统计过程控制(spc)案例分析(-03-24).电子教案
统计过程控制(SPC)

11
控制图的选择
控制图的选定
计量值 数据性质
计数值
平均值
“n”=10~25 “n”是否较大
n≧1 样本大小 n≧2
Cl的性质
中位数 “n”=2~5
“n”=1
不良数
缺陷数
不良数或
缺陷数
不一定
一定
“n”是否一定
单位大小 是否一定 不一定 一定
X-s 图
X-R 图
X-R
X-Rm “p”
图
图图
“np” “c”
数据类别: 计数值数据:只以缺陷数和个数表示,不能连续取值的数据 计量值数据:以产品本身的特性来表示,可以连续取值的数据
2
两种变异
普通性(特定性)变异:不易避免的原因(普通 原因)造成的变异,如操作人员的熟练程度的 差异、设备精度与保养好坏的差异、同批原材 料本身的差异
特殊性(偶尔性)变异:可以避免也必须避免 的原因(特殊原因)造成的变异,如不同原材料 之间的差异、设备故障
“u”
图图
图
12
案例1(控制图的选择)
质量特性 长度 重量 乙醇比重 电灯亮/不亮 每一百平方米的 脏点
样本数 5 10 1
100 100平方米
选用什么图
13
答案1
质量特性 长度 重量 乙醇比重 电灯亮/不亮 每一百平方米的 脏点
样本数 5 10 1
100 100平方米
选用控制图 均值极差控制图
通常用来消除变差的普通原因 几乎总是要求管理措施,以便纠正 大约可纠正85%的过程问题
8
控制图的目的
控制图和一般的统计图不同,因其不仅能 将数值以曲线表示出来,以观其变异之趋 势,且能显示变异系属于机遇性或非机遇 性,以指示某种现象是否正常,而采取适 当之措施。
统计过程控制(SPC)

第一节 统计过程控制概述
一、过程控制的基本概念
为实现产品生产过程质量而进行的有组 织、有系统的过程管理活动
主要内容
(1)对过程进行分析并建立控制标准 (2)对过程进行监控和评价 (3)对过程进行维护和改进
二、统计过程控制 应用统计技术对过程中的各个阶段进行评 估和监控,建立并保持过程处于可接受的 并且稳定的水平,从而保证产品与服务符 合规定的要求的一种质量管理技术。 内容 (1)利用控制图分析过程的稳定性,对 过程存在的异常原因进行预警; (2)计算过程能力指数分析稳定的过程 能力满足技术要求的程度,对过程质量进行 评价。-可接受性
2 K T/ 2 T
(0<K<1)
K: μ对M的偏移度,ε=|M-μ|
T 则:C pK 1 K C p 1 K 6
其中:ε——μ与公差中心M偏移量 T——公差带宽 T=TU—TL
(四)Cp和Cpk的比较与说明 Cp—— 反映过程加工的一致性,即 “质量能力”
或
1 5 n P P
P0 :给定标准值 P :未给定标准值 2. 计算样本不合格品率
3. 算P图的控制限
P 1 P UCLP P 3 n
CLP P
P1 P LCLP P 3 n
4. 样本不合格品率描点 5. 判稳/判异
6. 关于样本量ni的说明 ( 1 )若样本量 n 大小相等,则 P 图控制限为两条直线。 ( 2 )若样本量 ni 不全相等,则 P 图 控制限呈凹凸状。
分析过程若失控或异常,找出原因, 进行纠正,防止再发生。
7. 计算 X 图控制限并作图,判断状态。
8. 计算过程能力指数验证是否符合要求 9. 延长控制限,作控制用控制图,进行日 常管理
SPC统计过程控制培训讲义课件

上、下 控制线
样本数据点 目标值 样本平均值
上、下 规格线
数据点超出上下控制线
连续7个或以上数据在中心线上方或下方
数据呈固样品点的水平突变
样品点分布的水平位置渐变
样品点的离散度较大
制程失控
制程失去控制时的特征: 1.数据点超出上下控制线 2.连续7个或以上数据在中心线上方或下方 3.数据呈固定形式变化 4.较多数据点接近上下控制线 5.样品点的水平突变 6.样品点分布的水平位置渐变 7.样品点的离散度较大
