磷化处理影响因素及常见问题
磷化常见问题和处理方法

磷化常见问题及处理方法常见故障原因分析1、磷化膜结晶粗糙多孔:原因:1)游离酸过高。
2)硝酸根不足。
3)零件表面有残酸,加强中和及清洗。
4)Fe2+过高,用双氧水调整。
5)零件表面过腐蚀,控制酸洗浓度和时间。
2、膜层过薄,无明显结晶:原因:1)总酸度过高,加水稀释或加磷酸盐调整酸的比值。
2)零件表面有硬化层,用强酸腐蚀或喷砂处理。
3)亚铁含量过低,补充磷酸二氢铁。
4)温度低。
3、磷化膜耐腐蚀性差和生锈原因:1)磷化晶粒过粗或过细,调整游离酸和总酸度比值。
2)游离酸含量过高。
3)金属过腐蚀。
4)溶液中磷酸盐含量不足。
5)零件表面有残酸。
6)金属表面锈没有出尽。
4、磷化零件表面有白色沉淀:原因:1)溶液中沉淀物过多。
2)硝酸根不足。
3)锌、铁、P2O5含量高。
5、磷化膜不易形成:原因:1)零件表面有加工硬化层2)溶液里SO-2含量高,用钡盐处理。
3)溶液渗入杂质,更换磷化溶液。
4)P2O5含量过低,补充磷酸盐。
6、磷化层不均、发花:原因:1)除油不净、温度太低。
2)零件表面有钝化状态,加强酸洗或喷砂。
3)零件因热处理加工方法不同。
7、冷挤压后磷化膜产生条状脱落:原因:1)肥皂溶液里有杂质。
2)皂化前零件表面有杂质和沉淀物,重新磷化。
8、磷化膜发红抗蚀能力下降:原因:1)酸洗液里铁渣附在表面。
2)铜离子渗入磷化液磷化常见故障及处理方法冷挤压后磷化膜产生条状脱落1、肥皂溶液里有杂质;2、皂化前零件表面有杂质和沉淀物,重新磷化;3、磷化年热处理加工方法不同。
磷化膜发红抗蚀能力降低1、酸洗液里铁渣附在表面;2、离子渗入磷溶液。
磷化膜结晶粗大的原因及处理方法原因:①亚铁离子含量过多;②零件表面带有残酸;③溶液里硝酸根不足;④溶液里硫酸根含量增高;⑤零件表面过腐蚀。
处理方法:①用压缩空气搅拌,或用双氧水降低亚铁离子含量,升高温度;②加强中和或水洗;③添加硝酸锌;④用碳酸钡处理硫酸根;⑤控制酸的浓度和时间。
质量问题外观现象产生原因解决方法1、无磷化膜或磷化膜不易形成工件整体或局部无磷化膜,有时发蓝或有空白片(1)工件表面有硬化层;(2)总酸度不够;(3)处理温度低(4)游离酸太低(5)脱脂不净或磷化时间偏短;(6)工件表面聚集氢气;(7)磷化槽液比例失调,如P2O5含量过低;(8)工件重叠或工件之间发生接触方法:(1)改进加工方法或用酸洗、喷砂去除硬化层、达到表面处理要求;(2)补加磷化剂:(3)升高磷化槽液温度;(4)补加磷化剂;(5)加强脱脂或延长磷化时间;(6)翻动工件或改变工件位置;(7)调整或更换磷化槽液;(8)注意增大工件间隙,避免接触2、磷化膜过薄磷化膜太薄、结晶过细或无明显结晶,抗蚀性能差。
磷化处理影响因素及常见问题审批稿

磷化处理影响因素及常见问题YKK standardization office【 YKK5AB- YKK08- YKK2C- YKK18】一、磷化工艺参数的影响1、总酸度————总酸度过低、磷化必受影响,因为总酸度是反映磷化液浓度的一项指标。
控制总酸度的意义在于使磷化液中成膜离子浓度保持在必要的范围内。
2、游离酸度————游离酸度过高、过低均会产生不良影响。
过高不能成膜,易出现黄锈;过低磷化液的稳定性受威胁,生成额外的残渣。
游离酸度反映磷化液中游离H+的含量。
控制游离酸度的意义在于控制磷化液中磷酸二氢盐的离解度,把成膜离子浓度控制在一个必须的范围。
磷化液在使用过程中,游离酸度会有缓慢的升高,这时要用碱来中和调整,注意缓慢加入,充分搅拌,否则碱液局部过浓会产生不必要的残渣,出现越加碱,游离酸度越高的现象。
单看游离酸度和总酸度是没有实际意义的,必须一起考虑。
3、酸比————酸比即指总酸度与游离酸度的比值。
一般的说酸比都在5~30的范围内。
酸比较小的配方,游离酸度高,成膜速度慢,磷化时间长,所需温度高。
酸比较大的配方,成膜速度快,磷化时间短,所需温度低。
因此必须控制好酸比。
