转炉炼钢物料平衡计算
2019年物料平衡与热平衡计算.doc

钢铁冶金专业设计资料(炼铁、炼钢)本钢工学院冶化教研室二00三年八月第一章物料平衡与热平衡计算物料平衡和热平衡计算是氧气顶吹转炉冶炼工艺设计的一项基本的计算,它是建立在物质和能量不灭定律的基础上的。
它以转炉作为考察对象,根据装入转炉内或参与炼钢过程的全部物料数据和炼钢过程的全部产物数据,如图1-1-1所示的收入项数据和支出项数据,来进行物料的重量和热平衡计算。
通过计算,可以定量地掌握冶炼工重要参数,做到“胸中有数”。
对指导生产和分析研究改进冶炼工艺,设计转炉炼钢车间等均有其重要意义。
由于转炉炼钢过程是一个十分复杂的物理化学过程,很显然,要求进行精确的计算较为困难,特别是热平衡,只能是近似计算,但它仍然有十分重要的指导意义。
物料平衡和热平衡计算,一般可分为两面种方案。
第一种方案是为了设计转炉及其氧枪设备以及相应的转炉炼钢车间而进行的计算,通常侧重于理论计算,特别是新设计转炉而无实际炉型可以参考的情况下;另一种方案是为了校核和改善已投产的转炉冶炼工艺参数及其设备参数或者采用新工艺新技术等,而由实测数据进行的计算,后者侧重于实测。
本计算是采用第一种方案。
目前,我国顶吹转炉所采用的生铁基本上为低磷的(0.10~0.40%)和中磷的(0.40~1.00%)两种,对这两种不同含磷量生铁的冶炼工艺制度也不相同。
因此,下面以50吨转炉为例,分别就低磷生铁和高磷生铁两种情况,进行物料平衡和热平衡计算。
1.1原始数据1.1.1铁水成分及温度表1-1-11.1.2原材料成分表1-1-2 原材料成分2表铁水成分与温度2-1-1转炉冶炼钢种常为普通碳素钢和低合金钢,在此以要求冶炼BD3钢考虑,其成分见表2-1-331.1.4平均比热表1-1-41.1.5冷却剂用废钢作冷却剂,其成份与冶炼钢种成份的中限相同。
(见表1-1-3) 1.1.6反应热效应虽然炉内化学反应,实际上是在炉料温度和炉内上部气相温度之间的任一温度发生的,但反应热效应通常仍采用25℃作为参考温度,值得指出的是,反应热还与组分在铁水中存在形态有关,至今对参与化学反应有关的实际组成物还有不同的看法。
炼钢过程中的物料平衡与热平衡计算
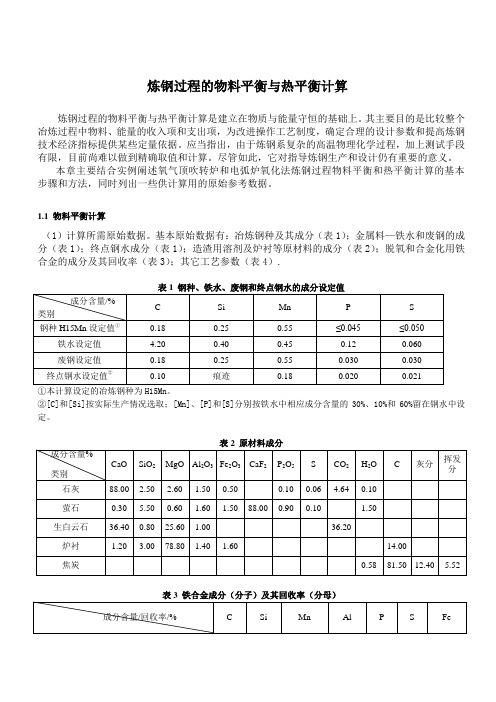
炼钢过程的物料平衡与热平衡计算炼钢过程的物料平衡与热平衡计算是建立在物质与能量守恒的基础上。
其主要目的是比较整个冶炼过程中物料、能量的收入项和支出项,为改进操作工艺制度,确定合理的设计参数和提高炼钢技术经济指标提供某些定量依据。
应当指出,由于炼钢系复杂的高温物理化学过程,加上测试手段有限,目前尚难以做到精确取值和计算。
尽管如此,它对指导炼钢生产和设计仍有重要的意义。
本章主要结合实例阐述氧气顶吹转炉和电弧炉氧化法炼钢过程物料平衡和热平衡计算的基本步骤和方法,同时列出一些供计算用的原始参考数据。
1.1 物料平衡计算(1)计算所需原始数据。
基本原始数据有:冶炼钢种及其成分(表1);金属料—铁水和废钢的成分(表1);终点钢水成分(表1);造渣用溶剂及炉衬等原材料的成分(表2);脱氧和合金化用铁合金的成分及其回收率(表3);其它工艺参数(表4).①本计算设定的冶炼钢种为H15Mn。
②[C]和[Si]按实际生产情况选取;[Mn]、[P]和[S]分别按铁水中相应成分含量的30%、10%和60%留在钢水中设定。
表2 原材料成分①10%C与氧生产CO2表4 其它工艺参数设定值收入项有:铁水、废钢、溶剂(石灰、萤石、轻烧白云石)、氧气、炉衬蚀损、铁合金。
支出项有:钢水、炉渣、烟尘、渣中铁珠、炉气、喷溅。
(3)计算步骤。
以100kg铁水为基础进行计算。
第一步:计算脱氧和合金化前的总渣量及其成分。
总渣量包括铁水中元素氧化、炉衬蚀损和加入溶剂的成渣量。
其各项成渣量分别列于表5、6和7。
总渣量及其成分如表8所示。
第二步:计算氧气消耗量。
氧气实际消耗量系消耗项目与供入项目之差,详见表9。
