手轮机械加工工艺规程
机械加工工艺的流程和注意事项

上下壳的配合定位靠止口保证,凹止口和凸止口的公差一般选单边0.1。通常机械加工工艺外壳大身上的配件(如透明镜)外形比大身上的尺寸单边小0.1—0.2。机械加工工艺配件表面形状如果和大身上的表面形状一致,可以从大身表面上相应位置修剪得到。机械加工工艺定位准确可靠,防止稍有震动便产生误动作。大身上的活动配件(如按钮)外形要比大身上的外形单边小0.1—0.5。便于操作,减少来回走动,避免不必要的动作,例如弯腰、踮脚等机床设备操作件运动方向以及被操作部件运动方向要符合作业规定,并有简易符号标志。手柄、手轮、按钮的结构和排列位置要符合规定。启动按钮应安装在机壳内或装设防止意外触动的护环。机械加工工艺安装在轴杆上的手轮、手柄,在机器自动进刀时,会随轴转动伤人,因此应安装自动脱出装置,保护个人健康。
ቤተ መጻሕፍቲ ባይዱ
对于大批大量生产的工厂,由于机械加工工艺生产组织严密,分工细致,要求机械加工工艺规程比较详细,才能便于组织和指挥生产。除此之外,热加工工程还是对加工精度的影响极大地一种影响,尤其是精密和大件零部件的加工方面,热变形所产生的误差往往会占总误差的百分之四十到百分之七十。除了上面讲到的这些干扰机械加工工艺要素之外。采用机械加工的方法,直接改变毛坯的形状、尺寸和表面质量等,使其成为零件的过程称为机械加工工艺过程。比如一个普通零件加工的工艺流程是粗加工-精加工-装配-检验-包装,就是个加工的笼统的流程。
机械加工工艺的流程和注意事项
在机械加工工艺的理论上为了达到加工零部件精确的表面,需要采用理想的加工原理和精准的成形运动。但在实际工作当中,精确的机械加工工艺原理很难实现,与理想值之间有着很大的差距,如果单一为了追求精准的理论,往往会严重影响加工效率,达不到预期的经济效益。
机械加工工艺流程是工件或者零件制造加工的步骤,采用机械加工的方法。直接改变毛坯的形状、尺寸和表面质量等,使其成为零件的过程称为机械加工工艺过程。比如一个普通零件的加工工艺流程是粗加工-精加工-装配-检验-包装,就是个加工的笼统的流程。其次,机械加工工艺工厂的设计和调度部门根据工艺规程,安排各零件的投料时间和数量,调整设备负荷。各工作地按工时定额有节奏地进行生产等,使整个企业的各科室、车间、工段和工作地紧密配合,保证均衡地完成机械加工工艺生产计划。
机械加工设备安全操作规程

机械加工安全操作规程一、划线1、划线号料工具用完后,应随时放入手提工具箱内,以免划针、划规之尖端刺伤皮肤、咽喉等。
2、冲眼所用的冲子,其尖端要磨好,头部要保持正确形状,不可带有毛刺,以防击碎而崩出裂片伤人。
3、用冲子冲眼,事先要检查锤柄和锤头是否牢固。
4、毛坯加工件带有尖边和毛刺,搬运时戴好手套。
划线区域通道必须畅通,工件必须整齐堆放在专用架上。
5、划线工作须在机床停车后进行,以免划线盘和其他工具被转动机床打翻伤人。
6、在火曲后和有氧化铁皮的钢材上号料时,须用刷子清理切屑,不得用手擦、嘴吹。
7、号料中,用撬棍摆放大型材时,头部躲开撬棍上端,以免击伤;成迭板材号料时,若需人力摆料,应使用撬棍、滚筒等工具,不得直接用手。
二、铆工1、使用大锤时执行“十不打”的规定:⑴劳动防护用品佩戴不好不打;⑵打锤前未仔细检查不打;⑶锤头松动不打;⑷锤头“毛刺”过多不打;⑸锤柄裂纹严重不打;⑹戴手套不打;⑺对面或后面站人不打;⑻周围有妨碍打大锤的障碍物不打;⑼两人用大锤打同一物件时,配合不协调不打;⑽未确认好不打。
