船机零件的疲劳破坏讲义
机械零件的疲劳强度与疲劳断裂ppt(共37页)

s
2s1 s0 s0
对于碳钢,σ≈0.1~0.2,对于合金钢,σ≈0.2~0.3。
§3-3影响机械零件疲劳强度的主要因素
一、应力集中:
有效应力集中系数 Ks1q(s1)
s —几何形状决定的理论系数 ( 图3-9) q—敏感系数 (图3-10) 铸铁:(q=0) 定性: 跟材料、形状有关
σB A B C
可用下式描述
srm N N = C (N C≤ N ≤ N D )
σrN σr
潘存云教授研制
D点以后的疲劳曲线呈 一水平线,代表着无限寿命
N=1/4
103 104 N
D N0≈107 N
区其方程为
s s rN r N ( N D )
由于ND很大,所以在作疲劳试验时,常规定一个
N=1/4 103 104 N
D N
N0≈107
式中, sr、N0及m的值由材料试验确定。 试验结果表明在CD区间内,试件经过相应次数的
边应力作用之后,总会发生疲劳破坏。而D点以后,如 果作用的变应力最大应力小于D点的应力(σmax<σr),
则无论循环多少次,材料都不会破坏。
CD区间——有限疲劳寿命阶段 D点之后——无限疲劳寿命阶段 高周疲劳
循环次数N0(称为循环基数),用N0及其相对应的疲劳
极限σr来近似代表ND和 σr∞。
于是有 srm N NsrmN0C
CD区间内循环次数N与疲 劳极限srN的关系为
srN
sr
m
N0 N
KNsr
N
sr s rN
m N0
σmax σB A B C
σ 潘存云教授研制 rN σr
二、极限应力图(σ m——σ a)
机械设计疲劳强PPT课件

疲劳曲线和极限应力图
与曲线的两个区相对应,疲劳设计分为:
2)有限寿命区: 非水平段(N<N0)的疲劳极限称为有限寿命疲劳极限,用 σ rN 表示 。当材料受到的工作应力超过 σ r 时,在疲劳破坏之前,只能经受有限次的应力循环。--寿命是有限的。
1)无限寿命设计: N ≥ N0 时的设计。取 σ lim = σ r 。
§2-5 受规律性不稳定循环应力时零件的疲劳强度
本节只介绍规律性变幅循环应力下的疲劳强度计算方法。
一、Miner 法则--疲劳损伤线性累积假说
由最大应力分别为σ 1 、σ 2、 σ3的三个恒幅循环应力构成的规律性变幅循环应力,如右图所示。
显然,在 σ i 的单独作用下,
影响零件疲劳强度的主要因素有以下三个:
一、应力集中的影响
机械零件上的应力集中会加快疲劳裂纹的形成和扩展。从而导致零件的疲劳强度下降。
用疲劳缺口系数 K σ 、 K τ (也称应力集中系数)计入应力集中的影响 。( K σ 、 K τ 的值见教材或有关手册)
第11页/共25页
第7页/共25页
疲劳曲线和极限应力图
3)对于受切应力的情况,则只需将各式中的 σ 换成 τ 即可。
4)当N <( 103 ~104 )时,因 N 较小,可按静强度计算。
二、σm - σa 极限应力图
是在疲劳寿命N 一定时,表示疲劳极限 σrN 与应力比 r 之间关系的线图。
疲劳寿命为 N0 (无限寿命)时的 σm - σa 极限应力图,如右图所示。
第8页/共25页
