无损检测技术,原理,方案。
无损检测实施方案

无损检测实施方案一、背景介绍无损检测是一种通过对被检测物体进行表面和内部缺陷的检测,而不破坏被检测物体的方法。
在工业生产和科学研究中,无损检测被广泛应用于材料、零部件、设备等领域,以确保产品质量和安全性。
本文将就无损检测的实施方案进行详细介绍。
二、无损检测的原理和方法无损检测的原理是利用各种物理学原理和技术手段,如超声波、X射线、磁粉、涡流等,对被检测物体进行全面、准确的检测。
其中,超声波检测是最常用的方法之一,通过超声波的传播和反射来检测材料内部的缺陷;X射线检测则是利用X射线的透射性质,对材料进行内部缺陷的检测;磁粉和涡流检测则是利用材料对磁场的响应来检测材料表面和近表面的缺陷。
这些方法各有特点,可以根据被检测物体的特点和要求来选择合适的方法进行检测。
三、无损检测的实施步骤1. 制定检测计划:在进行无损检测之前,需要制定详细的检测计划,包括被检测物体的材料、结构、尺寸等信息,以及检测的要求和标准。
2. 选择检测方法:根据被检测物体的特点和要求,选择合适的无损检测方法,如超声波、X射线、磁粉、涡流等。
3. 准备检测设备:根据选择的检测方法,准备相应的检测设备和工具,包括超声波探头、X射线发射器、磁粉液、涡流探头等。
4. 进行检测操作:按照检测计划和方法,进行无损检测操作,对被检测物体进行全面、细致的检测。
5. 分析和评定检测结果:根据检测数据和图像,对检测结果进行分析和评定,判断被检测物体是否存在缺陷,以及缺陷的类型和程度。
6. 编制检测报告:根据检测结果,编制详细的检测报告,包括被检测物体的信息、检测方法和过程、检测结果和评定等内容。
四、无损检测的应用领域无损检测广泛应用于航空航天、汽车制造、铁路运输、石油化工、电力能源、建筑结构、核工业等领域。
在航空航天领域,无损检测可以用于飞机结构、发动机零部件、液压系统等的检测;在汽车制造领域,无损检测可以用于车身、发动机、变速箱等零部件的质量检测;在石油化工领域,无损检测可以用于管道、储罐、压力容器等设备的安全检测。
无损探伤方法及主要原理

无损探伤方法及主要原理无损探伤,也被称作无损检测或无损评估,是指在不影响被测物体使用性能的前提下,通过一系列技术手段对其内部及表面的结构、性质、状态进行检测,并据此判断其是否存在缺陷或不均匀性,从而评估其适用性、可靠性及安全性。
无损探伤技术广泛应用于航空、航天、核能、电力、石油化工、铁路、桥梁、建筑等各个工业领域。
一、无损探伤的主要方法超声检测(Ultrasonic Testing, UT)超声检测是利用超声波在介质中传播时,遇到不同声阻抗的界面会产生反射、折射、透射和散射等物理现象,通过接收和处理这些现象带来的超声波信号,对被测物体的内部结构和缺陷进行检测和评估。
超声检测适用于金属、非金属、复合材料等多种材料,对裂纹、夹杂、气孔等体积型缺陷有很高的检出率。
射线检测(Radiographic Testing, RT)射线检测是利用X射线或γ射线穿透被测物体时,由于物体内部不同部位对射线的吸收和散射能力不同,从而在射线照片上形成不同的灰度图像,通过观察和分析这些图像来检测物体内部的缺陷。
射线检测适用于检测铸件、焊接件等材料的内部缺陷,如气孔、夹渣、未焊透等。
磁粉检测(Magnetic Particle Testing, MT)磁粉检测是利用磁粉在磁场作用下的排列规律,通过观察磁粉在被测物体表面的分布和形态来检测表面或近表面的裂纹等缺陷。
