加工中心加工箱体误差分析
加工中心精度不高原因分析及解决办法

加工中心因其在制造工业中保证了机械产品零件加工精度和产品质量稳定,所以在现代工业发展,机械制造中得到越来越广泛的应用。
但加工中心精度也时刻影响着机床加工工件的质量问题。
加工中心精度不高是什么原因引起?这种情况下在不考虑是机床的问题,加工中产生的误差造成加工工件的精度不高,如:1、计算失误造成的精度误差,人为因素,所以在加工工件前可以通过验算,试加工来排除。
2、材料变形引起的精度误差,需要加工前期采取相应的措施,加工时要采取相应的办法避免这种错误。
提升加工中心加工零件时精度加工精度就是零件加工后的几何参数,其与原图纸的理想几何参数差异越小,它的符合程度也就越高,加工精度也就越高。
在加工实践中,受到各种因素的影响,零件加工与理想几何参数存在较大的差异,这种偏差就是加工误差。
因此合理控制加工误差,就是提升加工精度的最佳方法。
而合理范围内的加工误差就是不超出零件设计要求的公差,只要在这个范围内,就能够进行零件加工精度的保证。
加工精度及加工误差都可以进行零件几何参数的评定。
加工误差的大小都能够影响加工精度的高低,通过对加工精度的有效控制,可以实现加工误差的减少,从而满足实际工作的要求。
在工作过程中,很多因素都影响到零件的加工精度。
即使使用同一种加工方法,在不同的工作环境下,它的精度也是不同的。
如果我们片面的追求零件的加工精度,就会导致生产效率的降低,从而导致工程成本的增加,为了满足实际工作的要求,我们必须要进行加工质量强化体系的应用,保证工作效率的有效提升,实现生产成本的有效控制。
在工作过程中,加工精度具体分为形状精度、位置精度、尺寸精度等,加工精度的高低变化,需要以形状公差、位置公差等来判断。
通过对试切法可以进行加工表面的试切,通过对试切所得尺寸的测量,可以满足零件的加工精度的要求。
过程中需要进行适当刀具的使用,做好不同数量的试切及测量工作,最终达到加工一个精度标准。
最后,就是对材料变形的问题处理,通过对零件变形问题的解决,可以有效提高零件的加工精度,在实际操作中不同的工作场景,对应不同的零件变形处理措施,需要辩证分析,因地制宜的进行工作,提升零件加工系统的整体工作效率。
数控机床技术中的加工误差分析与解决方法

数控机床技术中的加工误差分析与解决方法近年来,数控机床技术在工业领域得到了广泛的应用和推广。
然而,在数控机床加工过程中,由于多种因素的影响,加工误差是难以避免的。
加工误差的存在直接影响产品的质量和精度,因此,加工误差的分析和解决方法变得尤为重要。
本文将通过对数控机床技术中的加工误差的分析,提出相应的解决方法,以提高加工精度和降低误差。
一、加工误差的种类和特点数控机床在加工过程中常见的误差有以下几种:1. 几何误差:由于数控机床的结构和加工方式,导致加工出的零件的几何形状与设计要求有一定偏差。
例如,平面误差、圆度误差、直线度误差等。
2. 运动误差:数控机床的运动系统存在一定的误差,如位置误差、速度误差和加速度误差等。
3. 加工刀具误差:刀具的形状和磨损程度会直接影响加工效果和精度。
刀具的磨损和变形会引起误差的累积和扩大。
4. 环境误差:加工过程中,环境因素如温度、湿度和振动等会对数控机床产生影响,导致加工误差的产生。