极限应力线上的点称为极限应力点。三个特殊点 A、B、C 分别为对称循环、脉动循环、以及静应力下的极限应力点。
对于高塑性钢,常将其极限应力线简化为折线 ABDG 。
Chapter2 船机零件的磨损

Chapter2 船机零件的磨损§2-1 摩擦(Friction)摩擦磨损是船机零件的故障模式之一,是影响船舶机器正常运转和船舶安全航行的主要因素。
据资料介绍:世界能源的1/3~1/2是以不同形式消耗在克服机械零件对偶表面相互作用的摩擦上。
对于船用柴油机来说,目前无论是二冲程的低速机还是四冲程的中速机,燃油消耗率已降至163 g/(kW·h)左右,热效率达到50 %以上,但能量消耗在运动副的摩擦上约占10 %左右。
摩擦磨损→故障→能源浪费→必须重视1 摩擦表面的性质1.1摩擦表面的形貌(Surface Layer morphology)和表示方法外圆表面粗车会使表面产生100μm~25μm的粗糙度,抛光或超精研磨加工产生0.1μm~0.012μm的粗糙度。
零件表面的几何形态称为表面形貌。
零件表面形貌分为宏观几何形状、表面波度和粗糙度(微观几何形状)三部分。
宏观几何形状——宏观所见表面的轮廓线产生偏离名义几何形状的粗大偏差;表面波度——形成周期性的波状表面峰和谷,是由于机床加工系统振动的结果,为介于形状误差与粗糙度之间的误差;粗糙度——表面轮廓微观几何形状误差。
实际表面与理想表面存在一定的几何形状误差,表现在两个方面:(1)几何形状误差(宏观上):用圆度、圆柱度、平面度表示。
(2)表面微观几何形状误差:粗糙度。
Ra评定表面粗糙度的方法很多,常用的一种方法是轮廓算术平均偏差Ra,表面粗糙度分为14级。
1.2表面层的结构(Surface Layer Composition)金属表面一出现,就会与空气中的各种其它起作用而形成各种膜,这些膜的结构性质对摩擦性能的影响很大。
一般讲,这些膜是有益的,有利于减少摩擦磨损。
这些表面层为:污染层→气体吸附层→氧化层→加工硬化层→基体(外表层)(内表层)结论:(1)实际表面是凹凸不平的;(2)接触表面并非真正的全部接触:实际接触面积 名义接触面积;(3)即使在接触点上,也可能有表面膜把金属隔开。
4-1第一节 疲劳破坏
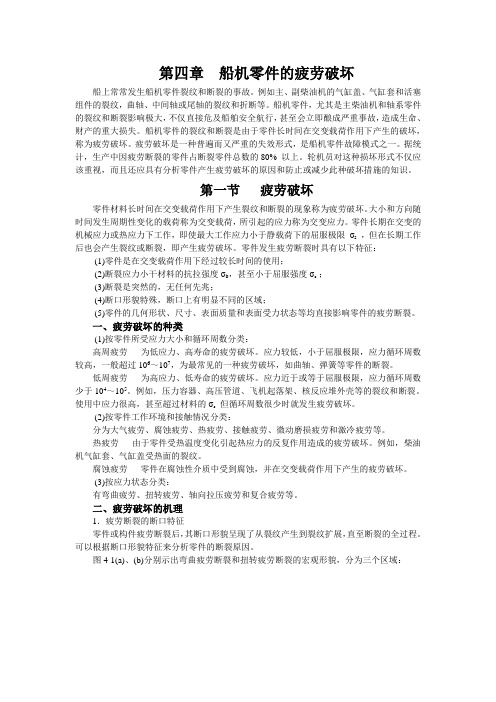
第四章船机零件的疲劳破坏船上常常发生船机零件裂纹和断裂的事故。
例如主、副柴油机的气缸盖、气缸套和活塞组件的裂纹,曲轴、中间轴或尾轴的裂纹和折断等。
船机零件,尤其是主柴油机和轴系零件的裂纹和断裂影响极大,不仅直接危及船舶安全航行,甚至会立即酿成严重事故,造成生命、财产的重大损失。
船机零件的裂纹和断裂是由于零件长时间在交变载荷作用下产生的破坏,称为疲劳破坏。
疲劳破坏是一种普遍而又严重的失效形式,是船机零件故障模式之一。
据统计,生产中因疲劳断裂的零件占断裂零件总数的80% 以上。
轮机员对这种损坏形式不仅应该重视,而且还应具有分析零件产生疲劳破坏的原因和防止或减少此种破坏措施的知识。
第一节疲劳破坏零件材料长时间在交变载荷作用下产生裂纹和断裂的现象称为疲劳破坏。
大小和方向随时间发生周期性变化的载荷称为交变载荷,所引起的应力称为交变应力。
