数控铣削加工的走刀路线
数控铣削加工的走刀路线

数控铣削加工的刀路线反映了工序的加工过程,走刀路线合理与否,关系到工件的加工质量与生产效率。
尤其在数控铣削曲面零件过程中,应认真分析零件的加工要求及其结构特点,找出走刀路线中影响加工效率的因素,在保证零件加工精度和表面粗糙度要求的前提下,应尽量缩短加工路线,从而提高数控机床的加工效率,降低加工成本。
数控加工过程中刀具相对于工件的运动轨迹称为走刀路线。
走刀路线反映了工序的加工过程,确定合理的走刀路线是保证铣削加工精度和表面质量的重要工艺措施之一,也是确定数控编程的前提。
数控铣削加工中走刀路线对工件的加工精度和表面质量有直接的影响,走刀路线合理与否,还关系到加工的生产效率,因此每道工序走刀路线的确定都是非常重要的。
一、走刀路线的确定原则影响走刀路线的因素很多,有工艺方法、工件材料及状态、加工精度及表面粗糙度要求、工件刚度、加工余量、刀具的刚度及耐用度、机床类型和工件的轮廓形状等。
在确定走刀路线时,主要应遵循以下原则:(1)保证产品质量,应将保证工件的加工精度和表面粗糙度要求放在首位。
(2)在保证工件加工质量的前提下,应力求走刀路线最短,并尽量减少空行程时间,提高加工效率。
(3)在满足工件加工质量、生产效率等条件下,尽量简化数学处理的数值计算工作量,以简化编程工作。
此外,在确定走刀路线时,还要综合考虑工件、机床与刀具等多方面因素,确定一次走刀还是多次走刀,以及设计刀具的切入点与切出点,切入方向与切出方向。
在铣削加工中,还要确定是采用顺铣还是逆铣等。
二、铣削方式的选择铣削有顺铣和逆铣两种方式。
铣削加工中是采用顺铣还是逆铣,对工件表面粗糙度有较大的影响。
确定铣削方式应根据工件的加工要求,材料的性质、状态、使用机床及刀具等条件综合考虑。
由于采用顺铣方式,工件加工表面质量较好,刀齿磨损小,因此,一般情况下,尽可能采用顺铣,尤其是精铣内外轮廓、精铣铝镁合金、钛合金或耐热合金时,应尽量按顺铣方式安排走刀路线。
三、铣削曲面类零件走刀路线的确定铣削曲面类零件的走刀路线加工面为空间曲面的零件称为曲面类零件。
数控加工走刀路线图介绍

14.4 数控加工走刀路线图
数控加工走刀路线图零件图号工序号 2 工步号 2 程序号O0002 机床型号KV650 程序段号加工内容铣心型轮廓共 6 页第 2 页
编程
校对
审批
符号
含义抬刀下刀编程原点起刀点
走刀
方向
走刀线
相交
爬斜坡铰孔行切数控加工走刀路线图零件图号工序号 3 工步号 3 程序号O0003 机床型号KV650 程序段号加工内容挖槽共 6 页第 3 页
编程
校对
审批符号
含义抬刀下刀编程原点起刀点走刀
方向
走刀线
相交
爬斜坡铰孔行切
数控加工走刀路线图零件图号工序号 5 工步号5-8 程序号O0005
钻孔
编程
校对
审批符号
含义抬刀下刀编程原点起刀点走刀
方向
走刀线
相交
爬斜坡铰孔行切
数控加工走刀路线图零件图号工序号 6 工步号13 程序号O0006 机床型号KV650 程序段号加工内容加工内球面共 6 页第 6 页
编程
校对
审批。
数控铣床编程模块6 曲面类零件加工

1 用户宏程序
变量
①空变量#0:该变量总是空的,不能赋值给该变量。 ②局部变量#1~#33:在用户宏程序中局部使用的变量。 ③公共变量:公共变量是在主程序及调用的子程序中通用的变量,分为保持型 变量#500~#999与操作型变量#100~#199两种。操作型(非保持型)变量断电后就 被清零,保持型变量断电后仍被保存。 ④系统变量:系统变量是根据用途而被固定的变量。
