轴的失效形式和原因分析
发动机高锡铝合金轴瓦失效形式和原因
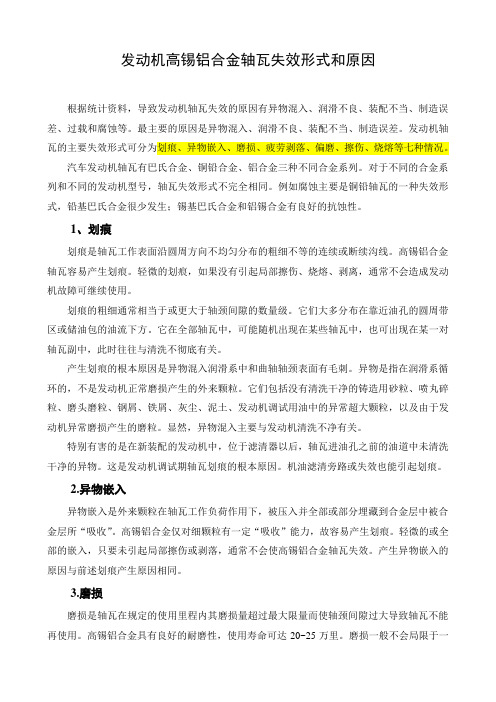
发动机高锡铝合金轴瓦失效形式和原因根据统计资料,导致发动机轴瓦失效的原因有异物混入、润滑不良、装配不当、制造误差、过载和腐蚀等。
最主要的原因是异物混入、润滑不良、装配不当、制造误差。
发动机轴瓦的主要失效形式可分为划痕、异物嵌入、磨损、疲劳剥落、偏磨、擦伤、烧熔等七种情况。
汽车发动机轴瓦有巴氏合金、铜铅合金、铝合金三种不同合金系列。
对于不同的合金系列和不同的发动机型号,轴瓦失效形式不完全相同。
例如腐蚀主要是铜铅轴瓦的一种失效形式,铅基巴氏合金很少发生;锡基巴氏合金和铝锡合金有良好的抗蚀性。
1、划痕划痕是轴瓦工作表面沿圆周方向不均匀分布的粗细不等的连续或断续沟线。
高锡铝合金轴瓦容易产生划痕。
轻微的划痕,如果没有引起局部擦伤、烧熔、剥离,通常不会造成发动机故障可继续使用。
划痕的粗细通常相当于或更大于轴颈间隙的数量级。
它们大多分布在靠近油孔的圆周带区或储油包的油流下方。
它在全部轴瓦中,可能随机出现在某些轴瓦中,也可出现在某一对轴瓦副中,此时往往与清洗不彻底有关。
产生划痕的根本原因是异物混入润滑系中和曲轴轴颈表面有毛刺。
异物是指在润滑系循环的,不是发动机正常磨损产生的外来颗粒。
它们包括没有清洗干净的铸造用砂粒、喷丸碎粒、磨头磨粒、钢屑、铁屑、灰尘、泥土、发动机调试用油中的异常超大颗粒,以及由于发动机异常磨损产生的磨粒。
显然,异物混入主要与发动机清洗不净有关。
特别有害的是在新装配的发动机中,位于滤清器以后,轴瓦进油孔之前的油道中未清洗干净的异物。
这是发动机调试期轴瓦划痕的根本原因。
机油滤清旁路或失效也能引起划痕。
2.异物嵌入异物嵌入是外来颗粒在轴瓦工作负荷作用下,被压入并全部或部分埋藏到合金层中被合金层所“吸收”。
高锡铝合金仅对细颗粒有一定“吸收”能力,故容易产生划痕。
轻微的或全部的嵌入,只要未引起局部擦伤或剥落,通常不会使高锡铝合金轴瓦失效。
产生异物嵌入的原因与前述划痕产生原因相同。
3.磨损磨损是轴瓦在规定的使用里程内其磨损量超过最大限量而使轴颈间隙过大导致轴瓦不能再使用。
浅谈风力发电机主轴轴承失效分析及解决办法
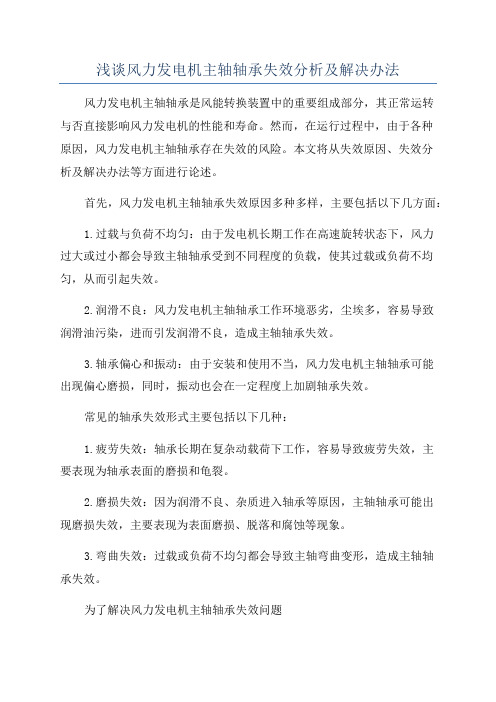
浅谈风力发电机主轴轴承失效分析及解决办法风力发电机主轴轴承是风能转换装置中的重要组成部分,其正常运转与否直接影响风力发电机的性能和寿命。
然而,在运行过程中,由于各种原因,风力发电机主轴轴承存在失效的风险。
本文将从失效原因、失效分析及解决办法等方面进行论述。
首先,风力发电机主轴轴承失效原因多种多样,主要包括以下几方面:1.过载与负荷不均匀:由于发电机长期工作在高速旋转状态下,风力过大或过小都会导致主轴轴承受到不同程度的负载,使其过载或负荷不均匀,从而引起失效。
2.润滑不良:风力发电机主轴轴承工作环境恶劣,尘埃多,容易导致润滑油污染,进而引发润滑不良,造成主轴轴承失效。
3.轴承偏心和振动:由于安装和使用不当,风力发电机主轴轴承可能出现偏心磨损,同时,振动也会在一定程度上加剧轴承失效。
常见的轴承失效形式主要包括以下几种:1.疲劳失效:轴承长期在复杂动载荷下工作,容易导致疲劳失效,主要表现为轴承表面的磨损和龟裂。
