催化裂化装置生产方法及基本原理
第三章_催化裂化装置
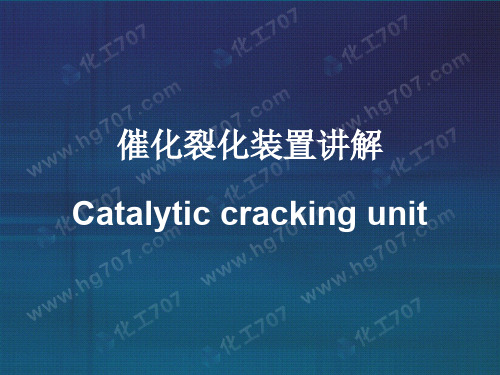
主要由吸收塔、解吸塔、再吸收塔及稳定塔组成。 吸收塔和解吸塔的操作压力为1.0~2.0MPa。 稳定塔实质上是个精馏塔,操作压力为1.0-1.5MPa。
四、能量回收系统
利用再生器出口烟气的热能和压力使余热 锅炉产生蒸汽和烟气轮机作功、发电等。
能量回收系统的工艺流程图
二、分馏系统
沉降器来的反应油气,经换热器进入分馏塔, 根据物料的沸点差,从上至下分离为富气、粗 汽油、柴油、回炼油和油浆。
分馏系统流程图
1.分馏塔底人字形挡板处用油 浆洗涤(1)防止少量催化剂细 粉堵塞塔盘和影响产品质量; (2)由于反应油气温度较高, 500℃左右,油浆洗涤可取走 多余的热量。 2.油浆:一部分回炼,一部分 回分馏塔,一部分送出装置作 自用燃料。 3富气经压缩后去吸收稳定系统 的凝缩油罐,粗汽油进吸收塔 上部。
490~510 ℃
2 ~3s
600~750 ℃
200~300 ℃
分馏系统
三、吸收—稳定系统
从分馏塔顶油气分离器出来的富气中带有汽油组分,而粗
汽油中又溶有C3、C4甚至C2组分,因此吸收稳定系统的作 用: 利用吸收和精馏的方法将富气和粗汽油分离成干气 (≤C2) 、液化气(C3、C4)和蒸汽压合格的稳定汽油。
富气经气压机升压、冷却并分出凝缩油后,由底部进入吸收塔;稳定 汽油和粗汽油则作为吸收液由塔顶进入,将富气中的C3、C4(含少量C2) 等吸收后得到富吸收油。吸收塔顶部出来的贫气中夹带有少量稳定汽油, 可经再吸收塔用柴油回收其中的汽油组分后成为干气,送出装置。 富吸收油和凝缩油均进入解吸塔,使其中的气体解吸后,从塔顶返回 凝缩油沉降罐,塔底的未稳定汽油送入稳定塔,通过精馏作用将液化气和 稳定汽油分开。有时,塔顶要排出部分不凝气(也称气态烃),它主要是 C2,并夹带有C3和C4.排出不凝气的目的是为了控制稳定塔的Ni+V:不大于 20 PPm 残碳:不大于 6% 产品分布: ★ 气体:10~20%,气体中主要是C3 、C4 ,烯烃含量很 高 ★ 汽油:产率在30~60%之间,辛烷值较高,约80~90 ★ 柴油:产率在0~40%, 十六烷值较低,需调和或精 制 ★ 油浆:产率在0~10% ★ 焦炭:产率在5%~10%,原子比大约是C:H=1:0.3~1
石油加工生产技术:催化裂化反应原理及工艺流程

二级旋风分离器 13~20m/s 7~8m/s 汽提
再生催化剂 650~700 ℃
200~℃250高低并列反应再生系统
二、分馏系统
过热油气 460~480 ℃
为了取走分馏塔的过剩热量,设有塔顶循环回流、一 个至两个中段回流以及塔底油浆循环
三、吸收解吸系统有两种流程:
双塔流程
单塔流程
双塔流程由于单塔流程,可同时满足高吸收率和高 解析率的要求。
2、三阀
单动滑阀用于床层反应器催化裂化和高低并列式提升管催化裂化装置。 其作用是:正常操作时用来调节催化剂在两器间的循环量,出现重大事故时用 以切断再生器与反应沉降器之间的联系,以防造成更大事故。
双动滑阀
双动滑阀是一种两块阀板双向动作的超灵敏调节阀,安装在再生器出口管线上 (烟囱),其作用是调节再生器的压力,使之与反应沉降器保持一定的压差。
单动滑阀结构示意图 双动滑阀结构示意图
塞阀
同轴式
塞阀用于同轴式催化 裂化装置
塞阀比滑阀具有以下优点: (1)磨损均匀而且较少; (2)高温下承受强烈磨损的部 件少; (3)安装位置较低,操作维修 方便。
(三)三机
三机包括
ห้องสมุดไป่ตู้主风机
