普通机械加工中常见缺陷与工艺结构
机械设计与加工中存在的问题探究

机械设计与加工中存在的问题探究江朝虎(国营长虹机械厂,广西桂林541003)【摘要】随着机械化生产技术的广泛应用,对机械加工的各个环节提出了更为严苛的要求,任何环节的各项因素均会对产品的质量与性能形成直接影响。
而设计与加工作为机械设备生产中的重要环节,对机械性能表现起到决定性作用。
所以,一定要进一步完善机械设计与加工的工序,确保机械设计与加工的产品质量,为工业生产提供更好服务。
基于此,本文将针对机械设计与加工中存在的主要问题进行分析,并针对问题提出具体的改善对策,以期为相关从业者提供参考借鉴。
关键词:机械设计;机械加工;问题;改善对策中图分类号:TH16文献标识码:BDOI:10.12147/ki.1671-3508.2023.05.092Research on the Problems Existing in Mechanical Design and MachiningJiang Chaohu(State-run Changhong Machinery Factory,Guilin,Guangxi541003,CHN)【Abstract】With the extensive application of mechanized production technology,more stringent requirements have been put forward for each link of mechanical processing.Every factor in any link will have a direct impact on product quality and performance.The design and processing of mechanical equipment as an important part of the production of mechanical performance plays a decisive role.Therefore,we must further improve the process of mechanical design and processing,to ensure the quality of mechanical design and processing products,for industrial production to provide better services.Based on this,this paper will analyze the main problems in mechanical design and processing,and put forward specific measures to improve the prob⁃lem,in order to provide reference for relevant practitioners.Key words:machine design;machine processing;problem;improvement countermeasure机械设计作为机器设备生产中的重要环节,要综合考量机器设备的多方面需求,结合需求以图文结合的形式表现出来,为后面的加工制造指明方向。
最新普通机械加工中常见缺陷与工艺结构

第二部分:切削加工
车削 四、平面中心凸起:由于刀具选用不当,加工过程中,刀 具磨损过快引起车削平面从外往中心逐渐外凸现象。 五、板、盘类工件中心内凹:工件装夹力过大,工件中心 区外凸,加工时切削过多使工件中心内凹。 六、板、盘、轴类各部分厚/高度不一,主要是装夹未校 平引起。 七、柱面锥度,加工过程中刀具磨损过快引起。 八、不同轴:当工件加工柱面时,由于工艺要求两次装夹 后,同轴线的柱面不同部分或不同柱面,加工完后不同轴 现像。主要是二次装夹时未找正回转轴心。 九、细长轴弯曲及中间段过细:
第一部分:铸造生产
常见工艺结构 *拔模斜度:在制造模型时,垂直与分型面的立壁做成一定 斜度的立壁,此斜度即为拔模斜度,做用是为方便在做砂 铸型时容易取出模型。 *结构圆角:铸件一般都在轮廓边沿或铸件壁的连接及转弯 处做出结构圆角。作用在于消除壁厚突变、尖角、直角, 从而防止局部应力集中,产生裂纹。
第二部分:切削加工
车削 一、表面粗糙、毛刺多 多与刀刃磨损,切削热,进给速度过快及积 屑瘤及系统振动大有关。 二、 表面刀伤(又称“乱刀痕”):退刀时在刀刃 未完全与加工面脱离接触,既后退刀架,在工件 表面产生螺旋线状刀痕。 三、未清根:加工轴类工件时,因刀刃钝角大在 轴肩、环槽根部圆角过大,或车平面时,由于横 向进刀未到位或刀尖未对正工件回转中心,致平 面中心有柱状小台现象。
第二部分:切削加工
金属切削过程实质 上就是,产生切屑和 形成已加工表面的过 程。 最具代表性的切 削加工是车削、铣削、 磨削及钻削,下面以 以上四种加工为主介 绍加工中常见的缺陷。
已加工表面变质层:切削表面质量很大程 度上取决于表面表面变质层。切削层金属 流经过切削刃后分为两支,一支成为切屑, 另一支沿后刀面形成已加工表面。在这个 过程中,由于切削刃有一定的钝角,实际 上有△a部分金属不会沿OM滑移成切屑, 而被钝圆部分挤到已加工表面,这层先受 压应力后又在BC区受到剪应力的金属层即 为已加工表面变质层。
零件上常见的工艺结构
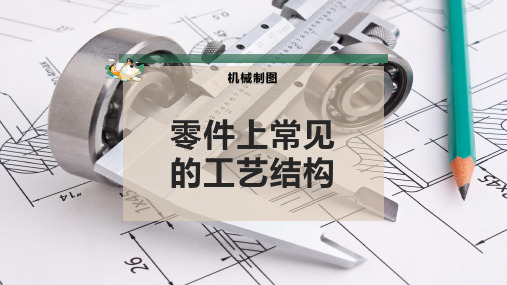
(c)正确
(d)错误
图8-58 钻孔应注意的问题
(e)正确
(a)不合理 (b)合理
图8-59 钻孔的方便性
机械制图
谢谢观看!
