§9[1].数控机床加工工艺实例分析
数控车床零件的工艺分析及编程典型实例

数控车床零件的工艺分析及编程典型实例更新日期:来源:数控工作室根据下图所示的待车削零件,材料为45号钢,其中Ф85圆柱面不加工。
在数控车床上需要进行的工序为:切削Ф80mm 和Ф62mm 外圆;R70mm 弧面、锥面、退刀槽、螺纹及倒角。
要求分析工艺过程与工艺路线,编写加工程序。
图1 车削零件图1.零件加工工艺分析(1)设定工件坐标系按基准重合原则,将工件坐标系的原点设定在零件右端面与回转轴线的交点上,如图中Op点,并通过G50指令设定换刀点相对工件坐标系原点Op的坐标位置(200,100)(2)选择刀具根据零件图的加工要求,需要加工零件的端面、圆柱面、圆锥面、圆弧面、倒角以及切割螺纹退刀槽和螺纹,共需用三把刀具。
1号刀,外圆左偏刀,刀具型号为:CL-MTGNR-2020/R/1608 ISO30。
安装在1号刀位上。
3号刀,螺纹车刀,刀具型号为:TL-LHTR-2020/R/60/1.5 ISO30。
安装在3号刀位上。
5号刀,割槽刀,刀具型号为:ER-SGTFR-2012/R/3.0-0 IS030。
安装在5号刀位上。
(3)加工方案使用1号外圆左偏刀,先粗加工后精加工零件的端面和零件各段的外表面,粗加工时留0.5mm的精车余量;使用5号割槽刀切割螺纹退刀槽;然后使用3号螺纹车刀加工螺纹。
(4)确定切削用量切削深度:粗加工设定切削深度为3mm,精加工为0.5mm。
主轴转速:根据45号钢的切削性能,加工端面和各段外表面时设定切削速度为90m/min;车螺纹时设定主轴转速为250r/min。
进给速度:粗加工时设定进给速度为200mm/min,精加工时设定进给速度为50mm/min。
车削螺纹时设定进给速度为1.5mm/r。
2.编程与操作(1)编制程序(2)程序输入数控系统将程序在数控车床MDI方式下直接输入数控系统,或通过计算机通信接口将程序输入数控机床的数控系统。
然后在CRT 屏幕上模拟切削加工,检验程序的正确性。
数控编程加工工艺实例分析

数控编程加工工艺实例分析文/罗谷清数控机床是一种技术密集度及自动化程度很高的机电一体化加工设备,是综合应用计算机、自动控制、自动检测及精密机械等高新技术的产物,它严格按照加工程序,自动地对被加工工件进行加工。
随着数控机床的发展与普及,现代化企业对于懂得数控加工技术、能进行数控加工编程的技术人才的需求量必将不断增加。
数控车床是目前使用最广泛的数控机床之一。
数控编程是指从零件图样到获得数控加工程序的全部工作过程。
编制数控加工程序是使用数控机床的一项重要技术工作,理想的数控程序不仅应该保证加工出符合零件图样要求的合格零件,还应该使数控机床的功能得到合理的应用与充分的发挥,使数控机床能安全、可靠、高效地工作。
一、数控程序编制的内容及步骤数控编程是指从零件图样到获得数控加工程序的全部工作过程,如图1所示。
二、编程方法数控加工程序的编制方法主要有两种:手工编制程序和自动编制程序。
1.手工编程手工编程指主要由人工来完成数控编程中各个阶段的工作,如图2所示。
一般对几何形状不太复杂的零件,所需的加工程序不长,计算比较简单,用手工编程比较合适。
手工编程的特点:耗费时间较长,容易出现错误,无法胜任复杂形状零件的编程。
据国外资料统计,当采用手工编程时,一段程序的编写时间与其在机床上运行加工的实际时间之比,平均约为30:1,而数控机床不能开动的原因中有20%~30%是由于加工程序编制困难,编程时间较长。
2.计算机自动编程自动编程是指在编程过程中,除了分析零件图样和制定工艺方案由人工进行外,其余工作均由计算机辅助完成。