①由CaO还原出的氧量,消耗的CaO量=0.013×56/32=0.023kg表7 加入溶剂的成渣量石灰加入量计算如下:由表5~7可知,渣中已含(CaO)= -0.455+0.004+0.002+0.910=0.461kg;渣中已含(SiO2)=0.857+0.009+0.028+0.022=0.914kg.因设定的终渣碱度R=3.5;故石灰加入量为:[R∑w(SiO2)-∑w(CaO)]/[w(CaO石灰)-R×w(SiO2石灰)]= 2.738/(88.00%-3.5×2.50%)=3.45kg②为(石灰中CaO含量)—(石灰中S→CaS自耗的CaO量)。
炼钢物料平衡热平衡计算概述
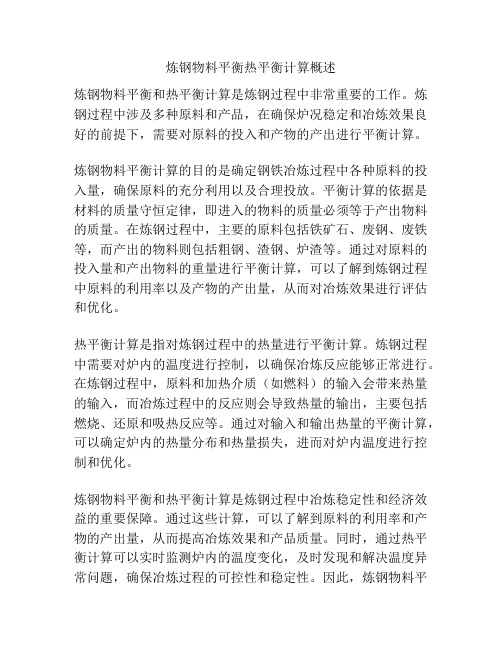
炼钢物料平衡热平衡计算概述炼钢物料平衡和热平衡计算是炼钢过程中非常重要的工作。
炼钢过程中涉及多种原料和产品,在确保炉况稳定和冶炼效果良好的前提下,需要对原料的投入和产物的产出进行平衡计算。
炼钢物料平衡计算的目的是确定钢铁冶炼过程中各种原料的投入量,确保原料的充分利用以及合理投放。
平衡计算的依据是材料的质量守恒定律,即进入的物料的质量必须等于产出物料的质量。
在炼钢过程中,主要的原料包括铁矿石、废钢、废铁等,而产出的物料则包括粗钢、渣钢、炉渣等。
通过对原料的投入量和产出物料的重量进行平衡计算,可以了解到炼钢过程中原料的利用率以及产物的产出量,从而对冶炼效果进行评估和优化。
热平衡计算是指对炼钢过程中的热量进行平衡计算。
炼钢过程中需要对炉内的温度进行控制,以确保冶炼反应能够正常进行。
在炼钢过程中,原料和加热介质(如燃料)的输入会带来热量的输入,而冶炼过程中的反应则会导致热量的输出,主要包括燃烧、还原和吸热反应等。
通过对输入和输出热量的平衡计算,可以确定炉内的热量分布和热量损失,进而对炉内温度进行控制和优化。
炼钢物料平衡和热平衡计算是炼钢过程中冶炼稳定性和经济效益的重要保障。
通过这些计算,可以了解到原料的利用率和产物的产出量,从而提高冶炼效果和产品质量。
同时,通过热平衡计算可以实时监测炉内的温度变化,及时发现和解决温度异常问题,确保冶炼过程的可控性和稳定性。
因此,炼钢物料平衡和热平衡计算是炼钢过程中不可或缺的重要环节。
炼钢物料平衡和热平衡计算在炼钢过程中起着非常重要的作用。
通过这些计算,冶炼厂可以更好地了解和控制物料的投入和产物的产出,实现冶炼过程的稳定运行和优化效果。
首先,炼钢物料平衡计算能够确保原料的充分利用和合理投放。
在炼钢过程中,钢厂会使用不同的原料,如铁矿石、废钢、废铁等。
这些原料的投入量需要经过平衡计算来确定,以确保原料的利用率最大化。
通过平衡计算,可以了解到每种原料的投入量,避免过量或不足的情况发生。
安钢150t转炉物料及热平衡计算分析与应用
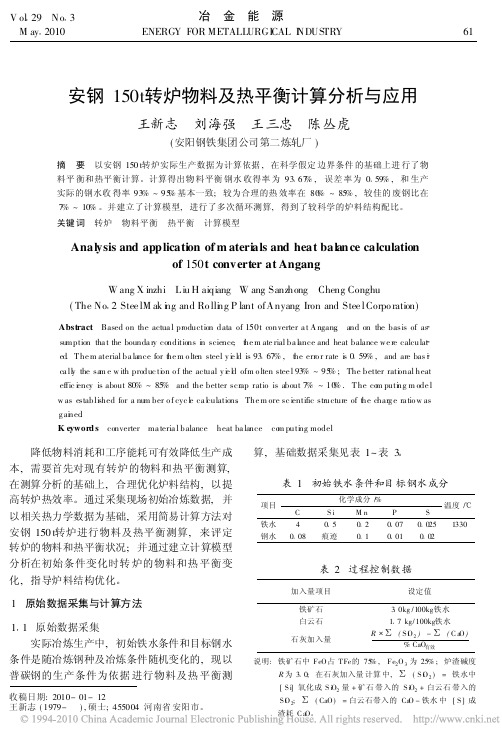
1 2 测算设定 ( 1) 炉气平均温度 1450 。 ( 2) 炉气中自由氧含量为 0 5% 。 ( 3) 金属中烧损的碳 90% 氧化为 CO, 10%
氧化为 CO2。 ( 4) 转炉渣中 TF e 15% 。 ( 5) 烟尘损失为钢铁料量的 1 16% , 其中
Analysis and app lication of m aterials and heat balan ce calculation of 150t converter at Angang
W ang X inzhi L iu H aiqiang W ang Sanzhong Cheng Conghu ( The No 2 Stee lM ak ing and Ro lling P lant of Anyang Iron and Stee l Corpo ration)
降低物料消耗和工序能耗可有效降低生产成 本, 需要首先对现有转炉的物料和热平衡测算, 在测算分析的基础上, 合理优化炉料结构, 以提 高转炉热效率。通过采集现场初始冶炼数据, 并 以相关热力学数据为基础, 采用简易计算方法对 安钢 150 t转炉进行物料及热平衡测算, 来评定 转炉的物料和热平衡状况; 并通过建立计算模型 分析在初始条件变化时转 炉的物料和热 平衡变 化, 指导炉料结构优化。