(a)
(b)
图8-55 退刀槽和砂轮越程槽
(c)
1.2 机械加工工艺结构 3.凸台和凹坑
为了保证零件表面在装配时接触良好和减少机械加工 的面积,常在零件表面上设计出凸台或凹坑,并尽量使多 个凸台在同一水平面上,以便于加工,如图8-56所示。
图8-56 凸台和凹坑
1.2 机械加工工艺结构
4.钻孔结构
1.2 机械加工工艺结构
2.退刀槽和砂轮越程槽
切削时(主要是车削和磨削),为了便于退出刀具或 砂轮,常在待加工面的轴肩处预先车出退刀槽和砂轮越程 槽。这样既能保证加工表面满足加工技术要求,又便于装 配时相关零件间靠紧。常见退刀槽和砂轮越程槽的简化画 法及尺寸标注如图8-55所示。
1.2 机械加工工艺结构机 Nhomakorabea制图零件上常见 的工艺结构
零件上常见的工艺结构
零件的结构形状主要是由零件在机器中的作用以及 其制造工艺所决定的。因此,零件的结构除满足使用要 求外,还应具有合理的工艺结构。零件上常见的工艺结 构有铸造工艺结构、机械加工工艺结构等。
1.1 铸造工艺结构
铸造是指将熔融的液态金属或合金浇入砂型型腔中, 待其冷却凝固后获得的具有一定形状和性能的铸造零件 的方法。铸造的工艺结构包括铸造圆角、起模斜度和铸 件壁厚等。
1.2 机械加工工艺结构
(a)45°倒角 (b)非45°倒角
图8-54 倒角和圆角
1.2 机械加工工艺结构
为了避免因应力集中而产生裂纹,在轴或孔中直径不 等的交接处,常加工成环面过渡,称为倒圆,如图8-54(c )所示。
圆锥加工缺陷的几种情况
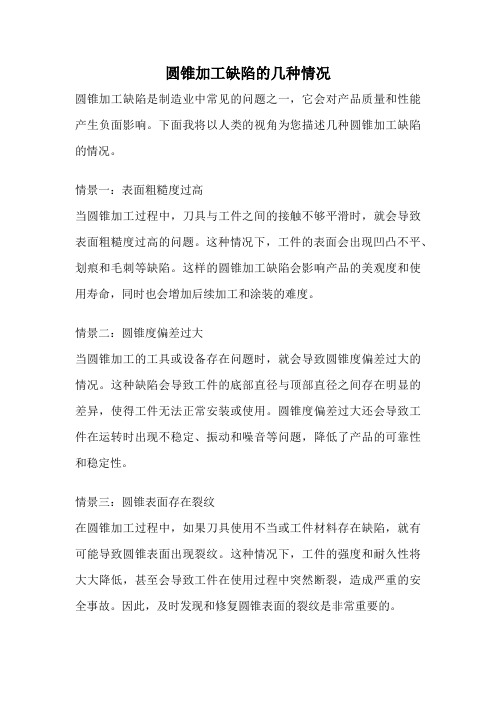
圆锥加工缺陷的几种情况圆锥加工缺陷是制造业中常见的问题之一,它会对产品质量和性能产生负面影响。
下面我将以人类的视角为您描述几种圆锥加工缺陷的情况。
情景一:表面粗糙度过高当圆锥加工过程中,刀具与工件之间的接触不够平滑时,就会导致表面粗糙度过高的问题。
这种情况下,工件的表面会出现凹凸不平、划痕和毛刺等缺陷。
这样的圆锥加工缺陷会影响产品的美观度和使用寿命,同时也会增加后续加工和涂装的难度。
情景二:圆锥度偏差过大当圆锥加工的工具或设备存在问题时,就会导致圆锥度偏差过大的情况。
这种缺陷会导致工件的底部直径与顶部直径之间存在明显的差异,使得工件无法正常安装或使用。
圆锥度偏差过大还会导致工件在运转时出现不稳定、振动和噪音等问题,降低了产品的可靠性和稳定性。
情景三:圆锥表面存在裂纹在圆锥加工过程中,如果刀具使用不当或工件材料存在缺陷,就有可能导致圆锥表面出现裂纹。
这种情况下,工件的强度和耐久性将大大降低,甚至会导致工件在使用过程中突然断裂,造成严重的安全事故。
因此,及时发现和修复圆锥表面的裂纹是非常重要的。
情景四:圆锥加工尺寸不准确在圆锥加工过程中,如果设备或工具的精度不够高,就会导致圆锥加工尺寸不准确的问题。
这种情况下,工件的尺寸可能会超出允许范围,无法满足设计要求。