Moving Range Chart 二. 移动偏差图
Line 1 Cp = 1.65 Mean=12.55
Qoo PET Cpk = 1.1
SD =0.03
35 100.0% 1500 SPC Brix Monitoring
Sample wthin spec 100.0 %
上控线(UCTLR)UE
(n-1)
标准偏差σ是衡量样本数据点与平均值间偏差平均
值的典型参数,广泛使用于数据统计中。
Cp-潜在过程能力指数
cp=
spe_max-spe_min 6
( -样本的标准偏差)
Cp不反映过程的集中性 (即与目标的偏离),因 此如果过程的平均值并不是我们的期望的目标值, 那么用Cp来衡量过程就会产生误差。
4.0 4.125
(下控线= 目标值 - 3×能力测试所得标准偏差)
样本标准偏差σ的计算
假设有以下一些数据:12.50,12.45,12.49,12.48,12.51…
X1
x2
x3
x4 x5 … xn
首先计算出它们的 平均值 x= X1 + x2+ x3+ x4+ x5 + … + xn
SPC统计过程控制电子教案

1.定义 设随机变量 X 的可能取值是一切非负整数,而概率函数是
p(x)xe,
x!
x0,1,2,
其中常数 >0,
泊松分布含有一个参数 , 通常记作 P () .
如果 X服从泊松分布 P (), 则记为 X~ P().
泊松分布的均值与方差相等,均入
泊松分布
在大量试验中,小概率事件发生的次数可以近似地看作服从
Probability of sample value
40%
30%
99.73%
20%
95.45%
10%
68.27%
0% -4 -3 -2 -1 0 1 2 3 4 195 210 225 240 255 270 285 Time (minutes)
Z XX S
Z-axis X-axis
正态分布的应用2
计量数据的基本统计—数据分布
对一个相同的输出变量Y,多个数据点绘图,它们形成了一个分布。 这些数据点的堆积可以不同的图形来代表:
▪ 散点图/概率图 ▪ 值数法 - 均等反映了所有数据的影响 - 会受极端值强烈影响
中位数 ▪ 反映50%的那个位置 ▪ 对一组排序数据点的中心数 ▪ 对极端值较”坚耐”
10%
68.27% 0%
-4
-3
-2
-1
0
1
2
3
4
Z-axis (scale in units of ‘s’)
Number of standard deviations from the mean
正态分布的应用
如果我们货物交付给顾客的平均时间是240分钟,这一过程的标准偏差是15分 钟,那么在270分钟后到货的概率为多少?
统计过程控制(SPC)-培训教材

02
拉图(决定控制重点)
03
计检定
04
制图
05
样计划
06
异数分析/回归分析
过程控制系统
设备 材料 环境 成品
人员
绩效报告
过程中对策
过程中对策
方法
成品改善
过程控制系统 1. 过程: 过程是指人员、设备、材料、方法及环境的输入,经由一 定的整理程序而得到输出的结果,一般称之成品。成品经 观察、测量或测试可衡量其绩效。SPC所控制的过程必须符 合连续性原则。 2. 绩效报告: 从衡量成品得到有关过程绩效的资料,由此提供过程的控 制对策或改善成品。 3. 过程中对策: 是防患于未然的一种措施,用以预防制造出不合规格的成品。 4. 成品改善: 对已经制造出来的不良品加以选别,进行全数检查并返工/ 返修或报废。
控制图(平均值与全距) 1.公式: (1) 控制图 CL = UCL = + A2 LCL = - A2 (2) R 控制图 CL = UCL = D4 LCL = D3 2.实例: 某工厂制造一批紫铜管,应用 -R控制图来控制其内径,尺寸 单位为m/m,利用下页数据表之资料,求得其控制界限并绘图。 (n = 5)