零件长期在交变的机械应力或热应力下工作,即使最大工作应力小于静载荷下的屈服极限σs,但在长期工作后也会产生裂纹或断裂,即产生疲劳破坏。
零件发生疲劳断裂时具有以下特征:(1)零件是在交变载荷作用下经过较长时间的使用;(2)断裂应力小干材料的抗拉强度σb,甚至小于屈服强度σs ;(3)断裂是突然的,无任何先兆;(4)断口形貌特殊,断口上有明显不同的区域;(5)零件的几何形状、尺寸、表面质量和表面受力状态等均直接影响零件的疲劳断裂。
一、疲劳破坏的种类(1)按零件所受应力大小和循环周数分类:高周疲劳为低应力、高寿命的疲劳破坏。
应力较低,小于屈服极限,应力循环周数较高,一般超过106~107,为最常见的一种疲劳破坏,如曲轴、弹簧等零件的断裂。
低周疲劳为高应力、低寿命的疲劳破坏。
应力近于或等于屈服极限,应力循环周数少于104~105。
例如,压力容器、高压管道、飞机起落架、核反应堆外壳等的裂纹和断裂。
使用中应力很高,甚至超过材料的σs 但循环周数很少时就发生疲劳破坏。
(2)按零件工作环境和接触情况分类:分为大气疲劳、腐蚀疲劳、热疲劳、接触疲劳、微动磨损疲劳和激冷疲劳等。
第4章 船机零件的疲劳破坏

3)按应力种类分:弯曲疲劳、扭转疲劳、复合疲劳等。
§4-1 疲劳破坏
4、 疲劳抗力指标
疲劳抗力指标——表征零件材料抗疲劳性能的力学参数。
主要有疲劳极限、过载抗力、缺口敏感度等。
1)疲劳极限——材料经无限多次应力循环
的作用而不破坏的最大应力。又称疲劳强
度,用符号σr表示(分为σ-1和 σ0 ) 材料的疲劳极限是由试验测定。通常碳钢 是以N=107时不断的最大应力作为疲劳极 限。有色金属N=106。
较陡直的材料。
§4-1 疲劳破坏
3)缺口敏感度——表示零件表面缺口使材料疲劳强度降低的程度 零件表面开有键槽、油孔、螺纹等各种缺口时,就会在缺口的根部产生应力集中,
使材料的疲劳强度降低。采用缺口敏感度q来表示疲劳强度降低的程度。
q
K f 1 Kt 1
平均正应力
max Kt为最大应力集中系数,反映应力集中的程度 K 最大正应力 t
§4-1 疲劳破坏
2)过载抗力 过载抗力一般可用通过试验建立的过载损害区和损害界来表示。 cde——过载损害区 cd——过载损害界 ed——过载持久线,表示在超过疲 劳极限的应力下直到断裂所能经受 的最大应力循环周数
由图可以看出,材料的过载损害区越狭窄,或过载持久线ed越陡直,则过载抗力 越高。由于零件短时间过载不可避免,所以零件选材时宜选用过载损害区狭窄而又
二、疲劳破坏的机理
1、疲劳断裂的断口特征
零件或构件疲劳断裂后,其断口形貌呈现了从裂纹产生到裂纹扩展,直至断 裂的全过程。可以根据断口形貌特征来分析零件的断裂原因。疲劳断口通常分
为三个区域:疲劳源、裂纹扩展区和最后断裂区
§4-1 疲劳破坏
疲劳源(疲劳核心)
用肉眼或低倍放大镜在断口上可以找到一个或多个疲劳裂纹的开始点,称为
4疲劳破坏

一、高温疲劳和热疲劳
1.高温疲劳
定义:零件在高于材料的0.5Tm(Tm用绝对温度 表示的熔点)或高于其再结晶温度时,在交变应 力(机械、热)作用下引起疲劳破坏的过程。
