高炉五大系统
简述高炉炼铁工艺流程及八大系统

简述高炉炼铁工艺流程及八大系统高炉炼铁是一种重要的冶炼工艺,通过高炉将铁矿石转化为生铁。
Blast furnace ironmaking is an important smelting process that converts iron ore into pig iron through a blast furnace.高炉炼铁工艺一般包括八大系统,分别是原料系统、燃料系统、风口系统、炉料系统、炉渣系统、渣铁系统、炉底系统和炉体冷却系统。
The blast furnace ironmaking process generally includes eight major systems: raw material system, fuel system, tuyere system, burden system, slag system, hot metal system, hearth system, and furnace cooling system.原料系统包括铁矿石、焦炭和石灰石等原料,这些原料经过预处理后送入高炉顶部。
The raw material system includes iron ore, coke, limestone, and other materials, which are pre-processed and then charged into the top of the blast furnace.燃料系统主要是焦炭和其他燃料的供给和燃烧控制。
The fuel system mainly involves the supply and combustion control of coke and other fuels.风口系统通过送风机将空气送入高炉内,控制高炉内的氧气含量和温度。
The tuyere system uses blowers to inject air into the blast furnace, controlling the oxygen content and temperature inside the furnace.炉料系统指的是铁矿石、焦炭和其他原料在高炉内的分布和堆积状况。
高炉系统的危险有害因素辨识
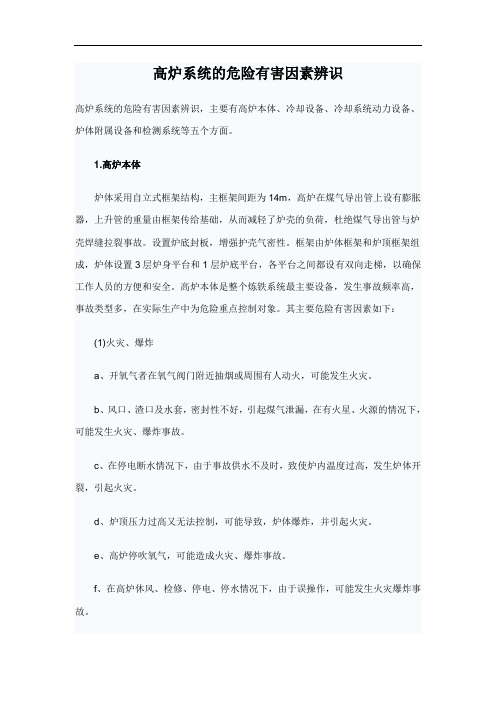
高炉系统的危险有害因素辨识高炉系统的危险有害因素辨识,主要有高炉本体、冷却设备、冷却系统动力设备、炉体附属设备和检测系统等五个方面。
1.高炉本体炉体采用自立式框架结构,主框架间距为14m,高炉在煤气导出管上设有膨胀器,上升管的重量由框架传给基础,从而减轻了炉壳的负荷,杜绝煤气导出管与炉壳焊缝拉裂事故。
设置炉底封板,增强护壳气密性。
框架由炉体框架和炉顶框架组成,炉体设置3层炉身平台和1层炉底平台,各平台之间都设有双向走梯,以确保工作人员的方便和安全。
高炉本体是整个炼铁系统最主要设备,发生事故频率高,事故类型多,在实际生产中为危险重点控制对象。
其主要危险有害因素如下:(1)火灾、爆炸a、开氧气者在氧气阀门附近抽烟或周围有人动火,可能发生火灾。
b、风口、渣口及水套,密封性不好,引起煤气泄漏,在有火星、火源的情况下,可能发生火灾、爆炸事故。
c、在停电断水情况下,由于事故供水不及时,致使炉内温度过高,发生炉体开裂,引起火灾。
d、炉顶压力过高又无法控制,可能导致,炉体爆炸,并引起火灾。
e、高炉停吹氧气,可能造成火灾、爆炸事故。
f、在高炉休风、检修、停电、停水情况下,由于误操作,可能发生火灾爆炸事故。
(2)中毒a、挖炉缸作业时,如通风不良,炉缸内煤气浓度过高,可能造成煤气中毒事故。
b、换风口及二套时,由于煤气泄漏,如不加强防护,可能造成煤气中毒事故。
c、在炉体清理作业中,由于残留煤气,如通风不良,无恰当防护措施,可能发生煤气中毒事故。
d、在高炉休风、检修、停电、停水情况下,由于误操作,可能发生火灾爆炸事故。
(3)烧伤a、在休风倒流阶段,炉前工离风口过近,可能被喷火烧伤。
b、在进行换风口操作时,由于风口内渣铁没有完全淌出,可能烧伤工人。
c、风管烧穿打水时,可能对工人造成伤害。
d、在风口区域、铁口旁取暖,工人可能被烧伤。
e、烧氧时,吹氧管顶的太死,氧气回火,可能造成工人烧伤。
(4)高空坠落a、平台四周栏杆走桥损坏、送脱,操作人员可能从高空坠落。
详细到哭!高炉炼铁工艺的系统组成!10大系统让你更了解高炉!

