太钢第二炼钢厂顶底复吹转炉工艺生产实践解读
顶底复吹转炉设备操作规程
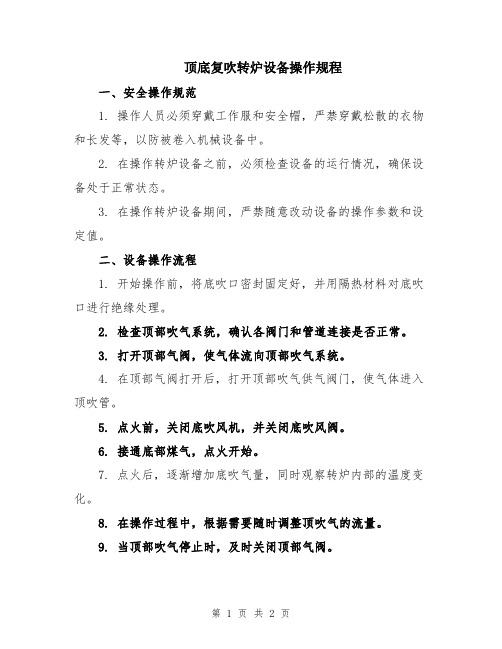
顶底复吹转炉设备操作规程一、安全操作规范1. 操作人员必须穿戴工作服和安全帽,严禁穿戴松散的衣物和长发等,以防被卷入机械设备中。
2. 在操作转炉设备之前,必须检查设备的运行情况,确保设备处于正常状态。
3. 在操作转炉设备期间,严禁随意改动设备的操作参数和设定值。
二、设备操作流程1. 开始操作前,将底吹口密封固定好,并用隔热材料对底吹口进行绝缘处理。
2. 检查顶部吹气系统,确认各阀门和管道连接是否正常。
3. 打开顶部气阀,使气体流向顶部吹气系统。
4. 在顶部气阀打开后,打开顶部吹气供气阀门,使气体进入顶吹管。
5. 点火前,关闭底吹风机,并关闭底吹风阀。
6. 接通底部煤气,点火开始。
7. 点火后,逐渐增加底吹气量,同时观察转炉内部的温度变化。
8. 在操作过程中,根据需要随时调整顶吹气的流量。
9. 当顶部吹气停止时,及时关闭顶部气阀。
10. 在转炉操作结束后,关闭底吹气门和底吹风机,停止底吹操作。
三、注意事项1. 在操作过程中,要不断观察炉内的温度和压力变化,确保煤气供给和底吹气的控制稳定。
2. 当炉内温度超过设定值时,必须及时调整顶吹气流量和底部煤气供给。
3. 当底部吹气系统出现异常情况时,应立即停止操作,并通知维修人员进行处理。
4. 在操作过程中,要时刻保持清洁,避免杂物进入设备内部,以防发生故障。
5. 在操作转炉设备时,必须严格遵守相关的操作规程和安全操作规定,确保人身和设备安全。
四、紧急情况处理1. 如果发生火灾,立即关闭顶部气阀和底吹气阀,切断气体供应。
2. 疏散人员应按照预定的逃生路线有序撤离现场,并迅速报告有关部门。
3. 在紧急情况发生后,不得擅自进行操作和抢修,必须等待维修人员到达现场进行处理。
以上就是对顶底吹转炉设备操作规程的详细介绍,希望能对您有所帮助。
如有疑问,请及时咨询相关人员。
第二炼钢厂炼钢工艺简介

日钢转炉主要工艺参数
转炉平均出钢量(扩容前)125-130吨/炉 转炉冶炼周期 28—32分钟 纯供氧时间 12--15分钟 最大日产炉数 50炉/日 转炉年作业天数 324日 转炉年有效作业率% 88.76% 设计年产钢水量 202.18万吨/年 4座转炉年设计能力 808.7万吨/年
转炉炼钢工艺
吹炼初期,炉渣主要来自铁水中Si、Mn、Fe的氧化 产物。由于发生Si、Mn、Fe的氧化反应,炉内温度升 高,促进了石灰熔化,这样炉渣的碱度逐渐得到提高。 吹炼中期,随着炉温的升高和石灰的进一步熔化, 同时脱碳反应速度加快导致渣中(FeO)逐渐降低,使石灰 融化速度有所减缓,但炉渣泡沫化程度则迅速提高。由于 脱碳反应消耗了渣中大量的(FeO),再加上没有达到渣系 液相线正常的过热度,使化渣条件恶化,引起炉渣异相 化,并出现返干现象。
吹炼末期,脱碳速度下降,渣中(FeO)再次升高,石 灰继续熔化并加快了熔化速度。同时,熔池中乳化和泡沫 现象趋于减弱和消失。