R
X1
X2
X3
X4
X5
X1
X2
X3
X4
X5
1
50
50
49
52
51
50.4
3
14
53
48
47
52
51
50.2
6
2
47
53
53
45
50
49.6
8
15
53
48
49
51
统计过程控制(SPC)-实例讲解

不良率控制图(np)、不良数控制图 (p)、缺点数控制图(c)、单位缺点
数控制图(u)
分析用控制图
根据样本数据计算出控制图的中心线和上、下控制界限,画 出控制图,以便分析和判断过程是否处于于稳定状态。如果 分析结果显示过程有异常波动,应找出原因并采取措施,然 后重新抽取样本、测定数据、计算控制图界限进行分析。
控制图制作及应用 控制图制作实例(X-R)
A1选择子组大小、频率和数据
A
阶 段
A2计算每个子组的均值X和极差R
-
收 集 A3选择控制图的刻度 数 据
A4将均值和极差画到控制图上
第23页,共50页
临港整车厂
控制图制作及应用
控制图制作详解(X-R)
A1:选择子组大小、频率和数据
1.每组样本数(子组大小):2-5; 2.子组数要求:最少25组,共100个以上样本;频率可参考下表。
B2:计算控制限
平均值控制图:
CLX =X UCLX=X+A2R LCLX=X-A2R
极差控制图:
CLR=R UCLR=D4R LCLR=D3R
第28页,共50页
注:D4、D3、A2为常数,随样本容量n的不同而不同,可查《SPC控制图常数表》。
临港整车厂
控制图制作及应用 控制图制作详解(X-R)
B3:在控制图上画出平均值和极差控制限: 1.将平均极差(R)和过程均值(X)画成黑色水平实线,各控制限 (UCLR、LCLR、UCLX、LCLX)画成红色水平虚线; 2.在初始研究阶段,这些控制限被称为试验控制限。
98 97 98 99 99 98.2 2
临港整车厂
控制图制作及应用
控制图制作详解(X-R)
SPC案例分析
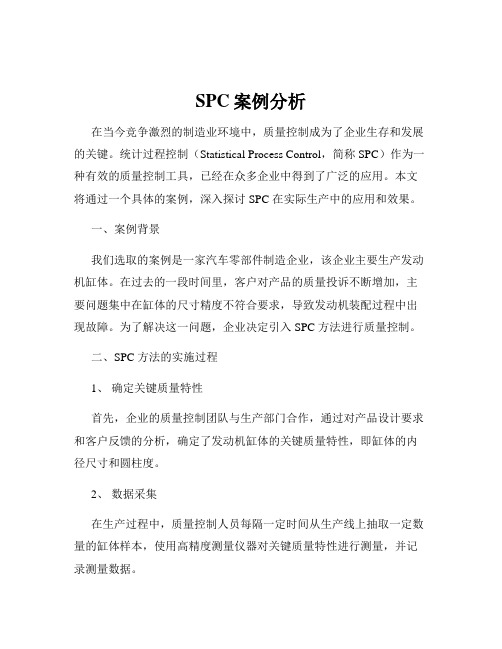
SPC案例分析在当今竞争激烈的制造业环境中,质量控制成为了企业生存和发展的关键。
统计过程控制(Statistical Process Control,简称 SPC)作为一种有效的质量控制工具,已经在众多企业中得到了广泛的应用。
本文将通过一个具体的案例,深入探讨 SPC 在实际生产中的应用和效果。
一、案例背景我们选取的案例是一家汽车零部件制造企业,该企业主要生产发动机缸体。
在过去的一段时间里,客户对产品的质量投诉不断增加,主要问题集中在缸体的尺寸精度不符合要求,导致发动机装配过程中出现故障。
为了解决这一问题,企业决定引入 SPC 方法进行质量控制。
二、SPC 方法的实施过程1、确定关键质量特性首先,企业的质量控制团队与生产部门合作,通过对产品设计要求和客户反馈的分析,确定了发动机缸体的关键质量特性,即缸体的内径尺寸和圆柱度。
2、数据采集在生产过程中,质量控制人员每隔一定时间从生产线上抽取一定数量的缸体样本,使用高精度测量仪器对关键质量特性进行测量,并记录测量数据。
3、控制图的绘制将采集到的数据输入到统计软件中,绘制均值极差控制图(XR 控制图)和均值标准差控制图(XS 控制图)。
控制图的横坐标表示样本序号,纵坐标表示测量值。
4、控制限的确定根据样本数据的分布特征和统计规律,计算出控制图的控制限。
控制限分为上控制限(UCL)、下控制限(LCL)和中心线(CL)。
中心线通常为样本数据的均值,上控制限和下控制限则根据一定的计算公式得出。
5、过程监控与分析定期对控制图进行观察和分析,判断生产过程是否处于受控状态。
