超精密机械加工技术发展及应用
高精度轴承关键部件精密超精密加工技术

精密·制造
三、高精度轴承的精密超精密加工技术
1 磨削加工技术
加工工艺:
磨削是指用磨料,磨具切除工件上多余材料 的加工方法。磨削加工是应用较为广泛的切削加 工方法之一。
根据工艺目的和要求不同,磨削加工工艺方法有多种形式,为了适应发展需要, 磨削技术朝着精密,低粗糙度,高效,高速和自动磨削方向发展。磨削加工方法的形
2 3 6
深沟球轴承
5
圆锥滚子轴承
推力球轴承
精密·制造
二、高精度轴承各部件加工工序概述
2 轴承的结构(深沟球轴承)
精密·制造
二、高精度轴承各部件加工工序概述
3 轴承加工工艺流程
洛阳汇普轴承加工流程图
精密·制造
二、高精度轴承各部件加工工序概述
保持架
体用 并以 将隔 其离 保滚 持动 在体 轴︐ 承通 内常 ︒还 引 导 滚 动 原材料——剪料——裁环——光整——成形——整形——冲铆钉孔
实际切削路程比普通磨削路程要长;
实际的切削宽度增加,增大金属去除率,提高生产效率; 单颗磨粒的运动轨迹为正弦曲线,一个砂轮上拥有多颗磨粒,相邻的磨粒运动 轨迹便会重叠,使被加工工件表面成网状结构,有利于提高工件的表面质量。
磨削力比普通磨削要小,这样便可以提高加工的稳定性,减小磨削热的产生,
精密·制造
三、高精度轴承的精密超精密加工技术
4 油石超精研加工技术
目前轴承超精密加工中广泛采用的是油石超精研 加工,简称超精加工,一般是指用低压弹性地将细粒 度磨料的油石压在工件加工表面上,工件做旋转运动, 油石在垂直于工件旋转方向上按一定规律做快速往复 摆动,并提供良好的润滑与冷却条件,降低加工表面 粗糙度,提高几何精度。
激光超精密加工技术在航空航天领域中的应用

激光超精密加工技术在航空航天领域中的应用随着航空航天技术的不断提升,对于材料加工精度和效率的要求也越来越高。
激光超精密加工技术作为一种先进的材料加工方法,已经在航空航天领域中得到广泛应用。
本文将从激光超精密加工技术的原理和特点出发,探讨其在航空航天领域中的应用和发展前景。
一、激光超精密加工技术的原理和特点激光超精密加工技术是利用高能量激光束对材料进行加工的一种方法。
其原理是通过控制激光束的聚焦度、功率密度和作用时间,将激光能量集中到微小的加工区域,通过瞬间高温和高能量的作用,使材料发生蒸发、熔化和气化等变化,从而实现对材料的加工和形变。
与传统机械加工方法相比,激光超精密加工技术具有以下几个特点:首先,激光超精密加工技术具有极高的加工精度。
激光束的直径可以达到微米甚至纳米级别,可以实现对微小细节的加工和控制。
这对于航空航天领域来说尤为重要,因为航空航天工程中涉及到许多微小部件的加工和组装,需要具备高精度加工的能力。
其次,激光超精密加工技术具有非接触性加工特性。
激光束可以在与材料无接触的情况下进行加工,避免了机械接触带来的划痕、变形等问题,能够更好地保持材料的原始性能和形态。
再次,激光超精密加工技术具有高效率和灵活性。
激光加工速度快,可以实现对复杂形状的加工,同时可以根据需要在不同材料上进行加工,非常灵活。
二、激光超精密加工技术在航空航天领域中的应用1. 航空发动机制造与维修航空发动机是航空领域中最核心的部件之一,其制造和维修过程需要极高的精度和安全性。
激光超精密加工技术可以应用于航空发动机的叶片修整、烧孔处理、修复和刻字等工艺中。
利用激光超精密加工技术,可以实现发动机叶片的精确修整,提高叶片的流体力学性能和燃烧效率。
