管壳式冷却器设计计算
管壳式换热器的建模、换热计算和CFD模拟
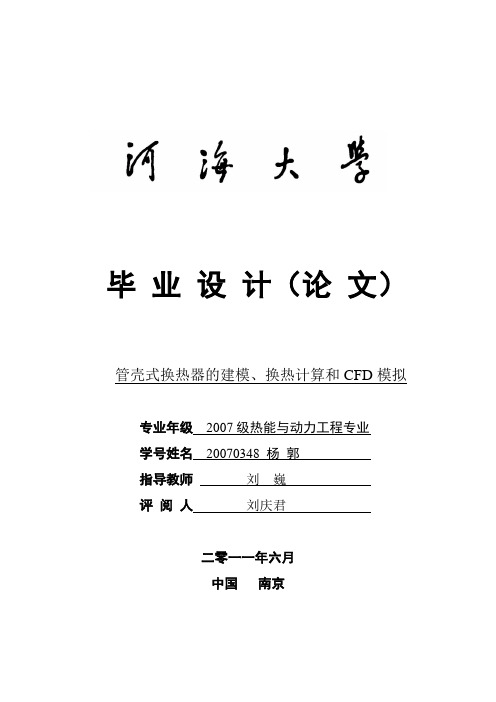
毕业设计(论文)管壳式换热器的建模、换热计算和CFD模拟专业年级2007级热能与动力工程专业学号姓名******** 杨郭指导教师刘巍评阅人刘庆君二零一一年六月中国南京任务书课题名称:管壳式换热器的建模、换热计算与CFD模拟课题类型:毕业论文任务书内容:1、英文资料的翻译5千个汉字字符以上(要求和热动、空调、能源、环境、新能源等本专业有关的内容,可以是英文著作、设备使用手册、英文文献检索、英文专利文献、网上专题介绍等实用性的、将来工作中可遇到的相关题材的文章,最好不要是科普类、教学类的英文)2、使用的原始资料(数据)及设计技术要求:2.1.管壳式换热器,热交换功率100kW,200kW。
2.2.温度进口350~500℃,出口温度150~200℃,流速可变;温度进口100~150℃,出口温度300~450℃,流速可变。
其总流阻损失应在满足规定要求。
2.3.换热器材料可选,几何尺寸可变;工作介质可选择(空气、水、氟利昂) 2.4.换热器外壁面绝热保温; 2.5.采用CFD模拟计算与能量分析,对系统进行相关工况的模拟;3、设计内容:3.1. 学习和消化设计任务书,按照设计任务书的设计内容,拟定工作内容和计划,拟定出设计和计算的每个过程中应该遵循设计要求与规定。
3.2.查找和收集有关管壳式换热器的历史和现状资料,查找相关管壳式换热器的运用案例,及其相关的技术条件和运行要求。
3.3.以科技文献检索,包括期刊、专利、设计标准、产品标准、设计手册、产品样本,寻找和熟悉相关的分析计算软件;熟悉设计工具软件、电脑等;3.4.根据已知参数,用ProE设计出符合要求的管壳式换热器,并学习如何导入相关软件进行网格设计;3.5.进行管壳式换热器CFD网格设计,用fluent软件对管壳式换热器进行变工况运行能量分析;3.5.分析计算换热器的流阻损失,其结果的合理性,分析提高换热效率主要手段和改进的方向。
3.6.输出的计算文件包括:3.6.1.完整的毕业设计任务书3.6.2.符合要求的算模型的结构、尺寸; 3.6.3.换热计算的过程、表格,计算结果的结论等等; 3.6.4.规定状态的CFD模拟结果和能量分析图; 3.6.5.毕业设计论文; 3.7.把所作的工作、学习的体会、方案的选择过程、计算方案过程等写在过程手册中,写好毕业设计论文。
管壳式换热器的设计及计算
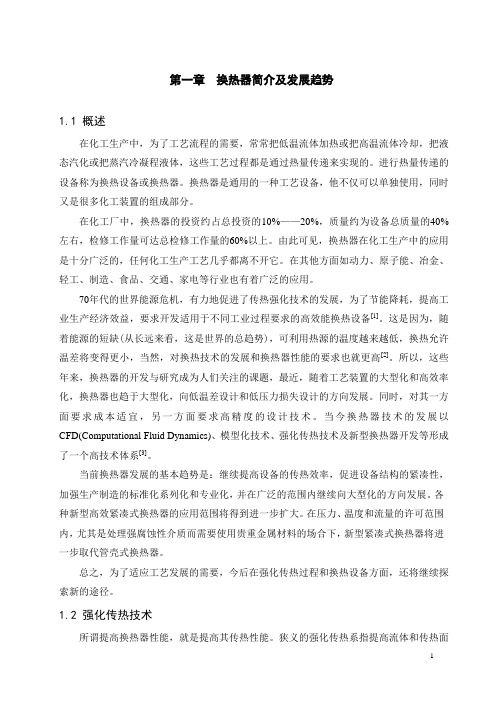
第一章换热器简介及发展趋势1.1 概述在化工生产中,为了工艺流程的需要,常常把低温流体加热或把高温流体冷却,把液态汽化或把蒸汽冷凝程液体,这些工艺过程都是通过热量传递来实现的。
进行热量传递的设备称为换热设备或换热器。
换热器是通用的一种工艺设备,他不仅可以单独使用,同时又是很多化工装置的组成部分。
