SPC统计过程控制案例分析(doc 24页)
统计过程控制(SPC):提升制程稳定性

统计过程控制(SPC):提升制程稳定性在制造业中,制程稳定性是一个至关重要的概念。
不论是生产电子产品、制造机械零件还是生产食品,保持生产过程的稳定性对产品质量和成本控制都至关重要。
统计过程控制(SPC)是一种有效的方法,用来监控和改进生产过程,提升制程稳定性。
什么是统计过程控制(SPC)?统计过程控制(SPC)是一种基于统计方法的质量管理工具,旨在通过监控生产过程中的关键变量,减少变异性,实现生产过程的稳定性。
SPC可以帮助厂商识别并消除造成产品缺陷的根本原因,提高产品质量,降低生产成本,增强市场竞争力。
SPC的原理及应用SPC的基本原理是通过收集和分析生产过程中的数据来了解生产过程的特征和变异性,从而判断生产是否处于受控状态。
通过统计技术,可以找出生产过程中的特殊原因变异和普通原因变异,进而采取相应的控制措施。
SPC的应用范围非常广泛,可以适用于各个行业的生产过程控制。
比如,在汽车制造业,通过对关键工艺参数进行实时监控,可以避免生产出次品车辆;在食品加工业,利用SPC可以确保产品符合质量标准,保障食品安全。
SPC的主要工具和技术SPC主要包含以下几种工具和技术:1.控制图:控制图是SPC的核心工具之一,用来监控生产过程中的变异性。
常见的控制图有X-bar图、R图、P图等,通过控制图可以及时发现异常情况。
2.过程能力分析:通过过程能力分析,可以评估生产过程是否稳定,并确定是否满足产品质量标准。
3.假设检验:假设检验用于判断生产过程中的参数变化是否具有统计显著性,帮助厂商做出正确的决策。
SPC的好处采用统计过程控制(SPC)可以带来诸多好处:1.提升产品质量:SPC可以实时监控生产过程,及时发现问题并及时纠正,确保产品质量稳定。
2.降低生产成本:通过降低废品率和提高生产效率,可以有效降低生产成本。
3.增强市场竞争力:生产出质量稳定的产品,可以提高客户满意度,增强企业在市场上的竞争力。
总结统计过程控制(SPC)是一种重要的质量管理工具,能够帮助企业提升制程稳定性,实现持续改进。
统计过程控制(SPC)

11
控制图的选择
控制图的选定
计量值 数据性质
计数值
平均值
“n”=10~25 “n”是否较大
n≧1 样本大小 n≧2
Cl的性质
中位数 “n”=2~5
“n”=1
不良数
缺陷数
不良数或
缺陷数
不一定
一定
“n”是否一定
单位大小 是否一定 不一定 一定
X-s 图
X-R 图
X-R
X-Rm “p”
图
图图
“np” “c”
数据类别: 计数值数据:只以缺陷数和个数表示,不能连续取值的数据 计量值数据:以产品本身的特性来表示,可以连续取值的数据
2
两种变异
普通性(特定性)变异:不易避免的原因(普通 原因)造成的变异,如操作人员的熟练程度的 差异、设备精度与保养好坏的差异、同批原材 料本身的差异
特殊性(偶尔性)变异:可以避免也必须避免 的原因(特殊原因)造成的变异,如不同原材料 之间的差异、设备故障
“u”
图图
图
12
案例1(控制图的选择)
质量特性 长度 重量 乙醇比重 电灯亮/不亮 每一百平方米的 脏点
样本数 5 10 1
100 100平方米
选用什么图
13
答案1
质量特性 长度 重量 乙醇比重 电灯亮/不亮 每一百平方米的 脏点
样本数 5 10 1
100 100平方米
选用控制图 均值极差控制图
通常用来消除变差的普通原因 几乎总是要求管理措施,以便纠正 大约可纠正85%的过程问题
8
控制图的目的
控制图和一般的统计图不同,因其不仅能 将数值以曲线表示出来,以观其变异之趋 势,且能显示变异系属于机遇性或非机遇 性,以指示某种现象是否正常,而采取适 当之措施。
SPC统计过程控制手册(doc 133页)

SPC统计过程控制手册(doc 133页)统计过程控制SPC中国汽车公司技术研究中心译1997年6月第一次印刷2000年5月第二次©1992,©1995版权由克莱斯勒、福特和通用汽车公司所有本手册所描述控制图的选用程序目录第I章持续改进及统计过程的控制概述 .......第1节预防与检测5第2节 ................................................................. 过程控制系统 . (7)第3节 ................................................................. 