机械加工新技术-第3章[13页]
第三章机械加工精度(3.2)
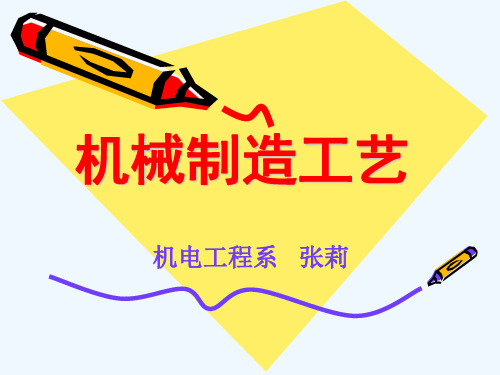
若齿轮Z1有转角误差δ1,造成Z2的转角误差为: δ12=i12δ1 传到丝杠上的转角误差为δ1n,即: Z1
Z2
δ1
δ2
δ1n=i1nδ1
δ2n=i2nδ2
………………
δn δnn=innδn
n
Zn
在任一时刻,各齿轮的转角误差反映到丝杠的总误差为:
i Σ 1 n 2 n nn j jn
学习目的
了解各种因素对加工精度的影响规律,找出提 高加工精度的途径,以保证零件的加工质量。
3. 2 工艺系统的几何误差
一、加工原理误差
加工原理误差是指由于采用了近似的加工方法、近似 的成形运动或近似的刀具轮廓而产生的误差。 例如滚齿用的齿轮滚刀,就有两种误差,一是为了制 造方便,采用阿基米德蜗杆代替渐开线基本蜗杆而产生的 刀刃齿廓近似造形误差;二是由于滚刀切削刃数有限,切 削是不连续的,因而滚切出的齿轮齿形不是光滑的渐开线, 而是折线,见图。 成形车刀、成形铣刀也采用了近似的刀具轮廓。
• 答:孔径没有误差,有圆柱度误差。轴线 不直。因为误差敏感方向不断变化。
讨 论
若镗杆进给,即镗杆既旋转又移动(图示), 导轨误差对加工精度有无影响?
答:不会产生孔的形状误差,但会产生孔的位 置误差。
讨
论
• 刨平面时,导轨误差对加工精度有何影 响? • 答:产生加工表面的直线度误差、平面 度误差。
主轴回转误差在实际中多表现为漂移。 漂移是指主轴回转轴线在每一转内的每一瞬时的变动 方位和变动量都是变化的一种现象。
Ⅰ理想回转轴线
Ⅱ实际回转轴线
2)影响主轴回转精度的主要因素
轴承本身误差
轴承间隙
轴承间同轴度误差 各段轴颈、轴孔的同轴度误差 主轴系统的刚度和热变形等 但它们对主轴回转精度的影响大小随加工方式而不同。
机械制造技术基础第3章习题解答

3、刀具既旋转又进给 镗杆的悬伸长量是变化的,镗杆的受力变形也是变化的,靠近主轴箱 处的孔径大,远离主轴箱处的孔径小,形成锥孔。镗杆悬伸长度增大, 主轴因自重引起的弯曲变形也增大,被加工孔轴线将产生相应的弯曲。
选择孔、端面的加工方法。 1.何种加工方法,2.何种机床,3.何种刀具,4.绘制示意图
1.孔:钻孔—半精镗—精镗; 端面:粗铣—半精铣—精铣 2.孔:卧式镗床; 端面:卧式铣床 3.孔:镗刀、麻花钻; 端面:组合三面刃铣刀
• 主轴前端采用短锥法兰式 C 型结构,用于安装卡盘或拨盘。如图 316所示,卡盘座 4 由主轴 3 端部的短圆锥定位,将4个螺栓5通过主轴 轴肩及锁紧盘 2上的孔拧入卡盘坐4的螺孔中,再将锁紧盘2沿顺时针 方向相对主轴转过一个角度,使螺栓5进入锁紧盘2的窄槽内,螺钉 1 锁紧。最后拧紧螺母6,即可将卡盘牢靠的安装在主轴的前端。这种 结构装卸方便,工作可靠,定心精度高。
– 最大齿轮加工直径为500mm滚齿机
机床的主要参数有哪些?p74
车床:最大车削直径 铣床:最大工作台宽度 钻床:最大钻孔直径 齿轮加工机床:齿轮分度圆最大加工直径 磨床:最大磨削直径 刨床:最大工作台宽度
3-4 何为外传动链?内传动链?其本质区别是什么?