如果数据点落在控制限内,且没有明显的趋势或异常模式,则认为过程处于受控状态;反之,如果数据点超出控制限,或者出现连续上升或下降的趋势,或者存在周期性的波动等异常模式,则认为过程失控,需要采取相应的措施进行改进。
三、案例结果与分析在实施 SPC 方法后的一段时间里,企业对生产过程进行了持续的监控和分析。
SPC案例分析
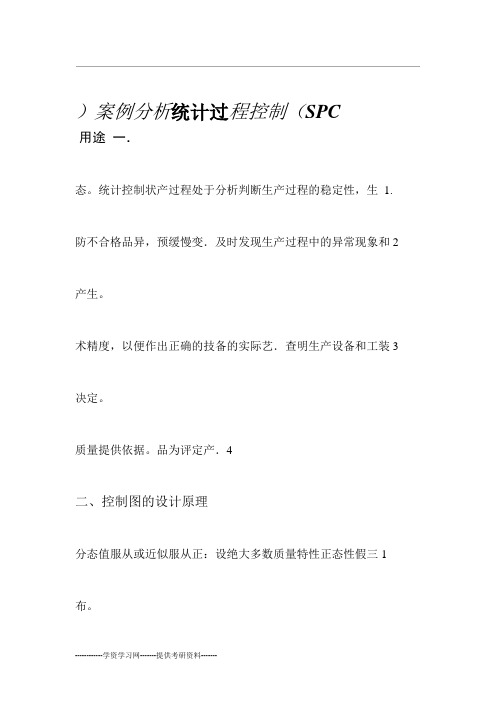
)案例分析统计过程控制(SPC用途一.态。
统计控制状产过程处于分析判断生产过程的稳定性,生1.防不合格品异,预缓慢变.及时发现生产过程中的异常现象和2产生。
术精度,以便作出正确的技备的实际艺.查明生产设备和工装3决定。
质量提供依据。
品为评定产.4二、控制图的设计原理分态值服从或近似服从正:设绝大多数质量特性正态性假三1布。
则:准73%9932三?发生的。
小概率事件原理:小概率事件一般是不会三3证法思想。
反三4控制图的种类四.~)量值(按产品质量的特性分()计11三SXRXRXRX ,,,????S。
图)(数值,,,()计up2cpn图。
)分析用控制图;()控制用控制按控制图的用途分:(212三控制图的判断规则五.:分析用控制图三1种情况);绝大多数点子在控制界限线内(准判规则稳则1-----3。
现象(规则种情况)排列无下述则判异准-----28-1--1-:图控制用控制三2每一个点子均落在控制界限内。
规则1现象。
控制界限内点子的排列无异常规则2量程产过质图元件的不合格率而为案例控制某无线电设计,生2][p 。
平均不合格率要求为≤2%-2--2-收集收据解:一.见程中收集数据准化的情况下从生产过在充分固定并标,,5M1E下表所表示:元件不合格品率数据表线电某无值平均711 1.4k本中不合格品率样计算二:.i列在上表?p.,k,i?1,2,.....,n i i 程平均不合格品率过三求:.?k i140%248/17775???p?n i-3--3-140%??p CL图线四计算控制:.p n/3p(1UCL?p??)p i n/p?3)p(1UCL??pi化而变时随的从上式可以看出当诸样本大小不相等,UCL,LCL, nn ii变化其图形为阶梯式的折线而非直线为了方便若有关系式:,,.n?2n max n?n/2min同时满足也即相差不大时可以令使得上下限仍为常数其图,,,,,nnn?ii形仍为直线.本例中诸样本大小满足上面条件故有控制线为:,,,n711n?i CL?p?140%图:p UCL?p?3p(1?p)/n?p?3p(1?p)/n?2.72%图五制作i UCL?p?3p(1?p)/n?p?3p(1?p)/n?0.08%i控制:.以样本序号为横坐标样本不合格品率为纵坐标做图.p,,六描点依据每个样本中的不合格品率在图上描点.:.七分析生产过程是否处于统计控制状态.从图上可以看到第个点超过控制界限上界出现异常现象这说,,14,明生产过程处于失控状态尽管但由于生产过程失控即,.=1.40%<2%,p -4--4-图化为控制用控制不合格品率波动大所以不能将此分析用控制图转,,正措施点失控的原因并制定纠应查明第.,14案例分析造成手表不用排列图量某手表厂为了提高手表的质应3][,用再次应摆占第一位为了解决停摆问题合格的各种原因发现停,---.,而发现主要是由于螺栓脱落造成的分析造成停摆的原因结果排列图,,中的螺装配作业厂方决定应用控制图对后者是有螺栓松动造成为此,.程控制行过栓扭矩进.又由于本例图选用正态分布控制分析螺栓扭矩是计量特征值故可,],[图用灵敏度高的难取得数据故决定选是大量生产不.,,R?x图按照下列步骤建立解][R x?下表见组预备根据合理分组原则取数据步骤一.25,,.X值为例如第一值组样本的平均计步骤二算各样本组的平均.,i X=(154+174+164+166+162)/5=164.01本的极差算各样步骤三计.20X}?174?154???R,Rmax{X}min{i1ii值计算样本总均骤步四.