气压机
增压机
五、催化裂化装置主要设备
(一)三器——提升管反应器、沉降器及再生器
提升管反应器
预提升:由提升 管底部吹入水蒸 气(称预提升蒸 汽),使出再生 斜管的再生催化 剂加速,以保证 催化剂与原料油 相遇时均匀接触。
沉降器
沉降器是用碳 钢焊制成的圆筒 形设备,上段为 沉降段,下段是 汽提段。
再生器
再生器的作用 是为催化剂再 生提供场所和 条件。
催化裂化反应原理及工艺流程
催化裂化的工艺特点及基本原理

教案叶蔚君5.1催化裂化的工艺特点及基本原理[引入]:先提问复习,再从我国催化裂化汽油产量所占汽油总量的比例引入本章内容。
[板书]:催化裂化一、概述1、催化裂化的定义、反应原料、反应产物、生产目的[讲述]:1.催化裂化的定义(重质油在酸性催化剂存在下,在470~530O C的温度和0.1~0.3MPa的条件下,发生一系列化学反应,转化成气体、汽油、柴油等轻质产品和焦炭的过程。
)、反应原料:重质油;(轻质油、气体和焦炭)、(轻质油);[板书]2.催化裂化在炼油厂申的地位和作用:[讲述]以汽油为例,据1988年统计,全世界每年汽油总消费量约为6.5亿吨以上,我国汽油总产量为1750万吨,从质量上看,目前各国普通级汽油一般为90-92RON、优质汽油为96-98RON,我国1988年颁布车用汽油指标有两个牌号,其研究法辛烷值分别为不低于90和97。
但是,轻质油品的来源只靠直接从原油中蒸馏取得是远远不够的。
一般原油经常减压蒸馏所提供的汽油、煤油和柴油等轻质油品仅有10-40%,如果要得到更多的轻质产品以解决供需矛盾,就必须对其余的生质馏分以及残渣油进行二次加工。
而且,直馏汽油的辛烷值太低,一般只有40-60MON,必须与二次加工汽油调合使用。
国内外常用的二次加工手段主要有热裂化、焦化、催化裂化和加氢裂化等。
而热裂化由于技术落后很少发展,而且正逐渐被淘汰,焦化只适用于加工减压渣油,加氢裂化虽然技术上先进、产品收率高、质量好、灵活性大,但设备复杂,而且需大量氢气,因此,技术经济上受到一定限制,所以,使得催化裂化在石油的二次加工过程中占居着重要地位(在各个主要二次加工工艺中居于首位)。
特别是在我国,车用汽油的组成最主要的是催化裂化汽油,约占近80%。
因此,要改善汽油质量提高辛烷值,首先需要把催化裂化汽油辛烷值提上去。
目前我国催化裂化汽油辛烷值RON偏低,必须采取措施改进工艺操作,提高催化剂质量,迅速赶上国际先进水平。
催化裂化装置

催化裂化装置催化裂化是炼油工业重要的二次加工装置,是提高轻质油收率,生产高辛烷值汽油,同时又多产柴油的重要手段,随着重油催化工艺的实现,其地位更加倍增。
作为一项传统的重油加工工艺,催化裂化实现工业化已经有60 年的历史,其总加工能力超过加氢裂化、焦化和减粘裂化之和,是目前最重要的重油轻质化工艺。
虽然曾多次受到加氢裂化工艺的竞争和清洁燃料标准的挑战,但由于催化裂化技术的进步,各种以催化裂化技术为核心的催化裂化“家族工艺”的不断出现,已经将催化裂化转变为“炼油-化工一体化”的主体装置,催化裂化仍然保持了其在石油化工行业中的重要地位。
我国的催化裂化技术与国际先进水平保持同步,进入21 世纪以后,由于我国催化裂化装置在炼厂地位的特殊性,技术发展的势头更猛,目前为止,基本解决了由于产品升级换代给催化裂化工艺带来的各种问题,而且在应对产品质量问题的技术开发过程中,拓宽了催化裂化产品的品种和范围,为确保催化裂化技术在未来石油化工中的核心地位提供了技术保证。
催化裂化装置的工艺原理是在流化状态下的催化剂作用下,重质烃类在480--520 C 及0.2-0.3MPa(a) 的条件下进行反应。
