数控加工路线的确定
数控车床加工工艺制定方法及步骤
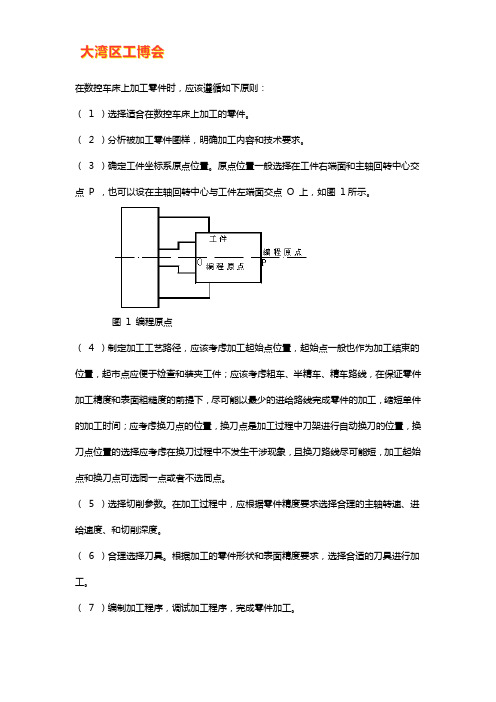
在数控车床上加工零件时,应该遵循如下原则:
(1 )选择适合在数控车床上加工的零件。
(2 )分析被加工零件图样,明确加工内容和技术要求。
(3 )确定工件坐标系原点位置。
原点位置一般选择在工件右端面和主轴回转中心交点P ,也可以设在主轴回转中心与工件左端面交点O 上,如图1所示。
图1 编程原点
(4 )制定加工工艺路径,应该考虑加工起始点位置,起始点一般也作为加工结束的位置,起市点应便于检查和装夹工件;应该考虑粗车、半精车、精车路线,在保证零件加工精度和表面粗糙度的前提下,尽可能以最少的进给路线完成零件的加工,缩短单件的加工时间;应考虑换刀点的位置,换刀点是加工过程中刀架进行自动换刀的位置,换刀点位置的选择应考虑在换刀过程中不发生干涉现象,且换刀路线尽可能短,加工起始点和换刀点可选同一点或者不选同点。
(5 )选择切削参数。
在加工过程中,应根据零件精度要求选择合理的主轴转速、进给速度、和切削深度。
(6 )合理选择刀具。
根据加工的零件形状和表面精度要求,选择合适的刀具进行加工。
(7 )编制加工程序,调试加工程序,完成零件加工。
加工进给路线的确定-2210

加工进给路线的确定来源:数控机床网 作者:数控车床 栏目:行业动态 进给路线是刀具在整个加工工序中相对于工件的运动轨迹,它不但包括了工步的内容,而且也反映出工步的顺序。
进给路线也是编程的依据之一。
加工路线的确定首先必须保持被加工零件的尺寸精度和表面质量,其次考虑数值计算简单、走刀路线尽量短、效率较高等。
因精加工的进给路线基本上都是沿其零件轮廓顺序进行的,因此确定进给路线的工作重点是确定粗加工及空行程的进给路线。
下面将具体分析:(1)加工路线与加工余量的关系在数控车床还未达到普及使用的条件下,一般应把毛坯件上过多的余量,特别是含有锻、铸硬皮层的余量安排在普通车床上加工。
如必须用数控车床加工时,则要注意程序的灵活安排。
安排一些子程序对余量过多的部位先作一定的切削加工。
①对大余量毛坯进行阶梯切削时的加工路线图5-5所示为车削大余量工件的两种加工路线,图(a)是错误的阶梯切削路线,图(b)按1→5的顺序切削,每次切削所留余量相等,是正确的阶梯切削路线。
因为在同样背吃刀量的条件下,按图(a)方式加工所剩的余量过多。
根据数控加工的特点,还可以放弃常用的阶梯车削法,改用依次从轴向和径向进刀、顺工件毛坯轮廓走刀的路线(如图5-6所示)②分层切削时刀具的终止位置当某表面的余量较多需分层多次走刀切削时,从第二刀开始就要注意防止走刀到终点时切削深度的猛增。
如图5-7所示,设以900主偏角刀分层车削外圆,合理的安排应是每一刀的切削终点依次提前一小段距离e(例如可取e=0.05㎜)。
如果e=0,则每一刀都终止在同一轴向位置上,主切削刃就可能受到瞬时的重负荷冲击。
当刀具的主偏角大于900,但仍然接近900时,也宜作出层层递退的安排,经验表明,这对延长粗加工刀具的寿命是有利的。
(a) (b)图5-5 车削大余量毛坯的阶梯路线图5-6 双向进刀走刀路线图5-7 分层切削时刀具的终止位置(2)刀具的切入、切出在数控机床上进行加工时,要安排好刀具的切入、切出路线,尽量使刀具沿轮廓的切线方向切入、切出。
数控机床加工路线的确定

科 之 学 友
Fnfie ar dd e ts e cc me o nA u S
27 0J 0 ̄7固 0 , E
数控机床加 工路线的确定
张士 印
( 台市技术学院 ,山东 烟 台 2 4 0 ) 烟 6 0 6 摘 要: 文章就数控加 工中加工路 线的最近确 定进行 了讨论 , 出了空行程路线如何最短 得
/
\
一 .
