烷基化装置概况特点及工艺原理
烷基化反应器介绍 (2)
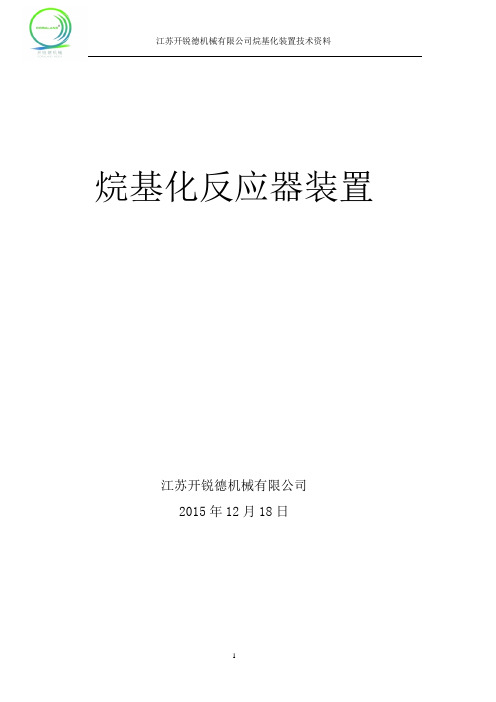
烷基化反应器装置江苏开锐德机械有限公司2015年12月18日目录第一部分公司简介 (3)第二部分烷基化反应器装置简图 (4)第三部分技术文件 (6)1.技术参数表2.产品主要技术特点描述3.烷基化反应器装置说明4.传动系统介绍第四部分产品质量控制 (10)1.主要制造、验收标准2.制造工艺第五部分安装、售后服务 (14)1.设备安装调试施工方案2.售后服务第六部分主要业绩 (15)第一部分公司简介江苏开锐德机械有限公司是一家以石油化工设备和环保设备的生产、化工技术服务为主的高科技、新能源、技术密集型企业。
公司位于江苏省扬州市邗江区扬州环保科技产业园内。
公司创立于2007年初,2014年6月11日改组注册为江苏开锐德机械有限公司,目前,公司已经取得A1(高压容器)、A2(第三类低、中压容器)级压力容器制造许可证,通过了ISO9001质量管理体系经、ISO14001环境管理体系认证。
公司主要从事化工机械、石油装备、环保水处理等行业的研发制造、销售。
同时公司与设计院(武汉炼化工程设计有限责任公司、中石油华东设计院、胜利油田炼化工业设计院、上海华西设计院、中国环球工程公司辽宁分公司等)、研究院所(石科院、抚顺石油化工研究院、大连化学物理研究所等)、高校(石油大学、东南大学、东华大学等)建立了良好合作关系。
公司将致力于为客户提供技术领先、节能低耗的优质产品和服务,致力于与客户共同发展。
“管理创造价值,服务提升优势,品质至上,服务至优”是公司的发展理念;“团结、创新、务实、奋进”是公司矢志不渝的追求。
公司将积极贯彻《中国制造2025》行动纲领,坚持落实创新驱动、质量为先、绿色发展、结构优化、人才为本的基本方针,致力于为客户提供优质产品和服务,致力于与客户共同发展。
第二部分烷基化反应器装置简图1.设备主体部件2.烷基化反应器开口说明第三部分技术文件1、技术参数表1.1 烷基化反应器主要技术参数表2、产品主要技术特点描述1.选用国内外先进可靠的工艺技术和生产方案,使设计的装置达到“安、稳、长、满、优”安全生产,产品的质量竞争力强,装置的能耗和物耗水平尽可能低。
烷基化装置

烷基化装置一、背景介绍烷基化是一种重要的化学反应过程,用于合成烷基化合物。
烷基化装置是用来进行烷基化反应的设备,通常由反应器、加热装置、冷却装置、催化剂装置等部分组成。
二、烷基化反应原理烷基化反应是一种通过在烷基化催化剂的作用下,将烯烃或烷烃与烯烃发生加成反应,生成烷基化合物的化学反应。
这种反应通常需要高温和高压条件下进行。
三、烷基化装置的组成1.反应器:通常为不锈钢或其他耐高温、高压材料制成,用于容纳反应物和催化剂进行反应。
2.加热装置:用于提供反应所需的高温条件,通常采用电加热或其他加热方式。
3.冷却装置:用于控制反应温度,防止反应温度过高。
常见的冷却方式包括水冷却和空气冷却。
4.催化剂装置:用于催化烷基化反应的进行,通常选择适合的催化剂可以提高反应速率和选择性。
四、烷基化装置的运行过程1.将原料加入反应器中。
2.启动加热装置,提高反应器内温度至反应所需温度。
3.注入催化剂。
4.加热反应器至反应温度,开始烷基化反应。
5.根据反应情况控制冷却装置的温度,保持反应温度稳定。
6.反应结束后,停止加热和冷却,将产物从装置中取出。
五、烷基化装置的应用烷基化装置广泛应用于石油化工、有机合成等领域,用于制备各种烷基化合物,如乙基苯、苯乙烯、异丙醇等。
这些化合物在化工生产中具有重要的用途,是许多化学产品的重要原料。
六、总结烷基化装置是进行烷基化反应的重要设备,其具有广泛的应用领域和重要的经济意义。
通过对烷基化装置的结构、原理和运行过程的研究,可以更好地掌握烷基化反应的工艺条件,提高生产效率和产品质量,促进化工行业的发展。
烷基化工艺:烷基化工艺主要操控点
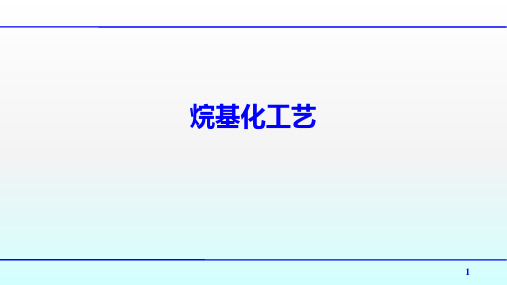
4
二、烷基化工艺主要操控点
2.分馏塔
分馏塔的操作较为重要的有:搞好丙烷和循环异丁烷、异丁烷和正丁烷的分离,既要保证 烷基化油的最大产量,同时也要兼顾好产品的辛烷值符合工艺卡片要求;要控制好塔内上升气 速和塔底再沸回流、中段回流的温升程度,达成良好的热平衡和馏分切割,以减少烷基化油中 HF、正丁烷的含量。
6
二、烷基化工艺主要操控点
5.酸烃比
