粘土湿型砂的控制要点
湿型砂的检测要求与质量控制
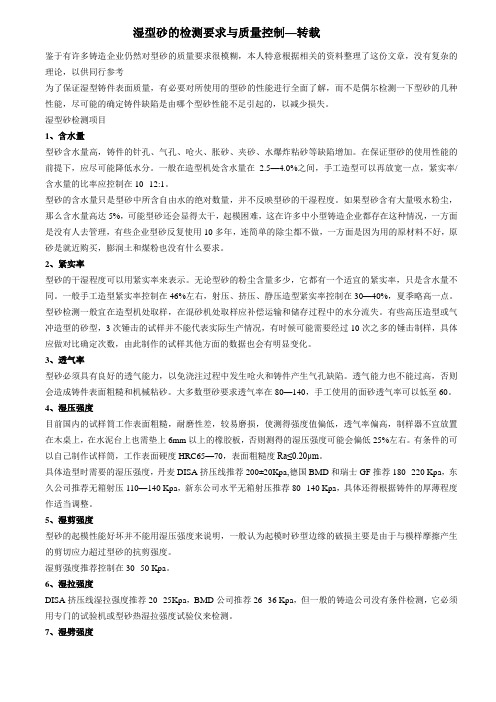
湿型砂的检测要求与质量控制—转载鉴于有许多铸造企业仍然对型砂的质量要求很模糊,本人特意根据相关的资料整理了这份文章,没有复杂的理论,以供同行参考为了保证湿型铸件表面质量,有必要对所使用的型砂的性能进行全面了解,而不是偶尔检测一下型砂的几种性能,尽可能的确定铸件缺陷是由哪个型砂性能不足引起的,以减少损失。
湿型砂检测项目1、含水量型砂含水量高,铸件的针孔、气孔、呛火、胀砂、夹砂、水爆炸粘砂等缺陷增加。
在保证型砂的使用性能的前提下,应尽可能降低水分。
一般在造型机处含水量在 2.5—4.0%之间,手工造型可以再放宽一点,紧实率/含水量的比率应控制在10--12:1。
型砂的含水量只是型砂中所含自由水的绝对数量,并不反映型砂的干湿程度。
如果型砂含有大量吸水粉尘,那么含水量高达5%,可能型砂还会显得太干,起模困难,这在许多中小型铸造企业都存在这种情况,一方面是没有人去管理,有些企业型砂反复使用10多年,连简单的除尘都不做,一方面是因为用的原材料不好,原砂是就近购买,膨润土和煤粉也没有什么要求。
2、紧实率型砂的干湿程度可以用紧实率来表示。
无论型砂的粉尘含量多少,它都有一个适宜的紧实率,只是含水量不同。
一般手工造型紧实率控制在46%左右,射压、挤压、静压造型紧实率控制在30—40%,夏季略高一点。
型砂检测一般宜在造型机处取样,在混砂机处取样应补偿运输和储存过程中的水分流失。
有些高压造型或气冲造型的砂型,3次锤击的试样并不能代表实际生产情况,有时候可能需要经过10次之多的锤击制样,具体应做对比确定次数,由此制作的试样其他方面的数据也会有明显变化。
3、透气率型砂必须具有良好的透气能力,以免浇注过程中发生呛火和铸件产生气孔缺陷。
透气能力也不能过高,否则会造成铸件表面粗糙和机械粘砂。
大多数型砂要求透气率在80—140,手工使用的面砂透气率可以低至60。
4、湿压强度目前国内的试样筒工作表面粗糙,耐磨性差,较易磨损,使测得强度值偏低,透气率偏高,制样器不宜放置在木桌上,在水泥台上也需垫上6mm以上的橡胶板,否则测得的湿压强度可能会偏低25%左右。
粘土湿型砂混砂机及混制工艺
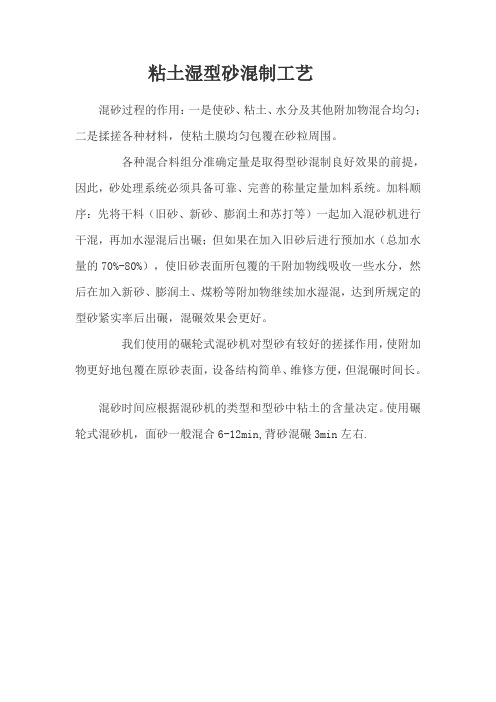
粘土湿型砂混制工艺
混砂过程的作用:一是使砂、粘土、水分及其他附加物混合均匀;二是揉搓各种材料,使粘土膜均匀包覆在砂粒周围。
各种混合料组分准确定量是取得型砂混制良好效果的前提,因此,砂处理系统必须具备可靠、完善的称量定量加料系统。
加料顺序:先将干料(旧砂、新砂、膨润土和苏打等)一起加入混砂机进行干混,再加水湿混后出碾;但如果在加入旧砂后进行预加水(总加水量的70%-80%),使旧砂表面所包覆的干附加物线吸收一些水分,然后在加入新砂、膨润土、煤粉等附加物继续加水湿混,达到所规定的型砂紧实率后出碾,混碾效果会更好。
我们使用的碾轮式混砂机对型砂有较好的搓揉作用,使附加物更好地包覆在原砂表面,设备结构简单、维修方便,但混碾时间长。
混砂时间应根据混砂机的类型和型砂中粘土的含量决定。
使用碾轮式混砂机,面砂一般混合6-12min,背砂混碾3min左右.。
湿型砂铸造混砂注意事项与配比!