4、温度————磷化处理温度与酸比一样,也是成膜的关键因素。
不同的配方都有不同的温度范围,实际上,他在控制着磷化液中的成膜离子的浓度。
温度高,磷酸二氢盐的离解度大,成膜离子浓度相应高些,因此可以利用此种关系在降低温度的同时提高酸比,同样可达到成膜,其关系如下:70℃ 60℃ 50℃ 40℃ 30℃ 20℃1/5 1/7 1/10 1/15 1/20 1/25生产单位确定了某一配方后,就应该严格控制好温度,温度过高要产生大量沉渣,磷化液失去原有平衡。
温度过低,成膜离子浓度总达不到浓度积,不能生成完整磷化膜。
温度过高,磷化液中可溶性磷酸盐的离解度加大,成膜离子浓度大幅度提高,产生不必要的沉渣,白白浪费了磷化液中的有效成分,原有的平衡被迫坏,形成一个新的温度下的平衡,如,低温磷化液在温度失控而升高时,H2PO4→H++PO43- 的离解反应向右进行,从而使磷酸根浓度升高,产生磷酸锌沉淀,使磷化液的酸比自动升高。
磷化处理影响因素及常见问题

磷化处理影响因素及常见问题一、磷化工艺参数的影响1、总酸度————总酸度过低、磷化必受影响,因为总酸度是反映磷化液浓度的一项指标。
控制总酸度的意义在于使磷化液中成膜离子浓度保持在必要的范围内。
2、游离酸度————游离酸度过高、过低均会产生不良影响。
过高不能成膜,易出现黄锈;过低磷化液的稳定性受威胁,生成额外的残渣。
游离酸度反映磷化液中游离H+的含量。
控制游离酸度的意义在于控制磷化液中磷酸二氢盐的离解度,把成膜离子浓度控制在一个必须的范围。
磷化液在使用过程中,游离酸度会有缓慢的升高,这时要用碱来中和调整,注意缓慢加入,充分搅拌,否则碱液局部过浓会产生不必要的残渣,出现越加碱,游离酸度越高的现象。
单看游离酸度和总酸度是没有实际意义的,必须一起考虑。
3、酸比————酸比即指总酸度与游离酸度的比值。
一般的说酸比都在5~30的范围内。
酸比较小的配方,游离酸度高,成膜速度慢,磷化时间长,所需温度高。
酸比较大的配方,成膜速度快,磷化时间短,所需温度低。
因此必须控制好酸比。
4、温度————磷化处理温度与酸比一样,也是成膜的关键因素。
不同的配方都有不同的温度范围,实际上,他在控制着磷化液中的成膜离子的浓度。
温度高,磷酸二氢盐的离解度大,成膜离子浓度相应高些,因此可以利用此种关系在降低温度的同时提高酸比,同样可达到成膜,其关系如下:70℃ 60℃ 50℃ 40℃ 30℃ 20℃Fe+2H+→Fe2++H2↑这个反应能够消耗大量的氢离子,促使固液界面的PH上升,进而促使磷化液中的磷酸二氢盐的三级离解平衡右移,以致使锌离子浓度和磷酸根浓度在界面处达到溶度积而成膜。
如果不添加一些有效物质,阴极析出的氢气的滞留会造成阴极极化,使反应不能继续进行,因而磷酸盐膜的沉积也不能连续下去。
因此凡能加速这个反应的物质,必能加速磷化。
氧化剂正是起着阴极去极化的作用而加速反应。
常用的氧化剂有硝酸盐、亚硝酸盐、双氧水、溴酸盐、碘酸盐、钼酸盐、有机硝基化合物、有机过氧化物等。
磷化处理影响因素及常见问题
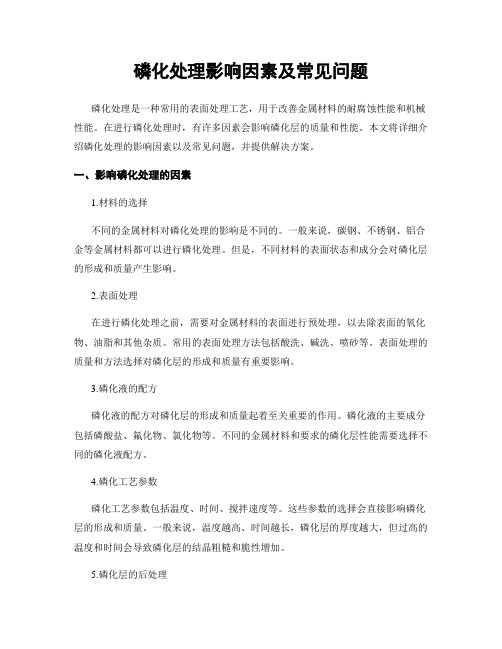
磷化处理影响因素及常见问题磷化处理是一种常用的表面处理工艺,用于改善金属材料的耐腐蚀性能和机械性能。
在进行磷化处理时,有许多因素会影响磷化层的质量和性能。
本文将详细介绍磷化处理的影响因素以及常见问题,并提供解决方案。
一、影响磷化处理的因素1.材料的选择不同的金属材料对磷化处理的影响是不同的。
一般来说,碳钢、不锈钢、铝合金等金属材料都可以进行磷化处理。
但是,不同材料的表面状态和成分会对磷化层的形成和质量产生影响。
2.表面处理在进行磷化处理之前,需要对金属材料的表面进行预处理,以去除表面的氧化物、油脂和其他杂质。
常用的表面处理方法包括酸洗、碱洗、喷砂等。
表面处理的质量和方法选择对磷化层的形成和质量有重要影响。
3.磷化液的配方磷化液的配方对磷化层的形成和质量起着至关重要的作用。
磷化液的主要成分包括磷酸盐、氟化物、氯化物等。