为了酸烃充分接触,在烃类完全雾化(雾化喷嘴)的情况下,还要维持酸的连续相,酸烃比一 般控制在 5.2∶1,否则烷基化油质量下降,副产物增多。
国内很多烷基化装置使用最初的原料是混合 C4,将其中的丁二烯加氢变为 1-丁烯和少量 的正丁烷,同时不影响单烯烃的收率,原料中 1-丁烯发生异构化反应生成顺反 2-丁烯,这对氢 氟酸烷基化是非常有利的,利用二甲醚与混合 C4组分的相对挥发度的差异,用蒸馏的方法脱除 混合 C4中的二甲醚,同时可将加氢反应剩余的氢气脱除。C4加氢操作的重点是要控制好反应 深度以及丁烷的产量,由此才能稳定好烷基化过程的烷烯比和酸烃比。
5
二、烷基化工艺主要操控点
3.烷烯比
烷烯比高则烯烃本身碰撞机会减少,烯烃与烷基化反应中间产物碰撞的机会减少,发生聚 合、叠合及过程产物自身烷基化反应的机会减少,有利于烷基化反应。但烷烯比过高则能耗 多,一般控制在(12.5~15)∶1。
4.HF 酸
HF 酸含水量低,则 HF 电离度低,酸性低,不利于生成正离子,但含水超过 2%,则加快设备的 腐蚀,一般折中控制酸中水含量在 1.5%~2%。HF 浓度一般控制在 86%~95%,浓度过高会使烷基 化产物质量下降,HF 浓度过低对设备腐蚀严重,显著增加烯烃叠合反应比例,造成烷基化油终 馏点升高和辛烷值的下降。
烷基化装置工艺流程

烷基化装置工艺流程概述王硕付强王娜(福斯特惠勒(河北)工程设计有限公司,天津300130)摘要:本文概括介绍了烷基化装置的工艺流程和特点。
烷基化装置是以液化气中的烯烃及异丁烷为原料,在催化剂的作用下烯烃与异丁烷反应,生成烷基化油的气体加工装置。
关键词:烷基化;流程1工艺技术路线及工艺特点烷基化装置是以液化气中的烯烃及异丁烷为原料,在催化剂的作用下烯烃与异丁烷反应,生成烷基化油的气体加工装置。
烷基化装置包括原料脱丙烷和烷基化两部分。
原料脱丙烷的目的是通过蒸馏脱除原料中的丙烷。
以液体酸为催化剂的烷基化工艺可分为硫酸烷基化和氢氟酸烷基化,两种工艺都为成熟的技术,在国内外都有广泛应用。
本设计采用的流出物致冷的硫酸烷基化工艺,该技术具有如下特点:1.1采用反应流出物致冷工艺:利用反应流出物中的液相丙烷和丁烷在反应器冷却管束中减压闪蒸,吸收烷基化反应放出的热量。
反应流出物经过气液分离后,气相重新经压缩机压缩、冷凝,抽出部分丙烷后,再循环回反应器。
与闭路冷冻剂循环致冷或自冷式工艺相比,流出物致冷工艺可使得反应器内保持高的异丁烷浓度,而从脱异丁烷塔来的循环异丁烷量最低。
1.2反应部分循环异丁烷与烯烃预混合后进入反应器,酸烃经叶轮搅拌,在管束间循环,机械搅拌使酸烃形成具有很大界面的乳化液,烃在酸中分布均匀,减小温度梯度,减少副反应发生。
1.3反应流出物采用浓酸洗、碱水洗工艺:反应流出物中所带的酯类如不加以脱除,将在下游异丁烷塔的高温条件下分解放出SO2,遇到水份,则会造成塔顶系统的严重腐蚀。
因此,必须予以脱除,本装置采用浓酸洗及碱洗的方法进行脱除,与传统的碱洗相比,能有效脱除硫酸酯,即用98%的硫酸洗后再用12%的NaOH脱除微量酸。
2工艺流程简述烷基化装置由脱丙烷部分、反应压缩部分、流出物处理及分馏部分组成。
2.1脱丙烷部分原料进入装置原料缓冲罐,由脱丙烷塔进料泵抽出并升压后进入脱丙烷塔。
脱丙烷塔的任务是脱去碳四馏分中的碳三以下的轻组分。
烷基化装置工艺流程概述
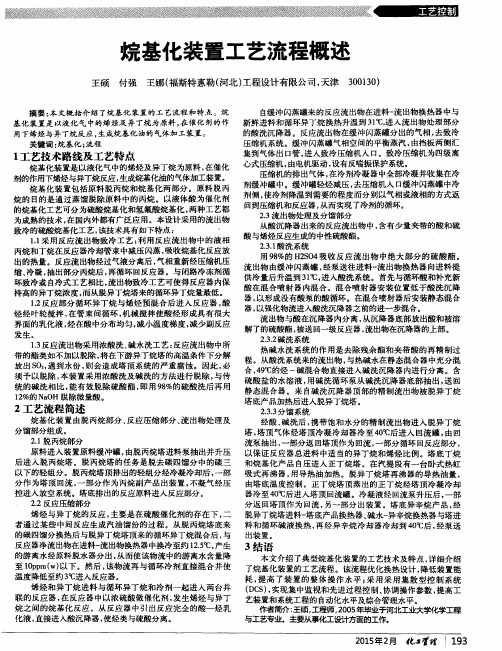
烷基化装置工艺流程概述
王硕 付强 王娜( 福斯特惠勒 ( 河北) 工程设计有限公司, 天津 3 0 0 1 3 0 )
摘要: 本 文概 括介 绍 了烷 基化装 置的 工艺流程 和特 点。烷 自 缓 冲 闪蒸罐来 的反应 流 出物 在进料一 流 出物 换热 器中与 1 ℃, 进 入 流出物 处理 部分 基化 装置是 以液化 气 中的烯烃及 异 丁烷 为原料 , 在 催化 剂的作 新鲜 进料 和循 环异 丁烷换 热升 温到 3 的酸 洗沉 降器 。反 应流 出物在缓 冲 闪蒸 罐分 出的气相 , 去 致冷 用下烯烃与异 丁烷 反应 , 生成烷基化 油的 气体加 工装置 。 压缩 机系统 。缓 冲闪蒸 罐气相 空间的平 衡蒸 汽 , 由挡板 两侧汇 关键词 : 烷基化 ; 流程 集 到气体 出 口管 , 进 入致冷 压缩机 入 口。致冷压缩 机为 四级离 1 工艺技术路线及工艺特点 心式 压缩机 , 由电机 驱动 , 设 有反喘振 保护系统 。 烷基 化装 置是 以液化 气 中的烯烃 及异丁烷 为原 料 , 在催化 压缩机 的排 出气体 , 在冷剂冷 凝器 中全部 冷凝并 收集在 冷 剂的作用 下烯烃 与异丁烷反应 , 生成烷基化 油的气体加 工装 置。 