设备利用率分析表格式
设备利用率
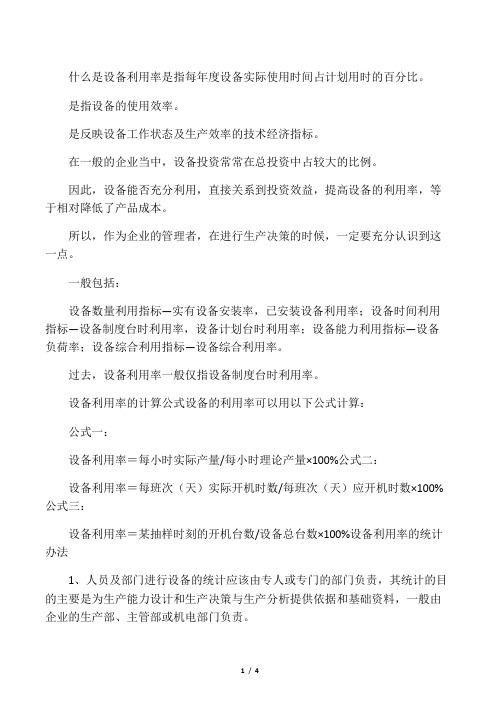
什么是设备利用率是指每年度设备实际使用时间占计划用时的百分比。
是指设备的使用效率。
是反映设备工作状态及生产效率的技术经济指标。
在一般的企业当中,设备投资常常在总投资中占较大的比例。
因此,设备能否充分利用,直接关系到投资效益,提高设备的利用率,等于相对降低了产品成本。
所以,作为企业的管理者,在进行生产决策的时候,一定要充分认识到这一点。
一般包括:设备数量利用指标―实有设备安装率,已安装设备利用率;设备时间利用指标―设备制度台时利用率,设备计划台时利用率;设备能力利用指标―设备负荷率;设备综合利用指标―设备综合利用率。
过去,设备利用率一般仅指设备制度台时利用率。
设备利用率的计算公式设备的利用率可以用以下公式计算:公式一:设备利用率=每小时实际产量/每小时理论产量×100%公式二:设备利用率=每班次(天)实际开机时数/每班次(天)应开机时数×100%公式三:设备利用率=某抽样时刻的开机台数/设备总台数×100%设备利用率的统计办法1、人员及部门进行设备的统计应该由专人或专门的部门负责,其统计的目的主要是为生产能力设计和生产决策与生产分析提供依据和基础资料,一般由企业的生产部、主管部或机电部门负责。
2、方法进行设备利用率的统计可依据生产报表分析进行,也可以采取实际统计的办法。
对于时产量固定的或产量容易计算的,可采用公式一;对于产量可变或设备较小的,可采用公式二、公式三;统计工作应该认真、严肃、长期坚持,只有长期的数据,才是更加准确和实事求是的调查数据设备完好率完好的生产设备在全部生产设备中的比重,它是反映企业设备技术状况和评价设备管理工作水平的一个重要指标。
计算公式为设备完好率=设备完好率完好设备总台数/生产设备总台数×100%所谓完好设备一般标准是:①设备性能良好,如机械加工设备的精度达到工艺要求;②设备运转正常,如零部件磨损、腐蚀程度不超过技术规定标准,润滑系统正常、设备运转无超温、超压现象;③原料、燃料、油料等消耗正常,没有油、水、汽、电的泄漏现象。
工厂数据分析报告(3篇)
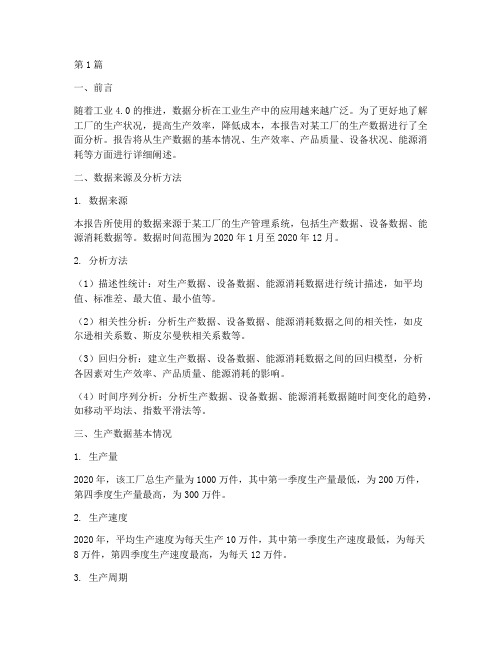
第1篇一、前言随着工业4.0的推进,数据分析在工业生产中的应用越来越广泛。
为了更好地了解工厂的生产状况,提高生产效率,降低成本,本报告对某工厂的生产数据进行了全面分析。
报告将从生产数据的基本情况、生产效率、产品质量、设备状况、能源消耗等方面进行详细阐述。
二、数据来源及分析方法1. 数据来源本报告所使用的数据来源于某工厂的生产管理系统,包括生产数据、设备数据、能源消耗数据等。
数据时间范围为2020年1月至2020年12月。
2. 分析方法(1)描述性统计:对生产数据、设备数据、能源消耗数据进行统计描述,如平均值、标准差、最大值、最小值等。
(2)相关性分析:分析生产数据、设备数据、能源消耗数据之间的相关性,如皮尔逊相关系数、斯皮尔曼秩相关系数等。
(3)回归分析:建立生产数据、设备数据、能源消耗数据之间的回归模型,分析各因素对生产效率、产品质量、能源消耗的影响。
