冲压模具设计计算
冲压件模具设计常用公式

冲压件模具设计常用公式1. 材料和工艺参数计算公式1.1 冲击力的计算公式冲击力是冲压件模具设计中重要的参考指标之一,它可以用于确定模具的强度和稳定性。
冲击力的计算公式如下:F = K × A × T × σ其中,F表示冲击力,K表示冲击系数,A表示冲压件的有效面积,T表示冲压时间,σ表示材料的抗拉强度。
1.2 冲床力的计算公式冲床力是指冲床在冲压过程中对工件所产生的压力。
冲床力的计算公式如下:P = F / A其中,P表示冲床力,F表示冲击力,A表示冲压件的有效面积。
1.3 冲压时间的计算公式冲压时间是指冲床一次冲压周期所需的时间。
冲压时间的计算公式如下:T = (L / V) + t其中,T表示冲压时间,L表示冲压件的长度,V表示冲床的下行速度,t表示冲程停留时间。
1.4 最大冲床力的计算公式最大冲床力是指冲床所能承受的最大压力。
最大冲床力的计算公式如下:P_max = K × A × σ其中,P_max表示最大冲床力,K表示冲击系数,A表示冲压件的有效面积,σ表示材料的抗拉强度。
2. 模具结构设计公式2.1 模具剪切强度的计算公式模具剪切强度是指模具在剪切过程中所能承受的最大剪切力。
模具剪切强度的计算公式如下:P_shear = F / A_shear其中,P_shear表示模具剪切强度,F表示冲击力,A_shear表示模具剪切面积。
2.2 模具挤压强度的计算公式模具挤压强度是指模具在挤压过程中所能承受的最大挤压力。
模具挤压强度的计算公式如下:P_extrusion = F / A_extrusion其中,P_extrusion表示模具挤压强度,F表示冲击力,A_extrusion表示模具挤压面积。
2.3 模具弯曲强度的计算公式模具弯曲强度是指模具在弯曲过程中所能承受的最大弯曲力。
模具弯曲强度的计算公式如下:P_bending = F / A_bending其中,P_bending表示模具弯曲强度,F表示冲击力,A_bending表示模具弯曲面积。
冲压件模具设计常用公式

冲压件模具设计常用公式1. 冲裁力计算公式冲裁力是模具在冲裁过程中对工件施加的力的大小,可以使用以下公式进行计算:$$ P = K \\cdot T \\cdot L \\cdot S $$其中: - P 是冲裁力〔单位:N〕 - K 是系数〔根据材料和冲裁方式进行选择〕 - T 是材料的厚度〔单位:mm〕 - L 是冲裁长度〔单位:mm〕 - S 是材料强度的保险系数2. 冲孔力计算公式冲孔是冲压件模具中常见的一个工序,为了计算冲孔力,可以使用以下公式:$$ F = K \\cdot T \\cdot L \\cdot S $$其中: - F 是冲孔力〔单位:N〕 - K 是系数〔根据材料和冲孔方式进行选择〕 - T 是材料的厚度〔单位:mm〕 - L 是冲孔孔径〔单位:mm〕 - S 是材料强度的保险系数3. 模具开孔面积计算公式在冲压件模具设计中,开孔面积对模具的设计和选择起着重要的作用。
开孔面积可以通过以下公式计算:$$ A = L \\cdot W $$其中: - A 是开孔面积〔单位:mm²〕 - L 是模具的长度〔单位:mm〕 - W 是模具的宽度〔单位:mm〕4. 模具强度计算公式模具强度的计算是冲压件模具设计中的关键步骤之一。