剂 缓冲罐 中 。缓 冲罐轻 烃减压 , 去 压缩机 入 口 缓 冲 闪蒸罐 中冷 烷 基化 装置 包括 原料 脱 丙烷 和烷 基化两 部 分 。原料 脱 丙 剂侧 , 使冷 剂降温 到需要 的程 度而分 别以气相 或液相 的方式 返 烷 的 目的是通 过蒸 馏 脱除原 料 中的 丙烷 。以 液体 酸为 催化 剂 回到压缩机和 反应器 , 从而实 现 了冷剂 的循 环 。 的烷基化 工艺 可分为 硫酸烷 基化和 氢氟酸烷 基化 , 两 种工艺都 2 . 3流 出物处 理及分馏部 分 为成 熟的技 术 , 在 国内外都有广 泛应 用。本设 计采用 的流 出物 从酸 沉 降器 出来 的反应 流 出物 中, 含有 少量夹 带的酸 和硫 致冷的硫 酸烷基化 工艺 , 该技术具有如 下特点 : ’ 酸与烯烃 反应生成 的中性硫酸酯 。 1 . 1 采用 反应 流 出物致 冷 工艺 : 利 用反 应流 出物 中的液 相 2 _ 3 . 1 酸洗 系统 丙烷 和丁烷 在反应 器冷却 管束 中减压 闪蒸 , 吸收烷 基化反 应放 用9 8 %的 H 2 S 0 4 吸收反应流出物中绝大部分的硫酸酯。 出的 热量 。反应流 出物经 过气液 分离后 , 气相重新 经压缩 机压 流 出物 由缓 冲闪 蒸罐 , 经泵送 往进 料一 流 出物 换 热 器向进 料提 缩、 冷凝, 抽 出部 分丙烷 后 , 再循环 回反应 器 。与 闭路冷 冻剂循 供冷 量后升 温到 3 1 ℃, 进入酸 洗 系统 。首先 与循 环酸和补 充新 环致 冷或 自冷式 工艺相 比 , 流出物致 冷工 艺可使 得反应 器内保 酸在 混 合喷 射器 内混 合 。混 合喷射 器安 装位 置低 于 酸洗 沉 降 持高 的异丁烷浓 度 , 而 从脱异丁烷 塔来的循环 异丁烷量最低 。 器, 以形成没有酸泵的酸循环。在混合喷射器后安装静态混合 1 . 2 反应 部 分循 环 异丁烷 与 烯烃 预混 合 后进 入 反应 器 , 酸 器, 以 强化物流进入 酸洗沉降 器之前的进一 步混合 。 烃 经 叶轮搅 拌 , 在 管束 间循 环 , 机 械搅拌 使 酸烃 形成 具有 很大 流 出物 与酸在 沉降 器内分 离 , 从 沉 降器底部 放出酸 和被溶 界 面的乳 化液 , 烃 在酸 中分 布均 匀 , 减 小温 度梯度 , 减 少副反应 解了的硫酸酯 , 被送 回一级反 应器 , 流出物在沉 降器的上部 。 发生 。 2 . 3 . 2 碱 洗系统 1 - 3 反应 流 出物 采用 浓酸洗 、 碱 水洗 工艺 : 反应 流 出物 中所 热碱 水 洗系 统的 作用 是去 除 残余 酯和 夹带 酸 的再精 制过 带的酯 类如 不加 以 脱除 , 将在下 游异丁 烷塔 的高温条 件下分 解 程 。从 酸洗 系统来的 流 出物 , 与热碱水 在静态 混合 器中充分 混 放出s ( ) 2 , 遇 到水份 , 则会 造成 塔顶 系统 的严 重腐蚀 。因此 , 必 合, 4 9  ̄ C 的烃 一碱混 合物 直接 进入碱 洗沉 降器 内进行分 离 。含 须予 以脱 除 , 本 装 置采用 浓酸 洗及 碱洗 的方 法进 行 脱除 , 与 传 硫酸盐的水溶液 , 用碱洗循环泵从碱洗沉降器底部抽出, 送回 统 的碱 洗相 比 , 能 有效 脱除 硫酸 酯 , 即用 9 8 %的硫 酸洗 后再 用 静态 混 合器 。来 自碱洗 沉 降器 顶部 的精 制流 出物 被脱 异丁 烷 1 2 %的 N a O H脱除 微量酸 。 塔底产 品加 热后进入 脱异丁烷塔 。 2 工艺流程简述 2 - 3 - 3 分馏 系统 烷 基化 装 置 由脱丙烷 部 分 、 反 应压 缩部分 、 流 出物 处理 及 经酸、 碱 洗后 , 携 带 饱和 水分 的精 制流 出物 进 入脱 异丁 烷 分馏部分 组成 。 塔, 塔顶气体经塔顶冷凝冷却器冷至4 0  ̄ C 后进入 回流罐 , 由回 2 . 1 脱 丙烷 部分 流泵 抽 出, 一部 分返 回塔顶作为 回流 , 一部 分循 环 回反应 部分 , 原料 进入 装 置原 料缓 冲罐 , 由脱 丙烷塔 进料泵 抽 出并 升压 以保 证 反应 器总 进料 中适 当的 异丁烷 和 烯烃 比例 。塔 底丁 烷 后 进入 脱丙 烷塔 。脱 丙烷 塔 的任务 是 脱去碳 四馏 分 中的 碳三 和烷 基化 产 品 自压进 入正 丁烷 塔 。在汽 提 段有一 台 卧式 热虹 以 下的轻组 分 。