根据铁水成分和所炼钢种来确定造渣方法。常用的造 渣方法有单渣法、双渣法和留渣法。 单渣法:整个吹炼过程中只造一次渣,中途不倒 渣、直到吹炼终点出钢。入炉铁水Si、P、S含量较低, 或者钢种对P、S要求不太严格,以及冶炼低碳钢,均可以 采用单渣操作。单渣操作一般脱磷效率在90%左右,脱硫 效率约为30%-40%。 双渣法:双渣法操作主要原因:铁水温度和Si元素含 量过高,热量富余,对操作带来一定的困难;对冶炼钢种 磷成分要求严格. 留渣法:转炉溅渣后在炉内留部分渣,再加料冶炼下 一炉的操作。留渣法利于脱磷,并减少石灰的消耗量。
30
LF炉主体设备
1.变压器及二次回路
2.电极、电极升降系统以及电机横臂
3.炉盖及除尘系统
转炉顶底复吹技术
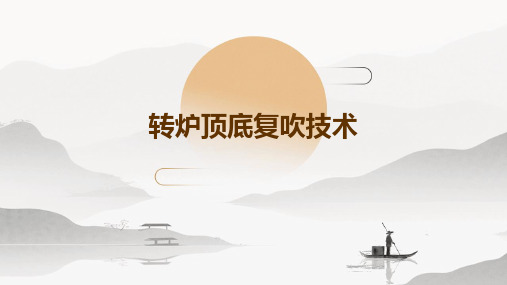
通过精确控制气体流量和吹炼参数,可以生产出 高质量的钢种。
强化冶金反应
通过顶底复吹技术,可以更有效地促进钢液中的 冶金反应,提高钢液纯净度。
节能减排
该技术能够降低炼钢过程中的能耗和减少污染物 排放。
技术发展历程
起源
转炉顶底复吹技术起源于20世纪 70年代,最初是为了解决传统转 炉炼钢技术中存在的冶金反应不
这种相互作用不仅有助于加速熔池的熔炼过程,还有助于提高钢水的纯净度和均 匀性,降低杂质含量。
顶底复吹对熔池搅拌的影响
顶底复吹技术通过向熔池底部吹入氧气或其他气体,产生强 烈的搅拌作用,使熔池内的钢水充分混合。这种搅拌作用有 助于加速钢水的传热和传质过程,提高熔炼效率。
顶底复吹的搅拌作用还能减少钢水中的夹杂物和气泡,提高 钢水的纯净度和致密性。
副枪测量准确
定期检查副枪测量准确性,确保钢水温度和 成分控制准确。
控制顶吹氧气流量
根据钢水氧化反应需求,调整顶吹氧气流量, 控制钢水温度和成分。
设备维护保养
定期对顶底复吹设备进行维护保养,确保设 备正常运行。
04
转炉顶底复吹技术的效果与 优化
转炉顶底复吹技术的效果
提高氧气利用率
通过底吹和顶吹的结合,使氧气更加 均匀地分布在熔池中,提高了氧气的 利用率,降低了能耗。
的远程监控和智能控制。
03
案例三
某欧洲大型钢厂采用先进的顶底复吹技术,提高了转炉的生产效率和产
品质量。该技术通过优化气体流量和吹炼工艺参数,降低了能耗和生产
成本,提高了企业的经济效益。
感谢您的观看
THANKS
减少氮气消耗
采用顶吹技术,可以减少氮气的消耗 量,降低生产成本。
太钢炼钢二厂AOD工艺培训教材(最终)

耐热性、耐磨蚀性良好,因含有Nb、Zr元素 洗衣机、汽车排气管、电
,故其加工性,焊接性优秀。
子产品、3层底的锅。
淬火后硬度高,耐蚀性好(有磁性)。
餐具(刀)、涡轮机叶片
作为马氏体钢的代表钢,虽然强度高,但不 刀刃、机械零件、石油精练置、螺
适合于苛酷的腐蚀环境下使用;其加工性好 栓、螺母、泵杆、1类餐具(刀叉)
AOD工艺的发现源于1954年在尼亚加拉瀑布城联合碳化公司的金属研究实验室 里。W.Krivsky当时正在研究碳-铬-温度之间的关系,并试图协调以前联合碳 化公司Hilty和CrafteQk以及英格兰Dennis所得到的某些不同的结果。
这些实验包括有向100磅融熔的铬合金熔池表面上吹氧。由于该实验反应的高 放热特性,在等温条件下是难于完成实验的。Krivsky就向氧中加氩以控制熔池 温度。他发现用氩稀释可使融熔的金属脱碳水平比以前所得到的结果低得多。且 不使铬过多地氧化。
