 侧面严重擦伤
2.2内容 a.问题部品依质量特性测定结果 b.问题再现确认结果(不良品质量特性再现) c.要因分析:特性要因图,FMEA手法等分析,要因事实追查确认 d??迨
7
2.查明原因
三現五原則
1. 利用要因分析、FMEA等引手起 法,寻求造成不良零件质量特性的原因。
不良零件质量特性
何种制程上的因素(设备、工夹治检
22
三现五原则法:
*三现:现场、现物、现状
发生状况
*五原则:
把握现状:时间、地点、现象、总生产量、不良数、不 良率 。
查明原因:制造不良原因:潜在因素、流出因素制造不 良要因:数据、不良简图
对策追踪:暂时对策 永久对策
确定所采措施
效果评估:改善后数据收集、左证成效
回馈源流:水平展开,引用于类似产品之设计开发
交 交期过短 货
三现五原则
5.回馈 1.使对策效果继续维持,将对策项目反应于标准类 ~1. QC工程表修订 ~2. 检验基准书修订 ~3. 图面修订 ~4. 作业标准书修订 2.对于造成原因之项目所做的解决方案(横、直向)给予反应 ~1.制程相关单位:厂商、资材、品管、生管等。 ~2.相关基准单位:厂商、资材、品管、研发。 ~3.技术累积 ???
1
何谓三现~ 三现主义
到现场 看现物 查现状
分析、确认
必 要 现实化〔具体化〕 的 情 报
何事 何时 何处 由谁 如何 怎么做
“赶到现场、透过现物、观察现状再来思考”
5W1H
2
三現五原則
例:汽车轮圈
1.现场 2.现物 3.现状
现场:北投区防波堤
现物:南阳汽车保养厂撞毁汽车
现状:轮圈断裂分离,车头及右车辆 侧面严重擦伤
2.2内容 a.问题部品依质量特性测定结果 b.问题再现确认结果(不良品质量特性再现) c.要因分析:特性要因图,FMEA手法等分析,要因事实追查确认 d??迨
7
2.查明原因
三現五原則
1. 利用要因分析、FMEA等引手起 法,寻求造成不良零件质量特性的原因。
不良零件质量特性
何种制程上的因素(设备、工夹治检
22
三现五原则法:
*三现:现场、现物、现状
发生状况
*五原则:
把握现状:时间、地点、现象、总生产量、不良数、不 良率 。
查明原因:制造不良原因:潜在因素、流出因素制造不 良要因:数据、不良简图
对策追踪:暂时对策 永久对策
确定所采措施
效果评估:改善后数据收集、左证成效
回馈源流:水平展开,引用于类似产品之设计开发
交 交期过短 货
三现五原则-品保部
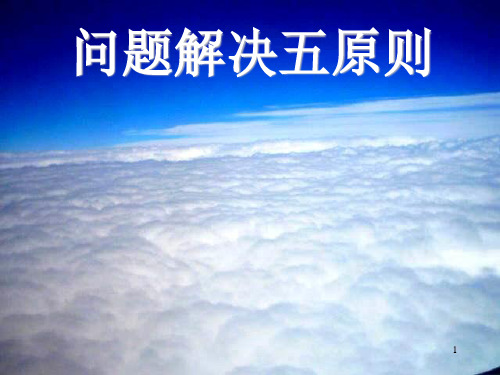
发现单位确认 签核
核准
审核
发现人
核准
责任单位确认 审核
负责人
核准
品质单位确认 稽核
确认
备注
保存年限:5年
17
版本: 2014.03.23 第5版
测试题: 1.三现五原则指哪三现、哪五原则? 2.用三现五原则分析对策时应注意那些问题?
3.制定适当的对策时应注意哪些方面?