2. 航空航天器结构加工航空航天器的结构加工对于其安全性和可靠性至关重要。
激光超精密加工技术可以应用于航空航天器结构的切割、焊接和打孔等工艺中。
与传统的机械加工方法相比,激光超精密加工技术可以减少材料的应力和变形,提高航空航天器的强度和稳定性。
超精密加工与超高速加工技术国内外发展趋势

超精密加工与超高速加工技术国内外发展趋势中国磨料磨具网发布日期:2005-10-31 点击率:1442超精密加工与超高速加工技术现状及国内外发展趋势超高速加工工业发达国家对超高速加工的研究起步早,水平高。
在此项技术中,处于领先地位的国家主要有德国、日本、美国、意大利等。
在超高速加工技术中,超硬材料工具是实现超高速加工的前提和先决条件,超高速切削磨削技术是现代超高速加工的工艺方法,而高速数控机床和加工中心则是实现超高速加工的关键设备。
目前,刀具材料已从碳素钢和合金工具钢,经高速钢、硬质合金钢、陶瓷材料,发展到人造金刚石及聚晶金刚石(PCD)、立方氮化硼及聚晶立方氮化硼(CBN)。
切削速度亦随着刀具材料创新而从以前的12m/min提高到1200m/min以上。
砂轮材料过去主要是采用刚玉系、碳化硅系等,美国G.E公司50年代首先在金刚石人工合成方面取得成功,60年代又首先研制成功CBN。
90年代陶瓷或树脂结合剂CBN砂轮、金刚石砂轮线速度可达125m/s,有的可达150m/s,而单层电镀CBN砂轮可达250m/s。
因此有人认为,随着新刀具(磨具)材料的不断发展,每隔十年切削速度要提高一倍,亚音速乃至超声速加工的出现不会太遥远了。
在超高速切削技术方面,1976年美国的V ought公司研制了一台超高速铣床,最高转速达到了20000rpm。
特别引人注目的是,联邦德国Darmstadt工业大学生产工程与机床研究所(PTW)从1978年开始系统地进行超高速切削机理研究,对各种金属和非金属材料进行高速切削试验,联邦德国组织了几十家企业并提供了2000多万马克支持该项研究工作,自八十年代中后期以来,商品化的超高速切削机床不断出现,超高速机床从单一的超高速铣床发展成为超高速车铣床、钻铣床乃至各种高速加工中心等。
瑞士、英国、日本也相继推出自己的超高速机床。
日本日立精机的HG400III型加工中心主轴最高转速达36000~40000r/min,工作台快速移动速度为36~40m/min。
超精密加工技术在航天器制造中的应用

超精密加工技术在航天器制造中的应用引言随着航天事业的不断发展,航天器的制造技术也在不断地提高和改进,其中超精密加工技术是一种非常重要的技术之一。
超精密加工技术是指在非常高精度和高效率的情况下,对工件进行精密加工的一种加工技术,具有高质量、高精度、高效率、高耐磨性等优点。
在航天器制造中,超精密加工技术可以被广泛地应用,可以大大提高航天器的制造精度和质量,从而提高整个航天工程的成功率和效益。
第一章超精密加工技术的基本概念超精密加工技术是一种高度精密和高效率的加工技术,它可以在非常高的精度和效率下对工件进行加工,从而保证加工后的工件具有高质量、高精度、高效率以及高耐磨性等优良性质。
超精密加工技术可以分为机械加工、电子加工、化学加工等多种加工方式,其中机械加工是最为常见的一种。
机械加工的超精密加工技术主要包括铣削、车削、磨削等方式,其加工精度可以达到微米乃至纳米级别。