5. 人为因素:操作人员的经验和技能水平也会对加工误差产生一定的影响。
操作不当或者不合理的操作方式可能导致误差的产生。
加工误差的特点是累积性和随机性。
误差会随着加工的次数的增加而累积,同时误差的产生也具有一定的随机性,难以精确预测。
二、加工误差的分析方法为了有效地降低加工误差,首先需要进行误差分析。
在数控机床中,常用的误差分析方法有以下几种:1. 建立误差模型:通过建立数控机床的误差模型,可以较为准确地分析和预测加工误差。
误差模型可以由实验测量和数据分析得到,或者通过建立数学模型进行求解。
2. 检测和测量:通过使用检测和测量设备对加工件进行精确的测量,可以获取加工误差的具体数值。
常用的测量设备有坐标测量机、三坐标测量仪等。
3. 统计分析:通过对大量的加工数据进行统计和分析,可以找出误差产生的规律和影响因素。
统计分析可以帮助人们更好地理解和掌握误差的特点和规律。
4. 数值仿真:利用计算机仿真软件对加工过程进行模拟和分析,可以在较短的时间内得到加工误差的大致范围和分布情况,为后续的优化提供依据。
数控机床技术中的加工误差分析与解决方法

数控机床技术中的加工误差分析与解决方法在数控机床技术中,加工误差是一个常见但重要的问题。
误差的存在会直接影响加工件的精度和质量,因此精确分析和解决加工误差是保证数控机床加工精度的关键。
首先,我们需要了解加工误差的来源。
加工误差可以分为机床误差和加工工艺误差两部分。
机床误差是由于机床本身的精度限制和机械结构造成的,比如导轨的精度、滚珠丝杠的间隙等。
而加工工艺误差则是由于刀具、切削力、材料特性等因素引起的。
了解误差来源有助于我们有针对性地解决加工误差问题。
为了准确分析加工误差,我们可以采用误差分离法。
这种方法通过实际加工一系列试样,然后测量试样的尺寸和形状差异,再通过数学模型进行误差分离。
通过分离机床误差和加工工艺误差,我们可以更好地掌握误差来源,为解决加工误差提供依据。
当我们确定了加工误差的来源后,接下来就是解决加工误差的关键。
下面介绍几种常见的解决方法。
首先是机床调试。
机床调试是解决机床误差的关键环节,包括对机床各个部件进行精确调整,以优化机床的精度。
比如,可以通过调整导轨的间隙来改善导轨的刚性,减小机床误差。
同时,还需保证机床的温度、湿度等环境条件稳定,以免环境因素对机床精度造成影响。
其次是加工工艺优化。
加工工艺优化可以降低加工工艺误差,提高加工精度。
在选择刀具时,应考虑刀具的刚度、切削角度、刃口尺寸等因素,以确保切削力的合理分布。
此外,应根据具体加工要求选择合适的切削参数,如切削速度、进给速度等,以保证加工质量。
还有一种方法是补偿技术。
补偿技术通过测量实际加工件与设计图纸的差异,然后在数控编程时引入补偿值,以实现误差的补偿。
常见的补偿技术包括半自动补偿和全自动补偿。
半自动补偿需要人工测量,将测量结果输入数控机床进行补偿;而全自动补偿则利用传感器等装置实时测量加工件的尺寸差异,并通过编程自动进行补偿。
补偿技术能够有效地减小加工误差,提高加工精度。
此外,定期维护和保养数控机床也是解决加工误差的重要措施。
数控加工中的加工误差分析与改进措施