’ } ≥
・
Байду номын сангаас
点
:
b 路线 I 图 1最短走刀路线的设计
/
、 、
a 零件图样
C 路线 2
12 合理设置起刀点 . 特别是采用矩形循 环出车外 圆 ,起刀点应设置 在离毛坯较 近的位置 。 13 合理选择换刀点 . 要在保证换刀时不碰工件及机床其他部位 的前提下尽可能的
的时间。 确定进给 路线的工作重点 ,主要 在于确定粗加 工及空行程
后一次走刀 中连续加工出来 。 图 2中 a图所示为用行切方式加 见 工内腔的走刀路线 , 这种走刀方法 能切 除内腔中的全部余量 , 不 留死角 , 不伤轮廓 。但行切法将在两次走刀的起点和终点间 留下 残留高度而达不 到表面要 求的粗糙度 。所 以如采用 图 2中 b图
一
1 9—
维普资讯
科 之 学 友
Fnfie ar rd e ts i cc me eo nA u S
27 0 国 0 ̄ 7 0 月
起砼表 面的早期裂缝 。新浇筑早期拆模 , 在表面引起很大的拉应 力, 出现“ 温度 冲击” 现象 。在砼浇筑初期 , 由于水 化热的散发 , 表 面引起相 当大的拉应 力 , 时表面温度亦较气温为 高 , 此 如果拆 除 模板 , 表面温度骤 降 , 必然引起温 度梯 度 , 从而在 表面 附加一拉 应力, 与水化热应 力迭加 , 再加上 砼干缩 , 表面 的拉应力 达到很 大 的数值 , 就有导致裂缝 的危险。但如果在拆除模板后及时在表 面覆盖一轻 型保 温材 料 , 沫海棉 等 , 于防止砼表面产生过 如泡 对 大 的拉应力 , 具有显著 的效果 。 加筋对大体积砼 的温度应力影响很小 ,因为大体 积砼 的含 筋率极低 , 只是对一般钢筋砼有影 响。在温度不太 高及应力低于 屈服极 限的条件 下 , 的各项性 能是稳定 的 , 与应力状 态 、 钢 而 时 间及温度无关 。钢 的线胀系数与砼线胀系数相差很小 , 在温度变 化时两者间 只发生很小 的内应 力。由于钢的弹性模量 为砼 弹性 模量的 7 1 倍 , 内 应力达到抗拉强度 而开裂时 , 的应 ~5 当 砼 钢筋 力将不超过 10k/ 20 g m , 0 g m ~ 0 / 因此 , 中想要利用钢筋 e kc 在砼 来防止细小裂缝的出现很 困难 。但 加筋 后结构 内的裂缝一般就 变得数 目多 、 间距小 、 宽度与 深度较小 了, 而且 如果钢 筋的直径 细而间距 密时 , 对提 高砼抗裂性的效果较好 。砼和钢筋 砼结构 的
数控加工路线的确定

(1)加工路线的确定原则在数控加工中,刀具刀位点相对于工件运动的轨迹称为加工路线。
确定加工路线是编写程序前的重要步骤,加工路线的确定应遵循以下原则。