这种加工方式不仅可以对各种材料进行加工,而且加工过程中对环境污染也非常小,因此被广泛地应用于各种高精度的加工领域中。
第二章超精密加工技术在航天器制造中的应用在航天器制造中,超精密加工技术得到了广泛的应用,可以大大提高航天器的制造精度和质量,从而保证整个航天工程的成功率和效益。
具体应用如下:2.1 航天器壳体制造航天器的壳体是一个非常关键的零部件,它要求具有高精度、高强度、耐热、防辐射等特点。
超精密加工技术可以在满足这些要求的基础上,对航天器的壳体进行加工,从而保证壳体的精度和质量,从而提高航天器的安全性和稳定性。
2.2 航天器零部件制造除壳体外,航天器的其他零部件也需要采用超精密加工技术进行制造,例如导弹喷雾板、电机减速装置等。
这些零部件要求具有精度高、耐热、耐磨等特点,超精密加工技术可以满足这些要求,从而提高航天器的质量和效率。
2.3 航天器加工技术研究超精密加工技术的应用还可以促进航天器制造技术的发展和研究。
例如,通过对航天器加工技术的研究和改进,可以提高航天器的制造精度和质量,从而保证整个航天工程的成功率和效益。
精密和超精密加工现状与发展趋势
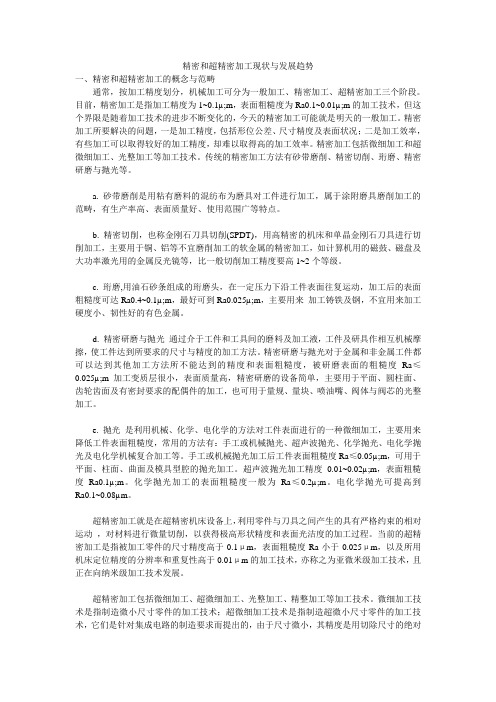
精密和超精密加工现状与发展趋势一、精密和超精密加工的概念与范畴通常,按加工精度划分,机械加工可分为一般加工、精密加工、超精密加工三个阶段。
目前,精密加工是指加工精度为1~0.1µ;m,表面粗糙度为Ra0.1~0.01µ;m的加工技术,但这个界限是随着加工技术的进步不断变化的,今天的精密加工可能就是明天的一般加工。
精密加工所要解决的问题,一是加工精度,包括形位公差、尺寸精度及表面状况;二是加工效率,有些加工可以取得较好的加工精度,却难以取得高的加工效率。
精密加工包括微细加工和超微细加工、光整加工等加工技术。
传统的精密加工方法有砂带磨削、精密切削、珩磨、精密研磨与抛光等。
a. 砂带磨削是用粘有磨料的混纺布为磨具对工件进行加工,属于涂附磨具磨削加工的范畴,有生产率高、表面质量好、使用范围广等特点。
b. 精密切削,也称金刚石刀具切削(SPDT),用高精密的机床和单晶金刚石刀具进行切削加工,主要用于铜、铝等不宜磨削加工的软金属的精密加工,如计算机用的磁鼓、磁盘及大功率激光用的金属反光镜等,比一般切削加工精度要高1~2个等级。
c. 珩磨,用油石砂条组成的珩磨头,在一定压力下沿工件表面往复运动,加工后的表面粗糙度可达Ra0.4~0.1µ;m,最好可到Ra0.025µ;m,主要用来加工铸铁及钢,不宜用来加工硬度小、韧性好的有色金属。
d. 精密研磨与抛光通过介于工件和工具间的磨料及加工液,工件及研具作相互机械摩擦,使工件达到所要求的尺寸与精度的加工方法。
精密研磨与抛光对于金属和非金属工件都可以达到其他加工方法所不能达到的精度和表面粗糙度,被研磨表面的粗糙度Ra≤0.025µ;m加工变质层很小,表面质量高,精密研磨的设备简单,主要用于平面、圆柱面、齿轮齿面及有密封要求的配偶件的加工,也可用于量规、量块、喷油嘴、阀体与阀芯的光整加工。
e. 抛光是利用机械、化学、电化学的方法对工件表面进行的一种微细加工,主要用来降低工件表面粗糙度,常用的方法有:手工或机械抛光、超声波抛光、化学抛光、电化学抛光及电化学机械复合加工等。
精密和超精密加工的机床设备技术

精密和超精密加工的机床设备技术引言精密和超精密加工技术在现代制造业中扮演着重要的角色。
为了满足高质量、高精度、高效率的加工需求,机床设备技术不断得到改进和发展。
