球团回转窑轮技术方案
回转窑设计方案手册

回转窑的设计一、窑型和长径比1.窑型所谓窑型是指筒体各段直径的变化。
按筒体形状有以下几种窑型:(1)直筒型:制造安装方便,物料在窑内移动速度较均匀一致,操作控制较易掌握,同时窑体砌造及维护较方便;(2)热端扩大型:加大单位时间内燃烧的燃料量及传热量,在原窑直径偏小的情况下,扩大热端将相应提高产量,适用于烧成温度高的物料;(3)冷端扩大型:便于安装热交换器,增大干燥受热面,加速料浆水分蒸发,降低热耗及细尘飞损,适用于处理蒸发量大、烘干困难的物料;(4)两端扩大型(哑铃型):中间的填充系数提高,使物料流动的机会减少,还可以节约部分钢材;还有单独扩大烧成带或分解带的“大肚窑”,这种窑型易挂窑皮,在干燥带及烧成带能力足够时,可以显著提高产量。
但这种窑型操作不便。
总之,不论扩大哪一带,必须保持预烧能力和烧结能力趋于平衡。
只有在生产窑上,经过生产实践和充分调查研究(包括必要的热工测定和计算),发现某一带确为热工上的薄弱环节,在这种特定条件下将该带扩大,才会得出较明显的效果。
目前国内外发展趋势仍以直筒型窑为主,而且尺寸向大型方面发展。
其他有色金属工业用回转窑(还原、挥发、硫化精矿焙烧、氯化焙烧、离析、烧结转化等)多采用较短的直筒窑。
2.长径比要得长径比有两种表示方法:一是筒体长度L与筒体公称直径D之比;另一是筒体长度L与窑的平均有效直径D均之比。
L/D便于计算,L/D均反映要的热工特点更加确切,为了区别起见,称L/D均为有效长径比。
窑的长径比是根据窑的用途、喂料方式及加热方法来确定的。
根据我国生产实践的不完全统计,各类窑的长径比示于表1中。
长径比太大,窑尾废气温度低,蒸发预热能力降低,对干燥不利;长径比太小,则窑尾温度高,热效率低。
同类窑的长径比与窑的规格有关,小窑取下限,大窑取上限。
表1各类窑的长径比窑的名称公称长径比有效长径比氧化铝熟料窑(喷入法)20~2522~27氧化铝焙烧窑20~2321.5~24碳素煅烧窑13.5~1917~24干法和半干法水泥窑11~15——湿法水泥窑30~42——单筒冷却机8~12——铅锌挥发窑14~1716.7~18.3铜离析窑——15~16氯化焙烧窑——12~17.7二、回转窑的生产率回转窑生产是一个综合热工过程,其生产率受多方面因素影响。
球团链蓖机回转窑机技术标doc
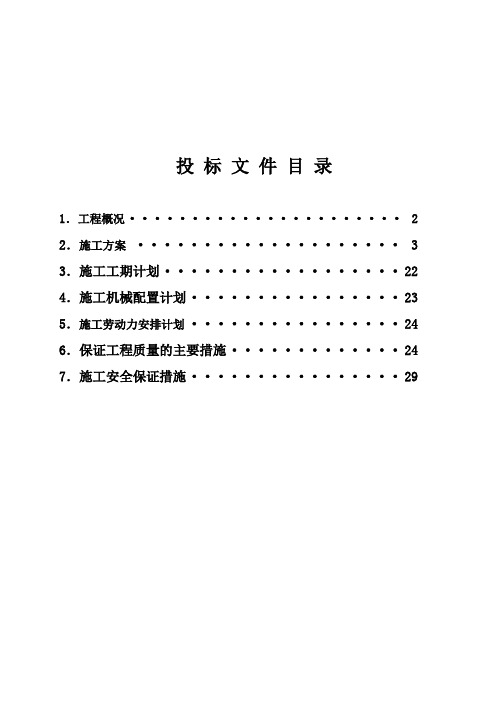
投标文件目录1.工程概况 (2)2.施工方案 (3)3.施工工期计划 (22)4.施工机械配置计划 (23)5.施工劳动力安排计划 (24)6.保证工程质量的主要措施 (24)7.施工安全保证措施 (29)1.工程概况本工程为矿业公司新建一条200万吨球团厂生产线。