2、切料和剁料时,切口正面不得有人,并注意防止飞刺崩人。
3、铲工件时,握铲者应将头部避开并戴好防护眼镜。
4、铆钉前,必须检查铆钉,并在木头上进行试验,确认正常后再行工作;铆钉时,不能以卧头对着他人,操作者戴好耳塞。
5、远距离抛铆钉时,注意四周或过道的行人。
6、受打击的工具须预热后使用;未辨明材料的凉热时,不能用手去拿。
7、使用电钻前,检查马达、电线是否漏电。
三、铣床1、操作时工作服做到“三紧”即“领口紧、袖口紧、下摆紧”;将长发和辫子放在工作帽内;禁止戴围巾和手套。
2、操作前,认真检查铣床各部件及安全装置是否可靠、电器部分是否良好,并检查各部手柄是否处于正常位置。
3、工件、刀具或夹具应牢固夹紧,不得有拨动的现象,防止切削时突然飞出伤人。
4、装卸工件时,应将工作台退到安全位置;使用扳手紧固工件时,用力方向应避开铣刀,以防扳手打滑而使手撞到刀具或夹具上。
机械加工工艺规程

机械加工工艺规程1.主题内容适用范围本规程规定了压力容器中机械零部件加工的有关技术内容。
适用于压力容器中零部件的加工。
2.机械加工的一般技术要求2.1操作人员应熟悉所用机械加工设备、模具、工具、量具的使用性能、结构及维护知识,严格遵守安全操作规程。
钻床、车床、刨床、铣床的操作人员必须经过培训考核合格,取得操作许可证方可上机操作。
2.2设备的精度和能力应符合设备说明书中的规定。
2.3工装、量具与仪表应按规定经周期检定合格。
2.4操作人员要认真做好现场管理工作,对工件、模具、工具应备有相应的工位器具,整齐地放置在指定地点,防止碰损、锈蚀。
3.钻孔3.1钻孔前准备工作3.1.1操作者在操作前必须对设备工装的完好状况按有关要求和标准进行检查和准备所有使用的检具,必须经过鉴定,并在规定的有效期限内。
3.1.2按钻孔要求领用或选用工具和钻杆。
3.1.3准备好冷却用乳化液,检查冷却液箱的乳化液是否充足及供液泵是否正常,乳化液应保证浓度适当,颜色正常,严禁用水冷却以免锈蚀工件及设备,机床所带冷却管道阀门均应畅通。
3.1.4需钻孔的工件划线后,经检验合格后打样冲眼锥夹角90~120°,样冲眼直径应小于2mm,不清晰及冲歪的样冲眼应重新描冲。
3.1.5待钻孔工件表面应清理干净,不准有焊接残渣及其它脏物。
3.1.6工件吊装时禁止碰撞钻床表面。
3.1.7工件应选择合适的工装和装夹位置,工件应装稳、找正、夹牢。
圆柱形工件装夹时必须保证通过待加工孔中心的母线处于最高位置,加工时尽量减少工件移动次数。
3.2钻孔方法及注意事项3.2.1划线钻孔:使钻头对准钻孔中心线,开动钻床先锪窝,锪窝的切削速度为钻孔时的1/2~1/3,一般采用手动进位。
检查是否偏斜,若偏了要进行纠正。
当孔快钻透时,应减小进位量和压力,防止刃具、工件损伤。
3.2.2钻盲孔:与钻通孔的方法相同,但需利用钻床的深度尺来控制钻孔的深度,或在钻头上套定位环或用粉笔作标记,定位环或粉笔标标记高度等于钻孔深度加1/3D(D为钻头直径)。
机械加工操作规程(三篇)

机械加工操作规程第一章总则第一条本规程是根据机械加工工艺和操作要求,制定的操作规程。
第二条本规程适用于机械加工工人。
第三条加工前,应先熟悉加工零件的图纸和加工工艺,掌握所操作设备的结构、性能和操作方法。