不同的金属材料和要求的磷化层性能需要选择不同的磷化液配方。
4.磷化工艺参数磷化工艺参数包括温度、时间、搅拌速度等。
这些参数的选择会直接影响磷化层的形成和质量。
一般来说,温度越高、时间越长,磷化层的厚度越大,但过高的温度和时间会导致磷化层的结晶粗糙和脆性增加。
5.磷化层的后处理磷化层形成后,需要进行后处理,以提高磷化层的耐腐蚀性能和机械性能。
常用的后处理方法包括中和、封闭、涂覆等。
后处理的质量和方法选择对磷化层的性能有重要影响。
二、常见问题及解决方案1.磷化层不均匀磷化层不均匀可能是由于磷化液的搅拌不均匀、材料表面存在油脂或氧化物等杂质、磷化液配方不合理等原因造成的。
解决方法包括加强搅拌、提高表面处理质量、优化磷化液配方等。
2.磷化层结晶粗糙磷化层结晶粗糙可能是由于磷化液温度过高、时间过长、磷化液配方不合理等原因造成的。
解决方法包括控制磷化液的温度和时间、优化磷化液配方等。
3.磷化层附着力差磷化层附着力差可能是由于材料表面存在油脂、氧化物等杂质、磷化液配方不合理等原因造成的。
解决方法包括提高表面处理质量、优化磷化液配方等。
磷化处理影响因素及常见问题

磷化处理影响因素及常见问题一、磷化工艺参数的影响1、总酸度————总酸度过低、磷化必受影响,因为总酸度是反映磷化液浓度的一项指标。
控制总酸度的意义在于使磷化液中成膜离子浓度保持在必要的范围内。
2、游离酸度————游离酸度过高、过低均会产生不良影响。
过高不能成膜,易出现黄锈;过低磷化液的稳定性受威胁,生成额外的残渣。
游离酸度反映磷化液中游离H+的含量。
控制游离酸度的意义在于控制磷化液中磷酸二氢盐的离解度,把成膜离子浓度控制在一个必须的范围。
磷化液在使用过程中,游离酸度会有缓慢的升高,这时要用碱来中和调整,注意缓慢加入,充分搅拌,否则碱液局部过浓会产生不必要的残渣,出现越加碱,游离酸度越高的现象。
单看游离酸度和总酸度是没有实际意义的,必须一起考虑。
3、酸比————酸比即指总酸度与游离酸度的比值。
一般的说酸比都在5~30的范围内。
酸比较小的配方,游离酸度高,成膜速度慢,磷化时间长,所需温度高。
酸比较大的配方,成膜速度快,磷化时间短,所需温度低。
因此必须控制好酸比。
4、温度————磷化处理温度与酸比一样,也是成膜的关键因素。
不同的配方都有不同的温度范围,实际上,他在控制着磷化液中的成膜离子的浓度。
温度高,磷酸二氢盐的离解度大,成膜离子浓度相应高些,因此可以利用此种关系在降低温度的同时提高酸比,同样可达到成膜,其关系如下:70℃ 60℃ 50℃ 40℃ 30℃ 20℃1/5 1/7 1/10 1/15 1/20 1/25生产单位确定了某一配方后,就应该严格控制好温度,温度过高要产生大量沉渣,磷化液失去原有平衡。
温度过低,成膜离子浓度总达不到浓度积,不能生成完整磷化膜。
温度过高,磷化液中可溶性磷酸盐的离解度加大,成膜离子浓度大幅度提高,产生不必要的沉渣,白白浪费了磷化液中的有效成分,原有的平衡被迫坏,形成一个新的温度下的平衡,如,低温磷化液在温度失控而升高时,H2PO4→H++PO43- 的离解反应向右进行,从而使磷酸根浓度升高,产生磷酸锌沉淀,使磷化液的酸比自动升高。
磷化处理工艺
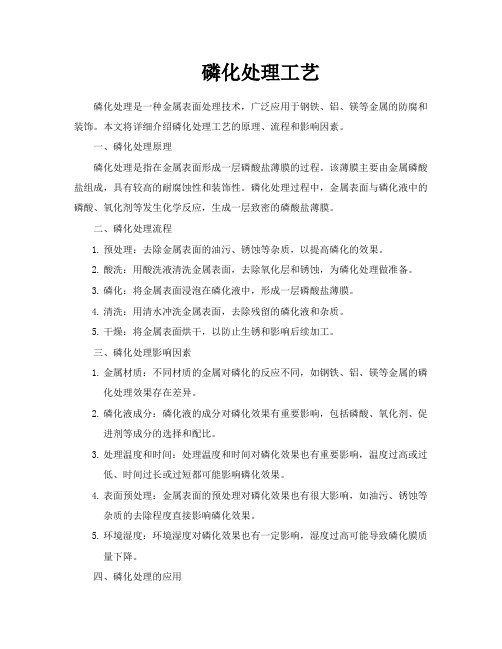
磷化处理工艺磷化处理是一种金属表面处理技术,广泛应用于钢铁、铝、镁等金属的防腐和装饰。
本文将详细介绍磷化处理工艺的原理、流程和影响因素。
一、磷化处理原理磷化处理是指在金属表面形成一层磷酸盐薄膜的过程。
该薄膜主要由金属磷酸盐组成,具有较高的耐腐蚀性和装饰性。
磷化处理过程中,金属表面与磷化液中的磷酸、氧化剂等发生化学反应,生成一层致密的磷酸盐薄膜。
二、磷化处理流程1.预处理:去除金属表面的油污、锈蚀等杂质,以提高磷化的效果。
2.酸洗:用酸洗液清洗金属表面,去除氧化层和锈蚀,为磷化处理做准备。
3.磷化:将金属表面浸泡在磷化液中,形成一层磷酸盐薄膜。
