圆柱滚子轴承套圈车加工工艺改进
轴承滚子加工工艺及现状分析

轴承滚子加工工艺及现状分析摘要:轴承滚子的加工质量水平直接影响整个轴承的使用性能及轴承的寿命和可靠性。
介绍轴承滚子的加工现状,针对轴承滚子加工中存在的问题,指出产品设计和工艺设计改进方向,提出切实可行的建议及措施,以提高轴承滚子的实物加工质量。
关键词:轴承滚子;加工工艺在轴承产品零件加工中,有些人多少存在一种重成品、轻配件的观念。
滚子的加工质量水平存在一定的差距,滚子对轴承质量影响之大,直接影响到整个轴承的使用性能、寿命和可靠性。
滚子作为轴承的主要部件之一,全项质量指标和稳定性仍有较大差距。
为了实现滚子轴承的减振降噪,提高轴承的寿命和可靠性,针对轴承滚子生产状况,提出需要关注的几个问题,并对轴承滚子加工质量中存在的问题分析如下。
1轴承滚子加工现状目前,轴承滚子的加工现状为:1.1精密Ⅰ级、Ⅱ级圆锥、圆柱轴承滚子不能批量生产市场对D级、C级精密轴承的需求量越来越大,但是精密轴承的大批量生产对轴承滚子来说,难度较大。
仅是与精密轴承配套的Ⅰ级、Ⅱ级滚子的批量加工,在滚子加工过程中就困难重重。
目前也只能小批量加工一些Ⅱ级圆锥、圆柱轴承滚子,并且是要从所加工的轴承滚子中挑选出一部分Ⅱ级品轴承滚子,能够加工0级、Ⅰ级轴承滚子的品种极少,还不能形成批量生产。
1.2普通Ⅲ级滚子精度的稳定性差轴承中使用最多、最广的Ⅲ级滚子约占70%~80%。
但是,普通滚子的尺寸、精度状况也不稳定,特别是球面轴承滚子尺寸、精度方面的问题急需解决。
整批滚子的尺寸精度和几何精度的一致性及稳定性较差,这种状况就给滚子轴承的减振降噪和轴承寿命带来了很大的不确定性。
这主要与现有的生产技术和管理水平参差不齐、设备状况差异较大以及大部分采用单机加工等有较大的关系。
1.3轴承滚子加工技术及其工艺装备方面存在问题作为组成轴承的四大部件之一,滚子一般与轴承配套加工,轴承滚子的加工大多采用单机、多工序、多工步加工,有些环节加工机床精度差、稳定性差,所加工的轴承滚子存在尺寸散差大,几何精度不统一、不稳定等问题,导致生产出来的轴承状态不一致、寿命不稳定。
圆柱滚子轴承套圈越程槽的加工改进

, 7
外滚
, / /
)l \ 酱
程槽的坐标尺寸, 还要给出圆弧 曲率半径 R和圆弧 两侧切 线 的角度 , 为越程槽 的加工 、 检查 提供依据 。
为 了保证 越 程 槽 的有 效 尺 寸 , 艺 中均 取 坐 工
4
挡 边
标最大值 , 越程槽车加工尺寸如 图 2所示 。作 图 过程 为 : 照 图 1中查 得 的 尺 寸 坐 标 值 做 成 品零 按 件越程槽 图, 滚道 与挡边 的交点为越程槽 圆弧的
中图分类号 :H13 3 2 T 3 .3 文献标 志码 : B 文章编 号 : 0 1 0—36 ( 02 0 0 1 0 0 7 2 2 1 ) 1— 0 8- 3
圆柱滚子轴承应用范围广泛 , 其滚子、 滚道 的 加工技术 已十分成熟 , 但对带挡边套 圈越程槽 的 加工还有一些需要改进 的地方。越程槽尺寸和形 状的设计 , 对越程槽 的加工工艺性及套 圈的质量 产生较大影响。下文 以 N 10 U 06型圆柱滚子轴 承 外 圈越 程槽 为例 , 分析 相 同坐 标 尺寸 、 同形状 的 不 越程槽在加工时的优缺点 , 出较好 的设计方法 , 得 并推广至其他型号轴承的加工中。
中心 。依 滚 道 、 边 的 车 加 工 留量 做 相 应 的 平行 挡 线 , 平 行线 与挡 边延 长 线 的交 点 为 C 与 外 滚 道 该 , 延 长线 的 交 点 为 D; 加 工 中 为 了增 强 刀具 刀 头 在 的强 度 , C, 点 间过 渡 圆角 R为 0 5m 连 取 D两 . m;