磁粉检测适用于铁磁性材料的表面缺陷检测,如锻件、铸件、焊接件等。
渗透检测(Penetrant Testing, PT)渗透检测是利用毛细作用原理,将含有荧光染料或着色染料的渗透液施加在被测物体表面,经过一段时间的渗透后,去除多余的渗透液,再施加显像剂,使渗入缺陷的渗透液在紫外光或白光下显现出来,从而检测表面开口的缺陷。
渗透检测适用于非多孔性材料的表面开口缺陷检测,如裂纹、气孔、疏松等。
涡流检测(Eddy Current Testing, ET)涡流检测是利用交变磁场在被测导体中感应出涡流,涡流又会产生与原磁场相交的磁场,从而影响原磁场的分布。
无损检测的原理及应用
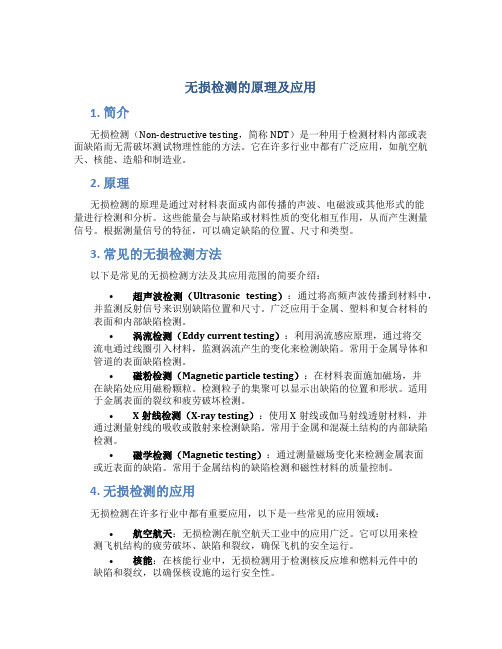
无损检测的原理及应用1. 简介无损检测(Non-destructive testing,简称NDT)是一种用于检测材料内部或表面缺陷而无需破坏测试物理性能的方法。
它在许多行业中都有广泛应用,如航空航天、核能、造船和制造业。
2. 原理无损检测的原理是通过对材料表面或内部传播的声波、电磁波或其他形式的能量进行检测和分析。
这些能量会与缺陷或材料性质的变化相互作用,从而产生测量信号。
根据测量信号的特征,可以确定缺陷的位置、尺寸和类型。
3. 常见的无损检测方法以下是常见的无损检测方法及其应用范围的简要介绍:•超声波检测(Ultrasonic testing):通过将高频声波传播到材料中,并监测反射信号来识别缺陷位置和尺寸。
广泛应用于金属、塑料和复合材料的表面和内部缺陷检测。
•涡流检测(Eddy current testing):利用涡流感应原理,通过将交流电通过线圈引入材料,监测涡流产生的变化来检测缺陷。
常用于金属导体和管道的表面缺陷检测。
•磁粉检测(Magnetic particle testing):在材料表面施加磁场,并在缺陷处应用磁粉颗粒。
检测粒子的集聚可以显示出缺陷的位置和形状。
适用于金属表面的裂纹和疲劳破坏检测。
•X射线检测(X-ray testing):使用X射线或伽马射线透射材料,并通过测量射线的吸收或散射来检测缺陷。
常用于金属和混凝土结构的内部缺陷检测。
•磁学检测(Magnetic testing):通过测量磁场变化来检测金属表面或近表面的缺陷。
常用于金属结构的缺陷检测和磁性材料的质量控制。
4. 无损检测的应用无损检测在许多行业中都有重要应用,以下是一些常见的应用领域:•航空航天:无损检测在航空航天工业中的应用广泛。
它可以用来检测飞机结构的疲劳破坏、缺陷和裂纹,确保飞机的安全运行。
•核能:在核能行业中,无损检测用于检测核反应堆和燃料元件中的缺陷和裂纹,以确保核设施的运行安全性。
•制造业:无损检测在制造业中用于产品质量的控制。
无损检测技术简介及基本原理
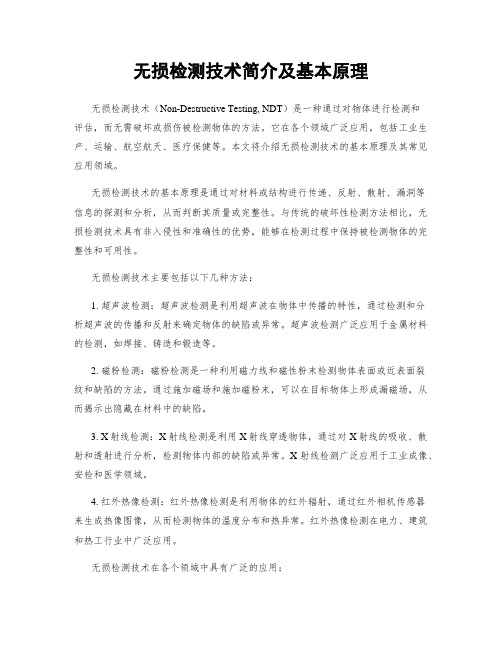
无损检测技术简介及基本原理无损检测技术(Non-Destructive Testing, NDT)是一种通过对物体进行检测和评估,而无需破坏或损伤被检测物体的方法。
它在各个领域广泛应用,包括工业生产、运输、航空航天、医疗保健等。
本文将介绍无损检测技术的基本原理及其常见应用领域。
无损检测技术的基本原理是通过对材料或结构进行传递、反射、散射、漏洞等信息的探测和分析,从而判断其质量或完整性。