本文将介绍精密和超精密加工的机床设备技术,并探讨其在制造业中的应用。
1. 精密加工的机床设备技术精密加工是指在工程加工中,对尺寸精度和表面质量要求较高的加工方法。
精密加工的关键在于机床设备的稳定性、刚性和精度。
以下是精密加工机床设备的几个关键技术:1.1 数控技术数控技术是精密加工中最为关键的技术之一。
通过数控技术,可以实现机床的高精度和高效率加工。
数控技术的应用可以大大提高生产效率,并且减少操作人员的工作强度。
1.2 精密传动系统精密传动系统是精密加工机床设备的核心组成部分。
精密传动系统的设计与制造涉及到轴承、传动装置、伺服驱动装置等多个方面。
通过精确的传动系统,可以提高机床的精度和稳定性。
1.3 线性驱动技术线性驱动技术是现代机床设备中的重要发展方向之一。
相比传统的滚动轴承驱动,线性驱动技术能够实现更高的速度和更高的精度。
线性驱动技术可以用于各种类型的机床设备,包括数控机床和超精密加工机床。
2. 超精密加工的机床设备技术超精密加工是指在微米甚至纳米级别下进行加工的技术。
超精密加工在光学、光电子、半导体等领域具有重要的应用。
以下是超精密加工机床设备技术的几个关键技术:2.1 超精密控制系统超精密控制系统是实现超精密加工的关键技术之一。
通过超精密控制系统,可以实现对微小位移和应力的精确控制。
超精密控制系统需要具备高精度、高灵敏度和高稳定性的特点。
2.2 超精密磨削技术超精密磨削技术是超精密加工的核心技术之一。
超精密磨削技术可以实现对工件表面的精确修整和光洁度的提高。
超精密磨削技术需要借助特殊材料和磨削工具,并配合高精度的机床设备。
2.3 超精密检测技术超精密加工过程中,对工件的检测和测量要求非常高。
超精密检测技术可以实现对工件尺寸、形状和表面质量的高精度测量。
精密加工技术在机械制造中的应用

精密加工技术在机械制造中的应用精密加工技术是一种高度精细和精确的制造技术,广泛应用于机械制造行业。
它通过先进的设备和精密的工艺,能够制造出高精度、高质量的机械零部件和产品。
本文将就精密加工技术在机械制造中的应用进行探讨。
一、精密加工技术的意义精密加工技术的应用对于提高机械制造行业的质量、效率和竞争力至关重要。
通过精密加工技术,能够实现零部件的高精度加工,使得机械设备的运行更加稳定,提高了设备的使用寿命和可靠性。
此外,精密加工技术还能够大幅提高产品的精度和表面质量,满足现代工业对于高精度零部件和产品的需求。
二、精密加工技术在机械制造中的具体应用1.数控加工技术数控加工技术是精密加工技术的重要组成部分,通过计算机控制数控机床进行加工,可以实现高度精确的操作。
数控加工技术广泛应用于机械制造中的各个领域,如车、铣、刨、钻等工艺。
它能够提高加工效率和精度,减少人为因素对产品质量的影响,提高生产线的自动化水平。
2.激光切割技术激光切割技术是一种快速、精确和无接触的加工方法,通过激光束对材料进行切割。
激光切割技术在机械制造领域的应用广泛,可以对各种材料进行高精度的切割,如金属、塑料、玻璃等。
它能够实现复杂形状和细小孔洞的加工,提高产品的精度和质量。
3.精密研磨技术精密研磨技术是一种针对零部件表面进行超精密处理的加工方法。
通过精密研磨技术,可以对零部件的尺寸、形状和表面质量进行高精度的控制和调整。
精密研磨技术广泛应用于航空航天、汽车制造等高精度要求的行业,如飞机发动机叶片、汽车发动机曲轴等。
