烷基化生产技术
烷基化工艺流程

烷基化工艺流程
《烷基化工艺流程》
烷基化是一种重要的化学反应,用于将烷烃类化合物转化为烷基化合物。
这种反应通常在烷基化催化剂的作用下进行,产生不同长度的烷基链。
烷基化工艺在化工行业中有着广泛的应用,用于生产各种烷基化合物,例如燃料添加剂、润滑油和界面活性剂等。
烷基化工艺流程包括几个主要步骤:反应物准备、催化剂选择、反应条件调节和产物提纯等。
首先,反应物通常是烷烃或烯烃类化合物,需要在一定温度和压力下准备好。
其次,选择合适的催化剂对于烷基化反应至关重要。
催化剂可以是酸性或碱性的固体催化剂,也可以是贵金属催化剂。
不同的催化剂会影响反应速率和产物选择性。
在选定催化剂后,需要调节反应条件,例如温度、压力和反应时间,以使反应达到最佳效果。
最后,产物需要经过提取、蒸馏和结晶等步骤进行纯化,得到高纯度的烷基化合物。
烷基化工艺流程在化工生产中有着重要的作用,可以用于制备各种化学品和材料。
同时,该工艺流程也需要注意安全环保,避免产生废物和有害物质。
随着化工技术的不断进步,烷基化工艺流程也在不断优化和改进,以满足市场需求,并减少对环境的影响。
烷基化技术在石油化工行业中的应用

烷基化技术在石油化工行业中的应用石油化工行业是当今世界最重要的经济支柱之一,它涉及到了能源、化工、机械、环保等多个领域。
石油及其衍生品对于人类的生活产生了深远的影响,无论是石油的开采还是化工产品的生产,都需要各类技术的支持和应用。
其中,烷基化技术就是石油化工行业中不可或缺的一环。
烷基化技术是一种将碳氢化合物(烷烃)转化为烷基化合物的化学反应过程。
该技术最早被应用于汽油生产,并被广泛用于聚合物、合成橡胶、生产塑料、合成洗涤剂、染料和颜料等领域。
在石油化工的各个领域中,烷基化技术都起着至关重要的作用。
首先,烷基化技术在石油化工中的应用最为广泛的领域就是汽油生产。
烷基化技术可以将低碳烷烃与高碳烷烃进行反应,得到烷基化合物,其主要成分就是汽油。
这种技术可以将石油多种组分进行有效分离,实现对成分的调节和控制。
此外,烷基化合物的主要特点是具有较高的辛烷值和较好的反爆性能,因此烷基化技术在提高汽油品质方面也发挥着举足轻重的作用。
除汽油生产外,烷基化技术还应用于聚合物的合成。
在聚合物的生产中,烷基化技术可以将低聚合度的烯烃进行聚合,形成高聚物。
由于聚合度的不同会直接影响到聚合物的性质和性能,因此烷基化技术的应用对于聚合物材料的研发至关重要。
聚合物在现代工业中得到了广泛应用,如塑料制品、纤维材料、复合材料等,这些产物的制造离不开烷基化技术的支持。
在生产合成橡胶方面,烷基化技术也是不可或缺的。
在橡胶生产中,烷基化反应可以将不饱和烃进行烷基化,得到线性烷基苯/烷基苯乙烯(LAB)或正戊烷等烷基烃,用于合成橡胶助剂,如橡胶机油、轮胎添加剂等。
这些助剂对于保护橡胶性能和稳定性非常关键,因此烷基化技术在橡胶生产过程中起着重要的作用。
另外,在生产洗涤剂、染料和颜料等产品时,烷基化技术也被广泛应用。
这些产品的生产都需要对原料进行调节和合成,而烷基化技术可以从石油中提取原材料,并转化为需要的化学物质。