主要包括:1) . 裂解反应:大分子烃类裂解为小分子,环烷烃进行断环或侧链断裂,单环芳烃的烷基侧链断裂。
2) . 异构化反应:正构烷烃变成异构烷烃,带侧链的环烃或烷烃变成环异烷,产品中异构烃含量增加。
3) . 芳构化反应:环己烷脱氢生成芳香烃,烯烃环化脱氢生成芳烃。
4) . 氢转移反应:多环芳烃逐渐缩合成大分子直至焦炭,同时一种氢原子转移到烯烃分子中,使烯烃饱和成烷烃。
催化裂化装置的规模近三十年来逐步发展到350 万吨/年(加工1000 万吨/ 年原油)。
加工的原料为常压蜡油、减压渣油以及蜡油加氢裂化尾油原料主要性质装置由反应再生、分馏、吸收稳定(包括产品精制)、烟气能量回收几个部分组成。
装置主要产品为液化气、汽油、重石脑油和轻柴油,副产部分干气和油浆。
催化裂化工艺流程简述

催化裂化工艺流程简述催化裂化工艺是炼油工业中最重要的生产工艺之一,其主要目的是将原油分解成较小的石油产品,如汽油、柴油和石蜡等。
下面将详细介绍催化裂化工艺的流程。
首先,原油在经过预热后进入预分离器。
预分离器的作用是将原油分离成气态、液态和固态组分。
气态组分主要是轻质油气,液态组分是重油和油脂,而固态组分主要是沥青和杂质。
然后,气态组分进入催化裂化器,该装置包含了催化剂床。
催化剂是由稀土和金属组成的固体颗粒,其具有促进油品分解反应的催化作用。
气态组分在催化剂床上通过催化剂时,原油中的长链烃分子会被分解成较短的分子链。
这个过程是通过裂解反应实现的,主要是通过热裂解和催化裂解两种方式。
催化裂化的裂解反应需要一定的温度和压力条件。
通常,裂化温度在480至540摄氏度之间,压力大约在1.5至3.5兆帕之间。
此外,还需要适量的氢气作为反应介质,以提高催化裂化过程的效果。
在裂解过程中,长链烃分子被分解为较短的分子链,并产生了大量的烃气。
这些烃气通过催化裂化反应器床顶部的气体出口进入分离器,以将轻质油气和重质油气进行分离。
分离后的轻质油气进一步冷凝成液体石油产品,如汽油和柴油。
而重质油气则返回到催化裂化器进行进一步的分解。
最后,经过一系列分离、冷凝和脱硫处理的液体石油产品被收集和储存。
而废气中的硫化氢、氯化氢等有害气体会进行处理,以保护环境。
总的来说,催化裂化工艺是一种高效且经济的原油加工工艺,可以将原油转化为各种石油产品。
其具有重要的意义,可以满足社会对汽油、柴油等石油产品的需求。
通过合理控制工艺参数,优化催化剂的选择和管理,可以进一步提高催化裂化工艺的效果,实现更高的产量和更好的产品质量。
因此,催化裂化工艺在炼油工业中具有重要的应用价值。
催化裂化工艺原理
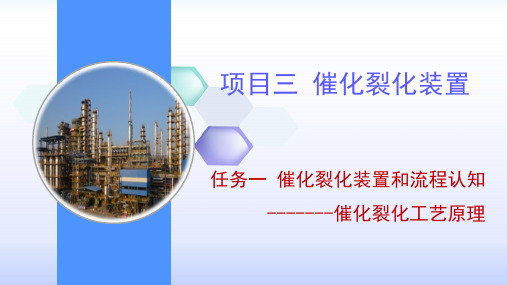
ห้องสมุดไป่ตู้
(3)氢转移反应 两个烯烃分子之间发生氢转移,变成烷烃和 二烯烃; 环烷烃或环烷-芳烃放出氢使烯烃饱和而自 身变成稠环芳烃。
8
(4)芳构化反应 烯烃环化脱氢生成芳烃。
C-C-C-C-C=C-C
CH3
9
3、环烷烃 (1)环断裂生成烯烃,烯烃继续反应; (2)长侧链断裂; (3)通过氢转移转化为芳烃;
RCH2 +
正碳离子的基本来源是由一个烯烃分子获得一
个氢离子而生成,如:
CnH2n + H+
CnH2n+1 +
12
1、正碳离子的形成
(1)烯烃与质子酸(H+)作用
RCH=CH2 + H+
+ RCHCH3
(2)芳烃与质子酸(H+)作用
+ H+
+
13
(3)烷烃在非质子酸中心脱去H-
RCH2CH2 + L
+ RCHCH2CH3
+ RC—CH3
CH3
15