2.磨损失效:因为润滑不良、杂质进入轴承等原因,主轴轴承可能出现磨损失效,主要表现为表面磨损、脱落和腐蚀等现象。
3.弯曲失效:过载或负荷不均匀都会导致主轴弯曲变形,造成主轴轴承失效。
为了解决风力发电机主轴轴承失效问题1.加强检查和维护:定期对风力发电机主轴轴承进行检查,确保其润滑状态良好,及时更换磨损严重的轴承。
2.提高轴承负荷承载能力:采用高强度材料制造轴承,增加轴承的负荷承载能力以及寿命。
3.减小振动幅度:通过优化设计和加强安装质量,降低风力发电机的振动幅度,减少对主轴轴承的影响。
4.加强润滑管理:严格控制风力发电机主轴轴承的润滑油品质和污染控制,确保轴承良好润滑,减少摩擦磨损。
总之,风力发电机主轴轴承的失效对风力发电机的性能和寿命具有重要影响。
通过加强检查和维护、提高轴承负荷承载能力、减小振动幅度、加强润滑管理等措施,可以有效预防和解决风力发电机主轴轴承失效问题,提高风力发电机的可靠性和经济性。
轴的失效形式和原因分析

轴的失效形式与特征轴是各种机械中最为普通而不可缺少的重要零件,根据使用条件的差异,轴有很大不同的类型,按其功能和所受载荷的不同,一般可分为心轴、转轴和传动轴三类。
心轴主要承受弯矩而不承受扭矩,它只能旋转零件起支撑作用,并不传递动力。
传动轴主要承受扭矩,其基本功能只传输动力,而转轴既承受弯矩又承受扭矩,它兼有支撑与传输动力的双倍功能。
由于各类轴自身的材质、结构和承载条件不同、运行环境和使用操作的差异可能发生各种不同类型的失效时有发生,失效的形式和特征也各异。
一.疲劳断裂疲劳断裂是指轴在交变应力的作用下,经过多次反复后发生的突然断裂。
是轴类零件在其服役过程中主要的失效形式。
轴在疲劳断裂前没有明显的塑性变形,反映在宏观形态上属于脆性断裂。
断口形貌有其本身的特征,在宏观形貌上可分为三个区域:图1 疲劳断裂示意图1)疲劳源区:通常是指断口上的放射源的中心点,源区表面细密光滑,多发生于轴的表面。
由于表面常存在缺口、刀痕、沟槽等缺陷,导致应力集中,从而诱发疲劳裂纹。
疲劳断口上可能只有一个疲劳裂纹源,也可能出现几个裂源。
疲劳源区有时存在疲劳台阶,这是由于不同高度的多源疲劳裂纹在其扩展过程中连接形成的。
2)疲劳扩展区:是断口上最重要的特征区域,海滩花样(贝壳花样、疲劳弧线、疲劳条带)的存在是鉴别疲劳断裂的宏观依据。
有时必须借住高倍的电子显微镜才能观察到疲劳条带。
根据弧线数量和间距可以略微地判断零件所承受交变应力幅值,弧线规律分布表示交变载荷是平稳的。
承受应力状态、工作环境以及材料性质的不同,疲劳裂纹扩展的形貌所异。
每条疲劳条带表示载荷的一次循环,条带间距离与外加载荷的应力幅值有关。
当交变载荷变化不大、零件内的残余应力很小时,往往不出现弧线或不明显,所以不是所以疲劳断口有存在疲劳条带,低周疲劳断口有时可呈现韧窝状,有时也可出现轮胎花样(图2),所以疲劳条带并不是疲劳断裂的唯一显微特征。
高频疲劳断口或腐蚀疲劳断口上的疲劳条带比较模糊,较难判断。
45号钢电机轴断裂失效分析

2江苏王牌 直流 电机制 造有 限公 司 , 江苏宝应 2 5 0 ) 280
摘 要 利 用光学金相显微 镜 、 学分析 、 化 扫描 电镜及能谱 分析 , 4 对 5号钢 电机轴在 使用过
程 中发生的断裂进行检测和 分析 , 结果 表明钢 中有非金 属夹 杂物 , 表观质 量差 、 金相 组织不 够优