例如,染料和颜料的合成需要特定的化学结构,烷基化技术可以将原材料进行分解、重组,形成合成所需要的物质结构,从而实现对产品性能的优化。
甲苯与甲醇侧链烷基化生产苯乙烯技术分析资料
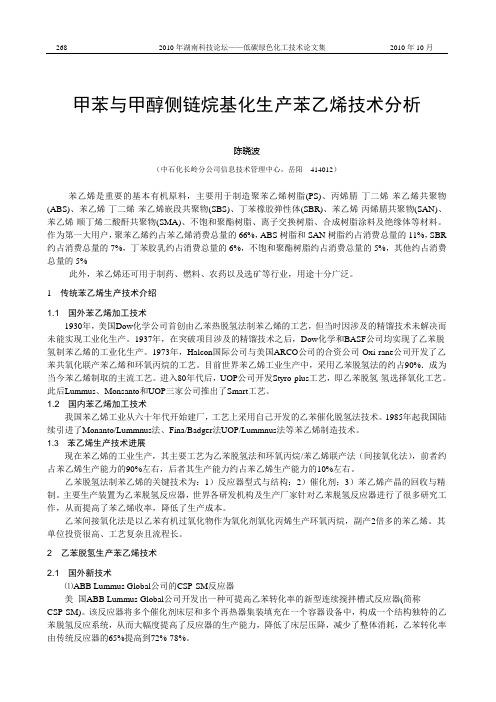
甲苯与甲醇侧链烷基化生产苯乙烯技术分析陈晓波(中石化长岭分公司信息技术管理中心,岳阳414012)苯乙烯是重要的基本有机原料,主要用于制造聚苯乙烯树脂(PS)、丙烯腈-丁二烯-苯乙烯共聚物(ABS)、苯乙烯-丁二烯-苯乙烯嵌段共聚物(SBS)、丁苯橡胶弹性体(SBR)、苯乙烯-丙烯腈共聚物(SAN)、苯乙烯-顺丁烯二酸酐共聚物(SMA)、不饱和聚酯树脂、离子交换树脂、合成树脂涂料及绝缘体等材料。
作为第一大用户,聚苯乙烯约占苯乙烯消费总量的66%,ABS树脂和SAN树脂约占消费总量的11%,SBR 约占消费总量的7%,丁苯胶乳约占消费总量的6%,不饱和聚酯树脂约占消费总量的5%,其他约占消费总量的5%此外,苯乙烯还可用于制药、燃料、农药以及选矿等行业,用途十分广泛。
1 传统苯乙烯生产技术介绍1.1 国外苯乙烯加工技术1930年,美国Dow化学公司首创由乙苯热脱氢法制苯乙烯的工艺,但当时因涉及的精馏技术未解决而未能实现工业化生产。
1937年,在突破项目涉及的精馏技术之后,Dow化学和BASF公司均实现了乙苯脱氢制苯乙烯的工业化生产。
1973年,Halcon国际公司与美国ARCO公司的合资公司-Oxi-rane公司开发了乙苯共氧化联产苯乙烯和环氧丙烷的工艺。
目前世界苯乙烯工业生产中,采用乙苯脱氢法的约占90%.成为当今苯乙烯制取的主流工艺。
进入80年代后,UOP公司开发Styro-plus工艺,即乙苯脱氢-氢选择氧化工艺。
此后Lummus、Monsanto和UOP三家公司推出了Smart工艺。
1.2 国内苯乙烯加工技术我国苯乙烯工业从六十年代开始建厂,工艺上采用自己开发的乙苯催化脱氢法技术。
1985年起我国陆续引进了Monanto/Lummnus法、Fina/Badger法UOP/Lummnus法等苯乙烯制造技术。
1.3 苯乙烯生产技术进展现在苯乙烯的工业生产,其主要工艺为乙苯脱氢法和环氧丙烷/苯乙烯联产法(间接氧化法),前者约占苯乙烯生产能力的90%左右,后者其生产能力约占苯乙烯生产能力的10%左右。
烷基化工艺

烷基化工艺的反应类型包括质子酸烷基 化、路易斯酸烷基化、酶催化烷基化等。
烷基化反应的机理
质子酸烷基化反应机理
• 质子酸作为催化剂,与烷基化剂发 生质子交换,生成活性中间体。 • 活性中间体与有机化合物发生烷基 化反应,生成新的烷基化合物。
路易斯酸烷基化反应机理
• 路易斯酸作为催化剂,与烷基化剂 发生配位反应,生成活性中间体。 • 活性中间体与有机化合物发生烷基 化反应,生成新的烷基化合物。
点。
01
烷基化工艺在 石油化工、制 药、新材料等 领域有广泛的 应用,具有较 高的经济效益。
02
烷基化工艺的缺点
烷基化工艺的催化剂成本较高,且部分催化剂具有毒性。