正碳离子进一步异构化和β-断裂, 导致气体中C3、C4含量很高
(2)β-断裂反应
正碳离子裂解生成烯烃和碳数较少的正碳离子。
RCH2CH2CH+CH3 (3)氢转移反应
RC+H2 +CH2=CHCH3
16
17
(三)石油馏分的催化裂化反应特征
1. 各烃类的吸附竞争和对反应的阻滞作用
22
2. 复杂的平行——顺序反应
重质石油馏分 中间馏分
汽油 气体
缩合产物
焦炭
23
二、催化裂化催化剂
催化剂的作用: (1)促进化学反应,提高反应器的处理能力 催化剂能使反应活化能降低,提高反应速率,如 石油馏分的热裂化反应的活化能约为210~293kJ/mol, 而催化裂化反应其活化能降至42~125 kJ/mol,从而 大大提高反应速率。
石油催化裂化技术的原理和应用
石油催化裂化技术的原理和应用石油催化裂化技术是炼油行业中一项重要的工艺技术,它通过催化剂的作用将重质石油馏分转化为轻质产品,具有广泛的应用价值。
本文将从原理和应用两个方面来探讨石油催化裂化技术。
一、原理石油催化裂化技术的原理是通过将重质石油馏分与催化剂接触,在适宜的温度和压力条件下,进行化学反应,将长链烃转化为较短的烃链。
这一过程主要包括裂化和重整两个步骤。
裂化是指将长链烷烃分子断裂为较短的碳链烃分子,主要通过催化剂的酸性中心吸附和吸热裂化的方式进行。
在裂化过程中,催化剂的酸性中心能够提供活性吸附位,吸附长链烷烃分子,并将其断裂为较短碳链。
裂化反应生成的低碳数烷烃则被释放出来,形成轻质产品。
重整是指将低碳数烷烃进一步转化为稳定的芳烃化合物,提高汽油辛烷值。
重整反应通过催化剂的酸中心和金属中心的协同作用来进行,将低碳烷烃分子进行重排和重构,生成含有苯、甲苯和二甲苯等芳烃分子,提高汽油的辛烷值,并使其具备较高的抗爆震性能。
二、应用石油催化裂化技术在炼油行业有着广泛的应用,主要体现在以下几个方面:1. 生产高辛烷值汽油:催化裂化技术可以将重质石油馏分中的长链烷烃分子分解为较短的烷烃,使得产生的汽油具有较高的辛烷值,提高了汽油的质量和性能。
2. 产生丙烯等化工原料:催化裂化技术可以将重质石油馏分中的部分烷烃分子转化为丙烯等化工原料,具有重要的经济价值和应用前景。
3. 减少重质燃料的生产:石油催化裂化技术能够将重质石油馏分转化为轻质产品,减少了重质燃料(如柴油和燃油)的生产,从而提高了石油产品的利用效率。
4. 生产石化装置的补充燃料:催化裂化技术还可以生产具有较高热值的低碳数烷烃,作为石化装置的补充燃料,提高了整个炼油过程的能量利用效率。
总而言之,石油催化裂化技术的原理和应用具有重要的意义。
通过催化剂的作用,将重质石油馏分转化为轻质产品,既提高了石油产品的质量,又降低了能源消耗和环境污染,具有广阔的发展前景。
催化裂化装置工艺流程
催化裂化装置工艺流程
《催化裂化装置工艺流程》
催化裂化装置是石油化工行业中常见的一种重要装置,主要用于将重质石油原料加工成轻质高值产品,如汽油、柴油和航空燃料。
在催化裂化装置中,石油原料通过加热和催化剂的作用,发生分子内部的饱和碳链裂解,生成较轻的烃类产品,并产生丰富的芳烃和液化石油气。
催化裂化装置的工艺流程通常包括以下几个主要步骤:
1. 原料加热:首先,将经过预处理的重质石油原料送入加热炉中进行加热,使其达到裂化反应的最佳温度。
2. 催化裂化:加热后的石油原料进入裂化反应器,与催化剂接触,发生裂化反应。
在裂化过程中,重质烃分子会发生碳链裂解,生成较轻的烃类产品,包括汽油、柴油和液化石油气。
3. 分离和净化:裂化反应产物进入分馏塔,通过精馏、冷却和净化等步骤,将不同碳数的烃类产品进行分离,以得到所需的轻质产品。