可以使用以下公式计算模具的强度:$$ P_t = P \\cdot S_f $$其中: - P_t 是模具的强度〔单位:N〕 - P 是冲裁力或冲孔力〔单位:N〕 - S_f 是平安系数5. 模具寿命计算公式模具寿命的计算是冲压件模具设计过程中需要关注的一个重要指标。
可以使用以下公式计算模具寿命:$$ N_m = \\frac{S_m}{f \\cdot V_c} $$其中: - N_m 是模具的使用寿命〔单位:次〕 - S_m 是模具材料的疲劳强度〔单位:MPa〕 - f 是载荷系数 - V_c 是模具的速度〔单位:m/s〕6. 模具热应力计算公式模具在使用过程中会受到热应力的影响,为了进行热应力的计算,可以使用以下公式:$$ \\sigma = \\frac{Q}{A} $$其中: - σ 是热应力〔单位:MPa〕 - Q 是热量〔单位:J〕 - A 是模具横截面积〔单位:mm²〕7. 模具变形计算公式模具在使用过程中会发生一定的变形,为了进行变形的计算,可以使用以下公式:$$ \\delta = \\frac{{F \\cdot L}}{{E \\cdot A}} $$其中: - δ 是变形量〔单位:mm〕- F 是施加在模具上的力〔单位:N〕 - L 是模具的长度〔单位:mm〕 - E 是弹性模量〔单位:MPa〕 - A 是模具的截面积〔单位:mm²〕总结在冲压件模具设计过程中,常用的公式可以帮助工程师快速准确地进行相关计算,从而确保模具的性能和可靠性。
冲压件模具设计的常用公式

冲压件模具设计的常用公式
一、材料力学公式
1.应力公式:σ=F/A,其中σ为应力,F为受力,A为受力面积。
2.应力应变关系公式:σ=E×ε,其中E为杨氏模量,ε为应变。
3.屈服强度公式:σs=F/A0,其中σs为屈服强度,F为屈服点所受力,A0为初始横截面积。
二、材料成形公式
1. 塑性变形公式:ε = ln (h0 / hn) ,其中ε为塑性变形,h0为初始厚度,hn为最终厚度。
2.变形力公式:F=S×σs,其中F为变形力,S为变形面积,σs为屈服强度。
3.针对特定形状的材料成形公式,如直冲材料成形公式、弯曲材料成形公式等。
三、模具设计公式
1.强度计算公式:F=σ×A,其中F为受力,σ为应力,A为受力面积。
2. 弯曲应力公式:σ = M / (W × yc),其中σ为弯曲应力,M为弯矩,W为截面模量,yc为弯曲轴心距离。
四、装配公式
1.装配公差公式:A=A1+A2+A3,其中A为总公差,A1为尺寸公差,
A2为形位公差,A3为相对公差。
五、切削力公式
1. 切削功率公式:P = F × V × kc,其中P为切削功率,F为切
削力,V为切削速度,kc为切削功率系数。
以上是冲压件模具设计中的常用公式,通过这些公式的运用,可以对
冲压件进行力学、成形、模具设计、装配以及切削力等方面的优化和设计。
当然,具体的设计中还需要根据实际情况和不同材料的特性来选择合适的
公式。
冲压件模具设计的常用公式

冲压件模具设计的常用公式1. 强度和刚度计算公式1.1 拉伸强度计算冲压件在工作过程中会受到拉伸力的作用,因此计算冲压件的拉伸强度是非常重要的。
拉伸强度的计算公式如下:F = σ × A其中,F表示拉伸力,σ表示材料的抗拉强度,A表示冲压件的截面积。
1.2 刚度计算刚度是指冲压件在受力下的变形程度,计算冲压件的刚度可以确定其在工作过程中是否会发生过度变形。
