钢管防腐施工工艺
钢管防腐施工方法

1、钢管外壁:无机富锌底漆,干膜厚度80μm;超厚浆型环氧沥青漆(面层)干膜厚度250μm;2、钢管内壁:超厚浆型环氧沥青底漆干膜厚度250μm;超厚浆型环氧沥青面漆干膜厚度250μm。
1、钢材表面防腐前,必须进行表面预处理。
在预处理前,钢材表面的焊渣、毛刺、油脂等污物清除干净;2、表面预处理质量,符合施工图纸的规定。
若施工图纸未规定,且钢管内壁及明管外壁采用涂料或金属喷涂时,除锈等级达到《涂装前钢材表面锈蚀等级和除锈等级》GB8923- 1988 规定的Sa2 级;埋管外壁采用喷涂水泥浆时,达到Sal 级;3 、预处理后,表面粗糙度达到:(1)常规涂料40~70μm;(2)厚浆重涂料、金属热喷涂60~100μm;4、表面预处理使用无尘、洁净、干燥、有棱角的铁砂喷射处理钢板表面。
喷射用的压缩空气经过过滤,除去油、水;5、当钢材表面温度低于露点以上塑、相对湿度高于85%时,不得进行表面预处理;6、喷刷后的表面不再与人手等物体接触,防止再度污染。
施喷涂料前,使用钢刷和真空吸尘器清除残留砂粒等杂物。
作业人员带纤维手套。
若不慎用手触及己清理好的表面,立即用溶剂清洗钢管表面。
1、一般要求(1)施涂前,根据施工图纸要求和涂料生产厂的规定进行工艺试验。
试验过程中有涂料生产制造厂的人员负责指导。
试验成果提交监理人;(2)组焊后的管节、岔管及附件(除安装焊缝外),在车间内完成防腐;现场安装焊缝及表面防腐损坏部位在现场进行防腐;(3) 清理后的钢材表面在潮湿气候条件下,涂料在4h 内防腐完成,金属喷涂在2h 内完成;在晴天和正常大气条件下,涂料防腐时间最长不超过12h,金属喷涂时间不超过8h;(4)防腐材料的使用按施工图纸及涂料生产制造厂的说明书进行。
防腐材料品种以及防腐层数、厚度、间隔时间、调配方法等严格按厂家要求执行;(5)当空气中相对湿度超过85%、钢材表面温度低于大气露点3℃以及产品说明书规定的不利环境时,均不得进行防腐;(6)钢管防腐其他技术要求遵守《水电水利工程金属结构设备防腐蚀技术规程》DL/T5358-2006 的有关规定。
管道工程钢管除锈、防腐方法
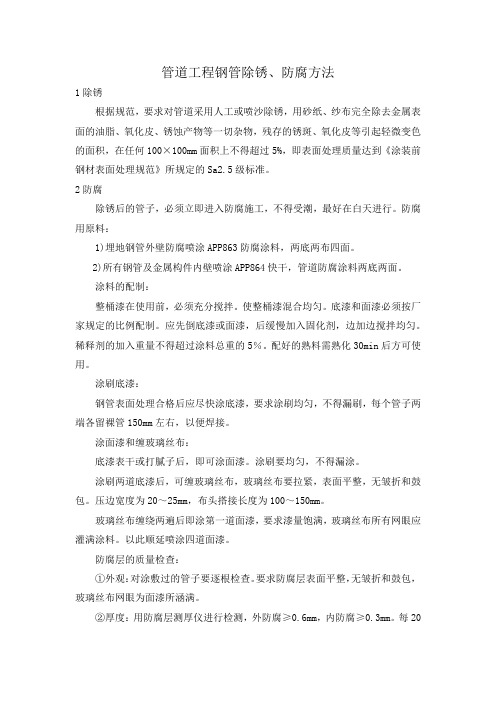
