数控机床加工工艺
数控的加工工艺
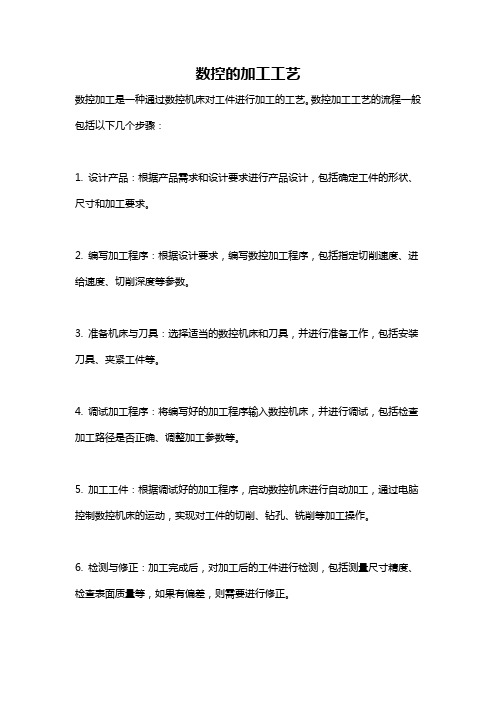
数控的加工工艺
数控加工是一种通过数控机床对工件进行加工的工艺。
数控加工工艺的流程一般包括以下几个步骤:
1. 设计产品:根据产品需求和设计要求进行产品设计,包括确定工件的形状、尺寸和加工要求。
2. 编写加工程序:根据设计要求,编写数控加工程序,包括指定切削速度、进给速度、切削深度等参数。
3. 准备机床与刀具:选择适当的数控机床和刀具,并进行准备工作,包括安装刀具、夹紧工件等。
4. 调试加工程序:将编写好的加工程序输入数控机床,并进行调试,包括检查加工路径是否正确、调整加工参数等。
5. 加工工件:根据调试好的加工程序,启动数控机床进行自动加工,通过电脑控制数控机床的运动,实现对工件的切削、钻孔、铣削等加工操作。
6. 检测与修正:加工完成后,对加工后的工件进行检测,包括测量尺寸精度、检查表面质量等,如果有偏差,则需要进行修正。
7. 收尾工作:清洁加工区域,处理加工废料,整理机床和刀具,保养机床设备等。
数控加工工艺具有高精度、高效率、高自动化程度等优点,可以满足复杂形状和高要求的工件加工需求。
它广泛应用于航空航天、汽车、机械制造等领域。
数控机床的加工工艺及编程步骤

外圆车刀 螺纹车刀
内孔车刀Βιβλιοθήκη 2.2.5 切削用量及刀具的选择
铣削刀具:
方肩 铣刀
整体硬质 合金铣刀
仿形 铣刀
三面刃和 螺纹铣刀
2.2.6 数值计算
1.基点、节点的含义 编程时的数值计算主要是计算零件加工轨迹的尺寸,即计算零件轮廓 基点和节点的坐标,或刀具中心轨迹基点和节点的坐标。 l 数控机床一般只有直线和圆弧插补功能,因此,对于由直线和圆弧组 成的平面轮廓,编程时主要是求各基点的坐标。 基点:就是构成零件轮廓不同几何素线元素的交点或切点。如直 线与直线的交点,直线段和圆弧段的交点、切点及圆弧与圆弧的 交点、切点等。根据基点坐标就可以编写出直线和圆弧的加工程 序。基点的计算比较简单,选定坐标原点以后,应用三角、几何 关系就可以算出各基点的坐标,因此采用手工编程即可。
2.2.5 切削用量及刀具的选择
切削用量包括主轴转速、进给速度和切削深度等。各种机床切削用量的 选择根据数控机床使用说明书、手册,并结合实践经验加以确定。 2.进给速度 进给速度根据零件的加工精度、表面粗糙度和刀具、工件的材 料选择,最大进给速度受机床刚度和进给系统的性能限制,并与脉冲 当量有关。在精度要求较高时,进给量应选小一些,一般在 20mm/min一50mm/min范围内选取。 3.切削深度 主要根据机床、刀具、夹具和工件的刚性确定。在机床刚度允许 的情况下,尽量选择较大的切削深度,以提高加工效率。有时为了改 善表面粗糙度和加工精度,要留一点余量,以便最后精加工一次。
在数控加工中,加工路线除了要保 证工件的加工精度、表面粗糙度外, 还要尽量缩短空行程时间,并能简 化程序。