采用计算机自动编程时,数学处理、编写程序、检验程序等工作是由计算机自动完成的,由于计算机可自动绘制出刀具中心运动轨迹,使编程人员可及时检查程序是否正确,需要时可及时修改,以获得正确的程序。
又由于计算机自动编程代替程序编制人员完成了繁琐的数值计算,可提高编程效率几十倍乃至上百倍,因此解决了手工编程无法解决的许多复杂零件的编程难题。
数控机床加工工艺实例分析

刀具 专用车刀T01 内螺纹车刀T02
车刀T03
审定
文件编号
第页
工序名称 精车大端 面各部
设备型号 CNC6132
走刀次数
7 1 批准
材料
HPb59-1
夹具
专用夹 具
量具及 检具 游标卡
尺 螺纹塞
规 塞规
3.数控加工走刀路线图
表9—9 数控加工走刀路线图
数控加 工走刀 路线图
零件图 号
CFAD316Z0
图9—7 盖板钻孔走刀路线
9.2.3 加工工序卡片和刀具使用卡片
盖板零件数控铣加工工序卡片和刀具使用卡片见表9—10和表6—11。
表9—10 盖板零件数控铣加工工序卡片
(单位名称)
0 工艺序号 2
数控加工工序卡 02
夹具名称
工 步 号
加工内 容
粗 铣
1
平 面
精
铣粗
2
外 轮精
廓
3
挖槽
程序号
刀具名称
刀具规 格 /mm
2.选择装夹和定位
该零件在生产时,可采用“一面、两销”的定位方式,以工件底面为第 一定位基准,定位元件采用支撑面,限制工件在X、y方向的旋转运动和Z 方向的直线运动,两个φ22mm的孔作为第二定位基准,定位元件采用带螺 纹的两个圆柱定位销,进行定位和压紧。限制工件在X、y方向的直线运动 和Z方向的旋转运动。挖φ2.5mm深的中心槽时,先用压板压紧工件,再松 开定位销螺母。在批量生产加工过程中,应保证定位销与工作台相对位置 的稳定。
此外,零件上不得有毛刺伤痕及油污,未注公差±0.1。φ6.8孔P处 不得有毛刺,但倒角不得大于0.3。零件上φ11外圆、φG1/2螺纹、Rc1/2 内螺纹6.8孔与G1/2螺纹、Rc1/2内螺纹有同轴度要求,φ6.8与G1/2一次 装夹加工,以保证同心。
数控车床加工工艺分析与程序设计

数控车床加工工艺分析与程序设计摘要:数控技术及数控机床在当今机械制造业中起着重要地位。
而现代数控机床是综合应用了计算机、自动控制、自动检测以及精密机械等高新技术的产物,集成了数控仿真,可以检查出代码的正确性,从而可以提高编程质量,减少出错率,加快编程速度,是典型的机电一体化产品,是完全新型的自动化机床;这显示了其在国家基础工业现代化中的战略性作用,并已成为传统机械制造工业提升改造和实现自动化、柔性化、集成化生产的重要手段和标志。
关键词:数控技术、数控仿真、机电一体化、自动化机床Abstract:Numerical control technology and CNC manufacturing industry in today is the importer position in the country. And the moder numerical control machine tool is the synthesis has applied the computer, the automatic nontrol antomatic detetion as well as the precision machinery and soon the high-tech product, integrated the numerical control simulation module,is allowed to inspect the code the accuracy, thus was allowed to improve the programming quality, reduced the error