变差:普通及特殊原因 (9)第4节 ................................................................. 局部措施和对系统采取措施 .. (11)第5节 ................................................................. 过程控制手过程能力 .. (13)第6节 ................................................................. 过程改进循环及过程控制 (17)第7节 ................................................................. 控制图:过程控制的工具 (21)第8节 ................................................................. 控制图的益处 .. (25)第II章计量型数据控制图 (27)第1节 ................................................................. 均值和极差图(X—R图). (29)A 收集数据 (31)B 计算控制限 (37)C 过程控制解释 (39)D 过程能力解释 (57)第2节均值和标准差图(X—s图)65A 收集数据 (65)B 计算控制限 (67)C 过程控制解释 (67)~D 过程能力解释 (67)第3节中位数图(x—R图)69A 收集数据 (69)B 计算控制限 (71)C 过程控制解释 (71)D 过程能力解释 (71)E 中位数图的替代方法 (72)第4节单值和移动极差图(X—MR图)75A 收集数据 (75)B 计算控制限 (75)C 过程控制解释 (77)D 过程能力解释 (77)第5节计量型数据的过程能力和过程性能的理解79A 过程术语的定义 (79)B 过程量度的定义 (80)C 条件和假设的描述 (81)D 使用过程量度的建议 (83)第II章计数型数据控制图 (89)第1节不合格品率的P图91A 收集数据 (93)B 计算控制限 (95)C 过程控制解释 (99)D 过程能力解释 (107)第2节不合格品数的np图111A 收集数据 (111)B 计算控制限 (111)C 过程控制解释 (111)D 过程能力解释 (111)第3节不合格数的c图113A 收集数据 (113)B 计算控制限 (113)C 过程控制解释 (113)D 过程能力解释 (113)第4节单位产品不合格数据的u图115A 收集数据 (115)B 计算控制限 (115)C 过程控制解释 (117)D 过程能力解释 (117)第IV章过程测量系统分析 (119)第1节引言119第2节均值和极差法121A 进行研究 (121)B 计算 (122)C 结果分析 (123)D 示例 (127)附录A 关于分组的一些评述131附录B 过度调整137附录C 本手册所描述控制图的选用程序139附录D C pm与其它指数(USL—T)=(T—LSL)的关系 (141)附录E 控制图的常数和公式表143附录F 标准正态分布147附录H ............................................................... 参考文献及建议的读物 .. (159)附录I 可复制的控制图表161插图目录图名称页次1过程控制系统 (6)2变差:普通及特殊原因 (8)3过程控制及过程能力 (12)4过程改进循规蹈矩环 (16)5控制图...............................................................206计量型数据——测量中间或最终过程输出的结果267X—R图 ..............................................................8X—R图建立数据 (32)9X—的图“初始研究” (34)10有控制限的X—R图 (36)11R图——有超出控制限的点存在 (38)12R图——链(极差) (40)13R图——非随机模式 (42)14X—R图——重新计算控制限(极差) 44 15X图——超出控制限的点 (46)16X图——链 ..................................................4817X图——非随模式 (50)18X—R图——重新计算控制限 (52)19X—R图——延长控制限 (54)20相对无规范限界的过程变差 (56)21计算过程能力 ..............................................5822评价过程能力 ..............................................6023数据收集 ......................................................6424X和s图.......................................................25中位数控制图 ..............................................6826中位数控制图—解释 (70)27单值移动极差图 (74)28单值和移动极差图的解释 (76)29“目标柱”与损失函数的比较 (82)30调整过程与要求一致 (84)31计数型数据 ..................................................8832不合格品率p图——数据收集 (92)33不合格品率p图——计算控制限制—表1 9433 不合格品率p图——计算控制限制—表2 .96 34不合格品率p图——超出控制限制的点9835不合格品率p图——链 (100)36不合格品率p图——非随机图形 (102)37不合格品率p图——重新计算控制限. 104 38不合格品数的np图 (110)39不合格品数的c图 (112)40交易会产品不合格数的u图 (114)41u图——重新计算控制限 (116)42量具的重复性和再现性数据记录表 (124)43量具的重复性和再现性报告 (125)44量具的重复性和再现笥数据表——示例12845量具的重复性和再现性报告——示例 . 129第I章持续改进及统计过程控制概述在今天的经济气候下,为了事业昌盛,我们——汽车制造商,供方及销售商必须致力于不断改进。
spc案例

spc案例SPC(Statistical Process Control,也叫统计过程控制)是一种通过统计方法对产品和过程进行监控和改进的质量管理方法。
下面是一个SPC案例,用以说明其在实际生产中的应用。
某制造公司生产一种产品,经过市场调查发现,该产品存在一定的质量问题,如尺寸偏差、露粉等。
为了解决这些问题,公司决定采用SPC方法来监控和改进生产过程。
首先,公司确定一组关键工艺参数,如温度、压力、转速等,以及相关的质量指标,如尺寸、外观等。
随后,公司对每个工艺参数进行测量和记录,并将其输入到SPC软件中。
同时,公司还设置了对应的上下限值,即规定了每个工艺参数的合理变化范围。
在生产过程中,SPC软件会自动进行统计分析,并生成控制图。
控制图上有一条中心线,表示期望值,以及上下限线,表示允许的变化范围。
同时,还有一些参考线,如标准偏差线,用于判断过程稳定性。
公司的技术人员定期对控制图进行检查,观察各参数是否在规定范围内波动,是否出现异常情况。
如果发现异常,技术人员会及时采取措施,如调整机器参数、更换工具等,以及及时通知相关操作人员。
通过SPC的实施,公司逐渐发现了一些问题。
例如,当温度过高时,产品尺寸会偏大;当压力过低时,产品内部会出现空隙。
公司根据这些发现,对生产过程进行了优化,并引入了更先进的控制系統,进一步提高了产品质量。
此外,SPC还帮助公司进行了质量变化的监控和评估。
公司可以利用SPC软件生成的统计报表,进行不同时间段内产品质量的对比。
同时,公司还可以进行根因分析,找出导致质量问题的根本原因,并提出相应的改进措施。
总的来说,通过SPC的应用,该制造公司有效地改善了产品质量,减少了不合格品的数量,并提高了自身的竞争力。
SPC 方法在实际生产中具有广泛的应用前景,可以帮助企业提升质量管理水平,降低成本,提高效率。
统计过程控制(SPC)(PPT58页)
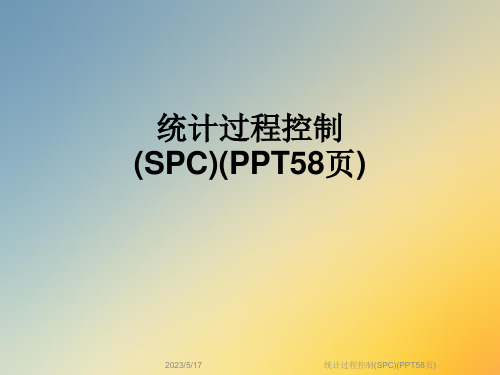
江铃汽车股份有限公司
统计过程控制(SPC)(PPT58页)
普通原因 普通原因造成变差的一个原因,它影响被研究过程的所
有单值。(处于统计控制状态;在统计上受控;受控) 造成随着时间的推移具有稳定的且可重复的分布过程中
的许多变差的原因 特点
过程分布将不发生变化 过程的输出是可预测的 过程是稳定、可控的。 采取系统的措施,由管理人员解决问题
江铃汽车股份有限公司
统计过程控制(SPC)(PPT58页)
2.3局部措施和系统措施
措施 对比
对象
系统措施
通常用来消除变差的普 通原因
局部措施
通常用来消除变 差的特殊原因
