玻璃熔窑结构
玻璃熔窑结构
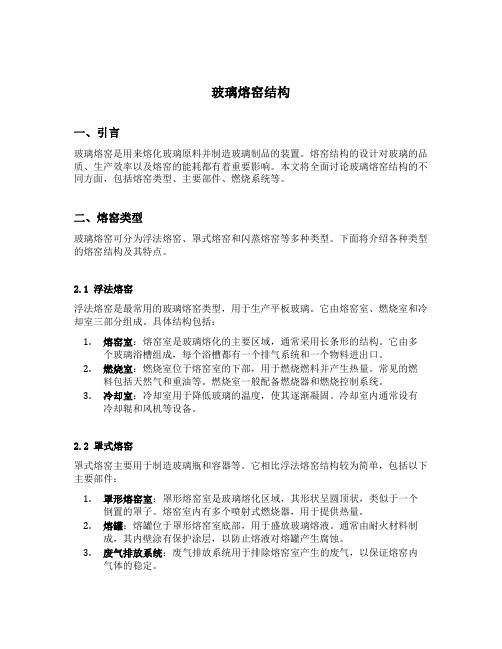
玻璃熔窑结构一、引言玻璃熔窑是用来熔化玻璃原料并制造玻璃制品的装置。
熔窑结构的设计对玻璃的品质、生产效率以及熔窑的能耗都有着重要影响。
本文将全面讨论玻璃熔窑结构的不同方面,包括熔窑类型、主要部件、燃烧系统等。
二、熔窑类型玻璃熔窑可分为浮法熔窑、罩式熔窑和闪蒸熔窑等多种类型。
下面将介绍各种类型的熔窑结构及其特点。
2.1 浮法熔窑浮法熔窑是最常用的玻璃熔窑类型,用于生产平板玻璃。
它由熔窑室、燃烧室和冷却室三部分组成。
具体结构包括:1.熔窑室:熔窑室是玻璃熔化的主要区域,通常采用长条形的结构。
它由多个玻璃浴槽组成,每个浴槽都有一个排气系统和一个物料进出口。
2.燃烧室:燃烧室位于熔窑室的下部,用于燃烧燃料并产生热量。
常见的燃料包括天然气和重油等。
燃烧室一般配备燃烧器和燃烧控制系统。
3.冷却室:冷却室用于降低玻璃的温度,使其逐渐凝固。
冷却室内通常设有冷却辊和风机等设备。
2.2 罩式熔窑罩式熔窑主要用于制造玻璃瓶和容器等。
它相比浮法熔窑结构较为简单,包括以下主要部件:1.罩形熔窑室:罩形熔窑室是玻璃熔化区域,其形状呈圆顶状,类似于一个倒置的罩子。
熔窑室内有多个喷射式燃烧器,用于提供热量。
2.熔罐:熔罐位于罩形熔窑室底部,用于盛放玻璃熔液。
通常由耐火材料制成,其内壁涂有保护涂层,以防止熔液对熔罐产生腐蚀。
3.废气排放系统:废气排放系统用于排除熔窑室产生的废气,以保证熔窑内气体的稳定。
2.3 闪蒸熔窑闪蒸熔窑是一种高温熔炼玻璃的特殊类型熔窑。
其结构相对简单,主要包括以下部件:1.熔化室:闪蒸熔窑的熔化室是玻璃熔化的主要区域。
熔化室内有多个加热电极,通过电阻加热的方式提供热量,使玻璃原料迅速熔化。
2.废气处理系统:废气处理系统用于处理熔窑室出口产生的废气,通常采用除尘和脱硫等工艺,以减少环境污染。
三、主要部件除了不同类型的熔窑有不同的结构,熔窑还包括许多常见的主要部件。
下面将介绍几个关键的部件。
3.1 熔化室熔化室是进行玻璃熔化的核心部分。
浮法玻璃熔窑的结构
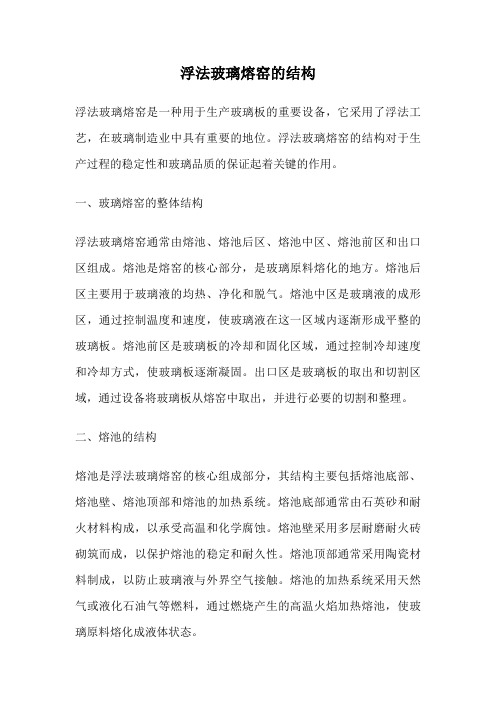
浮法玻璃熔窑的结构浮法玻璃熔窑是一种用于生产玻璃板的重要设备,它采用了浮法工艺,在玻璃制造业中具有重要的地位。
浮法玻璃熔窑的结构对于生产过程的稳定性和玻璃品质的保证起着关键的作用。
一、玻璃熔窑的整体结构浮法玻璃熔窑通常由熔池、熔池后区、熔池中区、熔池前区和出口区组成。