详细到哭!高炉炼铁工艺的系统组成!10大系统让你更了解高炉!高炉炼铁工艺的系统组成:原料系统、上料系统、炉顶系统、炉体系统、粗煤气及煤气清洗系统、风口平台及出铁场系统、渣处理系统、热风炉系统、煤粉制备及喷吹系统、辅助系统(铸铁机室及铁水罐修理库和碾泥机室)。
高炉炼铁主要工艺流程如图1-1所示。
一.原料系统(1)原料系统的主要任务。
负责高炉冶炼所需的各种矿石及焦炭的贮存、配料、筛分、称量,并把矿石和焦炭送至料车和主皮带。
原料系统主要分矿槽、焦槽两大部分。
矿槽的作用是贮存各种矿石,主要包括烧结矿、块矿、球团矿、熔剂等,其矿槽槽数及大小应根据各矿种配比及贮存时间确定,一般烧结矿贮存时间不小于10h,块矿、球团矿、熔剂等贮存时间相对更长一些。
贮焦槽的作用是贮存焦炭,其槽数及大小根据焦比和贮存时间确定,一般焦炭贮存时间在8?12h。
(2)矿槽和焦槽的形状及结构。
一般上部为正方体或长方体钢筋混凝土结构,下部为平截锥体钢筋混凝土结构或钢结构。
也有的厂矿槽和焦槽为全钢结构。
焦矿槽一般设有耐磨衬板,主要有铸铁衬板、铸钢衬板、合金衬板、陶瓷橡胶衬板、铸石衬板等。
其中,铸石衬板采用的最为广泛。
(3)原料来源及槽上运输方式。
烧结矿、球团矿、焦炭分别来自烧结厂、球团厂、焦化厂,块矿、熔剂等来自原料厂,运输方式有胶带运输机、汽车、火车和吊车等,后两者已很少见了,用胶带运输机的高炉最多。
(4)原料系统的工艺流程。
焦炭、烧结矿等原料应根据高炉炉料的配比及贮存时间的要求由皮带机等输送到焦、矿槽,焦、矿槽槽下根据高炉料批按程序组织供料,供料时,槽下给料机将炉料输送至振动筛进行筛分,合格粒度的炉料进入称量漏斗称量,返矿、返焦,由皮带或小车输送到返矿槽或返焦槽,再由皮带机或汽车运至烧结厂或焦化厂。
炉料在称量斗按料批大小进行称量后,由主供矿、供焦皮带输送至料车或主皮带,再输送至炉内。
为了节约焦炭资源,返焦一般还进行二次筛分,将5mm以上的焦丁回收利用,随烧结矿一起进入炉内,代替部分焦炭。
高炉安全生产的主要工艺过程及主要设备范本
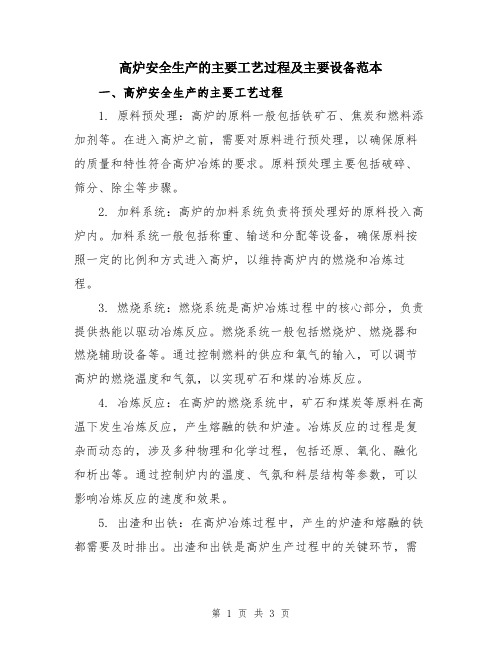
高炉安全生产的主要工艺过程及主要设备范本一、高炉安全生产的主要工艺过程1. 原料预处理:高炉的原料一般包括铁矿石、焦炭和燃料添加剂等。
在进入高炉之前,需要对原料进行预处理,以确保原料的质量和特性符合高炉冶炼的要求。
原料预处理主要包括破碎、筛分、除尘等步骤。
2. 加料系统:高炉的加料系统负责将预处理好的原料投入高炉内。
加料系统一般包括称重、输送和分配等设备,确保原料按照一定的比例和方式进入高炉,以维持高炉内的燃烧和冶炼过程。
3. 燃烧系统:燃烧系统是高炉冶炼过程中的核心部分,负责提供热能以驱动冶炼反应。
燃烧系统一般包括燃烧炉、燃烧器和燃烧辅助设备等。
通过控制燃料的供应和氧气的输入,可以调节高炉的燃烧温度和气氛,以实现矿石和煤的冶炼反应。
4. 冶炼反应:在高炉的燃烧系统中,矿石和煤炭等原料在高温下发生冶炼反应,产生熔融的铁和炉渣。
