药品生产过程质量风险评估报告
药品生产过程质量风险评估报告模板

药品生产过程质量风险评估报告模板XXXX胶囊生产过程质量风险管理报告起草人:审核人:审核人:批准人:质量风险管理号:QRM-起草日期:审核日期:审核日期:批准日期:XXXX药业有限公司年月年月年月年月日日日日目录XXXX胶囊生产过程质量风险管理报告1、简介2、目的3、范围4、引用资料5、风险管理小组组员及职责分工6、质量风险管理流程7、风险管理过程8、风险管理总结及结论9、风险管理回顾审核XXXX胶囊生产过程质量风险管理报告1.简介:产品概述:XXXX胶囊为以化学原料药XXXX和适量等辅料制成的化学药胶囊剂制剂,为耳鼻喉科及皮肤科用药类非处方药药品。
用于缓解过敏性鼻炎有关的症状,如喷嚏、流涕、鼻痒、鼻塞以及眼部痒及灼烧感。
口服药物后,鼻和眼部症状及体征得以迅速缓解。
亦适用于缓解慢性荨麻疹、瘙痒性皮肤病及其他过敏性皮肤病的症状和体征。
规格为10 毫克;贮藏:遮光,密闭保存;包装:铝塑泡罩包装。
每板6粒,每盒1板;每板6粒,每盒2板;每板12粒,每盒1板,每板4粒,每盒1板。
有效期:30个月。
生产批量:35万粒,140万粒。
主要生产工艺过程及参数:过筛:取XXXX、乳糖、硬脂酸镁及羟丙纤维素分别过100目筛。
预混合:批量为35万粒用SYH-200型三维运动混合机进行,混合速度900转/分,混合时间20分钟;批量为140万粒的预混合和35万粒相同,但原辅料均分4等分进行4次混合。
粘合剂15%聚维酮K30的乙醇溶液的配制:按聚维酮K30:95%乙醇量=:(重量比)进行配置,溶解完全100目滤布过滤。
制软材:上述预混合好的细粉,用GHL-250型高效混合制粒机中(每次35万粒量),设定混合I和切割I开动设备混合10分钟后,徐徐加入粘合剂(15%聚维酮K30的乙醇溶液),加完后继续混合3-4分钟,收集软材。
制粒:用YK-160型摇摆式颗粒机制粒,筛网目数为24目。
干燥:湿颗粒用GFG-120型高效沸腾干燥机干燥,每次干燥量为35万粒胶囊的颗粒量,控制干燥温度为50℃~70℃,干燥时间20分钟。
质量风险评估报告
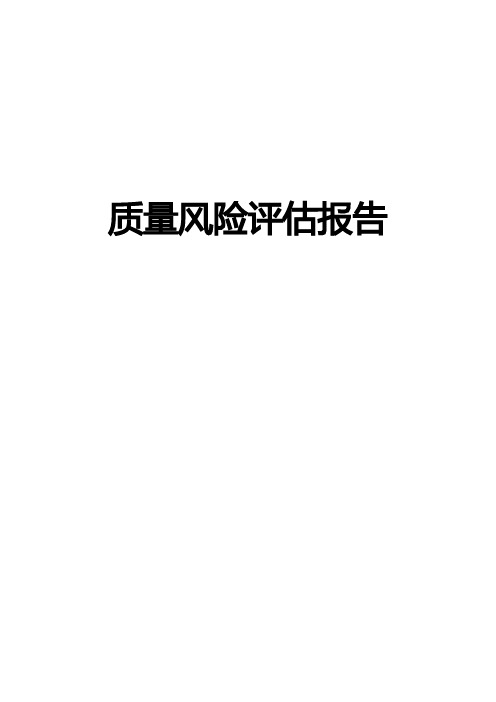
为有效加强药品质量管理,降低药品在经营环节中浮现的安全事 件的风险, 更好地维护人民群众身体健康和生命安全, 我公司成立了 以企业质量负责人为组长, 各业务部门负责人为成员的药品经营质量 风险排查领导小组,于 2022 年 9 月 21 日至 24 日对我公司药品的采 购、收货、验收、贮存、养护、销售、出库复核、运输等全过程和人 员、职责、制度全方位进行了两次风险排查与评估,具体情况报告如 下:一、建立风险评估的组织领导小组,明确职责和任务我公司成立了质量风险评估小组,明确了职责和任务,对我公司 药品的采购、收货、验收、贮存、养护、销售、出库复核、运输等全 过程和人员、设备、制度、环境四要素中可能存在的风险进行排查和 评估。
职责组织成立质量风险评估小组,提供风险管理所需的资源,批准风险管理计划,批准风险管理报告。
1 、起草风险评估方案;2 、参预风险识别、分析、制定控制措施及执行; 3、负责风险评估报告的汇总、 起草。
4、组织风险评估小组进行风险识别、评估, 提出风险控制实施方案, 报风险管理负责人批准后, 推动控制方案的执行,落实风险沟通。