4.清洗:用清水冲洗金属表面,去除残留的磷化液和杂质。
5.干燥:将金属表面烘干,以防止生锈和影响后续加工。
三、磷化处理影响因素1.金属材质:不同材质的金属对磷化的反应不同,如钢铁、铝、镁等金属的磷化处理效果存在差异。
2.磷化液成分:磷化液的成分对磷化效果有重要影响,包括磷酸、氧化剂、促进剂等成分的选择和配比。
3.处理温度和时间:处理温度和时间对磷化效果也有重要影响,温度过高或过低、时间过长或过短都可能影响磷化效果。
4.表面预处理:金属表面的预处理对磷化效果也有很大影响,如油污、锈蚀等杂质的去除程度直接影响磷化效果。
5.环境湿度:环境湿度对磷化效果也有一定影响,湿度过高可能导致磷化膜质量下降。
四、磷化处理的应用1.防腐:磷化膜具有较高的耐腐蚀性,可用于钢铁、铝、镁等金属的防腐处理。
例如,在建筑、船舶、汽车等领域,磷化处理被广泛应用于金属结构的防腐保护。
2.装饰:磷化膜具有较好的装饰性,可用于金属表面的美化处理。
例如,在电子产品、家具等领域,磷化处理被广泛应用于产品的外观装饰。
3.耐磨:磷化膜还具有较好的耐磨性,可用于提高金属表面的耐磨性能。
例如,在机械零件、工具等领域,磷化处理被广泛应用于提高产品的耐磨性能。
4.粘合:磷化膜还可以作为粘合剂使用,将不同金属材料粘合在一起。
常见磷化质量问题及解决方法
5
磷化膜发花
磷化膜不均匀,有明显流挂痕迹
1.除油不干净
2.表调剂效果不佳或已失效
3.磷化槽液喷淋不均匀
4.工件表面钝化
5.磷化温度低
1.强脱脂或更换脱脂剂
2.更换或补充表调剂
3.检查并调整喷嘴
4.加强酸洗或喷砂
5.提高磷化温度
6
磷化膜发黑
局部呈黑条状,膜黑且粗糙
1.促进剂浓度太低
常见磷化质量问题及解决方法(总2页)
常见磷化质量问题及解决方法
序号
质量
外观
外观
现 象
产生原因
解决方法
1
无磷化膜或磷化膜不易形成
工件整体或局部无磷化膜,有时发蓝或有空白片
1.工件表面有硬化层
2.总酸度不够
3.处理温度低
4.游离酸太低
5.脱脂不净或磷化时间偏短
6.工件表面聚齐氢气
7.磷化槽液比例失调,如P2O5含量过低
2.氧化剂,如高锰酸钾等
3.补充硝酸锌,提高总酸度
11
磷化膜发蓝
磷化膜部分表面产生紫蓝色彩
表调剂的PH值不在工艺范围
2.表调与磷化间隔区的水务喷嘴堵塞
3.磷化槽液的锌离子含量不足
4.磷化槽液的促进剂含量不够
1.补加表调剂或补加Na2CO3,以提高PH值
2.检查、清扫水务喷嘴
3.补加磷化液或硝酸锌
4.补加促进剂
2.降低游离酸含量,可加氧化锌或氢氧化锌
3.控制酸洗过程
4.补充磷酸二氢盐
5.加强中和水洗
6.检查喷嘴并进行清理,检查磷化槽沉淀量
7.提高处理温度
8.逐一检查设备是否运行正常
8
磷化处理工艺流程,磷化的影响因素及用途
磷化处理工艺流程| 磷化的影响因素及用途磷化是什么意思?磷化(phosphorization)是一种化学与电化学反应形成磷酸盐化学转化膜的过程,所形成的磷酸盐转化膜称之为磷化膜。
磷化的目的主要是给基体金属提供保护,在一定程度上防止金属被腐蚀;用于涂漆前打底,提高漆膜层的附着力与防腐蚀能力;在金属冷加工工艺中起减摩润滑使用。
磷化处理工艺应用于工业已有90多年的历史,大致可以分为三个时期:奠定磷化技术基础时期、磷化技术迅速发展时期和广泛应用时期。
磷化处理工艺流程:预脱脂→脱脂→除锈→水洗→(表调)→磷化→水洗→磷化后处理(如电泳或粉末涂装)。
磷化的影响因素:1、温度温度愈高,磷化层愈厚,结晶愈粗大。
温度愈低,磷化层愈薄,结晶愈细。
但温度不宜过高,否则Fe2+易被氧化成Fe3+,加大沉淀物量,溶液不稳定。
2、游离酸度游离酸度指游离的磷酸。
其作用是促使铁的溶解,已形成较多的晶核,使膜结晶致密。
游离酸度过高,则与铁作用加快,会大量析出氢,令界面层磷酸盐不易饱和,导致晶核形成困难,膜层结构疏松,多孔,耐蚀性下降,令磷化时间延长。
游离酸度过低,磷化膜变薄,甚至无膜。
3、总酸度总酸度指磷酸盐、硝酸盐和酸的总和。
