双股流低温缠绕管式换热器设计计算方法_张周卫
(整理)列管式换热器多种方案设计 计算过程详细

根据给定的原始条件,确定各股物料的进出口温度,计算换热器所需的传热面积,设计换热器的结构和尺寸,并要求核对换热器压强降是否符合小于30 kPa的要求。
各项设计均可参照国家标准或是行业标准来完成。
具体项目如下:设计要求:1.某工厂的苯车间,需将苯从其正常沸点被冷却到40℃;使用的冷却剂为冷却水,其进口温度为30℃,出口温度自定。
2.物料(苯)的处理量为1000 吨/日。
3.要求管程、壳程的压力降均小于30 kPa。
1、换热器类型的选择。
列管式换热器2、管程、壳程流体的安排。
水走管程,苯走壳程,原因有以下几点:1.苯的温度比较高,水的温度比较低,高温的适合走管程,低温适合走壳程2.传热系数比较大的适合走壳程,水传热系数比苯大3.干净的物流宜走壳程。
而易产生堵、结垢的物流宜走管程。
3、热负荷及冷却剂的消耗量。
=30℃,冷却介质的选用及其物性。
按已知条件给出,冷却介质为水,根进口温度t1=38℃,因此平均温度下冷却水物性如下:冷却水出口温度设计为t2=0.727Χ10-3Pa.s密度ρ=994kg/m3粘度μ2导热系数λ=62.6Χ10-2 W/(m.K) 比热容Cpc=4.184 kJ/(kg.K)苯的物性如下:进口温度:80.1℃出口温度:40℃=1.15Χ10-3Pa.s密度ρ=880kg/m3粘度μ2导热系数λ=14.8Χ10-2 W/(m.K) 比热容Cpc=1.6 kJ/(kg.K)苯处理量:1000t/day=41667kg/h=11.57kg/s热负荷:Q=WhCph(T2-T1)=11.57×1.6×1000×(80.1-40)=7.4×105W冷却水用量:Wc=Q/[c pc(t2-t1)]=7.4×105/[4.184×1000×(38-30)]=22.1kg/s4、传热面积的计算。
平均温度差△t ′m =△t2−△t1ln △t2△t1=(80.1−38)−(40−30)ln 80.1−3840−30=27.2℃确定R 和P 值 R =T 1−T 2t 2−t 2=80.1−4038−30=5.01 P =t 2−t 1T 1−t 1=38−3080.1−30=0.16查阅《化工原理》上册203页得出温度校正系数为0.8,适合单壳程换热器,平均温度差为△tm=△t’m ×0.9=27.2×0.9=24.5由《化工原理》上册表4-1估算总传热系数K (估计)为400W/(m ²·℃) 估算所需要的传热面积:S 0=QK(估计)△t m=740000400×24.5=75m ²5、换热器结构尺寸的确定,包括: (1)传热管的直径、管长及管子根数;由于苯属于不易结垢的流体,采用常用的管子规格Φ19mm ×2mm 管内流体流速暂定为0.7m/s所需要的管子数目:n =4V d iπu i=4×(11.57/880)3.14×0.7×0.0152=122.1,取n 为123管长:l ′=S 0nπd 0=75123×3.14×0.015=12.9m按商品管长系列规格,取管长L=4.5m ,选用三管程 管子的排列方式及管子与管板的连接方式:管子的排列方式,采用正三角形排列;管子与管板的连接,采用焊接法。
[工学]管壳式热交换器设计全解_OK
![[工学]管壳式热交换器设计全解_OK](https://img.taocdn.com/s3/m/ce480009770bf78a6429545b.png)
t1
t2
Q M 1 C1dt1 M 2 C2dt 2
t1
t2
适用于无相变流体
M1 M 2 分别为热流体与冷流体的质量流量 ,Kg/s
i1 i2 分别为热流体与冷流体的焓,J/Kg
C1 C2 分别为两种流体的定压质量比热,J/(Kg·℃)
6
Q M1c1 t1 t1t1 M1c1 t1 t2 t1 M1c1t1 W1t1