AOD炉的炉体由炉身和炉帽两部分组成, 炉身为圆柱体及一倒置的截头圆锥体,其尺寸的 比例大致为:熔池深度:钢渣面直径:炉膛总高 =1:2:3。炉身下部侧墙的倾角为20~25°, 风口装置在侧墙下部。炉身部分的耐火衬分两部 分:内层是工作层,由各种特性的铬镁质耐火砖 砌成,厚度为300—400毫米;外层为保温衬,一 般是用厚度为115毫米的耐火粘土砖砌筑。近来 在欧洲与日本,采用镁白云石质耐火材料的工厂 正在日益增多。炉帽一般由耐火混凝土捣打成型 ,也可以用砖砌筑。它的作用是防止吹炼过程中 产生激烈喷溅,并在装入钢水和出钢时,保护风 口不受钢水侵蚀。
山西太钢不锈钢股份有限公司炼钢二厂
AOD及不锈钢的发展简介
不锈钢分类
➢ 按美标标准分200系、300系、400系。如201、301、304、321、316、317、309、310、 410、409、430、429、436、439、443、445、446、447;
不锈钢冶炼工艺流程的分析比较

不锈钢冶炼工艺流程旳分析与比较目前,国内作为不锈钢生产和消费大国,不锈钢种类繁多,根据钢种用途及原材料旳不同形成了不同旳冶炼工艺路线。
近几年来,国内不锈钢冶炼技术沿着提高生产率、简化工艺、减少生产成本和提高钢水质量旳方向发展,在原材料和工艺装备方面得以不断优化。
三种冶炼工艺各有优缺目前世界上生产不锈钢旳冶炼工艺重要分为一步法、二步法和三步法,其中EAF+AOD(电弧炉+氩氧精炼炉)旳两步法工艺约占70%,三步法工艺约占20%。
随着低磷铁水被广泛应用于不锈钢生产,新型一步法不锈钢冶炼工艺也被越来越多旳不锈钢生产公司采用。
为适应不锈钢市场旳剧烈竞争,提高产品质量同步也减少生产成本,国内各公司应根据自身旳实际状况选择合适旳不锈钢冶炼工艺。
一步法不锈钢冶炼工艺。
初期旳一步法不锈钢冶炼工艺,是指在一座电炉内完毕废铁熔化、脱碳、还原和精炼等工序,将炉料一步冶炼成不锈钢。
随着炉外精炼工艺旳不断发展以及AOD炉在不锈钢生产领域旳广泛应用,这种仅用电炉冶炼不锈钢旳一步法冶炼生产工艺由于冶炼周期长、作业率低、生产成本高,被逐渐裁减。
目前诸多不锈钢生产公司采用部分低磷或脱磷铁水替代废钢,将铁水和合金作为原料进入AOD炉进行不锈钢旳冶炼,由此形成了新型一步法冶炼工艺。
新型一步法冶炼工艺与初期一步法相比在生产流程上取消了电炉这一冶炼环节,其长处涉及:一是减少投资;二是减少生产成本;三是高炉铁水冶炼减少了配料成本,减少了能耗,提高了钢水纯净度;四是废钢比低,适应既有旳废钢市场;五是对于冶炼400系列不锈钢尤为经济。
但新型一步法对原料条件和产品方案具有一定规定:一是规定AOD入炉铁水磷含量低于0.03%如下,因此冶炼流程中须增长铁水脱磷解决环节;二是不合用于成分复杂、合金含量高旳不锈钢品种。
新型一步法不锈钢生产工艺目前被广泛应用于生产400系列不锈钢。
作为发展中国家,国内废钢资源缺少,又是极度贫镍旳国家,加之400系列不锈钢在平常生活和工业生产领域旳应用范畴越来越广,这些客观条件都使得新型一步法不锈钢冶炼被越来越多旳生产公司采用。
复吹转炉工艺技术在太钢的应用及优化

