物料管理、采购管理与库存管理.pptx
合集下载
采购与库存管理概述(PPT67张)

4.2 ERP中的采购与库存管理
4.2.2库存控制与管理策略
例4-1 :第二步,按序数排列这些项目,并计算出累计年使用金额(将所有 表 4-3 ABC分析步骤2
项目编号 物料每年 单位成本 年度使用 序数 类别 所占百 累计百分 用金额数除以总金额,得到每个项目占总使用金额的百分比。在此基础 使用件数 (¥) 金额(¥) 分比 比
4.1 采购与库存管理概述
4.1.1 采购管理概述
1.采购管理的概念 采购管理就是对从采购订单产生到货物收到的采购 工作的全过程进行组织、实施与控制。 2.采购管理的重要性
如某企业将收入的50%用于购买物料,最终有20%的税前净利。 采购成本降低至4 500元(降低了10%) 销售收入 10 000元 销售收入 10 000元 购买物料 5 000元 购买物料 4 500元 其他费用 3 000元 其他费用 3 000元 税前净利 2 000元 税前净利 2 500元
教学要求
知识要点 采购管理的职能
第4章 采购与库存管理
能力要求 (1) 掌握采购管理的概念 (2) 了解采购管理的重要性 (3) 了解采购管理的目标和职能 (1) 掌握库存管理的概念 (2) 掌握库存的分类 (3) 掌握库存管理的目标 (1) 了解采购管理中常见问题及其出现原因 (2) 了解库存管理中常见问题分析及其出现原因 (1) 了解采购业务在ERP系统中的实现流程 (2) 了解供应商谈判及不同的谈判方式 (3) 了解供应商计划和供应商管理 (1) 理解库存管理的目标 (2) 了解库存费用构成 (3) 了解库存控制的主要环节 (4) 了解库存管理的主要事务工作 (1) 掌握ABC分类法及其库存控制策略 (2) 了解库存订货批量模型 (3) 了解安全库存及其计算方法 (1) 了解用友采购管理子系统操作流程 (2) 掌握请购、采购订货、采购到货等采购业务在用友ERP的 应用 (1) 了解库存管理系统与采购管理系统的接口 (2) 了解入库、出库、盘点等业务在用友ERP中的应用 相关知识 采购管理的职能
企业库存管理及物料管理(ppt 148页)
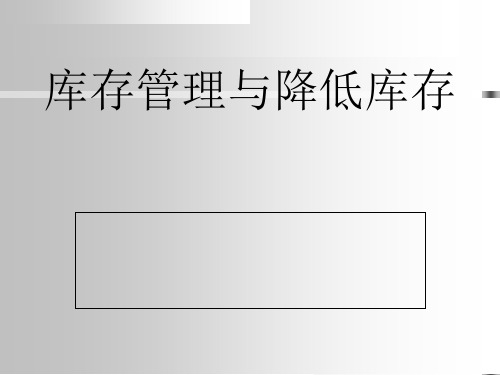
库存管理与降低库存
库存的价值
2
企业库存管理运作架构
3
基本的仓库运营
输入
接收
•对送货人做时间 上的安排
•卸货 •检查坏损 •比较P/O
仓储过程
入库
•产品识别 •存储位置识别 •移动物料 •更新记录
储存 •设备 •存货地点 周转率、单位规 格、体积
发货准备
•生产指令 •分拣 •分装 •等待
输 出
送货 •依生产指令对送 货做时间上的安 排 •车间交验 •单据
库存管理的课题
企业为了保证生产的连续性、均衡 性,需要保有一定的库存,但如何在保 证生产的连续性和均衡性的前提下,确 定一个合理的、经济的库存量,是库存 管理的一个重要课题。
16
80~20曲线
• 任何企业的物流问题都是个别产品问题 的总和。典型企业的产品系列包括处于 产品生命周期不同阶段的各种产品,销 售成功的程度也不同。在任何时间点, 都会导致80~20曲线现象—一个对企业物 料控制有 特殊意义的概念。
标明于“库位配置图”上,并随时显示库存动 态。
28
平面布置和立体布置
依物品的体积、 重量、类别规划 储放位置。
通 道
A区
