常见磷化质量问题及解决方法
磷化常见故障分析及处理

故障处理方法常温轻质锌:铁系浸渍磷化无膜①促进剂浓度低。
补加促进剂或磷化浓缩剂。
②FA过低。
补加磷酸或磷化浓缩剂(凡工件未经除锈,FA偏高些为好)。
③杂质积累过多。
更换槽液。
成膜速度慢①FA低。
补加磷酸或磷化浓缩剂,控制FA= 2一3点。
②温度低(<50C)。
稍加温。
若无加热条件,适当提高溶液浓度。
部分泛黄生锈①促进剂浓度低。
补加磷化浓缩剂。
②温度低。
稍升温。
③时间短。
延长时间。
挂白灰①磷化前工件生锈。
尽量缩短工件空停时间,提高工序间进度。
②Fe2+积累过多。
更换槽液。
③沉渣黏附。
减少沉渣,加强清渣。
挂黑灰①FA朴。
加人适量碳酸钠降低FA 。
②温度过高。
降温。
③时间过长。
缩短时间,控制5---15min。
④Cu2+浓度过高。
用废钢铁放人槽中,消耗Cu2+。
常(低)温锌系浸渍磷化磷化膜均匀疏松,耐蚀性差或返锈(红锈或黄锈)①工件锈蚀严重,除锈后表面有残酸。
除锈要彻底,充分中和和水洗。
②工件除锈后空停时间过长。
尽量缩短空停时间。
③表调液失效。
更换表调液。
④TA低,FA高。
补加磷化浓缩剂,升高TA;用中和剂降低FA。
控制酸比(25-40):1 ⑤温度低,时间短。
提高温度,延长时间。
⑥硝酸根浓度低。
多发生在新配槽时,补加适量硝酸。
可以调整磷化浓缩剂中硝酸浓度。
⑦促进剂浓度低。
补加促进剂。
⑧Cl-污染磷化液。
除锈后充分水洗。
⑨磷化膜水洗不干净或烘干前受到酸的污染。
水洗干净,避免磷化膜受到酸污染。
膜层局部呈彩色(用指甲划无划痕)①除油不彻底。
调整或更换脱脂液,提高除油后的水洗质量。
②表调不良。
补加表调剂或更换表调液。
③TA太低和FA偏高。
补加磷化浓缩剂,升高TA;用中和剂降低FA. ④促进剂过量,且分布不均匀。
减少促进剂用量或改每日添加为隔日添加。
⑤温度低。
适当升高温度。
膜层呈均匀蓝紫色①前处理不良。
保证除油除锈干净。
②TA太低或FA偏高。
处理同前。
③促进剂浓度过量。
处理同前。
④槽液杂质太多,老化严重。
磷化质量影响因素及其提高途径

磷化质量影响因素及其提高途径引言磷化是一种化学与电化学反应形成磷酸盐化学转化膜的过程。
早在1869年W. A. Ross 就申请了磷化专利技术 [ 2 ] ,随着科技的不断进步,金属磷化处理作为传统的表面处理技术在金属防护、减磨耐磨及涂层打底等方面得到广泛的发展和应用。
磷化处理有多种分类方法:按成膜体系可分为锌系、锌锰系、锰系、铁系、锌钙系及非晶相铁系等六大类;按磷化处理温度可分为常温(不加温)、低温(30~45℃)、中温(60~70℃)、高温(大于80℃)四类;按材质可分为钢铁件、铝件、锌件以及混合件磷化;其它的还有按磷化膜厚度或促进剂类型等分类。
用于防锈磷化的主要有铁系磷化、锌系磷化、锰系磷化三种;用于耐磨减磨磷化的种类有锌系磷化和锰系磷化;而锌锰系和锌钙系主要用于漆前磷化。
一磷化基本原理磷化成膜是一个化学动态平衡,目前,大多数学者认同的磷化原理由以下四个步骤组成:首先是金属的溶解过程。
当金属浸入磷化液中时,先与磷化液中的磷酸作用,生成一代磷酸铁,并有大量的氢气析出。
其化学反应为;Fe –2e→Fe2+2H+ + 2e→H2上式表明,磷化开始时,仅有金属的溶解,而无膜生成。
第二是促进剂加速形成磷化膜。