2 B类宏程序
(1)B类宏程序变量的赋值
引数 A B C D E F
变量 #1 #2 #3 #7 #8 #9
引数 H I J K M Q
变量 #ll #4 #5 #6 #13 #17
引数 R S T U V W
变量 #18 #19 #20 #2l #22 #23
三轴联动加工曲面走刀路线
三轴联动加工常用复杂空间 曲面的精确加工,但是编程计算 较为复杂,所用机床的数控装置 也必须具备三轴联动加功能。
2 曲面零件铣削加工方法
对叶轮、螺旋桨这样零件的 空间曲面,但困其曲面形状复杂 ,刀具容易与相邻表面干涉,需 常采用四轴或五轴联动加工。即 三个直角线性轴运动外,为防止 加工干涉,刀具还做沿坐标轴形 成的摆角运动。
3 曲面加工的切削行距
采用球头加工曲面精曲面时,同一刀具轨迹所在的平面称为截平面,截 平面之间距离称为行距。行路间残留余量高度的最大值称为残余高度,残 余高度与球形铣刀的直径、行距有关。在实际加工中,通常根据要求的残 余高度值来反推计算行距值,再通过行距来控制残余高度。
铣削平面时的残余高度
铣削斜面时的残余高度
3 曲面加工的切削行距
根据上述分析,为尽可能加大走刀行距以提高加工效率,可采取以下优化措施: l)合理选择刀具:除了凹曲面时为避免干涉而必须采用球头刀加工外,应优先考虑 使用非球面刀进行加工,以获得较高的加工效率和较好的表面质量。此外,还应选择 较大直径的刀具加工以提高刀具刚度和增大行距。 2)合理选择工件安装方位:平底刀或环形刀加工时,应使工件表面各处法矢与Z 轴 的夹角尽可能小以增大行距。此外,在加工凹曲面时选择的工件安装方位应不存在刀 具干涉。鼓形刀加工时,应使工件表面各处法矢与Z 轴的夹角尽可能大以增大行距。 3)合理选择进给方向:平底刀或环形刀加工时,选择的进给方向应使进给方向角尽 可能小。而鼓形刀加工时则相反。此外,应选择曲面曲率较小的方向作为行进给方向 ,但它对行距的影响比进给方向对行距的影响小。
数控加工工艺路线设计
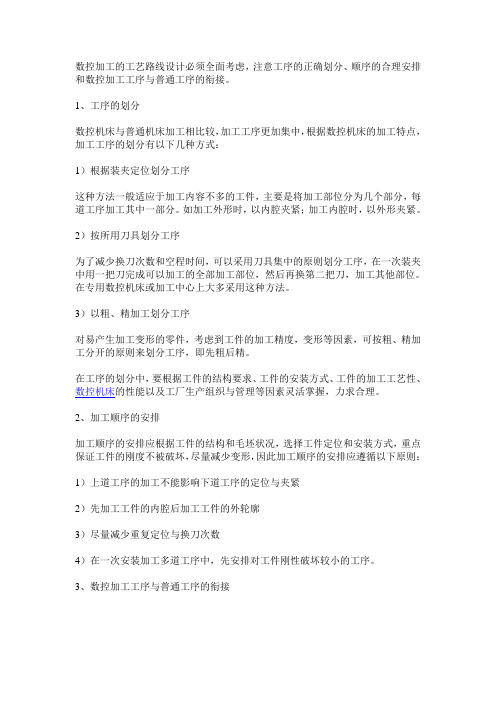
数控加工的工艺路线设计必须全面考虑,注意工序的正确划分、顺序的合理安排和数控加工工序与普通工序的衔接。
1、工序的划分数控机床与普通机床加工相比较,加工工序更加集中,根据数控机床的加工特点,加工工序的划分有以下几种方式:1)根据装夹定位划分工序这种方法一般适应于加工内容不多的工件,主要是将加工部位分为几个部分,每道工序加工其中一部分。
如加工外形时,以内腔夹紧;加工内腔时,以外形夹紧。
2)按所用刀具划分工序为了减少换刀次数和空程时间,可以采用刀具集中的原则划分工序,在一次装夹中用一把刀完成可以加工的全部加工部位,然后再换第二把刀,加工其他部位。
在专用数控机床或加工中心上大多采用这种方法。
3)以粗、精加工划分工序对易产生加工变形的零件,考虑到工件的加工精度,变形等因素,可按粗、精加工分开的原则来划分工序,即先粗后精。
在工序的划分中,要根据工件的结构要求、工件的安装方式、工件的加工工艺性、数控机床的性能以及工厂生产组织与管理等因素灵活掌握,力求合理。