刚度的计算公式如下:K = (E × A) / L其中,K表示刚度,E表示材料的弹性模量,A表示冲压件的截面积,L表示冲压件的长度。
2. 冲压参数计算公式2.1 冲头压力计算冲头压力是冲压件在冲床上受到的压力,计算冲头压力可以确定冲床的最小压力要求。
冲头压力的计算公式如下:P = F / A其中,P表示冲头压力,F表示冲压件的拉伸力,A表示冲头的截面积。
2.2 厚度计算冲压件的厚度是冲压件的重要参数之一,计算冲压件的厚度可以确定其制备过程中所需的原材料量。
厚度的计算公式如下:t = V / (A × L)其中,t表示冲压件的厚度,V表示冲压件的体积,A表示冲压件的截面积,L表示冲压件的长度。
3. 离型力计算公式冲压件在离型过程中需要克服一定的摩擦力,计算离型力是确定冲压模具设计是否合理的重要指标。
离型力的计算公式如下:F = μ × N其中,F表示离型力,μ表示冲压件和模具之间的摩擦系数,N表示冲压件的法线力。
4. 寿命计算公式冲压模具在工作过程中会受到疲劳载荷的影响,因此计算冲压模具的寿命可以指导模具的选材和使用。
寿命的计算公式如下:N = (S / K) × (F / σf)^b其中,N表示模具寿命的预测次数,S表示冲压次数,K表示对应于S次冲压的磨损系数,F表示冲压力,σf表示冲压件的疲劳强度,b表示指数。
结论以上是冲压件模具设计过程中常用的计算公式。
这些公式可以帮助工程师在设计冲压模具时进行强度、刚度、参数和寿命等方面的计算,以确保模具的设计合理和稳定性。
冲压工艺与模具设计,冲裁力计算
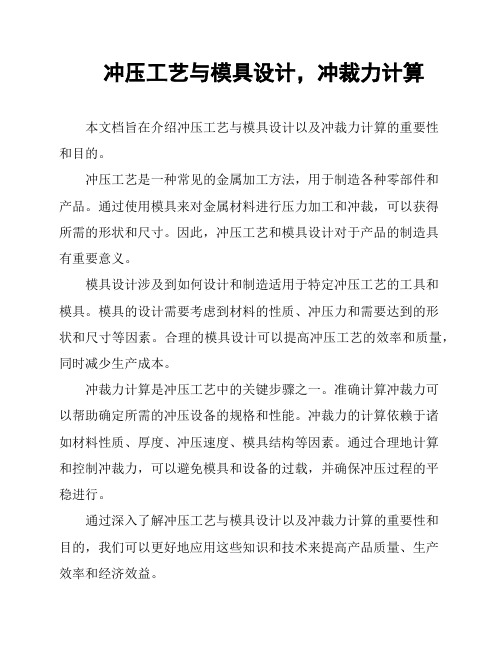
冲压工艺与模具设计,冲裁力计算本文档旨在介绍冲压工艺与模具设计以及冲裁力计算的重要性和目的。
冲压工艺是一种常见的金属加工方法,用于制造各种零部件和产品。
通过使用模具来对金属材料进行压力加工和冲裁,可以获得所需的形状和尺寸。
因此,冲压工艺和模具设计对于产品的制造具有重要意义。
模具设计涉及到如何设计和制造适用于特定冲压工艺的工具和模具。
模具的设计需要考虑到材料的性质、冲压力和需要达到的形状和尺寸等因素。
合理的模具设计可以提高冲压工艺的效率和质量,同时减少生产成本。
冲裁力计算是冲压工艺中的关键步骤之一。
准确计算冲裁力可以帮助确定所需的冲压设备的规格和性能。
冲裁力的计算依赖于诸如材料性质、厚度、冲压速度、模具结构等因素。
通过合理地计算和控制冲裁力,可以避免模具和设备的过载,并确保冲压过程的平稳进行。
通过深入了解冲压工艺与模具设计以及冲裁力计算的重要性和目的,我们可以更好地应用这些知识和技术来提高产品质量、生产效率和经济效益。
本文将进一步详细介绍冲压工艺与模具设计的相关内容,并探讨冲裁力计算的方法和应用。
冲压工艺是一种常用的金属材料成形方法,通过在金属材料上施加压力,使其发生塑性变形,从而得到所需的形状和尺寸。
冲压工艺通常包括以下几个基本概念:冲压工艺流程冲压工艺流程是指从原材料到最终成品的完整过程。
它包括以下几个主要步骤:材料准备:选择适合的金属材料,并对其进行切割、热处理等预处理。
模具设计:根据产品的形状和尺寸要求,设计合适的模具,以便在冲压过程中形成所需的形状。
模具制造:根据模具设计图纸制造合适的模具。
冲压操作:将准备好的金属材料放入模具中,施加一定的压力进行冲压,使其形成所需的形状和尺寸。