管道工程钢管除锈、防腐方法1除锈根据规范,要求对管道采用人工或喷沙除锈,用砂纸、纱布完全除去金属表面的油脂、氧化皮、锈蚀产物等一切杂物,残存的锈斑、氧化皮等引起轻微变色的面积,在任何100×100mm面积上不得超过5%,即表面处理质量达到《涂装前钢材表面处理规范》所规定的Sa2.5级标准。
2防腐除锈后的管子,必须立即进入防腐施工,不得受潮,最好在白天进行。
防腐用原料:1)埋地钢管外壁防腐喷涂APP863防腐涂料,两底两布四面。
2)所有钢管及金属构件内壁喷涂APP864快干,管道防腐涂料两底两面。
涂料的配制:整桶漆在使用前,必须充分搅拌。
使整桶漆混合均匀。
底漆和面漆必须按厂家规定的比例配制。
应先倒底漆或面漆,后缓慢加入固化剂,边加边搅拌均匀。
稀释剂的加入重量不得超过涂料总重的5%。
配好的熟料需熟化30min后方可使用。
涂刷底漆:钢管表面处理合格后应尽快涂底漆,要求涂刷均匀,不得漏刷,每个管子两端各留裸管150mm左右,以便焊接。
涂面漆和缠玻璃丝布:底漆表干或打腻子后,即可涂面漆。
涂刷要均匀,不得漏涂。
涂刷两道底漆后,可缠玻璃丝布,玻璃丝布要拉紧,表面平整,无皱折和鼓包。
压边宽度为20~25mm,布头搭接长度为100~150mm。
玻璃丝布缠绕两遍后即涂第一道面漆,要求漆量饱满,玻璃丝布所有网眼应灌满涂料。
以此顺延喷涂四道面漆。
防腐层的质量检查:①外观:对涂敷过的管子要逐根检查。
要求防腐层表面平整,无皱折和鼓包,玻璃丝布网眼为面漆所涵满。
②厚度:用防腐层测厚仪进行检测,外防腐≥0.6mm,内防腐≥0.3mm。
每20根管抽查1根。
每根测三个相隔一定距离的截面,每截面测上、下、左、右四点,如最薄点低于规定厚度,则为不合格,再抽查2根,其中l根仍不合格时,全部不合格。
③针孔:用5000V电火花检漏仪检测,以不打火花为合格。
每20根抽查l 根。
④粘附力:防腐层固化后(一般需7天),用小刀割开长形切口,用力撕切口处的防腐层,以不易撕开及破坏处管面仍为漆膜所覆盖而不露铁为合格,每20根管抽查l根。
镀锌钢管防腐施工工艺流程

镀锌钢管防腐施工工艺流程
镀锌钢管防腐施工工艺流程:
①施工准备:确保施工现场整洁,无杂物阻碍,准备施工所需工具和材料。
②材料检验:检查镀锌钢管的壁厚、镀锌层完整性和无损伤,确认其符合施工要求。
③清洗钢管:彻底清洗钢管表面,去除油污、锈迹、灰尘等杂质,保证表面干净。
④表面处理:使用砂纸或打磨机对钢管表面进行打磨,增加涂料的附着力。
⑤底漆涂覆:在清洁干燥的钢管表面上均匀涂覆一层底漆,确保无漏涂和流挂。