说明: 铁矿石中 FeO 占 TFe的 75% , Fe2O 3 为 25% ; 炉渣碱度 R 为 3 0; 在石灰加入量 计算 中, ! ( S iO 2 ) = 铁水中 [ S i] 氧化成 S iO2 量 + 矿石 带入的 S iO2 + 白云石 带入的 S iO 2; ! ( CaO ) = 白云石带入的 CaO - 铁水 中 [ S ] 成 渣耗 C aO。
炼钢物料平衡热平衡计算

安徽工业大学炼钢厂设计样本
指导中层隔水管计算 .................................................................................................... 34 3.3.4 外层管计算 ............................................................................................................ 34 3.3.5 氧枪冷却水升温的核算 ........................................................................................ 35 3.3.6 喷头与氧枪尺寸的结合:可最后确定喷头图尺寸。 ........................................ 35 3.4 列出喷头,氧枪的设计参数表 ....................................................................................... 35 4 转炉炼钢课程设计的主要内容 ................................................................................................. 36
周俐11原始数据收集或给定12物料平衡计算121炉渣量及炉渣成分的计算122矿石及烟尘中的铁量和氧量的计算123炉气成分及重量的计算124未加废钢时氧气的消耗量的计算10125钢水量计算11126未加废钢时的物料平衡表1113热平衡计算取冷料为2511131热收入项11132热支出项12133热平衡表1314加入废钢和脱氧后的物料平衡计算14141加入废钢的物料平衡计算14142脱氧后的物料平衡计算50吨转炉炉型设计计算1821转炉炉型及主要参数18211转炉三种炉型介绍18212炉子各部分主要尺寸参数的确定和计算1822炉型设计计计算举例22221原始条件22222熔池尺寸计算22223取炉帽尺寸计算24224出钢口尺寸计算24225炉子内型高度的计算24226炉衬厚度的选定24227炉子高宽比的确定24228氧气顶吹转炉主要参数表2631喷咀理论与设计26311有关公式553726312参数分析2732喷头计算步骤32321原始数据32322有关参数的计算和确定3233枪身设计33331设计数据33332中心氧管计算33安徽工业大学炼钢厂设计样本指导教师
第2章炼钢过程的物料平衡和热平衡计算
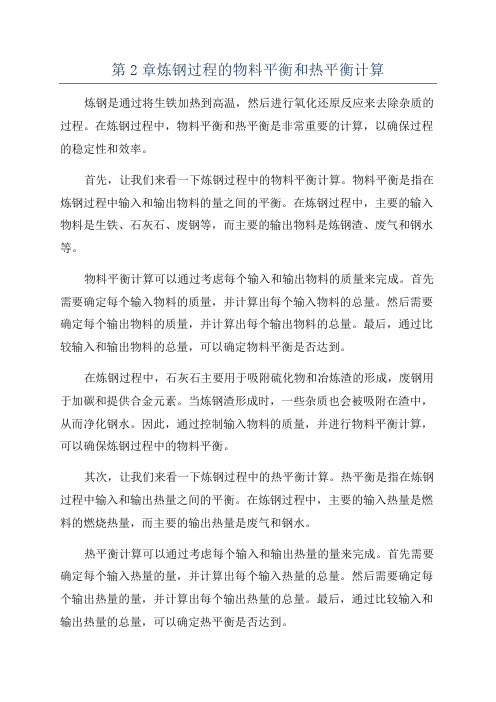
第2章炼钢过程的物料平衡和热平衡计算炼钢是通过将生铁加热到高温,然后进行氧化还原反应来去除杂质的过程。
在炼钢过程中,物料平衡和热平衡是非常重要的计算,以确保过程的稳定性和效率。
首先,让我们来看一下炼钢过程中的物料平衡计算。
物料平衡是指在炼钢过程中输入和输出物料的量之间的平衡。
在炼钢过程中,主要的输入物料是生铁、石灰石、废钢等,而主要的输出物料是炼钢渣、废气和钢水等。
物料平衡计算可以通过考虑每个输入和输出物料的质量来完成。
首先需要确定每个输入物料的质量,并计算出每个输入物料的总量。