熔池是熔窑的核心部分,是玻璃原料熔化的地方。
熔池后区主要用于玻璃液的均热、净化和脱气。
熔池中区是玻璃液的成形区,通过控制温度和速度,使玻璃液在这一区域内逐渐形成平整的玻璃板。
熔池前区是玻璃板的冷却和固化区域,通过控制冷却速度和冷却方式,使玻璃板逐渐凝固。
出口区是玻璃板的取出和切割区域,通过设备将玻璃板从熔窑中取出,并进行必要的切割和整理。
二、熔池的结构熔池是浮法玻璃熔窑的核心组成部分,其结构主要包括熔池底部、熔池壁、熔池顶部和熔池的加热系统。
熔池底部通常由石英砂和耐火材料构成,以承受高温和化学腐蚀。
熔池壁采用多层耐磨耐火砖砌筑而成,以保护熔池的稳定和耐久性。
熔池顶部通常采用陶瓷材料制成,以防止玻璃液与外界空气接触。
熔池的加热系统采用天然气或液化石油气等燃料,通过燃烧产生的高温火焰加热熔池,使玻璃原料熔化成液体状态。
三、熔池后区的结构熔池后区是玻璃液的均热、净化和脱气区域,其结构主要包括流道、均热区和净化区。
流道位于熔池后区的最上方,用于将熔池中的玻璃液引导至熔池后区。
均热区通过控制温度和搅拌玻璃液,使其达到均匀的温度和成分分布。
净化区通过添加特定的化学物质,去除玻璃液中的气泡和杂质,提高玻璃品质。
熔池后区的结构设计合理,能够实现玻璃液的均热、净化和脱气,为后续工序提供高质量的玻璃液。
四、熔池中区的结构熔池中区是玻璃液的成形区域,通过控制温度和速度,使玻璃液在这一区域内逐渐形成平整的玻璃板。
熔池中区的结构主要包括成形辊、支撑辊和冷却辊。
成形辊用于控制玻璃液的流动和形状,使其逐渐成形为平整的玻璃板。
支撑辊用于支撑和稳定玻璃板,以避免其变形或破裂。
第三节玻璃熔窑投料口和山墙钢结构

—
看 ,投 料池 立柱 布置 形式 大体 可分 为两 类 :其一 是
左 右两 侧 每侧 只设 一 根立 柱 ,这根 立柱 同时承 担 以
图1 全窑 宽投 料池 平 面布 置的左侧局 部 图 5
投 料 口立 柱受 力分 析 :全窑 宽投 料池 每侧 只设
一
其 中最 主要 的受 力为第 一种 功能 ,即夹持纵 向 的熔 窑 胸墙 、保 证小 炉喷 火 口碹 结构稳 定 的力 ,其它 夏
知识讲座 专题
第 三节
玻 璃熔 窑投 料 口和 山墙 钢结构
浮法 玻璃熔 窑 的熔 化部 和冷却 部 共有 四个 山墙
结构 :熔 化 部前 I 墙 、后 …墙 ,冷 却部 前 【 墙 、后 j I L I 山 墙 。熔 化 部 前 山墙 钢 结 构 即 投料 口钢 结 构 ,包 括 :投 料 口 柱 、投料 口前端 拦铁 和侧壁挡 铁等 。