通道
C区
D区
B区 E区
A
B
A3
B3
A2
B2
A1
B1
C 在不影响搬运的
C3
原则下尽量考虑
C2
空间的使用,如 储物架,并于编
C1
号。
29
物品堆放
应会同质量管理人员,依物品包装 形态及质量要求设定物品堆放方式及堆 积层数,以避免物品受挤压而影响质量。
Y=(1+A)X/(A+X) 式中 Y—累积销售比例;
库存的价值
2
企业库存管理运作架构
3
基本的仓库运营
输入
接收
•对送货人做时间 上的安排
•卸货 •检查坏损 •比较P/O
仓储过程
入库
•产品识别 •存储位置识别 •移动物料 •更新记录
储存 •设备 •存货地点 周转率、单位规 格、体积
发货准备
•生产指令 •分拣 •分装 •等待
输 出
送货 •依生产指令对送 货做时间上的安 排 •车间交验 •单据
库存管理的课题
企业为了保证生产的连续性、均衡 性,需要保有一定的库存,但如何在保 证生产的连续性和均衡性的前提下,确 定一个合理的、经济的库存量,是库存 管理的一个重要课题。
16
80~20曲线
• 任何企业的物流问题都是个别产品问题 的总和。典型企业的产品系列包括处于 产品生命周期不同阶段的各种产品,销 售成功的程度也不同。在任何时间点, 都会导致80~20曲线现象—一个对企业物 料控制有 特殊意义的概念。
标明于“库位配置图”上,并随时显示库存动 态。
28
平面布置和立体布置
依物品的体积、 重量、类别规划 储放位置。
通 道
A区
通道
C区
D区
B区 E区
A
B
A3
B3
A2
B2
A1
B1
C 在不影响搬运的
C3
原则下尽量考虑
C2
空间的使用,如 储物架,并于编
C1
号。
29
物品堆放
应会同质量管理人员,依物品包装 形态及质量要求设定物品堆放方式及堆 积层数,以避免物品受挤压而影响质量。
Y=(1+A)X/(A+X) 式中 Y—累积销售比例;
第9章采购及库存管理PPT课件

36
一、库存的概念
1、概念
(1)APICS:“库存(inventory)”一词的定
义是:“以支持生产,维护,操作和客户服
务为目的而存储的各种物料,包括原材料和
在制品,维修件和生产消耗品,成品和备件
等”。
(2)狭义:“仓库里存放东西”
(3)广义:库存就是为了满足未来需要而暂时
闲置的资源。闲置的资源就是库存,与这种
理的需要而对计划存储、流通的有关物品进 行相应的管理,如对存储的物品进行接收、 发放、存储保管等一系列的管理活动。 ▪ 库存管理主要是: “与库存物料的计划与控 制有关的业务”,目的是支持生产运作。
40
2.同仓库管理的区别:
仓库管理主要针对仓库或库房的布置,物 料运输和搬运以及存储自动化等的管理;库 存管理的对象是库存项目,即企业中的所有 物料,包括原材料、零部件、在制品、半成 品及产品,以及起辅助物料。库存管理的主 要功能是在供、需之间建立缓冲区,达到缓 和用户需求与企业生产能力之间,最终装配 需求与零配件之间,零件加工工序之间、生 产厂家需求与原材料供应商之间的矛盾。
▪ 这个成本模型用于分析企业因采购活动而产生的直 接和间接的成本的大小。企业将选择SiB值最小的供 应商。
25
6. 层次分析法
▪ 20世纪70年代由著名运筹学家赛惕 (T.L.Sattt)提出的,而韦伯(Weber)等人 把它应用于供应商的选择中。