总酸度一般以控制在规定范围上限为好,有利于加速磷化反应,使膜层晶粒细,磷化过程中,总酸度不断下降,反映缓慢。
总酸度过高,膜层变薄,可加水稀释。
总酸度过低,膜层疏松粗糙。
4、PH值锰系磷化液一般控制在2-3之间,当PH﹥3时,工件表面易生成粉末。
当PH‹1.5时难以成膜。
铁系一般控制在3-5.5之间。
5、溶液中离子浓度①溶液中Fe2+极易氧化成Fe3+,导致不易成膜。
但溶液中Fe2+浓度不能过高,否则,形成的膜晶粒粗大,膜表面有白色浮灰,耐蚀性及耐热性下降。
②Zn2+的影响,当Zn2+浓度过高,磷化膜晶粒粗大,脆性增大,表面呈白色浮灰;当Zn2+浓度过低,膜层疏松变暗。
磷化用途:(1)耐蚀防护用磷化膜①防护用磷化膜用于钢铁件耐蚀防护处理。
磷化工艺中的各种影响因素
磷化工艺的影响因素磷化膜的质量直接影响与有机膜、涂层的附着力和防护性,影响磷化工件的耐磨、耐微动力磨损和抗擦伤性,以及磷化膜能否成为润滑剂的载体。
磷化膜质量的高低,取决于磷化所采用的工艺是否恰当,磷化过程是否符合工艺要求,因此要十分注意影响磷化工艺的因素。
影响磷化工艺的主要因素有:材质及表面状态、磷化前处理、磷化后处理、磷化液的化学成分等。
下面试就影响磷化工艺的主要因素作一分析。
(一)材质及表面状态。
同是钢铁工件,受含有的其它元素不同,表面晶格是否遭受腐蚀等因素的影响,形成的磷化膜颜色、均匀性、抗腐蚀能力不一样。
低碳钢容易磷化,膜的结晶致密,颜色较浅;中、高碳钢和低合金钢比较容易磷化,结晶有变粗的倾向,磷化膜颜色深;含有较多铬、钼、钨、钒、硅等元素的钢材不容易磷化。
磷化膜随钢材中碳化物含量和分布的不同存在差异,因此,不同钢材应选用不同的磷化工艺和相应的磷化产品。
(二)前处理。
磷化前的表面处理程度是影响磷化质量的重要因素。
因此,要求除净所有的锈迹、油污。
具体要求是,脱脂后的工件,不应有油脂、乳浊液等污物,其表面应能被水完全湿润;酸洗后的工件,不应有目视可见的氧化物、锈及过腐蚀现象.为防止过腐蚀,减轻氢脆,应在酸洗液中加入缓蚀剂.为防止酸雾,酸洗液中可加入酸雾抑制剂;喷抛丸清理后的工件,不应有漏喷、磨料粘附、锈蚀及油污,其表面应露出金属本色.从除油后到磷化前这一过程,工件不允许直接接触手或有油的污物。
经强酸、强碱处理后的钢铁件,一般会增大结晶粒度,增加膜的重量。
水洗是将工件表面从前道处理工序中带出来的残留化学成分除去,防止对下道处理工序的影响。
除油后的不良水洗会使油污再沉积,更多地消耗酸,造成不均匀的酸洗,形成不均匀的磷化膜;酸洗后的不良水洗,导致磷化槽液游离酸度升高,形成稀疏、不均匀的磷化膜,甚至磷化后的工件生锈。
要保证水洗质量,应保持清水的特定pH值或更有效的导电率,延长清洗时间和次数。
(三)后处理。
影响磷化的因素
影响磷化的因素影响磷化的因素影响磷化的因素很多,当磷化膜出现质量问题时,可以从磷化工艺参数、促进剂、磷化工艺(含设备)管理以及被处理钢材表面几大方面考虑。
一、磷化工艺参数的影响1、总酸度————总酸度过低、磷化必受影响,因为总酸度是反映磷化液浓度的一项指标。
控制总酸度的意义在于使磷化液中成膜离子浓度保持在必要的范围内。
2、游离酸度————游离酸度过高、过低均会产生不良影响。
过高不能成膜,易出现黄锈;过低磷化液的稳定性受威胁,生成额外的残渣。
游离酸度反映磷化液中游离H+的含量。
控制游离酸度的意义在于控制磷化液中磷酸二氢盐的离解度,把成膜离子浓度控制在一个必须的范围。
磷化液在使用过程中,游离酸度会有缓慢的升高,这时要用碱来中和调整,注意缓慢加入,充分搅拌,否则碱液局部过浓会产生不必要的残渣,出现越加碱,游离酸度越高的现象。
单看游离酸度和总酸度是没有实际意义的,必须一起考虑。
3、酸比————酸比即指总酸度与游离酸度的比值。
一般的说酸比都在5~30的范围内。
酸比较小的配方,游离酸度高,成膜速度慢,磷化时间长,所需温度高。
酸比较大的配方,成膜速度快,磷化时间短,所需温度低。
因此必须控制好酸比。