实施人员
几乎总是要求管理措施, 以便纠正
通常由与过程直 接相关的人员实 施
效果
大约可纠正85%的过程 问题
通常可纠正大约 15%的过程问题
一个可接受的过程必须是处于受控统计控制 状态的且其固有变差(能力)必须小于图纸 的公差
应通过检查并消除变差的特殊原因使过程处 于受统计控制状态,那么性能是可预测的, 变可评定其满足顾客期望的能力。这是持续 改进的基础
江铃汽车股份有限公司
统计过程控制(SPC)(PPT58页)
3.4过程改进循环
2.1过程的理解及过程控制
1.过程—所谓过程是指共同作用以产出输出的供方、生产 者、人、设备、输入材料、方法和环境及使用输出的顾 客的集合。
过程性能取决于:
供方与顾客之间的沟通
过程设计及实施的方式
运作和管理的方式
2.过程的信息
通过分析过程输出可以获得许多与过程性能有关的信息。如过程 是否稳定,过程能力如何。
4.1控制图应用说明
统计过程控制SPC案例分析

【案例1】 R X -控制图示例某手表厂为了提高手表的质量,应用排列图分析造成手表不合格品的各种原因,发现“停摆”占第一位。
为了解决停摆问题,再次应用排列图分析造成停摆事实的原因,结果发现主要是由于螺栓松动引发的螺栓脱落成的。
为此厂方决定应用控制图对装配作业中的螺栓扭矩进行过程控制。
分解:螺栓扭矩是一计量特性值,故可选用基于正态分布的计量控制图。
又由于本例是大量生产,不难取得数据,故决定选用灵敏度高的R X -图。
解:我们按照下列步骤建立R X -图步骤1:取预备数据,然后将数据合理分成25个子组,参见表1。
步骤2:计算各组样本的平均数i X 。
例如,第一组样本的平均值为:0.16451621661641741541=++++=X其余参见表1中第(7)栏。
步骤3:计算各组样本的极差i R 。
例如,第一组样本的极差为:{}{}20154174min max 111=-=-=j j X X R其余参见表1中第(8)栏。
表1: 【案例1】的数据与R X -图计算表i故:272.163=X ,280.14=R 。
步骤5:计算R 图的参数。
先计算R 图的参数。
从D 3、D 4系数表可知,当子组大小n =5,D 4=2.114,D 3=0,代入R 图的公式,得到: 188.30280.14114.24=⨯==R D UCL R280.14==R CL R ==R D LCL R 3—极差控制图:均值控制图:图1 【案例1】 的第一次R X -图参见图1。
可见现在R 图判稳。
故接着再建立X 图。
由于n =5,从系数A 2表知A 2=0.577,再将272.163=X ,280.14=R 代入X 图的公式,得到X 图:512.171280.14577.0272.1632≈⨯+=+=R A X UCL X 272.163==X CL X032.155280.14577.0272.1632≈⨯-=-=R A X LCL X因为第13组X 值为155.00小于X LCL ,故过程的均值失控。
SPC案例分析
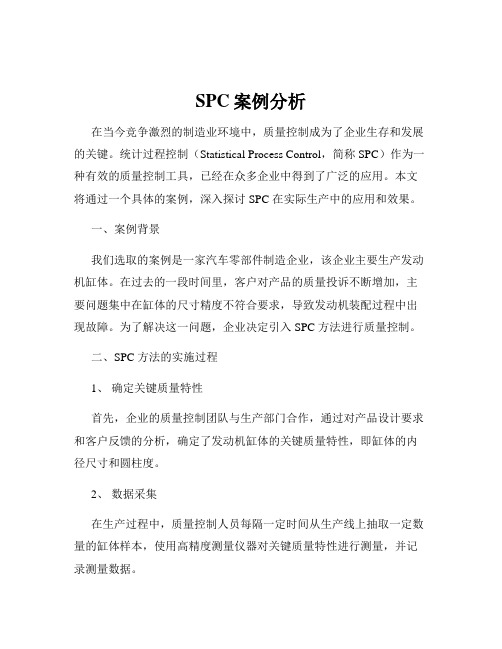
SPC案例分析在当今竞争激烈的制造业环境中,质量控制成为了企业生存和发展的关键。
统计过程控制(Statistical Process Control,简称 SPC)作为一种有效的质量控制工具,已经在众多企业中得到了广泛的应用。
本文将通过一个具体的案例,深入探讨 SPC 在实际生产中的应用和效果。
一、案例背景我们选取的案例是一家汽车零部件制造企业,该企业主要生产发动机缸体。
在过去的一段时间里,客户对产品的质量投诉不断增加,主要问题集中在缸体的尺寸精度不符合要求,导致发动机装配过程中出现故障。
为了解决这一问题,企业决定引入 SPC 方法进行质量控制。
二、SPC 方法的实施过程1、确定关键质量特性首先,企业的质量控制团队与生产部门合作,通过对产品设计要求和客户反馈的分析,确定了发动机缸体的关键质量特性,即缸体的内径尺寸和圆柱度。
2、数据采集在生产过程中,质量控制人员每隔一定时间从生产线上抽取一定数量的缸体样本,使用高精度测量仪器对关键质量特性进行测量,并记录测量数据。
3、控制图的绘制将采集到的数据输入到统计软件中,绘制均值极差控制图(XR 控制图)和均值标准差控制图(XS 控制图)。
控制图的横坐标表示样本序号,纵坐标表示测量值。
4、控制限的确定根据样本数据的分布特征和统计规律,计算出控制图的控制限。
控制限分为上控制限(UCL)、下控制限(LCL)和中心线(CL)。