▪ 基本原理:根据具有递阶结构的目标、子目 标(准则)、约束条件、部门等来评价方案, 采用两两比较的方法确定判断矩阵,然后把 与判断矩阵的最大特征相对应的特征向量的 分量作为相应的系数,最后综合给出各方案 的权重(优先程度)。
41
四、库存管理内容 1.库存控制 ▪ 控制库存量,加速库存周转,降低成本。评价
一、库存的概念
1、概念
(1)APICS:“库存(inventory)”一词的定
义是:“以支持生产,维护,操作和客户服
务为目的而存储的各种物料,包括原材料和
在制品,维修件和生产消耗品,成品和备件
等”。
(2)狭义:“仓库里存放东西”
(3)广义:库存就是为了满足未来需要而暂时
闲置的资源。闲置的资源就是库存,与这种
理的需要而对计划存储、流通的有关物品进 行相应的管理,如对存储的物品进行接收、 发放、存储保管等一系列的管理活动。 ▪ 库存管理主要是: “与库存物料的计划与控 制有关的业务”,目的是支持生产运作。
40
2.同仓库管理的区别:
仓库管理主要针对仓库或库房的布置,物 料运输和搬运以及存储自动化等的管理;库 存管理的对象是库存项目,即企业中的所有 物料,包括原材料、零部件、在制品、半成 品及产品,以及起辅助物料。库存管理的主 要功能是在供、需之间建立缓冲区,达到缓 和用户需求与企业生产能力之间,最终装配 需求与零配件之间,零件加工工序之间、生 产厂家需求与原材料供应商之间的矛盾。
▪ 这个成本模型用于分析企业因采购活动而产生的直 接和间接的成本的大小。企业将选择SiB值最小的供 应商。
25
6. 层次分析法
▪ 20世纪70年代由著名运筹学家赛惕 (T.L.Sattt)提出的,而韦伯(Weber)等人 把它应用于供应商的选择中。
▪ 基本原理:根据具有递阶结构的目标、子目 标(准则)、约束条件、部门等来评价方案, 采用两两比较的方法确定判断矩阵,然后把 与判断矩阵的最大特征相对应的特征向量的 分量作为相应的系数,最后综合给出各方案 的权重(优先程度)。
41
四、库存管理内容 1.库存控制 ▪ 控制库存量,加速库存周转,降低成本。评价
采购管理与库存控制培训课程PPT45页

储存的分类
按储存状态分类仓库储存 临时堆放 按储存性质分类 安全储备中转储备周转储备
库存过程概述
订货过程进货过程保管过程销售过程(或供应过程)
库存费用概述
订货费保管费缺货费补货费进货费与购买费
库存控制原理和方法
库存控制原理能影响库存量大小的只有订货、进货过程和销售供应过程。订货、进货过程使库存量增加,销售供应过程使库存量减少。要进行库存控制.既可以控制订货、进货过程,也可以控制销售出库过程,都能达到库存控制的目的。
经济订货批量的原理
经济订购批量(Economic Order Quantity,简称EOQ)的原理是平衡订货成本、存储成本,寻求使得包含采购成本、订货成本、存储成本在内的总库存成本最小的订货批量。
不允许缺货、瞬时到货的定量订货模型
首先介绍模型的假设条件:库存需求速率是固定的,且在整个时间段内保持一致。订货提前期是固定的。单位产品的价格是固定的。存储成本以平均库存为计算依据。订购成本或生产准备成本固定。不允许发生缺货。所订产品瞬时到货。
非瞬时到货情况下的EOQ模型
例3:某公司使用某零件,可外购也可自制,若外购,单价4元,一次订货成本为10元;若自制,单位成本为3元,一次生产准备成本600元,日产量50件。零件的全年需求量3600件,年库存持有成本为零件价值的20%,问自制还是外购?