烷基化工艺的产物分离和提纯过程较复杂,可能导致产物损失。
烷基化工艺的改进措施与发展方向
通过改进催化剂结构和性能,降低催化剂成本和毒性。 通过优化产物分离和提纯工艺,提高产物收率。 开发新型绿色烷基化工艺,提高工艺的环境友好性。
烷基化工艺的发展趋势
烷基化工艺的发展方向包括绿色烷基化 工艺的研究、新型催化剂的研究、智能 化生产技术的应用等。
烷基化工艺的发展将进一步提高工艺的 经济效益和环境友好性。
烷基化工艺在未来工业中的应用前景
01 烷基化工艺在未来工业中的应用前景广泛,包括石油化工、制药、新材料等领域。 02 烷基化工艺在未来工业中的应用将进一步提高产品的性能和价值,促进相关产业的发展。
烷基化工艺的催化剂研究
ห้องสมุดไป่ตู้
01 质子酸催化剂的研究
• 改进质子酸催化剂的结构,提高催化剂的活性和选择性。 • 通过添加助剂,改善催化剂的稳定性,延长使用寿命。
02 路易斯酸催化剂的研究
• 改进路易斯酸催化剂的结构,提高催化剂的活性和选择 性。 • 通过添加助剂,改善催化剂的稳定性,延长使用寿命。
烷基化技术进展状态分析报告
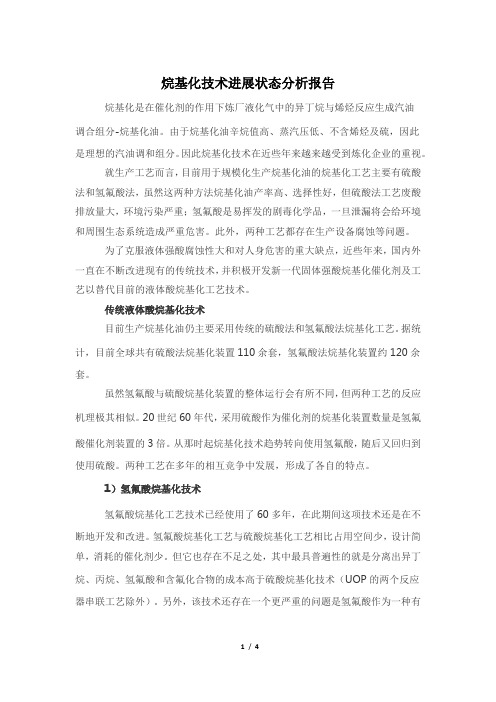
烷基化技术进展状态分析报告烷基化是在催化剂的作用下炼厂液化气中的异丁烷与烯烃反应生成汽油调合组分-烷基化油。
由于烷基化油辛烷值高、蒸汽压低、不含烯烃及硫,因此是理想的汽油调和组分。
因此烷基化技术在近些年来越来越受到炼化企业的重视。
就生产工艺而言,目前用于规模化生产烷基化油的烷基化工艺主要有硫酸法和氢氟酸法,虽然这两种方法烷基化油产率高、选择性好,但硫酸法工艺废酸排放量大,环境污染严重;氢氟酸是易挥发的剧毒化学品,一旦泄漏将会给环境和周围生态系统造成严重危害。
此外,两种工艺都存在生产设备腐蚀等问题。
为了克服液体强酸腐蚀性大和对人身危害的重大缺点,近些年来,国内外一直在不断改进现有的传统技术,并积极开发新一代固体强酸烷基化催化剂及工艺以替代目前的液体酸烷基化工艺技术。
传统液体酸烷基化技术目前生产烷基化油仍主要采用传统的硫酸法和氢氟酸法烷基化工艺。
据统计,目前全球共有硫酸法烷基化装置110余套,氢氟酸法烷基化装置约120余套。
虽然氢氟酸与硫酸烷基化装置的整体运行会有所不同,但两种工艺的反应机理极其相似。
20世纪60年代,采用硫酸作为催化剂的烷基化装置数量是氢氟酸催化剂装置的3倍。
从那时起烷基化技术趋势转向使用氢氟酸,随后又回归到使用硫酸。
两种工艺在多年的相互竞争中发展,形成了各自的特点。
1)氢氟酸烷基化技术氢氟酸烷基化工艺技术已经使用了60多年,在此期间这项技术还是在不断地开发和改进。
氢氟酸烷基化工艺与硫酸烷基化工艺相比占用空间少,设计简单,消耗的催化剂少。
但它也存在不足之处,其中最具普遍性的就是分离出异丁烷、丙烷、氢氟酸和含氟化合物的成本高于硫酸烷基化技术(UOP的两个反应器串联工艺除外)。
另外,该技术还存在一个更严重的问题是氢氟酸作为一种有毒气体扩散到大气中,氢氟酸气体浓度低时能刺激眼睛、皮肤和鼻子;浓度高时会威胁到生命。