表 1 化 学 成 分 分析 结 果
零件 常 用材料 , 经 过 调 质 ( 火 ) , 得 到 较 它 正 后 可 好 的切 削性能 , 且 能 获 得较 高 的强 度和 韧 性 等 而
综合 机械 性能 。失效 主 要是指 某零件 由于某种 原 因导致 某尺寸 、 形状 或 材 料 的组 织 与 性 能 的变 化
辉 纹 , 部出现 二次 裂纹 , 局 故可 推断 电机 轴 的断 裂 形 式为疲 劳断 裂 。比较光 滑 的疲 劳 区产 生 的原 因 是 由于在 疲劳 裂 纹 发 生和 发 展 的 区域 , 循 环 载 在 荷 的作 用下 , 多次发 生撞击 和研 磨现 象 , 疲劳 区 使 形成 光滑 的外 观 , 且应 力循环 的次数 越 多 , 劳 并 疲
区越 光滑 。在 最 后破 断 区 由于是 突 然 性 破坏 , 呈
1 失效 分 析
1 1 化 学分 析 . 来自表 1所示 为样 品化 学 分析 结 果 , 可见 锻 件 的 化学 成 分 符 合 标 准 J / 3 7 2 0 《 型 碳 素 B T69 - 06 大
滚动轴承常见失效形式及原因分析
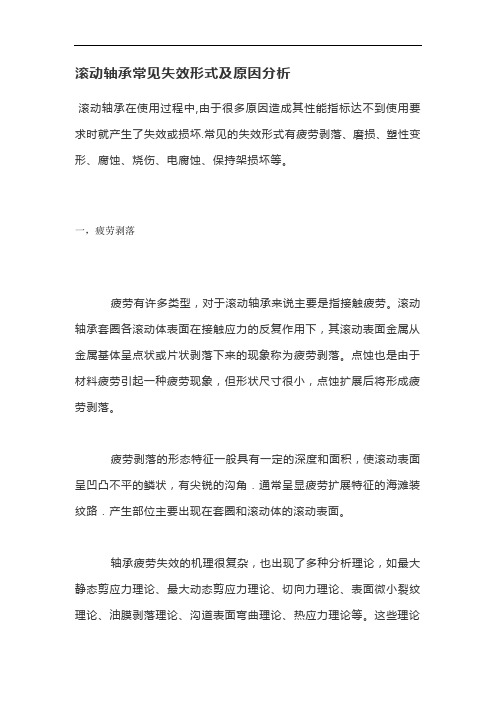
滚动轴承常见失效形式及原因分析滚动轴承在使用过程中,由于很多原因造成其性能指标达不到使用要求时就产生了失效或损坏.常见的失效形式有疲劳剥落、磨损、塑性变形、腐蚀、烧伤、电腐蚀、保持架损坏等。
一,疲劳剥落疲劳有许多类型,对于滚动轴承来说主要是指接触疲劳。
滚动轴承套圈各滚动体表面在接触应力的反复作用下,其滚动表面金属从金属基体呈点状或片状剥落下来的现象称为疲劳剥落。
点蚀也是由于材料疲劳引起一种疲劳现象,但形状尺寸很小,点蚀扩展后将形成疲劳剥落。
疲劳剥落的形态特征一般具有一定的深度和面积,使滚动表面呈凹凸不平的鳞状,有尖锐的沟角.通常呈显疲劳扩展特征的海滩装纹路.产生部位主要出现在套圈和滚动体的滚动表面。
轴承疲劳失效的机理很复杂,也出现了多种分析理论,如最大静态剪应力理论、最大动态剪应力理论、切向力理论、表面微小裂纹理论、油膜剥落理论、沟道表面弯曲理论、热应力理论等。
这些理论中没有一个理论能够全面解释疲劳的各种现象,只能对其中的部分现象作出解释。
目前对疲劳失效机理比较统一的观点有:>>>>1、次表面起源型次表面起源型认为轴承在滚动接触部位形成油膜的条件下运转时,滚动表面是以内部(次表面)为起源产生的疲劳剥落。
>>>>2、表面起源型表面起源型认为轴承在滚动接触部位未形成油膜或在边界润滑状态下运转时,滚动表面是以表面为起源产生的疲劳剥落。
>>>>3、工程模型工程模型认为在一般工作条件下,轴承的疲劳是次表面起源型和表面起源型共同作用的结果。
疲劳产生的原因错综复杂,影响因素也很多,有与轴承制造有关的因素,如产品设计、材料选用、制造工艺和制造质量等;也有与轴承使用有关的因素,如轴承选型、安装、配合、润滑、密封、维护等。
具体因素如下:(1)制造因素a.产品结构设计的影响产品的结构设计是根据使用性能目标值来确定的,这些目标值如载荷容量、寿命、精度、可靠性、振动、磨损、摩擦力矩等。
汽车发动机曲轴的热处理与失效分析
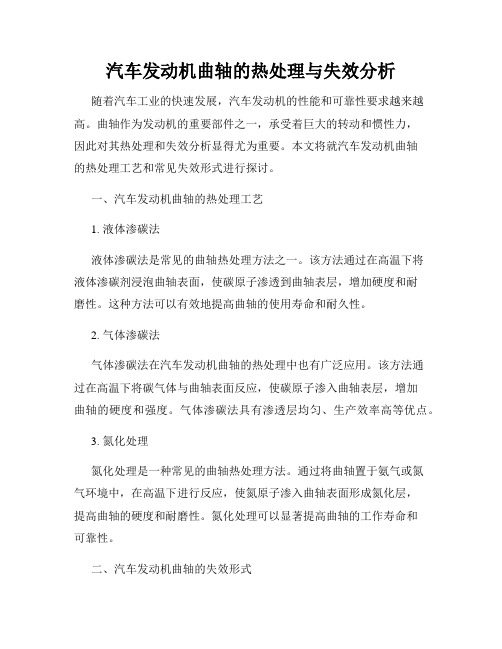
汽车发动机曲轴的热处理与失效分析随着汽车工业的快速发展,汽车发动机的性能和可靠性要求越来越高。