参预质量控制过程中风险的识别、评估,提出控制措施,对本次风险评估报告得出的控制措施予以执 行部门 质量负责人质管部经理各部门经理职务组长组员组员 姓 名二、对公司全年经营品种进行统计分析,查找经营过程中的质量问题及风险我们对2022 年6 月1 日至2022 年6 月30 日的所有经营产品的品种和存在的质量问题进行了统计、分析,特殊对浮现质量问题的品种,分析了浮现问题的原因(附件1),制定了整改措施。
对可能浮现的质量风险,按采购、收货、验收、贮存、养护、销售、出库复核、运输的工作流程,从人员、设备、制度、环境四个方面进行了分级查找和自审(附件2),找出了质量风险点 5 条。
三、按风险指数矩阵图要求对每一个风险点进行分析运用实用的信息和风险指数矩阵图要求,对已经识别每一个风险点和问题进行分析,估计影响的因素、范围、关联、趋势;确认将会出现问题的可能性有多大?浮现的问题是否能够及时地发现?以及造成后果的严重性如何?发生可能性第1 级希少(发生频次小于每十年一次)第2 级不太可能发生(发生频次为每五至十年一次)第3 级可能发生(发生频次为每一至五年一次)第4 级很可能发生(发生频次为约每年一次)第5 级较常发生(发生频次约为每2-3 个月1 次)第6 级时常发生(几乎每次都可能发生)四、开展风险评价,确定风险级别根据预先确定的风险标准,对已经识别并分析的风险进行评价:1、风险评价的标准:根据风险发生的可能性和严重性,用风险指数矩阵图来综合评价风险的等级。
药品生产过程中的质量风险评估与控制效果评估

药品生产过程中的质量风险评估与控制效果评估药品的生产过程中,质量风险评估和控制效果评估是非常重要的环节。
通过对药品生产过程进行评估,可以有效降低质量风险,并确保生产出符合质量标准的药品。
本文将介绍药品生产过程中的质量风险评估与控制效果评估的方法和重要性。
一、质量风险评估质量风险评估是指对药品生产过程中可能存在的质量风险进行全面评估和分析。
其目的是确定可能出现的风险,并采取相应的控制措施以降低风险发生的概率。
质量风险评估可以从以下几个方面进行:1. 原材料风险评估:对原材料进行检查和评估,确保其符合质量要求,同时评估原材料可能带来的潜在风险。
2. 制造工艺风险评估:评估制造工艺的合理性和风险性,包括工艺步骤、操作规范、设备设施等方面,以确定潜在的风险并采取相应的控制措施。
3. 环境条件风险评估:评估生产环境的清洁度、温湿度控制等条件,确保符合药品生产的标准,并降低环境条件对药品质量的不利影响。
4. 检测方法风险评估:评估药品的检测方法的准确性和可靠性,确保检测结果的准确性,并防止检测方法可能带来的误判。
二、控制效果评估控制效果评估是指对已经采取的控制措施的有效性进行评估和验证。
通过控制效果评估,可以判断已采取的措施是否有效,并进一步完善和改进控制策略。
控制效果评估可以从以下几个方面入手:1. 检测方法验证:对已采取的检测方法进行验证,确保其准确性和可靠性。
验证结果应与已知标准进行对比,以判断检测方法的有效性。
2. 生产过程监控:对生产过程中关键环节进行监控,确保操作规范的执行和质量控制的有效性。
如对温度、湿度、压力等参数进行实时监测,并对异常情况进行及时处理。
3. 质量管理体系审核:对质量管理体系进行定期的内部审核和外部审核,评估质量管理体系的有效性,并及时发现和纠正存在的问题。