ratio, sped up the programming speed, was the tyoical integration of machinery product, was the completely new automated engine bed: and has become a traditional mechanical manufacturing industry upgrading transformation and automation, flexibility and integrated production of important means and logo.Key words:Numerical control、Numerical control simulation、Integration of machinery、Automatic machine tool.引言随着科学技术的发展,机电产品日益精密复杂。
数控编程加工工艺实例分析
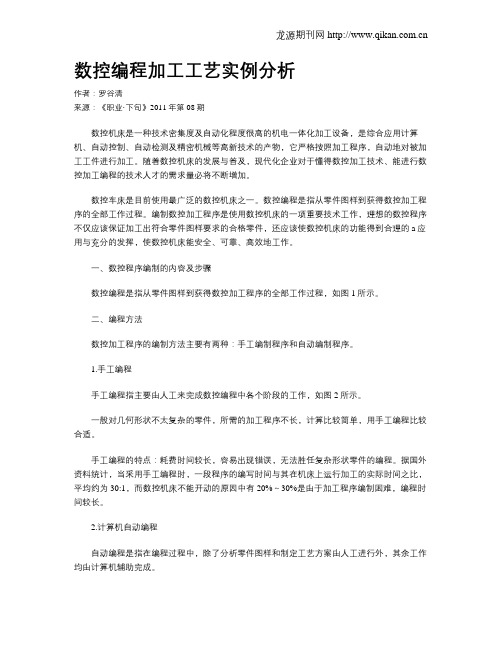
数控编程加工工艺实例分析作者:罗谷清来源:《职业·下旬》2011年第08期数控机床是一种技术密集度及自动化程度很高的机电一体化加工设备,是综合应用计算机、自动控制、自动检测及精密机械等高新技术的产物,它严格按照加工程序,自动地对被加工工件进行加工。
随着数控机床的发展与普及,现代化企业对于懂得数控加工技术、能进行数控加工编程的技术人才的需求量必将不断增加。
数控车床是目前使用最广泛的数控机床之一。
数控编程是指从零件图样到获得数控加工程序的全部工作过程。
编制数控加工程序是使用数控机床的一项重要技术工作,理想的数控程序不仅应该保证加工出符合零件图样要求的合格零件,还应该使数控机床的功能得到合理的a应用与充分的发挥,使数控机床能安全、可靠、高效地工作。
一、数控程序编制的内容及步骤数控编程是指从零件图样到获得数控加工程序的全部工作过程,如图1所示。
二、编程方法数控加工程序的编制方法主要有两种:手工编制程序和自动编制程序。
1.手工编程手工编程指主要由人工来完成数控编程中各个阶段的工作,如图2所示。
一般对几何形状不太复杂的零件,所需的加工程序不长,计算比较简单,用手工编程比较合适。
手工编程的特点:耗费时间较长,容易出现错误,无法胜任复杂形状零件的编程。
据国外资料统计,当采用手工编程时,一段程序的编写时间与其在机床上运行加工的实际时间之比,平均约为30:1,而数控机床不能开动的原因中有20%~30%是由于加工程序编制困难,编程时间较长。
2.计算机自动编程自动编程是指在编程过程中,除了分析零件图样和制定工艺方案由人工进行外,其余工作均由计算机辅助完成。
采用计算机自动编程时,数学处理、编写程序、检验程序等工作是由计算机自动完成的,由于计算机可自动绘制出刀具中心运动轨迹,使编程人员可及时检查程序是否正确,需要时可及时修改,以获得正确的程序。
又由于计算机自动编程代替程序编制人员完成了繁琐的数值计算,可提高编程效率几十倍乃至上百倍,因此解决了手工编程无法解决的许多复杂零件的编程难题。
数控机床技术的喷嘴加工实例解析
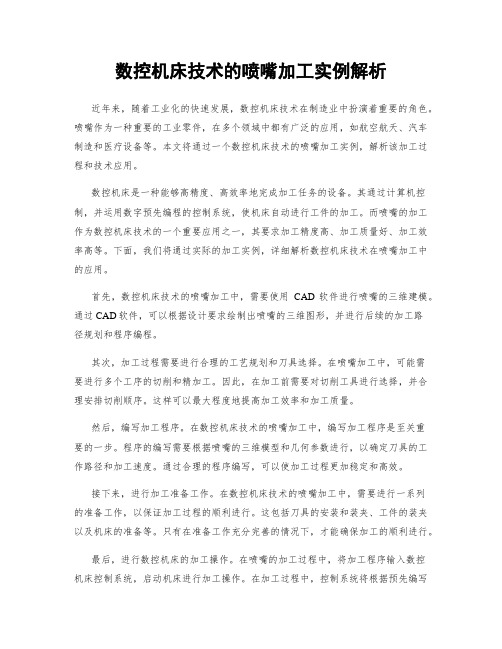
数控机床技术的喷嘴加工实例解析近年来,随着工业化的快速发展,数控机床技术在制造业中扮演着重要的角色。
喷嘴作为一种重要的工业零件,在多个领域中都有广泛的应用,如航空航天、汽车制造和医疗设备等。
本文将通过一个数控机床技术的喷嘴加工实例,解析该加工过程和技术应用。
数控机床是一种能够高精度、高效率地完成加工任务的设备。
其通过计算机控制,并运用数字预先编程的控制系统,使机床自动进行工件的加工。