池搅拌较顶吹强 。 碳氧浓度积更接近平衡值. 复吹效
果更加 明显 。
元件由 3 层不锈钢无缝钢管组成.最外层直径为 ̄2 2
m 每炉座 为 4 m。 个底吹供气元件 。 每个底吹供气元件
的气量可 以通过计算机单独检测与控制 。底 吹供气元
皿l Ⅲ {
缸
件 布置在炉底 以 0 5 D为炉底 直径 ) . D( 4 为半径 的同心 圆上 , 与耳轴连线成 3 。 并 0 夹角 , 与耳 轴连线成对称 布
t 。为充分利用顶底复合 吹炼转炉工艺 的冶 金特性 . 更
T 1L4 等钢 种进行 了终 点碳 同溶解 氧 的关 系及 50 、5号 终点 碳 同碳氧 积 的关 系测 定 ,结果 表 明 :当炉 龄为 30 炉 时 , 00 在终 点碳 含量 为 009 温度 为 1 7 . %, 7 8℃ 6 的条件下 . 碳氧浓 度积 为 0 0 6 当炉龄 为 850炉 . 27 : 0 0
时 ,在终点碳 含量 为 0 6 %,温度为 1 6 %的条件 .3 0 4 6 下 , 氧浓 度积为 00 27 。测定 结果表 明 : 碳 . 8 0 随着炉 龄
咖 啪 鲫 伽 瑚 。
好地发挥特钢 的优势 ,提高转炉钢的质量 ,04 1 20 年 1 月太钢将第二炼钢 厂 的 2、 吹氧气改 造为顶底 复 3顶 合 吹炼 转炉。通过近 2年 的生产 实践 , 3复吹改造 2、
宝
皿1 圜
抽
0.0 0
0.5 0
01 .0
0.5 1
0.0 2
0_ 5 2
图 1 底 吹 供 气元 件 的布 置 方式
终点碳
闰 3 终 点 碳 与 氧 含 量 关 系 ( 龄 : 0 炉 85 0炉 )
第三章转炉炼钢工艺1
铁水和废钢配比是根据热平衡计算确定。
通常,铁水配比为70~90%,其值取决于铁水温度和成 分、炉容量、冶炼钢种、原材料质量和操作水平等。
炉容比:
指转炉内自由空间的容积(V)与金属装入量(t)之比 (V/t , m3/t)。
它通常波动在0.83~1.0,它与铁水成分、冷却剂类型、 氧枪喷头结构和供氧强度等因素有关。
区)和光亮较弱的狭窄外围(二次反应区)所构成 。
反应区的温度在2000~2700℃之间(高温、高氧浓度) 。
穿透深度和冲击面积是 凹坑特征的主要标志。
枪位:喷嘴在静止 液面上的高度。
转炉炼钢供氧制度
熔池的搅拌程度与氧射流的冲击强度密切相关:
氧射流冲击力大(硬吹),则射流的穿透深度大 ,冲击面积小,对熔池的搅拌强烈;
厂名 太钢 二炼
吨位/t 50
炉容 0.97 比 /m3.t-1
首钢三 炼
80
攀钢 120
0.84 0.90
本钢二 炼
120
鞍钢三 首钢二
炼
炼
150 210
宝钢一 炼
300
0.91
0.86 0.97
1.05
第三节 转炉炼钢供氧制度
一.氧射流及其对熔池的相互作用
1.氧射流 顶部氧射流是转炉炼钢最重要的供氧渠道。 顶氧射流是通过水冷氧枪将高压、高纯的氧气从出
(3-1) (3-2) (3-3)
(3-4) (3-5)
(3-6) (3-7)
(3-8) (3-9)
反应(3-9)的发展程度取决于C、Si、Mn的浓度。
转炉炼钢供氧制度
②
在一次反应区以外的二次反应区,主要是间