(4)时间序列分析:分析生产数据、设备数据、能源消耗数据随时间变化的趋势,如移动平均法、指数平滑法等。
三、生产数据基本情况1. 生产量2020年,该工厂总生产量为1000万件,其中第一季度生产量最低,为200万件,第四季度生产量最高,为300万件。
2. 生产速度2020年,平均生产速度为每天生产10万件,其中第一季度生产速度最低,为每天8万件,第四季度生产速度最高,为每天12万件。
3. 生产周期2020年,平均生产周期为5天,其中第一季度生产周期最长,为7天,第四季度生产周期最短,为4天。
四、生产效率分析1. 生产效率指标(1)生产效率(产量/工时):2020年,平均生产效率为10件/小时。
(2)设备利用率:2020年,设备平均利用率为80%。
2. 生产效率分析(1)生产效率与工时关系:生产效率与工时呈正相关,工时增加,生产效率提高。
(2)生产效率与设备利用率关系:生产效率与设备利用率呈正相关,设备利用率提高,生产效率提高。
五、产品质量分析1. 产品合格率2020年,产品合格率为95%,其中第一季度合格率最高,为98%,第四季度合格率最低,为92%。
设备利用率OEE计算

如何计算工厂的整体设备效能日本工厂设备维修保养协会的Seiichi Nakajima曾表示,对于分散式生产的制造商来说,工厂整体设备效能(以下简称OEE)如果能达到85%,就可以被公认为世界一流的。
然而实际上目前并没有一个通用的工厂整体设备效能的计算方法。
在进行车间的OEE 的数据处理计算时,应考虑多种因素。
下面介绍的方法包含了一种计算生产线或生产流程的OEE,它也可推广用于计算整个工厂的OEE。
计算生产线或生产流程上的OEE如果所有的机器相对于生产率和生产能力来说其贡献是相同的,那么计算生产线的OEE就简单了。
但是完全均衡的生产线几乎没有,并且它也不能代表大多数工厂的真实情况。
另外,大多数工厂并非都是一条笔直的生产线,其生产的产品部件能从一台机器非常和谐的传到另一台机器而且设备之间也非常谐调。
实际上,一个生产流程往往是非常复杂的,生产线上的机器有些是串联关系,有些是并行工作,而且它们常常还有旁路流程。
因此直接计算生产线或生产流程的OEE而不计算各单个机器的OEE是不可能的。
生产线或生产流程的OEE计算,在理论上认为整个生产线或生产流程是一个单独的机器,它理论上的生产周期等于生产流程中瓶颈机器的生产周期。
例如,如果一条生产线上有三个机器,它们的生产周期分别为:3秒,2秒和4秒,则总的生产流程周期为4秒,即为瓶颈机器的生产周期。
生产线作为一个整体,在4秒钟之内它只能生产一个产品。
一个生产流程的关键是它要在瓶颈机器这一环节上保持一个高的可用度、生产率和优质率。
在典型的生产流程中各台机器的加工生产之间都有一定的时间冗余,如果这个时间冗余能够控制或允许一些机器短暂时间的停机,而不影响整个的生产流程,则它并不影响整个生产线或生产流程上的生产率。
如果这个时间冗余不能弥补其它机器的短暂停机时间,瓶颈机器就会由于没有原料而停机或阻塞下面的流程,而不能生产出额外的资料。
在所有的情形下,监控瓶颈机器的可用度和生产率,可提供一个非常好的整个生产线的生产剖面。
生产统计员一般要做的表格