与传统的破坏性检测方法相比,无损检测技术具有非入侵性和准确性的优势,能够在检测过程中保持被检测物体的完整性和可用性。
无损检测技术主要包括以下几种方法:1. 超声波检测:超声波检测是利用超声波在物体中传播的特性,通过检测和分析超声波的传播和反射来确定物体的缺陷或异常。
超声波检测广泛应用于金属材料的检测,如焊接、铸造和锻造等。
2. 磁粉检测:磁粉检测是一种利用磁力线和磁性粉末检测物体表面或近表面裂纹和缺陷的方法。
通过施加磁场和施加磁粉末,可以在目标物体上形成漏磁场,从而揭示出隐藏在材料中的缺陷。
3. X射线检测:X射线检测是利用X射线穿透物体,通过对X射线的吸收、散射和透射进行分析,检测物体内部的缺陷或异常。
X射线检测广泛应用于工业成像、安检和医学领域。
4. 红外热像检测:红外热像检测是利用物体的红外辐射,通过红外相机传感器来生成热像图像,从而检测物体的温度分布和热异常。
红外热像检测在电力、建筑和热工行业中广泛应用。
无损检测技术在各个领域中具有广泛的应用:1. 工业制造:无损检测技术可以用于检测和评估工业制造中的材料和构件的质量,如焊接接头的检测、铸造件的质量控制等。
2. 航空航天:无损检测技术在航空航天领域中发挥着关键作用,可以用于飞机的结构材料检测、发动机的检测和维修等。
3. 汽车工业:无损检测技术可以用于汽车零部件的检测和评估,如发动机的缺陷检测、车轮的裂纹检测等。
4. 医疗保健:无损检测技术在医疗保健领域中被广泛应用于医学成像,如X射线检测、超声波检测等。
无损检测技术的原理及其应用
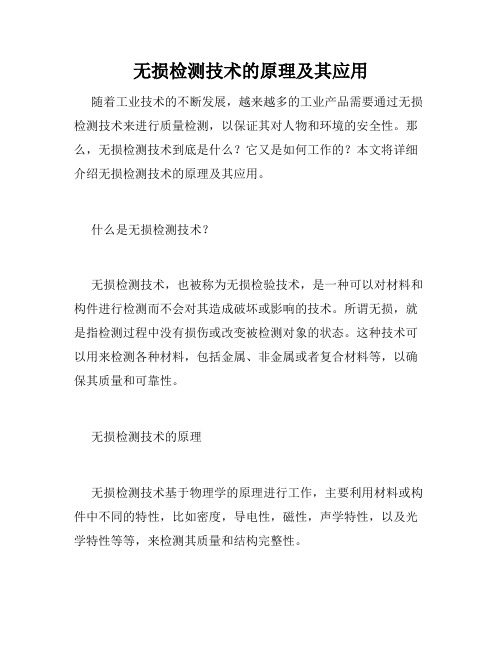
无损检测技术的原理及其应用随着工业技术的不断发展,越来越多的工业产品需要通过无损检测技术来进行质量检测,以保证其对人物和环境的安全性。
那么,无损检测技术到底是什么?它又是如何工作的?本文将详细介绍无损检测技术的原理及其应用。
什么是无损检测技术?无损检测技术,也被称为无损检验技术,是一种可以对材料和构件进行检测而不会对其造成破坏或影响的技术。
所谓无损,就是指检测过程中没有损伤或改变被检测对象的状态。
这种技术可以用来检测各种材料,包括金属、非金属或者复合材料等,以确保其质量和可靠性。
无损检测技术的原理无损检测技术基于物理学的原理进行工作,主要利用材料或构件中不同的特性,比如密度,导电性,磁性,声学特性,以及光学特性等等,来检测其质量和结构完整性。
1. 金属材料检测金属材料的无损检测主要基于材料中的电磁特性,例如电磁感应、电阻、涡流、磁粉等现象。
其中涡流检测技术通过引入一个交变电场,生成涡流,依据涡流作用于金属中导致感应电磁场变化的原理,对金属材料进行质量检测。
2. 焊缝检测焊接工艺是工业生产中常用的加工方式,无损检测技术也可以用于焊接接头的质量检测。
通常采用超声波检测和光电检测方式。
而超声波检测主要是通过投射高频声波到焊接接头上,利用声波在介质中的不同传播速度,得出焊缝中的缺陷信息。
3. 液面深度检测液体的无损检测技术主要应用于液体流量、液位及液体质量的检测。
其中液位检测是指通过检测液体表面与液体表面间的声速差,或检测表面反射波的时间差来实现工作的。
应用领域无损检测技术的应用范围广泛,包括石油工业、航空航天工业、汽车工业、船舶工业、建筑工业等领域。
下面,我们将详细介绍其中一些应用领域。