其化学反应式为:[O]+[H] → [R]+H2OFe2++[O] → Fe3++[R]式中[O]为促进剂(氧化剂),[R]为还原产物,由于促进剂氧化掉第一步反应所产生的氢原子,加快了反应(1)的速度,进一步导致金属表面H+浓度急剧下降。
同时也将溶液中的Fe2+氧化成为Fe3+。
第三是磷酸根的多级离解。
H3PO4→H2PO4-+H+→HPO42-+2H+→PO43-+3H+由于金属表面的H+浓度急剧下降,导致磷酸根各级离解平衡向右移动,最终离解为PO43-。
最后磷酸盐沉淀结晶成为磷化膜当金属表面离解出的PO43-与溶液中(金属界面)的金属离子(如Zn2+、Mn2+、Ca2+、Fe2+)达到溶度积常数Ksp时,就会形成磷酸盐沉淀Zn2++ Fe2++ PO43-+H2O→Zn2Fe(PO4)2·4H2O↓ (4)3Zn2++2PO43-+4H2O=Zn3(PO4)2·4H2O↓ (5)磷酸盐沉淀与水分子一起形成磷化晶核,晶核继续长大成为磷化晶粒,无数个晶粒紧密堆集形而上学成磷化膜。
磷化处理影响因素及常见问题

一、磷化工艺参数的影响1、总酸度————总酸度过低、磷化必受影响,因为总酸度是反映磷化液浓度的一项指标。
控制总酸度的意义在于使磷化液中成膜离子浓度保持在必要的范围内。
2、游离酸度————游离酸度过高、过低均会产生不良影响。
过高不能成膜,易出现黄锈;过低磷化液的稳定性受威胁,生成额外的残渣。
游离酸度反映磷化液中游离H+的含量。
控制游离酸度的意义在于控制磷化液中磷酸二氢盐的离解度,把成膜离子浓度控制在一个必须的范围。
磷化液在使用过程中,游离酸度会有缓慢的升高,这时要用碱来中和调整,注意缓慢加入,充分搅拌,否则碱液局部过浓会产生不必要的残渣,出现越加碱,游离酸度越高的现象。
单看游离酸度和总酸度是没有实际意义的,必须一起考虑。
3、酸比————酸比即指总酸度与游离酸度的比值。
一般的说酸比都在5~30 的范围内。
酸比较小的配方,游离酸度高,成膜速度慢,磷化时间长,所需温度高。
酸比较大的配方,成膜速度快,磷化时间短,所需温度低。
因此必须控制好酸比。
4、温度————磷化处理温度与酸比一样,也是成膜的关键因素。
不同的配方都有不同的温度范围,实际上,他在控制着磷化液中的成膜离子的浓度。
温度高,磷酸二氢盐的离解度大,成膜离子浓度相应高些,因此可以利用此种关系在降低温度的同时提高酸比,同样可达到成膜,其关系如下:70℃60 ℃50 ℃40 ℃30 ℃20 ℃1/5 1/7 1/10 1/15 1/20 1/25生产单位确定了某一配方后,就应该严格控制好温度,温度过高要产生大量沉渣,磷化液失去原有平衡。
温度过低,成膜离子浓度总达不到浓度积,不能生成完整磷化膜。
温度过高,磷化液中可溶性磷酸盐的离解度加大,成膜离子浓度大幅度提高,产生不必要的沉渣,白白浪费了磷化液中的有效成分,原有的平衡被迫坏,形成一个新的温度下的平衡,如,低温磷化液在温度失控而升高时,H2PO4→H++PO43- 的离解反应向右进行,从而使磷酸根浓度升高,产生磷酸锌沉淀,使磷化液的酸比自动升高。
钢铁零件磷化缺陷原因分析及解决方案
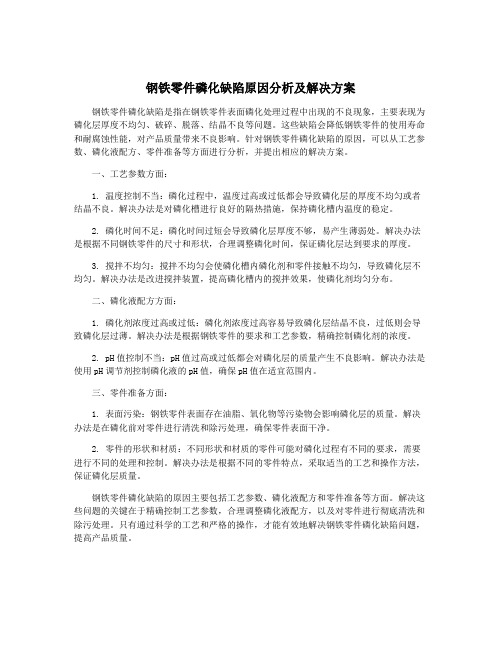
钢铁零件磷化缺陷原因分析及解决方案钢铁零件磷化缺陷是指在钢铁零件表面磷化处理过程中出现的不良现象,主要表现为磷化层厚度不均匀、破碎、脱落、结晶不良等问题。