圆锥加工尺寸不准确还会导致工件之间的配合不良,影响产品的装配和使用效果。
总结:圆锥加工缺陷是制造业中常见的问题,它会对产品质量和性能产生负面影响。
表面粗糙度过高、圆锥度偏差过大、圆锥表面存在裂纹和圆锥加工尺寸不准确是常见的圆锥加工缺陷情况。
为了避免这些缺陷的出现,制造企业应加强设备和工具的维护保养,提高加工技术和操作技能,严格控制各项加工参数,并对加工过程进行严格的质量检查和监控。
只有这样,才能确保圆锥加工的质量和产品的可靠性。
金属常见加工工艺缺陷的特征、原因、影响及措施

度下,金属再结晶退火加热温度过高或时间过长所致。晶粒粗大或粗细不均会导致在变形量较 大的部位产生裂纹,且裂纹多沿粗细混晶交界区择优分布。
三.由于材料成分、性能不合格
1.成分不合格 冷冲用钢板的化学成份应严格控,特别是碳、硫、磷元素极为重要。碳元素在钢中形成渗
2.带状组织 钢中带状组织是由铁素体和珠光体相间分布组成。它是由于碳、磷、硫晶间偏析,在热压
力加工中使之沿着金属变形方向被拉长,呈带状分布的夹杂物。 由于带状组织的取向平行于钢材轧制方向,而铁素体和珠光体的强度及塑性差异悬殊,因
此,冷冲时当钢件的变形方向与钢板带状组织相垂直,容易产生拉裂和撕裂。由于钢板带状组 织引起的冲裂,裂纹平行于钢板轧制方向,裂纹粗大,显微观察时裂纹多沿珠光体边缘分布、 取向平行于带状组织。
3.鳞片状毛刺
以较低或中等切削速度切削塑性金属时,加工表面往往会出现鳞片状毛刺,尤其对圆孔采 用拉削方法更易出现,若拉削出口毛刺没有去除,则将成为使用中应力集中的根源。
4.“R”加工过小
零件拐角半径小,尤其是横截面形状发生急骤的变化,会在局部发生应力集中而产生微裂 纹并扩展成疲劳裂纹,导致疲劳断裂。
3.涡流
金属在锻造过程中由于剧烈的热变形使金属组织发生晶粒结晶重新定向排列,形成结晶织 构和金属中的非金属夹杂物、树枝晶偏析、第二相质点等沿热加工方向形变延伸呈带状分布, 形成了锻件的纤维状组织即锻造流线。
产生的原因主要是表面氮浓度富集,化合物虽连续粗大网络状分布。在磨削时倾向于脱落 的氮化层的显微结构特点是沿奥氏体晶界存在稠密的网状氮化物,它的存在使晶格畸变加剧, 在位错与晶界处三向应力增大,在磨削力、热应力及组织应力的作用下,粗大的氮化物网络边 界区切口效应敏感性增大,造成综合应力叠加,当这种应力超过渗层的强度极限时,即产生脆 性破裂与剥落。当晶界强度大于晶内强度时,则裂纹沿晶扩展产生脆裂及剥落;当晶界强度等 于晶内强度时,则裂纹的扩展呈穿晶脆裂及剥落。
锻件缺陷的原因及处理

锻件缺陷的主要原因及处理一、原材料的主要缺陷及其引起的锻件缺陷锻造用的原材料为铸锭、轧材、挤材及锻坯。
而轧材、挤材及锻坯分别是铸锭经轧制、挤压及锻造加工成的半成品。
一般情况下,铸锭的内部缺陷或表面缺陷的出现有时是不可避免的。
例如,内部的成分与组织偏析等。
原材料存在的各种缺陷,不仅会影响锻件的成形,而且将影响锻件的最终质量。