1. 石油工业在石油工业中,无损检测技术主要应用于管道和储罐的检测。
其主要目的是检测管道或储罐是否出现渗漏、裂纹、腐蚀等问题,以确保其安全运行。
常见的无损检测技术包括超声波检测、电磁检测、涡流检测等。
2. 航空航天工业在航空航天工业中,无损检测技术主要用于飞机结构和发动机部件的质量检测。
无损检测技术的基本原理

无损检测技术的基本原理无损检测技术是一种用于检测材料和构件内部缺陷的方法,它通过不损伤被检测材料的表面和体积,获取关于材料内部结构和缺陷的信息。
无损检测技术广泛应用于航空航天、汽车制造、石油化工、核电站等领域。
无损检测技术的基本原理是利用物体对辐射的吸收、散射、透射等特性,对物体进行观察和分析。
主要包括以下几个方面的原理。
1. X射线检测原理:X射线检测是使用具有相对较高能量的X射线通过材料,观察材料内部结构。
射线在不同材质上产生不同的吸收和散射效果,从而检测出材料的缺陷或内部结构。
2. 超声波检测原理:超声波检测利用声波在物体中的传播方式,探测材料内部缺陷。
声波在不同材料中传播的速度和吸收程度不同,通过测量声波的传播时间和强度变化,可以检测出材料的缺陷。
3. 磁粉检测原理:磁粉检测是利用物体表面的磁场分布来检测材料表面和近表面的缺陷。
在施加磁场后,存在缺陷的材料表面会出现磁场的扭曲和泄漏,通过观察磁粉在缺陷处的沉积情况,可以发现缺陷的位置和大小。
4. 涡流检测原理:涡流检测利用交变电流在导体材料中产生的涡流效应,检测材料表面的缺陷。
在材料表面存在缺陷时,交变电流会在缺陷处产生涡流,进而改变电流的传播路径和阻抗,通过测量电流的变化,可以检测出材料的缺陷。
无损检测技术的基本原理是利用不同的物理原理来检测材料和构件的缺陷,其中的关键在于观察和分析物体对辐射的吸收、散射、透射等特性。
这些技术的应用范围非常广泛,可以检测出不同材料和缺陷的特点,从而评估物体的可靠性和安全性。
无损检测技术的优点在于可以在不破坏材料的情况下检测出缺陷,提高了材料和构件的使用寿命和安全性。
同时,无损检测技术还可以对材料进行定量分析和可视化显示,提供更多的信息来支持工程师的决策。
然而,无损检测技术也存在一些局限性。
不同的技术适用于不同类型的材料和缺陷,无法适用于所有情况。
此外,一些无损检测技术需要特殊设备和专家的操作,成本较高,难以在现场进行大规模应用。
无损检测技术的基本原理和方法

无损检测技术的基本原理和方法无损检测技术是一种非侵入性测试方法,可以帮助人们检测材料和结构内部的缺陷或损伤,而无需破坏材料本身。
这种技术在许多领域中得到广泛应用,包括航空航天、能源、制造业等。
本文将介绍无损检测技术的基本原理和常用方法。
无损检测技术的基本原理是基于材料对电磁、声波或辐射的相互作用,通过分析相应的信号来判断材料的质量和完整性。
根据不同的物理原理,无损检测技术可以分为几种不同的方法。
首先,电磁无损检测是利用电磁波与材料相互作用的原理,在材料中产生反射或透射的信号,从而检测材料的缺陷。
电磁无损检测方法包括磁性粉检测、涡流检测和磁通检测。
磁性粉检测利用材料表面的磁场分布来检测表面和近表面的缺陷,常用于金属材料的检测。
涡流检测则通过在导体中产生涡流,并检测反射的电磁信号来判断材料的质量。
磁通检测是利用磁场分布的变化来检测材料内部的缺陷。
其次,声波无损检测是利用声波在材料中传播的特性来检测缺陷。
常用的声波无损检测方法包括超声波检测和声发射检测。