答案:(外购14640元;自制12240元)。所以自制。
例
某零售商销售时装,每天平均需求100件,订货提前期为4天,订货点为500件,设需求呈正态分布,且需求相互独立,方差为30件,求该系统的安全库存,并分析其周期的服务水平。
周期服务水平的影响因素缩短提前期增大订货点减少周期需求的随机性
安全库存设计不确定需求根据标准正态分布的反函数定义
采购管理培训课件(PPT 39张)
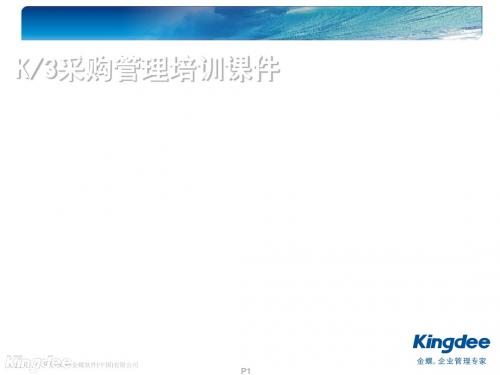
参数设置一
主要功能
应用场景 订单执行数量允许超过 订单数量 订单按比例入库 严格按申请采购
这些参数控制采购数 量,规范采购行为
版权所有 ©1993-2009 金蝶软件(中国)有限公司
P13
参数设置二
主要功能
应用场景 采购发票与入库单自动 钩稽 订单允许超额付款 系统支持部分钩稽 允许钩稽以后期间单据
采购管理的职责与目标
采购管理的职责
获得满足质量和数量要求的商品和服务。
用适当的成本获得商品和服务。
确保供应商提供尽可能好的服务及快速交货。 识别合格供应商,建立和维护稳定的供应商关系。
版权所有 ©1993-2009 金蝶软件(中国)有限公司
P3
采购管理的职责与目标
采购管理的目标
版权所有 ©1993-2009 金蝶软件(中国)有限公司
P32
采购订单全程跟踪
报表取数
取满足过滤条件的采购订单 已入库数量=订单中的入库数量 已开票数量=订单中的开票数量 已开票金额=与订单相关的发票的价税合计 已付款金额=订单中的付款关联金额 未入库数量=订单数量-入库数量 未开票数量=订单数量-开票数量 未开票金额=订单金额-开票金额 未付款金额=订单金额-已付款金额
需要钩稽的入库单列表 需要钩稽的费用发票 需要钩稽的发票列表 列表
版权所有 ©1993-2009 金蝶软件(中国)有限公司
P31
提纲
采购管理职责与目标 采购管理业务流程 基础数据设置 模块参数设置 供货信息与价格管理 采购需求处理 订单处理与跟踪 收货与退货作业 采购结算与付款 报表
采购管理与库存控制教学.pptx

第11页/共44页
二、供应市场分析的步骤
确定目标
成本效益 分析
可行性分析
撰写总结 报告及评估
方案的实施
制定分析计 划的方案
第12页/共44页
三、供应市场分析的内容(一)供应市场研究
确定目标 供
应 市
成效分析
场 研
可行性分析
究
过
制定研究方案与方案实施
程 总结报告
第13页/共44页
三、供应市场分析的内容(一)供应市场研究
第3页/共44页
知识目标
• 1.了解供应市场调查常用的分析工具和 技术。
• 2.掌握采购需求确定的方法和步骤。 • 3. 重点掌握定性和定量预测方法。
第4页/共44页
技能目标
• 1.能够进行供应市场分析。 • 2.会运用定性与定量方法对采购需求进行
预测。 • 3.能够制定需求报表。
第5页/共44页
第31页/共44页
加权平均法
Ft=W1×D1+W2×D2+…+Wi×Di+…+Wn×Dn 式中:Ft——预测值;
Di——第i时段的需求数据值; Wi——第i时段的需求数据的权重值。 如果权重进行归一化处理后,则权重之和为1。 例题:上题中第一周的权重为1/6,第二周的权重为2/6,第三周的权重为3/6, 利用加权平均法对第四周的需求量进行预测。
学习情境二 采购准备工作
第2页/共44页
内容简介
主要介绍了供应市场分析和需求预测的概念 及其重要作用,同时分析了采购作业的一般 流程。供应市场分析是指为了满足企业目前 及未来发展的需要,为企业的采购决策提供 依据。需求预测是企业编制生产计划的依据, 是库存管理的基础,也是企业增强竞争能力 的重要手段。采购流程是采购活动的全部操 作过程,是采购人员从事采购活动的执行标 准和业务规范,采购人员必须遵守执行。
二、供应市场分析的步骤
确定目标
成本效益 分析
可行性分析
撰写总结 报告及评估
方案的实施
制定分析计 划的方案
第12页/共44页
三、供应市场分析的内容(一)供应市场研究
确定目标 供
应 市
成效分析
场 研
可行性分析
究
过
制定研究方案与方案实施
程 总结报告
第13页/共44页
三、供应市场分析的内容(一)供应市场研究
第3页/共44页
知识目标
• 1.了解供应市场调查常用的分析工具和 技术。
• 2.掌握采购需求确定的方法和步骤。 • 3. 重点掌握定性和定量预测方法。
第4页/共44页
技能目标
• 1.能够进行供应市场分析。 • 2.会运用定性与定量方法对采购需求进行
预测。 • 3.能够制定需求报表。