接氧化; [Fe]+ 1/2{O2 } =(FeO)
顶底复吹转炉炼钢
感谢观看
(1)顶吹氧占100%,底吹惰性气体搅拌,顶部加石灰块造渣;
(2)顶吹氧占90%~95%,底吹氧占5%~10%,顶部加石灰块造渣;
(3)顶吹氧占70%~80%,底吹氧占20%~30%,底吹石灰粉造渣;
(4)顶吹氧占20%~40%,底吹氧占60%~80%,附加喷吹燃料以预热废钢。
基于以上分类,各种复吹法可据此作如下归纳:
(1)LD-KG,LBE,LD-OTB,NK-CB,LD-AB诸法。它们的特点是靠底吹惰性气体以搅拌熔池,所用气体主要为 Ar、N2及CO2。由于N2比较便宜,所以使用较多。不过使用N2带来的问题是钢液增氮,尤其对氮敏感的钢种,更 要慎重使用。为避免钢液增氮,有时使用Ar和CO2作为搅拌气体,或在吹炼全程使用,或于吹炼后期使用。个别 场合,还要在吹炼完毕后底吹氩3~5min,以进一步降低钢液氮含量并促进冶金反应接近平衡。
(2)BSC-BAP,LD-OB,LD-HC,STB及STB-P和STB-S诸法。它们的特点是从炉底吹入O2或其他氧化性气体来 搅拌熔池。使用上述气体时,都需要采用双套管喷嘴,使氧流得到屏蔽,以免氧气等与炉底耐火材料直接接触。 BSC-BAP法是用N2作保护气体,STB法通常在中心管中通入O2及CO2,外管通入CO2、N2或Ar。
顶底复吹Байду номын сангаас炉炼钢
介绍
目录
01 简史
03 工艺原理和设备配置
02 工艺特点 04 顶底复吹的类型
从转炉炉顶吹氧的同时又向炉底吹入不同气体进行吹炼的转炉炼钢方法。这是在氧气顶吹转炉炼钢法和氧气 底吹转炉炼钢法两种方法(简称顶吹法和底吹法)的基础上发展起来的一种方法。它发挥了氧气顶吹转炉和氧气底 吹转炉两种炼钢方法的优点,从而在一定程度上弥补了这两种方法的不足之处。
4顶底复合吹炼转炉
4 顶底复合吹炼转炉4.1 简述4.1.1各国顶底复合吹炼技术概况氧气转炉顶底复合吹炼是70年代中后期国外开始研究的炼钢新工艺。
它的出现,可以说是考察了顶吹氧气转炉与底吹氧气转炉炼钢方法的冶金特点之后所导致的必然结果。
所谓顶底复合吹炼炼钢法,就是在顶吹的同时从底部吹入少量气体,以增强金属熔池和炉渣的搅拌并控制熔池内气相中CO的分压,因而克服了顶吹氧流搅拌能力不足(特别在碳低时)的弱点,使炉内反应接近平衡,铁损失减少,同时又保留了顶吹法容易控制造渣过程的优点,具有比顶吹和底吹更好的技术经济指标(见表4-1、表4-2),成为近年来氧气转炉炼钢的发展方向。
表4-1 顶吹与顶底复合吹炼低碳钢成本比较表4—2 50吨顶吹与顶底复合吹炼转炉指标比较早在50年代后半期,欧洲就开始研究从炉底吹入辅助气体以改善氧气顶吹转炉炼钢法的冶金特性。
自1973年奥地利人伊杜瓦德(ard)等研试转炉顶底复合吹氧炼钢后,世界各国普遍开始了对转炉复吹的研究工作,出现了各种类型的复合吹炼法。
其中大多数已于1980年投入工业性生产,到1981年底,世界上共有复合吹炼转炉81座。
由于复吹法在冶金上、操作上以及经济上具有比顶吹法和底吹法都要好的一系列优点,加之改造现有转炉容易,仅仅几年时间就在全世界范围内广泛地普及起来。