超声波检测利用材料中的声波传播速度和反射信号来检测材料的内部缺陷。
声发射检测则是通过监测材料中发生的微小声波信号来判断材料是否存在缺陷或损伤。
另外,辐射无损检测是利用辐射材料的特性来检测缺陷。
常用的辐射无损检测方法包括X射线检测和γ射线检测。
X射线检测通过向材料中发射X射线,并通过接收反射或透射的X射线信号来检测材料的缺陷。
γ射线检测则是利用γ射线与材料相互作用的原理来检测缺陷。
此外,还有一些其他的无损检测方法,如热红外检测和激光检测。
热红外检测利用红外辐射来检测材料中的热量分布和热传导性能,从而判断材料是否存在缺陷。
激光检测则是利用激光的特性来检测材料的缺陷。
无损检测技术的应用非常广泛,包括材料制造、航空航天、核能工业和地震监测等领域。
在材料制造过程中,无损检测可以帮助检测材料的质量,防止次品产品的出现。
在航空航天领域,无损检测可以检测飞机的结构完整性,确保飞行安全。
无损检测 原理
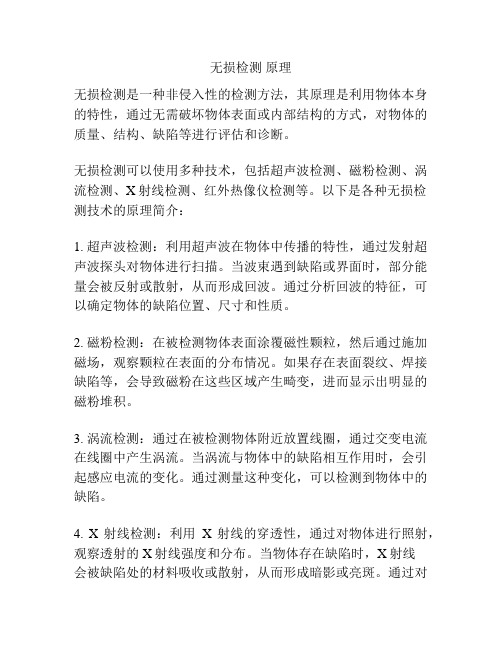
无损检测原理无损检测是一种非侵入性的检测方法,其原理是利用物体本身的特性,通过无需破坏物体表面或内部结构的方式,对物体的质量、结构、缺陷等进行评估和诊断。
无损检测可以使用多种技术,包括超声波检测、磁粉检测、涡流检测、X射线检测、红外热像仪检测等。
以下是各种无损检测技术的原理简介:1. 超声波检测:利用超声波在物体中传播的特性,通过发射超声波探头对物体进行扫描。
当波束遇到缺陷或界面时,部分能量会被反射或散射,从而形成回波。
通过分析回波的特征,可以确定物体的缺陷位置、尺寸和性质。
2. 磁粉检测:在被检测物体表面涂覆磁性颗粒,然后通过施加磁场,观察颗粒在表面的分布情况。
如果存在表面裂纹、焊接缺陷等,会导致磁粉在这些区域产生畸变,进而显示出明显的磁粉堆积。
3. 涡流检测:通过在被检测物体附近放置线圈,通过交变电流在线圈中产生涡流。
当涡流与物体中的缺陷相互作用时,会引起感应电流的变化。
通过测量这种变化,可以检测到物体中的缺陷。
4. X射线检测:利用X射线的穿透性,通过对物体进行照射,观察透射的X射线强度和分布。
当物体存在缺陷时,X射线会被缺陷处的材料吸收或散射,从而形成暗影或亮斑。
通过对这些暗影或亮斑进行分析,可以确定物体的缺陷情况。
5. 红外热像仪检测:利用物体辐射的红外热量,通过红外热像仪对其进行热成像。
物体表面温度的变化与其内部结构和缺陷之间存在一定的关系。
通过分析热图,可以确定物体的热分布,进而推断出可能存在的结构或缺陷。
综上所述,无损检测通过利用物体本身的特性,结合不同的检测技术,可以对物体进行全面、高效的质量和结构评估,为工程和生产领域提供了重要的技术手段。
- 1、下载文档前请自行甄别文档内容的完整性,平台不提供额外的编辑、内容补充、找答案等附加服务。
- 2、"仅部分预览"的文档,不可在线预览部分如存在完整性等问题,可反馈申请退款(可完整预览的文档不适用该条件!)。
- 3、如文档侵犯您的权益,请联系客服反馈,我们会尽快为您处理(人工客服工作时间:9:00-18:30)。
第1章无损检测技术1.1无损检测技术概述无损检测NDT (Non-destructive testing),就是利用声、光、磁和电等特性,在不损害或不影响被检对象使用性能的前提下,检测被检对象中是否存在缺陷或不均匀性,给出缺陷的大小、位置、性质和数量的所有技术手段的总称。