1.加工路线应保证被加工零件的精度和表面粗糙度,且效率较高。
2.使数值计算简单,以减少编程工作量。
3.应使加工路线最短,这样既可以减少程序段,又可以减少空刀时间。
此外,确定加工路线时,还要考虑工件的加工余量和机床、刀具的刚度等情况,确定是一次走刀,还是多次走刀来完成加工,以及在铣削加工中是采用顺铣还是逆铣等。
(2)辅助程序段的设计1.轮廓加工的进退刀路径设计在对零件的轮廓进行加工时,为了保证零件的加工精度和表面粗糙度符合要求,应合理地设计进退刀路径。
如图1所示,当铣削平面零件外轮廓时,一般采用立铣刀侧刃切削。
刀具切入工件时,应避免沿零件外廓的法向切入,而应沿外廓曲线延长线的切向切入,以避免在切入处产生刀具的刻痕而影响表面质量,保证零件外廓曲线平滑过渡。
同理,在切离工件时,也应避免在工件的轮廓处直接退刀,而应该沿零件轮廓延长线的切向逐渐切离工件。
图1 外轮廓加工刀具的切入切出图2 内轮廓加工刀具的切入和切出1铣削封闭的内轮廓表面时,若内轮廓曲线允许外延,则应沿切线方向切入切出。
若内轮廓曲线不允许外延(见图2),刀具只能沿内轮廓曲线的法向切入切出,此时刀具的切入切出点应尽量选在内轮廓曲线两几何元素的交点处。
当内部几何元素相切无交点时(见图3),为防止刀具在轮廓拐角处留下凹口,刀具切入切出点应远离拐角。
图3 内轮廓加工刀具的切入和切出2如图4所示,用圆弧插补方式铣削外整圆时,当整圆加工完毕时,不要在切点处直接退刀,而应让刀具沿切线方向多运动一段距离,以免取消刀补时,刀具与工件表面相碰,造成工件报废。
铣削内圆弧时也要遵循从切向切入的原则。
最好安排从圆弧过渡到圆弧的加工路线(见图5,这样可以提高内孔表面的加工精度和加工质量。
本篇文章来源于数控网|原文链接:2.孔加工时引伸距离的确定孔加工在确定轴向尺寸时,应考虑一些辅助尺寸,包括刀具的引入距离和超越距离。
数控技术复习题及参考答案
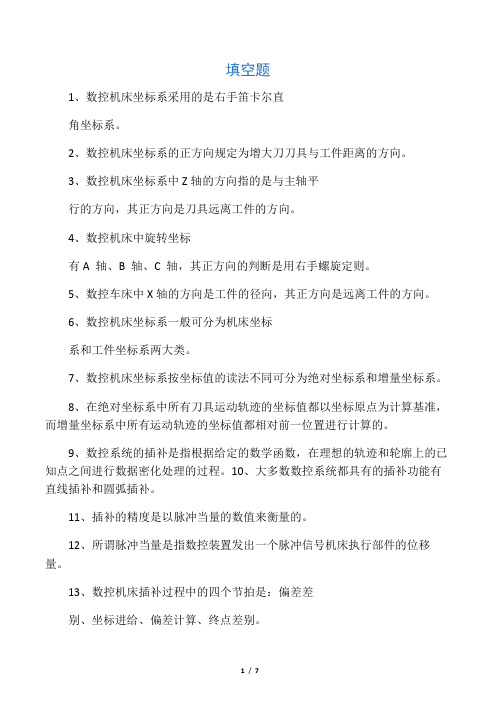
三、简答题
1、绝对坐标系和增量坐标系的区别是什么?举例说明。
答:在绝对坐标系中所有刀具运动轨迹的坐标值都以坐标原点为计算基准,而增量坐标系中所有运动轨迹的坐标值都相对前一位置进行计算的。
2、插补的定义。
答:数控系统的插补是指根据给定的数学函数,在理想的轨迹和轮廓上的已知点之间进行数据密化处理的过程。
8、数控车床的坐标轴是怎样规定的?试按右手笛卡尔坐标系确定数控车床中Z轴和X轴的位置及方向。
答:数控车床的坐标轴是用右手笛卡尔直角坐标系确定的。
Z轴的方向是主轴轴线的方向,其正方向是刀具远离工件的方向。
X轴的方向是垂直主轴轴线的方向,其正方向是刀具远离工件的方向。
9、制定加工方案的要求是什么?