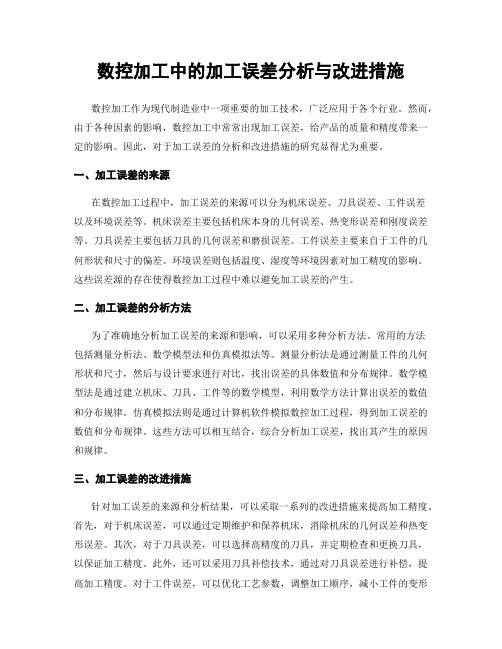
数控加工中的加工误差分析与改进措施数控加工作为现代制造业中一项重要的加工技术,广泛应用于各个行业。
然而,由于各种因素的影响,数控加工中常常出现加工误差,给产品的质量和精度带来一定的影响。
因此,对于加工误差的分析和改进措施的研究显得尤为重要。
一、加工误差的来源在数控加工过程中,加工误差的来源可以分为机床误差、刀具误差、工件误差以及环境误差等。
机床误差主要包括机床本身的几何误差、热变形误差和刚度误差等。
刀具误差主要包括刀具的几何误差和磨损误差。
工件误差主要来自于工件的几何形状和尺寸的偏差。
环境误差则包括温度、湿度等环境因素对加工精度的影响。
这些误差源的存在使得数控加工过程中难以避免加工误差的产生。
二、加工误差的分析方法为了准确地分析加工误差的来源和影响,可以采用多种分析方法。
常用的方法包括测量分析法、数学模型法和仿真模拟法等。
测量分析法是通过测量工件的几何形状和尺寸,然后与设计要求进行对比,找出误差的具体数值和分布规律。
数学模型法是通过建立机床、刀具、工件等的数学模型,利用数学方法计算出误差的数值和分布规律。
仿真模拟法则是通过计算机软件模拟数控加工过程,得到加工误差的数值和分布规律。
这些方法可以相互结合,综合分析加工误差,找出其产生的原因和规律。
三、加工误差的改进措施针对加工误差的来源和分析结果,可以采取一系列的改进措施来提高加工精度。
首先,对于机床误差,可以通过定期维护和保养机床,消除机床的几何误差和热变形误差。
其次,对于刀具误差,可以选择高精度的刀具,并定期检查和更换刀具,以保证加工精度。
此外,还可以采用刀具补偿技术,通过对刀具误差进行补偿,提高加工精度。
对于工件误差,可以优化工艺参数,调整加工顺序,减小工件的变形和误差。
对于环境误差,可以控制加工环境的温度和湿度,以减小环境对加工精度的影响。
除了以上的改进措施,还可以采用自适应控制技术来提高加工精度。
自适应控制技术是指根据实时测量的加工误差信息,通过调整加工参数和控制系统,实现对加工误差的自动补偿和控制。
数控机床加工误差分析及改善方案

数控机床加工误差分析及改善方案数控机床加工误差分析及改善方案随着制造业的发展,数控机床在工业生产中扮演着重要的角色。
然而,由于各种因素的影响,数控机床在加工过程中常常会出现误差,影响产品的精度和质量。
因此,对于数控机床加工误差的分析和改善变得至关重要。
下面将介绍一种逐步思考的方法,帮助我们分析加工误差,并提出改善方案。
第一步:收集数据首先,我们需要收集加工误差的相关数据。
这些数据可以包括加工零件的尺寸测量结果、加工过程中的工艺参数、机床的精度参数等。
通过收集这些数据,我们可以了解到加工误差的具体情况,并为后续的分析提供依据。
第二步:分析误差来源在收集到数据之后,我们需要对误差的来源进行分析。
数控机床加工误差通常可以分为几个主要来源,如机床本身的刚度、工具刀具的磨损、加工时的热变形等。
通过对这些来源的分析,我们可以确定造成加工误差的主要因素。
第三步:确定改善方向在了解了误差来源之后,我们需要确定改善的方向。
根据误差来源的不同,我们可以采取不同的改善措施。