• 外传动链:动力源与执行机构的联系 • 使执行机构按预定的速度运动和传递动力; • 传动比只影响运动速度不影响发生线的性质; • 不要求严格的传动比。 • 内传动链 • 两个执行机构之间的运动联系 • 将两个或以上独立运动组成一个复合成形运动 • 传动比及其相对位移量将影响发生线精度和性质。
机械制造工艺课件第三章机械加工精度
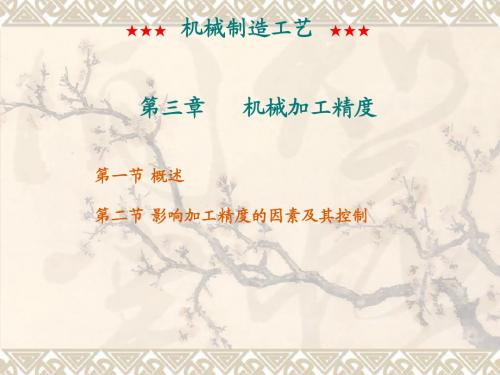
★★★
机械制造工艺
★★★
三、影响加工精度的原始误差
机械加工时,机床、刀具、夹具和工件等组成了一个工艺系统, 工艺系统的各个部分在加工过程中,应该保持严格的相对位臵关系。 由于受到许多因素的影响,系统的各个环节难免会产生一定的偏移, 使工件和刀具间相对位臵的准确性受到影响,从而引起加工误差。 原始误差即导致工艺系统各环节产生偏移的这些因素的总称。原始 误差中,有的取决于工艺系统的初始状态,有的与切削过程有关。 当原始误差的方向发生在加工表面法线方向时,引起的加工误 差最大;当原始误差的方向发生在加工表面的切线方向时,引起的 加工误差最小,一般可以忽略不计。为了便于分析原始误差对加工 精度的影响程度,我们把对加工精度影响最大的那个方向(即通过 切削刃的加工表面的法向)称为误差的敏感方向。而把对加工精度 影响最小的那个方向(即通过切削刃的加工表面的切向)则称为误 差的不敏感方向。
★★★
机械制造工艺
★★★
一、加工原理误差
原理误差即是在加工中由于采用近似的加 工运动、近似的刀具轮廓和近似的加工方法而 产生的原始误差。 完全符合理论要求的加工方法,有时很难实 现,甚至是不可能的。这种情况下,只要能满 足零件的精度要求,就可以采用近似的方法进 行加工。这样能够使加工难度大为降低有利于 提高生产效率降低成本。
★★★
机械制造工艺
ห้องสมุดไป่ตู้
★★★
3)定尺寸刀具法:是直接利用刀具的相应尺寸来 保证加工尺寸的方法。如用钻头钻孔,铰刀铰孔,用拉 刀、铣刀加工键槽等。加工尺寸精度的高低主要与刀具 的制造精度,安装精度和磨损及机床运动精度等因素有 关。这种加工方法加工精度稳定,生产率也高。 4)自动获得尺寸法:是利用测量装臵、调整装臵 和控制系统等组成的自动化加工系统,在加工过程中能 自动测量、补偿调整,当工件达到尺寸要求时,能自动 退回停止加工的方法。
机械制造技术基础第3章课后答案

机械制造技术基础(贾振元)第3章课后答案(总6页)--本页仅作为文档封面,使用时请直接删除即可----内页可以根据需求调整合适字体及大小--第三章机械加工与装配工艺规程制定1、什么是机械加工工艺过程答:用机械的加工方法(包括钳工的手工操作)按规定的顺序把毛坯(包括轧制材料)变成零件的全部过程。
2、工艺过程的基本单元是什么如何划分答:工序是工艺过程的基本单元。
工艺过程可分为工序、安装、工位、工步和走刀。
3、什么是工序、安装、工步、工位和走刀答:1、工序指的是一个工人(或一组工人)在一个工作地点(一般是指一台机床)对一个工件(对多轴机床来说是同时对几个工件)所连续完成的那一部分工艺过程。
2、一个工序有时在零件的几次装夹下完成,这时在零件每装夹一次下所完成的那部分工作称为一次安装。
3、在多轴机床上或在带有转位夹具的机床上加工时,工件在机床上所占有的一个位置上所完成的那部分工作称为一个工位。
4、在加工表面、切削刀具和切削用量(对车削来说,指主轴转速和车刀进给量,不包括切深,对其他加工也类似)都不变的情况下所连续完成的那一部分工作。
5、刀具在加工表面上对工件每一次切削所完成的那一部分工作称为一次走刀。