答:制定加工方案的要求有:
11、插补的精度是以脉冲当量的数值来衡量的。
12、所谓脉冲当量是指数控装置发出一个脉冲信号机床执行部件的位移量。
13、数控机床插补过程中的四个节拍是:偏差差
别、坐标进给、偏差计算、终点差别。
14、插补过程中终点判别的具体方法有:单向一、计
数、双向计数、分别计数。
15、数控编程是从零件图样到获得数控机床所能识别的数控加工程序的全过程。
16、数控铣加工中,进退刀位置应选在合适的位置,以保证加工质量。
(√)
17、工作坐标系是编程时使用的坐标系,故又称为编程坐标
系。(√)
18、数控机床坐标系是机床固有的坐标系,一般情况下不允许用户改动。
(√)(√)19、机床参考点是数控机床上固有的机械原点,该点到机床坐标原点在进给坐标轴方向上的距离可以在机床出厂时设定。(√)20、对于既有铣面,又有镗孔的工件,一般先铣面后镗
5、绝对值方式是指控制位置的坐标值均以机床某一固定点为原点来计算计数长度。(√)
浅述数控铣床加工中进给路线的合理确定

f \ 厂、 、 原\ 点
暖弧切人 唐
: 出 对多走 的 距 离 切
开始加工。
图 2 外轮廓h _ 的切入 与切 出 a. X 图 3 外圆铣 削 3 铣 削 内轮 廓 的进 给 路 线 31 铣削封闭的内轮廓表面 , . 若内轮廓曲线 不允许外 延, 刀具 只能沿内 y 轮廓 曲线的法 向切人 、 出 , 切 此时刀 具 的切人 、 切出点应尽量选在内轮廓 曲线 两 几 何 元 素 的交 点 处 。 内部 几 何元 素 当 相 切 无 交点 时 , 防止 刀 补 取 消 时在 轮 为 廓拐角处 留下 凹口, 刀具 切入 、 切出点 应 远 离 拐角 。如 图 4所示 。 32 当用 圆弧插补铣削 内圆弧 时也要 . 遵循从切 向切人 、 出的原 则 , 切 最好 安 排从 圆弧过渡到圆弧的加工路线 , 如图 图 4 内轮 廓 加 工的 切 入 与切 出 5所示 , 这样可 以提高 内孔表 面的加 工
11 顺铣和逆铣 。顺铣 : . 在铣削加工中 , 铣刀的走刀方向与在切削点的 切削分力方 向相 同。 逆铣 : 在铣削加工 中, 铣刀的走刀方向与在切削点的 切 削 分力 方 向相 反 。
如图 1 示 。 所
—]
F1 F I —
l
R
l
图 5 无 交 点 内轮 廓 加 工 的切 入 与 切 出
民 营科 技
21年第5 01 期
科技 论坛
浅述 数控铣 床 加工 中进 给路线 的合理确 定
杨 艳华
( 丹 江 林 业机 械 厂 , 牡 黑龙 江 牡 丹 江 17 0 ) 5 0 0
摘 要 : 数 控 k .. , 具 刀位 点 相 对 于 工 件 运 动 的 轨 迹 称 为 进 给 路 线 , 称 走 刀路 线 。 它 不但 包括 了X 步 的 内容 , 在 X中 刀 - 也 - 而且 也 反 映 出工 步 的 顺 序。 在数控加工 中, 进给路 线是 由数控 系统控制 的。 它对零件的加 工质量 、 加工效率有 直接影响 , 因此 , 工序设计时必须拟 定好 刀具合理的进给路线。 关 键 词 : 铣 床 ; 铣 和 逆 铣 ; 给路 线 数控 顺 进 1 顺 铣 和 逆 铣 的选 择 精 度 和 质量 。
浅谈数控铣削加工工艺路线的确定
浅谈 数控 铣 削 加 工 工 艺路 线 的确 定
杨 洪 岩 魏 领 会 于 济 群 。 , ,
(. 春工 业 大 学 工 程 训练 中心 ;. 春 职 业 技术 学 院 , 1长 2长 吉林 长春 100) 30 0 摘 要 : 章 提 出 了 数 控 铣 削 加 工 过 程 中 的 加 工 工 艺 路 线 的 确 定 原 则 和 选 择 要 点 , 数 控 铣 削 常 用 文 对