2、加工顺序的安排加工顺序的安排应根据工件的结构和毛坯状况,选择工件定位和安装方式,重点保证工件的刚度不被破坏,尽量减少变形,因此加工顺序的安排应遵循以下原则:1)上道工序的加工不能影响下道工序的定位与夹紧2)先加工工件的内腔后加工工件的外轮廓3)尽量减少重复定位与换刀次数4)在一次安装加工多道工序中,先安排对工件刚性破坏较小的工序。
3、数控加工工序与普通工序的衔接由于数控加工工序穿插在工件加工的整个工艺过程之中,各道工序需要相互建立状态要求,如加工余量的预留,定位面与孔的精度和形位公差要求,矫形工序的技术要求,毛坯的热处理等要求,各道工序必须前后兼顾综合考虑。
4、数控机床加工工序和加工路线的设计数控机床加工工序设计的主要任务:确定工序的具体加工内容、切削用量、工艺装备、定位安装方式及刀具运动轨迹,为编制程序作好准备。
其中加工路线的设定是很重要的环节,加工路线是刀具在切削加工过程中刀位点相对于工件的运动轨迹,它不仅包括加工工序的内容,也反映加工顺序的安排,因而加工路线是编写加工程序的重要依据。
详述数控铣床的对刀流程
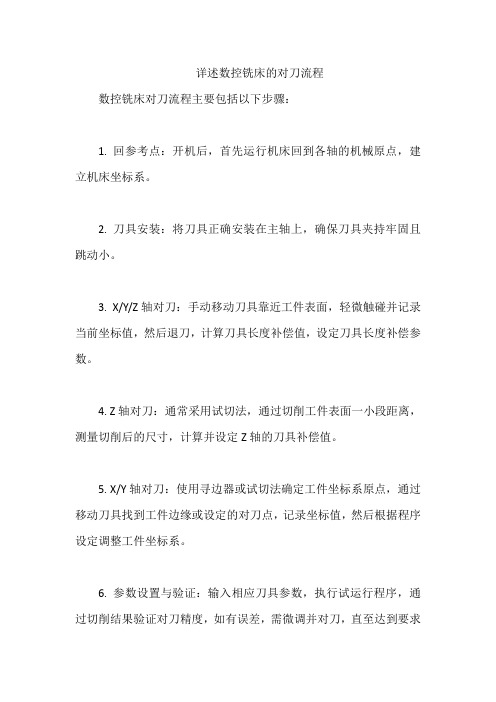
详述数控铣床的对刀流程
数控铣床对刀流程主要包括以下步骤:
1. 回参考点:开机后,首先运行机床回到各轴的机械原点,建立机床坐标系。
2. 刀具安装:将刀具正确安装在主轴上,确保刀具夹持牢固且跳动小。
3. X/Y/Z轴对刀:手动移动刀具靠近工件表面,轻微触碰并记录当前坐标值,然后退刀,计算刀具长度补偿值,设定刀具长度补偿参数。
4. Z轴对刀:通常采用试切法,通过切削工件表面一小段距离,测量切削后的尺寸,计算并设定Z轴的刀具补偿值。
5. X/Y轴对刀:使用寻边器或试切法确定工件坐标系原点,通过移动刀具找到工件边缘或设定的对刀点,记录坐标值,然后根据程序设定调整工件坐标系。
6. 参数设置与验证:输入相应刀具参数,执行试运行程序,通过切削结果验证对刀精度,如有误差,需微调并对刀,直至达到要求
精度。
铣削刀具走刀路线的最基本原则

球头铣刀在进行水平方向进刀时的零切削速度点 仿形铣削是传统的型腔精铣与半精铣加工方式,
刀具一般使用球头立铣刀,采用图中所示 的编程方法进行加工。这种铣削方式来自 于液压仿形铣床的靠模铣削方式。如果照 搬到数控机床上来使用,有如下的缺点
刀具频繁地切入与切出工件,造成刀具刃口容易 因振动而崩刃。
仿形铣削走刀方式,常用刀具和数控 语句中走刀量的倍率调整。
Ve = 0
仿形铣削中刀具在进出工件和触及型 腔根部时,余量变化对刀具的冲击
球头铣刀在进行水平方 向进刀时的零切削速度 点
二、轮廓铣削contouring
轮廓加工方式是推荐的型腔半精铣或精铣的数控编程方 式,此种方式有如下优点:
刀具的切削速度是稳定而持续的,并且避免了球头铣刀 顶端的零切削速度点,最大发挥刀具大直径点切 削速度高的优势。并且特别适合在四轴以上联动 机床上使用,有效利用球头立铣刀大直径加工; 以及高速铣削。
7.5.1 型腔粗加工
Pre-drilled entrance holes
上面所示的平面铣削编程方式,告诉我 们在编程时要尽量减少刀具的切入切出 次数,避免对刀具刃口的冲击。加工面 上如有孔或槽,尽可能安排在后续工序 中完成,这在耐热合金钢材料的面铣加 工时尤其重要。此外面铣削加工刀具走 刀编程时,当加工到孔、槽区域上方时 ,将推荐的进给速率降低25%。 当切削大平面时,选择刀具路径以保持 铣刀完全与其接触,而不是在执行几次 平行走刀。当铣刀进给需变换走刀方向 时,应用执行小直径圆弧转弯路径,以 保持刀具是持续运动的。从而避免出现 停顿和振颤。