第5页/共44页
第31页/共44页
加权平均法
Ft=W1×D1+W2×D2+…+Wi×Di+…+Wn×Dn 式中:Ft——预测值;
Di——第i时段的需求数据值; Wi——第i时段的需求数据的权重值。 如果权重进行归一化处理后,则权重之和为1。 例题:上题中第一周的权重为1/6,第二周的权重为2/6,第三周的权重为3/6, 利用加权平均法对第四周的需求量进行预测。
学习情境二 采购准备工作
第2页/共44页
内容简介
主要介绍了供应市场分析和需求预测的概念 及其重要作用,同时分析了采购作业的一般 流程。供应市场分析是指为了满足企业目前 及未来发展的需要,为企业的采购决策提供 依据。需求预测是企业编制生产计划的依据, 是库存管理的基础,也是企业增强竞争能力 的重要手段。采购流程是采购活动的全部操 作过程,是采购人员从事采购活动的执行标 准和业务规范,采购人员必须遵守执行。
采购和库存管理培训课件(PPT 44页)

物资及其用量情况表(二)
年费用
累积年费用 累积百分 比
分类
25,200 24,000 7,200 5,600 4,000 1,350 1,050
840 600 220
25,200 49,200 56,400 62,000 66,000 67,350 68,400 69,240 69,840 70,060
21
6.2.2 库存管理的主要功能
本节主要介绍管理的主要功能和处理业务流程
22
库存管理的业务功能
库存管理业务
物料入库管理 物料出库管理 物料移动管理 物料盘点管理 信息分析
ERP库 存 管 理 子 系 统
入出移物库员 库库动料存工 管管管盘分考 理理理点析核
图 3-15 库 存 管 理 的 功 能 树 图
37
一般情况下,库存项目存在着这样的规律:少数库存项
目占用着大部分库存资金,相反大多数的库存项目只占用小部 分库存 资 金 。 这 也 就是帕 累 托原理 (Pareto Principle)中的 “20–80现象”,即20%的物料占80%的价值。利用库存与资 金占用之间的这种规律对库存项目进行分类,便是库存管理中 的“ABC分类法”。 其中:
支付利息 搬运费用 有过时废弃损失风险 机会成本、损失收益
19
库存管理的定义
库存管理的概念
指企业为了生产、销售等经营管理的需要而对库存 进行相应的管理,如控制、收发、存储、保管等管 理活动.
20
库存管理的作用
维持销售产品的稳定 维持生产的稳定 平衡企业物流 平衡流通资金的占用
13
6.1.3 采购管理子系统与其他子系统的关系
本节主要介绍采购管理子系统和其他业务子系统的关系
采购管理与库存控制-PPT文档资料

采购业务单元
支持
审核
优化调整
批准实施
管理流程简图
业务单元运作实施
一. 采购管理
3. 采购组织 (1)采购组织建立的基本原则 a. 采购组织应体现多权分立、 互相制约、集权监控的原则。 b. 采购组织应设有专门的技术 支持团队。
c. 采购组织应具有不断变革和 自我调整的能力。
一. 采购管理
(2)采购组织框架
二. 库存管理与控制
3. 库存控制系统
4. (1)库存控制的基本要素及存 储状态图
5.
a. 需求
6.
b. 补充
7.
c. 库存水平
8.
d. 存储费用
9.பைடு நூலகம்
二. 库存管理与控制
3. 库存控制系统
4. (1)库存控制的基本要素及存储状 S态(图库存)
Q
L
L
L
T
间断补充、均匀需求
t(时间)
二. 库存管理与控制
订单计划
供应商送料
供应商收款
订单 准备
选择 供应商
订单 签订
订单 跟踪
物料 检验
物料 付款 接收 操作
供应 评估
物料入库 资金
订单计划简图
一. 采购管理
2. 采购流程 3. (4)管理评审流程
采购业务单元
支持
审核
优化调整
批准实施
管理流程简图
业务单元运作实施
一. 采购管理
2. 采购流程 3. (4)管理评审流程
采购需求
准备
评估需求 计算容量
制定计划
计划流程简图
采购计划
一. 采购管理
2. 采购流程
3. (2)认证流程
支持
审核
优化调整
批准实施
管理流程简图
业务单元运作实施
一. 采购管理
3. 采购组织 (1)采购组织建立的基本原则 a. 采购组织应体现多权分立、 互相制约、集权监控的原则。 b. 采购组织应设有专门的技术 支持团队。
c. 采购组织应具有不断变革和 自我调整的能力。
一. 采购管理
(2)采购组织框架
二. 库存管理与控制
3. 库存控制系统
4. (1)库存控制的基本要素及存 储状态图
5.