本标段机械专业主要工程内容有:(1)链篦机1台,总重1000吨;(2)辊式布料机1台,重16吨;(3)各种胶带输送机9台,总重67.5吨;(4)斗式提升机(D=400,L=24m) 1台, 重5.4吨;(5)散料拉链机 1台,重9吨;(6)C D5~20D电动葫芦1台,重0.8吨;(7)Q=5吨电动单梁悬挂式起重机1台,重4.5吨;(8)波汶膨胀器1台,重20吨;(9)回转窑(Φ6.1m,L=40m)1台,总重1065吨;(10)冷却风机Q=35052m3/h ,1台, 重1.75吨;(11)卸灰阀 1台, 重0.8吨;(12)卸料阀 1台, 重0.8吨;(13)钢结构(支架、漏斗等)安装,120吨;(14)热风管道制安:250吨;(15)给排水管道安装:14吨;(16)采暖管道安装:2.4吨;设备总重:2200吨。
2.施工方案:2.1链篦机安装(1)安装程序链篦机是烧结系统的主体设备,它是由很多系统部件组成的联合机组。
安装于主厂房内多层平台间,链篦机总重1000t,其安装程序如下:基础测量及垫板研放→机架→下托轮→风箱→头、尾轮→上托轮→传动装置→链篦装置(台车)→干燥及预热段钢结构→稀油润滑→冷却水系统→检修平台→其它附属设备安装。
设备安装吊装头尾部设备(包括宽胶带机、摆动胶带机、辊式布料机等)采用厂房内5t电动葫芦吊装,中间段设备可在17.2m平台上沿链篦机纵向横跨C—D柱列制安一台10t电动葫芦门型吊,利用门型吊进行设备吊装,其它部位设备吊装可利用卷扬机及链式起重机配合笨力吊装。
(2)链篦机设备中心线标板、标高基准点埋设与基础测量a.在施工中,对于中心标板及标高基准点的埋设工作应引起施工人员的特别注意,因为它是衡量设备空间坐标的唯一的相对依据。
回转窑方案
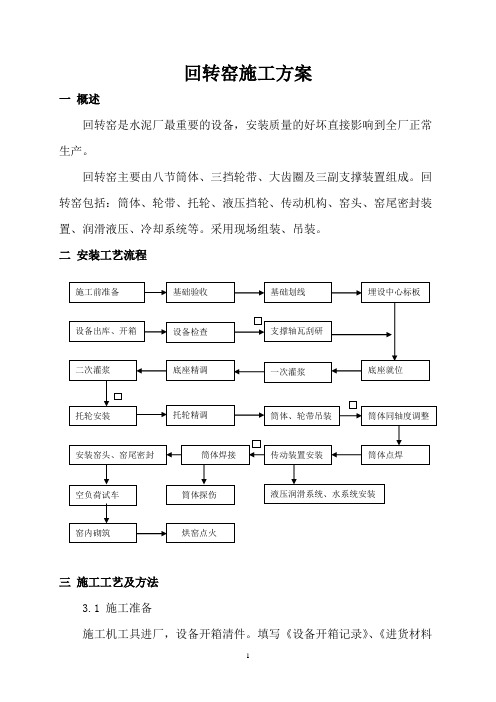
回转窑施工方案一概述回转窑是水泥厂最重要的设备,安装质量的好坏直接影响到全厂正常生产。
回转窑主要由八节筒体、三挡轮带、大齿圈及三副支撑装置组成。
回转窑包括:筒体、轮带、托轮、液压挡轮、传动机构、窑头、窑尾密封装置、润滑液压、冷却系统等。
采用现场组装、吊装。
二安装工艺流程三施工工艺及方法3.1 施工准备施工机工具进厂,设备开箱清件。
填写《设备开箱记录》、《进货材料验证记录》。
搭建临时设施,为施工作好准备。
3.2基础验收与划线设备安装前,混凝土基础应验收,验收合格后,方能进行安装。
提交的基础,必须达到下列要求:所有遗留的模板和露出混凝土外的钢筋,必须清除,并将设备安装现场及地脚孔内碎料、赃物及积水全部清理干净。
3.3埋设标板3.3.1中心标板在基础两端每条中心线上,便于安装找正的部位各埋设一块标板。
标板采用200×100×6-10mm的钢板制作。
用膨胀螺栓固定,钢板上用红油漆标出中心线。
3.3.2标高标板在每个窑墩的四角均埋设用作沉降标志的标高板。
采用φ15mm圆钢与80×80×10mm钢板焊接而且其圆顶顶呈半圆形。
埋设件必须埋设牢固,每个窑敦4个标高点在同一标高上,误差不大于0.5mm。
3.3.3在窑头、窑尾厂房内也各设置1个标高点,用于监测基础的沉降。