示 在相同的流体进出口温度条件下,按逆流工作所需的传热
面积 Fco与unte按r 某种流动形式工作所需的传热面积 之F比othe值r (传热系数相等的条件小),
即:
tm Fcounter
tlm,c
Fother
恒不大于0或≤1
26
值的求取方法
• 逆流时对数平均温差为 :
令:
t1m,c
t1
t2 ln
于4%;当
tma时x ,tm两in者的1.7差别小于2.3%。
23
2 复杂布置时换热器平均温差的计算 非混合流与混合流的区别:
以错流为例,带翅片的管束,在管外侧流过的气体 被限制在肋片之间形成各自独立的通道,在垂直于 流动的方向上(横向)不能自由流动,也就不可能 自身进行混合,称该气体为非混合流。
3 由 W=1t1 W=2Qt,2 还可以知道,在热交换器内,热容量越大
的流体,温度变化值越小,热容量越小的流体,温度变化值
越大
4 计算流体的热容量时,M与c的单位必须一致
5 已知热交换器热负荷的条件下,热平衡方程可用于确定 8 流体的流量
2.2热交换器传热计算的基本方法:
平均温差法
效率(效能)-传热单元数法(η-NTU) 一、平均温差法
t1
LNG缠绕管式换热器试验研究中的热物性计算方法_陈永东

天 然 气 工 业 2011 年 6 月
LNG 缠绕管式换热器试验研究中的热物性计算方法
陈永东1,2 吴晓红1,2 周 兵1,2
1.合 肥 通 用 机 械 研 究 院 2.国 家 压 力 容 器 与 管 道 安 全 工 程 技 术 研 究 中 心
(10)
气态纯物质在常压下的比热容cp 按照下式计算:
cp = A +BT +CT2 +DT3 +ET4 (11)
式(11)中cp 的 单 位 是 J/(mol·K),本 文 参 考 文
献[6]给 出 了 不 同 物 质 对 应 的 系 数 A~E。 表 1 为 甲
烷和乙烷在常压下的比热容计算系数表。
参 数 包 括 流 速 、蒸 汽 分 率 、当 地 摩 擦 压 降 和 当 地 传 热 系 数等),同 时 也 介 绍 了 其 采 用 的 热 物 性 计 算 方 法 的 来 源,并指出了相关 物 性 计 算 的 不 确 定 度。 而 我 国 目 前 的热物性计算大多依 靠 国 外 的 计 算 软 件,且 没 有 对 其 计算结果进行任何评 估,没 有 相 应 物 性 计 算 软 件 的 单 位从事相关研究与设 计 就 相 当 困 难,传 热 与 流 动 试 验 的主要结果 是 靠 测 试 数 据 和 介 质 的 热 物 性 推 衍 得 到 的,因此有必要对试验 介 质 (尤 其 是 混 合 物)的 热 物 性 计算方法进行 总 结,为 LNG 低 温 换 热 器 的 试 验 研 究 奠定基础。
表 1 甲 烷 和 乙 烷 在 常 压 下 的 比 热 容 计 算 系 数 表
组分 A
B
C
D
E
甲烷 34.942 -4.00×10-2 1.92×10-4 -1.53×10-7 3.93×10-11
换热器设计计算详细过程

换热器设计计算详细过程序号名称单位数值流体流向1有无相变01流体名称冷却水壳程流体名称进口温度t 1℃20进口温度T 1出口温度t 2℃40出口温度T 2定性温度℃30定性温度比热CP 1J/(kg·K)4174比热CP 2 黏度μ1Pa·s 0.000801黏度μ2导热系数λ1W/(m·K)0.618导热系数λ2密度ρ1kg/m 3995.7密度ρ2管程压强降Pa30000壳程压强降流量W 2计算过程&输出结果:热负荷QkW 376.83冷却水流量W 1kg/h 16250.60按逆流计算的传热温差℃49.71按并流计算的传热温差℃#DIV/0!传热温差输出值ΔT ℃49.71计算温度校正系数S 0.17R5查图得到温度校正系数ψΔT 0.85实际的传热温差ΔTm ℃42.25初选总传热系数K KW/(m 2·℃)395换热面积 Sm 222.58参照换热面积选取列管换热器结构参数换热器形式浮头式壳体直径 D mm 300列管数n 根40列管外径d 0mm25参照GBT 28712-2012 换热器型ΔTm=ΔT*ψΔT经验值,假设K值为固定值S=Q/(K*ΔTm )管径有25或19两种规格管壳式换热器的设计和选用输入参数当温度校正系数值小于0.8时,合理,此时应增加管程数或壳程数,或者用几热器串联,必要时可调节温度条件。