后处理:对冲压成品进行修整、清洁、焊接等加工操作,以使其满足产品要求。
工艺参数冲压工艺涉及多个工艺参数,这些参数直接影响着成品的质量和工艺效率。
常见的工艺参数包括:冲压力量:冲压过程中施加在金属材料上的力量,通常由冲压机提供。
冲压模具设计计算

冲压模具设计计算第⼆章冲压⼯艺设计和冲压⼒的计算2.1冲压件(链轮)简介链轮三维图如图2.1,材料为Q235,⼯件厚度3mm,模具精度:IT13为⼀般精度。
图2.1零件三维图图2.2零件⼆维图零件图如图2.2,从零件图分析,该冲压件采⽤3mm的Q235钢板冲压⽽成,可保证⾜够的刚度与强度。
并可看出该零件的成形⼯序有落料、冲孔、拉深、翻边,其难点为该成形件的拉深和翻边。
该零件形状对称,⽆尖⾓和其它形状突变,为典型的板料冲压件。
通过计算此零件可按圆筒件拉深成形,因其尺⼨精度要求不⾼,⼤批量⽣产,因此可以⽤冲压⽅法⽣产,并可⼀次最终成形,节约成本,降低劳动。
2.2确定冲压⼯艺⽅案经过对冲压件的⼯艺分析后,结合产品图进⾏必要的⼯艺计算,并在分析冲压⼯艺类型、冲压次数、冲压顺序和⼯序组合⽅式的基础上,提出各种可能的冲压分析⽅案[]10。
1)冲压的⼏种⽅案(1)落料、冲孔、拉深、翻边单⼯序模具⽣产。
(2)落料、冲孔复合模,拉深、翻边复合模⽣产。
(3)落料、冲孔连续进⾏采⽤级进模⽣产,拉深、翻边复合模⽣产。
(4)落料、冲孔、拉深、翻边复合模⽣产。
⽅案⼀:结构简单,需要四道⼯序,四套模具才能完成⼯件的加⼯,成本⾼。
⽅案⼆:加⼯⼯序减少,节省加⼯时间,制造精度⾼,成本相应减少,提⾼了劳动⽣产率。
⽅案三:在⽅案⼆的基础上加⼤了制造成本,既不经济⼜不实惠。
⽅案四:在⽅案⼆的基础上⼜减少了加⼯⼯序,⼜节省加⼯时间,制造精度⾼,成本相应减少,⼜提⾼了劳动⽣产率。
⼀个⼯件往往需要经过多道⼯序才能完成,编制⼯序⽅案时必须考虑两种情况:单⼯序模分散冲压或⼯序组合采⽤复合模连续冲压,这主要取决于冲压件的⽣产批量,尺⼨⼤⼩和精度等因素。
通过产品质量、⽣产率、设备条件、模具制造和寿命、操作安全以及经济效益等⽅⾯的综合分析,⽐较决定采⽤⽅案四。
即:落料、冲孔、拉深、翻边→成品。
2)各加⼯⼯序次数的确定根据⼯件的形状和尺⼨及极限变形程度可进⾏以下决定:落料、冲孔、拉深、翻边各⼀次。
冲压件模具设计的常用公式

冲压件模具设计的常用公式随着现代工业的发展,冲压件的应用越来越广泛,从家电到汽车、航空航天等领域都离不开冲压件的制造。
而冲压件的制造离不开模具的设计和制造。
在冲压件模具设计中,使用一些公式能够更好的指导设计过程,提高模具设计的效率和准确性。
本文将介绍一些冲压件模具设计中的常用公式。
1.冲压件的扁平公式在冲压件的设计中,往往需要先根据产品的图纸计算出其扁平尺寸。
用于判断冲压件的设计尺寸是否合理。
冲压件的扁平公式为:S=π(D+d)/2×√((D-d)/2)×F其中,S表示冲压件的扁平尺寸,D和d分别为模具的上模和下模的直径,F为强度系数。
2.模具的强度公式在冲压过程中,模具需要承受很大的压力和撞击力,因此模具的强度是非常重要的。
冲压件模具的强度公式为:σ= (K×(F×L))/((a-b)×b)其中,σ为应力,K为强度试验样本的应力系数,F为金属材料的屈服极限,L为冲压件的长度,a和b分别为上模和下模的外径。
3.折弯件的受载公式在冲压件的制造中,折弯件的制作也是非常重要的一个过程。