第四条加工作业前,应按规程对设备进行检查,检查应包括加工设备电源是否正常,各操作部位是否灵活,加工刀具磨损情况等。
第五条操作时,应按要求使用安全防护装置,严禁戴手套、带卷发或长发等操作。
第六条加工过程中,发现异常情况应及时停机,并向上级报告。
第七条加工完成后,应及时对加工设备进行清洁,刀具归位,加工废料清理完毕。
第二章机床操作规程第八条加工前,应检查机床各操作部位是否灵活,机床轴向、刀具刃部是否有磕碰。
第九条加工过程中,应严禁手放机床上进行加工,禁止用手直接触摸正在运转的主轴、工件、刀具等。
第十条进给运动方向的选择应根据工件的形状和尺寸来确定,并按照正确的进给路径进行操作。
第十一条加工中,严禁调节喷气冷却装置,更换刀具等操作。
第十二条加工结束后,应彻底清洗机床切削液,及时清理加工废料和刀屑,在加工下一个工件之前,应对机床进行保养和维护。
第三章刀具操作规程第十三条加工前,应检查刀具磨损情况,如严重磨损应更换新刀具。
第十四条更换刀具时,应关闭机床电源,并将主轴锁上。
第十五条刀具安装时,应确保刀具刀尖与工件接触时是垂直的,夹持紧固螺母要适度,避免过紧或过松。
第十六条切削过程中,要注意切屑的排出,保证冷却液的喷射。
第十七条刀具分为粗加工刀具和精加工刀具,加工过程中要根据要求进行合理选择。
第十八条加工结束后,要及时清洗刀具,并进行涂油保养,以防刀尖生锈。
第四章加工操作规程第十九条加工前,应检查工件的尺寸和形状,确保符合要求。
第二十条加工过程中,应掌握加工工艺和操作要领,避免出现加工失误。
第二十一条加工过程中,要注意切削力的大小和方向,调整刀具进给量和转速。
第二十二条加工结束后,要对工件进行清洁,严禁在不符合要求的情况下交付。
机械加工安全操作规程

江苏新苏机械制造有限公司安全操作规程编制:审核:批准:2013年2月8日发布2013年2月8日实施安全操作规程安全操作总则1、“安全生产,人人有责”。
所有职工必须认真贯彻执行“安全第一,预防为主”的方针。
严格遵守安全技术操作规程和各项安全生产规章制度。
2、凡不符合安全要求,有严重危险的厂房、生产线和设备、设施,职工有权向上级报告。
遇有严重危及生命安全的情况,职工有权停止操作,并及时报告领导处理。
3、操作人员未经三级安全教育或考试不合格者,不准参加生产或独立操作。
电气、起重、电梯等特种作业人员,均应经安全技术培训和考试合格,持特种作业许可证操作。
外来参观学习人员,亦应接受安全教育并由有关人员带领。
4、进入作业场所,必须按规定穿戴好防护用品。
女工要戴安全帽;操作旋转机床时,严禁戴手套或散开衣袖(襟、;不准穿脚趾及脚跟外露的凉鞋、拖鞋;不准赤脚赤膊;不准系领带或围巾;尘毒作业人员在现场工作时,必须戴好防护口罩或面具;在能引起爆炸的场所,不能穿能集聚静电的服装。
5、操作前,应检查设备或工作场地,排除故障和隐患;确保安全防护、信号联锁装置齐全、灵敏、可靠;设备应定人、定岗操作;对本工种以外的设备,须经有关部门批准,并经培训后方可操作。
6、工作中,应集中精力,坚守岗位,不准擅自把自己的工作交给他人;二人以上共同工作时,必须有主有从,统一指挥;工作场所不准打闹、睡觉和做本职工工作无关的事;严禁酗酒者进入工作岗位。
7、凡运转的设备,不准跨越、横跨运转部位传递物件,不准触及运转部位;不得用手拉、嘴吹切屑;不准站在旋转工件或可能爆裂飞出物件、碎屑部位的正前方进行操作、调整、检查、清扫设备;装卸、测量工件或需要拆卸防护罩时,要先停电关车;不准无罩或敞开防护罩开车;工作完毕或中途停电,应切断电源,才准离岗。