⑥干燥固化:让底漆自然干燥或使用加热设备加速固化过程。
⑦面漆涂覆:在底漆完全固化后,涂覆第一层面漆,确保涂层均匀。
⑧多层面漆:根据防腐等级要求,继续涂覆后续层面漆,每层之间需干燥固化。
⑨增强层处理:对于加强级和特加强级防腐,涂覆面漆后加贴玻璃布增强层,再涂面漆。
⑩最终面漆:完成所有增强层后,涂覆最后一层面漆,形成完整防腐层。
⑪质量检查:对防腐层进行外观检查,确保无气泡、针孔、裂缝等缺陷。
⑫固化保养:让最终的防腐层充分固化,期间避免物理损伤。
⑬验收:防腐施工完成后,进行质量验收,确保达到设计要求和规范标准。
钢管防腐工艺流程
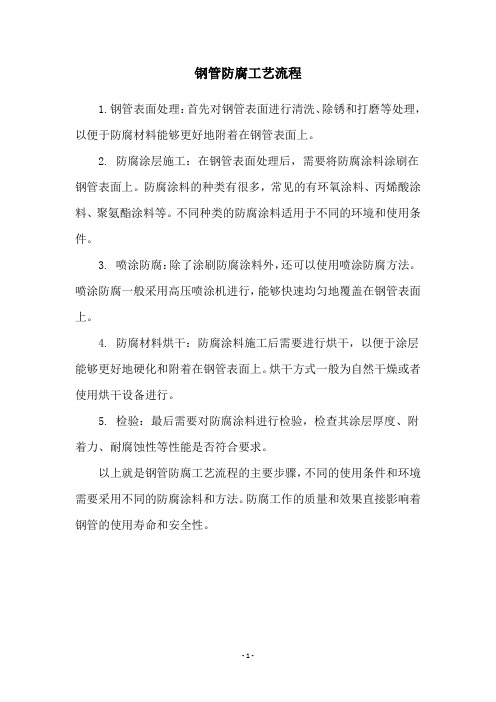
钢管防腐工艺流程
1.钢管表面处理:首先对钢管表面进行清洗、除锈和打磨等处理,以便于防腐材料能够更好地附着在钢管表面上。
2. 防腐涂层施工:在钢管表面处理后,需要将防腐涂料涂刷在钢管表面上。
防腐涂料的种类有很多,常见的有环氧涂料、丙烯酸涂料、聚氨酯涂料等。
不同种类的防腐涂料适用于不同的环境和使用条件。
3. 喷涂防腐:除了涂刷防腐涂料外,还可以使用喷涂防腐方法。
喷涂防腐一般采用高压喷涂机进行,能够快速均匀地覆盖在钢管表面上。
4. 防腐材料烘干:防腐涂料施工后需要进行烘干,以便于涂层能够更好地硬化和附着在钢管表面上。
烘干方式一般为自然干燥或者使用烘干设备进行。
5. 检验:最后需要对防腐涂料进行检验,检查其涂层厚度、附着力、耐腐蚀性等性能是否符合要求。
以上就是钢管防腐工艺流程的主要步骤,不同的使用条件和环境需要采用不同的防腐涂料和方法。
防腐工作的质量和效果直接影响着钢管的使用寿命和安全性。
- 1 -。
钢管防腐方法
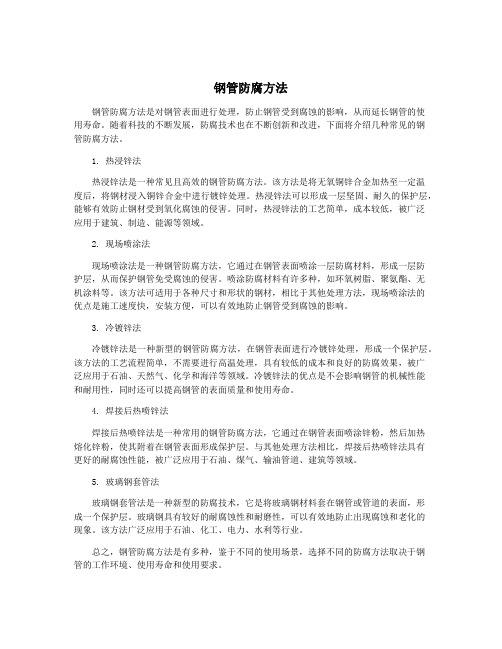
钢管防腐方法钢管防腐方法是对钢管表面进行处理,防止钢管受到腐蚀的影响,从而延长钢管的使用寿命。
随着科技的不断发展,防腐技术也在不断创新和改进,下面将介绍几种常见的钢管防腐方法。
1. 热浸锌法热浸锌法是一种常见且高效的钢管防腐方法。
该方法是将无氧铜锌合金加热至一定温度后,将钢材浸入铜锌合金中进行镀锌处理。
热浸锌法可以形成一层坚固、耐久的保护层,能够有效防止钢材受到氧化腐蚀的侵害。
同时,热浸锌法的工艺简单,成本较低,被广泛应用于建筑、制造、能源等领域。
