管桩生产工艺
管桩工艺流程
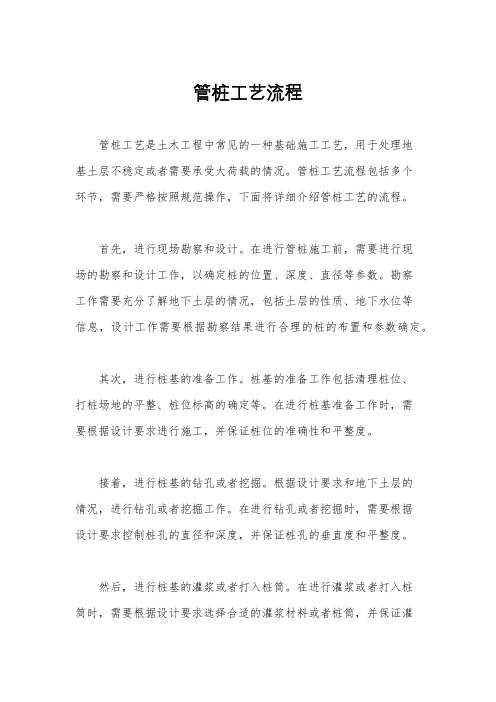
管桩工艺流程
管桩工艺是土木工程中常见的一种基础施工工艺,用于处理地
基土层不稳定或者需要承受大荷载的情况。
管桩工艺流程包括多个
环节,需要严格按照规范操作,下面将详细介绍管桩工艺的流程。
首先,进行现场勘察和设计。
在进行管桩施工前,需要进行现
场的勘察和设计工作,以确定桩的位置、深度、直径等参数。
勘察
工作需要充分了解地下土层的情况,包括土层的性质、地下水位等
信息,设计工作需要根据勘察结果进行合理的桩的布置和参数确定。
其次,进行桩基的准备工作。
桩基的准备工作包括清理桩位、
打桩场地的平整、桩位标高的确定等。
在进行桩基准备工作时,需
要根据设计要求进行施工,并保证桩位的准确性和平整度。
接着,进行桩基的钻孔或者挖掘。
根据设计要求和地下土层的
情况,进行钻孔或者挖掘工作。
在进行钻孔或者挖掘时,需要根据
设计要求控制桩孔的直径和深度,并保证桩孔的垂直度和平整度。
然后,进行桩基的灌浆或者打入桩筒。
在进行灌浆或者打入桩
筒时,需要根据设计要求选择合适的灌浆材料或者桩筒,并保证灌
浆或者打桩工艺的质量和效果。
最后,进行桩基的固结和验收。
在进行桩基的固结和验收时,
需要进行桩基的固结工作,包括灌浆固结、桩筒固结等工艺,同时
需要对桩基进行验收,确保桩基的质量和稳定性。
总的来说,管桩工艺流程包括现场勘察和设计、桩基的准备工作、桩基的钻孔或者挖掘、桩基的灌浆或者打入桩筒以及桩基的固
结和验收等环节。
在进行管桩工艺施工时,需要严格按照规范操作,确保施工质量和工程安全。
管桩车间生产工艺流程

管桩车间生产工艺流程1.桩管车间的生产工艺流程包括原材料准备、加工制造、检测和包装等环节。
The production process in the pile pipe workshop includes raw material preparation, processing, testing, and packaging.2.原材料准备阶段包括对钢材进行质量检验和筛选。
The raw material preparation stage includes quality inspection and selection of steel.3.钢材经过切割、翻边等工艺处理,进行预制成型。
Steel is precut and formed through processes such as flanging and bending.4.预制成型后,进行对接焊接工艺,使管道形成完整的结构。
After prefabrication, the pipes are welded together to form a complete structure.5.焊接完成后,进行外观检测和尺寸测量,确保产品符合要求。
After welding, visual inspection and dimension measurement are carried out to ensure the product meets requirements.6.完成检测后,进行内部防腐处理,提高产品的耐腐蚀性能。