例如在铣削外轮廓时,为防止刀具 在切入,切出时产生刀痕,一般采 用切线切入、切出方式以保证工件 轮廓的光滑过渡,如图2.2.2所示。
数控机床生产工艺流程
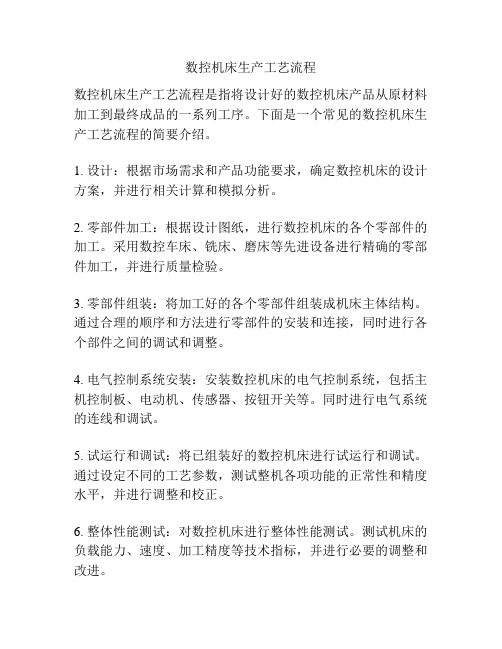
数控机床生产工艺流程数控机床生产工艺流程是指将设计好的数控机床产品从原材料加工到最终成品的一系列工序。
下面是一个常见的数控机床生产工艺流程的简要介绍。
1. 设计:根据市场需求和产品功能要求,确定数控机床的设计方案,并进行相关计算和模拟分析。
2. 零部件加工:根据设计图纸,进行数控机床的各个零部件的加工。
采用数控车床、铣床、磨床等先进设备进行精确的零部件加工,并进行质量检验。
3. 零部件组装:将加工好的各个零部件组装成机床主体结构。
通过合理的顺序和方法进行零部件的安装和连接,同时进行各个部件之间的调试和调整。
4. 电气控制系统安装:安装数控机床的电气控制系统,包括主机控制板、电动机、传感器、按钮开关等。
同时进行电气系统的连线和调试。
5. 试运行和调试:将已组装好的数控机床进行试运行和调试。
通过设定不同的工艺参数,测试整机各项功能的正常性和精度水平,并进行调整和校正。
6. 整体性能测试:对数控机床进行整体性能测试。
测试机床的负载能力、速度、加工精度等技术指标,并进行必要的调整和改进。
7. 维护保养:完成数控机床的生产工艺流程后,进行维护保养工作。
包括对机床的清洁、润滑剂的添加、零部件的更换等,以保证机床的正常运行和延长使用寿命。
8. 成品查验:对最终生产的数控机床进行全面的检验。
检查机床的外观质量、性能指标是否符合标准要求,并进行相应的试运转和实际加工测试。
9. 包装和发货:对通过检验的数控机床进行标准化的包装,包括木箱包装和外包装。
同时进行相应的货运手续办理,将机床发往客户指定的地点。
10. 售后服务:对客户使用的数控机床进行售后服务。
提供技术指导、设备维修和升级等服务,以保证客户的满意度和机床的正常运行。
以上是一个常见的数控机床生产工艺流程的简要介绍,不同类型和规模的数控机床生产厂家可能会有所差异。
通过科学的生产工艺流程,可以提高机床产品的质量和性能,并满足市场的需求。
数控加工的工艺流程
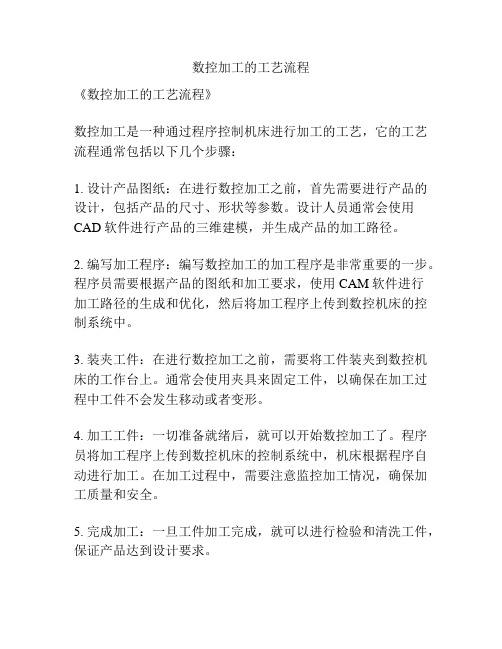
数控加工的工艺流程
《数控加工的工艺流程》
数控加工是一种通过程序控制机床进行加工的工艺,它的工艺流程通常包括以下几个步骤:
1. 设计产品图纸:在进行数控加工之前,首先需要进行产品的设计,包括产品的尺寸、形状等参数。
设计人员通常会使用CAD软件进行产品的三维建模,并生成产品的加工路径。
2. 编写加工程序:编写数控加工的加工程序是非常重要的一步。
程序员需要根据产品的图纸和加工要求,使用CAM软件进行
加工路径的生成和优化,然后将加工程序上传到数控机床的控制系统中。
3. 装夹工件:在进行数控加工之前,需要将工件装夹到数控机床的工作台上。
通常会使用夹具来固定工件,以确保在加工过程中工件不会发生移动或者变形。
4. 加工工件:一切准备就绪后,就可以开始数控加工了。