脱丙烷塔 顶排 出的轻组分 经冷 凝冷却后 , 一部 吸式 再 沸器 , 用 导热 油加 热 。脱异 丁烷 塔再 沸 器的导 热 油量 , 分 作为 塔顶 回流 , 一部 分作 为丙烷 副 产品 出装 置 , 不凝 气 经压 由塔 底温 度 控制 。正 丁烷 塔顶 蒸 出的正 丁烷 经塔 顶冷 凝 冷却 控进 入放空 系统 。塔底排 出的反应原料 进入反应部分 。 器冷 至 4 0 q C 后进入塔 顶 回流罐 。冷凝液 经 回流 泵升压 后 , 一部 2 . 2 反 应压缩部分 分返 回塔 顶 作为 回流 , 另一 部分 出装 置 。塔 底 异辛烷 产 品 , 经 烯烃 与异 丁烷 的反 应 , 主 要是 在硫 酸催 化剂 的 存在 下 , 二 脱异 丁烷塔进 料一 塔 底产 品换 热器 、 碱水 一 异辛烷 换热 器与塔进 者通 过 某些 中间反应 生成 汽 油馏份 的过 程 。从脱 丙烷 塔 底来 料和 循 环碱 液换 热 , 再 经异 辛烷 冷 却器 冷却到 4 0 ℃后 , 经 泵送 的碳 四馏分 换热后 与脱异 丁烷塔 顶来 的循 环异 丁烷混 合后 , 与 出装 置。 反应 器净流 出物 在进料一 流出物换热 器中换冷 至约 1 2 . 5  ̄ C , 产生 3结语 的游 离水 经原料 脱水器分 出 , 从而使 该物流 中的游 离水含 量降 本文介 绍了典 型烷基 化装 置的工艺 技术及 特点 , 详细 介绍 至1 0 p p m( w) 以下 。然 后 , 该 物流 再 与循 环冷 剂直 接混 合 并使 了烷 基化 装置的 工艺流程 。该 流程优 化换热设 计 , 降低 装置能 温度 降低至 约 3 ℃进 入反应器 。 耗, 提 高 了装 置 的 整 体操 作水 平 ; 采 用 采 用 集 散 型控 制 系统 烯烃 和异 丁烷 进料 与循 环 异丁 烷和 冷剂 一起 进 入两 台并 ( D C S ) , 实现 集 中监 视和 先进 过程控 制 、 协调 操作 参数 , 提 高 工 联 的反 应 器 , 在 反应 器中 以浓硫 酸做 催化 剂 , 发 生烯 烃与 异丁 艺装 置和 系统 工程的 自 动化 水平及综合 管理水平 。 烷 之 间的烷 基化 反应 。从 反应 器 中 引出反应 完 全的 酸一 烃乳 作者 简介 : 王硕 , 工程 师 , 2 0 0 5 年 毕业于 河 北工 业大 学化 学工 程 化液, 直接 进入酸沉 降器 , 使烃类与硫酸 分离 。 与工 艺 专业 。主要 从事 化 工设 计方 面的 工作 。
烷基化流程简述
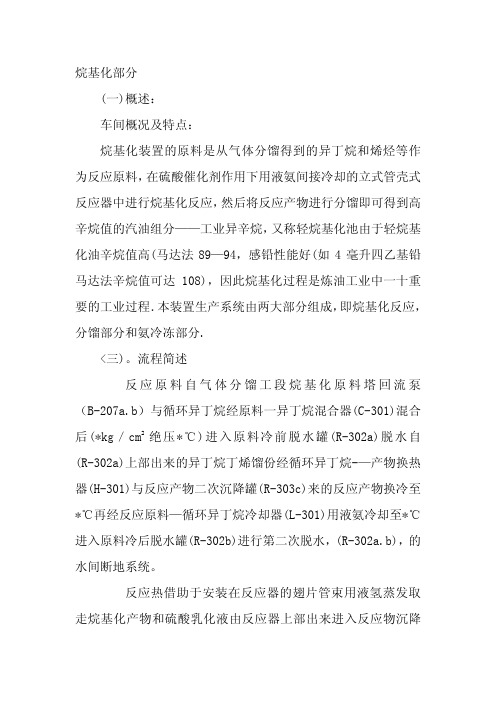
烷基化部分(一)概述:车间概况及特点:烷基化装置的原料是从气体分馏得到的异丁烷和烯烃等作为反应原料,在硫酸催化剂作用下用液氨间接冷却的立式管壳式反应器中进行烷基化反应,然后将反应产物进行分馏即可得到高辛烷值的汽油组分——工业异辛烷,又称轻烷基化池由于轻烷基化油辛烷值高(马达法89—94,感铅性能好(如4毫升四乙基铅马达法辛烷值可达108),因此烷基化过程是炼油工业中一十重要的工业过程.本装置生产系统由两大部分组成,即烷基化反应,分馏部分和氨冷冻部分.<三)。
流程简述反应原料自气体分馏工段烷基化原料塔回流泵(B-207a.b)与循环异丁烷经原料一异丁烷混合器(C-301)混合后(*kg/cm2绝压*℃)进入原料冷前脱水罐(R-302a)脱水自(R-302a)上部出来的异丁烷丁烯馏份经循环异丁烷-—产物换热器(H-301)与反应产物二次沉降罐(R-303c)来的反应产物换冷至*℃再经反应原料—循环异丁烷冷却器(L-301)用液氨冷却至*℃进入原料冷后脱水罐(R-302b)进行第二次脱水,(R-302a.b),的水间断地系统。
反应热借助于安装在反应器的翅片管束用液氢蒸发取走烷基化产物和硫酸乳化液由反应器上部出来进入反应物沉降罐(R-303a.b)沉降分离,分离出来的硫酸循环使用.反应产物由(R-303a.b)部出来进入反应物二次沉降罐(R-303c) 进行二次沉降分离,(R-303c)上部出来的反应产物经(H—301),与循环异丁烷换热后,经产物碱洗混合器.(C302)与碱液混合进入反应产物碱洗罐(R-305),自(R-305)顶出来经产物水洗混合器(C-303)与*~*℃温水混合后进入反应产物水洗罐(R-306)水洗后反应产物进入(T-301)进科缓冲罐(R-307)当*%的硫酸降至*%以下时,不再使用,由(R-302a.b)压入废酸沉降罐(R-304)沉降分离出来的废硫酸经循环硫酸泵送入废酸贮罐(R-324),用汽车槽车送往奎屯硫酸厂处理。