NDT 是指对材料或工件实施一种不损害等信息,进而判定被检对象所处技术状态,如合格与否、剩余寿命等或不影响其未来使用性能或用途的检测手段。
通过使用NDT,能发现材料或工件内部和表面所存在的缺欠,能测量工件的几何特征和尺寸,能测定材料或工件的内部组成、结构、物理性能和状态等。
如无损检测方法分类常规无损检测方法有超声检测Ultrasonic Testing,射线检测Radiographic Testing,磁粉检测Magnetic particle Testing,渗透检验Penetrant Testing ,涡流检测Eddy current Testing。
非常规无损检测技术有声发射Acoustic Emission,泄漏检测Leak Testing,光全息照相Optical Holography,红外热成象,微波检测Microwave Testing。
1.2无损检测的发展(1)由定性检测逐步向定量检测与评价过渡和发展用断裂力学等原理来确定极限寿命设计思想的出现,导致美国等一些发达国家在近年来较大幅度地增加无损检测与评价技术的研究经费,以开展缺陷的定量测定。
由原来的探伤技术发展成测伤技术。
检测时不仅要求探测出缺陷的有无及位置,而且还要测定出缺陷的类型、尺寸、形状和取向。
(2)发展新材料和新的无损检测与评定方法和技术随着材料科学和工程技术的发展,不断涌现出一些新材料和异型结构件。
对它们的无损检测与评价,用原有的技术和方法常常难以进行或达不到要求。
(3)发展自动化无损检测与评价系统自动化无损检测技术比非自动化无损检测能提供更好的重复性、结果一致性和检测的可靠性,降低了对操作人员操作技术高度熟练的要求,减少人为误差的几率。
值得指出的是,由于判断的复杂性,无损检测与评价的自动化,在目前并没有达到完全可以取代人工操作的地步,实现完全自动化还是人们长远的奋斗目标。
第2章无损检测分类2.1超声波检测介绍超声波是频率大于20 kHz 的一种机械波(相对于频率范围在20 Hz ~20 kHz 的声波而言)。
超声检测用的超声波,其频率范围一般在0.25 MHz ~15 MHz 之间。
用于金属材料超声检测的超声波,其频率范围通常在0.5 MHz ~10 MHz 之间,而用于普通钢铁材料超声检测的超声波,其频率范围通常为 1 MHz ~5 MHz。
超声波具有众多与众不同的特性,如声束指向性好(能量集中),声压声强大(能量高),传播距离远;穿透能力强,在界面处会产生反射、透射(或折射)和波型转换,以及产生衍射等。
超声波在被检材料(金属、非金属)中传播时,利用材料本身或内部缺陷所示的声学性质对超声波传播的影响来检测材料的组织和内部缺陷的方法,称为超声探伤。
它是一种非破坏性的材料实验方法,即不需破坏被检材料或工件就能探测其内部各种缺陷(如裂纹、气泡、夹杂物等)的大小,形状和分布状况以及测定材料性质。
超声探伤具有灵敏度高、快速方便、易实现自动化等优点,因此广泛应用于机器制造、冶金、化工设备、国防建设等部门,已成为保证产品质量,确保安全的一种重要手段。
2.1.1超声探伤按其方法和目的分类(1)脉冲反射法把超声脉冲发射到物体中再接收来自物体中的反射波,这种探伤方法称为脉冲反射法。
它是超声探伤中最基本的方法。
在脉冲反射法中,根据声束传播情况可分为直探法和斜探法;根据探伤所用波形可分为纵波探伤法、横波探伤法、表面波探伤法和板波探伤法;根据探头个数和作用可分为单探头法和双探头法;根据声耦合方式可分为直接接触法和水浸法等等。