属材料敏感的侵蚀介质,使金属工作即使低于屈服强度下, 也发生缓慢断裂。这种断裂常见的有:应力腐蚀断裂、氢 脆、碱脆、辐射脆裂。
5、蠕变断裂:金属材料在恒温、恒应力的长期作用下,
产生缓慢的塑性变形,最后导致断裂。
§4—1 金属疲劳的概念
一、疲劳断裂的概述 1.定义:零件或材料在交变载荷的长时间作用
下,会在应力小于σb(甚至小于σs)的情况下产 生裂纹或突然断裂,这种现象称为疲劳断裂。
3.疲劳断裂
最后断裂区的面积与所受载荷有关,面积大,说 明过载越重。当其面积小于断口面积的一半时, 说明零件无过载或过况与零件工作时所 受载荷、应力状态、零件材料性能和加工 情况有关。根据零件疲劳断口的宏观形貌 可以定性地分析零件疲劳断裂前的负荷情 况、材料性能和寿命等。对分析疲劳断裂 的原因十分有帮助。
3.使用管理方面
(1)防止过度磨损。 (2)避免严重腐蚀(冷却水投药,滑油) (3)控制燃烧。冲击、热负荷、热应力 3 (4)正常操纵使用(频繁起动、停车,长期超 负荷运转,暖缸不充分) (5)注意轴颈与轴瓦的配合间隙,减少冲击。 (6)定期测量曲轴臂距差,及时了解曲轴轴线 状态并及时调整。减少附加弯曲应力。
(3)按应力种类分:
★弯曲疲劳★ 扭转疲劳★ 复合疲劳等。
疲劳抗力指标
疲劳极限:当应力低于某一值时,循环无数次也 不会发生疲劳断裂。σr 过载抗力:适当过载对材料的疲劳性能无影响。
疲劳与断裂(1)知识讲解

随材质、应力状态的不同,断口三个区的 大小和位置不同。
1、疲劳源 ▼裂纹的萌生地;
▼裂纹处在亚稳扩展过程中; ▼由于应力交变,断面摩擦
而光亮; ▼伴随加工硬化; ▼随应力状态及应力大小的
不同,可有一个或几个疲
劳源。
2、疲劳扩展区(贝纹区) ▼断面比较光滑,并分布有贝纹线; ▼循环应力低,材料韧性好,疲劳区大,贝 纹线细、明显; ▼有时在疲劳区的后部,
本讲座主要介绍
金属疲劳的基本概念和一般规律。
疲劳失效的过程和机制。 介绍估算裂纹形成寿命的方法,以及延寿技术。
介绍一些疲劳研究的新成果。
循环应力 循环应力(交变应力、疲劳应力)是指应
力随时间呈周期性的变化。
常用导出量: 平均应力 m=( max+ min)/2 应力幅 a=( max- min)/2 应力比或循环特性参数 R= min/ max 应力幅度(应力变程 ) D = max- min
滑移带随着疲劳的进行逐步加宽加深,在表面出现 挤出带和挤入槽,这种挤入槽就是疲劳裂纹策源地 。 另外金属的晶界 及非金属夹杂物 等处以及零件应 力集中的部位 (台阶、尖角、 键槽等)均会产 生不均匀滑移, 最后也形成疲劳 裂纹核心。
疲劳裂纹的扩展
在没有应力集中的情况 下,疲劳裂纹的扩展可分为 两个阶段;
分析判断是否属于疲劳破坏。
疲劳的分类 (1)按应力状态:弯曲疲劳、扭转疲劳、复 合疲劳等; (2)按环境:腐蚀疲劳、热疲劳、高温疲劳、 接触疲劳等; (3)按循环周期:高周疲劳、低周疲劳; (4)按破坏原因:机械疲劳、腐蚀疲劳、热 疲劳。 (5)按初始状态:无裂纹零件和裂纹零件的 疲劳
疲劳研究、设计及分析的具体目的: ▲ 精确地估算机械结构的零构件的疲劳寿命 ,简称定寿,保证在服役期内零构件不会发生 疲劳失效; ▲ 采用经济而有效的技术和管理措施以延长 疲劳寿命,简称延寿,从而提高产品质量。