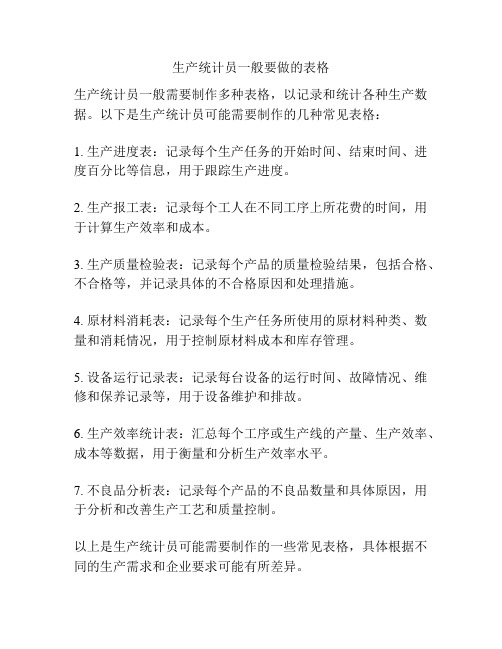
生产统计员一般要做的表格生产统计员一般需要制作多种表格,以记录和统计各种生产数据。
以下是生产统计员可能需要制作的几种常见表格:1. 生产进度表:记录每个生产任务的开始时间、结束时间、进度百分比等信息,用于跟踪生产进度。
2. 生产报工表:记录每个工人在不同工序上所花费的时间,用于计算生产效率和成本。
3. 生产质量检验表:记录每个产品的质量检验结果,包括合格、不合格等,并记录具体的不合格原因和处理措施。
4. 原材料消耗表:记录每个生产任务所使用的原材料种类、数量和消耗情况,用于控制原材料成本和库存管理。
5. 设备运行记录表:记录每台设备的运行时间、故障情况、维修和保养记录等,用于设备维护和排故。
6. 生产效率统计表:汇总每个工序或生产线的产量、生产效率、成本等数据,用于衡量和分析生产效率水平。
7. 不良品分析表:记录每个产品的不良品数量和具体原因,用于分析和改善生产工艺和质量控制。
以上是生产统计员可能需要制作的一些常见表格,具体根据不同的生产需求和企业要求可能有所差异。
8. 工时统计表:记录每个员工或工作组的工作时间、加班时间等,用于计算工资和控制工时成本。
9. 生产设备利用率统计表:记录每个生产设备的有效运行时间、停机时间、维修时间等,用于评估设备利用率和提升设备效率。
10. 产能分析表:根据生产任务和产能要求,记录每个工序或生产线的产能情况,用于规划和优化生产安排。
11. 库存管理表:记录原材料、半成品和成品的库存数量和变动情况,用于控制库存水平和进行周转分析。
12. 生产成本统计表:根据生产任务和相关成本项,统计每个生产任务的生产成本,包括人工成本、材料成本、设备折旧等,并进行成本分析和控制。
13. 客户订单统计表:记录客户的订单数量、交付日期、是否按时交付等信息,用于跟踪订单进展和满足客户需求。
14. 生产报表:根据上述表格的数据,综合分析和汇总生产数据,制作生产报表,用于向管理层提供有关生产情况的汇报和决策支持。
设备统计分析表
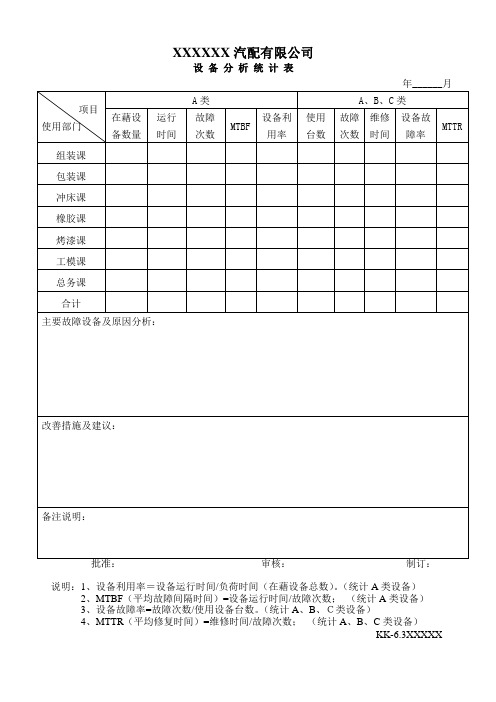
设备分析统计表
__________年______月
项目
使用部门
A类
A、B、C类
在藉设备数量
运行时间
故障次数
MTBF
设备利用率
使用台数
故障次数
维修时间
设备故障率
MTTRBiblioteka 组装课包装课冲床课
橡胶课
烤漆课
工模课
总务课
合计
主要故障设备及原因分析:
改善措施及建议:
备注说明:
批准:审核:制订:
说明:1、设备利用率=设备运行时间/负荷时间(在藉设备总数)。(统计A类设备)
2、MTBF(平均故障间隔时间)=设备运行时间/故障次数;(统计A类设备)
3、设备故障率=故障次数/使用设备台数。(统计A、B、C类设备)
4、MTTR(平均修复时间)=维修时间/故障次数;(统计A、B、C类设备)
KK-6.3XXXXX
设备利用率统计分析图表(年度)
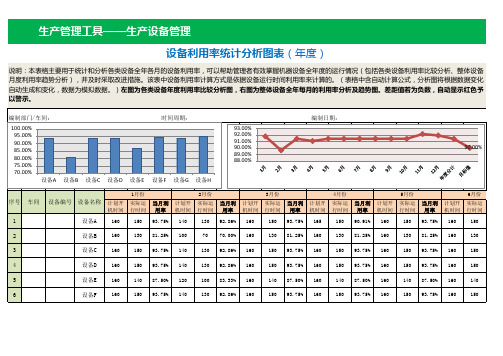
130 81.25% 160
130 81.25% 160
130 81.25% 1860
1500