4.再现性试验有哪几种方法,分别如何进行? 5.案例分析:结合实际工作中的某一问题点,采用三现五原则 的方法进行分析。
11
八、解析对策应依据三现(现物、现场、现状)
疑问点:有至现场去看吗?是否实车确认、实物、实地确认? 说明: 1.未三现,可能会得到错误的讯息,或疏略重点信息。 2.选择性事实:三现的目的,在于针对问题,全盘掌握事实,
而未三现,可能仅知道部份事实。
3.有三现,才能相信自己,说服别人。
解析对策必须遵守三现主义
13
十、解析对策应五层分析内容连贯
意义:五层分析是一个形容词,代表追根究底的意思,其目
的在寻找真正的原因,并不是一次要作五次为什么分 析,可以比五次少,也可以比五次多。 实例:不良现象:踩剎车时BrakePedal有上、下作动感觉
1 為什 麼之 Drum 內徑黑 五層 皮產生 分析 2 3 4 5 無檢查基準 目視檢查時 鑄造時 Drum 未檢查 加熱變形 Drum 內徑 模具與 Drum 尺寸 NG 間隙過大
4
一、解析对策应有科学的数据依据
疑问点:常发生的直觉判断 1.焊接强度不足→对策:焊道加长2mm,正确吗?
2.模温不足变形→对策:模温提高10℃,没问题吗?
思考:加长2mm、提高10℃如何得到的? 直觉+经验≠事实 100个直觉或经验不如1个数据 分析方法: 1.科学的根据=实验数据 2.有实验的数据才能决定新的标准 3.要去试验出焊道加长2mm及模温提高10℃是最好的条 件作业。
来自台湾的三现五原则说明PPT课件

a.成本UP:需有UP的合理原因,需檢討合理與不合理 b.成本不變動 c.成本下降:GOOD
3.成本UP部份由廠商吸收,雖然不影響SY, 但對總體成本仍是上升的,亦非好之對策。
解析對策必須顧慮成本面
4.以變更設計改善製程變異:
疑 問 點:1.變更設計就不會有問題了嗎?
2.新設計有新的問題,甚至比現在的問題更嚴重。 3.製程中4M問題未改善,新設計就不會發生相同問題嗎?
.發生場所/環境/使用條件 .發生日期 .發生件數/嚴重性 .製造日期/批量性 .不良現物品質確認 .設計變更履歷 .標準確認(圖面、作業、
QC工程檢驗.....)
※現狀把握目的 1 針對問題,全盤調查事實 2 掌握變異(機遇/非機遇原因) 3 歸納可疑方向
2 查明原因
查明要因
4M分析 5W分析法 特性要因圖 再現試驗 (不良再現)
NG再現 OK再現
~~
要因
真因
查明真因
不良原因 製造面 流出原因 流出面
三、何謂三現五原則 2/2
3 適當對策
4
效果確認 5 源流回饋
查明要因 永久對策 對策情報傳達
查明要因 永久對策 標準類反應 S.O.P修訂
.已流入市場處理 .半成品處理
.庫存品處理 .不良品處理
製造面、流出面之治本對策
水平展開對策
a.平均數X b.中位數 c.眾數。
2.掌握品質的均勻程度
a.全距R b.最大最小值Man、Min
3.掌握製程品質能力
a.CP值
b.CPK值
c.標準差。
3.增加不必要成本:
疑 問 點:利潤很高嗎?增加成本沒關係嗎?
思 考: 1.利潤=售價-成本 成本UP,自然利潤降低。 2.解析對策成本面結果有三種:
3.成本UP部份由廠商吸收,雖然不影響SY, 但對總體成本仍是上升的,亦非好之對策。
解析對策必須顧慮成本面
4.以變更設計改善製程變異:
疑 問 點:1.變更設計就不會有問題了嗎?
2.新設計有新的問題,甚至比現在的問題更嚴重。 3.製程中4M問題未改善,新設計就不會發生相同問題嗎?
.發生場所/環境/使用條件 .發生日期 .發生件數/嚴重性 .製造日期/批量性 .不良現物品質確認 .設計變更履歷 .標準確認(圖面、作業、
QC工程檢驗.....)