湿型砂铸造混砂注意事项与配比!湿型砂的主要特点是什么?湿型砂是以膨润土作粘接剂的一种不经烘干的型砂。
湿型砂的基本特点在于砂型不需烘干、不经固化、具有一定的湿强度,虽然强度较低但是退让性较好,而且便于落砂。
因为砂型不需烘干,所以造型效率高、生产周期短、材料成本低、便于组织流水生产。
但是因为砂型不经烘干,所以在浇注时,砂型表面就出现了水分的汽化和迁移,使铸件容易产生生气孔、夹砂以及砂眼、胀砂、粘砂等缺陷。
为了充分发挥湿型优点,提高铸件质量,在生产过程中必须保持型砂性能稳定、砂型紧实均匀及铸造工艺合理。
因此,湿型工艺的发展一直是和造型机械及造型工艺的发展紧密相连的。
目前湿型机械化造型已从普通的机器造型发展到高密度机器造型,造型的生产率、砂型的紧实度、铸件的尺寸精度不断提高,铸件表面粗糙度值则不断降低。
各种造型方法的特点及所生产的铸件尺寸精度和表面粗糙度见表3-12.。
一般来说,压实比压大于0.7MPa的称为高压造型。
高压造型的砂型密度可达1、5~1、6克/立方,硬度在90以上(用B型硬度计测量),故也称高密度造型。
高密度造型包括多触头高压造型、无箱挤压造型、气冲造型及静压造型等。
这几种造型所用湿型砂的性能和配比比较接近。
湿型砂主要应于生产中小型铸件,特别是应用于大批量机械化造型生产汽车、拖拉机、柴油机、轻砂机械等铸件。
采用湿型(不刷涂料时)也可生产重达几百千克的铸铁件。
湿型砂的主要原材料组分是什么?如何选用?湿型砂的基本组分有原砂、膨润土和煤粉。
为改善湿型砂的一些特殊性能,有时还添加重油、淀粉以及氧化铁粉等。
1)选用原砂时,首先要根据所浇注的合金种类确定原砂的二氧化硅含量,其次根据混合料种类确定原砂泥的含量及其他性能;还要根据铸件大小确定原砂粒度。
湿型砂所用原砂一般较细,粒度主要50/100、70/140和100/200筛号,如采用水洗砂,泥的质量分数最好在1%以下。
高密度造型的湿型砂,为减少砂型受热时的膨胀,避免引起夹砂,原砂的二氧化Si含量不必过高,粒形不必很圆,可以采用多角形原砂,粒度不宜过于集中,一般采用三篩砂或四筛砂,必要时可将两种粒度的原砂混合使用,以达到合适的粒度要求。
粘土水分调控措施
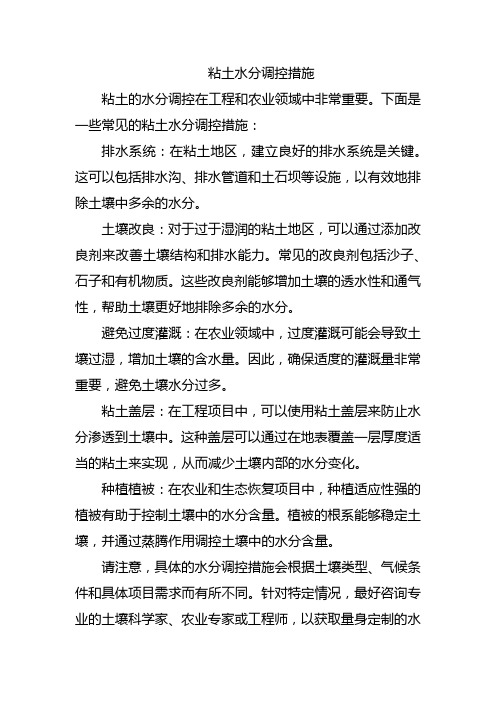
粘土水分调控措施
粘土的水分调控在工程和农业领域中非常重要。
下面是一些常见的粘土水分调控措施:
排水系统:在粘土地区,建立良好的排水系统是关键。
这可以包括排水沟、排水管道和土石坝等设施,以有效地排除土壤中多余的水分。
土壤改良:对于过于湿润的粘土地区,可以通过添加改良剂来改善土壤结构和排水能力。
常见的改良剂包括沙子、石子和有机物质。
这些改良剂能够增加土壤的透水性和通气性,帮助土壤更好地排除多余的水分。
避免过度灌溉:在农业领域中,过度灌溉可能会导致土壤过湿,增加土壤的含水量。
因此,确保适度的灌溉量非常重要,避免土壤水分过多。
粘土盖层:在工程项目中,可以使用粘土盖层来防止水分渗透到土壤中。
这种盖层可以通过在地表覆盖一层厚度适当的粘土来实现,从而减少土壤内部的水分变化。
种植植被:在农业和生态恢复项目中,种植适应性强的植被有助于控制土壤中的水分含量。
植被的根系能够稳定土壤,并通过蒸腾作用调控土壤中的水分含量。