这些缺陷会降低钢铁零件的使用寿命和耐腐蚀性能,对产品质量带来不良影响。
针对钢铁零件磷化缺陷的原因,可以从工艺参数、磷化液配方、零件准备等方面进行分析,并提出相应的解决方案。
一、工艺参数方面:1. 温度控制不当:磷化过程中,温度过高或过低都会导致磷化层的厚度不均匀或者结晶不良。
解决办法是对磷化槽进行良好的隔热措施,保持磷化槽内温度的稳定。
2. 磷化时间不足:磷化时间过短会导致磷化层厚度不够,易产生薄弱处。
解决办法是根据不同钢铁零件的尺寸和形状,合理调整磷化时间,保证磷化层达到要求的厚度。
3. 搅拌不均匀:搅拌不均匀会使磷化槽内磷化剂和零件接触不均匀,导致磷化层不均匀。
解决办法是改进搅拌装置,提高磷化槽内的搅拌效果,使磷化剂均匀分布。
二、磷化液配方方面:1. 磷化剂浓度过高或过低:磷化剂浓度过高容易导致磷化层结晶不良,过低则会导致磷化层过薄。
解决办法是根据钢铁零件的要求和工艺参数,精确控制磷化剂的浓度。
2. pH值控制不当:pH值过高或过低都会对磷化层的质量产生不良影响。
解决办法是使用pH调节剂控制磷化液的pH值,确保pH值在适宜范围内。
三、零件准备方面:1. 表面污染:钢铁零件表面存在油脂、氧化物等污染物会影响磷化层的质量。
解决办法是在磷化前对零件进行清洗和除污处理,确保零件表面干净。
2. 零件的形状和材质:不同形状和材质的零件可能对磷化过程有不同的要求,需要进行不同的处理和控制。
解决办法是根据不同的零件特点,采取适当的工艺和操作方法,保证磷化层质量。
钢铁零件磷化缺陷的原因主要包括工艺参数、磷化液配方和零件准备等方面。
解决这些问题的关键在于精确控制工艺参数,合理调整磷化液配方,以及对零件进行彻底清洗和除污处理。
只有通过科学的工艺和严格的操作,才能有效地解决钢铁零件磷化缺陷问题,提高产品质量。
常见的磷化质量问题及解决方法

(4)补加促进剂
11
涂膜起泡
涂装后,涂膜发生起泡现象
(1)磷化后水洗不充分;
(2)清洗水被污染;
(3)纯水的水质不好;
(4)吊架或传送带上滴落水;
(5)凹槽处残留有水
(1)检查喷嘴和水洗方法;
(2)增加供水量,控制清水的电导率在150μS/cm以下;
(3)控制纯水的电导率在5μS/cm以下;
(1)促进剂浓度过高;
(2)促进剂分布不匀;
(3)除油不彻底
(1)停止加促进剂;
(2)充分搅拌,使之均匀;
(3)补加脱脂剂
9
磷化槽液变黑
磷化槽液变黑变浑浊
(1)槽液温度低于规定温度;
(2)溶液中亚铁离子过量;
(3)总酸度过低
(1)停止磷化,升高槽液温度至沸点,保持1~2h,并用空气搅拌,直至恢复原色;
(4)加强脱脂或延长磷化时间;
(5)调整或更换磷化槽液
2
磷化膜过薄
磷化膜太薄、结晶过细或无明显结晶,抗蚀性能差
(1)总酸度过高;
(2)磷化时间不够;
(3)处理温度过低;
(4)促进剂浓度高;
(5)表调效果差或表调失效
(1)加水稀释磷化槽液;
(2)延长磷化时间;
(3)升高磷化槽液温度;
(4)停止添加促进剂;
(5)更换或添加表调剂
3
磷化膜结晶粗大
磷化膜结晶粗大、疏松、多孔、表面有水锈
(1)工件未清洗干净;
(2)亚铁离子含量偏低;
(3)游离酸度偏低;
(4)磷化温度低
(1)检查磷化前表面的预处理是否正确;