例如,如果误差主要来自机床的刚度不足,我们可以考虑加强机床的刚性结构,提高其稳定性;如果误差来自于工具刀具的磨损,我们可以采取定期更换刀具的措施,保证其切削效果。
第四步:实施改善措施在确定了改善方向之后,我们需要实施相应的改善措施。
这些措施可以包括机床结构的调整、刀具更换的计划、加工过程中的温度控制等。
通过实施这些措施,我们可以有效地降低加工误差,提高产品的加工精度和质量。
第五步:监控和评估效果最后,我们需要监控和评估改善措施的效果。
通过对改善后的加工数据进行分析,我们可以了解到改善措施的实际效果。
如果误差得到了有效的降低,我们可以继续保持改善措施;如果效果不理想,我们可以重新评估误差来源,并调整改善方案。
综上所述,数控机床加工误差的分析和改善是一个逐步思考的过程。
通过收集数据、分析误差来源、确定改善方向、实施改善措施以及监控和评估效果,我们可以有效地降低加工误差,提高产品的加工精度和质量。
机床加工中的精度误差分析与改进

机床加工中的精度误差分析与改进在现代制造业中,机床加工是不可或缺的一环。
在机床加工过程中,精度误差是无法避免的。
而这些精度误差可能会对产品的质量和性能产生负面影响。
因此,对机床加工中的精度误差进行分析,并采取相应的改进措施,对于提高产品的质量和竞争力具有重要意义。
一、精度误差的分类机床加工中的精度误差可分为系统误差和随机误差两类。
1. 系统误差系统误差是指由于机床结构、加工环境、材料特性等因素引起的固定的误差。
主要包括机床刚度误差、定位误差、传动误差等。
系统误差较为固定,通过调整机床或者加工方法可以减少或消除。
2. 随机误差随机误差是指由于材料特性、刀具磨损、操作者技术水平等因素引起的不稳定误差。
随机误差具有一定的随机性和不确定性,很难完全消除。
但可以通过加强操作者技术培训、提高加工环境的稳定性等方法来减小随机误差。
二、精度误差的影响因素1. 机床结构机床结构的刚度、稳定性和精度直接影响到加工的精度。
若机床结构不稳定、刚度不足,则易导致加工中出现振动,从而产生较大的精度误差。
2. 加工环境加工环境的温度、湿度和灰尘等因素对加工的精度有较大影响。
温度的变化会导致机床和工件发生热胀冷缩,从而造成加工精度的变化。
湿度和灰尘会影响机床的润滑效果,降低加工精度。
3. 工件材料工件材料的特性如热膨胀系数、硬度等也会对加工精度产生影响。
不同的材料在加工过程中会有不同的热膨胀量,从而引发精度误差。
4. 刀具磨损刀具磨损是机床加工中常见的问题之一。
刀具磨损会导致切削力增大、刀具载荷分布不均匀等问题,从而对加工精度产生重要影响。
三、精度误差的改进措施针对机床加工中的精度误差,可以采取以下改进措施:1. 优化机床结构通过提高机床的刚度、减小机床的振动,可以有效降低机床加工中的精度误差。
可以采用增加加工刚度的设计方案、优化机床结构、选用高刚度的材料等方法来改善机床的稳定性和精度。
2. 控制加工环境保持加工环境的稳定性是减小精度误差的重要手段。
关于数控加工的误差分析及应对措施

关于数控加工的误差分析及应对措施xx年xx月xx日•数控加工误差概述•数控加工误差分析•数控加工误差应对措施目录•数控加工误差控制案例分析•总结与展望01数控加工误差概述数控加工误差是指工件在数控加工过程中产生的尺寸、形状、表面质量等参数与理想状态下的工件参数之间的偏差。