请注意,具体的水分调控措施会根据土壤类型、气候条件和具体项目需求而有所不同。
针对特定情况,最好咨询专业的土壤科学家、农业专家或工程师,以获取量身定制的水
分调控建议。
粘土型(芯)砂
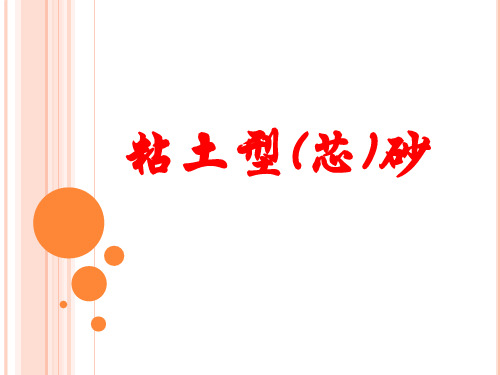
对湿型砂而言,混砂时严格控制加水量是 必要的。工厂中常用的加水量控制办法有 以下几种: ①人工加水。 ②定量水箱、定量水表、时间继电器控制 电磁水阀。边测量、边控制。
28
三、型砂的质量检验和控制
通过型砂的质量检验和宏观控制,不但可了解型砂 是否达到要求的性能,而且还可掌握型砂在使用中 的变化,这样就能及早采取措施,保证型砂符合要 求和保持稳定,保证铸件质量,预防缺陷产生。 试验结果的综合分析 每次取样测出的型砂性能,常在一定范围内波动, 故一次试验结果还不能说明问题,应取每天试验结果 的平均值,才能较好地代表整个型砂系统的状况。
20
铸钢型砂的特点:
为了防止铸件增碳,型砂中不含煤粉和煤粉烧损的残 留物,因而铸钢型砂的含泥量较铸铁型砂低,需水量少 。在同样紧实率下.铸钢型砂的水分低,有利于防止产 生针孔或皮下气孔。水分最好控制在4%-5%(质量分数) 或更低些。 由于型砂中不含煤粉和含泥量低,单一砂和面砂的透 气性容易偏高。单一砂的透气性最好不超过120,面砂 的透气性还应更低才能生产出表面光洁无机械粘砂的铸 件。为此,可选用粒度15Q(或2lQ)的硅砂,不宜使用粒 度为30Q的粗硅砂。
4.高密度造型型砂
(1)高密度造型特点 高密度造型是指提高造型紧实力制得较高紧实程度或较高 密度砂型的造型方法而言。过去高密度造型只指各种高压造 型。近十多年来,高速的冲击造型包括动力(机械)冲击和气 流冲击造型得到了越来越广泛的开发相应用,也属高密度造 型。 一般认为,压实比压高到0.7MPa以上称为高压造型,用 此法生产出来的铸件不仅尺寸精度高,表面粗糙度大大改善 ,而且能使铸件更加致密,力学性能更高,加工余量减少, 铸件质量减轻,劳动条件改善,生产率大大提高等。 高压造型中,由于其不良的砂型强度分布;另外,随着压 实比压的提高,还可能引起“水爆炸”,从而会出现型壁移 动,并使铸件产生气孔、局部表面粗糙和机械粘砂、甚至整 24 个铸件表面粘砂等缺陷 。
膨润土在粘土湿型砂中应用的几个应注意的控制要点

膨润土在粘土湿型砂中应用的几个应注意的控制要点膨润土在铸造中主要用于粘土粘结砂中,因为膨润土具有粘结力强、可塑性高、脱膜好、透气性优、高温湿态条件下物理化学性能稳定等特点。
粘土粘结砂作造型材料生产铸件,本是历史悠久的工艺方法,在各种化学粘结砂蓬勃发展的今天,粘土湿型砂仍是最重要的造型材料,其适用范围之广,耗用量之大,是任何其他造型材料都不能与之比拟的。
近代的高压造型、射压造型、气冲造型、静压造型及无震击真空加压造型等新工艺,也都是以使用粘土湿型砂为前提的,粘土湿型砂适应造型条件的能力极强。
现今,随着科学技术快速发展,各产业部门对铸件的需求不断增长,同时,对铸件品质的要求也越来越高。
也使粘土湿型砂面临许多新的问题,促使我们对粘土湿型砂的研究不断加强、认识不断深化。
前不久,笔者走访了国内一些铸造单位,发现铸件的废品较多,特别是一些小规模铸造单位,问题主要是有气孔等缺陷。
产生问题主要在生产新铸件、换其他厂家膨润土和长期使用旧砂期间。