4. 再生催化剂:随着反应的进行,催化剂会逐渐失活,需要通过再生来恢复其活性。
再生催化剂的过程包括焙烧和再活化,以保持催化剂的活性和稳定性。
以上便是催化裂化装置的基本工艺流程。
该装置能够将重质石
油原料转化为高附加值的轻质产品,对于提高石油炼制的产出和质量具有重要意义。
同时,催化裂化装置的工艺流程也在不断优化和改进,以适应不断变化的市场需求和环保要求。
催化裂化装置吸收稳定系统的原理是什么
催化裂化装置吸收稳定系统的原理是什么?催化裂化生产过程的主要产品是气体、汽油和柴油,其中气体产品包括干气和液化石油气,干气作为本装置燃料气烧掉,液化石油气是宝贵的石油化工原料和民用燃料。
所谓吸收稳定,目的在于将来自分馏部分的催化富气中C2以下组分与C3以上组分分离以便分别利用,同时将混入汽油中的少量气体烃分出,以降低汽油的蒸气压,保证符合商品规格。
吸收-稳定系统包括吸收塔、解吸塔、再吸收塔、稳定塔以及相应的冷换设备。
由分馏系统油气分离器出来的富气经气体压缩机升压后,冷却并分出凝缩油,压缩富气进入吸收塔底部,粗汽油和稳定汽油作为吸收剂由塔顶进入,吸收了C3、C4(及部分C2)的富吸收油由塔底抽出送至解吸塔顶部。
吸收塔设有一个中段回流以维持塔内较低的温度,吸收塔顶出来的贫气中尚夹带少量汽油,经再吸收塔用轻柴油回收其中的汽油组分后成为干气送燃料气管网。
吸收了汽油的轻柴油由再吸收塔底抽出返回分馏塔。
解吸塔的作用是通过加热将富吸收油中C2组分解吸出来,由塔顶引出进入中间平衡罐,塔底为脱乙烷汽油被送至稳定塔。
稳定塔的目的是将汽油中C4以下的轻烃脱除,在塔顶得到液化石油气〈简称液化气〉,塔底得到合格的汽油——稳定汽油。
吸收解吸系统有两种流程,上面介绍的是吸收塔和解吸塔分开的所谓双塔流程;还有一种单塔流程,即一个塔同时完成吸收和解吸的任务。
双塔流程优于单塔流程,它能同时满足高吸收率和高解吸率的要求。
催化裂化反应装置基本原理一、催化裂化工艺过程的特点催化裂化过程是使原料在有催化剂存在下,在470~530度和0.1~0.3兆帕的压力条件下,发生一系列化学反应,转化成气体,汽油、柴油等轻质产品和焦炭的过程。
催化裂化的原料一般是重质馏分油,例如减压馏分油(减压蜻油)和焦化馏分油等,随着催化裂化技术和催化剂工艺的不断发展,进一步扩大了催化裂化原料范围,部分或全部渣油也可作催化原料。
催化裂化过程具有以下几个特点: 1335920680(1)轻质油收率高,可达70~80%,而原油初馏的轻质油收率仅为10~40%。
催化裂化流程
催化裂化流程
催化裂化是石油炼制过程中的重要环节,它通过将长链烃分子裂解成短链烃分子,以生产更多的汽油和石脑油。
催化裂化流程主要包括进料预处理、裂化反应和产品分离三个部分。
首先是进料预处理。
在催化裂化过程中,原油经过蒸馏后得到的馏份进入预处理装置,主要目的是去除其中的硫化物、氮化物和金属杂质,以减少对催化剂的毒性和腐蚀作用。
预处理过程包括脱硫、脱氮和脱金属等步骤,通常采用加氢、吸附和萃取等方法。
接下来是裂化反应。
预处理后的馏份进入催化裂化反应器,加热至裂化温度后与催化剂接触,发生裂化反应。
在裂化反应中,长链烃分子断裂成为短链烃分子,生成大量的汽油和石脑油。
裂化反应过程需要控制反应温度、压力和催化剂的活性,以提高汽油和石脑油的产率和质量。
最后是产品分离。
裂化反应产生的混合油经过冷凝、分馏和精制等多道工艺,分离得到不同碳数范围的汽油、石脑油和其他副产物。
分离过程中需要控制温度、压力和分馏塔的进料和回流比,以保证产品的纯度和收率。