8、修理机械、电气设备或进入其工作前,必须在动力开关处挂上“有人工作,严禁合闸”的警示牌。
必要时设人监护或采取防治以外接通的技术措施。
机械加工工艺过程介绍
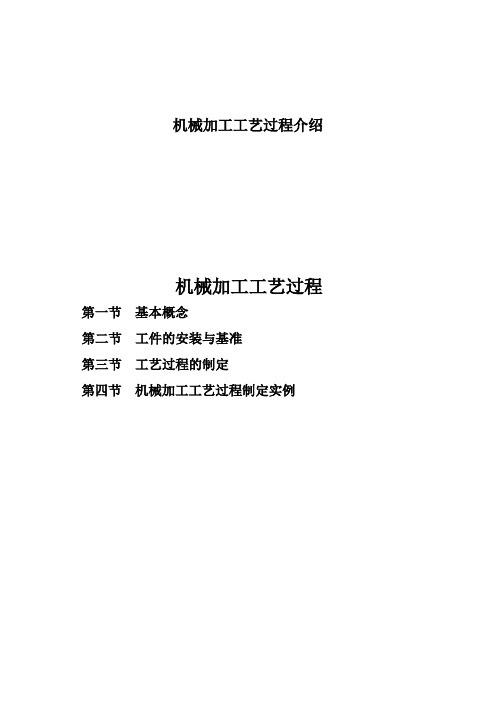
机械加工工艺过程介绍机械加工工艺过程第一节基本概念第二节工件的安装与基准第三节工艺过程的制定第四节机械加工工艺过程制定实例§6.1 基本概念一、工艺过程生产过程中直接改变原材料的性能、尺寸与形状、使之变为成品的过程称之工艺过程工艺过程由一系列工序、安装、工位、工步与进给等构成。
二、生产过程在机械制造中,从原材料到成品之间各个相互关联的劳动过程的总与,称之生产过程.生产过程实际上是由原材料到成品之间各个相互关联的劳动过程的总与。
三、生产纲领与生产类型1、生产纲领工厂或者产品的生产纲领是指包含备品与废品在内的该产品的年产量。
零件的生产纲领可按下式计算:式中,N 为零件的生产纲领(件/年);Q 为机器产品的年产量(台/年);n 为每台机器中该零件的数量(件/台);a 为备件百分率(%);β为废品百分率(%).2、生产类型单件生产、大量生产与成批生产)1)(1(βα++=Qn N§6.2 工件的安装与基准工件的安装直接找正安装划线找正安装使用夹具安装二、工件的定位(一)六点定位原则机床夹具物体的六个自由度一个物体在空间能够有六个独立运动。
以右图为例,它在直角坐标系OXYZ 中能够有三个平移运动与三个转动。
三个平移运动分别是沿X 、Y 、Z 轴平移运动,记为Z Y X \\三个转动分别是绕X 、Y 、Z 轴的转动,记为Z Y X //习惯上把六个独立运动称作六个自由度,假如使用一定的约束措施,消除物体的六个自由度,则物体被完全定位六点定位原理任何一个物体在空间直角坐6个自由度——用Z Y X Z Y X ,,,,,表示。
要确定其空间位置,就需要限制其 6 个自由度将 6 个支承抽象为6个“点”,6个点限制了工件的6 个自由度,这就是六点定位原理。
X自由度示意图ZYX六点定位原理图(二)六点定则的应用完全定位不完全定位超定位(三)工件的基准基准的概念:是在确定零件上其他面、线或者点的位置准确度时所根据的该零件上的面、线或者点。
1.机械加工类通用安全操作规程

机械加工类通用安全操作规程FDJ·AG—01·01—2012 1 目的为规范本企业机械加工类人员的安全操作行为,控制人、机、环的不安全因素,避免伤害事故的发生,特制定本规程。
凡机械加工类操作人员必须严格遵守。
2 适用范围本规程适用于本企业各类车床、铣床、刨床、插床、磨床、钻床、锯床、数控机床、镗床等设备操作人员。
3 危险因素及伤害方式3.1 机械的不安全状态引起的伤害3.1.1 机械静止时的危险机械静止的危险是指设备处于静止状态时,当人接触或与静止设备作相对运动时可引起的机械伤害。
它主要包括以下几种:a) 切削刀具的刃口。
b) 设备突出或较长的机械部分。
c) 毛坯、工具、设备边缘及锋利飞边。
3.1.2 机械旋转运动时的危险主要指人体或衣服卷进旋转机械部位引起的伤害。
a) 卷进旋转运动机械部件中的危险,如主轴、卡盘、卡盘爪、进给丝杠等单独旋转的机械部件以及各种切削刀具、圆锯、铣磨工具等。