一些国家如日本已基本淘汰了98单纯顶吹法。
4.1.2我国顶底复合吹炼技术的发展概况我国首钢及鞍钢钢铁研究所,分别于1980年和1981年开始进行复吹的试验研究,并于1983年分别在首钢30吨转炉和鞍钢150吨转炉推广使用。
到目前为止全国大部分转炉钢厂都不同程度的采用了复合吹炼技术,设备不断完善,工艺不断改进,复合吹炼钢种已有200多个,技术经济效果不断提高。
表4—3是90年代初我国已有的复吹工艺及其主要特征。
表4—3 我国已有的复合吹炼法及主要特征1)底部供气元件。
底部供气元件是复合吹炼技术的关键之一。
我国最初采用的是管式结构喷嘴,1982年采用双层套管,1983年改为环缝,虽然双层套管与环缝比,除了使用N2、CO2、Ar外,还可以吹入粉料等,但是从结构上看还是环缝最简单。
转炉顶底复吹工艺总结
转炉顶底复吹工艺总结我厂于2006年3月29日与钢铁研究总院合作完成了对3#转炉底吹工艺改造,并获得初步成功。
在8月3日完成了对1#转炉的改造,8月23日完成了对2#转炉的改造。
至此,我厂的3座转炉已经全部实现了顶底复吹。
现对顶底复吹工艺在我厂的使用情况做一总结。
1、冶炼过程1.1过程枪位控制的调整复吹转炉由于底吹的影响,熔池物化反应强度发生改变,冶炼操作方式也与顶吹有所不同。
经过技术人员与操作工的摸索,复吹总体枪位比顶吹高200mm,特别是吹炼进行到4分钟左右[C]-[O]反应初起,枪位必须提高到距钢液面1600~1700mm,以避免金属喷溅。
并将最低枪位由顶吹时的距液面800mm改为距液面1000mm,过程枪位的波动控制在1000mm~1700mm,减少了过程的喷溅和返干,并有效地减少了烧枪。
1.2渣料的调整由于复吹转炉反应速度加快,熔池搅拌均匀,渣中TFe较顶吹转炉低,石灰加入量有所减少,萤石的加入量较大。
1.3终点控制的差异复吹与顶吹转炉相比,终点控制存在一定的差异:复吹转炉由于熔池的搅拌比顶吹有所加强,拉碳时火焰收缩没有顶吹明显,终点碳容易拉低;复吹转炉成渣速度快,要求对过程温度、化渣情况的变化应及时做出反应;复吹终点成分、温度更加均匀,出钢温度可适当降低5℃左右,配[C]时要按成分的中上限控制。
2、复吹转炉冶金效果评价(部分)2.1钢水终点[C][O]浓度积采用“长寿复吹转炉冶炼技术(LCB)”后,增强了吹炼末期熔池搅拌强度,使钢液中的[C]-[O]反应更加接近平衡,降低了钢水的氧化性,提高了钢水的质量。
经检测表明,在[C]×[ O]积方面,比顶吹转炉降低0.000006。
我们取样分析,3#转炉[C]×[ O]积平均为0.002841, 2#转炉平均为0.002847,降低0.000006。
([C][O]浓度积只有3#炉数据))2.2复吹工艺对终渣氧化性的影响采用复吹工艺之后,由于熔池搅拌加强,使渣-钢间的反应更加趋于平衡,从而使渣中的TFe含量有所降低。
- 1、下载文档前请自行甄别文档内容的完整性,平台不提供额外的编辑、内容补充、找答案等附加服务。
- 2、"仅部分预览"的文档,不可在线预览部分如存在完整性等问题,可反馈申请退款(可完整预览的文档不适用该条件!)。
- 3、如文档侵犯您的权益,请联系客服反馈,我们会尽快为您处理(人工客服工作时间:9:00-18:30)。