烷基化装置资料
式流出物致冷反应器而进行的以节能、降耗、 扩产为目的的装置改造,使烷基化从原有的 四十年代工艺水平提高到八十年代初期水平。 改造后的硫酸烷基化与轻碳四选择性加氢装 置、MTBE装置组成联合装置,采用DCS控制, 首期生产能力为6.5万吨产品/年,2005年3 月份在原有装置的基础上开始扩能改造生产 能力扩到11.3万吨产品/年。
烷基化油以其辛烷值高(研究法辛烷值
为94-98、马达法辛烷值可达90-95), 调和性能好,有理想的挥发性和清洁的 燃烧性能等突出特征而成为优质汽油调 和组分。
CH3
H2SO4 HC CH3+CH2= C CH3 CH3 CH3
CH3
CH3
CH3 C CH2 CH CH3 CH3
二、原、辅助材料主要性质及各项指标
原料性质
无色、无臭气体,不溶于水,易溶于乙
醇,与空气形成爆炸混合物,易燃易爆。
原料指标
加工方案
项目 丁烷-丁烯 纯度 C3含量 C5含量 iC4o:∑C4= ≮95 ≯2 ≯3 ≥1.5:1 丁烷-丁烯 ≮95 ≯2 ≯3 ≥1.5:1 质检中心 质检中心 质检中心 质检中心
装置的主要特点是:采用STRATCO流出物制冷工
艺,取代了氨冷技术,消灭了氨泄漏造成的环 境污染,节省了制冷剂;利用高位酸沉降罐和 反应器构成的乳液循环,改善了反应条件,抑 制了副反应的发生,提高了产品质量,降低了 硫酸消耗;制冷部分采用外甩冷剂带走系统丙 烷工艺,取消了丙烷塔系统,节省了投资,减 少了能耗,方便了操作;全装置采用先进的DCS 自控系统,优化了操作,降低了操作强度。
异丁烷:沸点-11.2℃,冰点-
159.605℃,d420=0.557,无色有味气 体,微溶于水,易溶于乙醚,与空气形 成爆炸混合物。爆炸极限1.8%-8.5%。 易燃、易爆、低毒、窒息。灭火剂用泡 沫、雾状水、二氧化碳。
烷基化装置
二、原、辅助材料主要性质及各项指标
原料性质
无色、无臭气体,不溶于水,易溶于乙
醇,与空气形成爆炸混合物,易燃易爆。
原料指标
加工方案
项目 丁烷-丁烯 纯度 C3含量 C5含量 iC4o:∑C4= ≮95 ≯2 ≯3 ≥1.5:1 丁烷-丁烯 ≮95 ≯2 ≯3 ≥1.5:1 质检中心 质检中心 质检中心 质检中心
同时还会发生裂化反应、环化反应、聚 合反应、歧化反应、自身烷基化反应, 形成催化剂复合物及酯的副反应,减少 副反应,对烷基化反应过程是极其关键 的
五、流程叙述
经加氢预处理后的MTBE尾气与循环异丁烷混合后进 反应产物与原料换热器(E-1/A、B、C),与反应产 物换冷至13℃,与循环冷剂混合进入反应器(R-1/A、 B),在硫酸催化剂的作用下反应,生成烷基化油。 反应产物与硫酸自反应器(R-1/A、B)流出至酸沉降 罐(D-2/ A,B)沉降分离, 分出的硫酸大部分返回至反 应器循环使用至浓度89%以下,少部分排至废酸储罐 (D-16)。流出物经减压阀减压后至反应器(R-1/A、 B)管程取走反应热后,在吸入闪蒸罐(D-3)中反应侧 分出气液两相。液相由反应产物泵(P-2/A、B)送至精 制系统。
六、主要操作条件
1、反应系统操作条件
加工方案
项目 反应温度
航空异辛烷
车用异辛烷
4-12
℃
MPa
4-12
反应器压力
外分子(v/v)
0.35-0.5
≥8:1
0.35-0.5
≥8:1
硫酸浓度
D-5压力
%(m/m)
MPa
98-89
>0
98-89
>0
2、分馏系统操作条件
加工方案 航空异辛烷 0.55-0.65 43-58 60-100 38-55 0.35-0.45 90-145 ≮80 ≮95 车用异辛烷 0.55-0.65 43-58 60-100 35-55 0.35-0.45 75-130
烷基化装置操作规程(修改版)讲义
第一章工艺技术规程1.1 装置概况1.1.1 装置简介硫酸烷基化是以催化裂化的液态烃经气体精馏分离出来的C4组分中的异丁烷和丁烯为原料,以89%-98%的硫酸为催化剂,在低温下液相反应生成高辛烷值汽油组分—烷基化油的加工工艺过程。
装置全流程分为反应、制冷、流出物精制和分馏四个部分,其中反应部分主要是在催化剂的作用下,异丁烷和丁烯反应生成烷基化油,制冷部分是在压缩机的作用下,利用反应产物中大量的异丁烷减压汽化吸收热量,维持反应在低温液相下进行,同时为反应系统提供足够的循环冷剂,保证低温进料和反应器的分子比;流出物精制是将反应生成的烷基化油经过酸洗和碱洗,除去烷基化油中的酸性酯类物质,分馏部分主要是将经过精制系统的烷基化油经过脱异丁烷塔、脱正丁烷塔和再蒸馏塔分离出异丁烷、正丁烷和最终产物异辛烷的过程。