方法二、仍采用大直径的铣刀,但是不将圆角靠满,而是 预留余量,给下面的刀具做插铣或摆线铣。尤其对于较深
。 型腔要求过角铣刀较长的时候
铣削刀具走刀路线的最基本原则
如果采用往复式走刀,那么来程河去程各自为顺 铣和逆铣方式切削,造成刀具弹变刀痕及 表面质量的差异,并且逆铣对刃口寿命有 负作用。
需要更长的数控程序语句和较长的切削时间。 刀具在到达型腔底部时因为余量突然变化,导致
刀具弹变产生过切或让刀,使腔底形状产 生误差,为了减少这种影响,需要在此处 减小刀具进给速度,这又造成编程复杂。
7.3 面铣刀的直径和位置
F
F
n
n
Ra
铣刀直径比工件稍宽,此情形的面铣削是 比较理想的切削状态,一般面铣刀的直径 选择,推荐大于工件宽度20%,最大不超 过50%。面铣刀铣削时,刀具中心总是要 求稍微偏离工件中心,此时,每个刀片形 成的切口非常小。如果使面铣刀中心完全 与工件中心一致,就会出现非常不利的情 况,当切削刃进入和退出时,大小平均的 径向切削力会在方向上左右不断变化,引 起机床主轴振动,从而导致损坏;还可能 导致刀片破碎,形成很差的表面质量。
球头铣刀在进行水平方向进刀时的零切削速度deptnameproject二轮廓铣削contouring轮廓铣削走刀方式和常用刀具在四轴联动机床上使用球头铣刀进行水平方向进刀使用大圆弧刀尖角的整体硬质合金立铣刀进行淬硬钢的型腔粗铣削高速铣削hsm轮廓加工方式是推荐的型腔半精铣或精铣的数控编程方式此种方式有如下优点
球头铣刀在进行水平方向进刀时的零切削速度点 仿形铣削是传统的型腔精铣与半精铣加工方式,
刀具一般使用球头立铣刀,采用图中所示 的编程方法进行加工。这种铣削方式来自 于液压仿形铣床的靠模铣削方式。如果照 搬到数控机床上来使用,有如下的缺点
刀具频繁地切入与切出工件,造成刀具刃口容易 因振动而崩刃。
仿形铣削走刀方式,常用刀具和数控 语句中走刀量的倍率调整。
8-数控铣削加工的工艺路线的拟定
垂直切入切出: 优点: 编程快捷 缺点:刀具会在切入点留 下刀痕
圆弧切入、切出 优点:
切入、切出点平滑流畅, 表面质量高
缺点:编程繁杂,需增 加圆弧进刀和退刀
钻孔时刀具路线的设 计力Байду номын сангаас最短
此刀具较上一个路线长, 且繁杂,不宜采用
行切法铣削平面刀具路线
环切法铣削平面刀具路线
挖槽类加工适宜的螺旋下刀 方式
• 图片等\手功派 52年做减法,再造象牙佛韵 超清(720P).qlv • 图片等\手功派 练了一辈子刀法,她终于可以出刀无悔 超清(720P).qlv
作业: 编制数 控铣床 加工工 艺
数控铣削加工的工艺路线的拟定
• 数控铣加工流程: • 对零件图样进行工艺分析,确定加工方案 • 编写零件加工程序单 • 输入或传输零件的加工程序 • 进行程序校验和刀路模拟 • 正确操作机床,完成零件的加工