2. 现场喷涂法现场喷涂法是一种钢管防腐方法,它通过在钢管表面喷涂一层防腐材料,形成一层防护层,从而保护钢管免受腐蚀的侵害。
喷涂防腐材料有许多种,如环氧树脂、聚氨酯、无机涂料等。
该方法可适用于各种尺寸和形状的钢材,相比于其他处理方法,现场喷涂法的优点是施工速度快,安装方便,可以有效地防止钢管受到腐蚀的影响。
3. 冷镀锌法冷镀锌法是一种新型的钢管防腐方法,在钢管表面进行冷镀锌处理,形成一个保护层。
该方法的工艺流程简单,不需要进行高温处理,具有较低的成本和良好的防腐效果,被广泛应用于石油、天然气、化学和海洋等领域。
冷镀锌法的优点是不会影响钢管的机械性能和耐用性,同时还可以提高钢管的表面质量和使用寿命。
4. 焊接后热喷锌法焊接后热喷锌法是一种常用的钢管防腐方法,它通过在钢管表面喷涂锌粉,然后加热熔化锌粉,使其附着在钢管表面形成保护层。
与其他处理方法相比,焊接后热喷锌法具有更好的耐腐蚀性能,被广泛应用于石油、煤气、输油管道、建筑等领域。
5. 玻璃钢套管法玻璃钢套管法是一种新型的防腐技术,它是将玻璃钢材料套在钢管或管道的表面,形成一个保护层。
玻璃钢具有较好的耐腐蚀性和耐磨性,可以有效地防止出现腐蚀和老化的现象。
该方法广泛应用于石油、化工、电力、水利等行业。
总之,钢管防腐方法是有多种,鉴于不同的使用场景,选择不同的防腐方法取决于钢管的工作环境、使用寿命和使用要求。
钢管防腐施工方案
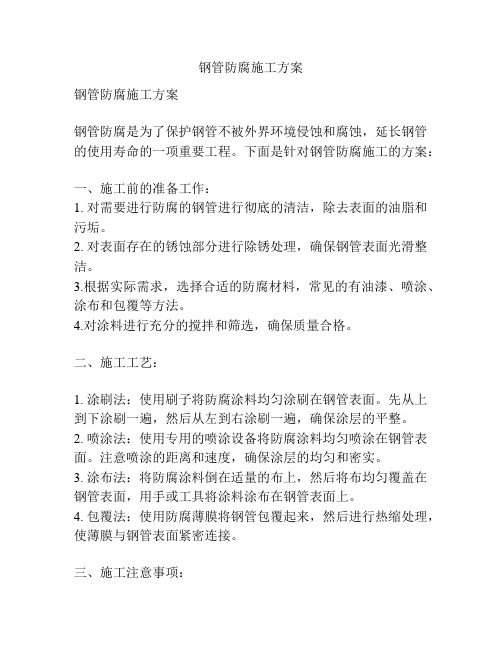
钢管防腐施工方案
钢管防腐施工方案
钢管防腐是为了保护钢管不被外界环境侵蚀和腐蚀,延长钢管的使用寿命的一项重要工程。
下面是针对钢管防腐施工的方案:
一、施工前的准备工作:
1. 对需要进行防腐的钢管进行彻底的清洁,除去表面的油脂和污垢。
2. 对表面存在的锈蚀部分进行除锈处理,确保钢管表面光滑整洁。
3.根据实际需求,选择合适的防腐材料,常见的有油漆、喷涂、涂布和包覆等方法。
4.对涂料进行充分的搅拌和筛选,确保质量合格。
二、施工工艺:
1. 涂刷法:使用刷子将防腐涂料均匀涂刷在钢管表面。
先从上到下涂刷一遍,然后从左到右涂刷一遍,确保涂层的平整。
2. 喷涂法:使用专用的喷涂设备将防腐涂料均匀喷涂在钢管表面。
注意喷涂的距离和速度,确保涂层的均匀和密实。
3. 涂布法:将防腐涂料倒在适量的布上,然后将布均匀覆盖在钢管表面,用手或工具将涂料涂布在钢管表面上。
4. 包覆法:使用防腐薄膜将钢管包覆起来,然后进行热缩处理,使薄膜与钢管表面紧密连接。