装置共有设备95台,其中主要设备包括:STRATCO公司的卧式流出物致冷反应器、制冷压缩机装置的主要特点:采用STRATCO流出物制冷工艺,取代了氨冷技术,消灭了氨泄漏造成的环境污染,节省了制冷剂;利用高位酸沉降罐和反应器构成的乳液循环,改善了反应条件,抑制了副反应的发生,提高了产品质量,降低了硫酸消耗;制冷部分采用外甩冷剂带走系统丙烷工艺,取消了丙烷塔系统,节省了投资,减少了能耗,方便了操作;全装置采用先进的DCS自控系统,优化了操作,降低了操作强度。
历年大修的改造情况:本烷基化装置始建于1965年,1966年元月正式投产。
为我国第一套烷基化装置,采用立式氨冷反应器进行生产,设计能力为1.5万吨产品/年。
随着石油工业的发展,1984年在原有装置的基础上进行扩建改造。
使生产能力提高到4.3万吨产品/年。
1996年由于引进美国STRATCO公司的卧式流出物致冷反应器而进行的以节能、降耗、扩产为目的的装置改造使烷基化从原有的四十年代工艺水平提高到八十年代初期水平。
改造后的硫酸烷基化与MTBE组成联合装置,采用DCS控制,首期生产能力为6.5万吨产品/年,并预留12万吨产品/年的加工能力,以适应远期的炼厂发展规划。
烷基化反应器
烷基化反应器
x
烷基化反应器
概述
烷基化反应器是一种利用反应化学方法,来进行有机分子上烷基化反应的设备,它主要用于有机合成,以改变有机物质的性质。
烷基化反应器的工作原理是饱和烃(例如烷烃)在催化剂的作用下,经过脱氢、烷基化反应的组合,从而产生一系列有机化合物,从而改变有机物质的性质。
结构
烷基化反应器通常由以下几个部分组成:反应室、反应炉、催化剂、冷却器、过滤器和控制系统等。
1.反应室:反应室由不锈钢制成,一般容积在50—500L之间,内部安装有旋转搅拌器,可以有效地将反应物混合和搅拌,以确保反应的顺利进行。
2.反应炉:反应炉可以选择不锈钢、铜及铝合金等材料制成,其功能是将反应物加热至反应温度,以促进反应的进行。
3.催化剂:催化剂一般选择金属铱或催化剂聚合物,可以用于加速反应的进行,提高反应效率。
4.冷却器:冷却器用于在反应过程中降低反应温度,以防止反应过热而发生爆炸事故。
5.过滤器:过滤器用于将反应产物和残余的反应物分别收集。
6.控制系统:控制系统用于检测反应温度,压力和流量等参数,以确保反应的质量和可控性。
应用
烷基化反应器广泛应用于化肥、染料、农药、医药、精细化工、新材料、环保等行业,是有机合成中不可缺少的重要设备。
- 1、下载文档前请自行甄别文档内容的完整性,平台不提供额外的编辑、内容补充、找答案等附加服务。
- 2、"仅部分预览"的文档,不可在线预览部分如存在完整性等问题,可反馈申请退款(可完整预览的文档不适用该条件!)。
- 3、如文档侵犯您的权益,请联系客服反馈,我们会尽快为您处理(人工客服工作时间:9:00-18:30)。
烷基化装置概况特点及工艺原理1.装置概况装置原料:本装置原料为上游MTBE 装置提供的未反应碳四馏分、加氢裂化液化气,所需的少量氢气由制氢装置提供。
装置建设规模:根据MTBE 装置所提供的液化气量及液化气中的烯烃含量,实际可生产烷基化油约13.13 万吨/年,本装置设计规模为16 万吨/年烷基化油。
装置建设性质:在硫酸催化剂的作用下,液化气中的异丁烷与烯烃反应生成高辛烷值汽油调合组分-烷基化油。
装置设计原则:1)选用成熟可靠的工艺技术和控制方案,使设计的装置达到安、稳、长、满、优操作。
2)优化工艺流程并推广应用新工艺、新技术、新设备、新材料,降低生产成本,同时降低装置能耗,提高产品质量档次。
3)在保证技术先进、装置生产安全可靠的前提下,利用联合装置的优势,降低能耗并尽量降低工程造价,节省投资。
4)为了降低工程投资,按照“实事求是、稳妥可靠”的原则,提高国产化程度,所需设备立足国内解决,只引进在技术、质量等方面国内难以解决的关键仪器仪表。
5)采用DCS 集中控制,优化操作,以提高装置的运转可靠性,提高产品收率和质量。
6)严格执行国家、地方及主管部门制定的环保和职业安全卫生设计规定、规程和标准,减少“三废”排放,维护周边生态环境,实行同步治理,满足清洁生产的要求。
装置组成:本装置由原料精制、反应、制冷,流出物精制和产品分馏、化学处理等几部分组成。
装置运行时数和操作班次:装置年开工时间按8400 小时计,操作班次按四班三倒。