根据不完全的统计,在航空工业系统中,导致航空锻件报废的诸多原因中,由于原材料固有缺陷引起的约占一半左右。
因此,千万不可忽视原材料的质量控制工作。
由于原材料的缺陷造成的锻件缺陷通常有:1.表面裂纹表面裂纹多发生在轧制棒材和锻制棒材上,一般呈直线形状,和轧制或锻造的主变形方向一致。
造成这种缺陷的原因很多,例如钢锭内的皮下气泡在轧制时一面沿变形方向伸长,一面暴露到表面上和向内部深处发展。
又如在轧制时,坯料的表面如被划伤,冷却时将造成应力集中,从而可能沿划痕开裂等等。
这种裂纹若在锻造前不去掉,锻造时便可能扩展引起锻件裂纹。
2.折叠折叠形成的原因是当金属坯料在轧制过程中,由于轧辊上的型槽定径不正确,或因型槽磨损面产生的毛刺在轧制时被卷入,形成和材料表面成一定倾角的折缝。
对钢材,折缝内有氧化铁夹杂,四周有脱碳。
折叠若在锻造前不去掉,可能引起锻件折叠或开裂。
3.结疤结疤是在轧材表面局部区域的一层可剥落的薄膜。
结疤的形成是由于浇铸时钢液飞溅而凝结在钢锭表面,轧制时被压成薄膜,贴附在轧材的表面,即为结疤。
锻后锻件经酸洗清理,薄膜将会剥落而成为锻件表面缺陷。
4.层状断口层状断口的特征是其断口或断面与折断了的石板、树皮很相似。
层状断口多发生在合金钢(铬镍钢、铬镍钨钢等),碳钢中也有发现。
这种缺陷的产生是由于钢中存在的非金属夹杂物、枝晶偏析以及气孔疏松等缺陷,在锻、轧过程中沿轧制方向被拉长,使钢材呈片层状。
如果杂质过多,锻造就有分层破裂的危险。
层状断口越严重,钢的塑性、韧性越差,尤其是横向力学性能很低,所以钢材如具有明显的层片状缺陷是不合格的。
机械加工常见热处理工艺

渗碳渗碳热处理渗碳:是对金属表面处理的一种,采用渗碳的多为低碳钢或低合金钢,具体方法是将工件置入具有活性渗碳介质中,加热到900--950摄氏度的单相奥氏体区,保温足够时间后,使渗碳介质中分解出的活性碳原子渗入钢件表层,从而获得表层高碳,心部仍保持原有成分。
相似的还有低温渗氮处理。
这是金属材料常见的一种热处理工艺,它可以使渗过碳的工件表面获得很高的硬度,提高其耐磨程度。
概述渗碳(carburizing/carburization)是指使碳原子渗入到钢表面层的过程。
也是使低碳钢的工件具有高碳钢的表面层,再经过淬火和低温回火,使工件的表面层具有高硬度和耐磨性,而工件的中心部分仍然保持着低碳钢的韧性和塑性。
渗碳工件的材料一般为低碳钢或低碳合金钢(含碳量小于0.25%)。
渗碳后﹐钢件表面的化学成分可接近高碳钢。
工件渗碳后还要经过淬火﹐以得到高的表面硬度﹑高的耐磨性和疲劳强度﹐并保持心部有低碳钢淬火后的强韧性﹐使工件能承受冲击载荷。
渗碳工艺广泛用于飞机﹑汽车和拖拉机等的机械零件﹐如齿轮﹑轴﹑凸轮轴等。
渗碳工艺在中国可以上溯到2000年以前。
最早是用固体渗碳介质渗碳。
液体和气体渗碳是在20世纪出现并得到广泛应用的。
美国在20年代开始采用转筒炉进行气体渗碳。
30年代﹐连续式气体渗碳炉开始在工业上应用。