(2)提高亚铁离子的含量,如补加磷酸二氢铁;
(3)加入磷酸等,提高游离酸度;(4)提高槽液来自度4磷化膜挂灰
磷化常见问题汇总
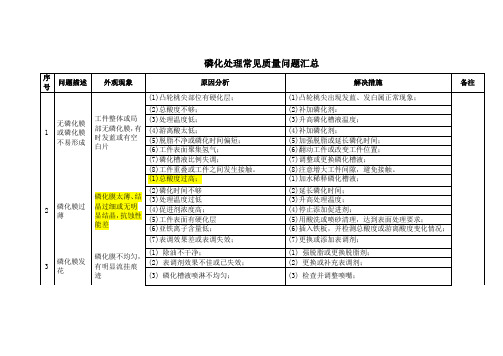
(8)逐一检查设备是否运行正常;
8
磷化膜发红
磷化膜红但不是锈
(1)铜离子渗入磷化液;
(1)注意不用铜挂具;用铁屑置换除支或用硫化处理,调整酸度;
(2)酸洗液中的铁渣附着;
(2)加强酸洗过程的质量控制;
9
膜呈彩虹花斑
用指甲划过无划痕,对光观察彩虹色
(1)促进剂浓度过高;
(6)工件表面产生过腐蚀现象;
(6)控制除锈时间或更换除锈剂;
5
磷化膜挂灰
磷化膜干燥后表面有白色粉末
(1)槽液含渣量过大;
(1)清除槽底残渣,并定期过滤;
(2)酸比太高;
(2)补加磷化剂;
(3)处理温度过高;
(3)降低磷化处理湿度;
(4)槽底沉渣浮起,黏附在工件上;
(4)静置磷化槽液,并翻槽;
(5)工件表面氧化物未除净;
(4)补加促进剂;
12
涂膜起泡
涂装后,涂膜发生起泡现象
(1)磷化后水洗不充分;
(1)检查喷嘴和水洗方法;
(2)清洗水被污染;
(2)增加供水量,控制清洗水的电导率<150μS/cm;
(3)纯水的水质不好;
(3)控制纯水的电导率<5μS/cm;
(4)吊架或传送带上滴落水;
(4)消除这类滴水。
(1)加水稀释磷化槽液;
(2)磷化时间不够
(2)延长磷化时间;
(3)处理温度过低
(3)升高处理温度;
(4)促进剂浓度高;
(4)停止添加促进剂;
(5)工件表面有硬化层
(5)用酸洗或喷砂清理,达到表面处理要求;
(6)亚铁离子含量低;
(6)插入铁板,并检测总酸度或游离酸度变化情况;
磷化处理工艺
磷化处理一、问题处理:铁件磷化后,表面发白,原因:磷化液中的沉渣,在铁件表面。
处理办法:磷化液中加入双氧水,沉淀,清除磷化液下边的沉渣。
加大在磷化后的水洗。
局部发黄,的原因是铁件表面开始反锈。
原因,1.工件的在做完磷化后,水洗不够彻底。
2.工件复杂,没有把水完全空出。
处理办法,1.加大水洗,2.用热水烫干,加大通风。
二、磷化工艺:磷化是常用的前处理技术,原理上应属于化学转化膜处理。
工程上应用主要是钢铁件表面磷化,但有色金属如铝、锌件也可应用磷化。
磷化原理:工件(钢铁或铝、锌件)浸入磷化液(某些酸式磷酸盐为主的溶液),在表面沉积形成不溶于水的结晶型磷酸盐转化膜的过程,称之为磷化。
把金属放入含有锰、铁、锌的磷酸盐溶液中进行化学处理,使金属表面生成一层难溶于水的磷酸盐保护膜的方法,叫做金属的磷酸盐处理。
磷化膜层为微孔结构,与基体结合牢固,具有良好的吸附性、润滑性、耐蚀性、不粘附熔融金属(Sn、Al、Zn)性及较高的电绝缘性等。
磷化分类:按处理温度分:高温型(75-100℃,能耗大,磷化物沉积多,形成的磷化膜厚度达10-30g/㎡)、中温型(50-75℃,处理时间5-15min,磷化膜厚度达1 -8g/㎡)、低温型(30-50℃)和常温型(10-30℃,节省能源,使用方便,除加氧化剂外还加促进剂,能耗小,但溶液配制较复杂,膜厚度达0.2-7g/㎡)。
按磷化液成分分:锌系磷化、锌钙系磷化、锌锰系磷化、铁系磷化、锰系磷化和复合磷化等。
按磷化处理方法分:化学磷化、电化学磷化。
按磷化膜质量分:重量级(膜重7.5g/㎡以上)、次重量级(膜重4.6-7.5g/㎡)、轻量级(膜重1.1-4.5g/㎡)和次轻量级(膜重0.2-1g/㎡)。