程序员将加工程序上传到数控机床的控制系统中,机床根据程序自动进行加工。
在加工过程中,需要注意监控加工情况,确保加工质量和安全。
5. 完成加工:一旦工件加工完成,就可以进行检验和清洗工件,保证产品达到设计要求。
总的来说,数控加工工艺流程包括产品设计、加工程序编写、工件装夹、加工和产品检验等步骤。
这种工艺流程不仅提高了加工效率和精度,也极大地减少了人工操作的需求,是现代制造业中不可或缺的一部分。
数控机床的工艺加工及操作编程

数控机床的工艺加工及操作编程数控机床是一种通过数字控制系统来实现自动化工艺加工的机床。
它可以根据预定的程序来进行精密的切削加工,具有高精度、高效率、灵活性强的特点。
在数控机床的工艺加工和操作编程中,需要考虑以下几个方面。
一、工艺加工:1.材料准备:首先需要准备加工所需的原材料,包括金属材料、塑料材料等。
2.工艺规划:根据零件的形状、尺寸和加工要求,制定出合理的工艺路线和加工工艺,包括切削刀具的选择、工件夹紧方式、切削刀具进给和转速等。
3.加工参数设定:根据工艺规划,设置数控机床的加工参数,包括切削速度、进给速度、主轴转速、切削深度和进给深度等。
4.工装夹具设计:设计和选择合适的工装夹具,用于固定工件和切削刀具。
5.数控编程:根据工艺路线和加工参数,编写数控程序,包括刀具路径、切削轨迹、切削方向和切削顺序等。
6.加工过程监控:在加工过程中,及时监控加工状态和加工精度,根据需要进行调整和修正。
7.加工后处理:对加工后的工件进行清洁、检查和检验,并进行必要的后续处理,如调整尺寸、修整表面等。
二、操作编程:1.数控机床的基本操作:包括开机、关机、启动和停止等基本操作。
2.数控系统操作:熟悉数控系统的功能和操作界面,学会使用数控系统的各种功能键和指令。
3.数控编程语言:掌握数控编程语言,如G代码和M代码,了解其语法规则和常用指令。
4.数控程序的编写:根据工艺路线和加工参数,编写数控程序,并进行模拟和调试。
5.数控程序的调整和修改:根据实际加工情况,对数控程序进行调整和修正,以保证加工质量和效率。
6.数控机床的故障排除:熟悉常见故障的排除方法,能够及时发现和解决数控机床的故障问题。
7.加工记录和统计:对每次加工进行记录和统计,包括加工时间、加工数量和加工效率等,以便于评估和改进加工工艺。
通过对数控机床的工艺加工和操作编程的详细了解与掌握,可以充分发挥数控机床的优势,提高加工效率和产品质量,实现机械制造的自动化和数字化。
数控车床 加工工艺流程
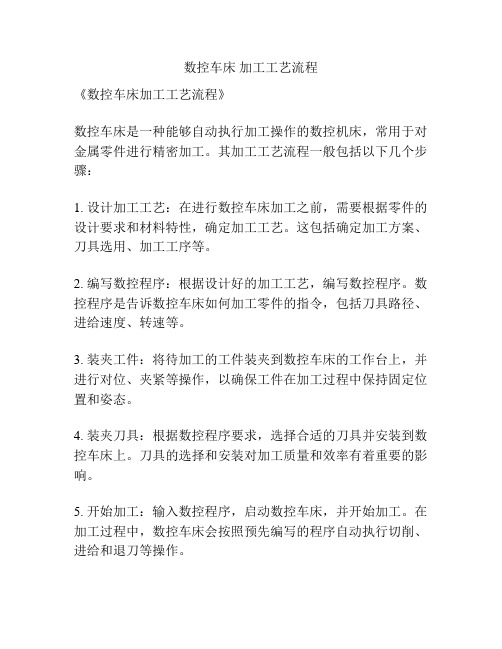
数控车床加工工艺流程
《数控车床加工工艺流程》
数控车床是一种能够自动执行加工操作的数控机床,常用于对金属零件进行精密加工。
其加工工艺流程一般包括以下几个步骤:
1. 设计加工工艺:在进行数控车床加工之前,需要根据零件的设计要求和材料特性,确定加工工艺。
这包括确定加工方案、刀具选用、加工工序等。
2. 编写数控程序:根据设计好的加工工艺,编写数控程序。