冶炼反应的过程是复杂而动态的,涉及多种物理和化学过程,包括还原、氧化、融化和析出等。
通过控制炉内的温度、气氛和料层结构等参数,可以影响冶炼反应的速度和效果。
5. 出渣和出铁:在高炉冶炼过程中,产生的炉渣和熔融的铁都需要及时排出。
出渣和出铁是高炉生产过程中的关键环节,需要确保渣铁的质量和产量。
出渣和出铁一般通过铁口和渣口来实现,需要合理设计和操作,避免堵口和漏渣等情况的发生。
6. 煤气处理:高炉冶炼过程中产生的煤气含有有害物质,需要经过处理才能排放。
煤气处理一般包括除尘、脱硫和脱氮等步骤,以确保煤气排放符合环保要求。
7. 高炉维修和维护:高炉作为一个复杂的工业设备,需要定期进行维修和维护,以确保其正常运行和安全生产。
高炉维修和维护包括设备检修、零部件更换和热态试车等活动,需要严格按照操作规程进行,遵守相关安全规定。
二、高炉安全生产的主要设备范本1. 筛分设备:筛分设备用于对原料进行筛分,以去除杂质和调整原料的粒度分布。
常用的筛分设备包括振动筛、旋振筛和鼓式筛等。
2. 称重设备:称重设备用于对原料和产物进行称重,以确保原料的配比和产物的质量。
高炉安全生产的主要工艺过程及主要设备

高炉安全生产的主要工艺过程及主要设备高炉是冶金行业中常见的设备,用于生产铁水。
在高炉的安全生产中,主要涉及到以下工艺过程和设备:1. 原料处理:高炉的主要原料是铁矿石、焦炭和石灰石。
原料处理的工艺过程包括原料破碎、磁选除铁、称重计量等。
主要设备有颚式破碎机、磁选机、传送带等。
2. 炉缸预热:高炉开始生产前,需要对炉缸进行预热。
预热过程中,将燃料逐渐加热升温,避免炉缸在燃烧过程中发生热应力破裂。
主要设备有空气预热炉、燃烧器等。
3. 喷吹燃料:高炉的燃料是焦炭,通过喷吹装置将焦炭喷吹到炉缸中。
燃料的喷吹需要保持稳定的压力和流量,以提供足够的热量和还原气体,并避免喷吹过程中产生爆炸。
主要设备有喷吹系统、压缩机等。
4. 还原反应:高炉的主要作用是将铁矿石还原为铁。
还原反应发生在高炉的炉缸中,需要维持适当的温度、还原气体和矿石料层厚度,以提供良好的还原条件。
主要设备有炉缸、砖衬等。
5. 炉渣处理:高炉生产过程中会产生大量的炉渣,包括硅酸盐炉渣、钙镁炉渣等。
炉渣处理的工艺过程包括炉渣剧烈奔腾、渣铁分离、炉渣浸出等。
主要设备有炉渣奔腾装置、炉渣运输设备、炉渣浸出槽等。
6. 照管系统:在高炉生产过程中,需要对关键参数进行监测和控制,以确保安全生产。
照管系统包括温度、压力、流量、含氧量等的监测和控制系统。
主要设备有温度计、压力计、流量计、氧气分析仪等。
7. 环保设备:高炉生产过程中会产生大量的烟气和炉渣,其中含有大量的有害物质,需要进行处理。
环保设备包括除尘器、废气处理装置等,用于过滤和净化烟气,减少对环境的污染。
除上述主要工艺过程和设备外,高炉安全生产还涉及到煤气发生炉、制气设备、蒸汽锅炉、水处理装置等辅助设备。
高炉安全生产的关键是严格按照操作规程,确保设备的正常运行和安全维护,防止意外事故的发生。