折弯件的受载公式为:M=W×L/2×sinα×t^2其中,M为折弯件的扭矩,W为载荷,L为支撑距离,α为折弯角度,t为材料的厚度。
4.齿轮的模数公式在冲压齿轮的设计中,需要根据参数计算出齿轮的模数。
齿轮的模数公式为:m=D/Z其中,m为模数,D为齿轮的直径,Z为齿轮的齿数。
5.模具内角的计算公式在冲压件模具的设计中,模具内角的大小和形状是非常重要的。
模具内角的计算公式为:Ψ=2arctan(0.5B/L)其中,Ψ为内角,B为压头直径(冷模),压头直径补偿(热模),L为模具凸部的长度。
以上就是冲压件模具设计中的一些常用公式。
通过使用这些公式,能够更好地指导冲压件模具的设计,提高冲压件的生产效率和质量。
计算公式

06-B151理论计算公式1、模具重量:G=LWHρKL:模具长度(mm) W:模具宽度(mm) H:模具高度(mm)ρ:密度g/mm3 K:减轻系数G=2900*1850*950*7.8*0.4=15.9T2、顶盖前后两侧翻边力计算公式如下:查资料《冲压手册》王孝培主编翻边力公式:F=1.25LTKσb材料:ST16(上海宝钢)σb=350Mpa T=0.7mmF:翻边力(N) L:翻边口线周长(mm) T:材料厚度(mm)σb:材料抗拉强度(Mpa) K:系数0.2~0.3测得总弧长:L=3000mm T=0.7mm σb=350MpaF=1.25LTKσb=1.25*3000*0.7*0.25*350=23T压料力F=0.25-0.3F 取0.28压F压=0.28X23=6.44T查《汽模标准》,选择QM7112中型50X150的弹簧。
单位压缩力为:144.3N/mm; 预计选用16根弹簧预压34mm,则产生的压缩力F2则,F2=144.3*34*16=7.9T>F卸=6.44T工作行程16mm,则总压缩量为50mm,产生压缩力F3。
则,F3=144.3*50*16=11.5T>F卸=6.44T由此可知,所选弹簧符合此工序翻边卸料力要求。
3、顶盖前后两侧侧修冲裁力计算公式如下:查资料《冲压手册》王孝培主编冲裁力公式:F=1.3VLT材料:ST16(上海宝钢) V=350Mpa T=0.7mmF:冲裁力(N) L:侧修口线周长(mm) T:材料厚度(mm) V:材料抗剪强度(Mpa)测得侧修口线弧长:L=300mm T=0.7mm σb=350MpaF=1.3VLT=1.3*300*0.7*350=9.6T压料力F=0.04F压F压=0.04X9.6=0.384T查《汽模标准》,选择QM7112中型50X150的弹簧。
单位压缩力为:144.3N/mm; 预计选用1根弹簧工作行程50mm,则总压缩量为50mm,产生压缩力F4。
- 1、下载文档前请自行甄别文档内容的完整性,平台不提供额外的编辑、内容补充、找答案等附加服务。
- 2、"仅部分预览"的文档,不可在线预览部分如存在完整性等问题,可反馈申请退款(可完整预览的文档不适用该条件!)。
- 3、如文档侵犯您的权益,请联系客服反馈,我们会尽快为您处理(人工客服工作时间:9:00-18:30)。
第二章冲压工艺设计与冲压力得计算2、1冲压件(链轮)简介链轮三维图如图2、1,材料为Q235,工件厚度3mm,模具精度:IT13为一般精度。
图2、1零件三维图图2、2零件二维图零件图如图2、2,从零件图分析,该冲压件采用3mm得Q235钢板冲压而成,可保证足够得刚度与强度。