而喷嘴的加工作为数控机床技术的一个重要应用之一,其要求加工精度高、加工质量好、加工效率高等。
下面,我们将通过实际的加工实例,详细解析数控机床技术在喷嘴加工中的应用。
首先,数控机床技术的喷嘴加工中,需要使用CAD软件进行喷嘴的三维建模。
通过CAD软件,可以根据设计要求绘制出喷嘴的三维图形,并进行后续的加工路径规划和程序编程。
其次,加工过程需要进行合理的工艺规划和刀具选择。
在喷嘴加工中,可能需要进行多个工序的切削和精加工。
因此,在加工前需要对切削工具进行选择,并合理安排切削顺序。
这样可以最大程度地提高加工效率和加工质量。
然后,编写加工程序。
在数控机床技术的喷嘴加工中,编写加工程序是至关重要的一步。
程序的编写需要根据喷嘴的三维模型和几何参数进行,以确定刀具的工作路径和加工速度。
通过合理的程序编写,可以使加工过程更加稳定和高效。
接下来,进行加工准备工作。
在数控机床技术的喷嘴加工中,需要进行一系列的准备工作,以保证加工过程的顺利进行。
这包括刀具的安装和装夹、工件的装夹以及机床的准备等。
只有在准备工作充分完善的情况下,才能确保加工的顺利进行。
最后,进行数控机床的加工操作。
在喷嘴的加工过程中,将加工程序输入数控机床控制系统,启动机床进行加工操作。
在加工过程中,控制系统将根据预先编写的程序,自动控制切削工具的运动和加工过程参数,以实现喷嘴的加工。
加工完成后,工件将获得高精度和高质量的表面。
总结起来,数控机床技术的喷嘴加工实例中,CAD软件的应用、合理的工艺规划和刀具选择、加工程序的编写、加工准备工作以及加工操作都是至关重要的环节。
典型零件数控加工工艺分析实例

说明:表格中刀尖半径和备注栏可以不要;25×25 指车刀刀柄的截面尺寸。
(5)切削用量选择
一般情况下,粗车:恒转速 n=800r/min 恒线速 v=100m/min
进给量 f=0.2mm/r 以下
vf=120m/min
背吃刀量 ap=2mm 以下
精车:恒转速 n=1100r/min 恒线速 v=150m/min
以零件右端面和中心轴作为 坐标原点建立工件坐标系。
根据零件尺寸精度及技术要 求,零件从右向左加工,将粗、 精加工分开来考虑。
加工工艺顺序为:车削右端面→复合型车削固定循环粗、精加工右端需要加工的所有轮 廓(粗车Φ44、Φ40.5、Φ34.5、Φ28.5、Φ22.5、Φ16.5 外圆柱面→粗车圆弧面 R14.25→ 精车外圆柱面Φ40.5→粗车外圆锥面→粗车外圆弧面 R4.75→精车圆弧面 R14→精车外圆锥 面→精车外圆柱面Φ40→精车外圆弧面 R5)。 (4)选择刀具
所选定刀具参数如表 1-2 所示。 说明:铣削内、外轮廓时,铣刀直径受槽宽限制,可选择φ6 的立铣刀;精铰的量通常 小于 0.2mm;刀刃和长度通常要比切削的深度大。 5.切削用量选择 一般情况下,粗铣:恒转速 n=600r/min
进给量 f=180mm/min 以下 背吃刀量 ap=5mm 以下 精车:恒转速 n=800r/min 进给量 f=120mm/min 以下
零件的底面和外部轮廓已经加工,本工序是在铣床上加工槽与孔。 1.零件图分析
凸轮内外轮廓由直线和圆弧组成。凸轮槽侧面和
20
0.021 0
、
12
0.018 0
两个内孔尺寸精
度要求较高,表面粗糙度要求也较高,Ra1.6;内孔
20
车床加工工艺案例

车床加工工艺案例一、零件分析本次车床加工的零件为轴类零件,主要结构包括圆柱面、圆锥面、螺纹等。
零件的尺寸精度和表面质量要求较高,需要进行精细加工。
二、材料选择根据零件的加工要求和性能要求,选择合适的材料是关键。
本次加工选用45号钢作为原材料,该材料具有较好的切削性能和机械性能,适合用于轴类零件的加工。