三、施工注意事项:
1. 选择合适的防腐材料,根据钢管的使用环境和要求进行选择。
2. 施工过程中注意安全,佩戴好防护装备,避免涂料接触皮肤和呼吸道。
3. 防止粉尘和杂质进入涂层,影响防腐效果。
4. 防腐施工时,留出一定的时间进行干燥和固化,确保涂层的质量。
5. 施工完毕后,进行验收,检查涂层的厚度和质量,确保达到防腐效果要求。
以上是钢管防腐施工方案的基本内容,根据具体情况可以对施工工艺进行调整和改进。
防腐施工是一项细致繁琐的工作,需要专业的技术和经验,保证钢管的防腐效果和使用寿命。
钢管的防腐施工方案
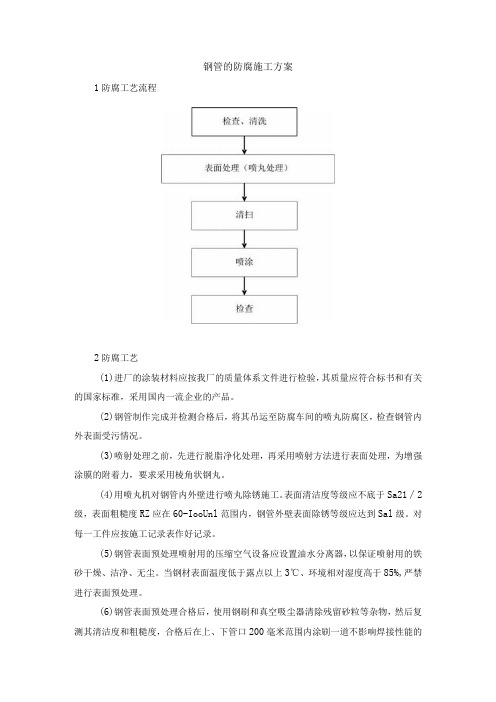
钢管的防腐施工方案1防腐工艺流程2防腐工艺(1)进厂的涂装材料应按我厂的质量体系文件进行检验,其质量应符合标书和有关的国家标准,采用国内一流企业的产品。
(2)钢管制作完成并检测合格后,将其吊运至防腐车间的喷丸防腐区,检查钢管内外表面受污情况。
(3)喷射处理之前,先进行脱脂净化处理,再采用喷射方法进行表面处理,为增强涂膜的附着力,要求采用棱角状钢丸。
(4)用喷丸机对钢管内外壁进行喷丸除锈施工。
表面清洁度等级应不底于Sa21∕2级,表面粗糙度RZ应在60-IooUnl范围内,钢管外壁表面除锈等级应达到Sal级。
对每一工件应按施工记录表作好记录。
(5)钢管表面预处理喷射用的压缩空气设备应设置油水分离器,以保证喷射用的铁砂干燥、洁净、无尘。
当钢材表面温度低于露点以上3℃、环境相对湿度高于85%,严禁进行表面预处理。
(6)钢管表面预处理合格后,使用钢刷和真空吸尘器清除残留砂粒等杂物,然后复测其清洁度和粗糙度,合格后在上、下管口200毫米范围内涂刷一道不影响焊接性能的车间底漆。
(7)用挡板将不需要喷涂油漆的部位盖住,然后开始进行钢管的涂漆施工。
(8)涂漆施工用高压无气喷涂机进行,涂料的配制、喷涂层数、层厚、层间喷涂时间间隔应按涂料的使用说明书进行施工。
(9)表面预处理、喷漆施工时严格在规范规定的环境条件下施工。
(10)每层涂装前应对上一层涂层进行外观进行检查。
涂装后进行外观检查,表面应光滑、颜色一致、无流挂、皱皮、针孔、裂纹、鼓泡等缺陷。
涂层厚度、致密性、粘附力应用专门仪器进行检测。
(11)涂层缺陷部位的补涂应将原表面打毛且周边打磨成45°斜面、清理干净后按正常喷涂工艺进行补涂施工。