催化裂化流程的优化对提高汽油和石脑油的产率和质量至关重要。
通过改进预处理工艺、优化裂化反应条件和提高产品分离效率,可以降低能耗、减少废物排放,提高产品质量和经济效益。
总的来说,催化裂化流程是炼油工艺中的重要环节,它通过预
处理、裂化反应和产品分离三个部分,将原油转化为更多的汽油和
石脑油。
优化催化裂化流程对提高产率和质量具有重要意义,需要
综合考虑预处理、反应和分离等环节,以实现经济、高效和环保的
生产目标。
- 1、下载文档前请自行甄别文档内容的完整性,平台不提供额外的编辑、内容补充、找答案等附加服务。
- 2、"仅部分预览"的文档,不可在线预览部分如存在完整性等问题,可反馈申请退款(可完整预览的文档不适用该条件!)。
- 3、如文档侵犯您的权益,请联系客服反馈,我们会尽快为您处理(人工客服工作时间:9:00-18:30)。
单位
GB17930-2006
试验方法
93号
研究法辛烷值(RONC)
---
≥93
GB/T5487
馏程
10%温度
℃
≤70
GB/T6536
50%温度
≤120
90%温度
≤190
终馏点
≤205
残留量
%(v/v)
≤2
GB/T6536
蒸气压
11月1日~4月30日
kPa
≤88
GB/T8017
5月11日~10月30日
5. 再生压力是通过分程调节烟机入口蝶阀(PV22101C)和烟机旁路双动滑阀(PV22101A、PV22101B)、来控制的。
6. 分馏塔(T22201A、B)液位和温度选择器切换控制塔底循环泵上返塔流量调节阀来达到控制液位和温度的目的。
7. 重油分馏塔顶油气分离器(V22203A)的液位与粗轻燃油去吸收塔流量阀(FV22218)实行串级调节,保持粗轻燃油进提升管反应器流量的稳定;芳烃分馏塔顶油气分离器(V22203B)的液位与粗轻燃油去吸收塔流量阀(FV22221)实行串级调节。
水份
%(v/v)
≤痕迹
GB/T260
酸度
mgKOH/100ml
≤7
GB/T258
10%蒸余物残炭
%(m/m)
≤0.3
SH/T0170
灰分
%(m/m)
≤0.01
GB/T508
铜片腐蚀(50℃,3h)
级
≤1
GB/T5096
机械杂质
---
无
GB/T511
运动粘度(20℃)
mm2/s
3.0~8.0
GB/T265
3. 轻燃油蒸汽压的控制
轻燃油馏程中规定10%馏出温度不高于某一数值,目的是保证发动机的启动性能,但10%馏出温度过低时将导致供油系统中产生气阻现象,而此现象和轻燃油的饱和蒸汽压有密切关系,因此必须控制轻燃油的饱和蒸汽压。
本装置通过调节稳定塔压力、回流比、进料位置(稳定塔有三处进料口)以及塔底重沸器返塔温度来控制轻燃油蒸汽压,同时还需考虑到液化气携带C5的可能。
凝点
℃
0
GB/T510
冷滤点
℃
≤-5
SH/T0248
闪点(闭口)
℃
≥55
GB/T261
十六烷值
---
≥45
GB/T11139
色度
号
≤3.5
GB/T6540
氧化安定性,总不溶物
mg/100ml
≤2.5
ቤተ መጻሕፍቲ ባይዱSH/T0175
(二)船燃油质量的控制
1.船燃油凝固点的控制
船燃油凝固点是由重油分馏塔和轻燃油分馏塔第十七塔层盘上气相温度控制的,本装置船燃油凝固点控制在0℃以下。
催化裂化生产的船燃油含有较多的芳烃,十六烷值较直馏船燃油低得多,只有25个单位左右。
三、液化气质量控制
(一).液化气的质量标准:见表6-3。
表 6-3 液化气规格
2. 反应沉降器(R22101)的藏量(WRCA22101)是通过调节待生塞阀的开度来控制的。
3.再生器温度(TRCA22102/1)通过串级调节外取热器的提升风的风量(FRCA22109)来调节。