船舶疲劳课件

则可求得存活率为p的,分别对应于S1, S2 ,…… Sn 的
S , N , S , N , N , S ,......,S , N
1 p1 2 p2 3 P3 n pn
试验次数多
少
假定应力范围水平下疲劳寿命N的分布为对数正态分布 时,采用极大似然法拟合得到P-S-N曲线为
• 从第1阶段向第2阶段转变所对应的裂纹尺 寸主要取决于材料和作用应力的大小,但 通常都在0.05mm内, 只有几个晶粒的尺寸。 第1阶段裂纹扩展的 尺寸虽小,对寿命的 贡献却很大,对于高 强度材料,尤其如此。
• 与第1阶段相比,第2阶段的裂纹扩展较便 于观察。Laird直接观察了循环应力作用下 延性材料中裂纹尖端几何形状的改变,提 出了描述疲劳裂纹扩展的“塑性钝化模 型”,如图所示。
S2 S2 S2 S2 N1 , NS2 , N , N N 2 3 4 …… i S3 S3 S3 N1 , NS3 2 , N3 , N 4
……
N S3 i
S1 NS2 假定 N i , 为某一概率分布 f N (一般为 Weibull分布) i
存活率
Np
f N dN p
第三节 疲劳断裂研究方法
疲劳断裂问题需要研究载荷谱、裂纹萌生及扩展规律、 构件细节应力分析,疲劳寿命预测和抗疲劳设计方法,等 等。一方面,由于涉及因素多,问题复杂,难以找到解析 的、普遍的寿命预报方法;另一方面,工程应用的需求迫 切。 因此,研究问题时必须抓住主要因素,建立简化模型,
逐步深化认识。
1)标准小尺寸试件断裂。对于高、中强度钢等脆性材料, 从裂纹萌生到扩展至小尺寸圆截面试件断裂的时间很短, 对整个寿命的影响很小,考虑到裂纹萌生时尺度小,观察 困难,故这样定义是合理的。
- 1、下载文档前请自行甄别文档内容的完整性,平台不提供额外的编辑、内容补充、找答案等附加服务。
- 2、"仅部分预览"的文档,不可在线预览部分如存在完整性等问题,可反馈申请退款(可完整预览的文档不适用该条件!)。
- 3、如文档侵犯您的权益,请联系客服反馈,我们会尽快为您处理(人工客服工作时间:9:00-18:30)。
第四章船机零件的疲劳破坏(Fatigue Fracture )很多柴油机零件(如曲轴、活塞、缸盖、齿轮、连杆螺栓等)承受交变载荷的作用,经过长时间运行后会发生断裂,在这些断裂中,疲劳断裂占80~90%。
§4-1 金属疲劳的概念1 疲劳断裂的概述1.1 定义零件或材料在交变载荷的长时间作用下,会在应力小于σb (甚至小于σs )的情况下产生裂纹或突然断裂,这种现象称为疲劳断裂。
说明:(1)应力:机械应力和热应力(交变)。
交变应力:平均应力:()min max 2/1σσσ+=m应力幅值:()min max 2/1σσσ-=a 应力循环特征:m axm in σσγ=;当1-=γ时,为对称循环。
(2)破坏:裂纹和断裂。
(3)特征:零件发生疲劳断裂时具有以下特征:(1)零件是在交变载荷作用下经过较长时间的使用;(2)断裂应力小于材料的抗拉强度σb ,甚至小于屈服强度σs ;(3)断裂是突然的、无任何先兆;(4)断口形貌特殊,断口上有明显不同的区域;(5)零件的几何形状、尺寸、表面质量和表面受力状态等均直接影响零件的疲劳断裂。