b) 卷进旋转机械部件与直线运动部件间的危险,如皮带与皮带轮、链条与链轮、齿条与齿轮等。
c) 旋转运动加工件及其上凸出物打击或绞轧的危险,如伸出机床的细长加工件,及转轴上的键、销铁、定位螺丝、联轴器螺丝等。
d) 旋转运动的手轮、手柄、摇臂及设备上其它旋转部位,可对人体造成打击、缠绕伤害等。
3.1.3 机械直线运动的危险它是指人体被直线运动的机械部位撞击引起的伤害。
a) 滑枕直线往复运动,横梁、刀架垂直或水平运动,对人身造成的挤压、撞击伤害。
b) 主传动箱、进给箱、工作台等直线运动,对人体造成的挤压、撞击伤害,并可造成高处坠落伤害。
c) 带锯、弓锯直线运动及其它直线运动,对人身造成割伤、撞击伤害。
3.1.4 机械飞出物击伤的危险a) 飞出的刀具或机械部件,如未夹紧的刀具、卡盘、螺栓、螺帽、销铁、垫板、砂轮片等。
b) 飞出的铁屑或工件、电机三角带、连轴器、弓锯碎片、带锯碎片等,对人体造成割伤、刺伤等伤害。
JIER机械加工工艺原则、工艺代码

二、生产制造单位及主要相关职能
(四)铸造公司
铸造零件工艺编制 铸造毛坯: 灰铸铁:零件重量≤45t,最大宽或高尺寸≤4500mm 球墨铸铁:零件最大重量≤35t,最大宽或高尺寸≤4500mm 有色金属离心浇注:最大外圆直径Ф ≤1380,毛坯长度L≤1200,毛坯重量 G≤1500Kg。
钒钛耐磨铸铁、铬钼铜耐磨铸铁、铬铜耐磨铸铁
精加工零件库房
二、生产制造单位及主要相关职能
(八)压力机及自动化公司
压力机及自动化产品的设计 装配一部:承担400T~800T压力机的装配。 装配二部:承担800T以上压力机的装配。 装配三部:承担400T以下压力机的装配。 装配五部:承担自动化产品的装配。
二、生产制造单位及主要相关职能
(九)数控机床公司
二、生产制造单位及主要相关职能
(一)生产制造单位
生产安全 部
物资公司
铸造公司
焊接与锻 热公司
机械加工 公司
数控机床 公司
铸造与切 割设备公 司
物流中心
质量管理 部理化中 心
压力机及 自动化公 司
二、生产制造单位及主要相关职能
(二)生产安全部:工时制定、订单下达
(三)物资公司
型材料供应:所有金属与非金属型材料,如尼龙材料、夹布塑料、钢板、圆 钢、角钢、槽钢等。
数控机床产品的设计
装配作业一部:承担金切机床中的定梁数控龙门铣床、龙门刨床等的装配。 装配作业二部:承担动梁数控龙门铣床等的装配。 装配作业三部:间承担数控机床中的功能部件(铣头、刀库)等的装配。 装配作业四部:承担落地镗铣床的装配 特殊说明:近期,数控机床的一些作业部帮助压力机公司装配压力机(技术问题处理时 注意)。 (十)铸造与切割设备公司 铸造与切割设备设计、工艺路线划分、装配 (十一)理化中心 探伤(超声波探伤、表面涡流探伤、表面着色探伤),硬度检验
- 1、下载文档前请自行甄别文档内容的完整性,平台不提供额外的编辑、内容补充、找答案等附加服务。
- 2、"仅部分预览"的文档,不可在线预览部分如存在完整性等问题,可反馈申请退款(可完整预览的文档不适用该条件!)。
- 3、如文档侵犯您的权益,请联系客服反馈,我们会尽快为您处理(人工客服工作时间:9:00-18:30)。