曲轴作为发动机的重要部件之一,承受着巨大的转动和惯性力,因此对其热处理和失效分析显得尤为重要。
本文将就汽车发动机曲轴的热处理工艺和常见失效形式进行探讨。
一、汽车发动机曲轴的热处理工艺1. 液体渗碳法液体渗碳法是常见的曲轴热处理方法之一。
该方法通过在高温下将液体渗碳剂浸泡曲轴表面,使碳原子渗透到曲轴表层,增加硬度和耐磨性。
这种方法可以有效地提高曲轴的使用寿命和耐久性。
2. 气体渗碳法气体渗碳法在汽车发动机曲轴的热处理中也有广泛应用。
该方法通过在高温下将碳气体与曲轴表面反应,使碳原子渗入曲轴表层,增加曲轴的硬度和强度。
气体渗碳法具有渗透层均匀、生产效率高等优点。
3. 氮化处理氮化处理是一种常见的曲轴热处理方法。
通过将曲轴置于氨气或氮气环境中,在高温下进行反应,使氮原子渗入曲轴表面形成氮化层,提高曲轴的硬度和耐磨性。
氮化处理可以显著提高曲轴的工作寿命和可靠性。
二、汽车发动机曲轴的失效形式1. 疲劳断裂汽车发动机曲轴承受着巨大的转动和振动力,长期工作下容易发生疲劳断裂。
曲轴的弯曲应力和旋转应力作用下,会产生应力集中现象,导致曲轴发生疲劳断裂。
疲劳断裂的发生会导致曲轴的完全失效,严重影响发动机的工作正常性。
2. 磨损曲轴在长时间工作中,会与连杆轴承、活塞等零部件产生摩擦,从而导致磨损。
磨损严重影响曲轴的精度和运转平稳性,进一步影响整个发动机的工作效率和寿命。
3. 腐蚀汽车发动机在工作中,由于油污和湿度等环境因素的影响,曲轴表面容易发生腐蚀。
腐蚀会导致曲轴表面的金属材料逐渐溶解,使曲轴的强度大幅下降,最终导致曲轴的失效。
三、失效分析与预防措施1. 失效分析在曲轴的热处理与失效分析中,需要通过工艺参数的分析和实验数据的对比,来确定曲轴热处理工艺的优化方案。
同时,可以通过金相显微镜等测试手段,对曲轴的金属组织进行分析,查找潜在的裂纹和磨损等问题。
轴承主要失效形式

轴承的主要失效形式1、剥离损伤状态:轴承在承受旋转载荷时,内圈、外圈的滚道或滚动体面由于滚动疲劳而呈现鱼鳞状的剥离现象。
原因:载荷不当;安装不良(非直线性);力矩载荷;异物进入、进水;润滑不良、润滑剂不合适;轴承游隙不适当;轴承箱精度不好、轴承箱的刚性不均、轴的挠度大;生锈、侵蚀点、擦伤和压痕(表面变形现象)。
措施:检查载荷的大小;改善安装方法、改善密封装置、停机时防锈;使用适当粘度的润滑剂、改善润滑方法;检查轴和轴承箱的精度;检查游隙。
2、剥离损伤状态:呈现出带有轻微磨损的暗面,暗面上由表及里有多条深至5~10μm,的微小裂缝,并在大范围内发生微小脱落(微小剥离)。
原因:润滑剂不合适;异物进入了润滑剂内;润滑剂不良造成表面粗糙;配对滚动零件的表面质量不好。
措施:选择润滑剂;改善密封装置;改善配对滚动零件的表面粗糙度。
3、卡伤损伤状态:卡伤是指由于在滑动面的微小烧伤汇总而产生的表面损伤,表面为滑道面、滚道面圆周方向的线状伤痕。
滚子断面的摆线状伤痕靠近滚子端面的轴环面的卡伤。
原因:过大载荷、过大预压;润滑不良;异物咬入;内圈外圈的倾斜、轴的挠度;轴、轴承箱的精度。
4、擦伤损伤状态:所谓擦伤,是在滚道面和滚动面上,由随着滚动的打滑和油膜热裂产生的微小烧伤汇总而成的表面损伤。
原因:高速轻载荷;急加减速;润滑剂不适当;水的进入。