4.微细加工技术微细加工技术是指对微小尺寸零部件进行高精度加工的技术方法。
微细加工技术广泛应用于微机电系统(MEMS)、光学器件等领域。
通过微细加工技术,可以制备出具有微米级精度的微小零部件,如光纤、微型传感器等。
5.精密装配技术精密装配技术是将精确加工的零部件进行组装,形成完整的机械设备或产品的技术。
精密装配技术在机械制造中起到了至关重要的作用,它能够确保零部件之间的吻合度和配合精度,提高装配质量和效率。
超精密加工技术在未来机械领域的发展前景概述
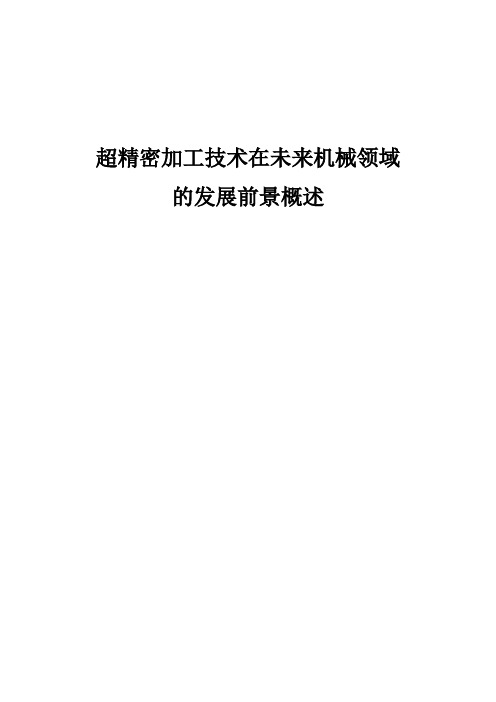
超精密加工技术在未来机械领域的发展前景概述超精密加工技术在未来机械领域的发展前景[前言]近二十年以来机械制造业正以迅猛的发展步伐向精密加工、超精密加工发展,在未来的发展过程中精密加工、超精密加工将成为在国际竞争、市场竞争中取胜的关键技术。
现代制造业之所发要致力于提高加工精度,其主要原因在于提高产品的性能和质量,提高其质量的稳定性和性能的可靠性,促进产品的小型化、功能性强,零件互换性好,产品的装配、调试生产率高,并促进制造装配自动化。
随着制造业的发展,现在的精密机械加工正在从微米、亚微米级工艺发展,在今后的加工中,普通机械加工、精密加工与超精密加工精度可分别达到1μm、0.01μm、0.001μm(即1nm),而且超精密加工正在向原子级加工精度逼进(0.1nm)。
随着极限加工精度的不断提高,为科学技术的发展和进步创造了条件,也为机械冷加工提供了良好的物质手段。
关键词超精密加工发展趋势发展策略后续研发一、引言我们一提到超精密这个词语,就觉得它比较神秘,但跟任何其他复杂的高新技术一样,经过一段时间的熟悉、适应,都会被大众所了解,也就不再是所谓的高科技了,超精密加工也是如此。
实际上,如果拥有超精密的加工设备,并且在其它相关技术和工艺上能匹配,经过一段时间的实践之后,就能很好地掌握它,但这需要一个过程。
超精密加工领域集成了很多IT、机械以及电气控制方面的技术,设备方面的操作和使用也非常复杂,所以,只有在对它有很深的理解之后才能把它用好。
二、正文超精密加工当前是指被加工零件的尺寸和形状精度高于0.1μm,表面粗糙度Ra小于0.025μm,以及机床定位精度的分辨率和重复性高于0.01μm的加工技术,亦称之为亚微米级加工技术,目前正在向纳米级加工技术发展。
超精密加工技术在国际上处于领先地位的国家是美国、英国和日本。
美国是开展超精密加工技术研究最早的国家,也是迄今处于领先地位的国家。
英国的克兰菲尔德精密工程研究所(简称CUPE)享有较高声誉,是当今世界上精密工程的研究中心之一。
- 1、下载文档前请自行甄别文档内容的完整性,平台不提供额外的编辑、内容补充、找答案等附加服务。
- 2、"仅部分预览"的文档,不可在线预览部分如存在完整性等问题,可反馈申请退款(可完整预览的文档不适用该条件!)。
- 3、如文档侵犯您的权益,请联系客服反馈,我们会尽快为您处理(人工客服工作时间:9:00-18:30)。
超精密机械加工技术发
展及应用
集团企业公司编码:(LL3698-KKI1269-TM2483-LUI12689-ITT289-
超精密机械加工技术发展及应用超精密机械加工技术作为微光学元件的一种制造方法,具有很多其他传统方法所不具有的优点。
本文回顾了超精密机械加工技术的发展,展望了其在微光学元件加工中的应用潜力。
1微光学概述