氢氟酸烷基化专利商:UOP和PHILLIPS(康菲公司)氢氟酸烷基化最大的问题是氢氟酸催化剂的挥发性、腐蚀性和毒性,受到美国环保部门的禁用,因此近20年新建的烷基化装置已经基本不采用氢氟酸法。
苯与甲醇烷基化生产芳烃技术

Table 2 Physical index of POY135 dtex / 72 F
测ꎬ金黄色葡萄球菌、大肠杆菌抑菌率达 99% 以上ꎬ
参考文献:
纤度 / dtex
134. 8
断裂强度 / (cNdtex - 1 )
1. 95
good performance was obtained by using a spinning box body of 281 °Cꎬa wind pressure of 30 Paꎬand a winding
speed of 2875 m / min.
Key words:PETꎻdynamic mixingꎻspinningꎻantibacterial fibers
苯与甲醇烷基化生产芳烃技术
日前ꎬ中石油乌鲁木齐石化分公司开发的苯与甲醇烷基化生产芳烃技术经专家鉴定达到国际领先水平ꎬ填补了国内由苯
增产二甲苯的技术空白ꎮ
该技术通过苯与甲醇进行烷基化反应生成甲苯、二甲苯ꎬ为对二甲苯原料来源提供新方法ꎬ缓解二甲苯原料短缺矛盾ꎮ
2008 年ꎬ乌石化开始进行苯与甲醇烷基化催化剂及工艺技术的探索性研究ꎬ历时 10 年科技攻关ꎬ经过前期小试和中试研究掌
握了催化剂制备技术ꎬ完成了催化剂的工业放大生产ꎮ 2018 年 10 月ꎬ乌石化公司完成了 3 万 t / a 的工业现场试验装置标定和
50 万 t / a 工艺包编制ꎮ
( 郑宁来供稿)
and so on. The effect of spinning conditions on the indexes of absorption of antibacterial polyester filament was stud ̄
烷基化反应的简介
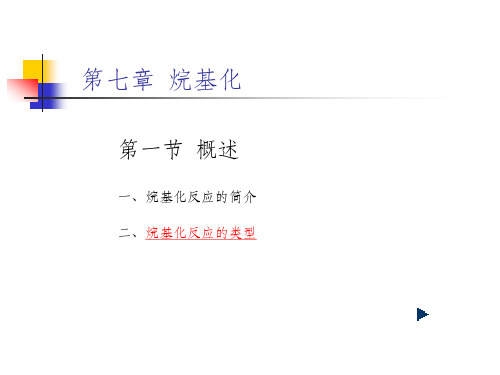
C12H25OH + n CH2 CH2 O
C12H25O(CH2CH2O)n H
n=20~22
将辛基酚与其质量分数为1%的氢氧化钠水溶液混合,真空脱水,氮气 置换,于160~180℃通入环氧乙烷,经中和漂白,得到聚醚产品,其商品 名为OP型乳化剂。
用环氧乙烷o烷基化小结第二节烷基化反应的基本原理三n烷基化反应简介三n烷基化反应1n烷化剂2n烷化反应类型2n烷化反应类型3n烷基化方法3n烷基化方法小结第三节相转移烷基化反应一相转移催化c烷基化二相转移催化o烷基化三相转移催化n烷基化第四节应用实例alcl3法生产异丙苯异丙苯的生产小结吲哚和溴苄在季铵盐的催化下可高收率得到n苄基化产物
第七章 烷基化
第一节 概述
一、烷基化反应的简介 二、烷基化反应的类型
一、烷基化反应的简介
1.研究作用: 可以合成塑料、医药、溶剂、合成洗涤剂、药物、染料、香料、催化剂、 表面活性剂等功能性产品。如通过C—烷基化反应可制得阴离子表面活性剂; 通过O-烷基化可制得聚乙二醇型非离子表面活性剂;通过N-烷基化合成 的季铵盐是重要的阳离子表面活性剂、相转移催化剂、杀菌剂等。