要求 r,为了增加横 向稳定性 而增加一块腹板 ,为双
( 3)柱顶拉 条拉力
=
竿
5 0 ×4 0 0 00 0 0
68 0 0
腹板结构 ( 见全窑宽投料池平面布置的左侧局部 )。 ( )立柱挠 度计算 8
, 一
=
3 0 k 00 0( g)
J 一 48 EI 5 0 ×68 00 0 0
=
第1 期
总第2 4 4 期
②对应 每个小炉 中心距 的熔 化部大碹重 量
( 2 中心角时 ,取 大碹 的弧长 =1 8 5。 . 碹跨 ) 0
G =1 8 ( 。 ,) p .B D 0 +D , L 。
10 16X ( .5×19+02X11) ×35 .8X 1 . 0 . . . .
玻璃窑炉结构及窑炉用耐火材料性能.

5、热源供给:蓄热室
1)用途:蓄热室是利用耐火材料做蓄热体 (称为格子体)蓄积从窑内排出烟气的部分 热量,用来加热进入窑内的助燃空气 ---这样不但可以利用烟气余热,而且使得助燃 空气加热到较高温度,有利于提高作业温度; ---同时还起到把窑内废气排出及助燃空气 进入的通道;
2)蓄热室是什么结构和材质? 蓄热室是由前、后墙、隔墙及蓄热室内格子体组成, 使用温度分为上部为1200~1500℃,中部为 800~1200℃,下部为<800℃: a.蓄热室碹(砖厚350mm,外有3*64mm保温砖),其使 用条件为粉料的飞散,高温的温度变化,氧化还原反应, 材质为优质硅砖; b.蓄热室目标墙(砖厚350mm,外有146 的粘土砖及 178mm保温砖)其使用条件同蓄热室碹,材质为 AZS33#锆刚玉砖或高纯电熔镁砖; c.主墙和隔墙:上部(砖厚350mm),使用条件同蓄热室 碹,材质为优质硅砖;中部(砖厚230mm),使用条 件为中温的温度变化,材质为高铝砖或镁质砖;下部 (砖厚350mm),使用条件为低温的温度变化,材质 为低气孔粘土砖。 d.底部炉条碹,使用条件同下部格子砖,材质为低气孔率
卡脖出 口矮碹 卡脖吊 平碹 熔化部 大碹 卡脖入口 J形吊墙
卡脖池底
卡脖大 水包
池壁
2)玻璃液分隔装置有卡脖、冷却水包、窑坎等: ---卡脖是熔化部和冷却部之间的一段缩窄窑池,与 矮碹、吊墙配合使用,对熔化部和冷却部之间的 气体空间及玻璃液起分隔作用,从而降低玻璃液 的温度; ---冷却水管是由一组通过冷却水的圆形或方形钢管 组成,水管高度根据实用确定。冷却水管附近的 玻璃液受冷却后,形成粘度较大的不动层,构成 一道挡墙、降温作用大,不但可以阻挡未熔化的 浮渣进入冷却部,而且通过调节水管的沉入深度, 可以控制进入冷却部玻璃液的质量; ---窑坎,是斜坡式分隔能阻挡玻璃液的对流,窑的 纵向有多个窑坎,如澄清带,进入卡脖及进入工 作部前端均可设置窑坎。