4、机械加工工艺规程制订的指导思想答:保证质量、提高效率、降低成本。
三者关系是,在保证质量的前提下,最大限度的提高生产率,满足生产量要求;尽可能地节约耗费、减少投资、降低制造成本。
5、不同生产类型的工艺过程的特点是什么答:企业生产专业化程度的分类称为生产类型,机械制造业一般有三种生产类型,即大量生产、成批生产和单件生产。
单件小批生产中,要能适应各种经常变化的加工对象,广泛使用万能机床、通用夹具、通用刀具和万能量具,一般采用较低精度的毛坯。
大批大量生产下,广泛使用各种高效率的、自动化程度高、专用的机床、夹具、刀具和量具,一般尽可能使用精度较高的毛坯。
6、什么是机械加工工艺规程它的作用是什么工艺规程的设计的原则和步骤有哪些答:将合理的工艺过程和操作方法,按照一定的格式写成文件,用来指导生产,这个工艺文件就叫做加工工艺规程。
金工实训——第三章 车削加工
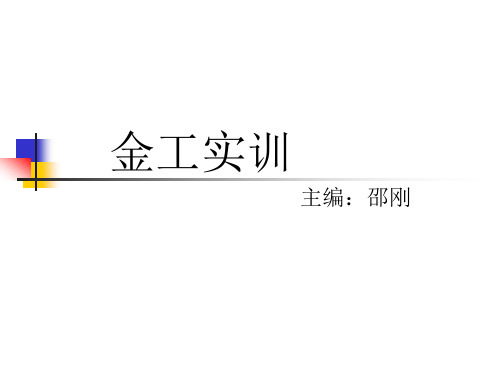
在车床上适合加工轴类、盘类中心位置的孔, 以及小型零件上的偏心孔,而不适合加工大 型零件和箱体、支架类零件上的孔。
一、镗孔
镗孔操作: 开车前先使车刀在孔内手动试走一遍 镗孔时,走刀量、切削深度要比车外圆
时略小 镗孔的切深方向和退刀方向与车外圆正
M—机床通用特性代号(精密机床)
6—机床组别代号(落地及卧式车床组)
1—机床系别代号(卧式车床系)
32—主参数代号(床身最大回转直径320mm)
3.2.2 普通车床的组成
主要由主轴箱、进给箱、溜板 箱、刀架、尾座、床身、电气 箱、床脚等部分组成
3.2.3、普通车床的传动
§3.3车削刀具
二、车削步骤
1、调整主轴速度,主轴转速 n=1000v/πd,其中D(mm)为工件直径, v(m/min)为所选的切削速度。
2、调整进给量 3、调整背吃刀量 在调整背吃刀量时,
不管是粗车还是精车,都要一边试切, 一边测量。
4、纵向进给
3.5.3车锥面
圆锥的参数
圆锥的锥度C=(D-d)/l=2tan(α/2) 圆锥的斜度K=(D-d)/2l= tan(α/2)
铰孔是利用定尺寸多刃刀具,高效率, 成批精加工的方法
五、车孔缺陷的原因及预防措施
3.5.5切槽和切断
一、切槽 1、槽刀的角度及安装 2、切槽的方法 切削5mm以下窄槽,可以主切刃和槽等宽,
一次切出。 切削宽槽时先分段横向粗车,最后一次横向
切削后,再进行纵向精车的加工方法。 3、切槽尺寸的测量和控制
3.3.1车刀的种类与用途 按用途不同可分为外圆车刀、端面车
刀、切断刀、内孔车刀、圆头车刀、 螺纹车刀和成型车刀等 3.3.2 车刀的组成及几何角度 一、车刀的组成 二、车刀的几何角度与切削性能的关 系
机械制造技术基础 03机械加工工艺规程设计

3.1 机械加工工艺规程的基本概念
• 3.1.1 机械加工工艺过程的概念及组成 其余 3.2
30js6 (两端)
• 例子:
0.8 ቤተ መጻሕፍቲ ባይዱ.8
50h6
0.8
0.8
40h6
35
80 220
35
工序号 1
工 序 内 容 (1)车端面、钻中心孔 (2)调头,车另一端面、钻中心孔 (1)车φ50h6外圆(留磨余量)、车φ30js6外圆(留磨余量),车槽并倒 角 (2)车右端φ40h6外圆(留磨余量)、φ30js6外圆(留磨余量),车槽并 倒角 铣键槽、去毛刺 磨各段外圆 检验
20~200
200~500
100~500
500~5000
大批
大量生产
300~1000
>1000
500~5000
>5000