a. 需求
6.
b. 补充
7.
c. 库存水平
8.
d. 存储费用
9.பைடு நூலகம்
二. 库存管理与控制
3. 库存控制系统
4. (1)库存控制的基本要素及存储状 S态(图库存)
Q
L
L
L
T
间断补充、均匀需求
t(时间)
二. 库存管理与控制
订单计划
供应商送料
供应商收款
订单 准备
选择 供应商
订单 签订
订单 跟踪
物料 检验
物料 付款 接收 操作
供应 评估
物料入库 资金
订单计划简图
一. 采购管理
2. 采购流程 3. (4)管理评审流程
采购业务单元
支持
审核
优化调整
批准实施
管理流程简图
业务单元运作实施
一. 采购管理
2. 采购流程 3. (4)管理评审流程
采购需求
准备
评估需求 计算容量
制定计划
计划流程简图
采购计划
一. 采购管理
2. 采购流程
3. (2)认证流程
- 1、下载文档前请自行甄别文档内容的完整性,平台不提供额外的编辑、内容补充、找答案等附加服务。
- 2、"仅部分预览"的文档,不可在线预览部分如存在完整性等问题,可反馈申请退款(可完整预览的文档不适用该条件!)。
- 3、如文档侵犯您的权益,请联系客服反馈,我们会尽快为您处理(人工客服工作时间:9:00-18:30)。
3.从准备方法上区分:
※常备材料:根据存量控制原理,定期采 购一定数量的材料作为储备,以供生产 需要
※非常备材料:特殊材料不经常使用或使 用量少等材料,根据生产计划的需要来 决定是否采购的材料
物料管理的精髓
❖ 不断料 不让制造单位领不到需要的物料,产生
待料的现象。 ❖ 不呆料
不让物料成为呆料。 ❖ 不囤料
❖ 订货点: =正常订货周期(天)×每天消耗量+安全存量
❖ 定期法的订购量: =预定订货周期(天)×每天消耗量
❖ 最大库存量
=订购量+安全库存 ❖ 案例:
某物品属常备性物料,拟采用批量 订货管制方式经统计得出:
❖ 平均每天耗用:200kg; ❖ 订购周期:正常6天,紧急4天;
考虑厂商备料时间、生产时间、运 输时间、验收时间等。
7.技术(Method)
企业的大脑
8.信息(Information) 企业的神经
第一节 物料管理(物控)
物料管理的定义: 即物料控制(Material Control), 主要职能是物料计划、物料请购、 物料调度,物料的控制(坏料控制 和正常进出用料控制)
物料的区分方式有哪些?
物料通常也称为材料,指用来维持产 品制造所需的原料,零配件等等,一般 从以下几个方式进行区分:
❖ 库存的本质
❖ 库存的内容:涵盖产品.物料.在制品, ❖ 反映管理水平. ❖ 库存的面纱:“救世主与坟墓”. ❖ 库存的坏处:管理浪费.
资本僵化.呆.废料损失. 掩盖问题. 消除企业的改善意愿.