措施:改善预压;改善轴承游隙;使用油膜性好的润滑剂;改善润滑防震;改善密封装置。
5、断裂损伤状态:由于对滚道的挡边或滚子角的局部施加冲击或过大载荷,而使其一小部分断裂。
原因:安装时受到了打击;载荷过大;跌落等;使用不良。
措施:改善安装方法(采用热装、使用适当的工具夹);改善载荷条件;轴承安装到位,使挡边受支承。
6、裂纹、裂缝损伤状态:滚道轮或滚动体有事会产生裂纹损伤。
如果继续使用,裂纹将发展为裂缝。
原因:过大过盈量;过大载荷、冲击载荷;剥落有所发展;由于滚道轮或安装构件的接触而产生的发热和微震磨损;蠕变造成的发热;锥轴的锥角不良;轴的圆柱度不良;轴台阶的圆角半径比轴承倒角大而造成与轴承倒角的干扰。
滚动轴承的失效形式及寿命计算

轴承寿命曲线
滚动轴承的失效形式及寿命计算
1.3 基本额定动载荷及寿命计算
大量试验表明:对于相同型号的轴承,在不同载荷F1, F2 , F3 ,…作用下,若轴承的 寿命分别为L1 , L2 , L3 ,… (106转),则它们之间有如下的关系:
滚动轴承的失效形式及寿命计算
1.4 当量动载荷的计算
滚动轴承的基本额定动载荷是在一定条件下确定的。对向心轴承是指承受纯径向载荷; 对推力轴承是指承受中心轴向载荷。如果作用在轴承上的实际载荷与上述条件不一样,必须 将实际载荷换算为与上述条件相同的载荷后,才能与基本额定动载荷进行比较。换算后的载 荷是一种假定的载荷,称为当量动载荷。径向和轴向载荷分别用Fr和Fa表示。
对于向心轴承,径向当量动载荷P与实际载荷Fr和Fa的关系式为
径向轴承只承受径向载荷时,其当量动载荷为
推力轴承只能承受轴向载荷,其当量动载荷为
滚动轴承的失效形式及寿命计算
1.1 主要失效形式
1. 滚动体ห้องสมุดไป่ตู้力
滚动轴承在通过轴心线的轴向载荷(中心轴向载荷)犉犪作用下,可认为各滚动体所承 受的载荷是相等的。当轴承受纯径向载荷Fr作用时(见图),由于各接触点上存在弹性变形, 使内圈沿Fr方向下移一距离δ,上半圈滚动体不承受载荷,而下半圈各滚动体承受不同的载 荷。处于Fr作用线最下位置的滚动体受载最大Fmax ,而远离作用线的各滚动体,其受载就逐 渐减小。对于α=0°的向心轴承可以导出
滚动轴承的失效形式及寿命计算
2. 滚动轴承的失效形式
(1)疲劳破坏 (2)塑性变形
径向载荷的分布
滚动轴承的失效形式及寿命计算
1.2 轴承寿命
轴承的套圈或滚动体的材料首次出现疲劳点蚀前, 一个套圈相对于另一个套圈的转数,称为轴承的寿命。 寿命还可以用在恒定转速下的运转小时数来表示。
- 1、下载文档前请自行甄别文档内容的完整性,平台不提供额外的编辑、内容补充、找答案等附加服务。
- 2、"仅部分预览"的文档,不可在线预览部分如存在完整性等问题,可反馈申请退款(可完整预览的文档不适用该条件!)。
- 3、如文档侵犯您的权益,请联系客服反馈,我们会尽快为您处理(人工客服工作时间:9:00-18:30)。
轴的失效形式与特征轴是各种机械中最为普通而不可缺少的重要零件,根据使用条件的差异,轴有很大不同的类型,按其功能和所受载荷的不同,一般可分为心轴、转轴和传动轴三类。
心轴主要承受弯矩而不承受扭矩,它只能旋转零件起支撑作用,并不传递动力。
传动轴主要承受扭矩,其基本功能只传输动力,而转轴既承受弯矩又承受扭矩,它兼有支撑与传输动力的双倍功能。