(12)钢管内壁喷涂施工完成后,采用水泥浆喷涂器进行钢管外壁苛性钠水泥浆的喷涂,水泥浆的喷涂应力求稠度适中,厚度均匀,干膜不起粉状。
钢管防腐工艺流程
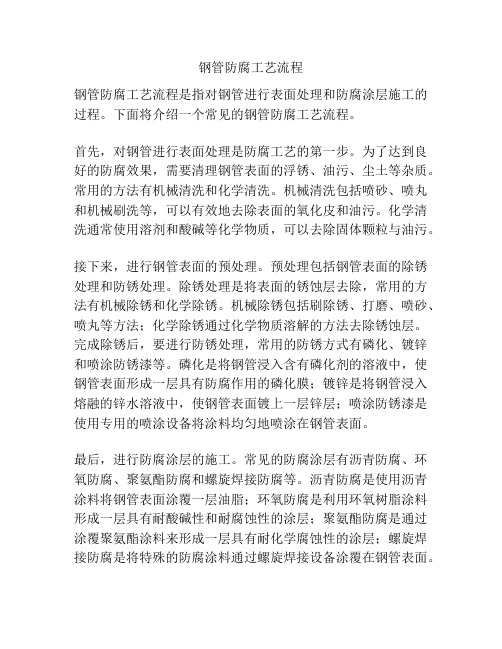
钢管防腐工艺流程钢管防腐工艺流程是指对钢管进行表面处理和防腐涂层施工的过程。
下面将介绍一个常见的钢管防腐工艺流程。
首先,对钢管进行表面处理是防腐工艺的第一步。
为了达到良好的防腐效果,需要清理钢管表面的浮锈、油污、尘土等杂质。
常用的方法有机械清洗和化学清洗。
机械清洗包括喷砂、喷丸和机械刷洗等,可以有效地去除表面的氧化皮和油污。
化学清洗通常使用溶剂和酸碱等化学物质,可以去除固体颗粒与油污。
接下来,进行钢管表面的预处理。
预处理包括钢管表面的除锈处理和防锈处理。
除锈处理是将表面的锈蚀层去除,常用的方法有机械除锈和化学除锈。
机械除锈包括刷除锈、打磨、喷砂、喷丸等方法;化学除锈通过化学物质溶解的方法去除锈蚀层。
完成除锈后,要进行防锈处理,常用的防锈方式有磷化、镀锌和喷涂防锈漆等。
磷化是将钢管浸入含有磷化剂的溶液中,使钢管表面形成一层具有防腐作用的磷化膜;镀锌是将钢管浸入熔融的锌水溶液中,使钢管表面镀上一层锌层;喷涂防锈漆是使用专用的喷涂设备将涂料均匀地喷涂在钢管表面。
最后,进行防腐涂层的施工。
常见的防腐涂层有沥青防腐、环氧防腐、聚氨酯防腐和螺旋焊接防腐等。
沥青防腐是使用沥青涂料将钢管表面涂覆一层油脂;环氧防腐是利用环氧树脂涂料形成一层具有耐酸碱性和耐腐蚀性的涂层;聚氨酯防腐是通过涂覆聚氨酯涂料来形成一层具有耐化学腐蚀性的涂层;螺旋焊接防腐是将特殊的防腐涂料通过螺旋焊接设备涂覆在钢管表面。
总之,钢管防腐工艺流程包括表面处理、预处理和防腐涂层施工。
通过这些步骤的全面施工,可以保证钢管的表面干净、无锈蚀,并且形成一层具有防腐性能的涂层,从而延长钢管的使用寿命。
- 1、下载文档前请自行甄别文档内容的完整性,平台不提供额外的编辑、内容补充、找答案等附加服务。
- 2、"仅部分预览"的文档,不可在线预览部分如存在完整性等问题,可反馈申请退款(可完整预览的文档不适用该条件!)。
- 3、如文档侵犯您的权益,请联系客服反馈,我们会尽快为您处理(人工客服工作时间:9:00-18:30)。
1、管道防腐的技术要求及检测
按要求,本工程所有钢管及钢制配件防腐涂料采用对防腐为无毒环氧富锌漆和环氧煤沥青.