4、温度————磷化处理温度与酸比一样,也是成膜的关键因素。
不同的配方都有不同的温度范围,实际上,他在控制着磷化液中的成膜离子的浓度。
温度高,磷酸二氢盐的离解度大,成膜离子浓度相应高些,因此可以利用此种关系在降低温度的同时提高酸比,同样可达到成膜,其关系如下:70℃60℃50℃40℃30℃20℃1/5 1/7 1/10 1/15 1/20 1/25生产单位确定了某一配方后,就应该严格控制好温度,温度过高要产生大量沉渣,磷化液失去原有平衡。
温度过低,成膜离子浓度总达不到浓度积,不能生成完整磷化膜。
温度过高,磷化液中可溶性磷酸盐的离解度加大,成膜离子浓度大幅度提高,产生不必要的沉渣,白白浪费了磷化液中的有效成分,原有的平衡被迫坏,形成一个新的温度下的平衡,如,低温磷化液在温度失控而升高时,H2PO4→H++PO43-的离解反应向右进行,从而使磷酸根浓度升高,产生磷酸锌沉淀,使磷化液的酸比自动升高。
- 1、下载文档前请自行甄别文档内容的完整性,平台不提供额外的编辑、内容补充、找答案等附加服务。
- 2、"仅部分预览"的文档,不可在线预览部分如存在完整性等问题,可反馈申请退款(可完整预览的文档不适用该条件!)。
- 3、如文档侵犯您的权益,请联系客服反馈,我们会尽快为您处理(人工客服工作时间:9:00-18:30)。
一、磷化工艺参数的影响1、总酸度————总酸度过低、磷化必受影响,因为总酸度是反映磷化液浓度的一项指标。
控制总酸度的意义在于使磷化液中成膜离子浓度保持在必要的范围内。
2、游离酸度————游离酸度过高、过低均会产生不良影响。
过高不能成膜,易出现黄锈;过低磷化液的稳定性受威胁,生成额外的残渣。
游离酸度反映磷化液中游离H+的含量。
控制游离酸度的意义在于控制磷化液中磷酸二氢盐的离解度,把成膜离子浓度控制在一个必须的范围。
磷化液在使用过程中,游离酸度会有缓慢的升高,这时要用碱来中和调整,注意缓慢加入,充分搅拌,否则碱液局部过浓会产生不必要的残渣,出现越加碱,游离酸度越高的现象。
单看游离酸度和总酸度是没有实际意义的,必须一起考虑。
3、酸比————酸比即指总酸度与游离酸度的比值。
一般的说酸比都在5~30 的范围内。
酸比较小的配方,游离酸度高,成膜速度慢,磷化时间长,所需温度高。
酸比较大的配方,成膜速度快,磷化时间短,所需温度低。
因此必须控制好酸比。
4、温度————磷化处理温度与酸比一样,也是成膜的关键因素。
不同的配方都有不同的温度范围,实际上,他在控制着磷化液中的成膜离子的浓度。
温度高,磷酸二氢盐的离解度大,成膜离子浓度相应高些,因此可以利用此种关系在降低温度的同时提高酸比,同样可达到成膜,其关系如下:70℃60 ℃50 ℃40 ℃30 ℃20 ℃1/5 1/7 1/10 1/15 1/20 1/25生产单位确定了某一配方后,就应该严格控制好温度,温度过高要产生大量沉渣,磷化液失去原有平衡。
温度过低,成膜离子浓度总达不到浓度积,不能生成完整磷化膜。
温度过高,磷化液中可溶性磷酸盐的离解度加大,成膜离子浓度大幅度提高,产生不必要的沉渣,白白浪费了磷化液中的有效成分,原有的平衡被迫坏,形成一个新的温度下的平衡,如,低温磷化液在温度失控而升高时,H2PO4→H++PO43- 的离解反应向右进行,从而使磷酸根浓度升高,产生磷酸锌沉淀,使磷化液的酸比自动升高。
当磷化液恢复到原有的温度时,原有的平衡并不能恢复。
因此实际中,当磷化液超过一定温度后,再降低到原来的温度时,如果不进行调整,就有可能磷化不上。
从减少沉渣,稳定槽液,保证质量来看,磷化液的温度变化越小越好。
5、时间————各个配方都有规定的工艺时间。
时间过短,成膜量不足,不能形成致密的磷化膜层。
时间过长,由于结晶在已形成的膜上继续生长,可能产生有疏松表面的粗厚膜。
二、促进剂的影响促进剂是必不可少的成分,如果没有他们,磷化将失去意义。
磷化液中的促进剂,主要指某些氧化剂。
氧化剂是作为阴极去极化剂而在磷化配方中采用的一种化学反应型的加速剂。