中心线通常为样本数据的均值,上控制限和下控制限则根据一定的计算公式得出。
5、过程监控与分析定期对控制图进行观察和分析,判断生产过程是否处于受控状态。
如果数据点落在控制限内,且没有明显的趋势或异常模式,则认为过程处于受控状态;反之,如果数据点超出控制限,或者出现连续上升或下降的趋势,或者存在周期性的波动等异常模式,则认为过程失控,需要采取相应的措施进行改进。
三、案例结果与分析在实施 SPC 方法后的一段时间里,企业对生产过程进行了持续的监控和分析。
SPC分析实例

SPC的核心思想是利用统计方法来分析生产过程中的波动找出影响产品质量的关键因素 并采取相应的措施进行改进。
SPC分析主要包括控制图、过程能力指数(Cp、Cpk)、过程性能指数(Pp、Ppk) 等工具和方法。
03
SPC分析实例介绍
感谢观看
汇报人:
Cpk:过程能力指数表示过程能力 满足规格要求的程度
Cpk:过程能力指数表示过程能力 满足规格要求的程度
过程性能指数解读
过程性能指数 (PPI):用于 衡量生产过程中 产品质量的指标
PPI的计算方法: PPI=(合格品 数量/总生产数 量)*100%
PPI的意义:反 映生产过程中产 品质量的稳定性 和可靠性
过程优化:SPC分析可以帮助企业优化生产过程提高生产效率和产品质量。
成本控制:通过SPC分析可以及时发现生产过程中的浪费现象并采取相应的措施进行改进。
风险管理:SPC分析可以帮助企业识别生产过程中的风险并采取相应的措施进行预防和控 制。
基于SPC分析的改进建议和措施
制定控制计划:根据关键质 量特性制定相应的控制计划
数据处理:对数 据进行清洗、整 理和标准化处理
实例分析过程和方法
确定分析目 标:选择需 要分析的产
品或过程
数据收集: 收集相关数 据包括时间、 数量、质量
等
数据处理: 对数据进行 整理、清洗、 转换等操作
建立SPC模 型:选择合 适的SPC模 型如控制图、
直方图等
分析结果: 根据模型分 析结果找出 问题所在并 提出改进措
效率。
增强市场竞争 力:通过SPC 分析可以提高 产品质量和生 产效率增强企 业的市场竞争
- 1、下载文档前请自行甄别文档内容的完整性,平台不提供额外的编辑、内容补充、找答案等附加服务。
- 2、"仅部分预览"的文档,不可在线预览部分如存在完整性等问题,可反馈申请退款(可完整预览的文档不适用该条件!)。
- 3、如文档侵犯您的权益,请联系客服反馈,我们会尽快为您处理(人工客服工作时间:9:00-18:30)。
SPC统计过程控制案例分析(doc 24页)统计过程控制(SPC)案例分析一.用途1. 分析判断生产过程的稳定性,生产过程处于统计控制状态。
2.及时发现生产过程中的异常现象和缓慢变异,预防不合格品产生。
3.查明生产设备和工艺装备的实际精度,以便作出正确的技术决定。
4.为评定产品质量提供依据。
二.控制图的基本格式1.标题部分X-R控制图数据表计算:X图:CL=X R图:CL=RUCL=X+RA2UCL=RD4LCL=X-RA2LCL=RD32质量特性在方格纸上作出控制图:RX 控制图X图R图CLLCLU 样本规则2 控制界限内点子的排列无异常现象。
[案例1] p控制图某半导体器件厂2月份某种产品的数据如下表(2)(3)栏所表示,根据以往记录知,稳态下的平均不合格品率0389p,作控制图对其进行控.0制.数据与p图计算表1394 0 0 0.099 1495 3 0.032 0.098 1581 0 0 0.103 1682 7 0.085 0.103 1775 3 0.040 0.106 1857 1 0.018 0.116 1991 6 0.066 0.100 2067 2 0.030 0.110 2186 3 0.035 0.101 2299 8 0.080 0.097 2376 1 0.013 0.105 3493 8 0.086 0.099 2572 5 0.069 0.107 2697 9 0.093 0.098 2799 10 0.100 0.097 2876 2 0.026 0.105 小计2315 90[解] 步骤一 :预备数据的取得,如上边表所示.步骤二: 计算样本不合格品率024.085/2/,/111====n D p n D p i i i步骤三: 计算p 图的控制线ii i i n n p p p LCL CL n n p p p UCL n D p /)0389.01(0389.030389.0/)1(30389.0/)0389.01(0389.030389.0/)1(30389.02315/90/--=--==-+=-+=====∑∑由于本例中各个样本大小i n 不相等,所以必须对各个样本分别求出其控制界线.例如对第一个样本n1=85,有UCL=0.102 CL=0.0389 LCL=-0.024此处LCL 为负值,取为零.作出它的SPC 图形.UCLCLLCL[案例2]为控制某无线电元件的不合格率而设计p 图,生产过程质量要求为平均不合格率≤2%。