样 才 能 进 一 步 提 高 生 产 效 率 、 工 精 度 根 据 零 件 的 加 材 料 、 构 和 技 术 要 求 不 同 , 种 零 件 的 加 工 工 艺 是 结 各 不 同 的 , 使 是 同 类 型 的 零 件 , 于 生 产 条 件 和 批 量 即 由 大 小 的 不 同 , 工 艺 也 不 同 , 此 , 须 根 据 具 体 情 其 因 必 况制定合 理的工 艺路线 。
安 排 好 刀 具 的 切 入 、 出 , 尽 量 避 免 交 接 处 重 复 加 切 要 工 , 则 会 出现 明 显 的 界 限 痕 迹 。 圆弧 插 补 方 式 铣 否 用
按 照 数 控 铣 削 加 工 工 艺 路 线 的确 定 原 则 , 面 下
对某 些典型 零件 的常用加工 路线进行 概略分 析 :
加 工 工 艺 路 线 作 了概 略 分 析 。
关键 词 : 控铣 削; 分 类 号 : TG5 6 0
文献标识码 : A
文 章 编 号 : O 7 6 2 ( 0 O O 一 O 8 ~ O 1 0 — 9 12 1 ) 9 O1 1 标 轴 的 反 向 间 隙 带 入 , 接 影 响 位 置 精 度 。 图 1所 直 如 示 的 孑 系 加 工 路 线 , 按 图 1a 所 示 的路  ̄ J T 时 , L 当 () J n 由 于 5 6孔 与 1 2 3 4孔 定 位 方 向 相 反 , 方 向 反 向 、 、、、 Y 间 隙 会 使 定 位 误 差 增 加 , 影 响 5 6孔 与 其 他 孔 的 而 、
数控加工中工序划分与加工路线的确定
毛刺 、 飞边 , 影响孔的精度 。 d 一次定位原则 对 于加工 中存在重复定位 ) 误 差 的装 夹情 况 , 采 用 一 次 定 位 按顺 序 连 续 换 应 刀, 依次连续加工完成 同一轴线上 的各孔 ( 例如加 。
b )刀具 集 中 原 则
为 减 少 换 刀 次数 , 短 辅 缩
பைடு நூலகம்
助时间 , 应按 刀具 进 入 加工 的顺 序 集 中工 序 。零 件 在 一 次装 夹 中 , 可 能使 用 同一 把 刀具 完 成 较 多的 尽 加 工 表面 。 当一 把 刀具 完 成加 工 的所 有 部位 后 , 尽
为 了充分发挥数控机床的效率 , 保证零件的加
a d t es o ts a hnn o t sslce o p o oe ma h nn r c in a d p o u t n ef in y o n h h retm c i i r u ei ee td t rm t c ii p e i o n r ci fi e c fNC g g s d o c
的 工序 划分 应 遵循 以下原 则 :
般先加工平面 、 定位面 , 后加工孔 ; 先加工简单的
几 何形 状 , 加 工 复 杂 的几 何 形 状 ; 加 工 精 度 较 再 先 低 的部 位 , 加 工 精 度 要 求 高 的 部位 。例 如 , 于 再 对 铣 一 镗复 合 加工 , 般 可 按 先 铣 后 镗 的顺 序 进 行 , 一
摘 要 : 据 数 控加 工 的工 艺特 点 , 力 求采 用 工序 集 中的方 法 , 根 应 并选 取 最 短 的加 工路 线 , 这样 有利 于保 证 零件 的加 工精度 , 高数 控机 床 的 生产 效 率 。 提 关 键词 : 工序 划 分 ; 工路 线 ; 加 数控 加 工 中图分 类 号 : TG1 文献 标识 码 : 文 章编 号 :6 15 7 ( 0 2 O —0 60 6 B 1 7 —2 6 2 0 l40 1 —2