子 。图 1 为外圈越程槽 的成 品图, 加强型 圆柱 依《 滚子轴承设 计方法》 越程槽 只给 出 , , 一和 尺 寸 , 有 规 定 槽 底 圆角 的 曲 率 半 径 及 圆 没 。 一
提高滚动轴承套圈滚道和滚子精度有序超精法

35提高滚动轴承套圈滚道和滚子精度的有序超精法无锡机床股份有限公司 (江苏 214061) 胡建清本文分析滚动轴承套圈、特别是大、中型轴承套圈或滚子超精加工后,轴承成品在使用中无法达到较高精度要求、回转精度不高,且可能在高速运转时产生较大噪声的原因,结合笔者长期以来的探讨和经验,分析选择一种科学获取超精参数的方法——有序超精法进行超精加工,以改善超精后的轴承套圈滚道,特别是大型轴承套圈滚道、滚子精度,从而满足高精度轴承的精度和低噪声要求。
这里所说的轴承套圈滚道是广义的,而滚子则主要是指调心轴承用的滚子(直径较大的腰鼓形柱体)。
1. 产生超精参数选择不当原因仅以圆柱滚子轴承的外圈进行滚道超精为例,结合轴承外圈滚道超精示意图(见图1),分析重要原因之一:模糊超精导致超精参数选择不当。
圈旋转一个角度后检测沿轴线与另一个直径组成的剖面内滚道的直线度则变为0.002mm ;并且轮廓形状也不同,前者可能为中凸偏左如图2a 所示,最高点在距基准端面为a 的位置,但后者可能变为中凸偏右如图2b 所示,最高点在距基准端面为b 的位置。
以及滚道、滚子的圆度值在轴向各不同圆截面上不一致。
例如在距滚道基准面轴向距离为a 处测得的圆度为0.001 5mm ,但在距滚道基准面轴向距离为b 处的圆度可能就为0.002 5 mm 了,并且圆度的形状也可能存在差异,从而该轴承圈在装配后的回转精度就不高,且在高速运转时会有较大噪声。
而形成轴承的滚道、滚子沿轴线剖面内轮廓度在不同圆周角度上不一致,以及滚道、滚子的圆度值在轴向各不同圆截面上不一致且形状不同的原因,就是传统的习惯性对轴承套圈滚道、滚子的模糊超精形成的。
我们假设滚子磨削加工精度和轴承套圈终磨削加工精度都是理想的,以便于集中讨论轴承套圈终磨削后的超精过程;另外,可以从本文下面所叙述的有序超精原理,自然延伸和理解滚子的超精过程及其他种类套圈的超精过程,用相同的方法来解决所有类似的问题。
轴承座加工工艺改进

轴承座加工工艺改进摘要:本文主要研究轴承座加工过程中出现的问题,最终目标是经过分析轴承座漏水或渗水、变形的问题,优化了加工工艺,解决了这些问题。
这些措施已在生产实践中推广应用,取得了可观的经济效益。
关键词:轴承座;加工工艺;改进前言轴承座是柴油机调控传动部套中的关键件之一,是轴与箱体连通的底座,起到支撑和连接的作用。
它的内孔和外圆的形位公差要求很高,加工精度的好坏决定着轴的安装和使用寿命。
因此,须要制定合理的工艺流程,,来保证轴承座达到加工要求。
1常规的加工工艺工件整体粗车后,先精车大头方向的①80K7、qC)0H7等尺寸,一次装夹加工完成,保证这两个孔的同轴度及其相对大头端面的垂直度,并且要精车外圆0142尺寸作为调头装夹时的找正基准;然后工件调头装夹,用杠杆表找外圆0142,再加工小头方向的内孔中80K7和外圆①90h7等尺寸。
该加工工艺增加了精车外圆0142尺寸这一工序,工时相应增加;同时工件调头后,找正大头圆心很困难,找正装夹的时间会很长,效率很难提高。
因此,须设计一副车夹具工装,以降低找正难度,缩短装夹找正时间,实现快速定位的同时满足加工精度要求。
通过对工件图纸的工艺分析,确定先精车大头方向的内孔qb80K7、4a90H7及端面等尺寸,然后以q)90H7孔作为定位基准,将工件圆心转化为工装圆心,这样通过找工装外圆定中心,就可以实现加工要求,提高工件加工精度和加工效率。