三、质量风险评估与控制效果评估的重要性质量风险评估和控制效果评估对药品生产过程的质量管理和控制具有重要意义。
其重要性主要表现在以下几个方面:1. 提高生产效率:通过准确评估质量风险和控制效果,可以合理安排生产中的各个环节,避免不必要的质量问题和生产延误,从而提高生产效率。
药品安全质量风险评估报告

药品安全质量风险评估报告药品安全质量风险评估报告1. 背景介绍本报告旨在对药品的安全质量风险进行评估,以确保药品的安全性和质量的合规性。
评估将从药品的生产、质量控制、销售和使用等环节进行全面分析,以识别潜在的风险和问题,并提出相应的控制和改进措施。
2. 评估方法评估将采用定性和定量相结合的方法,包括以下几个方面:- 药品生产环节的生产工艺、原材料采购、生产设备等是否符合药品安全和质量要求;- 药品质量控制环节的检测方法、检测设备、检测人员等是否具备有效性和可靠性;- 药品销售渠道和流通环节是否存在假冒伪劣药品、过期药品等问题;- 药品使用环节的合理用药和不良反应反馈情况等。
3. 评估结果根据评估的结果,将对药品安全质量存在的风险和问题进行分类和分级,提出相应的控制和改进建议。
- 高风险问题:对存在重大风险和严重影响人体健康或生命安全的药品进行优先处理,包括产品召回、停止生产和销售等;- 中风险问题:对存在一定风险但尚未造成严重影响的药品进行整改和监管,加强监管力度和提升质量控制水平;- 低风险问题:对存在较小风险和问题的药品进行改进和监测,提出相应的改进建议并持续监测。
4. 控制和改进措施根据评估结果,制定相应的控制和改进措施,包括但不限于以下几个方面:- 加强药品监管的法规和制度建设,提升监管部门的执法能力和监管水平;- 完善药品质量控制的标准和规范,保证药品生产和质量控制环节的合规性;- 加强药品销售渠道和流通环节的监管,严厉打击假冒伪劣药品和过期药品的违法行为;- 提升药品使用环节的管理和监督,加强合理用药的宣传和教育,及时反馈药品的不良反应情况。
5. 结论本评估报告对药品安全质量风险进行了全面的评估和分析,并提出了相应的控制和改进措施。
评估结果显示当前存在一定的风险和问题,但整体药品安全质量情况仍然具备可控的局面。
为了保障人民群众的用药安全和健康,在各相关部门和企事业单位的共同努力下,我国的药品安全质量水平将会不断提升。
药品生产过程质量风险评估报告

XXXX胶囊生产过程质量风险管理报告质量风险管理号:QRM-起草人:起草日期:年月日审核人:审核日期:年月日审核人:审核日期:年月日批准人:批准日期:年月日XXXX药业有限公司目录XXXX胶囊生产过程质量风险管理报告1、简介2、目的3、范围4、引用资料5、风险管理小组组员及职责分工6、质量风险管理流程7、风险管理过程8、风险管理总结及结论9、风险管理回顾审核XXXX胶囊生产过程质量风险管理报告1.简介:1.1产品概述:XXXX胶囊为以化学原料药XXXX和适量等辅料制成的化学药胶囊剂制剂,为耳鼻喉科及皮肤科用药类非处方药药品。
用于缓解过敏性鼻炎有关的症状,如喷嚏、流涕、鼻痒、鼻塞以及眼部痒及灼烧感。
口服药物后,鼻和眼部症状及体征得以迅速缓解。
亦适用于缓解慢性荨麻疹、瘙痒性皮肤病及其他过敏性皮肤病的症状和体征。
规格为10 毫克;贮藏:遮光,密闭保存;包装:铝塑泡罩包装。
每板6粒,每盒1板;每板6粒,每盒2板;每板12粒,每盒1板,每板4粒,每盒1板。
有效期:30个月。
1.2生产批量:35万粒,140万粒。