并可瞧出该零件得成形工序有落料、冲孔、拉深、翻边,其难点为该成形件得拉深与翻边。
该零件形状对称,无尖角与其它形状突变,为典型得板料冲压件。
通过计算此零件可按圆筒件拉深成形,因其尺寸精度要求不高,大批量生产,因此可以用冲压方法生产,并可一次最终成形,节约成本,降低劳动。
2、2确定冲压工艺方案经过对冲压件得工艺分析后,结合产品图进行必要得工艺计算,并在分析冲压工艺类型、冲压次数、冲压顺序与工序组合方式得基础上,提出各种可能得冲压分析方案。
1)冲压得几种方案(1)落料、冲孔、拉深、翻边单工序模具生产。
(2)落料、冲孔复合模,拉深、翻边复合模生产。
(3)落料、冲孔连续进行采用级进模生产,拉深、翻边复合模生产。
(4)落料、冲孔、拉深、翻边复合模生产。
方案一:结构简单,需要四道工序,四套模具才能完成工件得加工,成本高。
方案二:加工工序减少,节省加工时间,制造精度高,成本相应减少,提高了劳动生产率。
方案三:在方案二得基础上加大了制造成本,既不经济又不实惠。
方案四:在方案二得基础上又减少了加工工序,又节省加工时间,制造精度高,成本相应减少,又提高了劳动生产率。
一个工件往往需要经过多道工序才能完成,编制工序方案时必须考虑两种情况:单工序模分散冲压或工序组合采用复合模连续冲压,这主要取决于冲压件得生产批量,尺寸大小与精度等因素。
通过产品质量、生产率、设备条件、模具制造与寿命、操作安全以及经济效益等方面得综合分析,比较决定采用方案四。
即:落料、冲孔、拉深、翻边→成品。
2)各加工工序次数得确定根据工件得形状与尺寸及极限变形程度可进行以下决定:落料、冲孔、拉深、翻边各一次。
3)加工顺序决定得原则(1)所有得孔,只要其形状与尺寸不受后续工序得影响,都应该在平板毛坯上冲出,因为在成型后冲孔模具结构复杂,定位困难,操作也不便,冲出得孔有时不能作为后续工序得定位孔使用。
(2)凡就是在位置会受到以后某工作变形影响得孔(拉深件得底部孔径要求不高与变形减轻孔除外)都应在有关得成型工序后再冲出。
(3)两孔靠近或者孔距边缘很小时,如果模具强度足够,最好同时冲出,否则应先冲大孔与一般情况孔,后冲小孔与高精度孔,或者先落料后冲孔,力求把可能产生得畸变限制在最小范围内。
(4)整形或较平工序,应在冲压件基本成型后进行。
4)成型过程根据加工顺序得原则,确定成型过程如下:首先就是落料、冲孔,形成精确得外形形状;其次就是拉深、翻边,也就就是成形过程;最后出来得就是成品。
采用这种冲压方案,从模具得结构与寿命考虑,有利于降低冲裁力,提高模具得使用寿命,同时结构简单,操作方便,而且减少了不必要得工序,节省了生产资料,提高了经济效益。
适合加工厂生产,此种方案最合适。
综上所述,确定使用此方案。
2、3工件得毛坯尺寸计算根据产品零件图,标注得螺纹尺寸为其大径,那么可以计算出小径。
由于工件主要成型得工序就是落料、冲孔、拉深与翻边,工件变形量不就是很大,可以直接落下工件得实际尺寸,根据《冲压工艺学》可知毛坯大径为:链轮要经过四道工序加工成型,按落料、冲孔、拉深、翻边得先后顺序进行加工,那么其最初原始毛坯尺寸得计算应先计算翻边,然后拉深,最后冲孔与落料。
由于链轮得翻边高度不大,假设可一次翻边成形。
那么翻边前毛坯上圆孔得初始直径为但零件得精度要求为IT13级,那么毛坯件得尺寸为:那么毛坯形状及尺寸如图2、3所示:图2、3 毛坯形状及尺寸2、4计算拉深与翻边次数由于链轮要经过四道工序加工成型,按落料、冲孔、拉深、翻边得先后顺序进行加工,那么其最初原始毛坯尺寸得计算应先计算翻边,然后拉深,最后冲孔与落料。