三、刀具准备在车床加工中,刀具的选择和使用对加工质量和效率具有重要影响。
根据零件的结构和材料特性,准备以下刀具:外圆车刀:用于加工圆柱面和端面;圆锥车刀:用于加工圆锥面;螺纹车刀:用于加工螺纹;切槽刀:用于加工槽。
四、切削参数设定切削参数的合理设定对加工质量和效率具有重要影响。
根据零件的材料特性和刀具特性,设定以下切削参数:主轴转速:根据所使用的刀具和材料确定合理的转速;进给速度:根据加工表面的粗糙度和刀具寿命确定合理的进给速度;切削深度:根据加工余量和刀具刚度确定合理的切削深度。
五、加工流程设计加工流程的合理设计能够提高加工效率和质量。
本次加工流程如下:将原材料固定在车床工作台上;使用外圆车刀加工圆柱面和端面;使用圆锥车刀加工圆锥面;使用螺纹车刀加工螺纹;使用切槽刀加工槽;对加工完成的零件进行质量检测和成品检验。
六、冷却液使用在车床加工过程中,冷却液的使用能够有效降低切削温度,减少刀具磨损和热变形,提高加工质量和效率。
根据使用的刀具和切削参数,选择合适的冷却液并控制使用量。
七、质量检测在每道工序完成后,应对零件进行质量检测。
检测内容包括:尺寸精度、表面粗糙度、形状精度等。
检测方法可采用千分尺、表面粗糙度仪等测量工具进行测量和评估。
如发现不合格品,应及时进行调整和返工。
八、成品检验成品检验是确保最终产品质量的重要环节。
检验内容应包括:尺寸精度、表面质量、形状精度等。
检验方法与质量检测相同,可使用相同的测量工具进行测量和评估。
如发现不合格品,应进行追溯和整改。
九、优化与改进在实际生产过程中,应根据实际情况对加工工艺进行优化和改进。
- 1、下载文档前请自行甄别文档内容的完整性,平台不提供额外的编辑、内容补充、找答案等附加服务。
- 2、"仅部分预览"的文档,不可在线预览部分如存在完整性等问题,可反馈申请退款(可完整预览的文档不适用该条件!)。
- 3、如文档侵犯您的权益,请联系客服反馈,我们会尽快为您处理(人工客服工作时间:9:00-18:30)。
1
下料
卧 式 车床 卧 式 车床 卧 式 车床 卧 式 车床 卧 式 车床 数 控 机床 数 控 机床 审核
三爪平卡 盘 三爪平卡 盘 三爪平卡 盘 三爪平卡 盘 三爪平卡 盘 三爪平卡 盘 专用夹具
2
粗车小端外圆
3
粗车小端面及钻孔
4
粗车大端面及钻孔
5
钻锥孔
6
精车小端面各部
7
精车大端面各部
编制
批准
共1页
1.铜接头综合工艺过程卡
表9—1 铜接头综合工艺过程卡 1
零件名称 零 件 材料 HPb59 —1 毛坯种类 毛坯 硬度 毛 重 /kg 净 重 /kg 车型 每车件 数
铜接头
冷拔型材
工序号 工序名称 设备 名称 夹具
进给 量 /mm/ r
主轴 转速 /r/mi n
切削速 度 /m/min
冷却 液
负荷 /%
表9—3 铜接头工序卡 3
零件图号 机械加工工序卡 CF-AD316Z0
零件名称
文件编号
第 页
铜接头
工序号
工序名称
材料
2
车小端外圆
HPb59-1
加工车间
设备型号
夹具
C6140A1 三爪平卡 盘
工步号 粗车φ11外圆至φ12.6 1
工步内容
刀具
量具及检具
外圆车刀1 粗车φ20.8外圆至φ22.6
游标卡尺 游标卡尺
1
编制
校对
审定
批准
3.数控加工走刀路线图 3.数控加工走刀路线图
表9—9 数控加工走刀路线图 9
数控加 工走刀 路线图 机床型 号
零件图 号
CFAD316Z0
工 序 号
6
工步号
1
程序号
O0 09 9 第 页
CNC613 2
程序段号
加工 内容
精车小端外圆柱面、端面、 倒角及退刀槽
共1页
符号
含义
抬 刀
HT 32-52 使用设备 XK5025
工 步 号
加工内 容
程序号
刀具名称
刀具规 格 /mm