数控加工误差包括机床、刀具、夹具、工件、切削液等多个因素的影响,这些因素相互作用,导致加工误差的产生。
由于工件或刀具的位置不准确,导致加工出的工件与理想状态下的工件参数之间的偏差。
定位误差由于机床、刀具、夹具等设备的制造、安装、调整不当,导致加工出的工件与理想状态下的工件参数之间的偏差。
几何误差由于切削过程中切削力的大小、方向、作用点等因素发生变化,导致加工出的工件与理想状态下的工件参数之间的偏差。
切削力误差由于机床、工件、刀具等在切削过程中产生的热量变化,导致加工出的工件与理想状态下的工件参数之间的偏差。
热误差1 2 3数控加工误差会导致工件的尺寸、形状、表面质量等参数与理想状态下的工件参数存在偏差,从而影响加工精度。
加工精度下降由于数控加工误差的存在,可能导致工件在装配、使用过程中出现故障,影响产品的整体性能和寿命。
产品质量下降为了控制数控加工误差,需要进行反复的调试和修正,增加了生产周期和成本。
生产效率降低02数控加工误差分析编程误差数控编程过程中,由于计算方法或近似处理等原因,导致加工路径与实际路径存在偏差,从而产生误差。
工件误差工件本身存在形状、尺寸等方面的误差,也会对加工精度产生影响。
机床误差机床本身精度不高或长期使用导致磨损,也会对加工精度产生影响。
刀具误差刀具在加工过程中会受到磨损、变形等因素影响,导致加工精度降低。
误差产生的原因分析03尺寸误差加工过程中,由于刀具磨损、温度变化等因素影响,导致加工出的工件尺寸与设计要求存在偏差。
误差对加工精度的影响01位置误差加工过程中,刀具与工件之间的相对位置不准确,导致加工出的工件形状、尺寸与设计要求存在偏差。
机械加工工艺的技术误差问题及对策
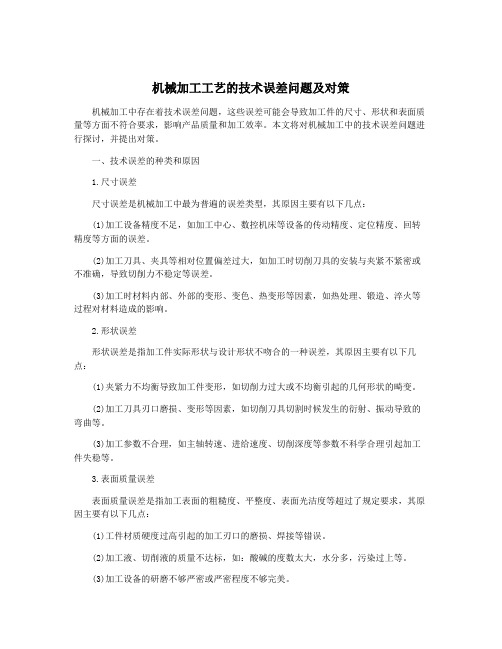
机械加工工艺的技术误差问题及对策机械加工中存在着技术误差问题,这些误差可能会导致加工件的尺寸、形状和表面质量等方面不符合要求,影响产品质量和加工效率。
本文将对机械加工中的技术误差问题进行探讨,并提出对策。
一、技术误差的种类和原因1.尺寸误差尺寸误差是机械加工中最为普遍的误差类型,其原因主要有以下几点:(1)加工设备精度不足,如加工中心、数控机床等设备的传动精度、定位精度、回转精度等方面的误差。
(2)加工刀具、夹具等相对位置偏差过大,如加工时切削刀具的安装与夹紧不紧密或不准确,导致切削力不稳定等误差。
(3)加工时材料内部、外部的变形、变色、热变形等因素,如热处理、锻造、淬火等过程对材料造成的影响。
2.形状误差形状误差是指加工件实际形状与设计形状不吻合的一种误差,其原因主要有以下几点:(1)夹紧力不均衡导致加工件变形,如切削力过大或不均衡引起的几何形状的畸变。
(2)加工刀具刃口磨损、变形等因素,如切削刀具切割时候发生的衍射、振动导致的弯曲等。
(3)加工参数不合理,如主轴转速、进给速度、切削深度等参数不科学合理引起加工件失稳等。
3.表面质量误差表面质量误差是指加工表面的粗糙度、平整度、表面光洁度等超过了规定要求,其原因主要有以下几点:(1)工件材质硬度过高引起的加工刃口的磨损、焊接等错误。