3.3.4划出回转窑的纵横中心线相邻两基础横向中心线间距允许偏差不大于±1.5mm。
首尾两基础横向中心线间距允许偏差不大于±6mm。
横向中心线的检查,采用对角线测量法,其目的不会产生平行四边形,减小误差,保证安装质量。
在放线时,钢卷尺应与弹簧秤配合使用,使钢盘尺受到相同张力,减少挠度的影响。
根据厂区标准水准点,测出基础上面基准点标高,作为安装设备的基准点,其偏差≤±1mm。
定期检查混凝土基础下沉情况。
在所有偏差均达到要求之后,所有预埋标板上打上样冲眼并作明显标记,成为永久性标记。
大型球团回转窑吊装、焊接施工工法2
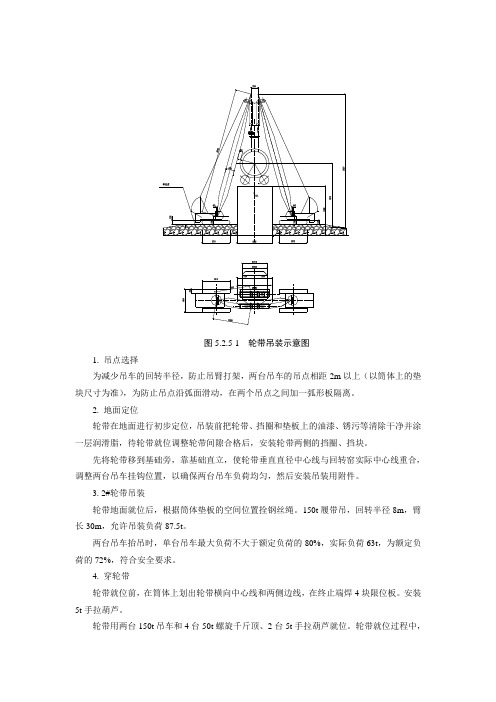
图5.2.5-1 轮带吊装示意图1. 吊点选择为减少吊车的回转半径,防止吊臂打架,两台吊车的吊点相距2m以上(以筒体上的垫块尺寸为准),为防止吊点沿弧面滑动,在两个吊点之间加一弧形板隔离。
2. 地面定位轮带在地面进行初步定位,吊装前把轮带、挡圈和垫板上的油漆、锈污等清除干净并涂一层润滑脂,待轮带就位调整轮带间隙合格后,安装轮带两侧的挡圈、挡块。
先将轮带移到基础旁,靠基础直立,使轮带垂直直径中心线与回转窑实际中心线重合,调整两台吊车挂钩位置,以确保两台吊车负荷均匀,然后安装吊装用附件。
3. 2#轮带吊装轮带地面就位后,根据筒体垫板的空间位置拴钢丝绳。
150t履带吊,回转半径8m,臂长30m,允许吊装负荷87.5t。
两台吊车抬吊时,单台吊车最大负荷不大于额定负荷的80%,实际负荷63t,为额定负荷的72%,符合安全要求。
4. 穿轮带轮带就位前,在筒体上划出轮带横向中心线和两侧边线,在终止端焊4块限位板。
安装5t手拉葫芦。
轮带用两台150t吊车和4台50t螺旋千斤顶、2台5t手拉葫芦就位。
轮带就位过程中,两个5t手拉葫芦控制移动进度,千斤顶倒换顶动,确保两边进度一致。
轮带就位后,松开千斤顶,轮带缓慢落放在托轮上,安装轮带附件,焊接垫板。
5.2.6传动装置吊装本台窑为双边驱动,干、稀油润滑。
因传动部基础施工较晚,因此在筒体焊接完毕后,再进行传动装置的安装。
传动部安装均用150t吊车吊装。
5.2.7电动机吊装电动机在地面清洗、检查,作电气试验后吊装。
5.2.8其它部件吊装其它部件主要包括:窑头、窑尾密封,点火喷煤系统,大齿轮罩,液压挡轮装置等。
这类部件重量较轻,但因安装位置高,吊车回转半径大,150t吊车尚在现场,故都用150t吊车吊装。
5.2.9回转窑焊接回转窑直径Φ6.858m,长45.72m,筒体壁厚为130/70/40mm,材质为Q345C。
回转窑的焊接时间在2005年9月,自然条件对焊接十分有利。
回转窑操作方案
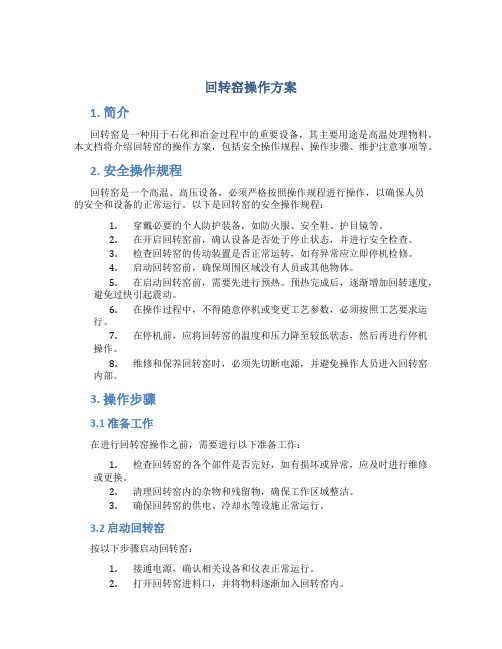
回转窑操作方案1. 简介回转窑是一种用于石化和冶金过程中的重要设备,其主要用途是高温处理物料。
本文档将介绍回转窑的操作方案,包括安全操作规程、操作步骤、维护注意事项等。