After inspection, internal anti-corrosion treatment is carried out to improve the corrosion resistance of the product.7.经过防腐处理后,进行喷砂清理和喷涂工艺,提高产品的表面光洁度和美观度。
After anti-corrosion treatment, sandblasting and painting processes are carried out to improve the surface finish and aesthetics of the product.8.最后产品进行包装,符合国际运输要求,确保产品在运输过程中不受损坏。
管桩生产标准化工艺
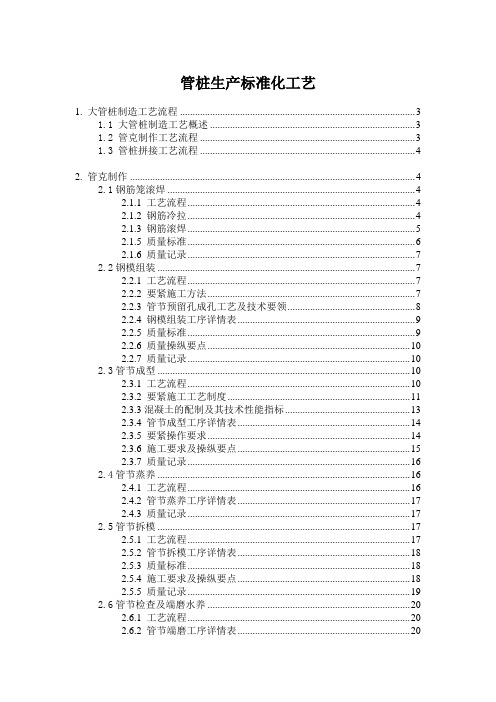
管桩生产标准化工艺1. 大管桩制造工艺流程 (3)1.1 大管桩制造工艺概述 (3)1.2 管克制作工艺流程 (3)1.3 管桩拼接工艺流程 (4)2. 管克制作 (4)2.1钢筋笼滚焊 (4)2.1.1 工艺流程 (4)2.1.2 钢筋冷拉 (4)2.1.3 钢筋滚焊 (5)2.1.5 质量标准 (6)2.1.6 质量记录 (7)2.2钢模组装 (7)2.2.1 工艺流程 (7)2.2.2 要紧施工方法 (7)2.2.3 管节预留孔成孔工艺及技术要领 (8)2.2.4 钢模组装工序详情表 (9)2.2.5 质量标准 (9)2.2.6 质量操纵要点 (10)2.2.7 质量记录 (10)2.3管节成型 (10)2.3.1 工艺流程 (10)2.3.2 要紧施工工艺制度 (11)2.3.3混凝土的配制及其技术性能指标 (13)2.3.4 管节成型工序详情表 (14)2.3.5 要紧操作要求 (14)2.3.6 施工要求及操纵要点 (15)2.3.7 质量记录 (16)2.4管节蒸养 (16)2.4.1 工艺流程 (16)2.4.2 管节蒸养工序详情表 (17)2.4.3 质量记录 (17)2.5管节拆模 (17)2.5.1 工艺流程 (17)2.5.2 管节拆模工序详情表 (18)2.5.3 质量标准 (18)2.5.4 施工要求及操纵要点 (18)2.5.5 质量记录 (19)2.6管节检查及端磨水养 (20)2.6.1 工艺流程 (20)2.6.2 管节端磨工序详情表 (20)2.6.3 质量标准 (20)2.6.4 质量操纵要点 (20)2.6.5 质量记录 (20)3. 