有必要对膨润土和旧砂的控制要点进行一下强调。
1.膨润土和膨润土粘土粘结砂中的,作用及变化,铸造用膨润土主要有钠基膨润土和钙钠膨润土两类,钠基膨润土是由天然钠基膨润土或人工钠化膨润土加工而成,以其复用性好和湿压强度高而受铸造行业欢迎。
因具有良好的可塑性,可遏止铸件夹砂、结疤、掉块、砂型塌方等现象,加之成型性强、型腔强度高,便于金属行业浇铸湿态或干态型模,是精密铸件首选的型砂粘结剂。
钙钠膨润土由天然基钙钠膨润土加工它以实用和铸件清砂便捷是轻型铸件普遍采用的型砂粘结剂。
而成,而受用户欢迎。
和其他黏结剂相比,膨润土有一个重要的特点,就是它具有一定的耐热能力。
只要加热温度不太高,脱除了自由水的膨润土只要加水,仍能恢复粘能力。
膨润土的粘结能力只有在加水以后才能表现出来。
膨润土失去粘结能力,也与它的脱水有关。
到目前为止,认为膨润土中的水分有3种形态:一种水是自由水,即膨润土颗粒吸附的水,加热到100℃以上,就可脱除自由水,脱除了自由水的膨润土,粘结能力不受影响;二种水是牢固结合水,110℃下长时间加热,膨润土可完全脱除自由水,但不会脱除牢固结合水。
粘土湿型砂的控制要点

粘土湿型砂的控制要点粘土湿型砂在铸造工艺中起着重要的作用,控制好粘土湿型砂的质量是确保铸件质量和生产效率的关键。
以下是控制粘土湿型砂质量的要点:1. 选择合适的粘土湿型砂配方:根据铸件的要求和工艺要求,选择合适的粘土种类和比例。
不同的粘土具有不同的粘结性和流动性,要根据具体情况进行选择,保证铸件的表面光滑度和精度。
2. 严格控制水分含量:粘土湿型砂中的水分含量对于浇铸过程和铸件的表面质量有着重要影响。
过少的水分会导致砂型难以成型和裂纹的产生,过多的水分则会造成砂型的变形和铸件的表面缺陷。
因此,要通过严格控制水分含量来确保砂型的强度和铸件的质量。
3. 控制粘度和流动性:粘度和流动性是粘土湿型砂的两个重要指标,直接影响到砂型的成型性能和浇注的顺利进行。
通过控制粘土的粒度分布、粘接剂的种类和比例等因素,调整粘土的粘度和流动性,确保砂型的成型质量和铸件的形状精度。
4. 保证砂型的干燥性能:粘土湿型砂在使用前需要进行干燥处理,以去除多余的水分。
因为湿度高的砂型易造成铸件内部气孔,降低铸件的强度和表面质量。
因此,在干燥处理过程中,要严格控制砂型的干燥温度和时间,确保砂型的干燥性能。
5. 严格控制砂型质量:粘土湿型砂的质量对于铸件的成型质量和表面质量至关重要。
因此,要定期进行砂型的质量检测,包括外观检查、尺寸测量、强度测试等。
对于不合格的砂型,要及时进行处理或更换,以保证生产的正常进行。
6. 做好砂型的储存和保管:在使用粘土湿型砂的过程中,要做好砂型的储存和保管工作。
砂型应放置在干燥、通风的环境中,避免接触水分和其他污染物。
同时,要定期检查砂型的保存状态,及时处理发现的问题,以保证下次使用时的质量。
通过以上的控制要点,可以有效地提高粘土湿型砂的质量,确保铸件的表面质量和生产效率的提升。
粘土湿型砂在铸造工艺中扮演着重要的角色,其质量的控制直接影响到铸件的成型质量和表面质量。
为了保证粘土湿型砂具备良好的流动性和粘结性,需要在配方设计、水分控制、粘土颗粒分布、干燥处理、质量检测以及储存保管等方面进行精细的控制。
湿型砂系统的控制