2. 安全操作规程回转窑是一个高温、高压设备,必须严格按照操作规程进行操作,以确保人员的安全和设备的正常运行。
以下是回转窑的安全操作规程:1.穿戴必要的个人防护装备,如防火服、安全鞋、护目镜等。
2.在开启回转窑前,确认设备是否处于停止状态,并进行安全检查。
3.检查回转窑的传动装置是否正常运转,如有异常应立即停机检修。
4.启动回转窑前,确保周围区域没有人员或其他物体。
5.在启动回转窑前,需要先进行预热。
预热完成后,逐渐增加回转速度,避免过快引起震动。
6.在操作过程中,不得随意停机或变更工艺参数,必须按照工艺要求运行。
7.在停机前,应将回转窑的温度和压力降至较低状态,然后再进行停机操作。
8.维修和保养回转窑时,必须先切断电源,并避免操作人员进入回转窑内部。
3. 操作步骤3.1 准备工作在进行回转窑操作之前,需要进行以下准备工作:1.检查回转窑的各个部件是否完好,如有损坏或异常,应及时进行维修或更换。
2.清理回转窑内的杂物和残留物,确保工作区域整洁。
3.确保回转窑的供电、冷却水等设施正常运行。
3.2 启动回转窑按以下步骤启动回转窑:1.接通电源,确认相关设备和仪表正常运行。
2.打开回转窑进料口,并将物料逐渐加入回转窑内。
3.启动回转窑的传动装置,逐渐增加回转速度,使物料均匀分布在回转窑内。
4.确保物料在回转过程中可以受到均匀的加热。
3.3 停止回转窑按以下步骤停止回转窑的运行:1.逐渐降低回转窑的回转速度,使其停止运转。
2.关闭回转窑的进料口,停止物料的供给。
3.关闭回转窑的传动装置,并切断电源。
4. 维护注意事项为确保回转窑的正常运行和延长其使用寿命,需要注意以下维护事项:1.定期对回转窑进行清洁,清除内部和外部的积尘和杂物。
2.检查回转窑的传动装置和电气设备,如有异常及时维修或更换。
浅析球团回转窑的设计与开发

浅 析 球 团 回转 窑 的设 计 与 开发
赫 禹 岳 ,
摘
悦 陆 朋 牟红 , ,
(. 1 北方重工集团有限公 司 矿 山冶金设备分公司 , 辽宁沈 阳 10 4 ;. 1 122 沈阳东北大学冶金技术研究所有限公司 , 辽宁沈阳 10 0 10 4)
要: 浅析 了球 团回转窑 的发展历程 、 工作原理 , 重点介绍 了球 团回转窑 的筒 体部 、 动装置 、 传 一
为 防 止窑 头 窑 尾 处 简 体表 面 过 热 , 响裙 片密 影 封性 能 , 窑头 、 尾 简 体 与裙 片 密封 附近 , 设 有 在 窑 均 风冷 式结 构 冷却 装置 。 此装 置 为一 管 环 状 焊接 件 包 在 筒体 上 , 环两 在
式 中 p—— 窑衬 密度 , 。 单位 k/ gm ; D —— 筒体 内经 , 位 m 单 m; h —— 衬 层厚 度 , 位 m 单 m。 4 14 物料 单位 长度 载荷 .. 物料 单位 长度 载荷
度 = 0 ; 3 。 ’
M= 号1 e + - 。一 (+) e F
4 2 5 支座 处的轴 向弯 曲应 力 ..