但是由于有工件中间外径尺寸凹1d9的存在,车刀加工外圆和内孔的进刀方向不一样,导致设计出的工装必须有两种装夹方式。
这就要求在工装设计过程中尽可能达到“一体两用”的效果。
2轴承座漏水或渗水的原因轴承座为铸钢件、水道上的盖板为钢板。
水道由机加工而成,然后焊接水槽盖板。
轴承座加工完成之后,要求水道畅通,水道打压15MPa,保压6min不得渗漏。
打压时发现漏水或渗水位置主要发生在焊缝或进、出水孔处的轴承座来看,在精加工之前,焊缝或进、出水孔都已经存在问题,但并没有发现,待精加工后发现,处理起来费时费力,说明工艺的安排存在一定的问题。
【精品】滚动轴承套圈加工工艺

滚动轴承(深沟球轴承)套圈的热处理工艺一.选择零件二.三.零件的服役条件及性能要求滚动轴承的机械及工作环境千差万别,套圈要在拉伸、冲击、压缩、剪切、弯曲等交变复杂应力状态下长期工作。
一般情况下,套圈的主要破坏形式是在交变应力作用下的疲劳剥落以及摩擦磨损,裂纹压痕锈蚀。
所以,这就要求套圈具有高的抗塑性变形的能力,较少的摩擦磨损,良好的尺寸精度及稳定性和较长的接触疲劳寿命。
综上所诉,要求套圈要有1)高的接触疲劳强度2)高的耐磨性3)高的弹性极限4)适宜的硬度5)一定的韧性6)良好的尺寸稳定性7)良好的防锈能力8)良好的工艺性能四.材料选择套圈的材料选择一般有6种GCr4,GCr15,GCr15SiMn,GCr15SiMo,GCr18Mo在这里我们选用的是GCr15,因为我们此次制造的是小尺寸套圈,GCr15SiMn和℃℃GCr15SiMo一般是用来制造壁厚的大轴承的套圈。
GCr15SiMn一般用来制造壁厚在15mm~35mm的轴承的套圈。
GCr15SiMo一般用来制造壁厚大于35mm的大型和特大型轴承的套圈。
GCr4是限制淬透性轴承钢,各方面性能较好。
GCr18Mo的淬透性比较高五.,性能优越,但价格较高。
GCr15是高碳铬轴承钢的代表钢种,综合性能良好,淬火和回火后具有高而均匀的硬度,良好的耐磨性能和高的接触疲劳寿命,热加工变形性能和削切加工性能均良好,但焊接性差,对白点形成较敏感,有回火脆性倾向,价格相对便宜。
六.加工工艺1.棒料→锻制→正火→球化退火→车削加工→去应力退火→淬火→冷处理→低温回火→粗磨→补加回火→精磨→成品2.正火正火的目的(1)消除网状碳化物及线条状组织(2)返修退火的不合格品(3)为满足特殊性能的需要为退火做组织准备加热温度正火加热温度主要依据正火目的和正火前组织状态来决定。
此处正火主要是为了消除或减少粗大网状碳化物,所以正火温度选在930~950℃之间。
如果一次正火不能消除粗大网状碳化物,可以以相同温度二次正火。
圆柱滚子轴承加工工艺的改进
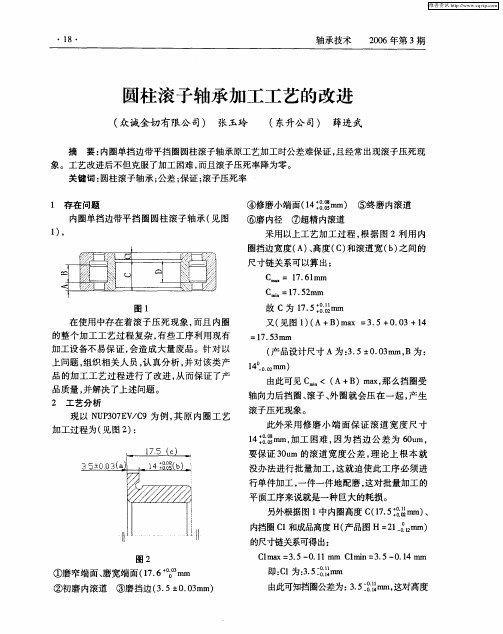
.
/ , ,/ ; // , , / , . i ,, ,
,
I I
内 挡圈 c 和成品高度 H 产品图 H= 1n nn 1 ( 2. l) 0 i
l J
的尺寸链关系可得 出:
图2
Cl x=3. ma 5—0. lh m mi 1 i C1 n:3 5—0 1 ln . . 4 ni
测量改 进示意 图如 图 4 a和图 4 : b
图3
① 磨窄端面、 磨宽端面( .: n ) 1 5 u ②初磨 7 嚣n
内滚道 ③磨挡边 (4。 nn ④超精 内滚 1‘0 u ) +∞ 0 . 6
高度环
图 4 原 测量 法 a
道 ⑤磨内径 ⑥超精内 滚道
经过工艺改进, 由图3 可以看出原来影响压
. .