在化工厂中,换热器的投资约占总投资的10%——20%,质量约为设备总质量的40%左右,检修工作量可达总检修工作量的60%以上。
由此可见,换热器在化工生产中的应用是十分广泛的,任何化工生产工艺几乎都离不开它。
在其他方面如动力、原子能、冶金、轻工、制造、食品、交通、家电等行业也有着广泛的应用。
70年代的世界能源危机,有力地促进了传热强化技术的发展,为了节能降耗,提高工业生产经济效益,要求开发适用于不同工业过程要求的高效能换热设备[1]。
这是因为,随着能源的短缺(从长远来看,这是世界的总趋势),可利用热源的温度越来越低,换热允许温差将变得更小,当然,对换热技术的发展和换热器性能的要求也就更高[2]。
所以,这些年来,换热器的开发与研究成为人们关注的课题,最近,随着工艺装置的大型化和高效率化,换热器也趋于大型化,向低温差设计和低压力损失设计的方向发展。
同时,对其一方面要求成本适宜,另一方面要求高精度的设计技术。
当今换热器技术的发展以CFD(Computational Fluid Dynamics)、模型化技术、强化传热技术及新型换热器开发等形成了一个高技术体系[3]。
当前换热器发展的基本趋势是:继续提高设备的传热效率,促进设备结构的紧凑性,加强生产制造的标准化系列化和专业化,并在广泛的范围内继续向大型化的方向发展。
各种新型高效紧凑式换热器的应用范围将得到进一步扩大。
在压力、温度和流量的许可范围内,尤其是处理强腐蚀性介质而需要使用贵重金属材料的场合下,新型紧凑式换热器将进一步取代管壳式换热器。
总之,为了适应工艺发展的需要,今后在强化传热过程和换热设备方面,还将继续探索新的途径。
换热器设计计算

污垢热阻的大致数值
流体种类
水(u<1m/s, t<50℃) 海水 河水 井水 蒸馏水
锅炉给水 未处理的凉水塔用水 经处理的凉水塔用水 多泥沙的水
盐水
污垢热阻 m2·℃/W
0.0001 0.0006 0.00058 0.0001 0.00026 0.00058 0.00026 0.0006 0.0004
校核性热计算 针对现成的换热器,其目的在于确定流体 的出 口温度
因此: 设计型——已知任务设备 操作型——已知一定设备预测、调节结果
1、设计型计算的命题
给定生产任务:ṁ1,T1T2(or ṁ2,t1t2) 选择工艺条件:t1,t2 计算目的:换热器传热面积A(管子规格,根数);ṁ2 特点:结果的非唯一性。
换热器设计计算
5.1 换热器类型
换热器类型 按结构分为
间壁式
套管式 交 壳 板叉 管 式流 式(换管热壳器式)管 管 板翅 束 翅式 式 式
螺旋板式
夹套式
混合式
蓄热式
按用途分为:加热器、冷却器、冷凝器、蒸发器、再沸器
蓄热器(蓄能器)
(一)间壁式换热器 一、套管式换热器
二 、管壳式换热器
2、设计计算公式:
质量衡算:ṁ1
ṁ2
ṁn = ?
dn = ?