和平均样本极差RX?X?4081.8i?357?Ri所以,X?163.272R?14.280步骤五计算图与的参数.R X先计算图的参数(1)R样本容量时,D4=2.114,D3=0n=5-5--5-UCL?DR?2.114*14.280?30.1884R代入图公式CL?R?14.280R R LCL?DR?03R均值控制图极差控制图X R图计的原始数据与算表例.2备观察值样本X i注序号R∑XijXi5Xi4Xi3Xi2Xi110820164162166164174154.20-6--6-值图。
- 1、下载文档前请自行甄别文档内容的完整性,平台不提供额外的编辑、内容补充、找答案等附加服务。
- 2、"仅部分预览"的文档,不可在线预览部分如存在完整性等问题,可反馈申请退款(可完整预览的文档不适用该条件!)。
- 3、如文档侵犯您的权益,请联系客服反馈,我们会尽快为您处理(人工客服工作时间:9:00-18:30)。
【案例1】 R X -控制图示例某手表厂为了提高手表的质量,应用排列图分析造成手表不合格品的各种原因,发现“停摆”占第一位。
为了解决停摆问题,再次应用排列图分析造成停摆事实的原因,结果发现主要是由于螺栓松动引发的螺栓脱落成的。
为此厂方决定应用控制图对装配作业中的螺栓扭矩进行过程控制。
分解:螺栓扭矩是一计量特性值,故可选用基于正态分布的计量控制图。
又由于本例是大量生产,不难取得数据,故决定选用灵敏度高的R X -图。
解:我们按照下列步骤建立R X -图步骤1:取预备数据,然后将数据合理分成25个子组,参见表1。
步骤2:计算各组样本的平均数i X 。
例如,第一组样本的平均值为:0.16451621661641741541=++++=X其余参见表1中第(7)栏。
步骤3:计算各组样本的极差i R 。
例如,第一组样本的极差为:{}{}20154174min max 111=-=-=j j X X R其余参见表1中第(8)栏。
表1: 【案例1】的数据与R X -图计算表i故:272.163=X ,280.14=R 。
步骤5:计算R 图的参数。
先计算R 图的参数。
从D 3、D 4系数表可知,当子组大小n =5,D 4=2.114,D 3=0,代入R 图的公式,得到: 188.30280.14114.24=⨯==R D UCL R280.14==R CL R ==R D LCL R 3—极差控制图:均值控制图:图1 【案例1】 的第一次R X -图参见图1。
可见现在R 图判稳。
故接着再建立X 图。
由于n =5,从系数A 2表知A 2=0.577,再将272.163=X ,280.14=R 代入X 图的公式,得到X 图:512.171280.14577.0272.1632≈⨯+=+=R A X UCL X 272.163==X CL X032.155280.14577.0272.1632≈⨯-=-=R A X LCL X因为第13组X 值为155.00小于X LCL ,故过程的均值失控。
经调查其原因后,改进夹具,然后去掉第13组数据,再重新计算R 图与X 图的参数。
此时,125.14241835724≈-=='∑R R617.16324.1558.408124≈-=='∑XX代入R 图与X 图的公式,得到R 图:13579111315171921232530.18814.2800.000 135791113151719212325171.512 163.272155.032860.29125.14114.24≈⨯='=R D UCL R 125.14≈'=R CL R 03='=R D LCL R从表1可见,R 图中第17组R=30出界。