由于这些方法具有各自的特点,所以广泛用来对金属和非金属材料及其制品进行无损检验。
(2)穿透法利用穿过被检物体的超声波的穿透率和有无声影进行探伤检验的方法称为穿透法。
穿透法有连续波穿透法,脉冲穿透法和共振穿透法等。
此方法的优点是适用于薄工件;由于超声波传播路程仅为反射法的一半,故适用于检查衰减大的材料;探伤图形直观,只要定好检查标准就可以进行作业;易实现自动探伤、检查速度快。
缺点是不能知道缺陷的深度位置;缺陷探测灵敏度一般比反射法低,难以检查较小缺陷。
(3)共振法把频率连续改变的超声波射入被检材料,根据材料的共振状况测量其厚度或检查有无缺陷等材料性质的方法称为共振法。
共振法一般用来测量金属板、管壁、容器壁的厚度或腐蚀程度,测量声速,检查板中的分层和进行材质判定。
(4)声阻法声阻法是利用被测物件的振动特性,即被测物对探头所呈现的机械阻抗的变化来进行检测的一种无损检测法。
它多用于检测物体表面的成层情况,例如用来检查基体材料上附粘的膜片是否粘接上等。
它的工作频率范围一般都较低(如几千赫兹)。
用这种方法工作时,把探头和被测件直接接触,使被测件和探头结合在一起构成一个共振体,探头一方面是振动源,同时也是检测部件,当被测件的有效厚度不同时(例如,若膜片未粘上,则有效厚度仅为膜片的厚度,若已完好的粘接上,则有效厚度包括膜片和基体材料的厚度),该共振体频率特性就不同,从而可根据其频率特性来判定膜片在某个小区域的粘接情况。
2.1.2超声波工作的原理(1)声源产生超声波,采用一定的方式使超声波进入试件;(2)超声波在试件中传播并与试件材料以及其中的缺陷相互作用,使其传播方向或特征被改变;(3)改变后的超声波通过检测设备被接收,并可对其进行处理和分析;(4)根据接收的超声波的特征,评估试件本身及其内部是否存在缺陷及缺陷的特性。
2.1.3超声波检测优缺点(1)超声波检测优点a.适用于金属、非金属和复合材料等多种制件的无损检测;b.穿透能力强,可对较大厚度范围内的试件内部缺陷进行检测。
如对金属材料,可检测厚度为1~2mm的薄壁管材和板材,也可检测几米长的钢锻件;c.缺陷定位较准确;d.对面积型缺陷的检出率较高;e.灵敏度高,可检测试件内部尺寸很小的缺陷;f.检测成本低、速度快,设备轻便,对人体及环境无害,现场使用较方便。
(2)超声波检测局限性a.对试件中的缺陷进行精确的定性、定量仍须作深入研究;b.对具有复杂形状或不规则外形的试件进行超声检测有困难;c.缺陷的位置、取向和形状对检测结果有一定影响;d.材质、晶粒度等对检测有较大影响;e.以常用的手工A型脉冲反射法检测时结果显示不直观,且检测结果无直接见证记录。
(3)超声波检测使用范围a.从检测对象的材料来说,可用于金属、非金属和复合材料;b.从检测对象的制造工艺来说,可用于锻件、铸件、焊接件、胶结件等;c.从检测对象的形状来说,可用于板材、棒材、管材等;d.从检测对象的尺寸来说,厚度可小至1mm,也可大至几米;e.从缺陷部位来说,既可以是表面缺陷,也可以是内部缺陷。
2.2磁粉检测(MT)2.2.1磁粉检测定义利用漏磁和合适的检验介质发现试件表面和近表面的不连续性的无损检测方法,称之为磁粉检测。
铁磁性材料和工件被磁化后,由于不连续性的存在,使工件表面和近表面的磁力线发生局部畸变而产生漏磁场,吸附施加在工件表面的磁粉,形成在合适光照下目视可见的磁痕,从而显示出不连续性的位置、形状和大小。