G— —轮 带质 量 ,g 3 7 g k 。G =1020k ; r 重力 加速 度 。g 9 8m s; = . /。 B—— 轮带 宽度 , m; m E—— 轮带 材料 的 弹性 模 量 , a =22× MP 。E 0
窑 尾 密 封罩 用 于 回转 窑 和链 篦 机 的联结 , 内设
耐火 衬 , 带有 观 察 门和 检 修 门 。窑 头 密 封 罩用 于 回 转 窑与 环冷 机 的联 结 , 内设 耐火 衬 , 有 喷煤 枪 口、 带 观察 孔 和检 修 门 。回转 窑 中的氧 化球 团在 罩 内经 过 固定 筛分 分 后 , 到 环 冷 机 的受 矿 漏 斗 。罩 上 还带 给 有 回热风 口并与 回热 风管 道 相联 。 为 保 证 密封 性 能 , 窑头 窑 尾 密封 罩 与 筒 体 的 密 封采 用裙 片式 密 封 。裙 片 密 封 的 特 点是 结 构 简 单 、
回转窑窑体串动调整方法及注意事项
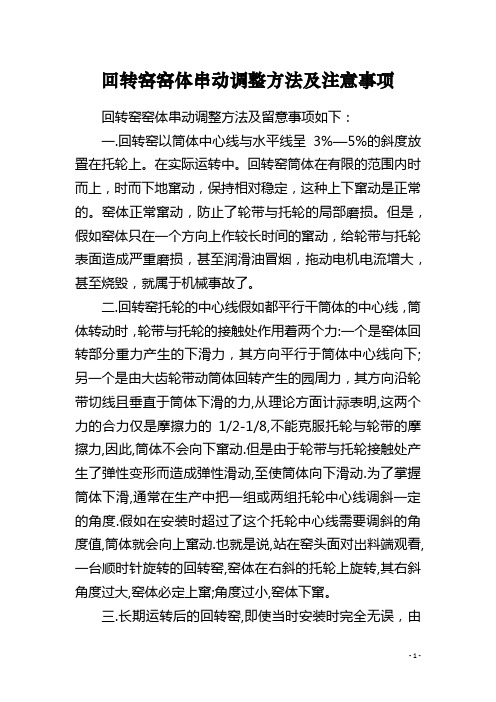
回转窑窑体串动调整方法及注意事项回转窑窑体串动调整方法及留意事项如下:一.回转窑以筒体中心线与水平线呈3%—5%的斜度放置在托轮上。
在实际运转中。
回转窑筒体在有限的范围内时而上,时而下地窜动,保持相对稳定,这种上下窜动是正常的。
窑体正常窜动,防止了轮带与托轮的局部磨损。
但是,假如窑体只在一个方向上作较长时间的窜动,给轮带与托轮表面造成严重磨损,甚至润滑油冒烟,拖动电机电流增大,甚至烧毁,就属于机械事故了。
二.回转窑托轮的中心线假如都平行干筒体的中心线,筒体转动时,轮带与托轮的接触处作用着两个力:一个是窑体回转部分重力产生的下滑力,其方向平行于筒体中心线向下;另一个是由大齿轮带动筒体回转产生的园周力,其方向沿轮带切线且垂直于筒体下滑的力,从理论方面计祘表明,这两个力的合力仅是摩擦力的1/2-1/8,不能克服托轮与轮带的摩擦力,因此,筒体不会向下窜动.但是由于轮带与托轮接触处产生了弹性变形而造成弹性滑动,至使筒体向下滑动.为了掌握筒体下滑,通常在生产中把一组或两组托轮中心线调斜一定的角度.假如在安装时超过了这个托轮中心线需要调斜的角度值,筒体就会向上窜动.也就是说,站在窑头面对岀料端观看,一台顺时针旋转的回转窑,窑体在右斜的托轮上旋转,其右斜角度过大,窑体必定上窜;角度过小,窑体下窜。
三.长期运转后的回转窑,即使当时安装时完全无误,由于基础沉降状况不一样,筒体弯曲和轮带与托轮不圴匀磨损,特殊是由于轮带与托轮接触之间的摩察系数的变化,使窑体只在一亇方向上作长时间窜动,必定会引起回转窑筒体的上或下窜动超出极限值。
四.当一组托轮两侧的斜度相反,即将托轮摆置成正八字或倒八字时,斜度相反就会产生相反方向的摩察力,俗称抱闸作用,这时如不准时调整,就会使轴承单侧受力,局部摩察加剧,又会导致润滑油冒烟,拖动电机电流增大甚至绕坏的恶性事故。
五.回转窑筒体只在一个方向上作长时间窜动时,必需进行调整。
⑴转变轮带与托轮表面摩察系数。
回转窑技术操作规程(10)