数控程序是告诉数控车床如何加工零件的指令,包括刀具路径、进给速度、转速等。
3. 装夹工件:将待加工的工件装夹到数控车床的工作台上,并进行对位、夹紧等操作,以确保工件在加工过程中保持固定位置和姿态。
4. 装夹刀具:根据数控程序要求,选择合适的刀具并安装到数控车床上。
刀具的选择和安装对加工质量和效率有着重要的影响。
5. 开始加工:输入数控程序,启动数控车床,并开始加工。
在加工过程中,数控车床会按照预先编写的程序自动执行切削、进给和退刀等操作。
6. 检测加工质量:在加工完成后,需要对加工零件进行质量检测。
这包括尺寸、表面粗糙度、形位公差等检测。
7. 完成工件:经过质量检测合格的零件,经过清洁、防锈等处理后,即可完成整个加工流程。
数控车床加工工艺流程的每一个步骤都需要严格执行,以确保零件加工的精度和质量。
同时,随着数控技术的不断发展和完善,数控车床加工工艺流程也在不断提高,为制造业的发展提供了更加高效和精密的加工手段。
数控加工工艺的特点
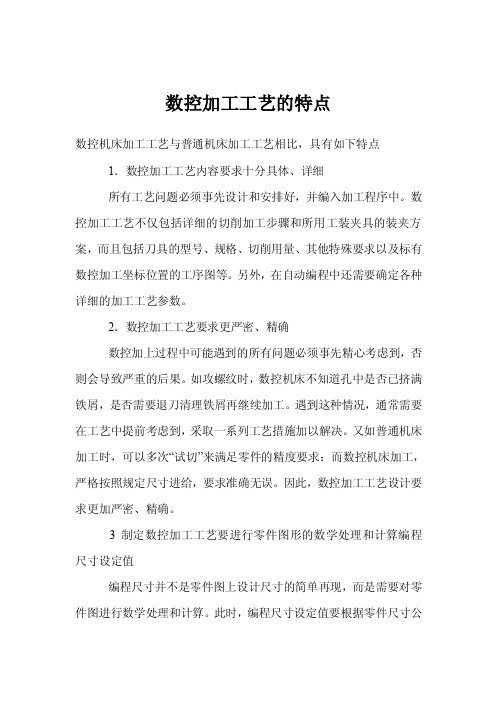
数控加工工艺的特点数控机床加工工艺与普通机床加工工艺相比,具有如下特点1.数控加工工艺内容要求十分具体、详细所有工艺问题必须事先设计和安排好,并编入加工程序中。
数控加工工艺不仅包括详细的切削加工步骤和所用工装夹具的装夹方案,而且包括刀具的型号、规格、切削用量、其他特殊要求以及标有数控加工坐标位置的工序图等。
另外,在自动编程中还需要确定各种详细的加工工艺参数。
2.数控加工工艺要求更严密、精确数控加上过程中可能遇到的所有问题必须事先精心考虑到,否则会导致严重的后果。
如攻螺纹时,数控机床不知道孔中是否已挤满铁屑,是否需要退刀清理铁屑再继续加工。
遇到这种情况,通常需要在工艺中提前考虑到,采取一系列工艺措施加以解决。
又如普通机床加工时,可以多次“试切”来满足零件的精度要求:而数控机床加工,严格按照规定尺寸进给,要求准确无误。
因此,数控加工工艺设计要求更加严密、精确。
3 制定数控加工工艺要进行零件图形的数学处理和计算编程尺寸设定值编程尺寸并不是零件图上设计尺寸的简单再现,而是需要对零件图进行数学处理和计算。
此时,编程尺寸设定值要根据零件尺寸公差要求和零件的形状几何关系重新调整计算,才能确定合理的编程尺寸。
4.考虑进给速度对零件形状精度的影响选挥切削用量时要考虑进给速度对加工零件形状精度的影响。
在数控加工中,刀具的移动轨迹足由插补运算完成的。
根据插补原理可知,在数控系统已定的条件下,进给速度越快,则插补精度越低,从而导致工件的轮廓形状精度就越差。
尤其是在高精度加工时,这种影响更加明显。
5.强调刀具选择的重要性复杂形面的加工编程通常采用自动编程方式。
自动编程时,必须先选定刀具再牛成刀具中心运动轨迹,因此,对于不具有刀具补偿功能的数控机床来说,若刀具预先选择不当,所编程序只能推倒重来。
6。
数控加工工艺的加工工序相对集中由于数控机床特别是功能复合化的数控机床,一般都带有自动换刀装置,因而在加工过程中能够自动换刀,一次装夹即可完成多迢工序或全部工序的加工。