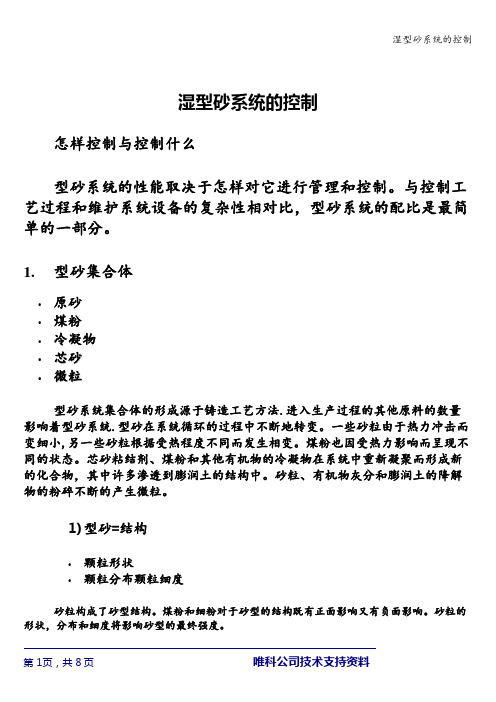
湿型砂系统的控制怎样控制与控制什么型砂系统的性能取决于怎样对它进行管理和控制。
与控制工艺过程和维护系统设备的复杂性相对比,型砂系统的配比是最简单的一部分。
1.型砂集合体•原砂•煤粉•冷凝物•芯砂•微粒型砂系统集合体的形成源于铸造工艺方法.进入生产过程的其他原料的数量影响着型砂系统.型砂在系统循环的过程中不断地转变。
一些砂粒由于热力冲击而变细小,另一些砂粒根据受热程度不同而发生相变。
煤粉也因受热力影响而呈现不同的状态。
芯砂粘结剂、煤粉和其他有机物的冷凝物在系统中重新凝聚而形成新的化合物,其中许多渗透到膨润土的结构中。
砂粒、有机物灰分和膨润土的降解物的粉碎不断的产生微粒。
1)型砂=结构•颗粒形状•颗粒分布颗粒细度砂粒构成了砂型结构。
煤粉和细粉对于砂型的结构既有正面影响又有负面影响。
砂粒的形状,分布和细度将影响砂型的最终强度。
颗粒形状也影响砂型的最终结构。
尖角状颗粒表面积对体积的比例高,通常流动性差,影响砂型的潜在密度.尖角状颗粒的热破裂更易造成系统中砂的过多磨损,也影响膨润土的消耗。
2)芯砂i.冷芯盒粘结剂不曾受曝热(不被焙烧 ),湿的颗粒可以被膨润土粘结进入砂系统的芯砂有多种类型。
没有受到热影响的芯砂颗粒如果残留的粘结剂能用水润湿可以被膨润土粘结.ii.在氧化性气体中加热之后 (部分煅烧),能润湿的颗粒可以被膨润土粘结一些芯砂上的粘结剂可被氧化,如果能被润湿就可以被粘结。
iii.暴露在还原性气体中加热,被残余的含碳物质覆盖,不能湿润,就不能被膨润土粘结暴露于还原气体中加热的芯砂颗粒不能被润湿,就不能被膨润土包裹iv.良好的重复粘结力,完全焙烧一些芯砂被完全煅烧,这样的芯砂可轻易的被膨润土包覆。
v.进入砂系统的砂芯数量,以公斤/吨金属表达,小于135公斤/吨金属通常可以接受,大于135公斤/吨则需要调整每天或每小时跟踪记录进入系统的芯砂的量非常重要。
如果芯砂进入量超过135公斤/吨金属,那么系统可能就要通过新砂冲淡或用某种方式擦磨以维持砂的质量.3)粘结剂 = 粘土•砂的颗粒被粘土粘结•密度决定粘结力在混砂机中型砂得到恢复性处理,因加热而失水的膨润土重新水化,受到煅烧的膨润土被代替.造型机通过压力将型砂紧实从而使砂型获得一定的密度.4)硬度与强度•砂型密度决定。
- 1、下载文档前请自行甄别文档内容的完整性,平台不提供额外的编辑、内容补充、找答案等附加服务。
- 2、"仅部分预览"的文档,不可在线预览部分如存在完整性等问题,可反馈申请退款(可完整预览的文档不适用该条件!)。
- 3、如文档侵犯您的权益,请联系客服反馈,我们会尽快为您处理(人工客服工作时间:9:00-18:30)。
粘土湿型砂的控制要点用粘土粘结砂作造型材料生产铸件,是历史悠久的工艺方法,也是应用范围最广的工艺方法。
说起历史悠久,可追溯到几千年以前;论其应用范围,则可说世界各地无一处不用。
值得注意的是,在各种化学粘结砂蓬勃发展的今天,粘土湿型砂仍是最重要的造型材料,其适用范围之广,耗用量之大,是任何其他造型材料都不能与之比拟的。
据报道,美国钢铁铸件中,用粘土湿型砂制造的占80%以上;日本钢铁铸件中,用粘土湿型砂制造的占73%以上。
适应造型条件的能力极强,也是粘土湿型砂的一大特点。