他的主要作用是加速氢离子在阴极的放电速度,促使磷化第一阶段的酸蚀速度加快,因此可以称为金属腐蚀的催化剂。
当金属表面接触到磷化液时,首先发生以下反应:Fe+2H+→Fe2++H2↑这个反应能够消耗大量的氢离子,促使固液界面的PH上升,进而促使磷化液中的磷酸二氢盐的三级离解平衡右移,以致使锌离子浓度和磷酸根浓度在界面处达到溶度积而成膜。
如果不添加一些有效物质,阴极析出的氢气的滞留会造成阴极极化,使反应不能继续进行,因而磷酸盐膜的沉积也不能连续下去。
因此凡能加速这个反应的物质,必能加速磷化。
氧化剂正是起着阴极去极化的作用而加速反应。
常用的氧化剂有硝酸盐、亚硝酸盐、双氧水、溴酸盐、碘酸盐、钼酸盐、有机硝基化合物、有机过氧化物等。
最常用的主要是硝酸盐、氯酸盐、亚硝酸盐。
亚硝酸盐的缺点是在酸性磷化液中不稳定,容易分解,需不断补充,否则磷化膜极易发黄。
他分解产生的酸气易使未磷化的湿工件生锈。
氯酸盐虽然不能产生酸性气体,在酸液中也稳定,但是他会还原成氯离子。
氯离子在槽液中积累,若随后的水洗不充分,使氯离子留在工件上,会带来很大的后患。
一方面污染电泳槽液,另一方面留在涂层下,会加快腐蚀速度。
过氧化氢尤其独特的优点,他的还原产物是水,他是工业开发中最强的氧化剂。
使用的浓度很低,大约0.01~0.1g/L ,但是他在酸中更不稳定,控制要求很高。
此外还有更巧妙的有机氧化还原剂,比如蒽醌类衍生物。
从原理上看,这上一种不消耗的循环使用的加速剂,他只起氧化载体的作用,利用其氧化性醌先与磷化第一阶段产生的氢气作用,自身被还原成酚,再用强制方法使磷化液与氧气接触,发生还原反应,又恢复成醌,同时给予磷化膜形成反应时必要的氧化电势。
目前工业生产中常用的是硝酸盐、亚硝酸盐、氯酸盐、有机硝基化合物、双氧水的不同组合。
硝酸盐、氯酸盐、有机硝基化合物等在磷化液中都较稳定,除定期抽查外,一般不进行日常检测。
而亚硝酸盐则需随时检测。
浓度不够时,立即反映在磷化膜外观泛黄生锈,因此必须重视。
各种加速剂系统的性能加速剂类型性能1 硝酸盐加速性高,稳定性好2 硝酸盐+亚硝酸盐加速性高,稳定性好3 氯酸盐加速性高,稳定性好,但要还原出氯离子4 氯酸盐+亚硝酸盐加速性高,稳定性低,有氯离子还原出5 高氮有机化合物用量少,稳定性高,但有还原物积累有的色泽深,影响测定6 氯酸盐+有机含氮化合物加速性高,还原物的色泽影响测定7 过氧化氢加速性高,稳定性低8 氯酸盐+亚硝酸盐+硝酸盐加速性高,稳定性低三、被处理钢材表面状态的影响近来的研究发现表明作为磷化膜基底的金属材料的表面状态对磷化质量影响很大。
现归纳如下:1、表面碳的污染钢铁表面碳的污染对磷化处理非常不利,磷化膜质量差。
碳浓度大的钢板耐式性差。
碳浓度高的部位,磷酸锌结晶不能析出,造成磷化膜缺陷,盐雾试验中会早期起泡和剥落。
因此选材时就应注意这一点。
2、钢铁表面氧化膜钢铁表面氧化膜的厚度直接影响磷化及效果。
用偏光分析氧化膜与耐蚀性之间关系后发现:当氧化膜厚度小于16*10-6mm时较好。
氧化膜过厚则耐蚀性差,当出现兰色的氧化膜时,常常磷化不上。
3、钢板表面的结晶方位有报导在改变热处理温度等钢板制造条件时,钢板表面有不同的结晶方位,而结晶方位的不同又影响着磷化性。
实验认为:(111)面反应性高,其在有氧化剂存在时比其他结晶防卫有较大的溶解度,这有利与磷化反应第一步骤——酸蚀,无疑也有利于整个磷化过程。
4、冷轧钢板组成元素在表面浓化对磷化的影响由于热力学和金属物理学方面的原因会使冷轧钢板组成元素在表面浓化,在不同的热处理条件下将出现的锰忽然磷的表面浓化。
当锰浓化高时,磷化反应良好。
另一方面,P 的浓化将延迟晶核的形成和生长,劣化反应性,浓化的P的氧化物,推迟了铁的溶解,使磷化性降低。
而表面的锡、铝、钛、铬、铅等会使磷化结晶粗大,造成耐蚀性降低。
5、镀锌板钝化与采用不同镀锌方式的镀锌板镀锌板是否经过钝化对磷化效果有很大的影响。
经过钝化处理后的镀锌板磷化性差,所生成的结晶杂乱粗大。