全氧燃烧玻璃熔窑的结构和应用第一章概述
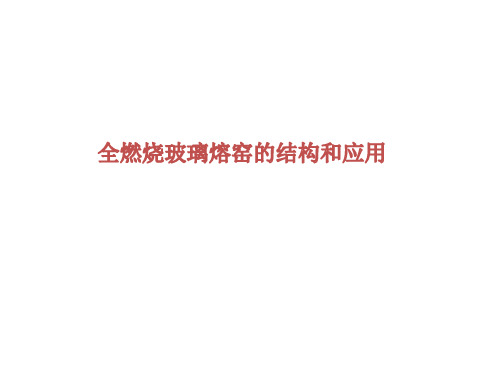
(8) 天然气/氧气预热技术。 可以通过利用废气余热把天然气和氧气预热到400℃以上进行燃烧, 在普通全氧窑炉的基础上还能再节约 5-10%能耗。 (9)热化学蓄热技术。 利用废气中 H2O、CO2与 燃料CH4热裂解反应生成CO和H2,然后再进 入窑炉内燃烧。相当于给燃料预热,同时提高火焰辐射能力。
1、概述
1.2 全氧燃烧技术的基本原理
纯氧燃烧技术最早主要被应用于增产、延长窑炉使用寿命以及减少 NOx排放,但随着制氧技术的发展以及电力成本的相对稳定,纯氧燃烧 技术正在成为取代常规空气助燃的更好选择,这得益于纯氧燃烧技术在 节能、环保、质量、投资等方面的优势。
对于日用玻璃和建材行业,以前多采用低热值燃料如发生炉煤气,由 于燃料本身含有大量N2和CO2,用它做全氧窑炉燃料时节能减排效果大 打折扣,同时由于燃料成本低廉,节省的燃料费用难以抵消氧气的制备 费用,因此很少采用全氧燃烧技术。当前环保要求玻璃窑炉采用清洁燃 料天然气,由于天然气成本居高不下,采用全氧燃烧窑炉的优势越来越 明显。
1、概述
表1光伏压延玻璃全氧燃烧和空气燃烧的窑炉对比(燃料为天然气)
1、概述
1.2 全氧燃烧技术的基本原理
在玻璃熔制过程中所需要的热量主要是通过燃料和氧气在高温下进行 燃烧反应而获得,传统的燃料燃烧反应所需要的氧气是从空气中获得, 这样大量的氮气被无谓地加热,并在高温下排入大气,同时,氮气在高 温下还与氧气反应生成NOx,NOx气体排入大气层极易形成酸雨造成环境 污染。甲烷的燃烧反应: 空气-燃料:CH4+2O2+8N2→2H2O+CO2+8N2 每Mcal热需1.97Nm3空气 氧气-燃料:CH4+2O2 →2H2O+CO2 每Mcal热需0.22Nm3氧气
玻璃熔融工艺

玻璃熔融工艺一、玻璃熔窑的类型、结构及特点按照熔窑的生产能力可分为坩埚窑和池窑。
1.坩埚窑坩埚窑是指在坩埚中熔化玻璃的一种间歇式作业的玻璃熔窑。
其结构主要包括作业室、喷火筒(小炉)、燃烧室、漏料坑、蓄热室等部分。
在作业室内安放8~12只坩埚(要求特殊的玻璃也有仅置放一只坩埚进行熔制)。
配合料可分3~5批加入到各坩埚中。
当配合料在坩埚中完成熔制、澄清和冷却过程后即可进行成型。
在成型结束后,又再重新分批加入配合料,进行下一循环的熔制周期。