解:一.收集收据在5M1E 充分固定并标准化的情况下,从生产过程中收集数据,见下表所表示:某无线电元件不合格品率数据表组号样本大小样本中不合格品数不合格品率1 835 8 1.02 808 12 1.53 780 6 0.84 504 12 2.45 860 14 1.66 600 5 0.87 822 11 1.38 814 8 1.09 618 10 1.610 703 8 1.111 850 19 2.212 709 11 1.613 700 10 1.414 500 16 3.215 830 14 1.716 798 7 0.917 813 9 1.118 818 7 0.919 581 8 1.420 550 6 1.121807 11 1.4 22595 7 1.2 23500 12 2.4 24760 7 0.9 25620 10 1.6 总和17775 248 平均值 711 1.4二.计算样本中不合格品率:k i n k p i i i ,.....,2,1,==,列在上表. 三.求过程平均不合格品率:%14017775/248===∑∑ii n kp四.计算控制线 p 图:ii n p p p UCL n p p p UCL p CL /)1(3/)1(3%140--=-+===从上式可以看出,当诸样本大小i n 不相等时,UCL,LCL 随i n 的变化而变化,其图形为阶梯式的折线而非直线.为了方便,若有关系式:2/2min max n n nn ≥≤同时满足,也即i n 相差不大时,可以令n n i =,,使得上下限仍为常数,其图形仍为直线.本例中,711=n , 诸样本大小i n 满足上面条件,故有控制线为:p 图:%08.0/)1(3/)1(3%72.2/)1(3/)1(3%140=--=--==-+=-+===n p p p n p p p UCL n p p p n p p p UCL p CL i i五.制作控制图:以样本序号为横坐标,样本不合格品率为纵坐标,做p 图.UCLCLLCL六.描点:依据每个样本中的不合格品率在图上描点.七.分析生产过程是否处于统计控制状态从图上可以看到,第14个点超过控制界限上界,出现异常现象,这说明生产过程处于失控状态.尽管p =1.40%<2%,但由于生产过程失控,即不合格品率波动大,所以不能将此分析用控制图转化为控制用控制图,应查明第14点失控的原因,并制定纠正措施.[案例3]某手表厂为了提高手表的质量,应用排列图分析造成手表不合格的各种原因,发现---停摆占第一位.为了解决停摆问题,再次应用排列图分析造成停摆的原因,结果发现主要是由于螺栓脱落造成的,而后者是有螺栓松动造成.为此,厂方决定应用控制图对装配作业中的螺栓扭矩进行过程控制.[分析]螺栓扭矩是计量特征值,故可选用正态分布控制图,又由于本例是大量生产,不难取得数据,故决定选用灵敏度高的R x -图. [解]按照下列步骤建立R x -图步骤一.根据合理分组原则,取25组预备数据,见下表. 步骤二.计算各样本组的平均值i X ,例如第一组样本的平均值为1X =(154+174+164+166+162)/5=164.0步骤三.计算各样本的极差20154174}m in{}m ax {,1=-=-=i i i X X R R 步骤四.计算样本总均值R X 和平均样本极差280.14272.163,3578.4081====∑∑R X RXii所以步骤五.计算R 图与X 的参数 (1) 先计算R 图的参数样本容量n=5时,D4=2.114,D3=0代入R 图公式0280.14188.30280.14*114.234=======R D LCL R CL R D UCL R R R均值控制图极差控制图例2的原始数据与RX 图计算表.