1890年震压式造型机问世,长期用于手工造型条件的粘土湿型砂,用于机器造型极为成功,并为此后造型作业的机械化、自动化奠定了基础。
近代的高压造型、射压造型、气冲造型、静压造型及无震击真空加压造型等新工艺,也都是以使用粘土湿型砂为前提的。
各种新工艺的实施,使粘土湿型砂在铸造生产中的地位更加重要,也使粘土湿型砂面临许多新的问题,促使我们对粘土湿型砂的研究不断加强、认识不断深化。
现今,随着科学技术的速发展,各产业部门对铸件的需求不断增长,同时,对铸件品质的要求也越来越高。
现代的铸造厂,造型设备的生产率已提高到前所未有的水平,如果不能使型砂的性能充分适应具体生产条件,或不能有效的控制其稳定、一致,则不用多久就可能将铸造厂埋葬于废品之中。
随着科学技术的发展,目前采用粘土湿型砂的铸造厂,一般都适合其具体条件的砂处理系统,其中包括:旧砂的处理、新砂及辅助材料的加入、型砂的混制和型砂性能的监控。
粘土湿砂系统中,有许多不断改变的因素。
如某一种或几种关键性能不能保持在控制范围之内,生产中就可能出现问题。
一个有效的砂处理系统,应能监控型砂的性能,如有问题,应能及时加以改正。
由于各铸造厂砂处理系统安排不同,选用的设备也不一样,要想拟定一套通用的控制办法是做不到的。
这里,打算提出一些目前已被广泛认同的控制要点。
各铸造厂认真地理解了这些要点之后,可根据自己的具体条件确定可行的控制办法。
而且,还要随着技术的进步和工厂的实际能力(包括人员和资金)不断改进对型砂系统的控制。
一.旧砂的处理用粘土湿型砂造型,浇注以后,除贴近铸件的部分型砂中活性膨润土受热失效成为死粘土外,大部分型砂可以回收使用。
这是粘土湿型砂的主要优点之一。
配制粘土湿型砂时,旧砂用量一般都在90%以上,如果对旧砂的处理不当,无论怎样加强混砂,无论添加什麽辅助材料,都不可得到好的型砂。
所以,对旧砂进行有效的处理,是保证型砂质量的前提。
1.旧砂温度的控制热砂问题,已被公认为粘土湿型砂铸造必须面对的最大问题。
型砂温度太高,铸件容易产生夹砂、表面粗糙、冲砂、气孔等缺陷。
热砂对铸件质量的负面影响,主要由于以下几个方面:・由于热砂使水分蒸发,混砂时无论怎样注意,也难以控制型砂的性能;・将热型砂送往造型机的过程中,由于水份损失,型砂性能改变,造型时实际上用的型砂,其性能与混砂时控制的性能差别很大;・造型时,热型砂的水分容易在模样表面上凝结,型砂粘模;・合型后,热砂的水分蒸发,凝结在冷的芯子上,会使芯子的强度降低,铸件也易于产生气孔;・如果旧砂要贮存在砂斗中备用,则热砂容易粘附在砂斗壁上。
严重时,砂斗四周堵满了型砂,只剩中间一个孔洞,使系统中的型砂只有一部分周期使用,这部分型砂周转快、温度又会进一步提高,使热砂问题更加严重。
多高温度的砂算是热砂?判断热砂的温度界限,是看其是否使混砂、造型及铸件质量方面出现问题。
对此,许多研究者从个方面进行了研究;有人研究了型砂温度对其性能稳定性的影响;有人研究了温度对膨润土-水系统流变性的影响;有人研究了型砂温度与铸件质量的关系。
各方面的研究,得到了一致的结论,即:为保证型砂的性能稳定,温度应保持在50℃以下。
使型砂冷却,最有效的办法是加水,但是,简单的加水,效果是很差的。
一定要吹入大量空气使水分蒸发,才能有效地冷却。