93.75% 160
150 93.75% 160
150 93.75% 160
150 93.75% 160
150 93.75% 160
150 93.75% 160
150 93.75% 1900
1780
93.75% 160
设备名称
计划开 机时间
1月份
实际运 行时间
当月利 用率
计划开 机时间
2月份
实际运 行时间
当月利 用率
计划开 机时间
3月份
实际运 行时间
当月利 用率
计划开 机时间
4月份
实际运 行时间
当月利 用率
计划开 机时间
5月份
实际运 行时间
当月利 用率
计划开 机时间
6月份
实际运 行时间
设备A
160
150 93.75% 140
100 83.33% 160
140 87.50% 160
140 87.50% 160
140 87.50% 10 93.75% 140
130 92.86% 160
150 93.75% 160
150 93.75% 160
150 93.75% 160
150
7
设备G
8
设备H
设备总体利用率合计
生产管理工具——生产设备管理
设备利用率统计分析图表(年度)
说明:本表格主要用于统计和分析各类设备全年各月的设备利用率,可以帮助管理者有效掌握机器设备全年度的运行情况(包括各类设备利用率比较分析、整体设备 月度利用率趋势分析),并及时采取改进措施。该表中设备利用率计算方式是依据设备运行时间利用率来计算的。(表格中含自动计算公式,分析图将根据数据变化 自动生成和变化,数据为模拟数据。)左图为各类设备年度利用率比较分析图,右图为整体设备全年每月的利用率分析及趋势图。差距值若为负数,自动显示红色予 以警示。
企业常用生产管理表格(44个)
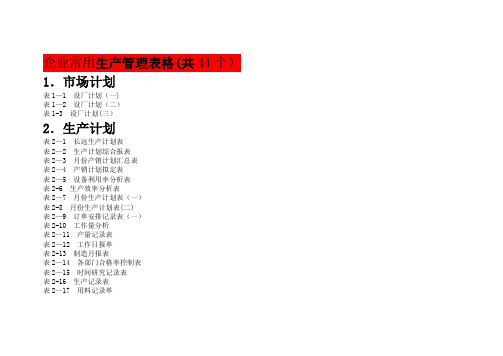
企业常用生产管理表格(共44个)1.市场计划表1—1 设厂计划(一)表1—2 设厂计划(二)表1-3 设厂计划(三)2.生产计划表2—1 长远生产计划表表2—2 生产计划综合报表表2—3 月份产销计划汇总表表2—4 产销计划拟定表表2—5 设备利用率分析表表2-6 生产效率分析表表2—7 月份生产计划表(一)表2-8 月份生产计划表(二)表2—9 订单安排记录表(一)表2-10 工作量分析表2—11 产量记录表表2—12 工作日报单表2-13 制造月报表表2—14 各部门合格率控制表表2—15 时间研究记录表表2-16 生产记录表表2—17 用料记录单表2-18 制造异常反应表表2—19 制造通知单表2—20 标准作业时间评定表(一) 表2-21 突发性工作量分析表(二)表2-22 最重要作业时间分析表2—23 作业标准时间研究表3.进度安排表3—1 生产进度安排检查表表3—2 生产进度计划表表3—3 生产管理安排核对表表3—4 生产故障分析表表3-5 生产进度表(一)表3—6 机器工作负荷图表(一)表3—7 生产进度控制表(一)4.生产记录表4—1 生产状况记录表表4—2 部门机器运转日记表4—3 生产用料记录单表4—4 考核人员记录表各表4—5 生产班次产量记录表5.生产日报表5-1 生产日报表表5—2 作业日报表(范例A)表5—3 作业日报表(范例B) 6.