太钢第二炼钢厂顶底复吹转炉工艺生产实践
发表日期:2007-3-14 阅读次数:328
摘要:太钢第二炼钢厂通过引进钢铁研究总院的“长寿复吹转炉炼钢工艺技术”,将2号、3号顶吹氧气转炉改造为顶底复吹转炉。
总结阐述了改造后复吹转炉终点碳氧积、脱磷、脱碳、造渣和吹炼等各项工艺的研究。
关键词:顶底复吹转炉工艺研究
太原钢铁(集团)有限公司(以下简称太钢)第二炼钢厂有3座转炉,其中2号、3号转炉冶炼碳钢,原设计公称容量为50t顶吹氧气转炉,是1970年从奥地利引进投产的,2000年将其出钢量扩容为80t。
2004年,引进钢铁研究总院的“长寿复吹转炉炼钢工艺技术”,将顶吹氧气转炉改造为顶底复吹转炉。
1 顶底复合吹炼转炉主要工艺技术指标
1.1 复吹转炉终点碳氧积
2005年对Q235-A、HP345、T5IOL、45钢等钢种进行了68炉碳氧积的测定,表明:在终点w(C)为0.07%,温度为1669℃的条件下,碳氧浓度积为0.00277。
顶底复吹转炉终点碳氧关系见图1。
从图1中看出,随着转炉终点C含量的降低,终点溶解氧含量升高,特别是w(C)低于0.05%,溶解氧升高明显,因此在生产高碳钢时应控制终点C含量。
使C含量控制在规格上限,降低溶解氧含量,提高钢液纯净度。
1.2 复吹转炉脱磷研究
1.2.1 复吹转炉吹炼终点渣中,FeO含量、碱度同磷分配比的关系
由于复吹终点渣中FeO含量明显降低,熔池相对平稳,致使脱磷困难,磷分配比低,仅为46.75。
2005年,通过工艺摸索,提高转炉造渣工艺,转炉成品P含量降低,磷分配比明显提高,达到了76.44。
取样分析渣中FeO含量、碱度同磷分配比的关系,结果见图2、图3。
从图2,图3中看出,随着渣中FeO含量的增加,磷分配比呈上升趋势,说明随着渣中FeO 含量的增加,脱磷率增加。
炉渣碱度在2~4范围内,脱磷能力随炉渣碱度提高而提高。
1.2.2 复吹转炉吹炼终点温度同磷分配比的关系
通过研究转炉终点温度同磷分配比得出,在转炉温度较低的情况下,磷分配比呈上升趋势,说明复吹转炉低温有利于脱磷。
终点温度同磷分配比的关系见图4。
1.2.3 底部供气强度对脱磷的影响
底部供气的效果:一方面改善熔池动力学条件,加强钢一渣间的传质,对脱磷有利。
另一方面对熔池温度和炉渣成分,尤其是FeO总含量的影响,进而对脱磷起作用。
从实际跟踪情况看底部供气强度在小范围波动,对脱磷的影响不明显。
根据以上一系列生产实践,采取的脱磷措施有:将炉渣碱度由2.8~3.0调整为3.0~3.2;冶炼过程加红泥球,提高渣中FeO,促进脱磷反应进行;针对P要求低的钢种,吹氧采用高拉补吹工艺。
此外,低磷钢出钢后钢包中加改性剂,降低渣的氧化性,提高碱度,有效地防止回磷。
1.3 复吹转炉脱碳研究
冶炼过程中,由于供氧强度的不同会影响吹炼的平稳。
吹炼前期,因熔池温度不均匀,化渣
不良,炉渣粘度高,当熔池高速脱碳时易发生泡沫渣喷溅。
吹炼中期随熔池脱碳速度增加,钢渣乳化形成泡沫渣,大量飞溅产生的铁滴进入炉渣中。
在脱碳前期,由于铁滴中C含量较高,对渣中FeO还原非常充分,渣中FeO含量降低,CaO
含量升高,造成炉渣返干,严重时会发生金属喷溅,造成粘枪、粘炉口等故障。