同时,还需要加强培训和监督,提高员工的安全意识和操作能力。
高炉自动化系统技术方案

高炉自动化系统技术方案
一、系统组成
1、系统结构:高炉自动化系统由管理系统、传输系统、报警系统、
模块系统以及网络系统组成,其中管理系统是整个自动化系统的核心,用
于实现数据的采集、传输,管理系统由一台监控机、一台打印机组成;传
输系统负责高炉的数据采集、处理以及计算;报警系统是为保证高炉的生
产安全而设置的;网络系统建立与其他计算机系统之间的连接,实现测控
数据的远程检测和维护;模块系统负责高炉的控制及监控。
2、软件系统:软件系统包括高级语言编程控制系统、数据处理系统、报警系统、监控系统以及模拟系统。
高级语言编程控制系统,利用高级语
言实现对高炉的运行参数和参数控制;数据处理系统负责处理各种测量、
控制和监控数据;报警系统负责预警高炉过程参数超出设定范围;监控系
统通过可视化形式监控高炉参数;模拟系统负责进行实物的仿真模型分析。
二、系统功能
1、实时监控:高炉自动化系统能够实时监控、控制、调整高炉各参数,保证高炉的安全、稳定运行。
2、图形显示:系统可以通过图形显。
高炉炼铁操作教学-高炉附属设备各系统的构造、日常检查操作
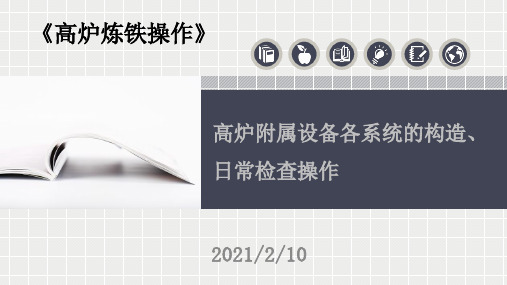
相关知识
二、高炉上料设备
相关知识
2. 闭锁装置 每个贮矿槽下设有两个漏嘴,漏嘴上装有闭锁装置,即闭锁器,其作用
是开关漏嘴,并调节料流。要求闭锁器能正确闭锁住料流,不卡不漏,而且 还应该有足够的供料能力。大型高炉漏料能力达 15-25m3/min ,目前常用 的闭锁装置有启闭器和给料机两种。
二、高炉上料设备
反排配料基本原则是远离主皮带的斗先放料,程序对烧结矿的料 头和料尾分别跟踪。
二、高炉上料设备
6. 料车坑 斜桥下端向料车供料的场所称为料车坑。
通常布置在主焦槽的下方。料车坑四壁一般由 钢筋混凝土制成。在地下水位较高地区,料车 坑的壁与底应设防水层,料车坑的底应考虑 0.5%~3% 的排水坡度。料车坑内所有设备均 应设置操作平台或检修平台。在布置设备时应 着重考虑各漏斗流嘴在漏料过程中能否准确地 漏入料车内,并应注意各设备之间的空间尺寸 关系,避免相互碰撞。
高炉槽下炉料的筛分、称量与运输操作
3. 称量斗备料操作 (1)根据料制要求选中某称量斗备料; (2)确认该称量斗空,称量斗闸门关好; (3)启动槽下的相应运矿或运焦皮带机; (4)启动相应振动筛; (5)称量斗达到预满值,停止振动筛; (6)运矿皮带停止工作时,焦丁皮带必须 停机。
任务实施
高炉槽下炉料的筛分、称量与运输操作
二、无钟炉顶设备
相关知识
并罐式无钟炉顶也有其不利的一面: (1)炉料在中心喉管内呈蛇形运动,因而造成中心喉管磨损较快。 (2)由于称量料罐中心线和高炉中心线有较大的间距,会在布料时产生料流 偏析现象,称之为并罐效应。高炉容积越大,并罐效应就越加明显。 (3)尽管并列的两个称量料罐在理论上讲可以互为备用,即在一侧出现故障 、检修时用另一侧料罐来维持正常装料,但是实际生产经验表明,由于并罐效应 的影响,单侧装料一般不能超过 6 h,否则炉内就会出现偏行,引起炉况不顺。