管桩拼接 (21)3.1管节检查上线及清理 (21)3.1.1 工艺流程 (21)3.1.2 钢模组装工序详情表 (21)3.1.3 质量标准 (21)3.1.4 质量操纵要点 (22)3.1.5 质量记录 (22)3.2管桩拼接 (22)3.2.1 工艺流程 (22)3.2.2 粘结剂的配制及技术性能 (22)3.2.3管桩拼接工序详情表 (23)3.2.4 质量标准 (23)3.2.5 质量操纵要点 (24)3.2.6 质量记录 (24)3.3管桩张拉 (24)3.3.1 工艺流程 (24)3.3.2 要紧施工方法 (24)3.3.3管桩张拉工序详情表 (25)3.3.4 质量标准 (25)3.3.5 质量操纵要点 (25)3.3.6 质量记录 (26)3.4管桩灌浆 (26)3.4.1 工艺流程 (26)3.4.2 水泥灰浆的配置及其技术性能 (26)3.4.3 管桩灌浆工序详情表 (28)3.4.5 质量操纵要点 (28)3.4.6 质量记录 (28)3.5堆场放张 (28)3.5.1 工艺流程 (28)3.5.2 管桩放张堆存工序详情表 (28)3.5.3 质量标准 (29)3.5.4 质量操纵要点 (29)3.5.5 质量记录 (29)4. 质量操纵点岗位责任制 (30)1. 大管桩制造工艺流程1.1 大管桩制造工艺概述预应力混凝土大直径管桩采纳离心—振动—辊压向结合的复合法工艺成型管节,在管节拼接端面涂刷粘结剂,管节的预留孔内穿入高强钢绞线(或高强钢丝束),然后施加一定的预压应力,进行压力灌注水泥灰浆自锚,将预制的管节拼接成一定长度的管桩。
管桩生产工艺

无机09-3班侯倩 0904230321管桩的生产工艺流程清模,装模1管模拆开后,模边止口用钢铲将黏附的水泥渣及草绳残留物铲掉,再用竹扫打扫干净,然后在模边刷上一层机油,但不可过多,否则要用抹布抹掉多余的。
2脱模剂配制时,不可过稀或过浓。
喷洒时不得过多或过少,需均匀覆盖。
底模模底不得有多余的脱模剂积存,并且在喷洒脱模剂时严禁将脱模剂喷洒到笼筋上。
3张拉头尾板应逐个清理干净,并在解除部位涂上柴油或机油。
4张拉锚固螺杆,螺环,要逐个检查,清理螺纹内的杂物并涂上润滑油,可正常转动时才能继续使用,如有损坏应及时维修好。
5放置过久的磨具再使用时,如果生锈要采取除锈措施后才能使用。
6笼筋入模时,应防止松散,抱箍板碰凹。
装配时,主筋镦头一定要完全进入到端板的沉头孔内。
装完张拉头板后,重新检查螺钉是不是全部上紧,以保持合力一致,防止桩端倾斜和保证安全。
7装配后进行抱箍板整形,主筋平直度纠正,松散的螺旋筋绑扎,凹陷的需要整形平整,合格后才能吊往台前布料。
砼布料:1、布料前的检查:a)笼筋顺直,与管模平行不扭曲,螺旋筋无松散,模尾板要紧贴管模。
b)螺丝是否齐全上紧,抱箍板有无凹陷等现象。
c)管模螺栓齐全,模内无杂物,模边是否清理干净。
2、布料前先按要求放好胶皮挡板,减少砼料的掉落和确保套箍的清洁度,管模规格必须与搅拌投料量相匹配,料在管模移动中均匀布满。
3、布料时应严格按照“先中间—两头—中间”的布料要求布料,严禁从头到尾直接布料。
如遇需要布二槽料的的管模,则第一槽料一定要均匀布在管模内,第二槽料加在上面以使两槽料能混合均匀。
4、布好料以后要有指定专人负责两头的插料,要求整堆撬入较饱满,不得过分插实,使砂石分离,中间砼料不得低于管模(两头砼料不能过高),掉下的料要及时铲起,但是不得放入头尾一米以内;但沾水粘灰,粘油及零散的料不得再用,端头撬入料时,注意不得将螺旋筋撬散。
合模1、合模前用钢铲将料铲起堆好,清理干净两侧模边和套箍表面,放好挡浆草绳。