数控加工工艺的概念及其内容

数控加工工艺的概念及其内容
数控加工工艺是指使用数控机床进行零件加工的一种工艺方法。
它涉及到加工设备、工艺、工装和自动加工过程的自动控制。
拟定数控加工工艺是进行数控加工的一项基础性工作,设备的最终使用效果取决于用户在数控加工中技术的掌握程度以及工艺的拟定是否正确和合理。
数控加工与普通机床加工在方法和内容上具有一定的相似之处,最大的区别在于控制方式。
数控加工的原理是运用专门的计算机,操作指令以数字方式表示,机器设备依照预先规定的程序进行工作。
在数控机床上进行零件加工,涉及的步骤和要素有工步、机床运动先后次序、位移量、行走路线、切削参数的选择等,这些都需要用数字化的代码表示,并编成程序,然后输入到数控装置中,通过计算机对输入的信息进行处理。
数控加工是解决零件品种多变、批量小、形状复杂、精度高等问题和实现高效化和自动化加工的有效途径。
零件图样的数控工艺性分析也是数控加工工艺的重要内容之一。
以上内容仅供参考,如需更多信息,建议查阅关于数控加工工艺的资料、文献或咨询该领域的专家。
- 1、下载文档前请自行甄别文档内容的完整性,平台不提供额外的编辑、内容补充、找答案等附加服务。
- 2、"仅部分预览"的文档,不可在线预览部分如存在完整性等问题,可反馈申请退款(可完整预览的文档不适用该条件!)。
- 3、如文档侵犯您的权益,请联系客服反馈,我们会尽快为您处理(人工客服工作时间:9:00-18:30)。
引言略目录1.数控加工工艺任务书 (1)2.零件的分析与毛坯的选择 (2)3.夹具的选择及工件定位方式的安排 (3)4.数控加工工艺规程的设计 (4)5.数控加工程序的具体编制 (5)6.对刀-加工坐标系设置的操作步骤……………6-77.数控铣床仿真操作具体要求………………… 8-98.数控加工工艺大作业体会 (10)9.参考文献 (11)10.附录(1)零件图(AUTOCAD出图)(2)三维立体图(3)数控加工工艺规程卡片(4)机械加工工序卡片(5)数控编程任务书(6)数控加工刀具卡片(7)数控加工走刀路线图(8)零件编程程序表上海第二工业大学数控加工工艺任务书题目:编排圆形坯料数控加工工艺及数控铣床FANUC-0i仿真加工内容: 1.零件图(AUTOCAD出图)2.三维软件出三维立体图3.数控加工工艺规程卡片4.机械加工工序卡片5.数控编程任务书6.数控加工刀具卡片7.数控加工走刀路线图8.零件编程程序表9.大作业设计报告原始资料:零件图一张,材料规格:¢80×20。
日期:x年x月x日-1-一、零件的分析与毛坯的选择1、零件的结构工艺性分析(1)零件的结构工艺性分析理论依据参见教科书。
(2)材料规格为¢80×20的圆料的数控机床加工工艺规程制定。
该零件的零件图如图1-1所示。