试述数控加工工艺路线的确定
先 将 刀具 在 y 面 内快 速 定 平 位 到孔 中心 线位 置 上 。 然后 刀
具再将按Z 运动进行加工 。 向 对 于位 置 精 度 要 求 较 高 的 孔 系加 工 。 要特 别 注 意安 排各 孔 的加工 顺序 和 加工 路线 。 安 若
排不 当 . 就可 能 带 入 坐标轴 的
入 方 向与切 出方 向 。 在铣 削 加工 中 , 采 用顺铣 还是 逆 是
直接影响孔系的位置精度。 如 图1 孔系 的加工路线图
图 1 系 的 加 工 路 线 为 :一 2 + ( 除 反 向 间 隙 )+ 孔 1 + -3 消 -
6 5 _4。 —+ 一+
() 多 次重 复 的加 工 动 作 , 编 写 子程 序 , 主 5对 可 由 程 序调用 。例 如 。 加工 一 系列孔 径 、 孔深 和孔 的确 定
余 丽 群
f 原 第 一机 床 厂 山 西 太 原 太 0 0 1) 3 0 2
【 摘
要 】 提 出数控加工过程 中的加工工艺路 线的确定原则和选择要 点, 以保证加工质量 , 高生产效率。 提 数控加工 加工质量 【 文章编号 】 10 — 7 X(0 6 0 — 0 2 0 0 3 7 3 2 0 )2 0 6 — 2 【 文献标识码 】 B
加工 内容也 反映 加工顺 序 , 编程 工作 的主 要依 据 。 是 1 加 工工 艺路 线的确 定 原则
加工工艺路线合理与否 ,关系到零件的加工质量
与生产 效率 。 在确 定加 工工 艺路线 时 , 综合 考虑 在保 应 证 加工 精度 的前 提下 .应 最 大限度 地缩 短 加 工工 艺路 线 。所 以数 控加 工工 艺路 线应 遵循 以下 原 则 : ( ) 证产 品质量 , 将 保证零 件 的 加工 精度 和 表 1保 应 面粗糙 度要 求放 在首 位 。 ( ) 高劳 动生 产率 和 降低生 产成 本 。 保 证零件 2提 在 加工 质量 的前提 下 , 应力 求 加工路 线 最短 , 尽 量减 少 并 空行程 时 间 , 高加 工效 率 。 提 () 满 足零 件 加 工 质量 、 产效 率 等 条 件 下 , 3在 生 尽
数控车床加工零件的顺序【详解】
在选定加工方法、划分工序后,接下来就是合理安排工序的顺序。
零件的加工工序通常包括切削加工工序、热处理工序和辅助工序,合理安排好切削加工、热处理和辅助工序的顺序,并解决好工序间的衔接问题,可以提高零件的加工质量生产效率,降低加工成本。
在数控车床上加工零件,应按工序集中的原则划分工序,安排零件车削加工顺序一般遵循下列原则。
1.数控车床在零件加工中先粗后精按照粗车→半精车→精车的顺序进行,逐步提高零件的加工精度。
粗车将在较短的时间内将工件表面上的大部分加工余量切掉,这样既提高了金属切除率,又满足了精车余量均匀性要求。
若粗车后所留余量的均匀性满足不了精加工的要求,则要安排半精车,以便使精加工的余量小而均匀。
精车时,刀具沿着零件的轮廓一次走刀完成,以保证零件的加工精度。
首先进行粗加工,将虚线包围部分切除,然后进行半精加工和精加工。
2.数控车床在零件加工中先近后远这里所说的远与近,是按加工部位相对于换刀点的距离大小而言的。
通常在粗加工时,离换刀点近的部位先加工,离换刀点远的部位后加工,以便缩短刀具移动距离,减少空行程时间,并且有利于保持坯件或半成品件的刚性,改善其切削条件。