5000~50000
>50000
3.1 机械加工工艺规程的基本概念
• 3.1.3 机械加工工艺规程
• • • • • • • • • 1.机械加工工艺规程的概念、内容及作用 (1)工艺规程是指导生产的主要技术文件。 (2)工艺规程是生产管理和组织管理的主要依据。 (3)工艺规程是新建或扩建工厂或车间的基本资料。 2.机械加工工艺规程的格式 (1)机械加工工艺过程卡片 (2)机械加工工艺卡片 (3)机械加工工序卡片 3.机械加工工艺规程的制定
• (1)保证零件加工表面与不加工表面之间的相互位置关系 此时应选 不加工面为粗基准。 • (2)保证各加工表面都有足够的加工余量 此时应选择余量小的表面 作为粗基准。 • (3)保证零件上的某些重要表面上的余量均匀 此时应选择重要表面 自身作为粗基准。
机械制造工艺学(王先逵)第三章参考答案(部分)

3-1 机械加工表面质量包括哪些具体内容?机械加工表面质量,其含义包括两个方面的内容:1.加工表面层的几何形貌主要由以下几部分组成:⑴表面粗糙度;⑵波纹度⑶纹理方向⑷表面缺陷2.表面层材料的力学物理性能和化学性能表面层材料的力学物理性能和化学性能主要反映在以下三个方面:⑴表面层金属冷作硬化;⑵表面层金属的金相组织变化;⑶表面层金属的残余应力。
3-2为什么机器零件一般总是从表面层开始破坏的?加工表面质量对机器使用性能有哪些影响?一、机器零件的损坏,在多数情况下都是从表面开始的,这是由于表面是零件材料的边界,常常承受工作负荷所引起的最大应力和外界介质的侵蚀,表面上有着引起应力集中而导致破坏的微小缺陷,所以这些表面直接与机器零件的使用性能有关。
二、加工表面质量对机器的耐磨性、耐疲劳性、耐蚀性、零件配合质量都有影响(一)表面质量对耐磨性的影响1.表面粗糙度、波纹度对耐磨性的影响表面粗糙度值越小,其耐磨性越好;但是表面粗糙度值太小,因接触面容易发生分子粘接,且润滑液不易储存,磨损反而增加;因此,就磨损而言,存在一个最优表面粗糙度值。
2.表面纹理对耐磨性的影响圆弧状、凹坑状表面纹理的耐磨性好;尖峰状的表面纹理由于摩擦副接触面压强大,耐磨性较差。
在运动副中,两相对运动零件表面的刀纹方向均与运动方向相同时,耐磨性较好;两者的刀纹方向均与运动垂直时,耐磨性最差3.冷作硬化对耐磨性的影响加工表面的冷作硬化,一般都能使耐磨性有所提高。
(二)表面质量对耐疲劳性的影响1.表面粗糙度对耐疲劳性的影响表面粗糙度值越小,表面缺陷越少,工件耐疲劳性越好2.表面层金属的力学物理性质对耐疲劳性的影响表面层金属的冷作硬化能够阻止疲劳裂纹的生长,可提高零件的耐疲劳强度。
(三)表面质量对耐蚀性的影响1.表面粗糙度对耐蚀性的影响表面粗糙度值越大,耐蚀性能就越差。
2.表面层金属力学物理性质对耐蚀性的影响表面层金属力学物理性质对耐蚀性的影响当零件表面层有残余压应力时,能够阻止表面裂纹的进一步扩大,有利于提高零件表面抵抗耐蚀的能力。
机械制造技术基础第三章课后答案

3-1 表面发生线的形成方法有几种? P69、70 轨迹法、成形法、相切法、展成法3-2试以外圆磨床为例分析机床的哪些是主运动、进给运动? P70 主运动:可以是旋转运动也可以是直线运动进给运动:纵向进给、横向进给、圆周进给、径向进给、切向进给3-3 机床有哪些基本组成部分?试分析其主要作用。
P70、71 动力源、运动执行机构、传动机构、控制系统和伺服系统、支承系统3-4 什么是外联系、内联系传动链?各有何特点 P71 3-5试分析提高外圆表面车削生产率的途径和方法。