按施工方法分:浸渍磷化、喷淋磷化和刷涂磷化。
磷化作用及用途:涂装前磷化的作用:增强涂装膜层(如涂料涂层)与工件间结合力;提高涂装后工件表面涂层的耐蚀性;提高装饰性。
非涂装磷化的作用:提高工件的耐磨性,令工件在机加工过程中具有润滑性;经适当的后处理,可提高工件的耐磨性。
磷化处理影响因素及常见问题
磷化处理影响因素及常见问题磷化处理影响因素及常见问题一、磷化工艺参数的影响1、总酸度————总酸度过低、磷化必受影响,因为总酸度是反映磷化液浓度的一项指标。
控制总酸度的意义在于使磷化液中成膜离子浓度保持在必要的范围内。
2、游离酸度————游离酸度过高、过低均会产生不良影响。
过高不能成膜,易出现黄锈;过低磷化液的稳定性受威胁,生成额外的残渣。
游离酸度反映磷化液中游离H+的含量。
控制游离酸度的意义在于控制磷化液中磷酸二氢盐的离解度,把成膜离子浓度控制在一个必须的范围。
磷化液在使用过程中,游离酸度会有缓慢的升高,这时要用碱来中和调整,注意缓慢加入,充分搅拌,否则碱液局部过浓会产生不必要的残渣,出现越加碱,游离酸度越高的现象。
单看游离酸度和总酸度是没有实际意义的,必须一起考虑。
3、酸比————酸比即指总酸度与游离酸度的比值。
一般的说酸比都在5~30的范围内。
酸比较小的配方,游离酸度高,成膜速度慢,磷化时间长,所需温度高。
酸比较大的配方,成膜速度快,磷化时间短,所需温度低。
因此必须控制好酸比。
4、温度————磷化处理温度与酸比一样,也是成膜的关键因素。
不同的配方都有不同的温度范围,实际上,他在控制着磷化液中的成膜离子的浓度。
温度高,磷酸二氢盐的离解度大,成膜离子浓度相应高些,因此可以利用此种关系在降低温度的同时提高酸比,同样可达到成膜,其关系如下:70℃ 60℃ 50℃ 40℃ 30℃ 20℃1/5 1/7 1/10 1/15 1/20 1/25生产单位确定了某一配方后,就应该严格控制好温度,温度过高要产生大量沉渣,磷化液失去原有平衡。
温度过低,成膜离子浓度总达不到浓度积,不能生成完整磷化膜。
温度过高,磷化液中可溶性磷酸盐的离解度加大,成膜离子浓度大幅度提高,产生不必要的沉渣,白白浪费了磷化液中的有效成分,原有的平衡被迫坏,形成一个新的温度下的平衡,如,低温磷化液在温度失控而升高时,H2PO4→H++PO43- 的离解反应向右进行,从而使磷酸根浓度升高,产生磷酸锌沉淀,使磷化液的酸比自动升高。
磷化常见问题及解决方法
对策
磷化后不干净
:
烘干前水洗要充分
加入表调液时,未充分溶解,固体附在工件上
用温水充分溶解表调剂(固体),再加入水槽中
用后处理剂时,浓度过高
后处理剂不应超过规定值
涂装后出现异常现象与磷化膜出现的现象相吻合,则为磷化出现问题
按(5)处理
烘干时,工件中存水,未烘干
充分烘干
~
序号
质量外观
外观现象
产生原因
结疤:磷化膜形成不完全
|
原因
对策
除油未尽
表调液中混入过多杂质
磷化槽中沉渣多
游离酸点高
重新除油
/
重配表调液
倒槽排渣
用中和剂处理
磷化膜出现水锈斑
原因
对策
、
钢材经铬酸处理或附着难除尽的植物油
加强除油剂的除油能力
脱脂剂(碱性)温度低,碱性低,槽液表面浮油太多
浮油除去,升高温度
酸性除油剂除油未尽
补加药剂
点状红锈经磷化后变成白点或黄色水锈