例如,当加工如图2.8所示零件时由于余量较大,粗车时,可按先车端面,再按40mm→35mm→29mm→23mm的顺序加工;精车时,如果按40mm35mm→29mm→23mm的顺序安排车削,不仅会增加刀具返回换刀点所需的空行程时间,而且还可能使台阶的外直角处产生毛刺,应该按23mm→29mm→35m→40mm的顺序加工。
如果余量不大则可以直接按直径由小到大的顺序一次加工完成,符合先近后远的原则,即离刀具近的部位先加工,离刀具远的部位后加工。
3. 数控车床在零件加工中内外交叉对既有内表面(内型、内腔)又有外表面的零件,安排加工顺序时,应先粗加工内、外表面,然后精加工内、外表面。
加工内、外表面时,通常先加工内型和内腔,然后加工外表面。
原因是控制内表面的尺寸和形状较困难,刀具刚性相应较差,刀尖(刃)的耐用度易受切削热的影响而降低,以及在加工中清除切屑较困难等。
- 1、下载文档前请自行甄别文档内容的完整性,平台不提供额外的编辑、内容补充、找答案等附加服务。
- 2、"仅部分预览"的文档,不可在线预览部分如存在完整性等问题,可反馈申请退款(可完整预览的文档不适用该条件!)。
- 3、如文档侵犯您的权益,请联系客服反馈,我们会尽快为您处理(人工客服工作时间:9:00-18:30)。
(1)加工路线的确定原则
在数控加工中,刀具刀位点相对于工件运动的轨迹称为加工路线。
确定加工路线是编写程序前的重要步骤,加工路线的确定应遵循以下原则。
1.加工路线应保证被加工零件的精度和表面粗糙度,且效率较高。
2.使数值计算简单,以减少编程工作量。
3.应使加工路线最短,这样既可以减少程序段,又可以减少空刀时间。
此外,确定加工路线时,还要考虑工件的加工余量和机床、刀具的刚度等情况,确定是一次走刀,还是多次走刀来完成加工,以及在铣削加工中是采用顺铣还是逆铣等。
(2)辅助程序段的设计
1.轮廓加工的进退刀路径设计在对零件的轮廓进行加工时,为了保证零件的加工精度和表面粗糙度符合要求,应合理地设计进退刀路径。
如图1所示,当铣削平面零件外轮廓时,一般采用立铣刀侧刃切削。
刀具切入工件时,应避免沿零件外廓的法向切入,而应沿外廓曲线延长线的切向切入,以避免在切入处产生刀具的刻痕而影响表面质量,保证零件外廓曲线平滑过渡。
同理,在切离工件时,也应避免在工件的轮廓处直接退刀,而应该沿零件轮廓延长线的切向逐渐切离工件。
图1 外轮廓加工刀具的切入切出
图2 内轮廓加工刀具的切入和切出1
铣削封闭的内轮廓表面时,若内轮廓曲线允许外延,则应沿切线方向切入切出。
若内轮廓曲线不允许外延(见图2),刀具只能沿内轮廓曲线的法向切入切出,此时刀具的切入切出点应尽量选在内轮廓曲线两几何元素的交点处。
当内部几何元素相切无交点时(见图3),为防止刀具在轮廓拐角处留下凹口,刀具切入切出点应远离拐角。
图3 内轮廓加工刀具的切入和切出2
如图4所示,用圆弧插补方式铣削外整圆时,当整圆加工完毕时,不要在切点处直接退刀,而应让刀具沿切线方向多运动一段距离,以免取消刀补时,刀具与工件表面相碰,造成工件报废。
铣削内圆弧时也要遵循从切向切入的原则。
最好安排从圆弧过渡到圆弧的加工路
线(见图5,这样可以提高内孔表面的加工精度和加工质量。
本篇文章来源于数控网| 原文链接:/Prog/Basis/2009-03-25/1134.html
2.孔加工时引伸距离的确定孔加工在确定轴向尺寸时,应考虑一些辅助尺寸,包括刀具的引入距离和超越距离。
数控钻孔的尺寸关系如图6所示,图中各参数的含义如下。
Zd——被加工孔的深度(mm);
ΔZ——具的轴向引入距离(mm),其经验数据为已加工面钻、镗、铰孔ΔZ=1-3mm;毛面上钻ΔZ=5-8mm;铣削前攻螺纹时ΔZ=5-10mm;
图4 外圆铣削
图5 内圆铣削
图6 数控钻孔的尺寸关系
Zp——钻孔深度(mm)。