P76 3-6车刀有哪几种?简述各种车刀的结构特征等 P77 3-7试述CA6140型卧式车床主传动链的传动路线。
P81 3-8 CA6140型卧式车床中主轴在主轴箱中是如何支承的?三爪自定心卡盘是怎样装夹在主轴上的? P81 3-9 CA6140型卧式车床是怎样通过双向多片摩擦离合器实现主轴正转、反转和制动的? P84、85 3-10 CA6140型卧式车床主轴箱Ⅰ轴上带的拉力作用在哪些零件上?3-11 CA6140型卧式车床主轴前轴承的径向间隙是如何调整的?3-12试分析外圆表面车拉削方法的工作原理和工艺特点。
P86、87 3-13试分析比较中心磨和无心磨外圆的工艺特点和应用范围。
P87 3-14试分析快速点磨法的工作原理和工艺特点。
P89 3-15试分析比较光整加工外圆表面各种加工方法的工艺特点和应用范围。
P91、923-16试分析比较钻头、扩孔钻和铰刀的结构特点和几何角度。
3-17用钻头钻孔,为什么钻出来的孔径一般都比钻头的直径大?3-18镗孔有哪几种方式?各有何特点? P97、98 3-19珩磨加工为什么可以获得较高的尺寸精度、形状精度和较小的表面粗糙度?3-20拉削速度并不高,但拉削却是一种高生产率的加工方法,原因何在?3-21对于相同直径、相同精度等级的轴和孔,为什么孔的公差值总比轴的公差值规定得大?3-22什么是逆铣、顺铣?试分析逆铣和顺铣、对称铣和不对称铣的工艺特征。
- 1、下载文档前请自行甄别文档内容的完整性,平台不提供额外的编辑、内容补充、找答案等附加服务。
- 2、"仅部分预览"的文档,不可在线预览部分如存在完整性等问题,可反馈申请退款(可完整预览的文档不适用该条件!)。
- 3、如文档侵犯您的权益,请联系客服反馈,我们会尽快为您处理(人工客服工作时间:9:00-18:30)。
比磨削提高效 率2倍
YT0 5
9
3.3.2 硬态车削的切削用量
加工工件 尺寸
/mm
外径
300
内孔
150×60 20×20×
200 方刀杆车
圆 外圆
34×80
表3-2 新型硬质合金刀具硬态车削实例(续)
切削用量
工件材料 uc/(m/ f/(mm/ ap/(
min)
r)
mm)
效果
5CrW2Si 59~60HR 56
刀具材料 牌号
密度
(103kg/ m3)
硬度 HRA
拉弯强度 断裂韧性
/MPa
KIC /MPa m1/2
用途
LD-1 4.79 93.5~94.5 700~860 5.8~6.5 断续切钢和铸铁
LD-2 FC-1 FC-2
6.51 93.5~94.5 700~860 5.8~6.5 断续切钢和铸铁
4.46
③ 认为刀具成本太高,不算综合成本(CBN的成本比硬质 合金高很多倍,但均摊到每一个零件上的成本就低了,且带来 的好处要多得多);
④ 对硬态车削机理研究不够; ⑤ 硬态车削的加工数据尚无实际指导作用。
13
现代机械加工新技术
第3章 硬态切削技术
3.1 硬态切削的概念
1ห้องสมุดไป่ตู้
3.1 硬态切削的概念
概述
所谓硬态车削是指把淬硬钢的车削作为最终精加工工序 的工艺方法。
图3-1 硬态切削
2
现代机械加工新技术
第3章 硬态切削技术
3.2 硬态切削的特点
3
3.2 硬态车削的特点
特点
(1)加工效率高,经济效益好 (2)是一种洁净的加工工艺 (3)适合柔性加工要求 (4)可获得良好的整体加工精度和表面质量
7
3.3.1 硬态车削刀具
硬态车削的刀片形状及刀具几何参数
从刀尖强度和散热情况来看,刀片形状性能的好坏依次 为:圆形、100°菱形、正方形、80°菱形、三角形、55° 菱形和35°菱形。