控制氧枪高度减少渣中铁滴的喷洒量是抑制返干的主要手段。
而采用底吹大流量搅拌,促进熔池温度均匀和钢渣反应平衡,提高成渣速度是抑制前期喷溅的重要手段。
由于第二炼钢厂转炉没有副枪,不能取过程渣样,只能取转炉终点渣样进行分析,见图5。
图5 渣中TFe、FeO含量与终点碳关系
从图5中看出,随着转炉终点C含量的降低,渣中TFe含量呈上升趋势,因此,要合理控制转炉顶枪枪位和底吹流量,调整渣中TFe含量,以控制终点C含量。
1.4 复吹转炉脱硫研究
从图6中可知,炉渣碱度在2~4范围内,复吹转炉脱硫能力随炉渣碱度提高而增加,炉渣与钢水间硫分配比大致波动在3~8之间。
复吹转炉渣中FeO含量低,钢水氧化性较顶吹弱,脱硫效果比顶吹好。
同时底吹加强了熔池的搅拌,脱硫动力学条件好,脱硫效果增加。
1.5 复吹转炉造渣工艺研究
复吹转炉吹炼初期吹炼过程较为平稳,炉渣易返干,喷溅较少,炉渣对炉衬的化学侵蚀较轻,但容易造成炉底上涨。
通过现场跟踪、分析,最后确定复吹转炉造渣工艺为:采用石灰、轻烧白云石和镁球等造渣,单渣法操作。
碱度控制:初渣R=1.8~2.8,终渣R=3.0~3.2。
同时过程中使用红泥球造渣,增
加过程中渣中FeO含量,促进脱磷反应进行。
1.6 复吹转炉冶炼工艺研究
通过对转炉冶炼过程进行跟踪分析,转炉的装入量、冶炼时间、氧耗之间的关系见图7,图8。
从图7,图8中看出,随着转炉装入量的增加,供氧时间逐渐增加,但是吨钢供氧时间明显下降,所以在保证转炉冶炼正常、不喷溅的情况下增加装入量,可以有效地增加转炉的炉产量。
而从图9看出,随着废钢量的增加,供氧时间呈倒抛物线型,说明废钢的配入有一个合理的范围,在这个范围内,转炉冶炼时间最短。
通过调整顶吹供氧制度,改变枪位,促进前期渣中FeO的大量生成,加速化渣,促进脱磷反应进行,确定装入制度为:每炉装入量按90t~94t控制,其中铁水70t~72t,生铁10t,废钢10t~12t;吹炼制度为:氧压控制在0.78MPa~0.8MPa,氧气流量控制在17800m3/h~18000m3/h;调整顶枪枪位,保证渣钢间充分乳化,增加钢渣反应面积,枪位较顶吹时提高100㎜~200㎜。
1.7 确定底部供气制度
根据转炉所炼钢种要求N含量不同,同时考虑降低转炉吨钢氩耗,通过调整底吹模式、改变N2、Ar切换时间,保证了复吹效果,降低了吨钢氩耗。
表1不同钢种使用的底吹模式。
表1 复吹工艺底吹供气强度
2 结论
一年多的生产实践表明,第二炼钢厂顶底复吹转炉的主要技术指标明显好于顶吹氧气转炉。
(1)2005年第二炼钢厂复吹转炉终点碳氧积达到0.00277。
(2)转炉脱磷率大幅度提高,从2005年6月份开始提高并稳定在75%以上。
(3)复吹转炉吨钢氩耗由2005年1月份的0.86Nm3/t,下半年下降为0.50Nm3/t。
(4)石灰消耗由2004年下半年的57.54kg/t降低为2005年的53.53kg/t。
(5)氧枪枪龄由2004年的55次提高到2005年的160次。
(6)复吹转炉炉龄:2号炉炉龄为10241炉,复吹炉数为9940炉,复吹率为97.06%;3号炉炉龄为9172炉,复吹炉数为8893炉,复吹率为96.96%。