一、对零件图样进行工艺分析,确定加工方案 1、确定加工设备:加工内容是钻两孔可选择的 机床有钻床、铣床、数控铣床和加工中心,如 果是单件加工,可利用钻床或铣床,手工操作 完成,准备周期短;如果是大批量加工,应选 择数控铣床或加工中心,一次准备长期加工, 又由于加工此零件刀具数量较多,故采用加工 中心,效率更高 2、确定装夹方案:毛坯是一块磨削加工好的方 料,根据毛坯的形状,可采用机用平口虎钳装 夹,如果是批量加工,需设置靠模 3、设计加工方案:Φ18孔属自由公差,可直接 由钻头钻孔得到 Φ 18+0.03公差要求较高,应先用Φ 17.8钻头 钻底孔,再用Φ18铰刀或镗孔刀进行精加工, 因为另有圆度要求,故选择镗孔加工,能更好 的保证圆度要求 4、设计走刀路线: 走刀路线不仅反映加工内 容,也反映加工顺序,是编程的依据:保证各 精度要求、路线最短、尽可能简化
数控加工路线的确定
(4)选择使工件在加工后变形小的路线
对横截面积小的细长零件或薄板零 件应采用分几次走刀加工到最后尺 寸或对称去除余量法安排走刀路线, 安排工步时,应先安排对工件刚性 破坏较小的工步。
(5)根据加工质量要求和工件毛坯的质量及材料, 选择好铣削的方式(顺铣或逆铣)。
6)孔加工时的加工路线确定,应根据技术
条件按加工路线最短或加工精度最高的原则, 同时,还应考虑孔加工时的引伸距离。 对于点位控制的数控机床,只要求定位 精度较高,定位过程尽可能地快,而刀具相 对于工件的运动路径无关紧要,因此这类机 床应按路径最短来安排走刀路线。 对于位置要求较高的孔系加工,特别要 注意孔的加工顺序的安排。在精镗孔系时, 镗孔路线一定要注意各孔的定位方向一致, 即采用单向趋近定位点的方法,以避免传动 系统反向间隙误差对定位精度的影响。
加工路线的确定
铣削内外圆时加工路线的确定 当铣切内圆时也应该遵循此 种切入的方法。最好安排从 圆弧过渡到圆弧的加工路线。 切出时也应多安排一段过渡 圆弧再退刀,这样可以降低 接刀处的接痕,从而可以降 低孔加工的粗糙度和提高孔 加工的精度,图是铣切内圆 的加工路线示意图。
切入、切出路径
铣削内轮廓的切入切出路径
b)路线1
c)路线2
交错加工内、 外圈孔,减少
空刀时间。
(a) (a)
(b) (b)
最短加工路线选择
2、确定对刀点与换刀点
刀具与工件原点 X 轴方向之距离
刀具与工件原点 Z 轴方向之距离
刀具与工件原点 Y 轴方向之距离
确定对刀点与换刀点
对于数控机床来说,在加工开始时,确定 刀具与工件的相对位置是很重要的,它是 通过对刀点来实现的。
对刀点
指通过对刀确定刀具与工件相 对位置的基准点。
《数控加工技术》数控编程技巧(1) 教你怎么样确定走刀路线和安排加工顺序
数控编程技巧:教你怎么样确定走刀路线和安排加工顺序
数控工序设计的主要任务是进一步把本工序的加工内容、切削用量、工艺装备、定位夹紧方式及刀具运动轨迹确定下来,为编制加工程序作好准备。
走刀路线就是刀具在整个加工工序中的运动轨迹,它不但包括了工步的内容,也反映出工步顺序。
走刀路线是编写程序的依据之一。
确定走刀路线时应注意以下几点:
1.寻求最短加工路线,减少空刀时间以提高加工效率
如加工图1a所示零件上的孔系。
b图的走刀路线为先加工完外圈孔后,再加工内圈孔。
若改用c图的走刀路线,则可节省定位时间近一倍。
a
b
c
图1 最短走刀路线的设计
2.为保证工件轮廓表面加工后的粗糙度要求,最终轮廓应安排在最后一次走刀中连续加工出来
如图2a为用行切方式加工内腔的走刀路线,这种走刀能切除内腔中的全部余量,不留死角,不伤轮廓。
但行切法将在两次走刀的起点和终点间留下残留高度,而达不到要求的表面粗糙度。
所以如采用b图的走刀路线,先用行切法,最后沿周向环切一刀,光整轮廓表面,能获得较好的效果。
图2c也是一种较好的走刀路线方式。
a
b
c