2.装置特点:烷基化装置是以液化气中的烯烃及异丁烷为原料,在催化剂的作用下烯烃与异丁烷反应,生成烷基化油的气体加工装置。
本装置包括原料加氢精制和烷基化两部分。
原料加氢精制的目的是通过加氢脱除原料中的丁二烯。
因为丁二烯是烷基化反应中主要的有害杂质,在烷基化反应过程中,丁二烯会生成多支链的聚合物,使烷基化油干点升高,酸耗加大。
脱除原料中的丁二烯采用选择性加氢技术,该技术已在国内多套烷基化装置上应用,为国内成熟技术。
由于MTBE 装置所提供的未反应碳四馏分中烷烯比不足,需补充部分异丁烷,因此引入部分加氢裂化液化气,与加氢后的碳四馏分混合进入分馏塔,分离出满足烷烯比要求的碳四馏分。
以液体酸为催化剂的烷基化工艺可分为硫酸烷基化和氢氟酸烷基化,两种工艺都为成熟的技术,在国内外都有广泛应用。
本设计采用的是DUPONT 公司的硫酸烷基化工艺,该技术具有如下特点:1)采用反应流出物致冷工艺:利用反应流出物中的液相丙烷和丁烷在反应器冷却管束中减压闪蒸,吸收烷基化反应放出的热量。
反应流出物经过气液分离后,气相重新经压缩机压缩、冷凝,抽出部分丙烷后,再循环回反应器。
与闭路冷冻剂循环致冷或自冷式工艺相比,流出物致冷工艺可使得反应器内保持高的异丁烷浓度,而从脱异丁烷塔来的循环异丁烷量最低。
此外,在这种致冷流程中采用了节能罐,使部分富丙烷物流在中间压力下闪蒸汽化进入压缩机第二段,从而节约能量。
2)STRATCO 公司反应部分循环异丁烷与烯烃预混合后进入反应器,酸烃经叶轮搅拌,在管束间循环,机械搅拌使酸烃形成具有很大界面的乳化液,烃在酸中分布均匀,减小温度梯度,减少副反应发生。
3)反应流出物采用浓酸洗、碱水洗工艺:反应流出物中所带的酯类如不加以脱除,将在下游异丁烷塔的高温条件下分解放出SO2,遇到水份,则会造成塔顶系统的严重腐蚀。
因此,必须予以脱除,本装置采用浓酸洗及碱洗的方法进行脱除,与传统的碱洗相比,能有效脱除硫酸酯,即用99.2%的硫酸洗后再用12%的NaOH 脱除微量酸。
3.选择性加氢工艺原理3.1 加氢工艺目的随着FCC原料的重质化以及FCC反应温度的提高,FCC碳四中丁二烯含量不断增高,有不少FCC装置产生的碳四中丁二烯浓度超过0.5%(m/m)。
如果FCC碳四用做烷基化原料,其中的丁二烯是耗酸的主要杂质,并且影响烷基化油的收率和质量,因此很有必要将其脱除。
加氢的方法可有效地脱除丁二烯,但该加氢工艺过程必须是高选择性的,因为单烯烃是烷基化的有用组分,在加氢过程中不能将其加氢,同时应尽量使丁烯-1异构为顺、反丁烯-2,因为顺、反丁烯-2是烷基化最理想的组分,它与异丁烷生成的烷基化油辛烷值高。
因此必须采用极具选择性的并且有较高异构化性能的催化剂和非常合适的工艺条件,以使混合碳四经过加氢脱丁二烯工艺处理后达到如下目的:1)丁二烯残留量低。
2)正构丁烯加氢成为丁烷的量最少。
3)丁烯-1异构成为丁烯-2的量最多。
4)异丁烯加氢成为异丁烷的量非常有限。
3.2 加氢化学反应1)热力学与动力学对于任一化学反应,热力学决定发生的可能性和各产物与反应物的数量。
实际上,有些反应100%完成,即各反应物都转化为产品,另一些则处于平衡状态,即只有部分反应物被转化,平衡时各种产品与反应物的量取决于操作条件并由热力学确定。
但热力学并不能说明达到平衡或完成反应所需的时间。
动力学确定化学反应的速率,反应速率取决于操作条件但也能通过适当选用催化剂而得到大幅度的变化,一个反应通常可被某一特定催化剂所强化。
换言之,热力学在假定时间为无限大时,可确定最终平衡组分。
动力学则能预测一限定时间后的组成,因为时间总是有限的,各种反应同时发生时,动力学一般占主导地位。
2)化学反应选择性加氢工艺所含化学反应有二种类型:·希望的反应,即与工艺目的相一致的反应:丁二烯加氢反应。
·不希望的反应:指造成原料中有价值的组分损失的反应,如丁烯、异丁烯加氢成丁烷、异丁烷。
①希望的反应希望的反应为丁二烯加氢反应,反应式如下:CH2=CH-CH=CH2+ H2CH3CH2CH=CH2丁二烯加氢反应涉及相当复杂的机理,连串反应和平行反应都会发生。
在中等温度20~100℃,1,3-丁二烯加氢生成丁烯-1,丁烯-1与丁烯-2也会进一步加氢生成丁烷,但反应速率低得多,只有当丁二烯几乎已完全被加氢之后,丁烯-1与丁烯-2的进一步加氢才明显表现出来。
②不希望的反应不希望的反应包括正构烯烃加氢变成正构烷烃、异构烯烃加氢变成异构烷烃的反应, 这些副反应的速度都远低于丁二烯加氢反应的速度,只有当丁二烯加氢接近完全时,才开始产生副反应。