坩埚窑的熔制周期从第一次加料开始到此坩埚料成型结束,一般为一昼夜。
对难熔的玻璃也可适当地延长熔制时间,但这样会对其他坩埚的熔制、澄清和成型带来影响。
坩埚窑占地、投资少,同一窑内可熔制多种不同组成或不同颜色的玻璃,生产灵活性大,适用于生产品种多、产量少、质量要求较高或有特殊工艺要求的玻璃。
对要求高温熔制、低温成型的硒硫化镉类着色的玻璃,或低价铁着色类的玻璃尤为合适。
但坩埚窑的生产能力低、燃料消耗大,难以实现机械化和自动化生产。
坩埚窑按废气余热回收设备分为蓄热室和换热器两种;按火焰在窑内的流动方向分为倒焰式、平焰式、联合火焰式;按坩蜗数量分为单坩埚窑、双坩埚窑和多坩埚窑;按燃料品种区分有全煤气、半煤气和燃油坩埚窑等。
以下选取4种坩埚窑进行介绍。
(1)蓄热室坩埚窑采用蓄热室作为废气余热回收设备的坩埚窑。
(2)换热室坩埚窑采用换热器作为废气余热回收设备的坩埚窑。
(3)倒焰式坩埚窑窑内火焰呈倒转流动的坩埚窑。
火焰由位于窑底的喷火口向上喷出,然后沿着坩埚自上向下经窑底吸火孔排出。
其特点是温度沿整个坩埚高度分布比较均匀,上下温差小,由于火焰自窑底排出,窑底部温度较高,因而使窑底和坩埚都容易损坏,限制了窑内温度的提高。
图 2.5(a)为倒焰式坩埚窑示意图。
倒焰式坩埚窑可以配置换热器,也可配置蓄热室。
(4)平焰式坩埚窑图2.5(b)所示为窑内火焰呈水平方向流动的坩埚窑。
火焰在坩埚上部流动,可以提高火焰温度,加强传热过程,有利于提高熔化率。
第五节玻璃熔窑小炉钢结构
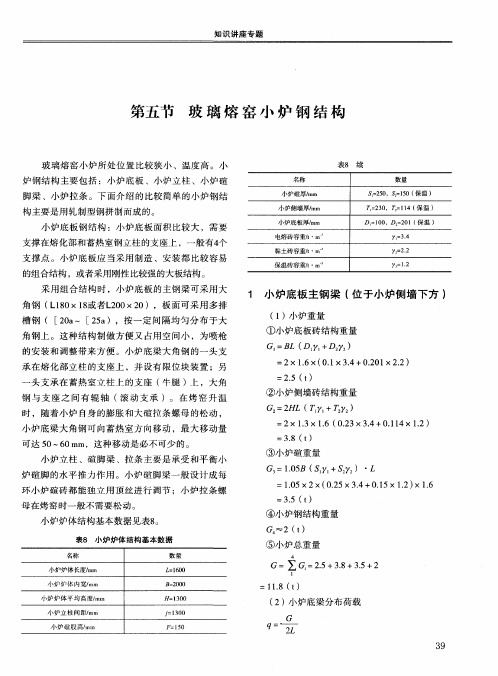
=
2×13×16( .3×34+0 1 4×12) . . 02 . .1 . 38( ) . t
=
小 炉立 柱 、碹 脚 梁 、拉 条 主要 是承 受和平 衡 小 炉 碹 脚 的水 平 推 力作用 。小 炉碹 脚梁 一般 设计 成 每
环 小 炉碹砖 都 能独 立用 顶丝 进行 凋节 ;小炉拉 条 螺
y= . 34 y= . 222 y= . ,1 2
支 撑点 。小 炉底 板应 当采用制 造 、安装 都 比较 容易
的组 合结构 ,或者采用刚性 比较强 的大板结构 。
保温砖容重/ ・ tm
采用组 合 结构 时 ,小炉底 板 的主钢 梁 可采用 大
角 钢 ( l0 8 L 8 ×1 或者 L 0 ×2 2 0 0),板 面 可采 用多 排
P =k , .5 4 = 0 k ) , r =11 ×5 5 65 0( g P 6
=
1 84 0( g・ m ) 1 0 k e