S=(t2-t1)/(T1-t1),冷流体温R=(T1-T2)/(t2-t1),热流体温备注:比热、粘度、导热系数、密度均为两流体在定性温度(t1+t2)/2和(T1+T2)/2 下的备换热器中两流体的流向,并流管子的排列方式,正三角形为1,正方形为2热流体无相变,0;热流体有相备注热流体无相变:Q=W 2/3600*C p2*(T 1-T 2);W 1=Q/(Cp 1*(t 2-t 1))*3600ΔT=((T1-t2)-(T2-t1))/LN((T1-t2)/(T2-t1壳程流体参管程流体参数(P)列管内径d i mm20列管长度L mm8000折流板间距mm150列管材质及导热系数W/(m·K)45设计的换热面积 m296管子排列方法正方形斜转45度管程数Np2串联的壳程数Ns1管间距mm32结垢校正因子Ft 1.4管子排列方式对压降的校正因子F0.4管程n值0.4流体被加热取0.4,被冷却取0壳程n值0.3管壁内侧表面污垢热阻(m2·℃)/K0.00058管壁外侧表面污垢热阻(m2·℃)/K0.00017换热管壁厚 mm 2.5换热管平均直径mm22.5采用此传热面积下的总传热系数W/(m2·℃)92.90592116(1)核算压力降①管程压强降-P管程流通面积 Ai m20.006283185管程流速ui m/s0.721536817管程雷诺数Rei17938.43217取管壁粗糙度 mm0.1相对粗糙度0.005查图求得摩擦系数λ0.035直管中压力降Δp1Pa3628.637123回弯管压力降Δp2Pa777.5650977管程总压力降ΣΔPi Pa12337.36622判断合理性cs_tj10②壳程压强降—S通过管束中心线的管子数n o8折流板数N B52.33333333壳程流通面积 A o m20.015壳程流速u o m/s0.116959064 Re o3743.635819壳程流体摩擦系数f o0.766053436流体横过管束的压力降Pa849.5112828流体流过折流板缺口的压强降Pa850.119125壳程总压力降Pa1954.574969合理性判断cs_tj20(2)核算总传热系数①管程对流传热系数流体被加热取0.4,被冷却取0查污垢热阻系数表得到查污垢热阻系数表得到管子按正三角形排列no=1.1*(排列no=1.19*(n)^0.5N B=(L列管长度L/折流板间距-1) Ao=h(D-n c d o)按壳程流通截面积Ao计算的流Δp2=3*ρu2/2ΣΔPi=(Δp1+Δp2)Fg NpΣΔPo=(Δp1’+Δp2')FsNsRe=ρdu/μ,湍流输入值当Re>500时,fo=5.0Reo^(-0正三角形、正方形、正方形斜计算值查摩擦系数与雷诺数和相对粗Δp1=λ*L/d*ρu2/2ΣΔPi=(Δp1+Δp2)FtNpA i=π/4*d i2*n/Npu i=W1/(ρ1*A i)K=Q/(S*ΔTm)DN25管子取为1.4,对DN19管子正三角形为0.5,正方形斜转4接近但不小于1.25倍的换热管Pr-管程5.409990291管程雷诺数Re017938.43217管程对流传热系数(湍流)W/(m2·℃)3531.770673低黏度湍流W/(m2·℃)3531.770673高黏度湍流W/(m2·℃)3519.429449管程对流传热系数(滞流)W/(m2·℃)340.5404362管程对流传热系数(过渡流)W/(m2·℃)3485.069082管程对流传热系数输出值W/(m2·℃)3531.770673②壳程对流传热系数Pr—壳程9.753848837流体流过管间最大截面积A㎡0.00984375根据管间最大截面积计算的流速u0m/s0.178223336当量直径 