(2)加工液、切削液的质量不达标,如:酸碱的度数太大,水分多,污染过上等。
(3)加工设备的研磨不够严密或严密程度不够完美。
1.选择高精度设备和刀具在进行加工前,要根据所需的工艺要求,选择合适的高精度设备和刀具,如:数控机床、加工中心等,确保设备传动精度、定位精度、回转精度等方面的误差越小越好。
同时,要使用具有高精度、高强度和高耐磨性的刀具,以达到加工精度的要求。
2.严格控制加工参数在进行加工时,要严格控制加工参数,如:主轴转速、进给速度、切削深度等,确保参数的合理科学,能够提高加工效率的同时保证加工质量。
3.优化加工工艺流程在加工过程中,要根据实际情况不断优化工艺流程,及时排查和处理加工中的问题,提高加工质量。
- 1、下载文档前请自行甄别文档内容的完整性,平台不提供额外的编辑、内容补充、找答案等附加服务。
- 2、"仅部分预览"的文档,不可在线预览部分如存在完整性等问题,可反馈申请退款(可完整预览的文档不适用该条件!)。
- 3、如文档侵犯您的权益,请联系客服反馈,我们会尽快为您处理(人工客服工作时间:9:00-18:30)。
参磊 工冷 工 加
WWW. met wo ki 95 . a1 r ng 7 0 com
!生 ! 幽 笪! 塑
圈
。 .。 J 三 。 堇
谶
:
褰 鏊
双 滑 履 水 泥 磨 筒 体 部 分 加 工 工 艺
朝 阳重型机器有限公司 ( 辽宁 120 ) 祝亚峰 2 00 郭丽霞
() 头 前 a调
() b调头 后
公 司引进 了德 国某 公司一 台卧式加 工 中心 ,作 为 C K系 列 主轴箱 的最 终 加工 。该 机床很 快 进 行 了几 次样 件 加
工 ,但在样件加工结果 中,主轴 孔同底 面的平行 度 ,主 轴孔 的同轴度 、圆度无法完全达 到图样要 求 ,多次 经过 三坐标测量机检测 ,检测结果 主轴 孑 同底 面的平行度 为 L
圈与简体段节组焊而成 ,如 图 2所示 。
图 2 简体部件
的缺点 ,新一代管磨机的简体部分多采用双滑履轴 承支 撑 ,由进出料滚 圈与简体 段节焊 接的整 体式简 体结构 。
以 6 .m 4 2 m×1m水泥磨为例 ,介绍如下 。 3 ( )简体部分 由进 口滚 圈 1 1 、简体 段节 2 、出 口滚 圈3 、传 动接管 5组成 。进 、出 口滚圈 与简 体段节之 间
2 .问题的解决
( )平行度 1 首先 ,根据现场实际情况 ,我们了辅助工作 台的平 面度。 同
时针对调头前 与调头后所镗孔 的高度距底 面的距离不 相
等 问题 ,我们反 映给机床生 产公司售后 人 员,他们对 工
作 台垫板进行 了研磨 , 保证工作 台在 向与导轨平行 度
( )传动接管为两端法兰与圆周 开卸 料 口的筒体组 3
焊的结构 ,如 图 3所示 。
( )进 口滚 圈和出 4
的精度有着 直 接 的影 响 ,尤 其对 该 零 件 的平 行度 有 影
响。该零件是用 四个固定等高块支撑 在工 作台上 ,零 件 装夹后 ,在这 四个等高块上有可 能存 在着 虚点 ,这样 引 起零 件在 夹 紧 、松 开 时形 变。 同时我 们 对零 件 进 行分 析 ,可知该零 件距定位侧基 准面距离 不等 ,造 成加工 时
1 双滑履水泥磨简体部分的结构特点 .