毕业设计说明书手轮机械加工工艺规程目录第一部分工艺设计说明书 (3)第二部分工序夹具设计说明书 (15)第三部分工序刀具设计说明书 (17)第四部分工序量具设计说明书 (19)第五部分毕业设计体会 (20)第六部分参考资料 (21)第一部分工艺设计说明书一、零件图工艺性分析1、零件结构功用分析横进给手轮是进给机构中用来传递动力的一个零件,其主要加工的是与手轮轴进行配合的孔,还有与中间体进行连接的端面和外圆。
2、零件技术条件分析由于毛坯是铸件,因此加工前需要进行时效处理,3、零件结构工艺性分析零件图样中的视图、尺寸、公差和技术要求都选择的很合理,材料选择HT150,结构工艺性良好。
尺寸精度:φ8H9,φ8H9都是H7的精度等级,要求较高,表面粗糙度:其中φ8的表面粗糙度为0.8um需要精铰才能达到,φ130的端面、外圆表面粗糙度为1.6um需要精车,其它各孔和面均为3.2um、6.8um等。
热处理:对于铸件在加工前需要进行时效处理以便消除内应力二、毛坯选择1、毛坯类型由材料可确定毛坯为铸件,其零件所要求的力学性能不高,且内腔形状复杂外形尺寸较大,又属于中批量生产,所以毛坯的铸造方法选用砂型机器造型,根据《机械制造工艺及设备设计指导手册》查的铸件的公差等级采用CT10级2、毛坯余量确定由于此零件为中批量生产,再根据《金属机械加工工艺人员手册》可查得它各表面的加工余量。
底面:基本尺寸为130,加工余量等级为MA-G,查表可得其单侧加工余量为8mm侧面:基本尺寸为100,双侧加工时单侧加工余量为3.5mm顶面:基本尺寸为130,它的加工余量等级比底面和侧面低一级,查得它的单侧加工余量为5mm孔:孔的加工余量等级与顶面的相同,所以可查得它的单侧加工余量为3mm根据铸件的基本尺寸和公差等级查出铸件的尺寸公差,确定出它的毛坯尺寸。
3、毛坯-零件合图草图三、机加工工艺路线确定1、加工方法分析确定要按照先加工基准面,先面后孔、先粗后精的原则来确定。
主要表面的加工方法:φ130的环形面和φ130的圆柱端面与外圆公差等级按IT18级算,表面粗糙度为1.6um,需要进行粗车,半精车,精车(成形车刀)φ51的内孔表面粗糙度为3.2um,粗扩,精扩。
φ8H7,表面粗糙度为1.6um,精度等级较高需要钻,精铰。
φ8H7,表面粗糙度为0.8um,钻,扩,粗铰,精铰。
φ18x9的台阶孔要钻孔和锪孔可达到。
φ28的台阶面,φ108的环形孔和φ70的台阶孔都需要粗车,半精车,精车。
3、加工顺序的安排工序01 .:铸造工序03. :热处理工序05 :以φ130mm外圆端面定位,粗车φ130端面外圆,粗车φ28mm的台阶面、粗车φ70m的台阶孔。
工序07:以粗车后的φ130mm外圆及端面定位,粗车φ130端面外圆、粗车φ108环形槽,粗镗孔φ51mm 工序09:检验工序11:以粗车后的φ130mm外圆及端面定位,半精车φ130端面外圆,半精车φ28mm的台阶面、半精车φ70mm的台阶孔。
工序13:以半精车后的φ130mm外圆及端面定位,半精车φ130mm外圆端面,工序17:以φ130底面定位,钻φ8H7,同时扩和粗铰φ8H7的孔工序19:钻φ8H7的孔,工序23:以φ130的底面,φ51和φ9的孔定位,锪φ55x18的盲孔工序25:以φ130的底面定位,先锪φ22的圆平面,再钻,攻M8的螺纹孔工序26:检验工序27:以φ130mm端面及外圆定位,精车φ130的端面外圆,精车φ108的环形槽工序29:以φ130mm外圆及端面定位,用成形车刀车φ130的环形面,精车φ28台阶面工序31.精铰φ8H7和φ8H7的孔工序33:去毛刺工序35:终检。