图2 铣切内腔的三种走刀路线
3.考虑刀具的进、退刀(切入、切出)路线
刀具的切出或切入点应在沿零件轮廓的切线上,以保证工件轮廓光滑;应避免在工件轮廓面上垂直上、下刀而划伤工件表面;尽量减少在轮廓加工切削过程中的暂停(切削力突然变化造成弹性变形),以免留下刀痕,如图3所示。
图3刀具切入和切出时的外延
4.选择使工件在加工后变形小的路线
对横截面积小的细长零件或薄板零件应采用分几次走刀加工到最后尺寸或对称去除余量法安排走刀路线。
- 1、下载文档前请自行甄别文档内容的完整性,平台不提供额外的编辑、内容补充、找答案等附加服务。
- 2、"仅部分预览"的文档,不可在线预览部分如存在完整性等问题,可反馈申请退款(可完整预览的文档不适用该条件!)。
- 3、如文档侵犯您的权益,请联系客服反馈,我们会尽快为您处理(人工客服工作时间:9:00-18:30)。
数控铣削加工的刀路线
反映了工序的加工过程,走刀路线合理与否,关系到工件的加工质量与生产效率。
尤其在数控铣削曲面零件过程中,应认真分析零件的加工要求及其结构特点,找出走刀路线中影响加工效率的因素,在保证零件加工精度和表面粗糙度要求的前提下,应尽量缩短加工路线,从而提高数控机床的加工效率,降低加工成本。
数控加工过程中刀具相对于工件的运动轨迹称为走刀路线。
走刀路线反映了工序的加工过程,确定合理的走刀路线是保证铣削加工精度和表面质量的重要工艺措施之一,也是确定数控编程的前提。
数控铣削加工中走刀路线对工件的加工精度和表面质量有直接的影响,走刀路线合理与否,还关系到加工的生产效率,因此每道工序走刀路线的确定都是非常重要的。
一、走刀路线的确定原则
影响走刀路线的因素很多,有工艺方法、工件材料及状态、加工精度及表面粗糙度要求、工件刚度、加工余量、刀具的刚度及耐用度、机床类型和工件的轮廓形状等。
在确定走刀路线时,主要应遵循以下原则:
(1)保证产品质量,应将保证工件的加工精度和表面粗糙度要求放在首位。
(2)在保证工件加工质量的前提下,应力求走刀路线最短,并尽量减少空行程时间,提高加工效率。
(3)在满足工件加工质量、生产效率等条件下,尽量简化数学处理的数值计算工作量,以简化编程工作。
此外,在确定走刀路线时,还要综合考虑工件、机床与刀具等多方面因素,确定一次走刀还是多次走刀,以及设计刀具的切入点与切出点,切入方向与切出方向。
在铣削加工中,还要确定是采用顺铣还是逆铣等。
二、铣削方式的选择
铣削有顺铣和逆铣两种方式。
铣削加工中是采用顺铣还是逆铣,对工件表面粗糙度有较大的影响。
确定铣削方式应根据工件的加工要求,材料的性质、状态、使用机床及刀具等条件综合考虑。
由于采用顺铣方式,工件加工表面质量较好,刀齿磨损小,因此,一般情况下,尽可能采用顺铣,尤其是精铣内外轮廓、精铣铝镁合金、钛合金或耐热合金时,应尽量按顺铣方式安排走刀路线。
三、铣削曲面类零件走刀路线的确定
铣削曲面类零件的走刀路线加工面为空间曲面的零件称为曲面类零件。
在机械加工中,常会遇到各种曲面类零件,如模具或螺旋桨叶片等。
由于这类零件型面复杂,需用多坐标联动加工,因此多采用数控铣床或数控加工中心进行加工。
规划这类曲面的粗、精加工刀具运动轨迹时,常用球头刀采用行切法及环切法进行加工,可选择环切走刀方式或行切走刀方式。
所谓“行切法”是指刀具与零件轮廓的切点轨迹是一行一行平行的,而行间的距离是按零件加工精度的要求确定的。