2.2.2磁粉检测适用性和局限性磁粉探伤适用于检测铁磁性材料表面和近表面尺寸很小、间隙极窄,目视难以看出的不连续性。
磁粉检测可对原材料、半成品、成品工件和在役的零部件检测,还可对板材、型材、管材、棒材、焊接件、铸钢件及锻钢件进行检测。
可发现裂纹、夹杂、发纹、白点、折叠、冷隔和疏松等缺陷。
磁粉检测不能检测奥氏体不锈钢材料和用奥氏体不锈钢焊条焊接的焊缝,也不能检测铜、铝、镁、钛等非磁性材料。
对于表面浅的划伤、埋藏较深的孔洞和与工件表面夹角小于20°的分层和折叠难以发现。
2.3渗透检测(PT)2.3.1液体渗透检测的定义及基本原理利用液体的毛细管作用,将渗透液渗入固体材料表面开口缺陷处。
再通过显象剂将渗入的渗透液吸出到表面显示缺陷的存在。
这种无损检测方法称为渗透检测。
液体渗透检测的基本原理是零件表面被施涂含有荧光染料或着色染料的渗透剂后,在毛细管作用下,经过一段时间,渗透液可以渗透进表面开口缺陷中;经去除零件表面多余的渗透液后,再在零件表面施涂显像剂,同样,在毛细管的作用下,显像剂将吸引缺陷中保留的渗透液,渗透液回渗到显像剂中,在一定的光源下,缺陷处的渗透液痕迹被显示,从而探测出缺陷的形貌及分布状态。
2.3.2渗透检测(PT)优缺点(1)渗透检测优点a.可检测各种材料;金属、非金属材料;磁性、非磁性材料;焊接、锻造、轧制等加工方式;b.具有较高的灵敏度(可发现0.1μm宽缺陷);c.显示直观、操作方便、检测费用低。
(2)渗透检测缺点及局限性a.它只能检出表面开口的缺陷;b.不适于检查多孔性疏松材料制成的工件和表面粗糙的工件;c.渗透检测只能检出缺陷的表面分布,难以确定缺陷的实际深度,因而很难对缺陷做出定量评价。
检出结果受操作者的影响也较大。
2.4涡流检测涡流检测(ET):涡流检测的英文名称是:Eddy Current Testing,工业上无损检测的方法之一。
给一个线圈通入交流电,在一定条件下通过的电流是不变的。
如果把线圈靠近被测工件,像船在水中那样,工件内会感应出涡流,受涡流影响,线圈电流会发生变化。
由于涡流的大小随工件内有没有缺陷而不同,所以线圈电流变化的大小能反映有无缺陷。
涡流检测是建立在电磁感应原理基础之上的一种无损检测方法.它适用于导电材料.如果我们把一块导体置于交变磁场之中,在导体中就有感应电流存在,即产生涡流.由于导体自身各种因素(如电导率,磁导率,形状,尺寸和缺陷等)的变化,会导致感应电流的变化,利用这种现象而判知导体性质,状态的检测方法叫做涡流检测方法.2.5射线照相法2.5.1射线照相法概述射线照相法是指用X射线或γ射线来检测材料和工件,并以射线照相胶片作为记录介质和显示方法的一种无损检测方法。
该方法是最基本的,应用最广泛的一种非破坏性检验方法。
通过观察记录(感光)在射线照相胶片(底片)上的有关X射线或伽玛射线在被检材料或工件中发生的衰减变化,来判定被检材料和工件的内部是否存在缺陷,从而在不破坏或不损害被检材料和工件的情况下,评估其质量和使用价值。
X射线是电磁波。
X射线具有众多与众不同的特性,如:折射系数接近于1,几乎无折射;穿透能力强;仅在晶体光栅中才产生干涉和衍射现象;与某些物质会发生电离作用、荧光作用、热作用和光化学作用;较易衰减,并对不同物质和密度,衰减系数明显不同;易杀伤生物细胞,破坏生物组织等。