补 偿 号
补偿值
进给速度 /mm·min-1
进给倍 率 /%
切削深 度 /mm
加工余量 /mm
粗 1 铣 平 面 铣 外 轮 廓 挖槽 点窝 钻孔 钻孔 立铣刀 精 φ25
202 402 粗 φ25 立铣刀 精 φ25 H1 402 H1 202
3.选择铣刀和切削用量
铣削上表面选取φ25mm立铣刀(由于采用两个中心孔定位,不能使用端 面铣刀),先进行粗铣,留0.2~0.5mm余量,再进行精铣;最大外形轮廓 铣削可选用直径较大的刀,根据余量决定铣削次数,最后余量加工应 ≤φ0.5mm;挖深度为2.5mm,选用直径≤φ8 mm的立铣刀;钻φ5.5和 φ6.5的孔,先用φ3的中心钻点窝,再分别用φ5.5mm和φ6.5mm的麻花钻 钻削。
表9—6 铜接头工序卡 6 零件图号 机械加工工序卡 CF-AD316Z0 铜接头 零件名称 文件编号 第 页
工序号
工序名称
材料 HPb5 9-1
5
钻锥孔
加工车间
设备型号
夹具 三爪 平卡 盘
CM6125
工步号 1 编制
工步内容 成形钻头钻锥形孔
刀具 锥形钻头
量具及检具
校对
审定
批准
表9—7 铜接头工序卡 7
3.工艺方案拟定
(1)下料 车端面、切断 (2)外表面各部分 粗车——精车 (3)钻孔 小端钻盲孔φ5.5;大端钻孔φ15 (4)钻锥孔 锥形钻头钻锥孔 (5)切退刀槽、外螺纹 切槽2.5×φ18,精车螺纹G1/2 (6)切内槽、内螺纹 切内槽2.5×φ22、精车内螺纹Rc1/2。
9.1.3 铜接头综合工艺过程卡和工序卡
2
外圆车刀2
编制
校对
审定
批准
表9—4 铜接头工序卡 4
第 页
零件图号 机械加工工序卡 CF-AD316Z0
零件名称 铜接头
文件编号
工序号
工序名称
材料
3
粗车小端 面及钻孔
HPb59 -1
加工车间
设备型号
夹具 三爪 平卡 盘
CM6125
工步号 车小端面 1
工步内容
刀具 车刀
量具及检具 游标卡尺
钻φ6孔至φ5.5,孔深18 2 编制 校对 φ5.5钻头 审定 批准
第9章 数控机床加工工艺实例分析 •9.1 大批量生产零件数控车削加工工艺 9 •9.2 数控铣削加工工艺实例分析 9 •9.3 9 •9.4 9 析 加工中心加工工艺实例分析 数控线切割机床加工工艺实例分
9.1 大批量生产零件数控车削加工工艺
9.1.1. 9.1.1.零件介绍
图9—1所示为铜接头零件简图。该零件材料为HPb59—1,毛坯为30铜六方冷拔型 材,是国内某精密仪器厂接洽日本的定单零件,为大批量生产类型产品。该零件 为外圆柱面、内外螺纹、内圆柱孔、内圆锥孔、内外环槽等表面组成的零件,加 工表面较多,适合在数控车床上加工。
零件图号 数控加工工序卡 CF-AD316Z0 铜接头 零件名称 文件编号 第 页
工序号
工序名称
材料
6
精车小端 面各部
HPb59-1
加工车间
设备型号
夹具
CNC6132
三爪平 卡盘
工步号
工步内容 精车小端面、φ11外圆、φ20.8端面、G1/2螺纹 底径至φ20.9和车大端左端面倒角及退刀槽 精车φ6.8到尺寸
2.确定装夹方案
该零件形状比较规则、简单,加工面与不加工面的位置精度要求不高, 可采用平口虎钳夹紧。但应先加工A面,然后以A面(主要定位基面)和两 个侧面定位,用虎钳从侧面夹紧。
3.确定加工顺序及走刀路线
按照先面后孔、先粗后精的原则确定加工顺序。总体顺序为粗、精铣A、B面粗镗、半精镗、精镗φ60H7孔-钻各中心孔-钻、锪、铰4-φ12H8和4-φ16孔-钻 4-M16螺纹底孔-攻螺纹。 由零件图可知,孔的位置精度要求不高,因此所有孔加工的进给路线按最短 路线确定。 图9—9 、图9—10、图9—11、图9—12、图9—13为孔加工各工步的进给路 线。