然后需要确定每个输出物料的质量,并计算出每个输出物料的总量。
最后,通过比较输入和输出物料的总量,可以确定物料平衡是否达到。
在炼钢过程中,石灰石主要用于吸附硫化物和冶炼渣的形成,废钢用于加碳和提供合金元素。
当炼钢渣形成时,一些杂质也会被吸附在渣中,从而净化钢水。
因此,通过控制输入物料的质量,并进行物料平衡计算,可以确保炼钢过程中的物料平衡。
其次,让我们来看一下炼钢过程中的热平衡计算。
热平衡是指在炼钢过程中输入和输出热量之间的平衡。
在炼钢过程中,主要的输入热量是燃料的燃烧热量,而主要的输出热量是废气和钢水。
热平衡计算可以通过考虑每个输入和输出热量的量来完成。
首先需要确定每个输入热量的量,并计算出每个输入热量的总量。
然后需要确定每个输出热量的量,并计算出每个输出热量的总量。
最后,通过比较输入和输出热量的总量,可以确定热平衡是否达到。
在炼钢过程中,需要控制燃料的燃烧速率和炉内气体的流动速率,以确保输入和输出热量的平衡。
此外,还可以通过热回收和余热利用来提高热平衡效果。
例如,可以使用余热回收装置来回收废气中的热能,并将其用于加热其他冷却介质。
综上所述,物料平衡和热平衡计算是炼钢过程中非常重要的计算。
通过控制输入物料的质量和量,并考虑输入和输出热量的平衡,可以确保炼钢过程的稳定性和效率。
此外,还可以使用其他技术和设备来提高物料平衡和热平衡效果,以进一步提高炼钢过程的效率。
转炉炼钢的物料平衡与热平衡
4.6 转炉炼钢的物料平衡及热平衡[5]炼钢过程的物料平衡和热平衡计算是建立在物质与能量守恒的基础上的。
其主要目的是比较整个冶炼过程中物料、能量的收入项和支出项,为改进操作工艺制度,确定合理的设计参数和提高炼钢技术经济指标提供某些定量依据。
应当指出,由于炼钢是复杂的高温物理化学过程,加上测试手段有限,目前尚难以做到精确取值和计算。
尽管如此,它对指导炼钢生产和设计仍有重要的意义。
转炉炼钢的过程是一个很复杂的物理化学变化过程,对其作完全定量的分析是不可能的,但是一些基本的规律和原理在该过程中仍然适用。
比如说转炉炼钢过程遵循物质不灭和能量守恒定律,在这个基础上建立了转炉炼钢过程中的物料平衡和热平衡计算。
用来研究转炉收入、支出的物质和能量在数量上的平衡关系,并用平衡方程式、平衡表或者物流及热流图表示出来。
通过物料平衡和热平衡的计算可以全面的掌握转炉的物料和能量的利用情况,了解转炉的工作能力和热效率,从而为改进工艺、实现转炉最佳操作探索途径,并为降低原材料消耗及合理利用能源和节能提供方向。
总的来说,物料平衡和热平衡的计算一方面可以指导车间或设备的设计,比如说转炉及其供氧设备,或者炼钢车间的设计;另一方面可以改善和校核已投产的转炉冶炼工艺参数、设备适应性能,比如说确定加入冷却剂的数量和时间,或者采用新技术等而由实测数据进行的计算,比如说设计一些自动控制模型时的计算。
4.6.1 物料平衡[12]物料平衡是计算炼钢过程中加入炉内和参与炼钢过程的全部物料(铁水、废钢、氧气、冷却剂、渣料和耐材等)及炼钢过程中产物(钢液、炉渣、炉气及烟尘等)之间的平衡关系。
以下通过举例进行计算分析。
1.原材料成分表4.9铁水、废钢成分(%)表4.10渣料和炉衬材料成分(%)表4.11各项目的热容表4.12反应热效应(25℃)2.其它假设条件(根据各类转炉生产实际过程假设):(1)炉渣中铁珠量为渣量的8%;(2)喷溅损失为铁水量的1%;(3)熔池中碳的氧化生成90%CO,10%CO2;(4)烟尘量为铁水量的1.6%,其中烟尘中FeO=77%,Fe2O3=20%;(5)炉衬侵蚀量为铁水量的0.5%;(6)炉气温度取1450℃,炉气中自由氧含量为总炉气量的0.5%;(7)氧气成分:98.5%O2,1.5%N2。
物料平衡 热平衡 转炉
物料平衡热平衡转炉物料平衡、热平衡和转炉是冶金工程领域中的重要概念。
本文将深入探讨这三个主题,从基本概念到实际应用进行逐步解析,并对其在转炉过程中的应用进行详细讲解。
一、物料平衡物料平衡是冶金工程中的一个重要概念,指的是在一个系统中输入和输出物料的总量必须保持平衡。