NH2 + 2 CH3OH N(CH3)2
H2 SO4 210℃/3MPa
+ 2 H2O
作用下向芳环碳上引入 烷基生成烷基苯 C 烷基化反应:在催化剂 中的氮原子上引入烷基 生成伯、仲、叔、季铵 盐 N 烷基化反应:向氨或胺 O 烷基化反应:向醇、酚 中的氧原子上引入烷基 生成醚类化合物
CH 3
CH 3
高辛烷值汽油组分生产技术

工艺条件
水,ppm 总硫,ppm
氢氟酸法
<20 <20
硫酸法
<20 <100
烷烯比,(V)
反应温度,(℃) 反应时间
≥8~12
30~40 20 s
≥8~12
8~12 20~30 min
研究法辛烷值
马达法辛烷值
95~96
92.5~93
94~96
91~92
48
硫酸法与氢氟酸法烷基化的对比
可以省掉酸洗工艺-空速低,减少酸性硫酸盐生成
35
Kellogg公司烷基化工艺
20世纪70年代以后基本不再采用-传动设备多
阶梯式反应器
自冷式烷基化工艺-烷烯比变化,难以精确控制
36
Kellogg公司烷基化流程
37
CDTECH硫酸烷基化工艺
CDAlky 是一个低温的硫酸烷基化过程,它利用轻 质烯烃和异丁烷反应生产烷基化油 这个过程在能生产高质量产品的同时比传统的工艺 也大大减少了酸的耗量 流程图比传统的设计更加简单,因此也减少了资金 和生产的投入
62-145 ℃ 62-85 ℃
甲苯
二甲苯 高辛烷值汽油组分
85-105 ℃
105-145 ℃ 80-180 ℃
10
大港油不同原料馏分铂铼重整试验结果
用宽馏分重整生产芳烃的优点
扩大了重整原料的来源,直馏宽馏分的量约为窄馏分的 1.8-2.2倍 增加了氢气和芳烃产量 副产高辛烷值汽油组分,重整生成油中 150-200℃ 馏分 的辛烷值在90以上
C C
C C C
+
C
C C
C
C
C
+
- 1、下载文档前请自行甄别文档内容的完整性,平台不提供额外的编辑、内容补充、找答案等附加服务。
- 2、"仅部分预览"的文档,不可在线预览部分如存在完整性等问题,可反馈申请退款(可完整预览的文档不适用该条件!)。
- 3、如文档侵犯您的权益,请联系客服反馈,我们会尽快为您处理(人工客服工作时间:9:00-18:30)。
CDALKYPlus 工 艺 的 特 点 是 优 化 OSV ( 烯 烃 空速) 和 I: O (异丁烷与烯烃比值), 以提高产 品辛烷值, 并降低装置建设投资, 且缩短回收期。
液体烷基化工艺成为绿色工艺路线的代表, 但是其催化剂失活与再生是该工艺路线发展的瓶颈。
关键词:烷基化; 催化剂; 述评; 展望
文章编号:1673-9647 (2016) 03-0023-08
中图分类号:TE624
文献标识码:A