QB 攀钢集团钢城企业总公司球团厂企业标准QJ/QT 5.010—2004 回转窑技术操作规程2004-11-20发布2004-12-20实施攀钢集团钢城企业总公司球团厂发布前言为了规范焙—环岗位的操作,确保焙烧球团质量,特制定本规程。
本规程由攀钢集团钢城企业总公司球团厂提出。
本规程由攀钢集团钢城企业总公司球团厂归口。
本规程由攀钢集团钢城企业总公司球团厂起草。
本规程主要起草人:王宾、任朝成本规程主要审核人: 覃金平、王宾本规程主要批准人: 何焕江本规程为首次发布。
回转窑技术操作规程1、范围本规程规定了攀钢集团钢城企业总公司球团厂回转窑的技术操作要求。
本规程适用于攀钢集团钢城企业总公司球团厂焙—环岗位。
2、岗位职责2.1、2.2、熟悉本岗位所属设备的性能及操作方法,负责所属设备日常维护、保养工作。
2.3、严格执行烘炉、转窑、停窑及焦炉煤气点火、停火操作制度。
2.4、负责提出本岗位所属设备的缺陷、隐患及要求检修项目;发生事故要及时处理并报告主控室,参加检修后试车验收工作。
2.5、做好本岗位操作原始记录。
2.6、2.7、负责本岗位设备及周围环境的清扫,搞好安全文明生产。
3、设备工艺参数3.1、回转窑总体参数3.1.1、回转窑直径:Φ5.0m(公称)3.1.2、回转窑长度:35m3.1.3、处理物料:酸性氧化球团3.1.4、工作温度:950~1300℃3.1.5、生产能力:165~202 t/h3.1.6、物料堆比重:2.0 t/m33.1.7、斜度:4.25%3.1.8、填充率:7.6%3.1.9、回转窑转速:0.3~1.3 r/min正常:1.0 r/min辅助:0.1 r/min3.1.10、回转窑有效容积:520 m33.1.11、物料焙烧时间:30~35min3.1.12、窑容利用系数:7t/ m3.D3.2、传动装置传动形式:液压驱动3.2.1、液压驱动装置3.2.1.1、液压马达:型号:MB560输出扭矩:144.396 KN.m最大输出扭矩:198.1 KN.m输出转速:0~12.5 r /min数量:23.2.1.2、传动主液压系统:3.2.1.2.1、液压泵:型号:P24S最大输出流量:592L/min×2工作压力:35 Mpa3.2.1.2.2、电机:型号:M2CA 315MB功率:160 KW×2转速:1485 r/min3.2.1.2.3、传动辅液压系统:3.2.1.2.3.1、液压泵:型号:P6S最大输出流量:144 L/min×2工作压力:35 Mpa3.2.1.2.3.2、电机:型号:M2AA 250SMA功率:55 KW转速:1475 r/min3.2.2、齿轮传动装置3.2.2.1、传动齿轮:模数:36mm速比:i=202/21=9.6193.3、支承装置3.3.1、轮带与筒体的连接形式:轮带为活套式,采用浮动垫板与筒体之间摩擦传力。
- 1、下载文档前请自行甄别文档内容的完整性,平台不提供额外的编辑、内容补充、找答案等附加服务。