热量衡算: Q = ṁ1Cp1(T1 - T2) = ṁ2Cp2(t2 - t1)
传热速率式: Q = KAtm
注意: 计算单位要统一
➢ 热量:由于温差的存在会导致能量的交换。 该交换过程称为热交换或热传递。 热量的国际单位:焦耳(J)或常用单位:卡(cal)。 换算关系:1cal=4.19J
(对数平均数)
Δt1 Δt2 ln Δt1
1化工原理课程设计(换热器)解析

一、设计题目:设计一台换热器二、操作条件:1、煤油:入口温度140℃,出口温度40℃。
2、冷却介质:循环水,入口温度35℃。
3、允许压强降:不大于1×105Pa。
4、每年按330天计,每天24小时连续运行。
三、设备型式:管壳式换热器四、处理能力:114000吨/年煤油五、设计要求:1、选定管壳式换热器的种类和工艺流程。
2、管壳式换热器的工艺计算和主要的工艺尺寸设计。
3、设计结果概要或设计结果一览表。
4、设备简图(要求按比例画出主要结构及尺寸)。
5、对本设计的评述及有关问题的讨论。
第1章设计概述1、1热量传递的概念与意义[1](205)1、1、1 传热的概念所谓的传热(又称热传递)就是间壁两侧两种流体之间的热量传递问题。
由热力学第二定律可知,凡是有温差存在时,就必然发生热量从高温处传递到低温处,因此传热是自然界和工程技领域中极普遍的一种传递现象。
1、1、2 传热的意义化工生产中的很多过程和单元操作,都需要进行加热和冷却,如:化学反应通常要在一定的温度进行,为了达到并保持一定温度,就需要向反应器输入或输出热量,又如在蒸发、蒸馏、干燥等单元操作中,都要向这些设备输入或输出热量。
所以传热是最常见的重要单元操作之一。
无论是在能源,宇航,化工,动力,冶金,机械,建筑等工业部门,还是在农业,环境等部门中都涉及到许多有关传热的问题。
此外,化工设备的保温,生产过程中热能的合理利用以及废热的回收利用等都涉及到传热的问题,由此可见;传热过程普遍的存在于化工生产中,且具有极其重要的作用。
归纳起来化工生产中对传热过程的要求经常有以下两种情况:①强化传热过程,如各种换热设备中的传热。
②削弱传热过程,如设备和管道的保温,以减少热损失。
1、2 换热器的概念与意义[2]1、2、1 换热器的概念在不同温度的流体间传递热能的装置称为热交设备,简称为换热器。
在换热器中至少要有两种不同的流体,一种流体温度较高,放出热量:另一种流体则温度较低,吸收热量。
化工原理课程设计-标准系列管壳式立式冷凝器的设计

化工原理课程设计标准系列管壳式立式冷凝器的设计姓名:学号:专业:应用化学班级设计时间:目录一、设计题目二、设计条件三、设计内容3.1概述3.2 换热3.3 换热设备设计步骤四、设计说明4.1选择换热器的类型4.2流动空间的确定五、传热过程工艺计算5.1计算液体的定性温度,确定流体的物性数据5.1.1正戊烷流体在定性温度(51.7℃)下的物性数据5.1.2水的定性温度5.2估算传热面积5.2.1换热器热负荷计算5.2.2平均传热温差5.2.3估算传热面积5.2.4初选换热器规格5.2.5立式固定管板式换热器的规格5.2.6计算面积裕度H及该换热器所要求的总传热系数K05.2.7折流板5.2.8换热器核算5.3核算壁温与冷凝液流型5.3.1核算壁温5.3.2核算流型5.4计算接口直径5.4.1计算壳程接口直径5.5计算管程接口直径5.6计算压强降5.6.1计算管程压降5.6.2计算壳程压降六、其他七、计算结果八、化工课程设计心得九、参考文献一.设计题目标准系列管壳式立式冷凝器的设计二.设计条件生产能力:正戊烷23760t/a,冷凝水流量70000Kg/h操作压力:常压正戊烷的冷凝温度51.7℃,冷凝水入口温度32℃每年按330天计,每天24小时连续生产要求冷凝器允许压降100000Pa三、设计内容3.1概述换热器在石油、化工生产中应用非常广泛。
在炼油厂中,原油常减压蒸馏装置中换热器的投资占总投资的20%;在化工厂中,换热器约占总投资的11%以上。
由于在工业生产中所用换热器的目的和要求不同,所以换热器的种类也多种多样。