随着人类环境保护意识的增强, 对车用汽油 的 质 量 提 出 了 更 高 的 要 求 。 2015 年 国 家 发 改 委 、 财政部等七部门发布 《加快成品油质量升级工作 方案》 指出, 2017 年 1 月 1 日起, 我国将全面供 应符合国Ⅴ标准的车用汽油、 车用柴油。 烷基化 油不含芳烃、 硫和烯烃, 从汽油的多种控制指标 如辛烷值、 蒸汽压、 氧含量、 烯烃含量及芳烃含 量综合考虑, 烷基化油作为汽油组分具有最佳的 综合性能, 是大幅降低硫含量、 烯烃含量的最有 效途径, 是未来国内推广国Ⅴ汽油标准的主要调 和组分。 随着社会的需求增加, 烷基化技术得到 了快速的发展, 先前成熟的烷基化技术不断改进 完善的同时, 又开发了固体酸、 离子酸和间接烷 基化等新技术。
分离, 实现助剂循环使用。 采用该工艺生产的烷 基 化 油 收 率 与 不 添 加 助 剂 相 同 , 辛 烷 值 (RON) 提 高 0.5~0.8, 操 作 费 用 比 常 规 液 体 酸 装 置 降 低 10% 左右。 ReVAP 工艺于 1997 年在 Phillips 公司 的 Wods Cross 炼油厂和 ExxonMobil 的一座炼油厂 进行了工业化生产。 1.1.2.2 Alkad 工艺
图 1 STRATCO 反应结构示意
措施提高了浓硫酸与烷烯烃进料率和混合程度、 提高了换热效率, 降低了反应温度, 提高设备使 用可靠性。
硫酸烷基化工艺中使用的催化剂浓硫酸不像 氢氟酸那样易挥发, 安全性比氢氟酸烷基化工艺 好。 但也存在腐蚀设备、 产生的大量酸渣污染环 境等缺点。 CDTECH 公司对硫酸烷基化作了改进。 1.1.1.1 CDALKY 工艺
烷基化工艺的管式反应器替换成配备静态内构件 的 立 式 反 应 器 , 并 添 加 包 括 3.4 MW 压 缩 机 及 其 相关设备的制冷部分, 氢氟酸工艺的精馏部分在 改造后可继续使用, 可使总成本降低约 20%。 1.1.1.2 CDALKYPlus 工艺
原料中的异丁烯具有强放热聚合反应倾向, 以往的烷基化技术难以加工含异丁烯的原料, 因 为异丁烯齐聚反应不仅会导致反应器温升, 还会 降 低 产 品 的 辛 烷 值 。 为 解 决 这 一 问 题 , CDTECH 公司将两种已工业化的技术 (CDOPT 和 CDALKY) 进行集成, 形成了以异丁烯为唯一烯烃来源的成 套烷基化工艺 (CDALKYPlus), 可 提 高 烷 基 化 油 的辛烷值、 降低酸耗、 提高能源利用率。
1 直接法烷基化工艺
直接烷基化是异丁烷与丁烯在强酸性催化剂 作用下烷基化反应, 生成 C8 为主要成分的烷基化 油。 按反应过程所使用催化剂的种类可将其分 为: 液体酸烷基化、 固体酸烷基化和离子液体烷 基化。 1.1 液体酸烷基化工艺
液体酸烷基化催化剂主要采用浓硫酸和氢氟 酸。 目前仅有 4 家液体酸烷基化技术商业许可商, 它 们 是 CDTECH、 DuPontSTRATCO、 ExxonMobil 和 UOP。 目前, 液体酸烷基化技术占据着全球烷 基化产能的 90%。 但考虑到液体酸烷基化技术相 关的安全隐患, 为了避免灾难性事故和高额保险 费用, 北美和欧洲的新建装置基本上都已停止使 用这种工艺技术。 根据 UOP 报道, 如果炼厂希望