长管节大管桩的管节生产工艺

1 5 m 厚 滑坡 形成 的乱 石层 , 锤击 数 达 3 1 0 0多 击 , 贯
入 度≤ 3 mm 工况 下锤 击 数 超 过 1 0 0 0击 , 未 发 现桩 身纵 向裂缝 和桩 顶破 碎现 象 。
华 润浙 江 苍 南 电 厂 卸 煤 码 头 项 目共 沉  ̄  ̄ 1 2 0 0
天设 专人 进行 喷 淋养 护 至 少 4遍 , 管 节 混 凝 土强 度
养 护达 到设计 值 的 8 O 时, 即可 吊运 至 拼接 区 。按
和计算 分 析等 手段 , 总结 开发 生产 实践 经验 , 并结 合
港 口工 程 特 点 和 发 展 方 向 , 继 续深 入研 究[ 4 ] , 这 样 才 能将 之更 好 的进行 推广 和完 善 。 浙 江省 交 通 运输 厅 工 程质 量 监 督 局 、 宁 波 海 港 工程 有 限公 司 、 浙 江省交 通 规划 设 计 研 究 院于 2 0 1 2 年开 始着 手修 订《 长 管 节 后 张 法 预 应 力 混 凝 土 大 管 桩设 计 与施工 规程 》 , 规 程 主 要 包 括 长 管 节 后 张 法 预
[ - 2 3 阮起楠. 预应力混凝土管桩[ M] . 北京 : 中 国建 材 工 业 出 版 社 ,
① 混凝 土 强 度 应 达 到 设 计 值 的 6 O 时 才 可 拆 钢模 , 拆模 顺序 为 : 放 松拉 杆螺 栓一 卸 除端盖 一抽 拔
拉杆 ( 带橡 胶套 管 ) 一 卸 除 上 半 部 管 节 钢 模 一 从 钢 模
内卸 出管 节 。 ②管 节混凝 土 强度养 护达 到设 计 值 的 1 O 时,
行 系 统 解 决 。本 文 所 描 述 的仅 是 桩 在 生 产 层 面 的 经 验总 结 , 其 它方 面 的也必 须通 过深 入调 查 、 试 验 研 究
混凝土管桩制造工艺流程
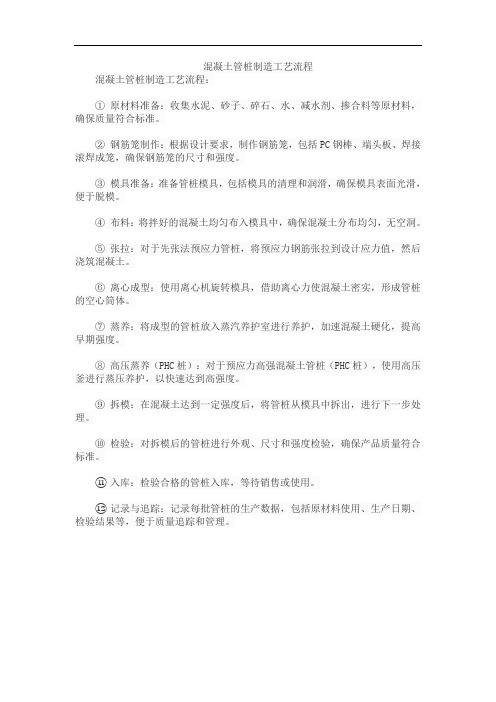
混凝土管桩制造工艺流程
混凝土管桩制造工艺流程:
①原材料准备:收集水泥、砂子、碎石、水、减水剂、掺合料等原材料,确保质量符合标准。
②钢筋笼制作:根据设计要求,制作钢筋笼,包括PC钢棒、端头板、焊接滚焊成笼,确保钢筋笼的尺寸和强度。
③模具准备:准备管桩模具,包括模具的清理和润滑,确保模具表面光滑,便于脱模。
④布料:将拌好的混凝土均匀布入模具中,确保混凝土分布均匀,无空洞。
⑤张拉:对于先张法预应力管桩,将预应力钢筋张拉到设计应力值,然后浇筑混凝土。
⑥离心成型:使用离心机旋转模具,借助离心力使混凝土密实,形成管桩的空心筒体。
⑦蒸养:将成型的管桩放入蒸汽养护室进行养护,加速混凝土硬化,提高早期强度。
⑧高压蒸养(PHC桩):对于预应力高强混凝土管桩(PHC桩),使用高压釜进行蒸压养护,以快速达到高强度。
⑨拆模:在混凝土达到一定强度后,将管桩从模具中拆出,进行下一步处理。
⑩检验:对拆模后的管桩进行外观、尺寸和强度检验,确保产品质量符合标准。
⑪入库:检验合格的管桩入库,等待销售或使用。