60年代高温(960~1100℃)气体渗碳得到发展。
至70年代﹐出现了真空渗碳和离子渗碳。
分类按含碳介质的不同﹐渗碳可分为气体渗碳、固体渗碳﹑液体渗碳﹑和碳氮共渗(氰化)。
气体渗碳是将工件装入密闭的渗碳炉内,通入气体渗剂(甲烷、乙烷等)或液体渗剂(煤油或苯、酒精、丙酮等),在高温下分解出活性碳原子,渗入工件表面,以获得高碳表面层的一种渗碳操作工艺。
固体渗碳是将工件和固体渗碳剂(木炭加促进剂组成)一起装在密闭的渗碳箱中,将箱放入加热炉中加热到渗碳温度,并保温一定时间,使活性碳原子渗人工件表面的一种最早的渗碳方法。
液体渗碳是利用液体介质进行渗碳,常用的液体渗碳介质有:碳化硅,―603‖渗碳剂等。
锻件毛坯等温正火常见缺陷及解决办法

锻件毛坯等温正火常见缺陷及解决办法锻件毛坯等温正火常见缺陷及解决办法文/张军改·河北东安精工股份有限公司等温正火是近年来汽车齿轮用钢预先热处理的一种方法,在实际操作中常常出现一些热处理缺陷,给后续机加工和最终热处理带来不良影响。
本文通过大量实践,总结了锻件毛坯等温正火中常见缺陷及解决办法。
正火和普通正火正火是将钢加热到Ac3(或Accm)以上适当温度(一般增加30~50℃),保温以后在空气中冷却得到珠光体类组织的热处理工艺。
其目的是消除或改善坯料制备时所造成的各种组织缺陷,获得最有利于切削加工的组织和硬度,改善组织中各组成相的形态和分布,细化晶粒,为最终热处理做好组织准备。
常用作齿轮用钢的预先热处理,但因其冷却方式是在空气中连续冷却,珠光体类组织形成温度跨度大,组织均匀性差,硬度离散度大,机加工性能不好,容易导致最终热处理变形。
因此,近年来汽车用齿轮钢件普遍采用等温正火作为其预先热处理。
等温正火是指将工件加热到Ac3或Accm以上30~50℃,保温适当时间后快冷至珠光体转变区的某一温度保温,以获得珠光体型组织,然后在空气中冷却的正火工艺。
与普通正火相比,等温正火因其组织转变是在恒定温度下完成的,容易控制非平衡组织(如贝氏体)的形成,使硬度更加均匀,可获得较理想的显微组织,提高机加工精度,减小机加工变形,延长机加工刀具寿命,减少最终热处理变形和开裂倾向,保证最终热处理质量。
但是,如果等温正火工艺参数选择不合适,也会产生各种热处理缺陷,给机加工和最终热处理带来不良影响。
经过多年实践,以下我们总结出等温正火的一些常见缺陷和解决办法。
晶粒细碎、不均晶粒细碎、不均缺陷如图1所示,该缺陷常出现在20CrMnTi材质中,因为这种材质中含有细化晶粒的Ti元素,具有阻止晶粒长大作用。
如果温度不够高,或保温时间不够长,会造成晶粒来不及长大;或部分晶粒长大,但另一部分晶粒还来不及长大。
形成的主要原因是:⑴加热温度低;⑵保温时间短;⑶锻坯快速冷却形成原始组织中有贝氏体或马氏体等,并在正火时难以转变所致。
- 1、下载文档前请自行甄别文档内容的完整性,平台不提供额外的编辑、内容补充、找答案等附加服务。