CDALKYPlus 技术可用于 MTBE 装置的改造, 已经通过了为期 5 个月的中试验证。 建成的示范 装置以脱氢装置产品为原料, 主要由异丁烯和异 丁烷组成 (异丁烯几乎是唯一烯烃来源), 还含有 少量的轻烃 (C1~C3)、 其他 C4 烯烃以及痕量的正 丁烷、 丁二烯、 C5 和 C6 以上烃类。 表 1 比较了采 用 相 同 原 料 、 由 MTBE 装 置 改 造 成 CDALKYPlus 装置与异辛烷装置的生产数据。 异辛烷装置生产 的汽油调和组分具有很高的辛烷值, 但改造成本
第 34 卷 第 3 期 2016 年 3 月
化学工业 CHEMICAL INDUSTRY
·23·
技术与评述
烷基化生产技术
贾领军
(中国石油吉林石化公司, 吉林 132000)
摘 要:介绍烷基化技术现状及发展趋势 。 目前直接法液体酸烷基化工艺占工业生产主流 , 但是各种液体酸烷
基化工艺都存在腐蚀设备、 产生大量酸渣污染环境, 尤其氢氟酸催化剂甚至有挥发性和毒性, 而固体酸和离子
1.1.2 氢氟酸烷基化技术 氢氟酸烷基化工艺可分为 Philips 公司开发的
技术和 UOP 开发的技术, 我国引进的 12 套氢氟 酸烷基化装置全部采用 Philips 公司的技术。 装置 主要由原料干燥脱水、 氢氟酸烷基化反应、 分馏、 产品精制、 氢氟酸再生和三废再生处理系统等几 部分组成。 氢氟酸烷 基 化 的 反 应 温 度 通 常 为 15~ 50℃, 反应温度一般控制在 30 ℃左右, 高于硫酸 烷基化的反应温度。 烷烯比为 12~15∶1, 酸烃比为 4∶1, 氢 氟 酸 质 量 分 数 控 制 在 82%~88%, 酸 中 含 水 1. 5%~2%。
UOP 公司对传统的氢氟酸烷基化做出工艺改 进, 主要在进料方式和降低氢氟酸的挥发。 通过 采用分开进料串联循环反应器不仅实现了反应热 量及时带出, 而且有效提高了反应中实际的异丁 烷 / 烯 烃 比 。 UOP 和 Texaco 合 作 开 发 成 功 Alkad 工艺和 AlkadTM 助剂技术, 其核心是采用一种蒸 气压抑制助剂 (AlkadTM)。 AlkadTM 是一种砜类 化合物, 可与氢氟酸分子进行强缔合的长链, 生 成蒸汽压较低的液态聚氟化氢络合物, 降低了氢 氟酸的挥发性。 通过该技术与水喷淋系统相结合, 可以将氢氟酸的雾化降至最低, 同时还能提高烷 基 化 油 的 辛 烷 值 。 Alkad 工 艺 的 第 一 套 工 业 化 生 产装置属于美国堪萨斯州的一家炼油厂。 在使用 AlkadTM 添 加 剂 后 , 烷 基 化 油 的 辛 烷 值 (RON) 提高了 1。 1.2 固体酸烷基化工艺
CDTECH 公司 (现归属 CB&I Lummus) 开发 的 CDALKY 工艺为低温硫酸烷基化技术, 其核心 是反应系统的设计, 传质效率高于传统工艺。 该 工艺为立式可放大的反应器系统, 用专有的静态 内构件代替搅拌方式, 实现了烃和酸的直接接触。 烷基化反应能在更低的温度下进行 (CDALKY 反 应器的操作温度在-3 ℃以下, 而传统工艺的反应 温度为 7~8 ℃)。 