1.2 种类1)根据应力大小和循环次数分:★高周疲劳破坏特点:σ小,应力循环次数大(>105),最常见(曲轴、弹簧等的断裂)。
★低周疲劳破坏特点:应力大(>σs ),低频加载,应力循环次数104~1052)根据工作环境等分类:★热疲劳:由于零件受温度的变化引起热应力的反复作用造成的疲劳破坏。
如缸盖疲劳裂纹。
★ 腐蚀疲劳:由于交变应力与腐蚀介质的共同作用而导致的疲劳破坏。
★ 接触疲劳破坏: 由于接触应力的反复作用,导致形成金属剥落,形成麻点。
如滚动轴承、齿轮等的破坏。
★ 其它疲劳形式:如接触疲劳、微动磨损疲劳和激冷疲劳等。
3)按应力种类分:弯曲疲劳、扭转疲劳、复合疲劳等。
1.3 疲劳抗力指标表征零件材料抗疲劳性能的力学参数,主要有:疲劳极限、超载抗力、疲劳缺口敏感度等。
1)疲劳极限(MPa ):当应力低于某一数值时,循环无限次,材料也不会发生疲劳断裂,该应力称为材料的疲劳极限。
材料的疲劳极限是由试验测定。
例如,常温下的碳钢、合金结构钢和铸铁,在N 达107后曲线出现水平阶段。
所以这类材料是以N =107时不断的最大应力作为疲劳极限。
2)过载抗力:是衡量过载对材料疲劳抗力的影响指标。
例如,柴油机紧急刹车、起动或超负荷运转等。
不适当过载(包括过载的大小和过载循环次数的多少)将会造成过载损伤,降低材料的疲劳极限,导致零件的疲劳破坏。
这是由于过载引发了材料内部的微裂纹扩展达到了一定尺寸,在过载后的正常运转中不断扩展导致疲劳断裂。
由图可以看出,材料的过载损害区越狭窄,或过载持久线ed 越陡直,则过载抗力越高。
过载持久值ed 表示在超过疲劳极限的应力下直到断裂所能经受的最大应力循环周数。
由于零件短时间过载不可避免,所以零件选材时宜选用过载损害区狭窄而又较陡直的材料。
3)疲劳缺口敏感度:零件表面开有键槽、油孔、螺纹等各种缺口时,就会在缺口的根部产生应力集中,使材料的疲劳强度降低。
q =(K f -1)/(K t -1)式中:K t ——静力理论应力集中系数,K t =σmax /σ;K f ——疲劳应力集中系数,K f =σ-1/σ-1HK t 是试件缺口根部处的最大应力σmax 与光滑试件横截面上均匀应力σ之比,与缺口的几何形状、尺寸及缺口曲率半径有关,与材料性能无关。
K t 值可从机械工程手册中查得。
K f 是光滑试件的疲劳极限σ-1与缺口疲劳极限σ-1H 之比,其与缺口的形状、尺寸和材料性能有关。
在中等强度范围内,材料强度越高,K f 值越大。
一般K f ≤K t 。
当K f =K t 时,q =1,表示此时疲劳应力集中最严重,缺口最敏感;当K f =1时,σ-1=σ-1H ,则q=0,表明零件虽有缺口但不影响材料的疲劳极限σ-1,缺口最不敏感。
材料的缺口敏感度q 在0~1之间。
q 值越小,缺口越不敏感。
铸铁对缺口极不敏感,q <0.1;一般结构钢对缺口较为敏感,q =0.55~0.80。
2 疲劳断裂的机理2.1疲劳断裂的断口特征零件或构件疲劳断裂后,其断口形貌呈现了从裂纹产生到裂纹扩展,直至断裂的全过程。