这个平衡关系可以通过以下公式表示:输入物料= 输出物料+ 增加物料- 减少物料其中,增加物料是系统内新增的物料量,减少物料是系统内减少的物料量。
物料平衡是冶金工程中进行计算和控制的基础。
通过对物料平衡的准确计算,可以确保系统正常运行,并保持稳定的生产状况。
在转炉过程中,物料平衡是非常重要的。
转炉是一种用于冶炼、精炼和合金化的设备,通过将原料和燃料加入到转炉中,利用高温和化学反应将原料转化为所需的金属产品。
在转炉中,物料平衡的准确控制和计算可以提高生产效率、降低能源消耗,并确保产品质量稳定。
二、热平衡热平衡是指系统中输入和输出的热量必须保持平衡。
一个系统中的热平衡可以通过以下公式表示:输入热量= 输出热量+ 产生热量- 消耗热量其中,产生热量是系统内产生的热量,消耗热量是系统内消耗的热量。
热平衡的准确计算和控制是保证系统正常运行和能量效率的关键。
在转炉过程中,热平衡是非常重要的。
在转炉内,燃料燃烧产生的热量被用于原料的冶炼、精炼和合金化。
同时,热量还会通过系统的一些其他途径(如散热、冷却等)被消耗。
通过准确计算和控制热平衡,可以提高能源利用率,降低能源消耗,确保系统高效稳定地运行。
三、转炉转炉是一种非常重要的冶金设备,广泛应用于钢铁和有色金属冶炼工业中。
通过转炉,原料和燃料被加入到设备中,利用高温和化学反应将原料转化为所需的产品。
在转炉过程中,物料平衡和热平衡是两个非常重要的概念。
通过准确计算和控制物料平衡,可以确保输入和输出物料的平衡,保证生产过程的稳定性和产品质量的一致性。
通过准确计算和控制热平衡,可以提高能源利用率,降低能源消耗,保证系统的高效运行。
炼钢过程中的物料平衡与热平衡计算
炼钢过程中的物料平衡与热平衡计算炼钢是一种重要的冶金工艺,通过加热和处理铁矿石和其他原料,从而将其转化为钢铁。
在炼钢过程中,物料平衡和热平衡的计算是保证炼钢过程顺利进行的关键。
1.物料平衡计算物料平衡计算是指在炼钢过程中,对原料和产物之间的质量变化进行控制和监测。
物料平衡计算的基本原理是质量守恒定律,即物质在任何化学反应和过程中,质量不能被创造或破坏。
在炼钢过程中,主要的原料包括铁矿石、废钢和其他合金。
物料平衡计算的目的是确定原料和产物之间的质量变化以及原料的流量。
以基本的炼钢炉为例,物料平衡计算可以分为三个主要步骤:1)原料质量和流量测量:测量并记录原料的质量和流量,包括铁矿石、废钢和其他合金的输入。
2)化学反应和质量变化计算:根据炼钢过程中的化学反应,计算原料和产物之间的质量变化。
这包括原料的表面吸附、化学反应和挥发物的产生。
3)产物质量和流量测量:测量并记录产物的质量和流量,包括钢铁和炉渣的输出。
通过这些步骤,可以得到原料和产物之间的质量平衡关系。
通过不断调整原料的输入和产物的输出,可以确保炼钢过程中的物料平衡。
热平衡计算是指在炼钢过程中,通过计算热量的吸收和释放,以确保炉内的温度可以达到所需的炼钢温度。
在炼钢过程中,有几种主要的热量转移方式,包括辐射、传导、对流和蒸发。
热平衡计算的基本原理是能量守恒定律,即能量不能被创造或破坏。
热平衡计算可以分为以下几个步骤:1)炉内温度测量:通过在炉内安装温度传感器,可以测量和记录炉内的温度分布。
2)热量输入和输出计算:通过测量原料的热量输入和产物的热量输出,可以计算总的热量平衡。
热量输入包括燃料燃烧生成的热量和化学反应产生的热量。
热量输出包括炉渣的热量、废气的热量以及钢铁的热量。
3)热量转移计算:通过计算炉内热量的传导、辐射、对流和蒸发,可以确定炉内的热量分布。
这可以通过数学模型和计算方法进行计算。
通过热平衡计算,可以确定炉内的温度分布,并根据需要进行调整。
炼钢过程中地物料平衡与热平衡计算
炼钢过程的物料平衡与热平衡计算炼钢过程的物料平衡与热平衡计算是建立在物质与能量守恒的基础上。
其主要目的是比较整个冶炼过程中物料、能量的收入项和支出项,为改进操作工艺制度,确定合理的设计参数和提高炼钢技术经济指标提供某些定量依据。