d e m0.027151892 ReS6195.614142φμ=(μ/μw)^0.140.95壳程对流传热系数as W/(m2·℃)563.8014636③总传热系数总传热系数k校W/(m2·℃)324.2192582此换热器安全系数%248.9758824合理性判断cs_tj31低黏度液体(μ1<2*常温下水的黏度),a0=0.023(λ/di)Re0.8Pr n高黏度液体,a0=0.027(λ/di)Re0.8Pr1/3φμ强制湍流,Re0大于10000A=hD(1-d0/t)u0=Vs/Ad e=4(t2-π/4d02)/πd0强制滞留,Re小于2300过渡流,Re=2300~10000对气体取1.0,加热液体取1.0安全系数介于11.5~12.5,初选需另设K值植物油℃140℃40℃90J/(kg·K)2261Pa·s 0.000742W/(m·K)0.172kg/m 3950Pa 30000kg/h6000104.7611114方法二:根据流速经验值计算换热器内参数管道内流体流速m/s 0.75列管外径mm 25列管内径mm 20计算单程管传热管数根20热器型式与基本参数值.8时,换热器的经济效益不加管程数或壳程数,或者用几台换时可调节温度条件。
(完整word版)热管换热器设计计算及设计说明书
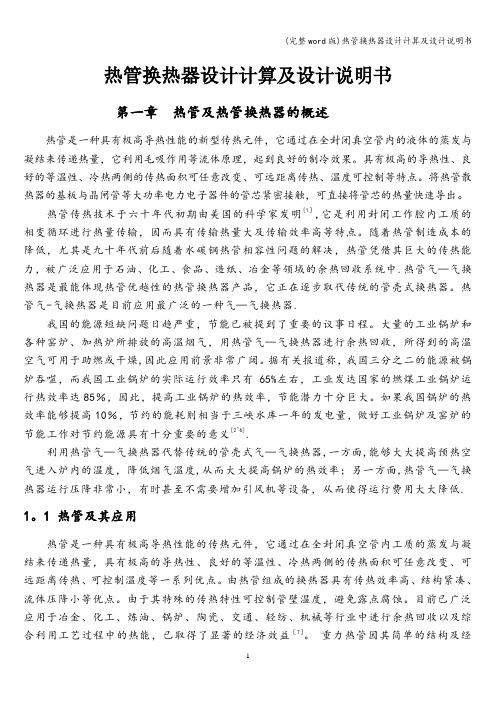
热管换热器设计计算及设计说明书第一章热管及热管换热器的概述热管是一种具有极高导热性能的新型传热元件,它通过在全封闭真空管内的液体的蒸发与凝结来传递热量,它利用毛吸作用等流体原理,起到良好的制冷效果。
具有极高的导热性、良好的等温性、冷热两侧的传热面积可任意改变、可远距离传热、温度可控制等特点。
将热管散热器的基板与晶闸管等大功率电力电子器件的管芯紧密接触,可直接将管芯的热量快速导出。
热管传热技术于六十年代初期由美国的科学家发明[1],它是利用封闭工作腔内工质的相变循环进行热量传输,因而具有传输热量大及传输效率高等特点。
随着热管制造成本的降低,尤其是九十年代前后随着水碳钢热管相容性问题的解决,热管凭借其巨大的传热能力,被广泛应用于石油、化工、食品、造纸、冶金等领域的余热回收系统中.热管气—气换热器是最能体现热管优越性的热管换热器产品,它正在逐步取代传统的管壳式换热器。
热管气-气换热器是目前应用最广泛的一种气—气换热器.我国的能源短缺问题日趋严重,节能已被提到了重要的议事日程。
大量的工业锅炉和各种窑炉、加热炉所排放的高温烟气,用热管气—气换热器进行余热回收,所得到的高温空气可用于助燃或干燥,因此应用前景非常广阔。
据有关报道称,我国三分之二的能源被锅炉吞噬,而我国工业锅炉的实际运行效率只有65%左右,工业发达国家的燃煤工业锅炉运行热效率达85%,因此,提高工业锅炉的热效率,节能潜力十分巨大。
如果我国锅炉的热效率能够提高10%,节约的能耗则相当于三峡水库一年的发电量,做好工业锅炉及窑炉的节能工作对节约能源具有十分重要的意义[2~6].利用热管气—气换热器代替传统的管壳式气—气换热器,一方面,能够大大提高预热空气进入炉内的温度,降低烟气温度,从而大大提高锅炉的热效率;另一方面,热管气—气换热器运行压降非常小,有时甚至不需要增加引风机等设备,从而使得运行费用大大降低. 1。
1 热管及其应用热管是一种具有极高导热性能的传热元件,它通过在全封闭真空管内工质的蒸发与凝结来传递热量,具有极高的导热性、良好的等温性、冷热两侧的传热面积可任意改变、可远距离传热、可控制温度等一系列优点。
换热器的快速设计计算