( )小炉底梁需要抗 弯模量 4
=
⑤ 小炉立 楗受力 图
l 84 0 l 0
l4 0 0
l j I
=
8 c 5( m )
=
的 安装 和调 整带来 方 便 。小炉 底梁 大角 钢 的一头 支
承在 熔化 部立 柱 的支 座上 ,并 没有 限位 块装 置 ;另
一
2 .×( .×34 .0 .) ×1 6 01 . +02 1 22 X
25 ( ) . t
头 支 承在 蓄热 室立 柱上 的支 座 ( 牛腿 ) E,大 角
知 识 讲 座 专 题
第五节
玻 璃 熔 窑 小 炉 钢 结 构
玻璃熔窑设计-2---副本
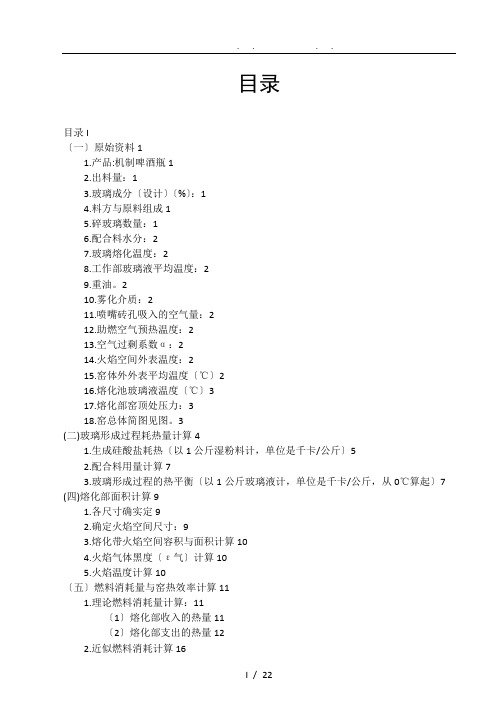
目录目录I〔一〕原始资料11.产品:机制啤酒瓶12.出料量:13.玻璃成分〔设计〕〔%〕:14.料方与原料组成15.碎玻璃数量:16.配合料水分:27.玻璃熔化温度:28.工作部玻璃液平均温度:29.重油。
210.雾化介质:211.喷嘴砖孔吸入的空气量:212.助燃空气预热温度:213.空气过剩系数α:214.火焰空间外表温度:215.窑体外外表平均温度〔℃〕216.熔化池玻璃液温度〔℃〕317.熔化部窑顶处压力:318.窑总体简图见图。
3(二)玻璃形成过程耗热量计算41.生成硅酸盐耗热〔以1公斤湿粉料计,单位是千卡/公斤〕52.配合料用量计算73.玻璃形成过程的热平衡〔以1公斤玻璃液计,单位是千卡/公斤,从0℃算起〕7(四)熔化部面积计算91.各尺寸确实定92.确定火焰空间尺寸:93.熔化带火焰空间容积与面积计算104.火焰气体黑度〔ε气〕计算105.火焰温度计算10〔五〕燃料消耗量与窑热效率计算111.理论燃料消耗量计算:11〔1〕熔化部收入的热量11〔2〕熔化部支出的热量122.近似燃料消耗计算163.实际燃烧消耗量计算164.列熔化部热平衡表165.熔化部热负荷值,单位耗热量与窑热效率计算〔按实际耗油量〕17 〔六〕蓄热室受热外表计算17〔七〕排烟系统阻力计算181.局部阻力计算列下表182.摩擦阻力计算列表:193.蓄热室几何压头计算:20〔八〕烟囱计算201.烟囱高度〔H〕计算202.烟囱出口直径〔D〕计算:20〔一〕原始资料1.产品:翠绿料2.出料量:每天熔化玻璃135吨。
3.玻璃成分〔设计〕〔%〕:4.料方与原料组成5.碎玻璃数量:占配合料量的50%。
6.配合料水分:靠石英砂和纯碱的外加水分带入,不另加水。
7.玻璃熔化温度:1400℃。
8.工作部玻璃液平均温度:1300℃。
9.重油。