⑫记录与追踪:记录每批管桩的生产数据,包括原材料使用、生产日期、检验结果等,便于质量追踪和管理。
管桩的制作工艺与流程(实用)

先张法预应力混凝土离心方桩的制作工艺建筑基础工程中预制混凝土桩桩体截面形状主要有圆形截面的预制混凝土管桩和正方形或长方形截面的预制混凝土方桩。
上世纪90年代以来,随着预制混凝土管桩的标准化和生产及施工技术的不断发展,基础工程对管桩产品已经得到广泛的认可,在实际工程中管桩产品有其显著的优越性,但在以下几个方面表现不足:①管桩为外圆形结构,运输中不易帮扎、固定;②由于管桩桩身存在一定的椭圆度,采用抱压施工时易出现桩身抱碎事故;③管桩在软土地基施工后,在基坑开挖时,容易出现桩位倾斜;④管桩基础的承台较方桩大,基础成本较高等。
预制混凝土方桩除港工基础采用先张法工艺的预应力混凝土空心方桩(内腔主要采用预置橡胶充气方式,有正方形或长方形两种截面形式)外,大多数基础工程主要采用手工作业的非预应力、振动成型工艺居多,混凝土采用自然养护,结构多为实心的正方形截面。
该预制方桩主要存在下列缺陷:①生产效率低,生产周期长;②产品品质不稳定,硬化混凝土结构截面中含气孔较多;③混凝土强度低,桩身承载力未能充分发挥;④混凝土自然养护时间长,生产占地面积大。
自2003年至今,武汉金石工程技术有限公司、云南中技管桩有限公司、上海中技桩业有限公司等单位的技术人员将先张法预应力混凝土管桩生产工艺应用于预制混凝土方桩的生产,即利用离心成型工艺,研究开发了先张法预应力混凝土离心方桩(以下简称离心方桩),现将该产品的生产工艺、产品类型及技术要求等做一一说明。
生产工艺离心方桩生产工艺与现有的管桩生产工艺基本相同,主要不同点:①采用与离心方桩钢模模具相配套的近似方形的钢筋骨架;②成型用的模具截面呈正方形结构。
具体生产工艺如下:1.混凝土原材料的计量、搅拌。
根据设计好的配合比,将砂、石、水泥、水、外加剂和掺合料等经精确计量,用混凝土强制式搅拌机制成3cm~5cm的低坍落度的新拌混凝土,设计要求混凝土强度等级不低于C60或C80。
2.离心方桩端板制作。
管桩生产工艺流程

管桩生产工艺流程管桩生产工艺流程是指在管桩制造过程中的一系列工艺步骤,包括材料准备、制管、焊接、校直、探伤、腐蚀防护等。
下面将详细介绍管桩生产工艺流程。
一、材料准备1. 首先选择合适的钢板,通常采用低碳结构钢、中碳结构钢或低合金高强度结构钢。
2. 根据设计要求,将钢板按照规定的长度和宽度进行切割。
二、制管1. 将切割好的钢板弯曲成圆管形,并通过自动焊机进行连续焊接。
2. 通过高频感应加热的方法将边缘焊缝加热至焊接温度,然后通过压力辊将焊缝挤压成一致的形状。
3. 经过冷却和探伤检验后,将制成的管材进行编堆、整理和标记。
三、焊接1. 结构管焊接工艺根据设计要求,通过准备焊材和焊接设备,将钢板按照规定的尺寸进行焊接。
2. 进行端部焊接后,采取连续焊接的方式将管材焊接成整体。
3. 检验焊缝的质量,对不合格的焊接缝进行修补或重新焊接。
四、校直1. 通过校直机将焊接好的管材进行校直,使其达到规定的矫正精度。
2. 首先将管材进入校直机的传动装置,然后通过辊子的旋转运动将管材逐步校直。