换热器的快速设计计算
Pedro,E;史新辉
【期刊名称】《化学工程》
【年(卷),期】1990(018)004
【摘要】工程师们在设计或确定两程或多程换热器时必须校正非逆流时的LMTD 值(温差的对数平均值)。
作者等人参考了许多文献的有关公式,总结出了关于计算温差校正因子(或称F因子)的一组方程。
但更重要的是,本文将向大家介绍一个简单的方法来解这些计算方程。
以前是采用迭代法来解这些方程,所以比较复杂、困难。
【总页数】4页(P66-69)
【作者】Pedro,E;史新辉
【作者单位】不详;不详
【正文语种】中文
【中图分类】TQ051.502
【相关文献】
1.土壤源热泵桩基埋管换热器的传热分析和设计计算 [J], 张娇健
2.双股流低温缠绕管式换热器设计计算方法 [J], 张周卫;薛佳幸;汪雅红
3.烟气协同治理中烟气换热器的设计计算 [J], 王迎春; 梁启煜
4.两段式塑料换热器的设计计算与可行性分析 [J], 袁昌旗;张岩
5.两段式塑料换热器的设计计算与可行性分析 [J], 袁昌旗;张岩
因版权原因,仅展示原文概要,查看原文内容请购买。
第三节 换热器计算方法
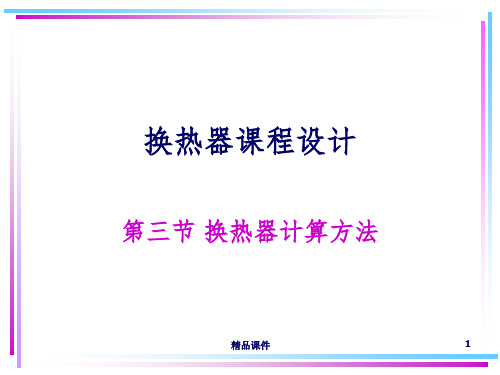
先Байду номын сангаас体的压强、防腐蚀和清洗等精要品课求件,再校核对流传热系数和压强降。5
二、流体流速的选择
•增加流速
对流传热系数↑ ,污垢热阻↓→总传热系数↑ → 传热面积↓ 流动阻力↑和动力消一耗定传↑热面积
还需考虑结构上:
高流速→管子数目↓→较长管子或增加程数
p 0 ( p 1 ' p 2 ')F sN s
p 1 ' 流 体 横 过 管 束 的 压 强 降 , P a ; p 2 ' 流 体 通 过 折 流 板 缺 口 的 压 强 降 , P a ;
F s 壳 程 压 强 降 的 结 垢 校 正 系 数 , 液 体 可 取 1 . 1 5 , 气 体 可 取 1 . 0 Ns串 联 的 壳 程 数 。
管间距:两相邻换热管中心的距离。其值的确定需要考虑 以下几个因素:
① 管板强度; ② 清洗管子外表面时所需要的空隙; ③ 换热管在管板上的固定方法。
通常,胀管法取t =(1.3~1.5)d0,且相邻两管外壁间距不 应小于6mm,即t≥6+d0
焊接法取t =1.25d0。
精品课件
12
五、管程和壳程数的确定
流速u的经验值可取为: 对液体 u =1.5~2m/s;对蒸气u =20~50m/s ;
对气体u =(0.15~0.2)p/ρ精品(课p件为压强,kPa; ρ为气体密度)。 21
九、材料选用
材料应根据操作压力、温度及流体的腐蚀性等来选用。
目前常用的金属材料有:碳钢、不锈钢、低合金钢、铜 和铝等。
非金属材料有:石墨、聚四氟乙烯和玻璃等。
管子太长不易清洗,且管长都有一定标准;
换热器设计计算范例
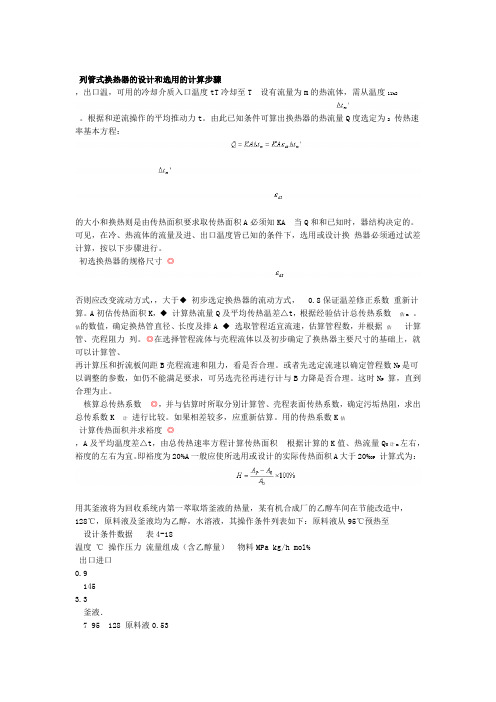
列管式换热器的设计和选用的计算步骤,出口温,可用的冷却介质入口温度tT冷却至T 设有流量为m的热流体,需从温度11h2。
根据和逆流操作的平均推动力t。
由此已知条件可算出换热器的热流量Q度选定为2传热速率基本方程:的大小和换热则是由传热面积要求取传热面积A必须知KA 当Q和和已知时,器结构决定的。
可见,在冷、热流体的流量及进、出口温度皆已知的条件下,选用或设计换热器必须通过试差计算,按以下步骤进行。
初选换热器的规格尺寸◎否则应改变流动方式,,大于◆初步选定换热器的流动方式, 0.8保证温差修正系数重新计算。
A初估传热面积K,◆计算热流量Q及平均传热温差△t,根据经验估计总传热系数估m。
估的数值,确定换热管直径、长度及排A ◆选取管程适宜流速,估算管程数,并根据估计算管、壳程阻力列。
◎在选择管程流体与壳程流体以及初步确定了换热器主要尺寸的基础上,就可以计算管、再计算压和折流板间距B壳程流速和阻力,看是否合理。