1.3主要生产工艺过程及参数:1.3.1过筛:取XXXX、乳糖、硬脂酸镁及羟丙纤维素分别过100目筛。
1.3.2预混合:批量为35万粒用SYH-200型三维运动混合机进行,混合速度900转/分,混合时间20分钟;批量为140万粒的预混合和35万粒相同,但原辅料均分4等分进行4次混合。
1.3.3 粘合剂15%聚维酮K30的乙醇溶液的配制:按聚维酮K30:95%乙醇量=1.5:8.5(重量比)进行配置,溶解完全100目滤布过滤。
1.3.4制软材:上述预混合好的细粉,用GHL-250型高效混合制粒机中(每次35万粒量),设定混合I和切割I开动设备混合10分钟后,徐徐加入粘合剂(15%聚维酮K30的乙醇溶液),加完后继续混合3-4分钟,收集软材。
1.3.4制粒:用YK-160型摇摆式颗粒机制粒,筛网目数为 24目。
药品质量风险评估报告
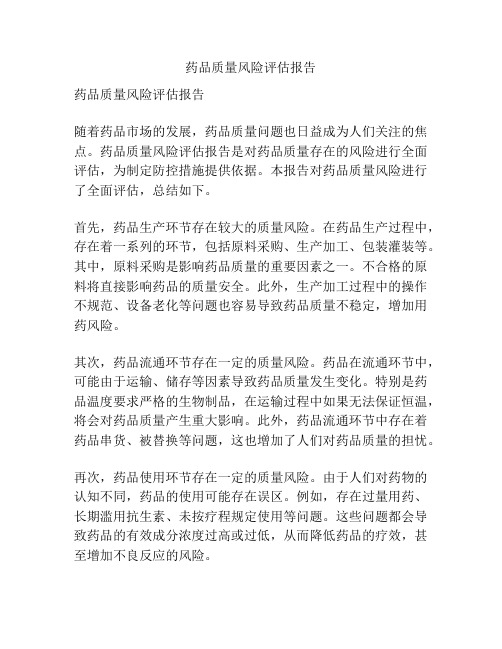
药品质量风险评估报告药品质量风险评估报告随着药品市场的发展,药品质量问题也日益成为人们关注的焦点。
药品质量风险评估报告是对药品质量存在的风险进行全面评估,为制定防控措施提供依据。
本报告对药品质量风险进行了全面评估,总结如下。
首先,药品生产环节存在较大的质量风险。
在药品生产过程中,存在着一系列的环节,包括原料采购、生产加工、包装灌装等。
其中,原料采购是影响药品质量的重要因素之一。
不合格的原料将直接影响药品的质量安全。
此外,生产加工过程中的操作不规范、设备老化等问题也容易导致药品质量不稳定,增加用药风险。
其次,药品流通环节存在一定的质量风险。
药品在流通环节中,可能由于运输、储存等因素导致药品质量发生变化。
特别是药品温度要求严格的生物制品,在运输过程中如果无法保证恒温,将会对药品质量产生重大影响。
此外,药品流通环节中存在着药品串货、被替换等问题,这也增加了人们对药品质量的担忧。
再次,药品使用环节存在一定的质量风险。
由于人们对药物的认知不同,药品的使用可能存在误区。
例如,存在过量用药、长期滥用抗生素、未按疗程规定使用等问题。
这些问题都会导致药品的有效成分浓度过高或过低,从而降低药品的疗效,甚至增加不良反应的风险。
为了降低药品质量风险,我们建议从以下几个方面进行改进:一是加强药品生产过程的质量管控。
应加强对药品生产企业的监管,确保其按照药品质量标准进行生产加工。
同时,完善监管体系,加大对药品原料的抽检力度,确保原料的合格率。
二是加强药品流通过程的监管。
应建立完善的药品流通追溯体系,确保药品在运输、储存等过程中符合质量要求。
加强对药品经销商的监管,严禁药品串货、被替换等违规行为。
三是加强药品使用过程的宣传教育。
通过加强对公众的用药指导,提高人们对药品的正确使用意识。
加强对医务人员的培训,提高其对药品的合理用药知识,减少用药误区。
综上所述,药品质量问题是一个复杂的系统工程。
通过对药品质量风险进行评估,可以及时发现问题,采取相应的防控措施。
药品生产安全风险评估

药品生产安全风险评估
药品生产安全风险评估是指对药品生产过程中可能存在的各种安全风险进行评估和分析,以确定风险的严重程度,并采取相应的控制措施来降低风险发生的可能性和影响。
药品生产过程中可能存在的安全风险包括但不限于以下几个方面:
1. 原料和辅料的安全性风险:原料和辅料的质量不合格、含有有害物质或微生物污染等情况可能存在安全风险,可能导致药品的质量问题和不良反应。