更低的反应温度使得烷基化反应 朝着更有利于生成高辛烷值三甲基戊烷的方向进 行 , 而 且 减 少 了 酸 耗 (30%~50%), 解 决 了 低 温 下反应物因粘度过高而引起的混合不充分等问题。 此外, 为降低酸耗及对下游设备的腐蚀, 酸洗和 水洗过程均被取消。 与其他工业化的硫酸烷基化 工艺相比, CDALKY 提高了装置的可放大性和可 靠性, 降低了装置操作费用和设备投资费用。 浙 江 宁 波 海 越 新 材 料 公 司 引 进 产 能 60 万 t / a 的 CDALKY 工艺, 已在 2014 年建成投产。 CDALKY 工艺见图 2。
CDALKY 技术同样可用于对现有氢氟酸 和 硫 酸烷基化装置改造。 据 CDTECH 公司称, 某产能 为 40 万 t / a 的氢氟酸烷基化装置采用 CDALKY 技 术改造成硫酸烷基化装置, 所用原料为含少量丙 烷和丙烯的 FCC 混合碳四。 改造时, 需将氢氟酸
图 2 CDALKY 工艺流程
从事化工生产的管理。
·24·
化学工业 CHEMICAL INDUSTRY
2016 年 第 34 卷
1—冷剂入口; 2—冷剂出口; 3—混合物至酸沉 积 物 器 ; 4.—反 应 器 壳 体 ; 5—循 环 器 ; 6—U 型 管束; 7—酸进料口; 8—烃进料口; 9—十字轴; 10—叶轮; 11—水压头; 12—电机
DuPont 公司不断对原有的卧式偏心反应器进 行改进, 主要是从两方面入手: 提高浓硫酸和烷 烯烃原料的混合程度; 最大限度带走反应热。 主 要措施有: 采用专有的管插件技术、 新型换热管 束、 新型进料分布器和可靠密封技术。 通过上述
收稿日期: 2016-03-17 作者简介: 贾领军 (1968-), 男 , 江 苏 省 人 , 高 级 工 程 师 , 主 要
增加液体酸烷基化产能, 那么对现有装置进行改 造更为合适。 1.1.1 硫酸烷基化技术
硫 酸 烷 基 化 以 美 国 杜 邦 公 司 的 STRATCO 急 冷烷基化技术为代表。 该工艺利用反应段出来的 部分或全部流出液对反应段制冷。 反应器是带有 叶轮搅拌的卧式列管式换热器, 靠机械搅拌实现 酸-烃混合, 具有酸 / 烃比例可以灵活调节、 硫酸 分布均匀的特点。 其适宜的反应温度 4~8 ℃, 采 用换热取走反应热, 单台反应器处理能力约为 8 万 t / a。 反应产物需经酸洗、 碱洗, 然后分馏。 该 技 术 成 熟 , 诸 如 CDTECH、 DuPont STRATCO、 ExxonMobil 和 RHT 等公司都能够提供硫酸烷基化 技术。
2007 年 UOP 收 购 了 Philips 公 司 的 氢 氟 酸 烷Байду номын сангаас基化股权, 成为目前唯一具有氢氟酸法烷基化技 术许可的公司。 氢氟酸烷基化工艺与硫酸烷基化 工艺相比, 占用空间小、 设计简单、 催化剂的消 耗少, 但分离异丁烷、 丙烷、 氢氟酸和含氟化合 物的成本高于硫酸烷基化技术。 氢氟酸烷基化技 术的弱点是所采用的氢氟酸催化剂具有腐蚀性、 挥发性和毒性。 氢氟酸烷基化的改进技术如下。 1.1.2.1 ReVAP 工艺