或者先选定流速以确定管程数N P是可以调整的参数,如仍不能满足要求,可另选壳径再进行计与B力降是否合理。
这时N P算,直到合理为止。
核算总传热系数◎,并与估算时所取分别计算管、壳程表面传热系数,确定污垢热阻,求出总传系数K 计进行比较。
如果相差较多,应重新估算。
用的传热系数K估计算传热面积并求裕度◎,A及平均温度差△t,由总传热速率方程计算传热面积根据计算的K值、热流量Q0计m左右,裕度的左右为宜。
即裕度为20%A一般应使所选用或设计的实际传热面积A大于20%0P计算式为:用其釜液将为回收系统内第一萃取塔釜液的热量,某有机合成厂的乙醇车间在节能改造中,128℃,原料液及釜液均为乙醇,水溶液,其操作条件列表如下:原料液从95℃预热至设计条件数据表4-18温度℃操作压力流量组成(含乙醇量)物料MPa kg/h mol%出口进口0.91453.3釜液.7 95 128 原料液0.53试设计选择适宜的列管换热器。
- 1、下载文档前请自行甄别文档内容的完整性,平台不提供额外的编辑、内容补充、找答案等附加服务。
- 2、"仅部分预览"的文档,不可在线预览部分如存在完整性等问题,可反馈申请退款(可完整预览的文档不适用该条件!)。
- 3、如文档侵犯您的权益,请联系客服反馈,我们会尽快为您处理(人工客服工作时间:9:00-18:30)。
低
பைடு நூலகம்
温
工
程
2014 年
( 1) ( 2) ( 3)
2. 6
总传热系数计算
采用对数平均值法按气液分相及显热与潜热独 立计算方法计算对流传热系数及总传热系数 。 壳侧 对流传热系数: ho = Q总 / ( Qs / hs + Qr / hr ) h s = R Lo h Lo + ( 1 - R Lo ) h Vo Q s = ( C pLo平 m Lo平 + C pVo平 m Vo平 ) Δt Qr = Q总 - Qs ( 9) ( 10 ) ( 11 ) ( 12 )
壳程为 - 43. 29 ℃ 低温甲醇。 模拟参数须满足换热 器设计参数并以获得最佳单元模型物理参数为条件 。 根据数值模拟结果, 确定缠绕管束基本物理结构参 数, 选取最佳缠绕管束物理模型并进行计算 。
图3 Fig. 3
单元模型数值模拟效果图
Effect of numerical simulation of unit model
0805 ; 修订日期: 20141026 收稿日期: 201413C26216205878 ) 。 基金项目: 中国博士后基金项目( 2012M521814 ) 、 国家中小企业创新基金项目 ( 12C26216207017 , 40 岁, 作者简介: 张周卫, 男, 博士后、 副教授。
18 引 言
是一种换热管道经层 层缠绕后形成的一种双管束螺旋盘管型热交换设备 , 主要由螺旋管束 1 、 螺旋管束 2 、 壳体、 芯筒、 支撑等主 要部件构成, 应用缠绕管束内两股不同流体同时与壳 侧流体换热, 为缠绕管式换热器中较为基础的双股流 主要用于管程存在较大温差的流体换热过 换热器, 程。双股流缠绕管式换热器以其结构紧凑 , 单位容积 具有较大的传热面积, 传热管热膨胀可自行补偿, 容 易实现大型化, 可减少设备台数等优点成为天然气液 化、 低温液氮洗、 低温甲醇洗等低温净化、 液化工艺中 的重要设备。 由于双股流缠绕管式换热器大多应用于低温环 , 境 内部管道缠绕复杂, 没有通用设计标准, 也没有统 一的换热工艺设计计算方法, 随着工艺流程或物性参 数特点不同而存在较大差别, 因此给双股流螺旋缠绕 由于双股 管式换热器标准化过程带来了困难 。此外, 螺旋管缠绕方法很多, 没 流缠绕管式换热器螺旋管、 有统一的管道缠绕模式及理论设计计算方法用于计 算机辅助计算过程, 给双股流缠绕管式换热器的科学 计算过程带来了障碍。 