0 6
图 4 改进 后 的测量 法 b
5 结论
关 系可 得 出 :
C1 x=3 5 —0 0 an ma . . 8r i C1 n=3 5 —0 1 an mi . . 7 ri
新 工艺经过 试 验 和完 善 , 用 于 同类 型 产 应
品的批量生产 , 达到了预期的效果。实践表明,
现 以 N P0 E / 9为 例 , 原 内 圈工 艺 U 37 V C 其 加 工过 程 为 ( 图 2 : 见 )
此外采用修磨小端 面保证 滚道宽度 尺寸
8 1 :0 In加 工 困难 , 4。 I , 0 u 。 因为 挡 边 公 差 为 6u 0 m,
. .
要保证 3u 0 m的滚道宽度公差 , 理论 上根 本就
2 工艺分 析
=
又( 图 1 ( 见 ) A+B m x = . 0 0 ) a 3 5+ .3+1 4
滚动轴承套圈数控车削缺陷分析及改进措施

序言目前,国内轴承行业的轴承套圈已经采用先进的数控车削加工技术。
生产实践中发现,轴承套圈在数控车削加工过程中,由于受到各种因素的影响,加工出来的工件不仅达不到规定的技术要求,还会出现各种各样的质量问题,从而造成不合格品甚至废品。
因此,必须进行质量分析,找出质量问题产生的原因,采取相应的纠正预防措施。
滚动轴承套圈数控车削加工过程中的常见缺陷有:车刀纹粗大、垫伤、漏工序、工件放偏、车削瘤、滚道留筋、振纹、倒角异常、挡边低及崩刀等。
有些缺陷出现在表面,很容易被发现,例如车刀纹粗大、漏工序等,可以将缺陷件挑出来后进行返工,经检验合格后流转至下道工序;有些缺陷如垫伤、倒角异常及挡边低等,必须将缺陷件挑出来做报废处理;另外一些缺陷,例如工件放偏、车削瘤及滚道留筋等,不容易被发现,若流入下道工序,则会带来质量隐患,甚至会导致产品报废。
下面以实例分析方式,对滚动轴承套圈数控车削加工过程中产生的缺陷进行原因分析并加以整理归纳,提出相应的改进措施。
缺陷分析与改进措施2.1 工件车刀纹粗大轴承套圈车削完成后,发现端面有非常明显的粗大车刀纹(见图1)。
产生这种缺陷的主要原因是车削刀具选用不合理,如刃口形状、角度不正确(如刀头太尖等),甚至刃口有缺陷;进刀速度快,进给量选择不合理;主轴的间隙大,车削过程中产生振动;材料硬度不合格,如果套圈锻件太硬或太软,则也会出现刀纹粗大问题。
图1端面车刀纹粗大针对该问题采取的改进措施如下。
1)选择合适的车削刀具、合理的进刀速度,调整机床主轴间隙在合适的范围。
2)要求轴承套圈锻件球化退火后硬度在合格范围之内(如GCr15轴承钢退火硬度为8 8~94HRB),这样可避免因硬度不合格而导致的车削刀纹粗大问题。
3)改善机床的刚度,避免机床、工件及刀具在车削过程中产生振动。
4)对于端面有明显车刀纹的轴承套圈,挑出来做报废处理,决不能流入下道工序。
2.2 工件垫伤数控车削后的轴承套圈端面或外径某部位有明显的凹坑,称为车削垫伤。
轴承套圈磨加工工艺过程改进

使用球 轴承套 圈沟道 自动超精机 (M 31, 3 Z20
3 z l) M 36 取代四轴超精机, 以陶瓷材料为支承材料 , 外圈采用无心支承方式 , 内圈采用 内孔定心方式 , 端面夹紧, 有两个加工工位 , 实现粗 , 精超一次完成 , 超精后工件沟道圆度、 粗糙度得到较好改善。 增加外圈外径修磨工序 , 去除工件支 承造成
l 原设备及 工艺存在 的问题
原内、 外圈磨超工 艺如下 。 外圈: 磨端面 ( B40 退磁 、 M 78 ) 清洗 _磨 外 径 +