- 2、"仅部分预览"的文档,不可在线预览部分如存在完整性等问题,可反馈申请退款(可完整预览的文档不适用该条件!)。
- 3、如文档侵犯您的权益,请联系客服反馈,我们会尽快为您处理(人工客服工作时间:9:00-18:30)。
五、板、盘类工件E中v心al内ua凹t:io工n 件on装ly夹. 力过大,工件中心 ted w六i区th、外A板凸s、,p盘o加s、工e轴时.S类切li各d削e部过s分多fo厚使r/工.高N件度E中不T心一3内,.5凹主C。要li是en装t夹P未ro校file 5.2
7、偏析,铸件上下各部分化学成分不均匀现象,宏观表现为:各部分比重明显不一致。
第一部分:铸造生产
常见工艺结构 *拔模斜度:在制造模型时,垂直与分型面的立壁做成一定 斜度的立壁,此斜度即为拔模斜度,做用是为方便在做砂 铸型时容易取出模型。
*结构圆角:铸件一E般va都lu在a轮ti廓on边o沿n或ly铸. 件壁的连接及转弯 ted wi处从th做而A出防s结止po构局s圆部e角应.S。力lid作集e用中s在,fo于产r消生.N除裂E壁纹T厚。3突.5变C、l尖ie角nt、P直r角of,ile 5.2
普通机械加工中常见 ------缺陷与工艺结构
Evaluation only. ted with Aspose.Slides for .NET 3.5 Client Profile 5.2
Copyright 2004-2011 A制sp作os:e P段ty长L青td. 审批:
目录
第一部分:铸造生产
Copyright 2004-2011 Aspose 特点是细小平直,缝内干静如放置时间较短,缝内呈金属原色。
三、表面缺陷类
Pty
Ltd.
1、粘砂,铸件表面粘着一层难以除去的砂粒,铸件表面特别粗糙。
2、夹砂,铸件表面上有一层突出的金属片状物,在金属片与铸件基体之间有一层型砂的现象,夹砂 又称:起皮或结疤。
未表C完面o全产p与 生yri加 螺gh工 旋t 面 线20脱状0离刀4-接痕20触。11,A既s后po退se刀P架ty,L在td工. 件
三、未清根:加工轴类工件时,因刀刃钝角大在 轴肩、环槽根部圆角过大,或车平面时,由于横 向进刀未到位或刀尖未对正工件回转中心,致平 面中心有柱状小台现象。
第二部分:切削加工
3、砂眼,铸件内部或表面上有充满型砂的孔眼称为“砂眼”.注要是由于铸型被破坏型砂被卷入液 态金属内形成。
Evaluation only. 4、渣眼,由于液态金属的熔渣进入型腔形成。特点是孔眼内充满熔渣,孔形不规则。
5、铁豆,液态金属飞溅形成。 二、裂纹类
ted with Aspose.Slides for .NET 3.5 Client Profile 5.2 1、热裂,高温下形成的裂缝,特点是裂缝短而宽,形状曲折无规则,缝内呈氧化颜色。 2、冷裂,铸件冷却时形成,注要在受拉应力处,由其是尖角及工件筋位根部及其它形状突变部位。
平引C起op。yright 2004-2011 Aspose Pty Ltd.