反应式如下:CH2=CH(CH3)-CH3+ H2CH3-CH2(CH3)-CH3CH2=CH-CH2-CH3+ H2CH3CH2CH2CH33.3 加氢催化剂催化剂通常由一种载体(碱土氧化物、氧化铝、氧化硅、氧化镁……)及其上所沉积分散极细的一种或多种金属所构成。
此金属总是对催化剂起决定作用,载体(与其化学性质有关)也经常具有催化作用。
催化剂并不消耗,但可被原料中的杂质或化学反应产生的某些产品(如催化剂上形成的聚合物或焦炭沉积物)所失活。
1)催化剂活性、选择性、稳定性催化剂除其物理性质外的主要特性是:·活性活性是催化剂加快反应速率的能力。
对于其它操作条件相同的既定进料,活性由催化剂的操作温度来衡量,催化剂必须在可产生合格产品的温度下操作。
·选择性选择性表示催化剂对所要求的反应(而不是其它反应)的能力。
·稳定性稳定性的特征是操作条件与原料稳定时催化剂的性能(活性、选择性)随时间的变化。
主要是原料中的杂质和聚合物或焦炭的沉积影响稳定性。
2)催化剂特性与机理加氢反应所选用的HSE-401催化剂属Pd/AI2O3型。
该催化剂由分散于氧化铝载体上的钯所构成,并且以氧化态交货,不具备活性,使用前必须用氢气还原。
催化剂的载体机械强度好,呈弱酸性,能抑制聚合反应、能经受住蒸汽、氢气和空气温度高于400℃的处理(催化剂再生需要这种处理)。
催化剂的主活性组分为贵金属钯, 钯对二烯烃类加氢的高选择性来自与其它烯烃相比,对二烯烃和炔烃有高得多的吸附能力。
同时钯也有异构化的活性,但比二烯烃类加氢的速度低。
3)催化剂污染物催化剂的污染物分为三类:抑制剂或活性调节剂、暂时毒物、永久毒物。
①抑制剂或活性调节剂抑制剂是一种在催化剂活性表面上与反应物竞争,使可利用的活性面积减少的化合物。
它们强有力地吸附于催化剂金属之上,但这种吸附是完全可逆的,当进料中不再含有所述污染物时,毋需特别处理活性就恢复。
CO就是一种典型的活性调节剂。
②暂时毒物暂时毒物是吸附力强到能在活性表面上积累的污染物,只能采用就地或异地使用特有方法清除毒物恢复活性。
游离水即为典型的暂时毒物,用热氢气汽提即可有效地恢复活性。
③永久毒物永久毒物是采用蒸汽—空气烧焦和热氢汽提等方法所不能去掉的。
铅和氯就是典型的永久性毒物,催化剂必须卸出另换新剂。
毒物清单及其作用、来源与去除方法见表1-1。
本表并未列全,只是按所知道的类型列举了最经常遇到的杂质,原料中可能存在的其它杂质仍可能对催化剂性能有不利的影响。
3.4 影响加氢因素分析影响加氢因素的重要工艺参数有四个:H 2与丁二烯摩尔比、液相体积空速、反应温度、反应压力。
1)H 2与丁二烯摩尔比如前所述,丁二烯加氢的选择性与丁烯-1不同,主要在于活性金属表面对丁二烯有更强的吸附作用。
因此,一旦丁二烯完全加氢后,丁烯-1就会争夺活性表面则迅速加氢。
这意味着H 2/丁二烯比对本工艺性能而言很关键,过高的H 2/丁二烯比会导致丁烯因被加氢为丁烷而减少(即选择性差),过低的H 2/丁二烯比会造成残余丁二烯量高于期望值。
附:H 2与C 4进料中丁二烯的摩尔比的计算方法通过调节氢气的流量就可以确定H 2与C 4进料中丁二烯的摩尔比,氢气流量的计算方法如下:公式(1)中:V —氢气的流量,Nm 3/h 。
(氢气质量流量计可显示标准体积流量)W —碳四的流量,Kg/h 。
m —碳四中丁二烯的质量分率。
R —所需要的H 2与C 4进料中丁二烯的摩尔比。
公式(1)计算出的氢气流量为纯的氢气流量,当氢气为混合物时需确定出其中组分的种类及各自的含量,然后经过专门的公式(氢气质量流量计使用说明书中提供)计算后,直接由质量流量计给定即可。
很显然当碳四流量和组成变化时,也需要重新调整氢气的流量。
例:碳四的流量W 为14788Kg/h ,其中丁二烯含量为0.4%(m/m ),即质量分率为0.004,氢气为纯氢,所需要的H 2与C 4进料中丁二烯的摩尔比R 为3,则需要的氢气流量计算如下:W =14788Kg/h m=0.004 R =3将上述数值代入公式(1)得:则氢气的流量为73.61 Nm 3/h2)液相体积空速(LHSV ))1(544.22R m W V ⋅⋅⨯=h Nm R m W V /61.73354004.0147884.22544.223=⨯⨯⨯=⋅⋅⨯=LHSV定义为液体体积流量与催化剂体积之比,二者体积必须用同一种单位表示。
在其它条件不变的情况下,空速增大物料在催化剂床层中的停留时间减少,反应效果会变差;反之,反应效果会变好。