1.1定义与名称
微光学是一门属于多门前沿学科交叉领域的新兴科学。
微光学借助于微电子工业技术的最新研究成果,是国际上最前沿研究方向之一,并具有广泛的应用前途。
微光学元件(MOC),指面形精度可达亚微米级,表面粗糙度可达纳米级的自由光学曲面及微结构光学元件。
自由光学曲面包括有回转轴的回转非球面(如抛物面、渐开面等),和没有任何对称轴的非回转非球面,如Zernike像差方程曲面。
微结构是指具有特定功能的微小表面拓扑形状,如凹槽、微透镜阵列等,如图1所示(图1略)的微金字塔结构表面。
这些结构决定了对光线的反射,透射或衍射性能,便于光学设计者优化光学系统,减轻重量,缩小体积。
典型微光学元件如全息透镜、衍射光学元件(DOE)和梯度折射率透镜等,将这些微光学元件应用在各种光电子仪器中,可以使光电子仪器及其零部件更加小型化、阵列化和集成化。
1.2微光学元件的应用
微光学元件是制造小型光电子系统的关键元件,它具有体积小、质量轻、造价低等优点,并且能够实现普通光学元件难以实现的微小、阵
列、集成、成像和波面转换等新功能。
随着系统小型化不断的成为一种趋势,几乎在所有的工程应用领域中,无论是现代国防科学技术领域,还是普通的工业领域的应用前景。
军用方面,西方国家在70年代以后研制和生产的军用光电系统,如军用激光装置、热成像装置、微光夜视头盔、红外扫描装置、导弹引导头和各种变焦镜头,均已在不同程度上采用了非球面光学零件。
在一般民用光电系统方面,自由非球面零件可以大量地应用到各种光电成像系统中。
如飞机中提供飞行信息的显示系统;摄像机的取景器、变焦镜头;红外广角地平仪中的锗透镜;录像、录音用显微物镜读出头;医疗诊断用的间接眼底镜,内窥镜,渐进镜片等。
微结构光学元件应用更是广泛,如光纤连接器中的微槽结构,液晶显示屏的微透镜阵列,及用于激光扫描的F-theta镜片,激光头的分光器等,这些微结构光学元件在很多我们日常使用的产品中都有应用,比如手机、掌上电脑、CD和DVD等。
1.3微光学元件加工方法
由于受应用需求的驱动,对微光学元件加工技术的研究也在不断深入,出现了多种现代加工技术,如电子束写技术、激光束写技术、光刻技术、蚀刻技术、LIGA技术,复制技术和镀膜技术等,其中最为成熟的技术是蚀刻技术和LIGA技术。
这些技术基本都是从微电子元器件的微细加工技术发展而来,但与电子原件不同,三维成型精度和装配精度对光学元件来说是至关重要的,将会直接影响其性能,因此这些方法各自都有它自身的缺陷和使用的局限性。
如由于视场深度的限制,光刻技术仅限于二微结构和小深宽比三维结构的加工;采用牺牲层蚀刻技术,虽然
可以实现准三维加工,但易使材料产生内应力,影响最终的机械性能,且设备造价非常昂贵;LIGA技术利用的高准直度的X射线光源,一般要通过同步辐射加速器得到,造价比光刻设备还要高许多,一般实验室和企业都很难负担得起;电子束写技术能够加工纳米级的精密结构,但效率低,难以进行批量生产。
复制技术,包括热压成型法、模压成型法和注射成型法等,是一种适于批量生产的低成本技术,但要求其模具具有较高精度和耐用性。
微光学元件的另一加工方法是超精密机械加工技术。
最近“财富”杂志上有这样一句话:“超精密加工技术对光学元件的作用犹如当初集成电路对电子元件的作用”。
这句话虽然不无夸张,却说明了用超精密机械加工技术进行微光学元件的加工已经引起人们极大的重视。
超精密机械加工技术在微光学元件加工中的应用将在下一节详细论述。