高炉炼铁有关知识点总结
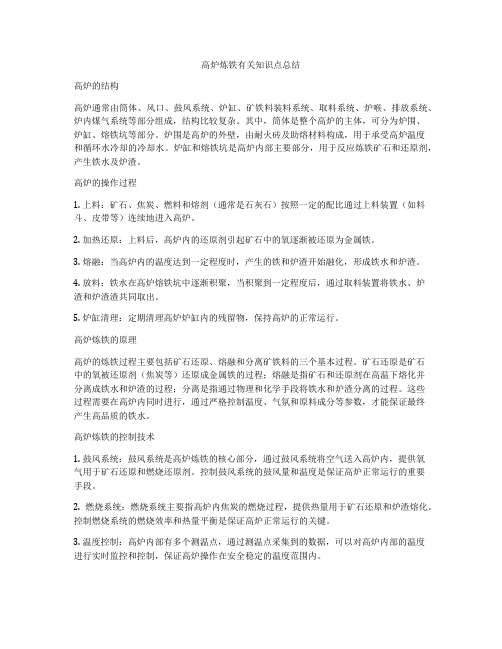
高炉炼铁有关知识点总结高炉的结构高炉通常由筒体、风口、鼓风系统、炉缸、矿铁料装料系统、取料系统、炉喉、排放系统、炉内煤气系统等部分组成,结构比较复杂。
其中,筒体是整个高炉的主体,可分为炉围、炉缸、熔铁坑等部分。
炉围是高炉的外壁,由耐火砖及助熔材料构成,用于承受高炉温度和循环水冷却的冷却水。
炉缸和熔铁坑是高炉内部主要部分,用于反应炼铁矿石和还原剂,产生铁水及炉渣。
高炉的操作过程1. 上料:矿石、焦炭、燃料和熔剂(通常是石灰石)按照一定的配比通过上料装置(如料斗、皮带等)连续地进入高炉。
2. 加热还原:上料后,高炉内的还原剂引起矿石中的氧逐渐被还原为金属铁。
3. 熔融:当高炉内的温度达到一定程度时,产生的铁和炉渣开始融化,形成铁水和炉渣。
4. 放料:铁水在高炉熔铁坑中逐渐积聚,当积聚到一定程度后,通过取料装置将铁水、炉渣和炉渣渣共同取出。
5. 炉缸清理:定期清理高炉炉缸内的残留物,保持高炉的正常运行。
高炉炼铁的原理高炉的炼铁过程主要包括矿石还原、熔融和分离矿铁料的三个基本过程。
矿石还原是矿石中的氧被还原剂(焦炭等)还原成金属铁的过程;熔融是指矿石和还原剂在高温下熔化并分离成铁水和炉渣的过程;分离是指通过物理和化学手段将铁水和炉渣分离的过程。
这些过程需要在高炉内同时进行,通过严格控制温度、气氛和原料成分等参数,才能保证最终产生高品质的铁水。
高炉炼铁的控制技术1. 鼓风系统:鼓风系统是高炉炼铁的核心部分,通过鼓风系统将空气送入高炉内,提供氧气用于矿石还原和燃烧还原剂。
控制鼓风系统的鼓风量和温度是保证高炉正常运行的重要手段。
2. 燃烧系统:燃烧系统主要指高炉内焦炭的燃烧过程,提供热量用于矿石还原和炉渣熔化。
控制燃烧系统的燃烧效率和热量平衡是保证高炉正常运行的关键。
3. 温度控制:高炉内部有多个测温点,通过测温点采集到的数据,可以对高炉内部的温度进行实时监控和控制,保证高炉操作在安全稳定的温度范围内。
4. 负压控制:通过调节高炉的负压,可以影响高炉内气氛的组成和流动状况,保证高炉内的气氛对炼铁有利。
- 1、下载文档前请自行甄别文档内容的完整性,平台不提供额外的编辑、内容补充、找答案等附加服务。
- 2、"仅部分预览"的文档,不可在线预览部分如存在完整性等问题,可反馈申请退款(可完整预览的文档不适用该条件!)。
- 3、如文档侵犯您的权益,请联系客服反馈,我们会尽快为您处理(人工客服工作时间:9:00-18:30)。
Mn、P、S ),因为在钢水中Fe最多! *转炉炼钢温度来源:铁水物理热40%,炼钢反应热60%。 *四脱二去一升温一合金化: (1)四脱:脱C、Si、Mn、P、S; (2)二去去废气、水汽【H】和【N】氮使钢老化。 (3)一升温升温加热铁水,转炉无法冶炼温度过低铁水(1250C°) (4)一合金化:在钢水中加入合金元素.