列管式换热器在石油化工生产中应用最为广泛,而且技术上比较成熟。
在不同温度的流体间传递热能的装置称为热交换器,简称为换热器。
在换热器中至少要有两种温度不同的流体,一种流体温度较高,放出热量;另一种流体则温度较低,吸收热量。
35%~40%。
随着我国工业的不断发展,对能源利用、开发和节约的要求不断提高,因而对换热器的要求也日益加强。
管壳式换热器设计-课程设计
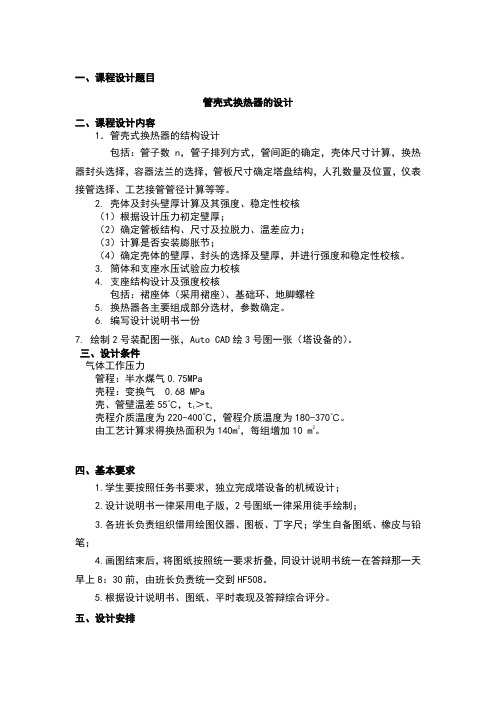
一、课程设计题目管壳式换热器的设计二、课程设计内容1.管壳式换热器的结构设计包括:管子数n,管子排列方式,管间距的确定,壳体尺寸计算,换热器封头选择,容器法兰的选择,管板尺寸确定塔盘结构,人孔数量及位置,仪表接管选择、工艺接管管径计算等等。
2. 壳体及封头壁厚计算及其强度、稳定性校核(1)根据设计压力初定壁厚;(2)确定管板结构、尺寸及拉脱力、温差应力;(3)计算是否安装膨胀节;(4)确定壳体的壁厚、封头的选择及壁厚,并进行强度和稳定性校核。
3. 筒体和支座水压试验应力校核4. 支座结构设计及强度校核包括:裙座体(采用裙座)、基础环、地脚螺栓5. 换热器各主要组成部分选材,参数确定。
6. 编写设计说明书一份7. 绘制2号装配图一张,Auto CAD绘3号图一张(塔设备的)。
三、设计条件气体工作压力管程:半水煤气0.75MPa壳程:变换气 0.68 MPa壳、管壁温差55℃,tt >ts壳程介质温度为220-400℃,管程介质温度为180-370℃。
由工艺计算求得换热面积为140m2,每组增加10 m2。
四、基本要求1.学生要按照任务书要求,独立完成塔设备的机械设计;2.设计说明书一律采用电子版,2号图纸一律采用徒手绘制;3.各班长负责组织借用绘图仪器、图板、丁字尺;学生自备图纸、橡皮与铅笔;4.画图结束后,将图纸按照统一要求折叠,同设计说明书统一在答辩那一天早上8:30前,由班长负责统一交到HF508。
5.根据设计说明书、图纸、平时表现及答辩综合评分。
五、设计安排六、说明书的内容1.符号说明2.前言(1)设计条件;(2)设计依据;(3)设备结构形式概述。
3.材料选择(1)选择材料的原则;(2)确定各零、部件的材质;(3)确定焊接材料。
4.绘制结构草图(1)换热器装配图(2)确定支座、接管、人孔、控制点接口及附件、内部主要零部件的轴向及环向位置,以单线图表示;(3)标注形位尺寸。
(4)写出图纸上的技术要求、技术特性表、接管表、标题明细表等5.壳体、封头壁厚设计(1)筒体、封头及支座壁厚设计;(2)焊接接头设计;(3)压力试验验算;6.标准化零、部件选择及补强计算:(1)接管及法兰选择:根据结构草图统一编制表格。
冷凝器计算书
= 12.47m / s
-7-
Reo
=
deuo ρ气 µ气
=
0.02×12.47 × 4.76 0.00008
= 14839.3
fo = 5 ×14839.3−0.288 = 0.175
NTC = 1.1NT 0.5 = 1.1× 2220.5 = 16.39
N B = 14
∆po
= 0.5×0.175×16.39×(14+1)×
= 861.2Pa
对 φ25× 2.5m m 的管子有 Ft = 1.5, 且N p = 2, Ns = 1
∑ ∆pi = (∆p1 + ) ∆p2 Ft N p N s = (1421 + 861.2)×1.5 × 2 ×1 = 6846.6Pa <30KPa
管程压降在允许范围之内。 (2)计算壳程压降
ns
=
π 4
V di 2u
=
13.2 / 994 0.785 × 0.022 ×1.0
=
42.3
≈
43 (根)
按单程管计算,所需的传热管长度为
L= Ap =
38.2
≈ 12m
πd ons 3.14 × 0.025 × 43
按单程管设计,传热管过长,宜采用多管程结构。根据本设计实际情况,现
取传热管长 l=3m,则该换热器的管程数为
随着经济的发展,各种不同型式和种类的换热器发展很快,新结构、新材料的换热 器不断涌现。为了适应发展的需要,我国对某些种类的换热器已经建立了标准,形成了 系列。完善的换热器在设计或选型时应满足以下基本要求:
(1) 合理地实现所规定的工艺条件; (2) 结构安全可靠; (3) 便于制造、安装、操作和维修; (4) 经济上合理。 换热器的应用广泛,日常生活中取暖用的暖气散热片、汽轮机装置中的凝 汽 器 和航 天火箭上的油冷却器等,都是换热器。它还广泛应用于 化工、石油、动力和原子能等
列管式煤油冷却器的工艺设计
列管式煤油冷却器的工艺设计1.引言列管式煤油冷却器作为工业生产过程中的重要设备之一,其工艺设计直接关系到生产效率和产品质量。
本文将介绍列管式煤油冷却器的工艺设计原理、参数计算以及设计注意事项。
2.工艺设计原理列管式煤油冷却器是通过将热交换管束与冷却介质进行传热交换,使煤油的温度降低,从而提高其可靠性和性能稳定性。
其工艺设计原理主要包括热交换器类型选择、传热方式选择和流量计算等。
2.1热交换器类型选择根据煤油的使用要求和工艺条件,可以选择不同类型的列管式煤油冷却器,如管壳式、管束式、管板式等。
在选择时需考虑煤油流量、压力损失、传热效果和清洗维护等因素。
2.2传热方式选择传热方式的选择在很大程度上影响着煤油冷却器的传热效率和能耗。
常见的传热方式包括对流传热、传导传热和辐射传热。
通过合理选择传热方式,可以提高传热效率和节约能源。
2.3流量计算煤油冷却器的流量计算是工艺设计中的关键步骤之一,直接影响到传热效果和生产效率。
流量计算需要考虑煤油进出口温度、流量、压力以及热交换系数等因素,并结合经验数据进行计算。
3.工艺设计参数计算在进行列管式煤油冷却器的工艺设计时,需要对一些重要参数进行计算,以保证煤油冷却器的正常运行和传热效果。
3.1煤油流量计算煤油流量计算是工艺设计中的重要环节,其计算公式为:$$Q=\f ra c{{m\c do tCp\cd ot(T1-T2)}}{{3600}}$$其中,Q为煤油的流量(m³/h),m为煤油的质量流量(kg/h),C p 为煤油的比热容(J/k g·℃),T1为煤油的进口温度(℃),T2为煤油的出口温度(℃)。
3.2热交换面积计算热交换面积的计算是工艺设计的关键环节,其计算公式为:$$A=\f ra c{{Q}}{{U\c d ot\D el ta T}}$$其中,A为煤油冷却器的热交换面积(m²),Q为煤油的流量(m³/h),U为煤油冷却器的传热系数(W/m²·℃),ΔT为煤油平均温差(℃)。
ASME中国制造-标准系列化管壳式换热器的设计计算步骤
565 427 / 427100% 32.3%
表明该换热器的传热面积裕度符合要求。 (5)核算壁温与冷凝液流型 核算壁温时,一般忽略管壁热阻,按以下近似计算公式计算
T tw t tw 51.7 t w t 35.67 w 1 1 1 1 Rso Rsi 0.000172 0.0002 αo αi 1051 3736
ρ 596kg/m3, μ 1.8 104 Pa s, c p 2.34kJ/kg C,λ 0.13W/m C,r 357.4kJ/kg。
井水的定性温度: 入口温度为 t1
32C ,出口温度为
t2
ms1r t ms 2 c p 2 1
2.376104 103 / 330 24 3000kg/h 0.833kg/s 3000 357.4 t2 32 35.67C 70000 4.174 井水的定性温度为 t m 32 35.67 / 2 33.84 C 两流体的温差 Tm t m 51.7 33.84 17.86 C 50 C ,故选固定管板式换热器
非标准系列化列管式换热器的设计计算步骤
(1)了解换热流体的物理化学性质和腐蚀性能 (2)计算传热量,并确定第二种流体的流量 (3)确定流体进入的空间 (4)计算流体的定性温度,确定流体的物性数据 (5)计算有效平均温度差,一般先按逆流计算,然后再校核 (6)选取管径和管内流速 (7)计算传热系数,包括管程和壳程的对流传热系数,由于壳程对流传热系数与壳径、管束等结构有关, 因此,一般先假定一个壳程传热系数,以计算 K,然后再校核 (8)初估传热面积,考虑安全因素和初估性质,常采用实际传热面积为计算传热面积值的 1.15~1.25 倍 (9)选取管长 (10)计算管数 (11)校核管内流速,确定管程数 (12)画出排管图,确定壳径和壳程挡板形式及数量等 (13)校核壳程对流传热系数 (14)校核平均温度差 (15)校核传热面积 (16)计算流体流动阻力。若阻力超过允许值,则需调整设计。