为更好地解决双股流缠绕管 本文从双股流缠 式换热器的标准化及科学计算问题 , 绕管式换热器换热工艺设计计算出发 , 给出了一种双 股流缠绕管式换热器的简捷设计计算方法 。 双股流缠 绕 管 式 换 热 器 设 计 计 算 方 法 主 要 应 用于气体低温液化分离领域 , 包括 - 162 ℃ 天然气 - 197 ℃ 空气低温液化分离 、- 197 ℃ 低 低温液化 、 - 70 ℃ 低温甲醇洗工艺等气体低温 温液氮洗工艺 、 净化 、 低温液 化 分 离 技 术 领 域 , 包括双股流缠绕管 式换热器流速计算 、 雷诺数计算 、 普朗特数计算 、 总 传热系数计算及有效换热高度计算 5 个主要换热 甲醇双股流缠绕管式 工艺计算过程 。 本文以甲醇 换热器换热工艺设计计算为例 , 研究开发更科学的 设计计算方法 。 2 计算方法
管 外 传 热 膜 数 按 Gilli 公 式、 管内传热膜数按 [3 ] Schmidt 公式计算 , 式( 10 ) 中: . 61 0 . 333 h Vo = 0 . 338 F i F n F t Re0 ( λ Vo / 0 . 001 d o ) Vo Pr Vo ( 13 ) h Lo = 0 . 338 F i F n F t Re
双股流缠绕管式换热器
图1 Fig. 1
管束缠绕结构
Tube winding structure
根据传热学及流体力学基本原理 , 应用对数平均 值法、 体积分率法及质量分率法求解过程参数, 并将 所得参数应用于总传热系数计算过程 ; 双股流螺旋缠 绕管式换热器换热工艺设计计算方法已通过基础设 计参数修正。采用对数平均值法校核流速; 计算雷诺 数和普朗特数; 采用平均值法按气液分相及显热与潜
图2 Fig. 2 管束排列剖面图 Tube bundle arrangement profile
第6 期
双股流低温缠绕管式换热器设计计算方法
19
2. 2
双股流管束数值模拟 根据管束物理模型, 取单元模型( 如图 3 ) 进行管 确定边界条件。模拟过程中管束 1 内为 束数值模拟, - 17. 43 ℃ 低温甲醇, 管束 2 内为 - 25 ℃ 低温甲醇,
2. 3
流速计算 预设柱筒外为 , 管程内流速为 v i ( m / s ) , 管子
中心间距 g, 螺旋角 β。 则相邻层螺旋管外层比内层 的增加弧度:
20 Δl = g / sinβ 总管道数量: n = 4 V i平 / π d i v i平 其中: V i平 = ( V i进 - V i出 ) / ln( V i进 / V i出 )
2014 年第 6 期 总第 202 期
低
温
工
程
CRYOGENICS
No. 6 2014 Sum No. 202
双股流低温缠绕管式换热器设计计算方法
张周卫
2
1
薛佳幸
1
汪雅红
1, 2
( 1 兰州交通大学环境与市政工程学院 ( 甘肃中远能源动力工程有限公司
兰州 730070 ) 兰州 730070 )
要: 提出一种适用于双股流逆流型缠绕管式换热器的换热工艺计算方法 , 应用数值模拟方法 。 确定双股流缠绕管束基本物理参数 按照双股流甲醇 甲醇缠绕管式换热器计算流程进行编程迭代 摘 计算, 对比分析计算数据并建立双股流低温缠绕管式换热器管束模型 。研究表明: 引入数值模拟方法 可简化双股流缠绕管式换热器管束的缠绕工艺 , 获得双股流缠绕管式换热器结构总体设计参数并应 用于建模过程。将所建模型及相应三维物理模型应用于传热工艺计算过程 , 可通过编程计算并优化 双股流换热整体设计计算过程。 关键词: 缠绕管式换热器 中图分类号: TB657. 5 管束数值模拟 缠绕结构 三维数值模型 6516 ( 2014 ) 06001707 文献标识码: A 文章编号: 1000-
2 W / ( m2 ·K ) , 其中 h r = 1 000 —1 100 W / ( m ·K) , 取