炼钢生产原料和能源来源
原料: (1)转炉:铁水(≥70%)、废钢
(≥30%) (2)电炉:铁水(≥30%)、废钢
(≤70%) 能源: (1)转炉:铁水物理热和反应化学热 (2)电炉:通过电击空气产生高压电弧产生
高温
炼钢的原材料(金属料)
金属料:铁水、废钢。 铁水:作为炼钢原料占70%以上。 对铁水的要求: 温度要求:铁水温度必须大于1250°C且要相对稳定!铁水的温度过
低,转炉炼钢的温度就低,各种化学反应无法快速发生,氧枪吹氧, 熔池的温度升高,形成泡沫渣,CO无法快速排出,积累过多,使熔 池液面上升,渣子溢出转炉,产生喷溅,主要原因是铁水的物理热占 转炉温度的40%! 对铁水的成分要求:对[P]要求铁水中含[P] ≤0.4%,P过高使钢产生 冷脆现象,使钢容易断裂,也降低了钢的焊接性能,除P的方法有: 单渣操作、双渣或双渣留渣、多次造渣。 对S,S来源于铁水和造渣材料,可以使钢产生热脆现象,对S含量要 求S≤0.07%,去除硫可以经过铁水预处理和精炼炉精炼。 对Si,大概含量范围在0.4%-0.8%。来源于铁矿石, Si含量高可以 提高废钢比,降低成本,但当Si含量过高的时候,渣量很大,使焦比 上升,易产生喷溅,对炉衬有侵害作用,减少炉龄,使冶炼时间增加
在无特殊情况下,在生产中不额外添加锰矿石,产生的MnO增
多,所需的还原剂也增加, (1)要清洁少锈无混杂,不含有色金属(Pb、Zn等)有 色金属能侵害炉衬。
(2)尺寸:最大长度不超过炉口直径二分之一,最大截 面小于炉口五分之一。
(3)分类存放:分类存放 (4)要干燥避免有水,避免有H (5)无封闭器皿或爆炸物。
金属料(铁合金)
(1)铁合金作用:脱氧剂、合金剂。 (2)种类:Si铁合金、Mn铁合金、Si-Mn合金 (3)对铁合金要求:铁合金成分要准确、块度一
般在10——40mm、使用前要进行烘烤。
高炉五大系统
*高炉五大系统:上料系统、送风系统、渣铁分离系统、废气处理系统、煤气处 理系统。
*混铁路作用:保温、均匀铁水成分及温度。 铁水主要成分:Fe、C、Si、Mn、P、S (P、S能使产生铁的冷脆和热脆。 *转炉炼钢目的:把铁水中的碳降到2.11%以下。脱出Si、Mn、P、S等有害元
素 *化学温度:通常在转炉炼钢生产中用Si的含量多少来表征铁水的温度, Si的
吹损的的贴也增加,托S、P的时间也增长了. Si的含量过小, 化学热减少,各种钢的化学反应无法进行。
对 Mn,大多数钢厂的Mn含量在0.2%-0.4%
Mn氧化后生成的MnO有化渣的作用,[化渣的物质有: MnO MnO、 FeO、CaF2、(萤石)MgO];[化渣的优点:改 善渣子的流动性,使各种化学反应容易进行,对脱S、P有好 处,还能降低氧枪的粘钢量。