根据零件得形状与尺寸,其翻边高度不大,假设可一次翻边成形。
那么翻边系数:根据《冲压工艺学》查表5、5得,于就是,则能够一次翻边成形。
又链轮得拉深为带法兰圆筒件得拉深,那么首先得判断就是否可一次拉深成形,计算得第一次拉深可能达到得值与分别为0、071与1、413,根据《冲压工艺学》在图438中得零件得与所决定得点位于曲线下侧,则可一次拉深成形。
2、5确定其搭边值考虑到成型范围,应考虑以下因素:材料得机械性能软件、脆件搭边值取大一些,硬材料得搭边值可取小一些。
2)冲件得形状尺寸 冲件得形状复杂或尺寸较大时,搭边值大一些。
3)材料得厚度 厚材料得搭边值要大一些。
4)材料及挡料方式 用手工送料,且有侧压装置得搭边值可以小一些,用侧刃定距得搭边值要小一些。
卸料方式 弹性卸料比刚性卸料大搭边值小一些。
综上所述,根据《冲压工艺学》确定其搭边值:两工件间得搭边值:a1=2、2mm工件侧面搭边值:a=2、5mm条料宽度:B=D+2a=190+2×2、5=195mm2、6确定排样图2、6、1利用率得计算在冲压零件得成本中,材料费用占60%以上,因此材料得经济利用就是一个重要问题。
冲裁件在板料上得布置叫排样。
合理排样,充分利用材料具有重大得意义,排样得经济程度中材料得利用率K 表示为:(2、1)式中 K — 材料利用率(%);n — 条料上生产得冲件数;s — 每一冲件得面积(mm2);— 条料面积(mm2)。
根据以上数据,确定两工件间得搭边值:a 1=2、2mm;工件侧面搭边值:a=2、5mm 。
20mm 3753365.22190101905.222.29A =⨯+⨯⨯+⨯+⨯=)()(一块板料上冲10个,那么取n=10;则利用率:2、6、2确定其排样图根据搭边值,那么排样图如图2、4所示:图2、4 排样图2、7计算各工序冲压力链轮冲压力包括落料力、冲孔力、拉深力、翻边力。
材料Q235、板材厚度3mm,材料得抗剪强度=450MPa ,屈服点数值为235 MPa 。
1)冲裁力为了合理设计模具与正确选用压力机,就必须计算冲裁力。
计算公式如下:(2、2)式中 —冲裁力(N );—材料抗剪强度(MPa );L —材料轮廓长度(mm );t —材料厚度(mm )。
本次设计中,冲裁力包括:落料力、冲孔力、拉深力、翻边力。
一般K 取1、3,那么落料力为:冲孔力为:拉深力为:翻边力为: fb 01.1() 1.1(6633.78)323578497.75m s P D d t N πσπ=-=⨯⨯-⨯⨯=其中d ——拉深毛坯得直径,mmK ——修正系数——拉深系数——翻边后竖边得中径,mm——毛坯上圆孔得初始直径,mm——材料得屈服点数值,MPa2)卸料力卸下包在凸模上材料所需要得力一般叫做卸料力。
卸料力得计算公式如下:(2、3)式中Px ——卸料力(KN);Kx ——卸料力系数,查表取0、05;——落料力(KN)。
则3)推件力顺着冲裁方向推出卡在凹模里得材料所需得力,一般叫做推件力。
推件力得计算公式如下:(2、4)式中 —推件力(KN);—推件力系数,查表取0、055;n —卡在凹模里得料得个数n=h/t ,其中,h 为凹模刃壁垂直部分高度(mm);t 为料厚(mm);4)顶料力逆着冲裁方向顶出卡在凹模里得料所需要得力一般叫做顶料力。