Zp=Deot++/2=0.3d
Zf——刀具轴向位移量,即程序中的坐标尺寸(mm),
Zp=Zd+ΔZ+Zp
钻孔时刀具超越距离为1 / / 3mm。
3.螺纹加工的引伸距离的确定在数控车床上车螺纹时,沿螺距方向的Z向进给应和车床主轴的旋转保持严格的速度比例关系,因此应避免在进给机构加速或减速的过程中切削。
为此要有引入距离ε1和超越距离ε2。
如图7所示,ε1和ε2的数值与车床拖动系统的动态特性、螺纹的螺距和精度有关。
一般ε1为2-5mm,对大螺距和高精度的螺纹取大值;ε2一般取ε1的1 / 4 左右。
若螺纹收尾处没有退刀槽时,收尾处的形状与数控系统有关,一般按45°退刀收尾。
图7 切削螺纹时的引入与超越距离
(3)孔加工路线的确定
孔加工时的加工路线确定,应根据技术条件按加工路线最短或加工精度最高的原则,同时,还应考虑孔加工时的引伸距离。
对于点位控制的数控机床,只要求定位精度较高,定位过程尽可能地快,而刀具相对于工件的运动路径无关紧要,因此这类机床应按路径最短来安排走刀路线。
对于位置要求较高的孔系加工,特别要注意孔的加工顺序的安排。
在精镗孔系时,镗孔路线一定要注意各孔的定位方向一致,即采用单向趋近定位点的方法,以避免传动系统反向间隙误差对定位精度的影响。
例如,加工图8(a)所示的孔系,在该零件上镗6个尺寸相同的孔,当按加工路线最短原则确定的走刀路线如图8(b)所示。
由于5、6孔与1-4孔定位方向相反,Y方向反向间隙会使定位误差增加,而影响5、6孔与其他孔的位置精度。
如按定位精度最高的原则确定孔加工路线,如图8(c)所示,按此加工路线,加工完4孔后往Y正方向多移动一段距离到P点,然后再折回来加工5、6孔,这样各孔的定位方向一致,可以避免反向间隙的引入,提高了5、6孔的位置精度。
本篇文章来源于数控网| 原文链接:/Prog/Basis/2009-03-25/1134_2.html
4)内型腔加工路线设计
铣削内型腔轮廓表面时,切入和切出无法外延,这时铣刀可沿零件轮廓的法线方向切入和切出,并将其切入、切点选在零件轮廓两几何元素的交点处。
图9所示为加工凹槽的3种加工路线。
其中图(a)和(b)分别为用行切法加工和环切法加工凹槽的走刀路线;图(c)为先用行切法,最后环切一刀光整轮廓表面。
三种方案中,(a)图方案最差,(c)图方案最好。
轮廓加工中应避免进给停顿。
因为加工过程中的切削力会使工艺系统产生弹性变形并处于相对平衡状态,进给停顿时,切削力突然减小,会改变系统的平衡状态,刀具会在进给停顿处的零件轮廓上留下刻痕。
为提高工件表面的精度和减小粗糙度,可以采用多次走刀的方法,精加工余量一般以0.2-0.5为宜。
而且精铣时宜采用顺铣,以减小零件被加工表面粗糙度的值。
图8 孔加工路线的确定
图9 凹槽加工走刀路线
图10 曲面加工的走刀路线
(5)曲面加工路线的确定
铣削曲面时,常用球头刀采用行切法进行加工。
所谓行切法是指刀具与零件轮廓的切点轨迹是一行一行的,而行间的距离是按零件加工精度的要求确定的。
对于边界敞开的曲面加工,可采用两种走刀路线。
图10所示为发动机大叶片,采用图10(a)所示的加工方案时,每次沿直线加工,刀位点计算简单,程序少,加工过程符合直纹面的形成,可以准确保证母线的直线度。
当采用图10(b)所示的加工方案时,符合这类零件数据给出情况,便于加工后检验,叶形的准确度较高,但程序较多。
由于曲面零件的边界是敞开的,没有其他表面限制,所以边界曲面可以延伸,球头刀应由边界外开始加工。
【整理】
本篇文章来源于数控网| 原文链接:/Prog/Basis/2009-03-25/1134_3.html。