序号样本观察值∑XijiXR备注Xi1Xi2Xi3Xi4Xi54 4 4 6 22 166 17162166164828 165.6 83 168 1661616216816 163.2 84 168 16417164166832 166.4 65 153 165162165167812 162.4 146 164 158162172168824 164.8 147 167 169159175165835 167.0 168 158 16162164166810 162.0 89 156 162164152164798 159.6 1210 174 162162156174828 165.6 1811 168 17416616166934 166.8 148 0 2 4 013 165 159147153151775 155.0 18 超限14 164 16616417164828 165.6 615 162 158154168172814 162.8 1816 158 162156164152792 158.4 1217 151 158154181168812 162.4 3018 166 166172164162830 166.0 1019 170 171661616826 165.2 1020 168 1616215416804 160.8 1421 162 164165169153813 162.6 1622 166 1617172158826 165.2 1423 172 164 159 165 160 822 164.0 1324 174 164 166 157 162 823 164.6 17 25 151 160164158170803 160.6 19∑ 4081.8 357 平均163.27214.280(2)可见现在R 图判稳,故接着再建立均值图。
032.155280.14*577.0272.163272.163512.171280.14*577.0272.163,280.14,272.163577.0222=-=-====+=+====R A X LCL X CL R A X UCL X R X A X X X 得到图的公式代入将 第13组数据是例外值,需要用判定准则(判稳/判异)判断。
125.14868.29125.14*114.2,617.16324/)0.1558.4081(24/125.1424/)18357(24/.,13,14,,,.,032.155,00.15534========-===-===∑∑R D LCL R CL R D UCL R X R X X R R X R LCL X R R R I X 图得到图的公式图与代入此时的参数图与并重新计算组数据故本例可以去掉第决组数据时该问题已经解采集到第很快进行了调整夹具松动调查其原因发现故过程的均值失控小于值为另外,由表可见,R 图中的第17组R=30出界,于是再次执行20字方针:“查出异因,采取措施,保证消除,纳入标准,不再出现”,消除异因纳入标准之后,应再收集35组数据,重新计算,但为了简化本例题,而采用舍去第17组数据的方法(注:舍弃数据的办法不是不能用,而必须是调整没有改变原有的4M1E 的关系,例如刚才对第13组数据的舍弃,异因对后面的数据没有影响),重新计算如下:670.16323/)4.1628.3926(23/435.1323/)30339(23/=-===-==∑∑i I X X R RR 图:0435.13401.28435.13*114.234=======R D LCL R CL R D UCL R R R由表知道,R 图可以判稳,计算均值控制图如:918.155435.13*577.0670.163670.163421.171435.13*577.0670.163:22=-=-====+=+=R A X LCL X CL R A X UCL X X X X 图将23组样本的极差值与均值分别打点与R 图和x 图上(下图表示),根据判稳准则,知此过程的波动情况与均值都处于稳态.[注意]严格地讲,23组数据根本不能运用判稳准则,一般建议收集35—40组数据,运用第二条判稳准则来判断过程是否处于稳态.步骤六.与规格进行比较.已知给定质量规格为TL=100,YU=200. 现把全部预备数据作直方图并与规格进行比较.如下图所表示.由此可见,数据分布与规格比较均有余量,但其平均值并未对准规格中心,因此还可以加以调整以便提高过程适应能力指数,减少不合格品率.调整后要重新计算RX 图.SU=200145 150 155 160 165 170 175 180 185 SL=100 m=150 u=163.69步骤七. 延长上述RX 图的控制线,进入控制用控制图阶段,对过程进行日常控制.[例4]某厂生产一种零件,其长度要求为49.50±0.10mm,生产过程质量要求为Cp≥1,为对该过程实行连续监控,试设计RX 图。