于是舍去该组数据,重新计算如下:435.13233033923≈-==''∑R R670.163234.1628.392623≈-==''∑XXR 图:402.28435.13114.24≈⨯=''=R D UCL R 435.13=''=R CL R =''=R D LCL R 3—从表1可见,R 图可判稳。
于是计算X 图上,见图2此时过程的变异度与均值均处于稳态。
步骤6:与规范进行比较对于给定的质量规范140=L T ,180=U T ,利用R 和X 计算P C 。
极差控制图:均值控制图:图2 【案例1】 的第二次R X -图776.5326.2435.132≈==d R ρ)σ15.1776.561401806≈⨯-=-=σ)L U P T T C 由于670.163=X 与容差中心M=160不重合,所以需要计算PK C 。
18.02/)140180(670.1631602/=--=-=T M K μ)94.015.1)18.01()1(=⨯-=-=P PK C K C可见,统计过程状态下的P C 为1.16>1,但是由于μˆ与M 偏离,所以1<PK C 。
因此,应根据对手表螺栓扭矩的质量要求,确定当前的统计过程状态是否满足设计的、工艺的和顾客的要求,决定是否以及何时对过程进行调整。
若需调整,那么调整数应重新收集为据,绘制R X -图。
步骤7:延长统计过程状态下的R X -图的控制限,进入控制用控制图阶段,实现对过程的日常控制。
1 35791113151719212328.40213.435 0.000 1 357911131517192123171.422163.670155.918X-图【案例2】sX-图。
为充分利用子组信息,对【案例1】选用s解:步骤如下:步骤1:依据合理分组原则,取得25组预备数据,参见表2。
表2:手表的螺栓扭矩步骤2:计算各子组的平均值i X 和标准差i s 。
各子组的平均值见表2(与表1相同),而标准差需要利用有关公式计算,例如,第一子组的标准差为:211.715)164162()164166()164164()164174()164154(15)(2222251111=--+-+-+-+-=--=∑=j jX Xs 其余参见表2中的标准差栏。
步骤3:计算所有观测值的总平均值X 和平均标准差s 。
得到256.163=X ,644.5=s 。
步骤4:计算s 图的控制限,绘制控制图。
先计算s 图的控制限。
从计量控制图系数表可知,当子组大小n =5时,089.24=B ,03=B ,代入s 图公式,得到:790.11644.5089.24=⨯==s B UCL s 644.5==s CL s ==s B LCL s 3—相应的s 控制图见图3。
标准差控制图: 13579111315171921232511.7905.644 0.000图3 表1中25个子组的标准差控制图可见,s 图在第17点超出了上控制限,应查找异常的原因,采取措施加以纠正。
为了简单起见,我们将第17子组剔除掉。
利用剩下的24个子组来重新计算s X -控制图的控制限。
得到:292.163=X ,370.5=s089.24=B ,03=B ,代入s 图的控制限公式,得到: 218.11370.5089.24=⨯==s B UCL s 370.5==s CL s ==s B LCL s 3—参见图4的标准差控制图。
可见,标准差s 控制图不存在变差可查明原因的八种模式,那么,可以利用s 来建立X 图。
由于子组大小n =5,从计量控制图系数表知,427.13=A ,将292.163=X ,370.5=s 代入X 图的控制限公式,得到:955.170370.5427.1292.1633≈⨯+=+=s A X UCL X292.163==X CL X629.155370.5427.1292.1633≈⨯-=-=s A X LCL X相应的均值控制图见图4。