以下,给出一个简略的计算比较:型砂的比热大致是:9.22×102J/kg・℃,水的比热是:4.19×103J/kg・℃,水的蒸发热是:2.26×106J/kg,1吨砂中加20℃的水10kg(加水1%),使其温度升到50℃,所能带走的热量为4.19×103 ×10×30,即12.57×105J。
1吨砂温度降低1℃,需散热9.22×102×1000 J,即9.22×105 J。
所以,在旧砂中加水1%,只能使温度降低24.5℃。
使1吨砂中的水分蒸发1%(10kg),能带走的热量为2.26×107J,却可使砂温降低24.5℃。
以上的分析表明:简单地向皮带机上加水或向砂堆洒水,冷却效果是很差的。
即使加水后向砂表面吹风,也不能有多大的改善。
加水后,要使水在型砂中分散均匀,然后向松散的砂吹风,使水分迅速蒸发,同时将蒸汽排除。
目前,型砂冷却装置的品种、规格很多,主要有冷却滚筒、双盘冷却器和冷却沸腾床等,都是利用水分蒸发冷却型沙。
其中,冷却沸腾床效果较好。
2.旧砂的水分控制几乎所有的铸造厂都检查和控制混成砂的水分,但是,对于严格控制旧砂水分的重要性,很多铸造厂的领导和技术人员还缺乏足够的认识。
进入混砂的旧砂水分太低,对混砂质量的影响可能并不亚于砂温过高。
试验研究和经验都已证明,加水润湿干膨润土比润滑湿膨润土难得多。
型砂中的膨润土和水,并非简单的混在一起就行,要对其加搓揉,使之成为可塑状态。
这就像用陶土和水制陶器一样,将水和土和一和,是松散的,没有粘接能力;经过搓揉和摔打,使每粒土都充分吸收了水分,就成为塑性状态,才可以成形,制成陶器毛坯。
铸型浇注以后,由于热金属的影响,很多砂粒表面上的土-水粘结膜都脱水干燥了,加水使其吸水恢复塑性是很不容易的。
旧砂的水分较低,在混砂机中加水混碾使之达到要求性能所需要的时间就越长。
由于生产中混砂的时间是有限的,旧砂的水分越低,混成砂的综合质量就越差。
目前,各国铸造工作者已有了这样一种共识:进入混砂机的旧砂,水分只能比混成砂略低一点。
较好的做法是:在旧砂冷却过程中充分加水冷却后所含的水分略低于混成砂。
这样,从砂冷却到进入混砂机还有一段相当长的时间,水可以充分润湿旧砂砂粒表面上的膨润土。
更好的做法是:在系统中设混砂机对旧砂进行预混,冷却后的旧砂在预混混砂机中加水进行预混,以改善旧砂中膨润土和水的混合状态。
国外,有的铸造厂预混时,将需补加的新砂、膨润土、煤粉等附加料全部加入。
天津的新伟祥铸造公司,用德国制造的EiRich混砂机预混。
经过预混的旧砂,进入混砂机后加水量很少,只是略微调整。
型砂中的膨润土和水在混砂机进一步得到调制,型砂的性能就更为稳定一致。
3.旧砂的粒度对于用粘土湿型砂制造的铸铁件,型砂的粒度以细一些为好。
由于混砂时旧砂用量一般都在90%以上,决定型砂粒度的因素主要是旧砂。
新砂加入量很少,不可能靠加入新砂来改变型砂的粒度。
所以,应该经常检测旧砂的粒度。
检测粒度时,取样后先清洗除去泥分(可用测定含泥量时剩下的砂样),烘干后筛分。
对粒度有以下两点要求。
(1)140目筛上的砂粒应在10-15%之间。
保持较多的细砂,可以减轻铸件表面粘砂。
而且,会增加砂粒之间粘结桥的数量,从而降低型砂的脆性,避免冲砂缺陷。
此外,这对提高型砂的温强度、干强度和水分迁移后增湿层强度都有好处。
(2)200目筛、270目筛和底盘上细砂的总和应尽量地少。