由于各类轴自身的材质、结构和承载条件不同、运行环境和使用操作的差异可能发生各种不同类型的失效时有发生,失效的形式和特征也各异。
一.疲劳断裂疲劳断裂是指轴在交变应力的作用下,经过多次反复后发生的突然断裂。
是轴类零件在其服役过程中主要的失效形式。
轴在疲劳断裂前没有明显的塑性变形,反映在宏观形态上属于脆性断裂。
断口形貌有其本身的特征,在宏观形貌上可分为三个区域:图1疲劳断裂示意图1)疲劳源区:通常是指断口上的放射源的中心点,源区表面细密光滑,多发生于轴的表面。
由于表面常存在缺口、刀痕、沟槽等缺陷,导致应力集中,从而诱发疲劳裂纹。
疲劳断口上可能只有一个疲劳裂纹源,也可能出现几个裂源。
疲劳源区有时存在疲劳台阶,这是由于不同高度的多源疲劳裂纹在其扩展过程中连接形成的。
2)疲劳扩展区:是断口上最重要的特征区域,海滩花样(贝壳花样、疲劳弧线、疲劳条带)的存在是鉴别疲劳断裂的宏观依据。
有时必须借住高倍的电子显微镜才能观察到疲劳条带。
根据弧线数量和间距可以略微地判断零件所承受交变应力幅值,弧线规律分布表示交变载荷是平稳的。
承受应力状态、工作环境以及材料性质的不同,疲劳裂纹扩展的形貌所异。
每条疲劳条带表示载荷的一次循环,条带间距离与外加载荷的应力幅值有关。
当交变载荷变化不大、零件内的残余应力很小时,往往不出现弧线或不明显,所以不是所以疲劳断口有存在疲劳条带,低周疲劳断口有时可呈现韧窝状,有时也可出现轮胎花样(图2),所以疲劳条带并不是疲劳断裂的唯一显微特征。
高频疲劳断口或腐蚀疲劳断口上的疲劳条带比较模糊,较难判断。
图3 为外加载荷较小,但轴周应力较集中,所以扩展前区条带不明显,随截面的减小载荷逐渐增大,疲劳条带较明显,瞬时断裂区较小。
图4 外加载荷较大,呈低周疲劳断裂形貌,由于材料强度较高、塑性较差,宏观疲劳条带不明显,瞬时断裂区较大3)瞬时断裂区:疲劳裂纹扩展到最后阶段的快速断裂区,此区 域灰暗,粗糙,呈撕裂状或粗晶粒状,或在45°角上呈延生剪断(剪 切唇)。
轴类的疲劳断裂仅就承载性质而言,可分为:单向弯曲疲劳断口、 双向弯曲疲劳断裂、旋转弯曲疲劳断裂、扭转疲劳断裂、接触疲劳断 裂和复合应力疲劳断裂等。
二. 单向弯曲疲劳断裂轴在弯曲载荷的作用下,其表面应力最大,中心应力最小,一侧 受拉,另一侧受压(图5)。
在长期的反复的交替作用下,由于轴的表 面经常存在缺口、刀痕、沟槽等缺陷,导致应力集中,从而诱发疲劳图3图2轮胎花样(TEM图8 不同载荷下单向弯曲疲劳断口示意图裂纹,成为疲劳源。
随着交变应力的继续,疲劳裂纹沿着与正应力相 垂直的方向扩展,直至发生突然断裂。
其断口与轴线成 90°。
单向疲劳断口具有比较典型的疲劳断裂特征, 可明显地观察到裂 源区、扩展区和粗糙的瞬时断裂区(图 6)图5 图6对于有台架转角的轴,其断口往往不是一个平面,而是呈碟状曲 面,这是由于圆角根部应力集中的结果(图 7)。
从断口上可以看出弯曲载荷的大小,如图 8所示。
a 为低载荷, b 为高载荷形态,其瞬时断裂区的大小明显不同。
+ —*-拉 ab另外轴表面无应力集中时,瞬时断裂区载荷较小时,瞬时断裂区较小。
而有应力集中,如有台阶、缺口、粗糙的加工刀痕等,瞬时断裂区较大。
三.双向弯曲疲劳断裂固定心轴承受上下正负两个方向交变弯曲载荷,轴的上小对应都受拉、压两面变化的应力,由此导致的断裂称之为轴双向弯曲疲劳断裂。