图1-1 ¢80×20圆料零件的零件图(2)由图1-1可以看出,该零件主要由凸台、内轮廓、盲孔等组成,结构形状较简单;零件的¢700+0.05 mm、30-0.05mm、12.5+0.05 mm、40-0.05mm四处尺寸精度要求较高,加工精度要求高;图上有4处R3的孔、8处R5的圆角、4处R10的圆弧;零件的全部粗糙度为3.2 ;该零件需在数控铣床上加工。
2、毛坯的选择(1)毛坯的选择理论依据参见教科书。
(2)实例依照加工题目知:要加工的零件为铣床圆料零件,材料为45#钢。
-2-二、夹具的选择及工件定位方式的安排(1)确定装夹方案根据零件外形、加工方案以及零件图分析可知,该工件采用如图2-1所示的三爪卡盘进行装夹。
该夹具满足一次装夹加工。
保证了零件的加工精度。
图2-1 三爪卡盘(2)工件定位方式的安排图2-2是圆料工件的装夹图,该工件在卡盘上的定位,便于在加工中对刀和测量,能保持较高的重复安装精度。
图2-2工件的装夹定位铣床圆料毛坯的安装方法是直接找正安装法,是借助于角尺、橡皮锤等工具,通过目测,一边校验,一边调整,来找正工件在机床上的位置,然后将其夹紧。
根据六点定位原则,使用三爪卡盘限制了三个自由度,待工件加紧之后,工件的六个自由度完全限制。
继而可以进行加工。
六点定位原则理论依据参见教科书。
-3-三、数控加工工艺规程的设计(1)工艺分析该零件的在精度方面有几处要求,粗糙度全部为Ra3.2mm。
(2)确定加工顺序及走刀路线1)加工顺序的拟定按照基面先行、先粗后精的原则确定。
因此,以底面为基准,开始加工各轮廓表面。
根据零件对各加工表面的要求,可采用如下的加工方案:铣外轮廓→铣内轮廓→打孔。
2)走刀路线以毛坯圆心为坐标系原点,然后对刀。
起刀点和终刀点分别为P1、P2。
铣外轮廓,刀具从P1点切入零件然后沿着点划线上的箭头的方向进行加工,最后回到P2点。
如图3-1:P2P3 P4P1图3-1外轮廓刀具轨迹图图3-2 内轮廓刀具轨迹图铣内轮廓,刀具从P3点切入然后沿着点划线上的箭头的方向进行加工,最后回到P3点。
如图3-2。
根据以上刀具轨迹图,将其制作填写到走刀路线图表中,详见附录。
(2)数控加工工艺规程路线的制定实例(理论依据参见教科书)主要三道工序:1) 工序3:以底面为基准,铣削工件的外轮廓,按图示尺寸达到要求;2)工序4:以底面为基准,铣削工件的内轮廓,按图示尺寸达到要求;3)工序5:以底面为基准,铣削工件的盲孔,按图示尺寸达到要求。
(3)工序规程卡片的填写机械加工工艺卡片详见附录。
在卡片中填入各个部分内容。
(4)机械加工工序的具体编制1)、加工设备与工艺装备的选择一般加工设备指机床,工艺装备指夹具、刀具和量具。
选择的理论依据参见教科书。
2)工序卡片的填写机械加工工序卡片详见附录。
在卡片中填入各个部分内容。
理论依据参见教科书。
3)根据零件加工的各道工序,使用合适的刀具,并制作一张刀具卡片。
详见附录。
-4-四、数控加工程序的具体编制1、用FANUC系统格式编写零件的轮廓加工程序,采用¢10、¢6铣刀,毛坯¢80×20mm 钢块,轮廓加工后多余部分用程序编程去除。
1) 加工图形轮廓。