这样的细砂对改善铸件表面质量的作用不大,却会使混成砂的水分较高,而且会使型砂的透气性降低。
细砂的总和一般应少于4%。
4.吸水细粉的含量吸水细粉中主要是死粘土,还包括焦化了的煤粉细粒和其他细粉。
吸水细粉的含量并非越低越好,最好将其控制在2-5%之间。
吸水细粉,混砂时会和膨润土争夺水分,使混成砂达到可紧实性目标值所需的水分增高。
但是,据目前大家的认识,吸水细粉的吸水能力比膨润土强,而保持水分的能力却低于膨润土。
因此,在型砂中加水量略有不当时,吸水细粉对型砂性能有一定的"微调和稳定"作用。
水分高时,细粉首先吸水,膨润土所吸收水可较稳定一致;混成砂在输送过程中水分蒸发时,吸水细粉所吸的水先蒸发,粘结砂粒的粘土膏中的水分较为稳定,型砂的性能也就较小波动。
吸水细粉含量太高也不好,会使型砂的水分较高,易于导致铸件上产生针孔、表面粗糙和砂孔的缺陷。
吸水细粉含量太低,则型砂的性能(尤其是可紧实性)不易稳定。
二.补加新砂及辅助材料粘土湿型砂在系统中反复使用,由于铸件粘附的砂粒被带走,部分膨润土受热成为死粘土,煤粉受热失效以及抽尘系统吸走粉状材料等因素,补加新材料以保持系统砂的总量稳定、性能一致是绝对必要的。
这里,只简单谈谈各种材料补加量的确定,不想罗列各种材料的规格。
1、新砂用新砂配成的型砂,是简单的混合物。
在生产条件下,混砂时间不可能很长,膨润土和水形成的粘土膏不可能均匀涂布在砂粒表面上,砂粒的结构见图1(a)。
反复使用的旧砂,砂粒结构见图1(b),砂粒表面上积了多层变质烧结层,粘土膏的涂布则相当均匀。
图1 粘土湿型砂的砂粒结构因此,混砂时补加的新砂不宜太多,以保持系统砂总量稳定为原则。
新砂加入量太多,会对型砂质量有负面的影响。
国外一些运转良好的型砂系统,新砂补加量一般是每浇注1吨铁水120~150kg。
如考虑砂-铁比平均为5,则混砂时新砂补加量为2.6~3%。
当然,新砂补加量还要考虑很多因素,如设备条件,芯砂进入量。
很多铸造厂要根据自己的条件确定,外厂的经验只能参考。
我国铸造厂一般散落砂都较多,很多厂新砂补加量为5-8%,这也是合适的。
也有少数铸造厂以为多家新砂可以提高型砂质量,这种想法可能来自旧砂完全没有处理、生产量又小的条件。
2、膨润土和其他黏结剂相比,膨润土有一个重要的特点,就是它具有一定的耐热能力。
只要加热温度不太高,脱除了自由水的膨润土只要加水,仍能恢复粘能力。
不同的膨润土,丧失粘结能力的温度不同。
通过一系列加热试验和差热分析实验,得知天然钠膨润土的失效温度为638℃,钙膨润土为316℃。
人工活化的钠膨润土,由于活化条件各异,准确的失效温度不详。
据日本报道的实验结果,人工活化的钠膨润土,在最初使用时,失效温度略低于天然钠膨润土;几次反复加热后,就与钙膨润土相近,其"耐用性"不佳。
(1)膨润土中水的形态活性膨润土的粘结能力,只有在加水以后才能表现出来。
膨润土失去粘结能力,也与它的脱水有关。
到目前为止,认为膨润土中的水分有三种形态。
一种是自由水,即膨润土颗粒吸附的水。
加热到100℃以上,就可脱除自由水。
脱除了自由水的膨润土,粘结能力不受影响。
第二种是牢固结合水。
将膨润土置110℃下长时间加热,可完全脱除自由水,但但不会脱除牢固结合水。
已完全脱除自由水的膨润土,再在较高的温度(如200℃,300℃)下加热仍会继续减重,说明仍有水分损失。