10.雾化介质:用压缩空气,预热到120℃,用量为0.6标米3/公斤油。
11.喷嘴砖孔吸入的空气量:0.5标米3/公斤油。
- 1、下载文档前请自行甄别文档内容的完整性,平台不提供额外的编辑、内容补充、找答案等附加服务。
- 2、"仅部分预览"的文档,不可在线预览部分如存在完整性等问题,可反馈申请退款(可完整预览的文档不适用该条件!)。
- 3、如文档侵犯您的权益,请联系客服反馈,我们会尽快为您处理(人工客服工作时间:9:00-18:30)。
玻璃熔窑结构
一、引言
玻璃是一种常用的建筑材料,它广泛应用于建筑、家居、工业制品等领域。
而玻璃的生产离不开熔窑,熔窑的结构对于玻璃的生产效率和品质起着至关重要的作用。
本文将详细介绍玻璃熔窑的结构。
二、玻璃熔窑基本概念
1. 玻璃熔窑定义
玻璃熔窑是指将原材料(如二氧化硅、碳酸钠等)在高温下融合成液态玻璃的设备。
2. 玻璃成分
玻璃主要由硅酸盐和金属氧化物组成,其中硅酸盐占主导地位。
常见的硅酸盐有二氧化硅、三氧化二铝等,常见的金属氧化物有钙、镁、铝等。
3. 玻璃制备过程
将原材料放入玻璃窑中进行加热,使其融化成液态玻璃。
然后通过调节温度和时间来控制玻璃的成分和性质。
三、玻璃熔窑结构
1. 熔窑本体
熔窑本体是指玻璃熔化的主要区域,通常由炉壳、内衬和保温层组成。
内衬一般采用耐火材料,如高铝砖、硅酸铝板等。
保温层则使用耐高
温绝缘材料,如氧化铝纤维毯等。
2. 燃料系统
燃料系统是指为加热玻璃提供能量的设备,通常由锅炉、风机、管道
和喷嘴等组成。
常见的燃料有天然气、重油和液化气等。
3. 玻璃出口
玻璃出口是指将液态玻璃从窑中排出的设备。
通常由出口管道和出口
机构组成。
出口机构一般采用液压或电动方式控制。
4. 风冷系统
风冷系统是指为降低玻璃温度而设置的设备,通常由风机、散热器和
管道等组成。
通过将冷却空气吹入窑内来降低玻璃温度。
5. 玻璃搅拌系统
玻璃搅拌系统是指为保证玻璃成分均匀而设置的设备,通常由电机、
减速器和搅拌器等组成。
通过搅拌器将液态玻璃搅拌均匀。
四、玻璃熔窑运行过程
1. 加料
将原材料放入窑内,开始加热。
2. 熔化
当温度达到一定程度时,原材料开始融化成液态玻璃。
3. 调温
通过调节火力和风冷系统来控制窑内温度,以保证玻璃质量和生产效率。
4. 出口
当液态玻璃达到一定浓度时,通过出口机构将其排出。
五、总结
本文详细介绍了玻璃熔窑的结构和运行过程。
在实际生产中,需要根据不同的需求和使用环境来选择合适的设备,并加强维护保养工作,以确保生产效率和产品质量。