标准差控制图:均值控制图:1 35791113151719212311.2185.370 0.000 170.955163.292155.629图4 剔除第17子组后得到的s X -控制图由图4的均值控制图可知,第13组X 值为155.00小于X LCL ,故过程的均值失控。
调查其原因发现是夹具松动造成的,已经很快进行了纠正,在采集第14个子组的数据时,该问题已获解决。
故可以去掉第13子组的数据,重新计算R 图与X 图的参数。
此时,617.163=X ,265.5=s 。
代入R 图与s 图的控制限公式,得到: s 图:999.10265.5089.24=⨯==s B UCL s 265.5==s CL s ==s B LCL s 3—参见图5的标准差控制图。
可见,标准差s 控制图不存在变差可查明原因的八种模式,那么,可以利用s 来建立X 图。
由于子组大小n =5,从计量控制图系数表知,427.13=A ,将617.163=X ,265.5=s 代入X 图的控制限公式,得到:131.171265.5427.1617.1633≈⨯+=+=s A X UCL X617.163==X CL X104.156265.5427.1617.1633≈⨯-=-=s A X LCL X参见图5的均值控制图。
标准差控制图均值控制图:图5 再去掉第13个子组后得到的s X -控制图1 35791113151719212310.9995.265 0.000 1 357911131517192123171.131163.617 156.104由图5的均值控制图可知,没有出现变差可查明原因的八种模式。
即标准差控制图和均值控制图都没有出现可查明原因的八种模式,说明装配作业中螺栓扭矩的生产过程处于统计控制状态。
步骤5:与容差限比较,计算过程能力指数。
已知手表螺栓扭矩的容差限为:140=L T ,180=U T 。
利用得到的统计控制状态下的617.163=X ,265.5=s 来计算过程能力指数:601.5940.0265.54===c s σ)19.1601.561401806=⨯-=-=σL U P T T C由于617.163=X 与容差中心1602/)(=+=L U T T M 不重合,所以,有必要计算有偏称的过程能力指数。
18.020617.32/)(617.1631602/==--=-=L U T T T M K μ) 9758.019.1)18.01()1(=⨯-=-=P PK C K C可见,统计控制状态下的过程能力指数为1.19,大于1,但是,由于存在分布中心与容差中心的偏移,故有偏移的过程能力指数不足1。
因此,应该根据对手表螺栓扭矩的质量要求,确定当前的统计控制状态是否满足设计的、工艺的、顾客的要求,决定是否以及何时对过程进行调整。
若需进行调整,那么调整后,应重新收集数据,绘制s X -控制图。
由于R X -控制图以平均极差R 为σ的估计值,s X -控制图以平均子组标准差s 为σ的估计值,所以,运用R X -控制图与运用s X -控制图分析同一个问题,得到的过程能力指数一般略有不同。
因为子组极差R 只利用了子组中的最大值和最小值的信息,而子组标准s 充分利用了子组中所有的信息,所以,当R X -控制图与s X -控制图的分析结果不同时,尽管R 图计算上比s 图简单,但仍建议以s X -控制图的结果为准。
步骤6:延长统计控制状态下的s X -控制图的控制限,进入控制用控制图阶段,实现对过程的日常控制。
【案例3】s R X -图表3给出了连续10批脱脂奶粉的样本“水分含量百分比”的实验室分析结果。
半一个样本的奶粉作为一批的代表,在实验室对其成分特性进行分析测试,如脂肪、水分、酸度、溶解指数、沉积物、细菌以及乳清蛋白。