255吨每小时U形管式冷却器设计
摘要本文介绍了U型管冷却器的整体结构设计计算。
U型管冷却器仅有一个管板,管子两端均固定于同一管板上,管子可以自由伸缩,无热应力,热补偿性能好;管程采用双管程,流程较长,流速较高,传热性能较好,承压能力强,管束可从壳体内抽出,便于检修和清洗,且结构简单,造价便宜。
U型管式冷却器的主要结构包括管箱、筒体、封头、换热管、接管、折流板、防冲板和导流筒、防短路结构、支座及管壳程的其他附件等。
换热器的设计工作主要有换热器综述,换热器的工艺计算以及结构强度计算。
其中换热器工艺计算中需要根据初始数据计算其处理量以及工艺参数,换热器的结构强度计算主要集中在折流板,筒体以及开口上。
换热器是化学工艺生产中重要的设备之一,它是一种冷热流体间的传递热量的设备,他们的使用条件和要求差别很大,如容量,温度,压力和工作介质的性质等,涉及的种类很多,因此换热器的结构形式也多种多样。
U形管换热器仅有一个管板,管束可从壳体内抽出,便于检修和清洗,而且结构简单,造价便宜。
U形管换热器主要结构包括筒体,封头,换热管,接管,折流板,防冲板,导流筒,防短路结构,支座和管壳层的其他设备等。
本次设计为二类压力容器,设计温度和设计压力都较高,因而设计要求高。
冷却器采用双管程,不锈钢换热管制造。
设计中主要进行了冷却器的结构设计,强度设计以及零部件的选型和工艺设计。
关键词: U型管冷却器;结构;强度;设计计算AbstractThis paper introduces the U-tube heat exchanger design and calculation. U-tube heat exchanger has only one tube sheet, tubes are fixed at both ends of boards in the same tube, and tubes could telescopic freely, non-thermal stress, thermal performance and compensation; use of double-tube process, the process is longer, higher speed, better heat transfer performance, pressure capacity, and control can be extracted from the shell with easy maintenance and cleaning, and simple structure cost less. The main structure of U-tube heat exchanger, includes Equipment control, shell, head, exchanger tubes, nozzles, baffled, impingement baffle, guide shell, anti-short-circuit structure, support and other shell-tube accessories.This time I designed a second category pressure vessel, which has high design temperature and high design pressure. Thus the design demands are strict. It has dual heat exchanger tube, stainless steel