1.促进剂浓度过高
2.游离酸度过高
3.工件磷化时间过长
4.中和过度形成结晶沉淀
1.让其自然降低
2.补加碱
3.:
4.缩短时间
5.补加磷酸
磷化膜的缺陷及解决方法:
磷化膜生锈,其中红锈产生于原料,黄锈产生于前处理 过程
现象
原因
对策
*
红锈
磷化后,磷化膜完整,但疏松。
局部泛黄,膜粗厚
原材料锈蚀过重,在工艺条件稳定的情况下,表调失去效果。
1.槽液含渣量过大
2.酸比太高
3处理温度过高
4.槽液沉渣浮起,黏附在工件上
5.工件表面氧化物未除净
磷化常见问答及解决方法
B、添加磷化液
C、倒槽或重配表调液
磷化后工件表面挂灰,磷化膜上覆盖一层白粉(粉末状)
原因
对策
酸比高
添加一定量磷化液
游离酸点高
按比例加入中和剂
促进剂浓度高或磷化液长时间不加促进剂,再突然大量加大;游离酸点高时加入促进剂。
应缓慢加入促进剂,多批次少量加入,出现问题后及时添加磷化液与中和剂。
10
磷化槽液变黑
磷化槽液变黑浑浊
1.槽液温度低于规定温度
2.溶液中亚铁离子过量
3.总酸度过低
1.停止磷化,升高槽液温度至沸点,保持1-2h,并用空气搅拌,直至灰色到原色
2.氧化剂,如高锰酸钾等
3.补充硝酸锌,提高总酸度
11
磷化膜发蓝
磷化膜部分表面产生紫兰色彩
1.表调剂的PH值不在工艺范围
2.表调与磷化间隔区的水务喷嘴堵塞
结疤:磷化膜形成不完全
原因
对策
除油未尽
表调液中混入过多杂质
磷化槽中沉渣多
游离酸点高
重新除油
重配表调液
倒槽排渣
用中和剂处理
磷化膜出现水锈斑
原因
对策
钢材经铬酸处理或附着难除尽的植物油
加强除油剂的除油能力
脱脂剂(碱性)温度低,碱性低,槽液表面浮油太多
浮油除去,升高温度
酸性除油剂除油未尽
补加药剂
点状红锈经磷化后变成白点或黄色水锈
磷化常见问题及解决方法
一、锌系磷化常见问题
序号
质量问题
外观现象
产生原因
解决方法
1
工件表面均匀泛黄,但均匀疏松的磷化膜
1、工件表面均匀泛黄,但均匀疏松的磷化膜
2、磷化成膜速度慢,但延长磷化时间仍可形成完整膜
- 1、下载文档前请自行甄别文档内容的完整性,平台不提供额外的编辑、内容补充、找答案等附加服务。
- 2、"仅部分预览"的文档,不可在线预览部分如存在完整性等问题,可反馈申请退款(可完整预览的文档不适用该条件!)。
- 3、如文档侵犯您的权益,请联系客服反馈,我们会尽快为您处理(人工客服工作时间:9:00-18:30)。
4.补充磷酸二氢盐
5.加强中和水洗
6.检查喷嘴并进行清理,检查磷化槽沉淀量
7.提高处理温度
8.逐一检查设备是否运行正常
8
磷化膜发红
磷化膜红但不是锈
1.铜离子渗入磷化液
2.酸洗液中的铁渣附着
1.注意不用铜挂具,用铁屑置换除去或用硫化处理,调整酸度
2.加强酸洗过程的质量控制
9
膜呈彩虹花斑
磷化膜干燥后表面有白色粉末
1.槽液含渣量过大
2.酸比太高
3.处理温度过高
4.槽液沉渣浮起,黏附在工件上
5.工件表面氧化物未除净
6.溶液氧化剂含量过高,总酸度过高
1.清除槽底残渣,并定期过滤
2.补加磷化剂
3.降低磷化处理温度
4.静置磷化槽液,并翻槽
5.加强酸洗并充分水洗
6.停加氧化剂,调整酸的比值
5
磷化膜发花
2.氧化剂,如高锰酸钾等
3.补充硝酸锌,提高总酸度
11
磷化膜发蓝
磷化膜部分表面产生紫蓝色彩
表调剂的PH值不在工艺范围