热浸镀锌与电镀锌板相比,前者的磷化性差,后者的磷化性好。
各种合金的镀锌板磷化差别也很大。
综上所述,在进行磷化处理前,应该先对所处理的材质进行详细的了解,只有这样,才能选择好合适的工艺及配方。
四、磷化前表面调整处理的影响所谓磷化表面调整句是采用磷化表面调整剂使需要磷化的金属表面改变微观状态,促使磷化过程中形成结晶细小的、均匀、致密的磷化膜。
磷化前零件的表面处理对磷化膜质量影响极大,尤其是酸洗或高温强碱清洗对薄层磷化影响最明显。
研究结果表明,冷轧钢板表面存在着一层厚度为(50~150)*10-10m 的四氧化三铁和三氧化二铁的完整氧化层,磷酸盐结晶就在此基础上生成,得到完整致密的磷化膜。
如果经过酸洗,则只剩下30*10-10m 以下的三氧化二铁氧化层,过于薄且不完整,所以很难得到良好均匀的磷化膜,还因为酸洗表面产生析碳,也影响磷化膜的形成。
对于高温或强碱清洗,由于钢板表面上的活性点转变成氧化物或氢氧化物,使构成磷化膜的结晶晶核减少,因而促使生成稀疏粗大的结晶,影响磷化质量,尤其是低温薄层里边化及低锌磷化对预处理特别敏感,不进行表面调整处理,就难形成磷化膜。
最初采用的是3~5%的草酸水溶液做磷化表面调整剂,现在采用效果更好的磷酸钛胶体溶液处理,由于胶粒表面能很高,对物体表面有极强的吸附作用,胶体微粒吸附在零件表面上形成均匀的吸附层,在磷化时,这层极薄的吸附层就是一层分布均匀,数量极多的磷酸盐结晶晶核,因而促进结晶均匀快速形成,限制了大晶体的生长,结果就促使了磷化膜的细化和致密,提高了成膜性,缩短了磷化时间,降低膜厚,同时也能消除钢铁表面状态的差异对磷化质量的影响。
在工艺生产中,表面调整剂的用量约为0.5g/m2 ,在生产中应注意保持槽液的良好,避免沉淀。
另外应防止碱酸及磷化液进入表面调整工作液,以防止工作液因污染而失效。
五、磷化工艺(含设备)管理方面的影响除了磷化处理剂及被处理钢材的影响外,很多影响因素存在于磷化工艺及管理方面。
1、磷化工艺的设计应合理磷化工艺包括脱脂、除锈、表面调整、磷化、钝化及各工序间的水洗,有的还包括水洗后的烘干。
一般希望除锈工序不安排在前处理生产线上,他会造成很大的弊端。
酸雾对生产线环境的污染易造成零件再度生锈,零件焊缝处很难洗净,造成耐蚀性大幅度下降。
因此要加强防锈,让冷轧板不通过酸洗,非酸洗的在成型前先进行酸洗。
2、前处理的结构是否满足工艺与材料的要求生产实践中,由于窜水、加热系统、除渣系统、加料系统等方面的原因,造成许多磷化质量问题。
这就要求对设备结构进行管理和要求:3、工艺管理工艺管理是必不可少的环节,因此必须严格控制各道工序的工艺参数。
在生产中每天对工艺参数加以检测。
工序控制项目检测频率预脱脂碱度、温度、喷射压力、喷嘴喷射情况脱脂碱度、温度、喷射压力、浸渍搅拌压力、喷嘴情况每班俩次水洗碱度、喷射压力、或浸渍搅拌压力、喷嘴情况表调Ti 浓度、PH值(或总碱度)、喷射搅拌压力喷嘴情况每班数次磷化总酸度、游离酸度、温度、喷射或浸渍搅拌压力、促进剂浓度、磷化膜每班数次外观(目测)、喷嘴情况、换热器进出口压力水洗总酸度(污染度)、喷嘴情况、喷射或浸渍搅拌压力6+ 3+钝化Cr每班俩次、Cr 浓度、PH值、喷射压力、喷嘴工作情况去离子水洗电导率(含滴水电导率)、喷射压力、喷嘴工作情况烘干温度、抽风机情况上述所有控制项目对磷化都有不同程度的影响。
此外,每周要测一次槽液含渣量(要求V//V< 体积分数0.5%),每月测一次脱脂液含油量(要求<4g/L )。
此外,设备维护也很重要,要做到及时换槽。
除磷化液外,一般槽液更换期均不超过三个月。
磷化换热器应定期用硝酸清洗一次,以保证管道畅通。
喷嘴、喷管也要进行疏通,保证畅通。
4、材料间配套及其他相关项目的影响磷化剂与其前后处理材料间有一定相关性。
如酸洗及高碱度的脱脂处理后,钢材表面发生变化,不利于磷化,必须配合表面调整剂才能进行低锌薄膜磷化。
配槽用的工业水质也有较大的影响,某些地区的水质很硬,电导率高达800 μS/cm。