(1)、内防腐为无毒环氧富锌漆注意事项:
涂刷底漆时,要求均匀涂刷,不得漏涂; 底漆表干后即可涂刷面漆.
涂刷后的管道或钢涂件对遗漏、空鼓、褶皱、划伤处应进行修补。
要注意避免在运输、吊装过程中损坏防腐层,若有损伤应及时补涂,否则不准安装。
当在管沟内进行管接口防腐涂刷时,必须清除防腐部位的泥土、水迹;回填土时应注意避免损伤外防腐层。
在通风条件不好的部位施工时,要采用人工通风设备。
不得在雨、雪、雾天进行露天施工。
(2)、施工质量及检验标准:
外观检查:防腐管应逐根检查,其表面平整、呈现光亮的漆膜,涂层均匀,无褶皱空鼓和凝块,防腐层的玻璃纤维布网眼应灌满面漆。
厚度检查:每20根抽查1根,用电脑膜层测厚仪(MCH-2004J)进行检测,在每根管道两端和中间共测3个截面,每个截面上、下、左、右4点,最薄点的厚度应符合防腐等级要求。
漆膜击穿强度检查:用JG—3型直流电火花检测逐根检查。
无打火花现象。
施涂干漆膜为450μm,电压测试为2500—2800V。
(3)、管道防腐施工工艺
管道的预处理:采手工和电动工具除锈。
清除防腐件表面的油污、
尘土、焊渣、氧化皮及疏松的锈蚀物,表面应保持干燥、无水迹,并具有金属光泽。
人工除锈达到Sa2.5级要求.
施涂:①、内防腐:采用无毒环氧富锌漆涂料二底二面,具体施工步骤为:先涂两层底漆,然后施涂两道漆每涂一层表面干后再涂下一层.厚度不小于2.5μm.
②、外防腐:环氧煤沥青采用四油三布,具体施工步骤:先涂一道底漆(无色),待其表干后,再涂一道底漆,缠玻璃布三道,最后涂两道面漆.总厚底不小于200μm.
③、防腐涂料的补口及补伤
补口、补伤处的涂层结构及所用材料应与管体涂层相同补口工作应在对口焊接后,管道表面温度冷却至50°C以下进行。
(4)、补口处和露铁的补伤处心须进行预处理
补口处应对管端阶梯形接茬处的表面进行清理,去除油污、泥土等杂物,然后用砂纸将其打毛。
施工方法按上述要求进行,补口涂层与管体涂层的连接不应小于100mm。
补伤处涂层的搭接应做成阶梯形接茬,其搭接长度不应小于100mm;若补伤处涂层未露铁,应先对其表面进行处理,并用砂纸打毛,补涂面和贴玻璃纤维布;若补伤处已露铁,先进行表面预处理后。
再按涂层的施工顺序及方法补涂底漆、面漆和贴玻璃纤维布。
当涂层破损面积较大时,应按补口方法处理。