生产月报表6-1 生产月报表表6—2 生产计划科月报表表6—3 工作效率及工时月报表设厂计划(一)一、产销计划设厂计划(二)二、详细制造过程设厂计划(三)三、制造过程及设备分析长远生产计划表月日订定审核: 填表:生产计划综合报表月日至月日月份产销计划汇总表类别页次审核拟定产销计划拟定表月份总经理 ________________ 副总经理_________________ 审核 _______________ 填表_____________设备利用率分析表年度类别生产效率分析表月份生产计划表本月份预定工作数________日审核计划月份生产计划表(二)月份总经理厂长审核拟定订单安排记录表(一)月日至月日 NO。
设备综合效率指标的比较分析和运用
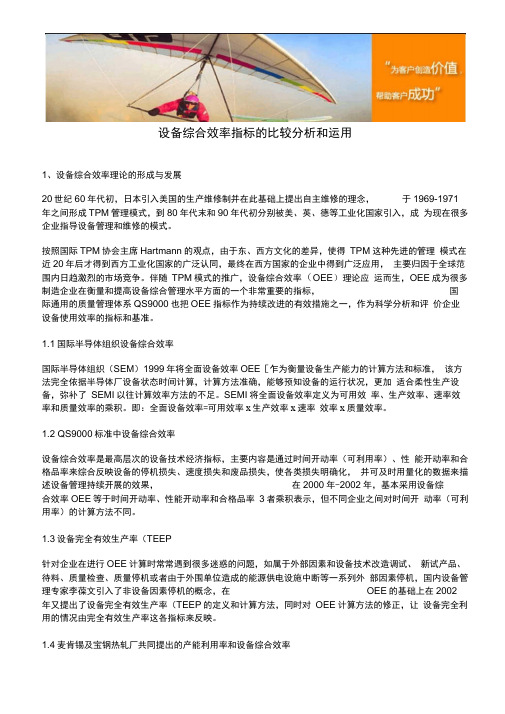
设备综合效率指标的比较分析和运用1、设备综合效率理论的形成与发展20世纪60年代初,日本引入美国的生产维修制并在此基础上提出自主维修的理念,于1969-1971年之间形成TPM管理模式,到80年代末和90年代初分别被美、英、德等工业化国家引入,成为现在很多企业指导设备管理和维修的模式。
按照国际TPM协会主席Hartmann的观点,由于东、西方文化的差异,使得TPM这种先进的管理模式在近20年后才得到西方工业化国家的广泛认同,最终在西方国家的企业中得到广泛应用,主要归因于全球范围内日趋激烈的市场竞争。
伴随TPM模式的推广,设备综合效率(OEE)理论应运而生,OEE成为很多制造企业在衡量和提高设备综合管理水平方面的一个非常重要的指标,国际通用的质量管理体系QS9000也把OEE指标作为持续改进的有效措施之一,作为科学分析和评价企业设备使用效率的指标和基准。
1.1国际半导体组织设备综合效率国际半导体组织(SEM)1999年将全面设备效率OEE[乍为衡量设备生产能力的计算方法和标准,该方法完全依据半导体厂设备状态时间计算,计算方法准确,能够预知设备的运行状况,更加适合柔性生产设备,弥补了SEMI以往计算效率方法的不足。
SEMI将全面设备效率定义为可用效率、生产效率、速率效率和质量效率的乘积。
即:全面设备效率=可用效率x生产效率x速率效率x质量效率。
1.2 QS9000标准中设备综合效率设备综合效率是最高层次的设备技术经济指标,主要内容是通过时间开动率(可利用率)、性能开动率和合格品率来综合反映设备的停机损失、速度损失和废品损失,使各类损失明确化,并可及时用量化的数据来描述设备管理持续开展的效果,在2000年-2002年,基本采用设备综合效率OEE等于时间开动率、性能开动率和合格品率3者乘积表示,但不同企业之间对时间开动率(可利用率)的计算方法不同。
1.3设备完全有效生产率(TEEP针对企业在进行OEE计算时常常遇到很多迷惑的问题,如属于外部因素和设备技术改造调试、新试产品、待料、质量检查、质量停机或者由于外围单位造成的能源供电设施中断等一系列外部因素停机,国内设备管理专家李葆文引入了非设备因素停机的概念,在OEE的基础上在2002年又提出了设备完全有效生产率(TEEP的定义和计算方法,同时对OEE计算方法的修正,让设备完全利用的情况由完全有效生产率这各指标来反映。