应当指出,由于炼钢系复杂的高温物理化学过程,加上测试手段有限,目前尚难以做到精确取值和计算。
尽管如此,它对指导炼钢生产和设计仍有重要的意义。
本章主要结合实例阐述氧气顶吹转炉和电弧炉氧化法炼钢过程物料平衡和热平衡计算的基本步骤和方法,同时列出一些供计算用的原始参考数据。
1.1 物料平衡计算(1)计算所需原始数据。
基本原始数据有:冶炼钢种及其成分(表1);金属料—铁水和废钢的成分(表1);终点钢水成分(表1);造渣用溶剂及炉衬等原材料的成分(表2);脱氧和合金化用铁合金的成分及其回收率(表3);其它工艺参数(表4).表1 钢种、铁水、废钢和终点钢水的成分设定值①本计算设定的冶炼钢种为H15Mn。
②[C]和[Si]按实际生产情况选取;[Mn]、[P]和[S]分别按铁水中相应成分含量的30%、10%和60%留在钢水中设定。
表2 原材料成分表3 铁合金成分(分子)及其回收率(分母)①10%C与氧生产CO2表4 其它工艺参数设定值(2)物料平衡基本项目。
收入项有:铁水、废钢、溶剂(石灰、萤石、轻烧白云石)、氧气、炉衬蚀损、铁合金。
支出项有:钢水、炉渣、烟尘、渣中铁珠、炉气、喷溅。
(3)计算步骤。
以100kg铁水为基础进行计算。
第一步:计算脱氧和合金化前的总渣量及其成分。
总渣量包括铁水中元素氧化、炉衬蚀损和加入溶剂的成渣量。
其各项成渣量分别列于表5、6和7。
总渣量及其成分如表8所示。
第二步:计算氧气消耗量。
氧气实际消耗量系消耗项目与供入项目之差,详见表9。
表5 铁水中元素的氧化产物及其成渣量①由CaO还原出的氧量,消耗的CaO量=0.013×56/32=0.023kg表6 炉衬蚀损的成渣量表7 加入溶剂的成渣量石灰加入量计算如下:由表5~7可知,渣中已含(CaO)= -0.455+0.004+0.002+0.910=0.461kg;渣中已含(SiO2)=0.857+0.009+0.028+0.022=0.914kg.因设定的终渣碱度R=3.5;故石灰加入量为:[R∑w(SiO2)-∑w(CaO)]/[w(CaO石灰)-R×w(SiO2石灰)]= 2.738/(88.00%-3.5×2.50%)=3.45kg②为(石灰中CaO含量)—(石灰中S→CaS自耗的CaO量)。
- 1、下载文档前请自行甄别文档内容的完整性,平台不提供额外的编辑、内容补充、找答案等附加服务。
- 2、"仅部分预览"的文档,不可在线预览部分如存在完整性等问题,可反馈申请退款(可完整预览的文档不适用该条件!)。
- 3、如文档侵犯您的权益,请联系客服反馈,我们会尽快为您处理(人工客服工作时间:9:00-18:30)。
1.转炉炼钢物料平衡计算 1.1计算原始数据 基本原始数据:冶炼钢种及其成分、铁水和废钢成分、终点钢水成分(表1);造渣用溶剂及炉衬等原材料的成分(表2);脱氧和合金化用铁合金的成分及其回收率(表3);其他工艺参数(表4)。 表1 钢水、铁水、废钢和终点钢水的成分设定值 成分含量/% 类别 C Si Mn P S
钢种Q235设定值 0.18 0.25 0.55 ≤0.045 ≤0.050 铁水设定值 4.10 0.90 0.55 0.300 0.035 废钢设定值 0.18 0.25 0.55 0.030 0.030 终点钢水设定值 0.10 痕迹 0.18 0.020 0.021 aa[C]和[Si]按实际产生情况选取;[Mn]、[P]和[S]分别按铁水中相应成分含量的30%、10%和60%留在刚水中设定。 表2 原材料成分 成分/% 类别 CaO SiO2 MnO Al2O3 Fe2O3 CaF2 P2O5 S CO2 H2O C 灰分 挥发分 石灰 87.00 2.80 2.70 1.80 0.60 0.10 0.06 4.84 0.10 萤石 0.30 5.40 0.70 1.60 1.50 88.00 0.90 0.10 1.50 生白云石 37.40 0.80 24.60 1.00 36.2 炉衬 1.20 3.00 78.80 1.40 1.60 14.0 焦炭 0.58 81.5 12.4 5.52 表3 铁合金成分(分子)及其回收率(分母) 成分含量/回收率/% 类别 C Si Mn Al P S Fe