heat exchanger manufacturers. I mainly carried out the design of heat exchanger structural design, strength of design and parts selection and process design.The design for the second category pressure vessel, design temperature and design pressure are high, so the design requirements is high. Double tube heat exchange, heat transfer tubes of stainless steel manufacturing. Design mainly for the design, selection and process design and strength design of heat exchange components.Key words: U-tube heat exchanger; Frame; Intensity; Design and calculation目录第一章绪论 (1)第二章换热器传热工艺计算 (3)2.1起始数据 (3)2.2定性温度及确定其物性参数 (3)2.3热量守恒与油流量的计算 (3)2.4有效平均温度的公式计算 (4)2.5管程换热系数的计算 (4)2.6 结构的初步设计 (5)2.7壳程换热系数计算 (5)2.8 传热系数计算 (6)2.9 管壁温度计算 (7)2.10 壳程压力降计算 (7)2.11 管程压力降计算 (7)第三章管壳式冷却器的类型、结构与型号 (9)3.1 主要设计参数 (9)3.2 冷却器的零部件名称 (9)3.3 冷却器的主要组合部件 (9)第四章冷却器材料选择 (11)4.1 选材原则 (11)第五章冷却器结构设计 (12)5.1 壁厚的确定 (12)5.2 管箱圆筒短节设计 (13)5.3 壳体圆筒设计 (14)5.4 封头设计[1~3] (15)5.4.1 后封头计算 (16)5.4.2 管箱封头计算 (17)5.5 换热管设计 (18)5.5.1 换热管的规格和尺寸偏差 (18)5.5.2 U形管的尺寸 (19)5.5.3 管子的几种排列方式 (19)5.5.4 布管限定圆 (20)5.6 管板设计 (21)5.7 管箱结构设计 (22)5.7.1 管箱的最小内侧深度 (22)5.7.2 分程隔板 (22)第六章冷却器其他各部件结构 (24)6.1 进出口接管设计 (24)6.1.1 接管法兰设计 (24)6.1.2 接管外伸长度 (26)6.1.3 接管开孔补强的设计计算 (26)6.1.4 接管最小位置 (30)6.1.5 壳程接管位置的最小尺寸 (30)6.1.6 管箱接管位置的最小尺寸 (30)6.2 管板法兰设计 (31)6.2.1 垫片的设计 (31)6.2.2 螺栓设 (32)6.2.3 法兰设计 (34)6.3 折流板 (37)6.3.1 折流板尺寸 (37)6.3.2 折流板的布置 (38)6.4 拉杆与定距管 (39)6.4.1 拉杆的结构型式 (39)6.4.2 拉杆的直径和数量 (39)6.4.3 拉杆的尺寸 (39)6.4.4 拉杆的布置 (40)6.5 防冲与导流 (40)6.5.1 防冲板的形式 (40)6.5.2 防冲板的位置和尺寸 (41)6.5.3 导流筒 (41)6.6 双壳程结构 (41)6.7 防短路结构 (42)6.7.1 旁路挡板的结构尺寸 (42)6.7.2 挡管 (42)6.7.3 中间挡板 (42)6.8 鞍座 (43)结论 (44)参考文献 (45)致谢 (46)第一章绪论能源是当前人类面临的重要问题之一,随着时间的推移,人类对能源的需求越来越急,为此它却成为我们生活中的重要部分,这个过程中冷却器是能源转换的重要组成,其应用面涵盖整个工业领域,它应用尤为广泛。