七、柱面锥度,加工过程中刀具磨损过快引起。 八、不同轴:当工件加工柱面时,由于工艺要求两次装夹 后,同轴线的柱面不同部分或不同柱面,加工完后不同轴 现像。主要是二次装夹时未找正回转轴心。 九、细长轴弯曲及中间段过细:
Evaluation only. ted with Aspose.Slides for .NET 3.5 Client Profile 5.2
3、冷隔,铸件未完全熔和的缝隙,特点是缝隙的两边呈圆滑状。主要是浇注时温度过底,流动性不 好,或浇注速度太慢及浇注时发生中断引起。
4、浇不足,液态金属未充满型腔,铸件形状不完整现象。Fra bibliotek四、其它类
5、错箱,铸件沿分型面产生相对位置错移现象。主要是上下抬箱内模型未对准引起。
6、飞边,铸件在分型面边沿呈片状的凸起,主要是上下抬箱为完全密和,有缝隙引起。
Copyright 2004-2011 Aspose Pty Ltd.
第二部分:切削加工
金属切削过程实质
上就是,产生切屑和
形程成。已加工表面E的va过luation only.
ted with A最s具po代s表e.S性l的ide切s for .NET 3.5 Client Profile 5.2
而被钝圆部分挤到已加工表面,这层先受 压应力后又在BC区受到剪应力的金属层即 为已加工表面变质层。
第二部分:切削加工
车削 一、表面粗糙、毛刺多 多与刀刃磨损,切削热,进给速度过快及积
屑瘤及系统振动E大va有lu关at。ion only. ted w二ith、A表sp面o刀se伤.S(li又de称s “fo乱r .刀NE痕T”3):.5退C刀lie时nt在P刀ro刃file 5.2
1、铸造工艺简述及特点 2、常见缺陷及产生原理 3、常见工艺结构
第二部分:切削加E工valuation only. ted w12i、、th普车A遍削性中s加典p工型os缺缺e陷陷.与S工li艺d结e构s for .NET 3.5 Client Profile 5.2
34、、铣磨C削削o中中p典典y型型r缺缺ig陷陷h与与t工工2艺艺0结结0构构4-2011 Aspose Pty Ltd.
2、铸C造op种y类rig很h多t 2,00砂4铸-2是01最1基A本sp最os常e见P的ty方Lt法d.,关
于铸造常见缺陷将重点讲叙砂铸缺陷。
第一部分:铸造
砂铸工艺:
Evaluation only. ted with Aspose.Slides for .NET 3.5 Client Profile 5.2
Copyright 2004-2011 Aspose Pty Ltd.
第一部分:铸造生产
常见缺陷
一、孔眼类
1、气孔,铸件内部及表面都可能分布,特点是孔内部光滑,多呈圆形。注要原因是浇注过程中排 气不畅造成。
2、缩孔与缩松,铸件在冷却时,由于液态和凝固收缩得不到足够的液态金属补充所行成的孔洞为 缩孔。缩孔形状不规则,孔内粗糙,呈倒锥形。成片分散的细小缩孔称缩松,习惯称“针孔”。
Copyright 2004-2011 Aspose Pty Ltd.
削C加o工p是yri车gh削t 、20铣0削4-、2011 Aspose Pty Ltd.
磨削及钻削,下面以
以上四种加工为主介
绍加工中常见的缺陷。
已加工表面变质层:切削表面质量很大程 度上取决于表面表面变质层。切削层金属
流经过切削刃后分为两支,一支成为切屑,
另一支沿后刀面形成已加工表面。在这个
过程中,由于切削刃有一定的钝角,实际 上有△a部分金属不会沿OM滑移成切屑,
5、其它
第三部分:压力加工
1、冷冲压加工 2、热压加工
第四部分:焊接加工
第一部分:铸造生产
1、铸造生产特点 * 能制造各种尺寸和形状复杂的工件 * 铸件形状和尺寸与零件很接近,能节省材料和加 工工时
*原材料来源方便E,va价lu格at低io廉n ,on且ly可. 回收使用。 ted w*i但th也A有sp生o产se工.S序lid较e多s f,or质.N量E不T够3稳.5定C。lient Profile 5.2