( 18 , G 00 ) M 00 M 1 0 _支外径磨外沟道(M 16 - 2 3 Z4)+ 退磁、 清洗_支外径超精外沟道 ( + 四轴超精机) 。 内圈: 磨端面( B40 _ 退磁、 M 78 )÷ 清洗 磨 内圈 挡 边 ( 15 , G 1 0 - 支 内沟 道 磨 内 沟 道 M 00 M T0 ) + 5 ( M 13 _ 退 磁、 洗 _ 支 内 沟 道 磨 内 径 3 Z3 ) ÷ 清 + (M 23 _ 退磁、 3 Z0)÷ 清洗- 支 内圈挡边超精 内沟道 + ( 四轴 超精机 ) 。 使用立轴 圆台平面磨床 ( B40 , M 78 )要分别磨 削套圈两 个端面, 套圈磨第一端面后需要退磁清 洗, 再磨第二端面, 再退磁清洗。如果对 工件端面 磨 削量大小控制 不均 , 就会使 磨削 后沟 位置 受到影 响 , 磨削工序 产生 沟 道黑皮 , 时 , 造成 同 电磁 工作 台 如有脏物或工件定位不平将造成磨后工件的端面 平行度增 大, 沟时沟道对基准端面的平行度增 磨 大, 此类工 件影响到成品轴承旋 转精度和运转噪 声。使用该设备加工工件周期长、 效率低、 劳动强 度大 。
- 1、下载文档前请自行甄别文档内容的完整性,平台不提供额外的编辑、内容补充、找答案等附加服务。
- 2、"仅部分预览"的文档,不可在线预览部分如存在完整性等问题,可反馈申请退款(可完整预览的文档不适用该条件!)。
- 3、如文档侵犯您的权益,请联系客服反馈,我们会尽快为您处理(人工客服工作时间:9:00-18:30)。
圆柱滚子轴承套圈车加工工艺改进
在轴承加工中,圆柱滚子轴承套圈的结构不同与圆锥滚子轴承,结构相对比较复杂,工序多,现以圆柱滚子轴承NUP310ENTNI/01为例,其结构如下图所示;
1.非基准端面;
2.外圆;
3.止动槽;
4.挡边;
5.外内径;
6.外滚道;
7.油沟
我公司NUP310ENTNI/01车加工原工艺流程为;粗车-——软磨端面(平端面)——软磨外圆——打字——车基面倒角——车非基面倒角-——车外滚道——油沟——挡边内倒角——车止动槽,从上述工艺流程上可以看到,从粗车到精车要经过十道工序才能完成,而圆锥滚子轴承外圈一般从粗车到精车需五道工序完成,可见,多五道工序须占用机床,人员,仓储,物耗,劳动强度、生产成本大大增加,为提高生产效率,降低成本,在不影响产品质量的前提下,对原工艺进行调整,在某些加工方法上进行改进,对一些工序进行取消和合并,调整后的工艺流程为;粗车-——软磨端面(平端面)——软磨外圆——车基面倒角——车外滚道——车止动槽——油沟。
和前工艺流程相比,删减了打字工序,打字工序即就是在软磨端面后,在压力机上用字头在非基面上打印特殊符号工序,它是用来区分基准面和非基准面的,在轴承加工中,有利的一面,它的基准统一,检测方便,不利面,在加工中须翻面,增加劳动强度,甚至还会因干错面而造成废品,从NUP310ENTNI/01的结构图上,我们不难发现它的二端面外倒角尺寸相差大,如我们加工其任一端面倒角为基准面,就能达到打字工序的效果,又能消除打字工序引发的弊端,而对产品的检测和定位无影响,又减少了一道工序,这样提高了效率,节约了成本。
另外,在车外滚道工序上,通过将滚道切槽刀具稍加改变,由原切槽刀如图2改磨成如图3所示图样。
将外滚道挡边内倒角(两面)一次车成形,由两道工序合二为一道工序。
由多次装夹、多台机床多人完成的而变成一次装夹,一机单人操作完成。
减少了因多次装夹定位积累误差,大大的提高了机床和人员的利用率。
而在改进后车止动槽工序上,由原单一车止动槽工序而变成车止动槽与车非基面倒角相结合的方法同时车削,即用机床的后刀架车止动槽,而前刀架装夹两把倒角刀,分别车削非基面外倒角和内倒角。
通过以上在工艺方面的优化和车加工方法上的改进,由原工艺的十道工序变成改进后的七道工序,在加工中缩短了周期,提高了生产效率,节省了人员和设备,减少了周转次数,降低了发生磕碰伤的机率,从而既保证了质量,又降生产成本,达到了改进工艺后预期的目标。