第一次切深0.5mm,图形正确后再修改到Z-3.的深度,直到达到需要的深度。
2)刀补粗加工时可取D01=D02=5.2mm,(加工余量取0.1×2=0.2mm)全部深度切削完成后,修改刀补D01和D02的数值进行精加工调整。
3)在精加工时,要测量粗加工结束后的零件尺寸,再计算D01与D02的数值,修改后再进行精加工,计算如下:D01精=D01粗-|(B实际尺寸-B图纸尺寸)/2| D02精=D02粗-|(B实际尺寸-B图纸尺寸)/2|4)工件坐标系原点位于零件的中心,Zp位于工件的上表面。
O13801N10 G54 ;N20 M03 S800 ;N30 G90 G00 Z50. ;N40 X0 Y0 ;N50 X-40. Y-40. ‘N60 Z5. M08 ;N70 G01 Z-3. F10 ;N80 G41 X-35. Y-30. H01 ;N90 Y0 ;N100 G02 X-14.907 Y31.667 R35. ; N110 G02 X-8.518 Y29.762 R5. ;N120 G03 X8.518 Y29.762 R10. ; N130 G02 X14.907 Y31.667 R5. ; N140 G02 X31.667 Y14.907 R35. ; N150 G02 X29.762 Y8.518 R5. ;N160 G03 X29.762 Y-8.518 R10. ; N170 G02 X31.667 Y-14.907 R5. ; N180 G02 X14.907 Y-31.667 R35. ; N190 G02 X8.518 Y-29.762 R5. ;N200 G03 X-8.518 Y-29.762 R10. ; N210 G02 X-14.907 Y-31.667 R5. ; N220 G02 X-31.667 Y-14.907 R35. ; N230 G02 X-29.762 Y-8.518 R5. ; N240 G03 X-29.762 Y8.518 R10. ; N250 G02 X-31.667 Y14.907 R5. ; N260 G02 X-35. Y0 R-35. ; N270 G01 X-35. Y10. ;N280 G40 X-40. Y40. ;N290 G01 Z5. M09 ;N300 G00 Z50. ;N310 M05 ;N320 M00 ;N330 G54 ;N340 M03 S800 ;N350 G90 G00 Z50. ;N360 X-13. Y5. ;N370 Z5. M08 ;N380 G01 Z-4. F100 ;N390 G41 X-5. Y7.5. H02 ;N400 X0 ;N410 G02 X7.5 Y0 R7.5. ;N420 G03 X20. Y0 R6.25 ;N430 G03 X-10. Y17.32R-20. ;N440 G03 X-3.75 Y-6.495R6.25 ;N450 G02 X0 Y7.5 R7.5 ;N460 G01 X5. ;N470 G40 