3、定位基准选择(1)精基准的选择本零件的设计基准是外圆与端面,所以采用外圆和端面作为定位基准可以避免基准部重合产生的误差,所以选用φ130的端面和外圆作为精基准。
(2)粗基准的选择对于零件而言,尽可能选择不加工表面为粗基准。
由于零件是以φ130外圆端面为精基准的,所以应选另一端的外圆和端面作为粗精准做出精基准,即选用φ130的端面和外圆作为粗基准。
8、加工阶段的划分说明加工阶段分为:粗加工阶段、半精加工阶段、精加工阶段。
(1.)粗加工阶段:a.毛坯退火热处理 b.粗加工,粗车φ130外圆,粗车φ28台阶面,粗车φ130外圆,粗车φ108的环形孔,粗镗φ51孔、φ70的台阶孔。
目的:切除大部分余量,把毛坯加工至接近零件的最终形状和尺寸,只留下少许加工余量,通过这个阶段还可以及时发现铸件的一些缺陷。
(2.)半精加工阶段:a.半精车φ130外圆,半精车φ28台阶面,半精车φ130外圆,半精车φ108的环形孔,精镗φ51孔,半精镗φ70的台阶孔。
目的:切除小部余量,使毛坯各类尺寸及各项要求很接近零件的最终尺寸和技术要求。
(3.)精加工阶段:精车外圆端面及成形面、精精加工各台阶面及台阶孔目的:达到零件设计要求。
5、主要机加工工序简图01.铸造03.热处理05.粗车φ130端面外圆,粗车φ28的台阶面,粗车φ70的台阶孔07.粗车φ130端面外圆,粗扩φ51的孔,粗车φ108的环形槽09.检验11.半精车φ130端面外圆,半精车φ28的台阶面,半精镗φ70的台阶孔13.半精车φ130端面外圆,半精车φ108的环形槽,精扩φ51的孔17.钻扩粗铰φ15.95的孔19.钻3个φ9的孔,扩孔至φ18x9的台阶孔21.钻φ3.9x9的盲孔23.锪φ55x18的盲孔25.锪φ22的圆平面,钻、攻M8的螺纹孔26. 检验27.精车φ130端面外圆,精车φ108的环形孔29.精车φ130的成型面,精车φ28的台阶面,精镗φ70的台阶孔31.精铰φ8H7和φ8H7的孔33.钳工去毛刺38.检验四、工序尺寸及其公差确定五、设备及其工艺装备确定1、选择机床(1)工序05 、07 、11、13是粗车和半精车。
选用卧式车床就能满足要求。
本零件尺寸不大,精度要求不高,选用最常用的CA6180型卧式车床即可。
(2)工序17、19、21、23,25,31钻孔,铰孔,锪平面和孔。
可采用专用的分度夹具在立式钻床上加工,可选用Z3025型摇臂钻床。
(3)工序27,29是精车,选用最常用的CA6180型卧式车床。
2、选择夹具本零件除钻削加工需设计专用夹具,其他工序使用通用夹具即可,车床上用三爪自定心卡盘。
3、选择刀具①在车床上加工的工序,一般都用硬质合金车刀和镗刀,加工灰铸铁零件采用YG型硬质合金,粗加工用YG6,半精加工用YG8,精加工用YG10。
②钻孔用麻花钻,攻螺纹用丝锥。
8、选择量具外圆用游标卡尺测量,内孔用塞规。
六、切削用量及工时定额确定工序05 切削用量及工时定额的确定1.切削用量mm外圆的切削用量所选刀具为YG6硬质合金可转位车刀,根《切削用量简明手册》①确定φ1300046-.0表1.1,由于CA6180机床的中心高为130mm,故选用刀杆尺寸B×H=8mm×25mm,刀片厚度为8.5mm根据《切削用量简明手册》表1.3,选择车刀几何形状为卷槽带倒棱型前刀面,前角γo=5°,后角αo=8°、主偏角Kr=90°、,副偏角Kr’=5°、刃倾角λs=-10°、刀尖圆弧半径εr=2mm。