双向弯曲疲劳断裂的特征:与单向弯曲疲劳断裂的区别之一是双向弯曲疲劳断面有两个裂源,分别处于在相对的两侧。
如果两个方向上的弯矩幅值相等,则在相对的两个靠近表面的区域内产生疲劳源,并同时向内扩展。
两个裂纹扩展深度大致相等(图9a)。
当轴承受到弯矩幅值较低时,两个疲劳源往往不会同时产生。
因此两条裂纹的扩展深度将会相差很大(图9b)。
轴上有无应力集中以及应力集中程度的大小,对疲劳断口的形貌影响很大,如图10所示不同载荷水平与应力集中程度下的疲劳断口b图10四.旋转弯曲疲劳断裂1)裂源的形成轴承受旋转弯曲时,轴上各点均受到拉伸应力和压缩应力的连续交替作用,裂纹可能起源于表面任何一点。
承受载荷不大时,疲劳源往往只在一处生核,并向内部和两侧扩展,而弯曲载荷逆轴的旋转方向移动,此时疲劳裂纹的前沿顺着载荷的移动方向扩展速率较快,逆载荷移动方向扩展速率较慢,从而导致裂纹前沿的偏移,使瞬时断裂区往往是向轴旋转的相反方向偏移一个角度,通常偏移角可达15°或更大。
图11旋转弯曲疲劳断口瞬时断裂区偏转示意图2)宏观断口特征:(1)疲劳裂纹垂直轴向心部扩展,断口上出现疲劳条带;(2)瞬时断裂区逆轴旋转方向偏转一定角度。
轴上应力大小、应力集中程度不同断口出现不同特点:a.交变载荷较低,无应力集中的光滑轴往往只产生一个疲劳源,瞬时断裂区在外周。
b.轴有台阶或缺口等应力集中,而且弯曲矩幅值大,则会产生多次疲劳源,且同时扩展,最后形成圆弧疲劳弧线和瞬时断裂区,如图12所示。
图12多个疲源的旋转断口承受应力水平高,应力集中又严重时,瞬时断裂区位于中心,则断裂前的交变载荷循环次数一般不会超过万次,其应力水平约为疲劳极限的1.5 ~2倍。
所以轴上的应力大小、应力集中程度不同,其旋转弯曲疲劳断口也呈现不同的特点(图13)图13应力水平及应力集中程度对旋转弯曲疲劳断口形态的影响示意图五.轴的扭转疲劳断裂轴在机械中承担传递扭矩,承受扭转载荷的作用,轴的表面所受到的应力最大,而心部为零,如图14所示。
图14轴扭转剪应力分布图1.扭转疲劳断裂的产生与类型轴在承受扭转力时,其力矩在轴的横截面与纵截面上引起剪应力,45°斜截面上产生拉应力和压应力。
在交变应力作用下,疲劳源优先在轴的表面的薄弱点萌生,其扩展有两种可能:1)沿最大拉应力相垂直的方向扩展,称为正断型,一般出现在脆性材料上;2)沿最大剪应力作用面扩展断裂的称为切断型,一般出现在塑性较好的材料上。
图15轴上任一点的应力状态对于承受交变扭转载荷的轴,其纵向应力集中是同样重要的,而纵向应力集中更具有危险性,因为材料中非金属夹杂物总是平行于轴线方向,成为先天性的微裂纹,成为疲劳源。
所以扭转疲劳裂纹常在纵向夹杂物、表面划痕或键槽尖角等处发生。
2.扭转疲劳断裂的特征1)切断型扭转疲劳断裂:断口垂直轴线的平断口或台阶型2)正断型扭转疲劳断裂:断口多呈斜面状、棘轮状或锯齿状和星状棘轮状断口通常是单向变化的扭转应力下形成,在反复的扭转应力作用下,首先在缺口、尖角或某些薄弱环节产生多源疲劳源,随后在拉伸应力作用下,沿着与主轴线成45°角方向扩展,同时在单向扭转力矩的作用下,裂纹呈螺旋状向中心扩展致断。
锯齿型断口是在双向交变扭转应力作用下形成。
e C dC 0 C^U)图16扭转疲劳断裂类型六.轴的接触疲劳轴件的接触疲劳多产生在轴与轴承滚针相接触的表面,经反复的滚动或滑动而在高的循环接触应力作用下产生的兼有疲劳和摩擦特征的一种破坏形式。