传统的水泥行业用管磨机简体部分是 由中空轴 、端 盖和简体采用铰孑螺栓联接而成 ,磨机运转过程 中由主 L
轴承支撑中空轴 ,通过传动装置带动而运转 。这种结 构 形式 由于结构上 的缺点 ,使得 中空轴与端盖 、端 盖与筒 体联接用铰制螺栓在简体运转的过程 中受到剪切 力的作 用 ,容易发生联接螺栓剪断的故障。为克服上述结 构上
进给 ;各轴移动采用海德汉公 司高精度光 栅尺 ,保证 单
轴重复定位精度在 0 0 2 m 以内 ,工作 台采用 圆光栅 , .0 r a 其重复定 位精 度 在 0 0 2 m 内;主轴 跳动 在 0 0 2 m .0 r a .0r a 以内;主轴 与 工作 台平 行 度为 0 05 / 0 m . 0 mm 3 0 m;工 作 台平面度在 60 3 mm×6 0 m 内为 00 m 3m .2 m。经 过计算 和 研究 ,该机床完全有能力加_ T此零件 。 ( )机床 丁装 夹具 的可靠性 2 机床工 装夹具对零 件
在 O0 m 以内。其次 ,我们将 每一 个零件放 在垫块 上 .1 m 之后 ,用手 去推 四个等 高块 ,若有虚接 触 ,即该块 就能 推动 ,则可 以用塞尺检查 ,使其 四个等 高块 都保持 支撑 状态 ,保证零件在夹 紧时不会有 过大 的形 变 、减少形 变 对零件精度的影响 。
图
2
结果各轴定位精度和重复定位精度都符合 出厂精度 要求。 我们 又进 一 对机床进 行多次双轴 联动定位 检测 ,这项 步 精度 在 0~00 8 r 围 内 不 断 变化 ,机床 不 能 保 证 .0 m n范 0O 2 m 的定位精 度 ,也就是说 联动后 定位精度 和重复 .0 m
一
00 0 0 n . 2~ . 8 l m,主 轴 孔 同 轴度 为 q 0 岫. 1—4 . 1 m , O4 m, o 圆度为 0 05~ . 1 m。因此 ,分析并解决 该问题 对保 . 0 00 m
证加工质量 、满足生产需要显得十分重要 。
_ l 定位精度的不确定 ,对零件加工的同轴度有着直接的影响。
( )主轴箱结构 该 机床 的主轴 箱 结构 采 用悬 挂 4 式 ,系统 刚性差 ,同时工作 台装夹零 件后 ,加工 位距 z 向导轨 面垂直距离 大 ,呈立 矩性 ,高宽 比例 为 2 1 : ,加
工 时力矩 大 、稳定性差 。
1 .问题形成的原因分析
( ) 机床的硬件精 度 1 该卧式加 工中心采用工作 台
( 见图 2 。 )
回转 轴 孔 轴 孔 轴 回 转轴
( 3)机 床 各
轴联 动 时 的 精 度
以保 证 形 位 精 度 。为 了 满 足 设 计 要 求 ,我 图 1
保持性
我 们 对
x— x一
当单 轴 的 定 位 精 度和 重 复 定 位 精
度 进 行 了检 测,
《 鬻 囊 目 囊 栏 主持 朱 光明
L. 。。 圜 王 兰
加 工 中 心 加 工 箱 体 误 差 分 析
宝鸡机床集 团有 限公司 ( 陕西 7 1 1 ) 张笑雷 2 0 3 吴 高位
图 1主轴箱体 为我公 司 C K系列产 品中的典型结 构 其 精 度 要 求 高 ,孔 内 有 台
阶 ,两 孑 之 间 L 跨 距 较 长 ,在
加 工 过 程 中 难
孔 在 轴 方向坐标 与回转 台中心不重合 ,若工作 台面与 主轴 在 z向和 向不平行则会造成孑 系轴线 与底 面不平 L 行 ,即 “ 仰头 ”或 “ 低头”,引起两 端孔调 头加工后 距
底 面 高 度 不 同