硅铁 — 73.00/75 0.50/ 80 2.50/ 0 0.05/ 100 0.03/ 100 23.92/100
锰铁 6.60/ 90 0.50/ 75 67.8/ 80 — 0.23/ 100 0.13/ 100 24.74/100
10%与氧生成CO2。 表4 其他工艺参数设定值 名称 参数 名称 参数 终渣碱度 萤石加入量 生白云石加入量 炉衬蚀损量 终渣∑ω(FeO)含量(按向钢中传氧量ω(Fe2O3) =1.35ω(FeO)折算) 烟尘量 喷吹铁损 W(CaO)/W(SiO2)=3.5 为铁水量得0.5% 为铁水量得2.5% 为铁水量得0.3% 15%,而W(Fe2O3)/∑w(FeO)=1/3,即W(Fe2O3)=5% W(FeO)=8.25% 为铁水量得1.5%(其中W(FeO)75%, W(Fe2O3)为20%) 为铁水量得1% 渣中铁损(铁珠) 氧气纯度 炉气中自由氧含量 气化去硫量 金属中[C]的氧化产物 废钢量
为渣量的6% 99%,余者为N2
0.5%(体积比) 占总去硫量得1/3 90%C氧化成CO,10%C氧化成CO2
由热平衡计算确定,本计算结果为铁水量的13.64%,即废钢比为12.00% 1.2物料平衡基本项目 收入项有:铁水、废钢、溶剂、氧气、炉衬损失、铁合金。 支出项有:钢水、炉渣、烟尘、渣中铁珠、炉气、喷溅。
1.3计算步骤 以100kg铁水为基础进行计算。 1.3.1计算脱氧和合金化前的总渣量及其成分
总渣量包括铁水中元素氧化,炉衬蚀损和加入溶剂的成渣量。其各项成渣量分别列于表5-表7。总渣量及其成分如表8所示。
表5 铁水中元素的氧化产物及其成渣量 元素 反应产物 元素氧化量/kg 耗氧量/kg 产物量/kg 备注
C Si Mn P S Fe [C]→{CO} [C]→{CO2} [Si]→(SiO2) [Mn]→(MnO) [P]→(P2O5) [S]→{SO2} [S]+(CaO)→(CaS)+(O) [Fe]→(FeO) [Fe]→(Fe2O3) 4.09×90%=3.681 4.09×10%=0.409 0.870 0.430 0.160 0.015×1/3=0.005 0.015×2/3=0.010 1.16×56/72=0.902 0.645×112/160 = 0.452 4.908 1.087 0.979 0.123 0.204 0.005 -0.005① 0.258 0.194 8.589 1.496 1.860 0.553 0.364 0.010 0.021(CaS) 1.16 0.645
入渣 入渣 入渣
入渣 入渣(见表8)
入渣(见表8) 合 计 6.919 7.753 成渣量 4.613 入渣组分之和 由CaO还原出的氧量;消耗的CaO量=0.01×56/32=0.018kg。
表6 炉衬蚀损的成渣量 炉衬蚀损量/kg 成渣组分/kg 气态产物/kg 耗氧量/kg CaO SiO2 MgO Al2O Fe2O C→CO C→CO2 C→CO,CO2
0.3 (据表4) 0.004 0.009 0.236 0.004 0.005 0.3×14%×90%×28/12=0.088 0.3×14%×10%×44/12=0.015 0.3×14%(90%×16/12+10%×32/12)=0.062
合 计 0.258 0.103 0.062 表7 加入溶剂的成渣量
类 别 加入量/kg
成渣组分/kg 气态产物/kg
CaO MgO SiO2 Al2O3 Fe2O3 P2O5 CsS CaF2 H2O CO2 O2
萤 石 0.5(表4) 0.002 0.004 0.027 0.008 0.008 0.005 0.001 0.440 0.008
生白云石 2.5(表
4) 0.935 0.615 0.020 0.025 0.905