2.表调与磷化间隔区的水务喷嘴堵塞
3.磷化槽液的锌离子含量不足
4.磷化槽液的促进剂含量不够
1.补加表调剂或补加Na2CO3,以提高PH值
2.检查、清扫水务喷嘴
3.补加磷化液或硝酸锌
4.补加促进剂
7
磷化表面生锈
磷化后工件表面产生黄色锈斑或锈点
1.磷化膜晶粒过粗或过细,使耐蚀性降低
2.游离酸含量过高
3.工件表面过过腐蚀
4.溶液中磷酸盐含量不足
5.工件表面有残酸
6.磷化槽沉淀多,已堵塞喷嘴
7.处理温度低
8.设备原因,如喷淋的压力过大、喷嘴方向等
1.调整游离酸度与总酸度的比例
2.降低游离酸含量,可加氧化锌或氢氧化锌
12
涂膜气泡
涂装后,涂膜发生起泡现象
1.磷化后水洗不充分
2.清洗水被污染
3.纯水的水质不好
4.吊架或传送带上滴落水
1.检查喷嘴或水洗方法
2.增加供水量,控制清洗水的电导率在150μS/cm以下
3.控制纯水的电导率在5μS/cm以下
4.消除这类滴水
1.改进加工方法或用酸洗、喷砂去除硬化层,达到表面处理要求
2.补加磷化剂
3.升高磷化槽液温度。
4.补加磷化剂
5.加强脱脂或延长磷化时间
6.翻动工件或改变工件位置
7.调整或更换磷化槽液
8.注意增大工件间间隙,避免接触
2
磷化膜过薄
磷化膜太薄,结晶过细或无明显结晶,抗蚀性能差
1.总酸度过高
2.磷化时间不够
1.工件未清洗干净
2.工件在磷化前生锈
3.亚铁离子含量偏低
4.游离酸度偏低
5.磷化温度低
6.工件表面产生过腐蚀现象
1.强磷化前工件的表面预处理
2.除锈水洗后减少工件在空气中的暴露时间
3.提高亚铁离子的含量,如补充磷酸二氢铁
4.加入磷酸等,提高游离酸度
5.提高槽液温度
6.控制除锈时间或更换除锈剂
4
磷化膜挂灰
常见磷化质量问题及解决方法
序号
质量
外观
外观
现象
产生原因
解决方法
1
无磷化膜或磷化膜不易形成
工件整体或局部无磷化膜,有时发蓝或有空白片
1.工件表面有硬化层
2.总酸度不够
3.处理温度低
4.游离酸太低
5.脱脂不净或磷化时间偏短
6.工件表面聚齐氢气
7.磷化槽液比例失调,如P2O5含量过低
8.工件重叠或工件之间发生接触
磷化膜不均匀,有明显流挂痕迹
1.除油不干净
2.表调剂效果不佳或已失效
3.磷化槽液喷淋不均匀
4.工件表面钝化
5.磷化温度低
1.强脱脂或更换脱脂剂
2.更换或补充表调剂
3.检查并调整喷嘴
4.加强酸洗或喷砂
5.提高磷化温度
6
磷化膜发黑
局部呈黑条状,膜黑且粗糙
1.促进剂浓度太低
2.酸洗过度
1.加促进剂
2.控制酸洗时间
3.处理温度过低
4.促进剂浓度高
5.工件表面有硬化层
6.亚铁离子含量低
7.表调效果差或表调失效
1.加水稀释磷化槽液
2.延长磷化时间
3.升高处理温度
4.停止添加促进剂
5.用酸洗或喷砂清理,达到表面处理要求
6.插入铁板,并检测总酸度或游离酸度变化情况
7.更换或添加表调剂
3
磷化ห้องสมุดไป่ตู้结晶粗大
磷化膜结晶粗大、疏松、多孔、表面有水锈
用指甲划过无划痕,对光观察呈彩虹色
1.促进剂浓度过高
2.促进剂分布不均匀
3.除油不彻底
1.停加促进剂
2.充分搅拌,使之均匀
3.补加脱脂剂
10
磷化槽液变黑
磷化槽液变黑浑浊
1.槽液温度低于规定温度
2.溶液中亚铁离子过量
3.总酸度过低
1.停止磷化,升高槽液温度至沸点,保持1-2h,并用空气搅拌,直至灰色原色