A 为壳侧流通面积, m2 ; 式中: 下标 o 表示壳侧, D m 为螺旋管束中径, m。 若考虑 两 相 流 动, 则 分 别 计 算 气、 液两态流速 v Vo平 和 v Lo平 如 式 ( 6 ) 。 而 其 中 气、 液两态体积流量 V Vo平 、 V Lo平 的计算方法同式( 3 ) 。 2. 4 雷诺数计算 壳侧雷诺数: Re o = v o平 ρ o平 d o / μ o平 ( 7)
根据缠绕模型方法重新统计管道数量 n 并重新 计算管内流速, 则螺旋管 1 内对数平均流速: v1i = V1i平 / a i n1
3
( 4)
式( 2 ) —( 4 ) 中: 下标 i 表示管侧; d i 为螺旋管内 mm; V 为流质体积流量, m / h; a 为内管道通流截 径, m2 。 面面积, 同样用螺旋管束 1 的计算方法可得到螺旋管束 2 的平均流速 v2i 及两相流动时流速 v2i平 。 由此可推 出每层所布置的螺旋管数目, 再确定盘管层数 N z 及 壳侧流通面积。 A = πD m [ ( N z - 1 ) B m + 2 S1 ] 理想状态下壳侧计算平均流速: v o平 = V o平 / ( 3 600 A) ( 5) ( 6)
Abstract: A calculation method for countercurrent type doublestream coilwound heat exchanger was presented for heat exchange process. The numerical simulation method was applied to determine the basic physical parameters of doublestream wound bundles. In accordance with methanolmethanol doublestream coilwound heat exchanger to program and calculate the iterative process. Ccalculation data was analyzed by comparison and a doublestream coilwound heat exchanger bundle model was built. Studies show that the introduction of numerical simulation method can simplify the tube bundles winding process calculations of doublestream coilwound heat exchanger. The overall structure design parameters of the heat exchanger can be obtained and be applied to the modeling process. The corresponding threedimensional physical model can be applied to heat transfer calculation process. It can be programmed to calculate and optimize the overall design of the doublestream heat exchange calculation process. Key words: coilwound heat exchanger; tube bundles numerical simulation; wind structure; threedimensional physical model