4. 反应沉降器压力正常由气压机C22301转速调节;气压机停运或压力高时可通过压缩机入口大小放火炬阀的开度大小控制。
二、船燃油的质量控制
(一).船燃油的质量标准
船燃油的规格见表6-2。
表 6-2 船燃油规格
项目
单位
企业标准
检验方法
指标
密度(20℃)
kg/m3
实测
GB/T1884或GB/T1885
馏程:50%温度
℃
≤300
GB/T6536
90%温度
≤355
干点温度
≤365
硫含量
%(m/m)
≤1.0
GB/T17040
催化裂化装置生产方法及基本原理
第一节 主要控制方案
一、主要控制方案
1. 重油提升管(R22101A)出口温度(TRCA22101A)是通过重油再生滑阀(TV22101A)调节催化剂循环量来控制的,接力管滑阀控制重油提升管起始温度;芳烃提升管(R22101B)出口温度是通过芳烃再生滑阀(TRCA22101B)调节催化剂循环量来控制的,循环立管滑阀调节轻燃油提升管起始温度。
水分
诱导期
min
≥480
GB/T8018
芳烃含量
%(v/v)
≤40
GB/T11132
烯烃含量
%(v/v)
≤35
GB/T11132
苯含量
%(v/v)
≤2.5
ASTM D3606
(二).轻燃油质量的控制
1. 轻燃油烯烃含量的控制
本装置使用双提升管技术,轻燃油进单独提升管回炼,在降低轻燃油烯烃含量和硫含量的同时增产丙烯。同时提高装置平衡催化剂活性和提高剂油比也可降低轻燃油烯烃含量。
2. 船燃油的闪点控制
船燃油的闪点通过船燃油汽提塔的液位与汽提蒸汽量来调节,高液位和大蒸汽量对控制闪点有利,蒸汽量过大,会增加汽提塔顶负荷且造成液面波动,影响操作,本装置船燃油闪点控制为≮55℃。
3.船燃油的十六烷值控制
本装置为重油催化裂化装置,原料性质较差,船燃油品质较低,主要表现在:胶质升高,油品安定性变差,颜色变深,十六烷值降低等几方面。
≤74
实际胶质
mg/100ml
≤5
GB/T509
硫含量
%(m/m)
≤0.05
GB/T17040
硫醇(满足一条即可)
博士实验
---
通过
SH/T0174
硫醇硫含量
%(m/m)
≤0.001
GB/T1792
铜腐(50℃,3h)
级
≤1
GB/T5096
水溶性酸或碱
---
无
GB/T259
机械杂质
---
无
观察后有异议按GB/T511、GB/T260测
本装置轻燃油蒸汽压夏季控制为≯67KPa,冬季控制为≯80KPa,稳定塔顶压力控制为 1.15MPa(绝)。
4. 轻燃油硫化物含量的控制
轻燃油中含有硫化氢、硫醇等活性硫化物,会使轻燃油铜片腐蚀不合格,使用这种轻燃油会严重腐蚀机器和容器,所以必须进行碱洗精制。
硫化氢和硫醇通过碱洗精制除掉,保证轻燃油硫含量合格,碱还能除掉一部分环烷酸和酚类物质。
2. 轻燃油干点的控制
轻燃油干点控制以轻燃油分馏塔顶温度为主要控制指标,通过调整顶循环、冷回流来改变塔顶温度,以达到控制轻燃油干点的目的,由于粗轻燃油干点比稳定轻燃油高,调整粗轻燃油干点使控制来得更加及时,且同样能达到控制稳定轻燃油干点的目的,因此控制粗轻燃油干点而不是稳定轻燃油干点,本装置轻燃油干点控制为198℃。
8. 气压机出口油气分离器(V22302)的液位与脱吸塔(T22302)进料量实行串级调节。
9. 稳定塔(T22304)塔顶压力实行热旁路与卡脖子相结合的方法进行调节。
10. 余热锅炉实行三冲量调节。
第二节 质量控制
一、轻燃油质量的控制
(一). 轻燃油的质量标准
轻燃油规格见表6-1。
表 6-1 轻燃油规格