2. 生产工艺和设备的安全风险:生产工艺和设备存在不合理、不稳定或不安全的设计,可能导致生产过程中的事故和事故风险,例如爆炸、火灾等。
3. 工人操作的安全风险:工人在生产过程中的操作不规范、缺乏培训和安全意识等问题可能导致事故和职业伤害的发生。
4. 管理和监督控制的安全风险:药品生产中缺乏有效的管理制度和监督控制措施,可能导致生产环境不合格、质量问题被忽视等情况发生。
为了对上述安全风险进行评估,可以采取以下步骤:
1. 风险识别和分类:对药品生产过程中可能存在的各类风险进行识别和分类,包括原料和辅料安全、生产工艺和设备安全、工人操作安全和管理控制安全等。
2. 风险评估和分析:对已识别的风险进行评估和分析,包括确定风险的严重程度、可能性和影响等因素,以便确定重点关注的风险。
3. 风险控制措施的制定:根据风险评估的结果,制定相应的风险控制措施,包括采取技术措施、管理措施和培训措施等,以降低风险发生的可能性和影响。
4. 风险监控和评估:实施控制措施后,需要对风险的监控和评估,以确定是否有效控制了风险,并及时对措施进行调整和改进。
最后,药品生产安全风险评估需要遵守相关的法律法规和标准,确保评估的准确性和可靠性,并及时报告和处理评估结果中发现的问题和风险。
药品生产企业的质量风险评估
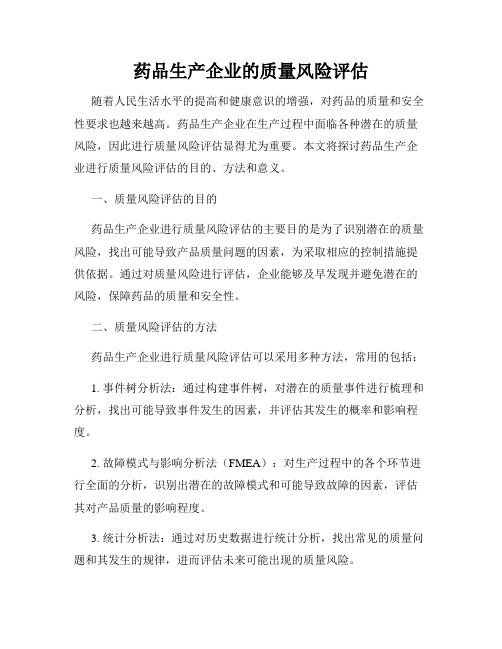
药品生产企业的质量风险评估随着人民生活水平的提高和健康意识的增强,对药品的质量和安全性要求也越来越高。
药品生产企业在生产过程中面临各种潜在的质量风险,因此进行质量风险评估显得尤为重要。
本文将探讨药品生产企业进行质量风险评估的目的、方法和意义。
一、质量风险评估的目的药品生产企业进行质量风险评估的主要目的是为了识别潜在的质量风险,找出可能导致产品质量问题的因素,为采取相应的控制措施提供依据。
通过对质量风险进行评估,企业能够及早发现并避免潜在的风险,保障药品的质量和安全性。
二、质量风险评估的方法药品生产企业进行质量风险评估可以采用多种方法,常用的包括:1. 事件树分析法:通过构建事件树,对潜在的质量事件进行梳理和分析,找出可能导致事件发生的因素,并评估其发生的概率和影响程度。
2. 故障模式与影响分析法(FMEA):对生产过程中的各个环节进行全面的分析,识别出潜在的故障模式和可能导致故障的因素,评估其对产品质量的影响程度。
3. 统计分析法:通过对历史数据进行统计分析,找出常见的质量问题和其发生的规律,进而评估未来可能出现的质量风险。
4. 专家评估法:邀请相关领域的专家进行评估,利用其经验和知识来识别潜在的质量风险,并评估其发生的可能性和影响程度。
三、质量风险评估的意义1. 风险预警:通过质量风险评估,企业能够及早识别潜在的风险,及时采取相应的预防措施,避免质量问题的发生,降低风险损失。
2. 资源优化:企业在质量控制和风险管理方面可以根据评估结果合理配置资源,优化生产过程,提高生产效率和质量水平。
3. 提升市场竞争力:药品市场竞争激烈,优质的产品更容易获得市场认可和消费者的信赖。
通过质量风险评估,企业能够提高产品的质量水平,增强市场竞争力。
4. 合规管理:随着监管政策的不断加强,企业需要确保自身的质量管理符合法规要求。
质量风险评估能够帮助企业发现潜在的合规风险,并采取相应的控制措施,确保生产过程的合规性。