※現狀把握目的 1 針對問題,全盤調查事實 2 掌握變異(機遇/非機遇原因) 3 歸納可疑方向
2 查明原因
查明要因
4M分析 5W分析法 特性要因圖 再現試驗 (不良再現)
NG再現 OK再現
~~
要因
真因
查明真因
不良原因 製造面 流出原因 流出面
三、何謂三現五原則 2/2
3 適當對策
4
效果確認 5 源流回饋
查明要因 永久對策 對策情報傳達
查明要因 永久對策 標準類反應 S.O.P修訂
.已流入市場處理 .半成品處理
.庫存品處理 .不良品處理
製造面、流出面之治本對策
水平展開對策
a.平均數X b.中位數 c.眾數。
2.掌握品質的均勻程度
a.全距R b.最大最小值Man、Min
3.掌握製程品質能力
a.CP值
b.CPK值
c.標準差。
3.增加不必要成本:
疑 問 點:利潤很高嗎?增加成本沒關係嗎?
思 考: 1.利潤=售價-成本 成本UP,自然利潤降低。 2.解析對策成本面結果有三種:
五原则表五个步骤
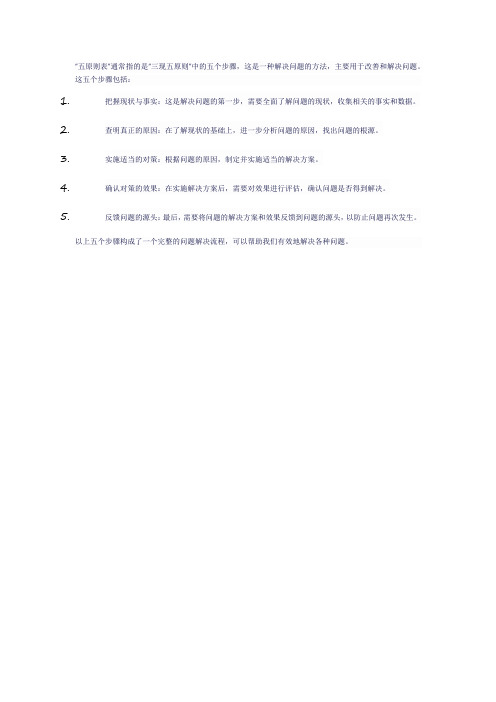
“五原则表”通常指的是“三现五原则”中的五个步骤,这是一种解决问题的方法,主要用于改善和解决问题。
这五个步骤包括:
1.把握现状与事实:这是解决问题的第一步,需要全面了解问题的现状,收集相关的事实和数据。
2.查明真正的原因:在了解现状的基础上,进一步分析问题的原因,找出问题的根源。
3.实施适当的对策:根据问题的原因,制定并实施适当的解决方案。
4.确认对策的效果:在实施解决方案后,需要对效果进行评估,确认问题是否得到解决。
5.反馈问题的源头:最后,需要将问题的解决方案和效果反馈到问题的源头,以防止问题再次发生。
以上五个步骤构成了一个完整的问题解决流程,可以帮助我们有效地解决各种问题。
5WHY解决问题的三现五原则

三现五原则
1.现场:不良品发生的原地,环境因素。
2.现物:实际不良品。
3.现状:不良发生的状况,包括实际状况 五原则
1.把握现状:零件的品质状态,确认结果,要因分析。
2.查明原因:再现试验,原因分析。
3.适当对策:对策内容,效果预测。
45.回馈更正:体制改善,反应修正。
如何做有效的分析与报告
问题解决之五大原则
1.1 发生状况:现场、现物、现状、日期、数量、LOT NO。
1.2 把握现状:基准值与实测的差异,再现试验,要因分析。
现在生产品质状况。
发生对象与相关原材料、中间制品。
1.3 原因的查明:分析主要要因。
再现性原因的确认。
1.4 适当的额对策:暂时或者永久性的对策内容,日期、LOT NO.在库品处理,已出库品处理。
1.5 确认对策的效果:比较对策前后都额差异。
1.6 回馈。