石 灰 7.49 6.498 0.202 0.221 0.135 0.045 0.007 0.010 0.008 0.363 0.002 合 计 7.435 0.821 0.257 0.168 0.053 0.012 0.011 0.440 0.016 1.268 0.002 成渣量 9.197 石灰加入量计算如下:由表5—表7可知,渣中已含(CaO)=–0.018+0.004+0.002+0.935=0.923kg;渣中已含(SiO2)=1.860+0.009+0.027+0.020=1.916kg。因设定的终渣碱度R=3.5,故石灰加入量为: [R∑ω(SiO2)-∑ω(CaO)]/[ω(CaO石灰)-R×ω(SiO2石灰)]=5.783/(87.0%-3.5×2.8%)=7.49kg。 (石灰中CaO含量)—(石灰中S—CaS自耗的CaO量) 由CaO还原出来的氧量,计算方法同表5的注。
表8 总渣量及其成分 炉渣成分 CaO SiO2 MgO Al2O3 MnO FeO Fe2O3 CaF2 P2O5
CsS 合计
元素氧化成渣量/kg 石灰成渣量/kg 炉衬蚀损成渣量/kg 生白云石成渣量/kg 萤石成渣量/kg
6.498 0.004 0.935 0.002 1.860 0.210 0.009 0.020 0.027 0.202 0.236 0.615 0.004 0.135 0.004 0.025 0.008 0.553 1.16 0.607 0.045 0.005 0.008 0.440 0.364 0.007 0.005 0.021 0.010 0.001 4.603 7.107 0.258 1.585 0.495 总渣量/kg 7.439 2.126 1.057 0.172 0.553 1.160 0.703 0.440 0.375 0.032 14.056
质量分数/% 52.92 15.13 7.52 1.22 3.93 8.25 5.00 3.13 2.68 0.23 100.00 总渣量计算如下:表8中除(FeO)和(Fe2O3
)以外的渣量为:
7.439+2.216+1.057+0.172+0.553+0.44+0.376+0.032=12.194kg,而终渣∑ω(FeO)=15%(表4),故总量为:12.194÷86.75%=14.056kg。 ω(FeO)=14.056×8.25%=1.16kg。 ω(Fe2O3
)=14.056×5%-0.045-0.005-0.008=0.645kg。
1.3.2计算氧气消耗量 氧气实际消耗量消耗项目与供入项目之差。见表9。 表9 实际耗氧量 耗氧项/kg 供氧项/kg 实际氧气消耗项/kg 铁水中氧化耗氧量 (表5) 7.753
炉衬中碳氧化耗氧量 (表6) 0.062 石灰中S与CaO反应还原出的氧气量(表7) 0.002
烟尘中铁氧化耗氧量 (表4) 0.340
8.215-0.002+ 0.065①=8.28 炉气自由氧含量(表10) 0.06 合 计 8.215 合 计 0.002 炉气N2
(存在于氧气中,表4)的质量,详见表10。.
1.3.3计算炉气量及其成分
炉气中含有CO、CO2、N2、SO2和H2O。其中CO、CO2、SO2和H2O可由表5-表7查得,O2和N2则由炉气总体积来确定。现计算如下。 炉气总体积V∑: V∑=Vg+0.5%V∑+1/99×(22.4/32Gs+0.5%V∑-Vx) V∑=99Vg+0.7Gs-Vx98.5 =(99×8.375+0.7×8.155-0.002×22.4/32)/98.50=8.475㎡ 式中 Vg—CO、CO2、SO2和H2O各组分总体积,m3。本计算中,其值为:
8.677×22.4/28+2.729×22.4/44+0.010×22.4/64+ 0.016×22.4/18=8.375m3。
Gs—不计自由氧的氧气消耗量,kg。本计算中,其值为:7.753+0.062+ 0.34=8.155kg(见表9); Vx—石灰中的S与CaO反应还原出的氧量(其质量为:0.002kg,见表9),m3;