②确定切削深度a p由于粗车单边余量仅为3mm,可一次走刀完成.③确定进给量f 根据表1.8,在粗车灰铸铁、刀杆尺寸为8 mm×25 mm、a p≤3 mm、工件直径为100 mm ——800 mm时,f=0.8 mm/r2.基本时间①确定粗车外圆φ130mm的基本时间根据表6.2-1车外圆基本时间为V=72.3,n=95r/min, a p =3mm,f=0.8mm/r,则T1=0.61min第二部分工序夹具设计说明书1.工序尺寸精度分析由工序图知,本道工序用来钻M8的螺纹孔,孔的加工及尺寸精度要求不高,该工序在钻床加工,零件属于中批量生产,所以主要考虑的是夹具的制造工艺简单。
限制自由度分析:孔在圆周上分布,为了保证此要求,因为钻头沿轴向切削,不会引起工件在轴向上的转动,所以应限制6个自由度就行,X移动.X转动.Y移动 .Y转动.Z移动. Z转动2.定位方案确定由零件图可知,加工本道工序需要限制6个自由度,前道工序已将Φ8的孔钻好,所以采用一心轴和一菱形销与一面定位就能达到要求。
Φ130外圆端面布大平面,限制Z 移动.X 转动.Y 转动。
Φ108孔与φ8的孔: X 移动..Y 移动 .Z 转动.综合结果实际限制:X 移动.X 转动.Y 移动 .Y 转动.Z 移动. Z 转动 故此定位方案可行。
3.定位元件的设计过程1.布置销位:心轴布在φ108孔的位置,φ8布置菱形销2.确定销间距:L ±△j= L ±1/2△k=89±0.07/2=89±0.0353.确定圆柱销直径: d1=D1g6=108012.0034.0--Φ△1=0.088.确定菱形销的直径:查表2.1可知b=8,所以,△2=2b/D2(△k+△j+△/2)=0.089d2=(D2-△2)h6=16049.006.0--8.定位误差分析计算由以上可知 △1max=0.056,△2max=0.071分析尺寸96的定位误差:基准不重合误差: 因钻孔时,定位基准为心轴的中心线,工序基准也为心轴的中心线。
故:△jb=0基准位移误差:△db=△D1+△d1+△1=0.022+0.022+0.08=0.056 定位误差: △dw=△jb+△db=0+0.056=0.056故:△dw ≤1/3T=0.18对平行方向的尺寸:△jb=0△db 应该是上下平移△db1转动角度后最大:△db1=0.056, ±tg θ2=±(△2max-△1max )/2x89=±0.00015 △db=△db1+2x96x0.00015=0.085 所以,△dw=△jb+△db=0.085≤1/3T5.夹紧方案及元件确定根据工件定位方案考虑夹紧力作用点及方向。
如图所示采用螺母,螺杆与开口垫圈组合对工件进行夹紧,钻模板通过心轴与夹具体连接定位,所以加紧力与切削力互相平行。
6. 确定夹具体结构采用铸件整体式7. 绘制总装图、标注尺寸、写技术要求。
第三部分设计说明书(铰Φ8 H9内孔)一已知条件1.被加工孔直径:Φ8 H9(+0.018) Ra0.8 Dw=82.工件材料:HT150 铰削长度为26mm3.预制孔直径: Dw1=15.85mm8.使用机床:Z3025二铰刀设计过程:第四部分工序量具设计说明书1.工序尺寸精度分析尺寸精度等级达到7级。