硬态车削时刀具几何参数的特点是,要选择较大的负前 角或预磨出负倒棱。
8
3.3.2 硬态车削的切削用量
加工工件 尺寸
拉弯强度 断裂韧性
/MPa
KIC /MPa m1/2
用途
LT55 4.96 93.7~94.8 900
5.04
适于加工55HRC淬硬钢和硬 铸铁
SG-4 6.65 94.7~95.3 850
4.94
适 于 加 工 60~65HRC 淬 硬 钢 和硬铸铁
JX-1 3.63 94~95 700~800 8.5 适于加工Ni基高温合金
T10A 58HRC
2 31.4 (螺
距P)
0.1
完全达到磨削 要求
刀片 牌号
YT7 26
YT7 67
GCr15 60~62HR 20.2
C
0.24
0.4~ 0.5
连续车削20件, 刀具使用寿命T 90
min
YM0 52
38CrMoA l氮化层
1.5 mm 68HRC
32.5~ 41
0.2
0.2~ 1.0
图3-2 硬态切削车床
11
现代机械加工新技术
第3章 硬态切削技术
3.4 硬态车削的应用与展望
12
3.4 应用与展望
硬态车削虽有前述优点,且也有不少成功实例,但至今应 用还不广,究其原因有下列几点:
① 要达到硬态车削的水平,机床、刀具、夹具及其加工工 艺应有最佳组合,工件硬度和余量应均匀;
② 对硬态车削效果宣传推广不够,很多人还不了解,观念 陈旧;
/mm
M90×1.5 螺纹环规
M8×2 螺纹塞规
外径
460
内孔
380×22
96×100 外圆
表3-2 新型硬质合金刀具硬态车削实例
切削用量
工件材料 uc/(m/ f/(mm/ ap/(
min)
r)
mm)
效果
CrWMn 60~63HR
C
1.5 20~30 (螺
距P)
0.3~ 尺 寸 精 度 合 格 , 0.8 Ra为0.8 m
4
现代机械加工新技术
第3章 硬态切削技术
3.3 硬态切削的必要条件
5
3.3.1 硬态车削刀具
硬态车削的刀具材料
能够作为硬态车削的刀具材料有立方氮化硼(CBN)、
陶瓷和新型硬质合金及涂层硬质合金。
表3-1 国产部分新型陶瓷刀具材料的物理力学性能及用途
刀具材 密度
料 (103 牌号 kg/m3)
硬度 HRA
JX-2 3.73 93~94 650~750 8.0~8.5 适于加工纯Ni和高Ni合金
LP-1 4.08 94~95 800~900 5.2 加工各种钢和铸铁
LP-2 3.94 94~95 700~800 7~8 断续切钢和铸铁
6
3.3.1 硬态车削刀具
硬态车削的刀具材料
表3-1 国产部分新型陶瓷刀具材料的物理力学性能及用途(续)
94~95 700~800 9.0 适 铁于加工超硬钢和冷硬铸
6.08 94.7~95.3 700~800 8.4 适于加工淬硬钢
FH-1 复合刀片 94~95 800~1 000 5.3~5.8 加工高硬钢和高硬铸铁
FH-2 复合刀片 94.7~95.3 800~1 000 5.3~5.8 断续加工淬硬钢
C
0.15
0.3
比磨削提高效 率8倍
W6Mo5C r4V2Al
68HRC
5.9
0.1~0. 2
1.0
车圆后再车螺 纹加工顺利
45钢淬火 42HRC
128
0.15
0.5
刀具使用寿命 比YT类提高5倍
刀片 牌号
YG6 00
YG6 10
YG6 10
10
3.3.3 硬态车削机床
机床导轨的精度要高、直线性要好、间隙要小,特别不 能有爬行现象;硬态车削对机床的另一要求是要有良好的热 稳定性能,机床热变形量要在一定范围内,这样才能保证连 续生产的加工精度要求。