4.确定走刀路线
盖板挖槽走刀线路如图9—6所示,采用由内向外“平行环切并清角”或采用由 外向内“平行环切并清角”的切削方式。盖板钻孔走刀线路如图9—7所示。编程 与工件坐标系大端φ22mm孔的中心点为坐标系原点,对刀点根据实际情况而定, 定位销与工作台固定以后,可以套装一标准块,然后再进行定位。
图9—6 盖板挖槽走刀路线 6
刀具
走刀次数
量具及 检具 游标卡 尺
1
车刀T01
2 精车G1/2螺纹到尺寸 3
车刀T02
1
塞规 螺纹环 规
外螺纹车刀T03
6
编制
校对
审定
批准
表9—8 铜接头工序卡 8
零件图号 数控加工工序卡 CF-AD316Z0 铜接头 零件名称 文件编号 第 页
工序号
工序名称
材料
7
精车大端 面各部
HPb59-1
表9—5 铜接头工序卡 5 零件图号 机械加工工序卡 CF-AD316Z0 铜接头 零件名称 文件编号 第 页
工序号
工序名称 粗车大端 面及钻孔
材料 HPb59 -1
4
加工车间
设备型号
夹具 三爪 平卡 盘
CM6125
工步号 车大端面 1
工步内容
刀具 车刀
量具及检具 游标卡尺
钻Rc1/2螺纹底孔,孔深17 2 编制 校对 φ15钻头 审定 批准
下 刀
编程 原点
起刀点
走刀 方向
走刀 线相 切
爬斜坡
铰 孔
行 切
4.刀具调整图
图9—2 2
工序6 小端外轮廓精加工) 工序6(小端外轮廓精加工)刀具调整图
图9—3 3
工序7 大端外轮廓精加工) 工序7(大端外轮廓精加工)刀具调整图
5.专用夹具
图9—4 4
工序7 工序7专用夹具零件图
9.2 数控铣削加工工艺实例分析
第1页
2.工序卡
表9—2 铜接头工序卡 2
零件图号 机械加工工序卡 CF-AD316Z0 铜接头 零件名称 文件编号 第 页
工序号
工序名称
材料
1
下料
HPb59 -1
加工车间
设备型号 CW6140A
夹具 三爪 平卡 盘
工步号 车端面 1 切断 2 编制
工步内容
刀具 切断刀1
量具及检具
游标卡尺 切断刀1 校对 审定 批准
闭尺寸及其他标注错误;尺寸精度要求不高。 (2)加工工艺 该零件为铸造件(灰口铸铁),其结构并不复杂,但对要求加
工部分需要一次定位二次装夹。根据数控铣床工序划分原则,先安排平面铣削, 后安排孔和槽的加工。对于该工件加工顺序为:先铣削上平面;铣削轮廓;用中 心钻点窝;钻φ5.5mm的孔;钻φ6.5mm的孔;然后,先用压板压紧工件,再松开 定位销螺母,进行挖φ2.5mm深的中心槽。
200 200 200
30 20 30 0.5
2
200
10
0.5
3 4 5 6 注 意 事 项
键槽铣刀 中心钻 麻花钻 麻花钻
φ8 φ3 φ5.5 φ6.
402 800 602 602
200 100 200 50
10 20 20 10
①启动机床回零后,检查机床零点。
②换刀后,应松开主轴锁定,并对Z轴进行对刀。
图9—1 铜接头零图 1
9.1.2 工艺分析
1.加工技术要求分析
该 零 件 有 众 多 的 精 度 要 求 : 大 端 内 螺 纹 RC1/2 , 大 端 内 螺 纹 倒 角 1×45°,小端内孔直径φ,连接小端内孔与大端内螺纹的内锥孔长16.5 、大径φ10.7,小端外径φ11,外螺纹G1/2,大端端面2—φ29,大端外 表面刻字6.8。以及其它各轴向尺寸、粗糙度要求等。 此外,零件上不得有毛刺伤痕及油污,未注公差±0.1。φ6.8孔P处 不得有毛刺,但倒角不得大于0.3。零件上φ11外圆、φG1/2螺纹、Rc1/2 内螺纹6.8孔与G1/2螺纹、Rc1/2内螺纹有同轴度要求,φ6.8与G1/2一次 装夹加工,以保证同心。 上述技术要求决定了需加工的表面及相应加工方案(见表9—1)。