可以根据断口形貌特征来分析零件的断裂原因。
图4-3a )、b )分别示出弯曲疲劳断裂和扭转疲劳断裂的宏观形貌,分为三个区域:(1)疲劳源 用肉眼或低倍放大镜在断口上可以找到一个或多个疲劳裂纹的开始点,称为疲劳源。
疲劳源一般出现在零件表面或近表面处。
(2)裂纹扩展区 呈光滑状或贝纹状,一般占有较大面积。
光滑状是两个断裂表面长时间互相研磨所致;贝纹是负荷变化时裂纹前沿线扩展遗留下的痕迹。
贝纹从疲劳源开始后向四周扩展并与裂纹扩展方向垂直。
(3)最后断裂区域称脆断区零件瞬间突然断裂,断口晶粒较粗大,与发暗的裂纹扩展区明显不同。
脆性材料呈结晶状;塑性材料呈纤维状。
交变应力的反复作用→产生微观疲劳裂纹→裂纹扩展(时而扩展,时而停止)→承载面积减少→最后断裂。
因此,疲劳断裂的过程包含三个过程:疲劳裂纹的形成、裂纹的扩展和断裂。
1) 疲劳裂纹的形成:形成部位:应力最大、薄弱环节。
在截面突变、有切槽的地方、加工缺陷处等有较大应力集中。
2) 疲劳裂纹的扩展:第一阶段:切向扩展阶段。
沿最大切应力(与正应力成45o角)的方向金属内部扩展,深度较浅(0.1mm),扩展速度很小。
第二阶段:裂纹改变方向,沿与正应力垂直方向扩展,正应力对裂纹的扩展起重要作用。
3) 疲劳断裂最后断裂区的面积与所受载荷有关,面积大,说明过载越重。
当其面积小于断口面积的一半时,说明零件无过载或过载很小。
3 疲劳断裂的特点1) 突发性:断裂前无明显的塑变;2) 疲劳断裂前零件一般经较长时间的使用;3) 工作应力小于材料的强度极限,甚至小于屈服强度;4) 零件的几何形状、尺寸、表面质量和表面受力状态直接影响零件的疲劳断裂;5) 断口形貌特殊:分三个区(每个区对应一个过程)。
(1)疲劳源。
一般出现在零件的表面。
一般有1~2个。
(2)裂纹扩展区:呈贝纹状,是裂纹扩展留下的痕迹。
以上两部分由于受长时间的研磨,呈磨光状态。
若疲劳源区与裂纹扩展区断面粗糙、疲劳源数较多和贝纹线间距较大时,可能是应力集中较严重和有较大的过载作用。
(3)最后断裂区:晶粒粗大。
甚至超过断口面积一半以上,其寿命也越短。
若所占面积较小,小于断口面积之半时,说明零件无过载或过载很小。
在相同条件下,高应力状态零件的最后断裂区面积大于低应力状态零件;疲劳源数目不同,单相弯曲仅有1个,而双向弯曲有2个;最后断裂区形状不同,单相弯曲与扭转弯曲相比,后者的疲劳源与最后断裂区相对位置发生偏转,同时由于零件上缺口应力集中的影响较大,最后断裂区很小且与零件断面呈同心状。
4 影响疲劳强度的因素零件材料疲劳强度的大小受诸多因素的影响,外部因素主要是零件的形状、尺寸、表面粗糙度和使用条件等;内部因素主要是材料的成分、组织、夹杂物和表面应力状态等。
而疲劳强度是零件设计、选材和制订加工工艺时的重要参数,直接关系到零件的使用寿命。
4.1 应力集中应力集中引起的疲劳破坏居所有导致疲劳失效因素中的首位。
试验表明,零件上缺口引起应力集中使疲劳极限降低,缺口越尖锐,降低越厉害。
4.2 表面状态和尺寸因素零件加工表面状态主要是指表面粗糙度、表面成分和性能的变化、表面残余应力等。
表面粗糙度越低,表面越粗糙,疲劳极限越低。