X13. Y5. ;N480 G01 Z5. M09 ;N490 G00 Z50. ;N500 M05 ;N510 M30;O13802N10 G55;N20 G17;N30 G90;N50 M03 S800;N60 G00 Z50.M08;N65 X0.Y0.;N70 G43 G00 Z5. H01;N80 G99 G81 X0. Y35.;Z-6. R5. F120;N90 X35.Y0.;N95 X0. Y-35.;N100 X-35. Y0.;N105 G80;N110 G01 Z5. M09;N120 G00 Z50.;N130M05;N140 M30;-5-五、对刀-加工坐标系设置的操作步骤数控编程时,应该首先确定工件坐标系和工件原点。
通常把零件的基准点作为工件原点。
以工件原点Op为坐标原点建立的Xp,Yp,Zp轴直角坐标系,称为工件工件坐标系,如图5-1所示。
这里介绍用工件原点相对于机床坐标系偏置的方法来设定工件坐标系,此时G54-G59指令来进行调用执行。
图5-1 工件坐标系的设定(1) G54-G59指令的含义格式:G54-G59说明:指令后参数(X,Y,Z,)值是工件原点在机床坐标系中的坐标值。
该方法是通过设置工件工件原点相对机床坐标系的坐标值,来设定工件坐标系的坐标值,来设定工件坐标系的。
工件坐标系设置过程又称为对刀操作。
通过对刀操作,得出工件坐标系相对于机床坐标系的偏移量(Lx,Ly,Lz)后输入数控系统。
再由程序调用执行,以确认工件坐标系的位置。
(2)机床坐标系的设置机床坐标系的设置是通过用手动返回机床参考点(回零)的操作来完成的,只要不断电或轴未进行锁住操作,机床零点就一直保持。
机床零点就一直保持。
因此,数控铣床开机或轴锁住解除后,必须先确定机床参考点。
机床参考点在以下三种情况下必须重新设定:1)机床关机以后重新接通电源开关时;2)机床解除急停状态后;3)机床超程报警信号解除以后;4)机床进行过轴锁住,如图形模拟显示后。
(3) G54-G59 设置的操作步骤1)机床进行手动回零后,选择手轮操作方式;2)正确安装并夹紧工件在工作台上的三爪卡盘内,正确安装并夹紧立铣刀在刀柄内;3)摇首轮,使刀具中心大约对准工件中心,将百分表的磁性表座上磁吸附在刀柄的外圆表面上,表座内安装百分表,调节表座使表测头触及工件的外圆表面,如图5-2(a)所示。
-6-(a)(b)图5-2 工件坐标系设定的操作4)转动表座,观察百分表指针的变化,摇手轮不断调节工作台的位置,使表座在转动大半圈的范围内,百分表在0.02范围内摆动即可。
将表座退磁,小心取下表座与表体;5)记录机床坐标系中X,Y轴坐标值(均为负值):-Lx,-Ly;6)用塞尺垫在工件上表面,摇手轮使主轴下移如图5-2(b)所示,直到移动塞尺的松紧适宜为止;7)记录机床坐标系中Z轴坐标值(均为负值):-Lz’,计算-Lz=-Lz’-塞尺厚度;8)摇手轮使主轴上移至安全位置;9)选择“录入”方式,进入G54-G59的设置界面;10)即工件坐标系就取代了机床坐标系。