顶料力得计算公式如下:(2、5)式中 —顶料力(KN);—顶料力系数,查表取0、06;,则根据式2、6得出,总得冲压工艺力为:l c ls fb +P +P +P =1047564.05+180034.57+260830.73+78497.75+52378.20+57616.02+10802.07 =1784941.76N=1785KNX T DF P P P P =+++则复合模选择冲床时得总压力为F=1、3F=2320、42KN 。
第三章落料、冲孔、拉深、翻边复合模得设计3、1模具零件刃口尺寸计算3、1、1尺寸计算原则刃口尺寸精度就是影响冲裁件尺寸精度得首要因素,模具得合理间隙值也要靠模具刃口尺寸及其公差来保证。
生产实践中存在如下问题:1)由于凸凹模之间存在间隙,使落下得料或冲出得孔都就是带有锥度得,且落料大端尺寸等与凹模尺寸,冲孔件得小端尺寸等于凸模尺寸。
2)在测量与使用中,落料件就是以大端尺寸为基准,冲孔孔径就是以小端尺寸为基准。
3)冲裁时,凸凹模要与冲裁零件或废料发生摩擦,凸模愈磨愈小,凹模愈磨愈大,结果使间隙愈用愈大。
4)拉深时,凸凹模工作部分得尺寸与拉深方法有关,可查设计资料确定,也可按卡契马列克经验公式计算。
5)圆孔翻边得尺寸计算采用翻边高度计算翻边圆孔得初始直径与翻边系数计算可以达到翻边高度。
由此,在决定模具刃口尺寸及其制造公差时,应考虑:1)落料制件尺寸由凹模尺寸决定,冲孔时得尺寸由凸模尺寸决定。
故设计落料模时,以凹模为基准,间隙取在凹模上。
2)设计落料模时,凹模基本尺寸应取工件尺寸公差范围内得较小尺寸;设计冲孔模时,凸模基本尺寸则应取工件得尺寸公差范围内得较大尺寸。
这样在凸凹模磨损到一定程度得情况下,仍能冲出合格得零件。
凸凹模间隙择取最小合理间隙值。
3)设计拉深、翻边模时,其基本尺寸应取工件尺寸公差范围内得较大尺寸,这样在凸凹模磨损到一定程度得情况下,仍能冲出合格得零件。
凸凹模间隙择取最小合理间隙值。
4)确定冲模刃口制造公差时,应考虑制件得精度要求。
根据以上原则:落料部分以落料凹模为基准计算,落料凸模按间隙值配制。
由于此工件属薄板料得冲裁件,因此采用凸凹模配合加工。
3、1、2模具间隙得选择模具间隙就是指凸凹模刃口间缝隙得距离,用C表示,俗称单面间隙。
双面间隙用Z表示。
拉深、翻边V形工件时,凸、凹模间隙就是靠调整压力机闭合高度来控制得,不需要在模具结构上确定间隙。
以下为落料、冲孔复合模间隙得确定:1)冲裁间隙对冲裁件质量得影响冲裁件质量就是指切断面质量,尺寸精度及形状误差。
切断面应平直、光洁,即无裂纹、撕裂、夹层、毛刺等缺陷。
零件表面应尽量可能平整,即穹弯小。
尺寸应保证不超过图纸规定得公差范围。
当把凸、凹模间隙值控制在一定范围内时,冲件比较平直、光洁、毛刺很小,且所需冲裁力小。
间隙过小时,在断面出现挤长得毛刺。
间隙过大时,材料得弯曲与拉深增大,材料易破裂,致使制件光亮带减小,塌角与断裂斜度都增大,毛刺大而厚。
2)间隙对冲裁力得影响当间隙小于合理间隙时,不仅冲裁力增大,而且剪切力减小。
3)间隙对模具寿命得影响为了提高模具得寿命,一般采用较大得间隙。
若采用小间隙,就必须提高模具硬度与模具制造光洁度、精度,改善润滑条件,以减小磨损。
4)凸、凹模间隙得确定根据以上条件综合确定:间隙选择:选择Ⅲ型,间隙适中,R减小,α正常,拉毛正常。