例如,钢、铝合金粗车后的疲劳极限比抛光低10%~20%。
表面强化处理使零件表面化学成分和组织发生变化,从而使表面的机械性能变化。
例如,经渗碳或氮化处理的光滑钢试样的弯曲、扭转疲劳极限提高15%~100%;缺口试样经渗碳或氮化处理后疲劳极限提高更大,甚至达230%~300%,柴油机曲轴常采用此种强化工艺。
表面变形强化处理使表面塑性变形抗力增加,在表面层内形成残余压应力,有效地提高疲劳极限。
滚压、喷丸等工艺广泛用来提高零件的疲劳极限。
试验表明,材料的疲劳极限随试样尺寸增大而降低,材料强度越高疲劳极限下降越快。
这种现象称为疲劳强度的尺寸效应。
尺寸效应是由于:疲劳破坏源于零件表面,零件尺寸增加,表面积增加,相应增大表面疲劳破坏的概率;试验时,在试样表面拉应力相等情况下,尺寸大的试样,自表层至中心的应力梯度小,处于高应力区的表层体积大及相应的内部缺陷多,也增加了疲劳破坏的概率。
4.3 使用条件:过载情况(过载将造成过载损伤,降低材料的疲劳极限。
)、使用温度(使用温度升高,材料的疲劳极限降低,温度降低则使疲劳极限增加。
)、环境介质等(零件在腐蚀介质中工作时的零件表面被腐蚀形成缺口,产生应力集中而使零件材料的疲劳极限下降。
)。
4.4 材料的成分、组织和夹杂物一定条件下凡使材料的强度提高的因素,一般来说也可使其疲劳强度提高。
热处理对材料疲劳强度的影响较材料成分对疲劳强度的影响大得多。
钢中的非金属夹杂物是产生疲劳裂纹的发源地,钢中的夹杂物越少其疲劳强度越高。
§4-2 柴油机气缸盖的疲劳破坏1 高温疲劳和热疲劳1.1 高温疲劳零件在高于材料的0.5T m (T m 用绝对温度表示的熔点)或高于其再结晶温度时,受到循环交变应力作用所引起的疲劳破坏。
汽轮机和燃气轮机的叶轮和叶片、柴油机的排气阀等处于这种工作状态。
在高温下,材料的持久强度、蠕变极限、疲劳极限均下降。
高于常温,低于0.5 T m 的疲劳称为中温疲劳,高温疲劳具有以下特点:1)高温疲劳的疲劳曲线中不出现水平部分,疲劳极限随着交变应力作用的循环周次增加不断降低。
因此,高温下材料的疲劳极限用规定循环周次下的疲劳极限表示,一般取5×107或108次。
2)高温疲劳总伴随发生蠕变,并且温度越高蠕变所占比例越大,疲劳和蠕变交互作用也越强烈。
不同材料显著发生蠕变的温度不同,一般当材料温度高于0.3 T m (用绝对温度表示的熔点)时蠕变显著发生。
例如碳钢温度超过300℃~350℃,合金钢温度超过350℃~400℃时发生蠕变,引起材料的疲劳极限急剧降低。
3)高温下疲劳极限与蠕变极限、持久极限的关系对高温工作的零件具有重要的意义。
实验表明,在较低温度时材料的蠕变极限、持久强度比疲劳极限高。
而在高温时材料的蠕变极限、持久强度和疲劳极限均下降。
但前两者的下降速度远高于后者,如图4-7所示。
材料的蠕变极限随温度变化曲线1与疲劳极限随温度变化曲线2相交于一点。
当温度低于此点对应温度时,材料以疲劳破坏为主,高于此温度时以蠕变破坏为主。
1.2 热疲劳1)热应力★柴油机工作时,缸盖外表或冷面温度:60~80℃,而触火面的高温区的温度为400~480℃。
由触火面传来的热量被冷却水带走,冷却水温度为70℃左右。