表现为轴的表面损伤,如出现麻点或剥落。
七•轴超载一次性断裂(有两种破坏形式)1.延性破坏是在纯扭转过程中,剪切应力超过了材料剪切强度而产生与轴线方向垂直或平行的剪切断裂。
2.脆性破坏是最大拉伸应力超过其抗拉强度之后而产生的与最大拉应力方向相垂直的正断断裂。
轴的脆性断裂通常是指不发生塑性变形或只有少量塑性的突然断裂,断裂前无宏观变形预兆,所以是非常危险的断裂。
发生脆性断裂的原因很多,除淬火硬度过高,回火不足,加热温度过高发生过热过烧等因素外,常见的有以下几种:1)脆性相或杂质原子在晶格上沉淀,是导致金属产生沿晶断裂的主要原因之一。
(1)晶格上存在脆性相,如碳化物。
在外力作用下,由于变形能力不同,首先形成微空洞,这些空洞长大连接在一起,形成沿晶裂纹。
或折出脆性相粒子连在一起,形成连续的脆性薄膜而分割基体的界面,形成脆断。
(2)晶界上杂质元素存在降低了晶界聚合能,从而为沿晶断裂提供了有利条件。
因此,在一定的条件下造成了金属的沿晶断裂。
2)氢脆:是指由于氢渗入钢件内部而在低应力作用下产生的一种脆性断裂。
大型轴件发生氢脆断裂也是一种常见的失效形式。
钢中氢的来源由冶炼过程中吸收的,或加工、使用过程中渗入的。
一般认为溶解在钢中的氢通常是以原子状态下存在的。
氢原子为尽量降低能量而与杂质原子、位错、空位等相互作用,力图结合成氢分子,在钢的晶格或缺陷处富集,形成高压。
使微孔洞周围形成高的应力集中和滑移,在应力的作用下,使空洞不断长大,合并形成裂纹,扩展至一定程度时,产生突丝脆性断裂。
3)回火脆性:淬火钢回火时,其冲击韧性随回火温度升高出现复杂的变化,在某些温度范围内使冲击韧性下降。
在250〜350 C和450〜600C的温度区间韧性下降,而在300C左右和500C左右出现两个低谷,即产生脆性现象,通称为回火脆性。
250〜350 C区间产生的脆性称第一类回火脆性,是一种不可逆回火脆性。
它与残余奥氏体的转变、马氏体分解沿晶界和亚晶界析出薄膜状渗碳体以及S.P.N 等杂质元素在晶界的偏聚等因素有关。
第一类回火脆性对力学性能影响程度是不同的。
对强度影响较小,即拉伸和弯曲应力对回火脆性的敏感程度较小。
对应力集中较严重,冲击载荷较大或承受扭转载荷的工件。
要求较大的塑性和韧性与强度相配合时,会增大脆性开裂的危险性。
对于应力集中不严重,承受拉伸、压缩或弯曲应力工作的工件影响较小。
450〜600 C区间的称第二类回火脆性,是一种可逆的回火脆性。
主要含有Ni、Cr、Mn等元素的合金钢中,并与钢中的P、As、Sb和Sn 等杂质元素有关。
回火脆性只有马氏体组织在回火过程中才产生高温回火脆性,其实其它原始组织在高温回火脆性区回火也会发生不同程度的回火脆性。
第二类回火脆性敏感程度按F-P、B M的顺序增大,另外钢的回火脆性倾向随奥氏体晶粒的增大而增大。
第二类回火脆性可通过高温回火后快速冷却来抑制回火脆性的发生。
但对大型工件,由于心部冷却速度达不到要求,使这种方式受到限制。
另一方面快速冷却又会在工件中产生很大的残余内应力,故对大型工件往往需要采用低于回火脆性温度(450C)进行补充回火脆性断裂的基本特征:脆性断裂按断裂机制可为两类:解理断裂(穿晶断裂)和沿晶断裂。
其共同特征为:(1)断口附近没有颈缩现象,开裂边缘不存在剪切“唇口”(2)断裂方向一般垂直于最大主应力,断口表面平齐。