- 2、"仅部分预览"的文档,不可在线预览部分如存在完整性等问题,可反馈申请退款(可完整预览的文档不适用该条件!)。
- 3、如文档侵犯您的权益,请联系客服反馈,我们会尽快为您处理(人工客服工作时间:9:00-18:30)。
球团回转窑轮带垫板磨损分析及更换技术方案
一、回转窑垫板更换的理论依据
二、回转窑轮带垫板更换技术方案
三、需要准备的备件
2012年3月
一、回转窑轮带垫板更换的理论依据
球团回转窑轮带以及垫板磨损之后间隙过大在耐火材料方面导致窑内耐火砖的松动、碎裂、脱落;在机械方面会造成轮带裂纹、窑体裂纹、回转窑偏心旋转、轴瓦温度高等不良后果。
根据贵公司现场照片,结合以下理论依据,建议利用停机时间及时更换垫板,以免造成不应有的经济损失。
●球团回转窑的轮带与垫板之间的冷态下设计预留间隙为
8mm,是考虑筒体温度高,膨胀量大;窑转速高,线速度大;窑重力负荷大,磨损快而预留的间隙;因此筒体在轮带里活动的空间相对较大。
当轮带两边筒体出现较大温差的时候,温度高的一边筒体则刚度下降,挠度增加,下垂的筒体与轮带的接触面随之增大,而轮带另一端的接触面则相对变小,轮带两端与托轮的接触面发生变化,造成托轮两边轴瓦受力不均而引起发热。
●轮带间隙最简单点的检测方式为:测出筒体与轮带的相对滑移量ΔS,再用公式ΔS/π计算便得出轮带间隙。
一般ΔS为5-15mm属正常值范围,大于或小于该范围应引起警觉。
ΔS≤5mm则表明可能会发生轮带将筒体抱死现象,严重时使筒体产生缩颈,引起窑内耐火砖松动,甚至掉落;在ΔS>15mm,若筒体温度在正常范围内,则表明可继续运行一段时间;若此时筒体温度过高,则应考虑添加或更换垫板,使间隙恢复到正常范围。
●在检查垫板的磨损情况的同时,应重视对该部位的润滑。
采用喷射专用高温固体润滑剂或石墨块嵌入方式润滑摩擦部位可有效缓
解磨损,提高轮带和垫板的使用周期。
使用嵌入石墨块方法时,为了不影响筒体散热,石墨块放置应间隔2-3个空挡,石墨块的两端在筒体或垫板上焊上挡板,可防止石墨块从端部滑落。
石墨块随窑的转动在轮带内圈不断地摩擦,将石墨粉附着在轮带内圈上,润滑效果很好,一年更换一次,费用比采用喷射专用高温固体润滑剂要少得多。
●窑检修期间当垫板处于可换可不换时,应该更换,切不可忽视而因小失大。
在这种情况下往往耐火材料的龄期不一定会跟垫板磨损的限期相吻合,到时不可能因轮带间隙过大而停止正常的生产来更换垫板。
类似的实例很多,如某生产线的回转窑上,中间挡轮带与垫板间隙在设备大检修时,由于检修计划工作量大,轮带间隙处于垫板可换可不换的情况下,没有被列入检修计划之中,结果在大修完两个域左右发生重大事故,造成严重损失。
事故发生过程是:由于间隙大,轮呆在垫板上长时间的轴向移动形成轴向冲击力,导致部分挡块先后被顶掉,轮带向下窜动20cm左右,托轮受力状态失衡,轴瓦开始发热。
事发为夜班之时,轴瓦温度升高时才发现轮带已经移位,此时应当停窑,将轮带复位后才能继续生产。
然而在处理中采取了寄希望于通过调动托轮,让托轮对轮带形成的轴向发作用力将轮带复位。
然事与愿违,此时忽略了。