库存管理不良对企业经营的影响
1.库存过多
A.资金积压 B.潜在的呆废料损失 C.更多的管理费用 / 场地费用 2.库存不足 A.订单交期延误 B.整体生产力低落/ 成本高 C.紧急弥补对策的损失
进料适时、适量,不至于因过量、过时 而囤积。
物料管理不善造成的损失
❖ 停工待料 ❖ 物料闲置 ❖ 占用生产场地
物料管理的职能(5R)
❖ 适时(Right Time) ❖ 适质(Right Quality) ❖ 适量(Right Quantity) ❖ 适价(Right Price) ❖ 适地(Right Place)
物料管理的目标
❖适时,适质,适量,适价,适地地供应生产所 需 ❖防止呆料的发生 ❖提高用料周转率,减低财务无形成本 ❖控制及降低物料成本,确保并提高利润 ❖确保企业资产之数量及价值
物料管理不良的影响
❖明显的浪费 ❖潜在的浪费
物料管理常见的缺失
❖ 1.料帐不准 ❖ 2.料品报废损失多 ❖ 3.库存积压多、周转率低 ❖ 4.呆料比率高 ❖ 5.仓储备料时间长影响现场生产绩效 ❖ 6.停工待料损失工时多
专用订单型计划
多品种少批量的订单采购。 购买单价往往较高。 不重复性且不能通用的物料。 保管谨慎,易损.易变质的物料。 能对应订单及设计变更的变化。
采购管理主要范围
❖ 1.价格管理 ❖ 2.请购管理 ❖ 3.订购作业管理 ❖ 4.进料时间与品质管理 ❖ 5.应付帐款管理
采购管理的目标
PMC课程之------
物料管理与控制 2011-6
很多制造工厂常见的缺失
❖ 1.生产现场要领料时 , 需等待长时间 , 生 产力损失
❖ 2.生管制订的细排程 , 实际领料时才发现 缺料 ,
❖ 3.领料超出标准 (成本/量) , 无法及时管 制 , 利润无法维护 , 超损耗无从追究
❖ 4在制品 (包含已投入未真正加工) 堆置 , 造成混乱
批量订货的适合对象
❖ 消费、使用量基本固定的物料; ❖ 容易获得和保管的物料; ❖ 价格较便宜的物料;
批量订货方式的设定
❖ 求得平均每天消耗量; ❖ 确定订货前置时间; ❖ 设定安全库存量; ❖ 设定订货点; ❖ 确定每次的订货量; ❖ 求得最大库存量。
批量订货方式的计算公式
❖ 安全存量: =紧急订货周期(天)×每天消耗量
第二节 采购管理
供应商管理的主要范围
❖ 1.供应商的开发 / 选择 ❖ 2.采购 / 委外加工管理 ❖ 3.供应商评价 ❖ 4.供应商辅导
采购计划(物料需求计划)
存量型计划
库存生产型产品的物料(少种多量或中种中量)。 重复性及通用性的物料。 购备时间较长的物料。 市场性较差的物料。 购买金额较低,影响较小的物料。
❖ 定期法管理:每月采购3次,每10天订货 1次。
则批量定货管制所需确定的项目如下: ❖ 安全存量=200kg×4(天)=800kg ❖ 订货点=200kg×6(天)+800kg=2000kg ❖ 订购量=200kg×10(天)=2000kg ❖ 最高存量=2000kg+800kg=2800kg
第三节 库存管理
理简便;
❖
批量订货,即当库存降低到定货点时,就补足
一定数量的货,如此循环不已。
库存量
订货量 期间
入库 订货
入库 订货
入库 订货
批量订货的特征
❖ 即使不知道需求的变动也能管理; ❖ 不适合于需求量变动剧烈的项目; ❖ 运作费用可减少; ❖ 可进步为自动订货制度; ❖ 订货事务作业平均化; ❖ 库存量容易增加。
1.从功能上区分:
※主材料:为构成制成品的主要部份, 如原料、零件等
※辅助材料:配合主要材料的加工而附属 于在制品上的材料,如包裝、劳保用品 等
2.从成本控制上区分:
※直接材料:直接供产品制造的材料,其 消耗与产品的产量成正比,一般会记录 于材料清冊上(BOM)
※间接材料:指间接帮助产品制造的材料, 其消耗品,机器维护用的油类等
❖ 5.物品先进先出无法落实 , 造成损废 / 呆 料
构成企业的8个重要因素(7M 1I)
1.资金(Money) 企业的血液
2.市场(Market) 企业的目标
3.人力资源(Man power) 企业的心脏
4.机器设备(Machine) 企业的肌肉
5.材料(Material) 企业的粮食
6.管理(Management) 企业的血脉
❖ 配合生产排程需求
包括投产之顺畅性
❖ 降低 (及控制) 进料成本 ❖ 维护进料品质 ❖ 缩短产销 Lead Time ❖ 抑减呆废料的潜在原因
批量订货方式
❖
批量订货就是当库存经使用而逐渐减少至一定
数量时,就发出订单;
❖
“一定数量”是指在事前决定的存量基准,亦即
订货点,因此又称为订货点法;
❖
批量订货,须先决定订货点和订货量,所以管