图1为加工某曲面的三种走刀路线,即沿参数曲面的U向行切方式、沿V向行切方式和环切方式。
对
于直母线类表面,采用图1b的方案显然更有利,每次沿直线走刀,刀位点计算简单,程序段小,而且加工过程符合直纹面的形成,可以准确保证母线的直线度。
图1a方案的优点是便于在加工后检验型面的准确度。
实际生产中最好将以上两种方案结合起来。
图1c所示的环切方案一般应用在内槽加工中,而在型面加工中由于编程麻烦,一般不用。
当工件的边界敞开时,为了保证加工的表面质量,应从工件的边界外进刀和退刀。
空间曲面加工应根据曲面形状、刀具形状以及精度要求采用不同的铣削方法。
(1)对曲率变化不大和精度要求不高的曲面的粗加工,常用两轴半坐标的行切法加工,即X、Y、Z
三轴中任意两轴做联动插补,第三轴做单独的周期进给,如图2所示,将X向分成若干段,球头铣刀沿YZ面所截的曲线进行铣削,每一段加工完后进给△X,再加工另一相邻曲线,如此往复,依次切削,即可加工出整个曲面。
图2两轴半坐标行切法加工曲面
采用两坐标联动的三坐标行切法加工,通常采用球头铣刀,球头铣刀的刀头半径应选得大些,有利于散热,但刀头半径不应大于曲面的最小曲率半径。
由于二轴半坐标加工的刀心轨迹01O2为平面曲线,如图3所示,刀心轨迹0102为零件加工曲面ABCD的等距面IJKL与行切面PYZ的交线,故编程计算比较简单,常在工件曲率变化不大及精度要求不高的粗加工中使用。
图3两轴半坐标行切法加工曲面的切削点轨迹
(2)对曲率变化较大和精度要求较高的曲面进行精加工,常采用三坐标联动加工,即X、Y、Z三轴可同时插补联动。
用三坐标联动加工曲面时,通常也用行切方法。
如图4所示,Pyz平面为平行于YZ坐标面的一个行切面,它与曲面的交线为ab,若要求ab为一条平面曲线,则应使球头刀与曲面的切削点总是处
于平面曲线ab上(即沿ab切削),以获得规则的残留沟纹。
显然,这时的刀心轨迹0102不在Pyz平面上,而是一条空间曲面(实际是空间折线),因此三轴联动加工常用于复杂空间曲面的精确加工,但编程计算较为复杂,所用机床的数控装置也必须具备三轴联动功能。
图4三坐标加工走刀路线
(3)对叶轮、螺旋桨这样的零件的空间曲面,仍然可采用“行切法”加工,但因其叶片形状复杂,刀具容易与相邻表面干涉,应采用从里到外的环切,这样,有利于减少工件在加工过程中的变形,且常采用四坐标联动或五坐标联动加工。
即除了三个直角坐标运动外,为保证铣刀端面始终与曲面贴合,铣刀还应做由坐标形成的摆角运动,在摆角的同时,还应做直角坐标的附加运动,以保证铣刀端面始终位于编程值所规定的位置上,即在切削成型点时,铣刀端平面与被切曲面相切,铣刀轴心线与曲面该点的法线一致。
这种加工的编程计算相当复杂,一般采用自动编程。
四、结束语
数控机床的使用效果很大程度上取决于用户数控加工工艺技术水平的高低。
在数控机床上加工零件,每道工序中每道工步的走刀路线确定都十分重要,因为它不仅与被加工零件表面粗糙度有关,而且与加工精度和加工效率有关系。
实际生产中,在不同的数控机床上加工相同的零件时,选择走刀路线所考虑的内容不完全一样,走刀路线的确定要根据零件的具体结构特点,综合考虑,灵活运用。
在工艺处理的过程中,应认真分析零件的加工要求及其结构特点,找出走刀路线中影响加工效率的因素,在保证零件加工精度和表面粗糙要求的前提下,尽量缩短加工路线,从而提高数控机床的加工效率,降低加工成本,最大限度发挥数控机床的优越性。