五、探伤1. 采用超声波或射线等无损检测方法对管材进行探伤。
2. 对管材进行找焊缺陷、破裂、腐蚀等缺陷检测,并记录检测结果。
3. 根据检测结果,对有缺陷的管材进行修复或淘汰。
六、腐蚀防护1. 采用喷砂或喷丸等方法对管材表面进行处理,去除锈蚀和氧化物。
2. 在管材表面涂刷防腐涂料或进行镀锌等防腐处理,以增强其抗腐蚀能力。
以上就是管桩生产工艺流程的简要介绍,每个环节都需要严格控制工艺参数和质量要求,以确保生产出符合设计要求和使用要求的管桩产品。
- 1、下载文档前请自行甄别文档内容的完整性,平台不提供额外的编辑、内容补充、找答案等附加服务。
- 2、"仅部分预览"的文档,不可在线预览部分如存在完整性等问题,可反馈申请退款(可完整预览的文档不适用该条件!)。
- 3、如文档侵犯您的权益,请联系客服反馈,我们会尽快为您处理(人工客服工作时间:9:00-18:30)。
管桩生产工艺一、钢筋笼制作:由主钢筋定长切断、镦头、滚焊(或绑扎)钢筋笼三道工序组成。
主筋采用SBPDL-1275/1420预应力砼用钢筋(PC钢棒)。
其性能如表-1:表-1实际采用时,可根据具体情况选用。
1、主钢筋定长切断:A、主筋定尺切断长度:不同长度管桩的主筋定尺切断长度应符合表-2要求:表-2B、技术及操作要求:a、主筋进厂必须随交合格证,并经复验合格,方可使用。
c、严格按生产计划通知单所要求的钢筋直径、材质、数量、切断长度等下料。
d、下料长度偏差不得大于定尺长度1/5000,超差的必须分组组合使用。
e、不同技术性能的钢筋严禁混用。
f、切口平整,与中线垂直,无飞边、切斜现象。
2、镦头A、镦头几何尺寸按表-3要求:表-3B、PC钢棒采用热镦。
应根据线径及材质,调校加热时间、电流和镦头行程,气压应大于0.55MPa,使镦头形状和尺寸符合要求。
C、技术操作要求:a、出现单边镦、偏头、歪头、爆裂、尺寸超差等不得使用。
b、镦头强度应不低于母材的90% ,即不低于1280MPa .c、镦头前应使用废料短钢棒进行预试,一般锤头和夹具距离19-21mm。
正常后开始成品生产。
3、钢筋笼成型:A、对主筋为PC钢棒的钢筋笼,应滚焊成型。
成型的钢筋笼均应符合管桩设计要求。
B、技术操作要求:a、螺旋筋应采用乙级冷拉低碳钢丝,表面不得有油污、锈蚀;b、螺旋筋螺距:两端1.5m为40-60mm,中间间距为100 mm,两端密绕3-4圈并收头,密绕圈距端板应不大于50 mm。
c、骨架成型后,应符合下列要求:(1)预应力主筋间距偏差≯±5mm;(2)螺旋筋螺距偏差≯±10mm ;(3)成型后,主筋同心圆的直径应符合设计要求,偏差≯±2mm。
d、要防止钢筋笼主筋扭斜,做到机头穿筋孔和牵引台车主筋固定孔方位一致。
e、螺旋筋焊点应牢固,脱焊点要绑扎。
焊点深度应小于1mm,以保护主筋(焊点深度太深主筋易拉断)。
C、钢筋笼堆放:a、不同规格滚焊钢筋应分别整齐堆放,层数为:Φ400,小于4层,Φ500—600,小于3层。
b、钢筋笼搬运应多点悬吊,不得在地面拖拉和从高处抛下,以免骨架变形,焊点脱落。
c、锈蚀、坍垮、油污的骨架,不得使用。
一、钢筋笼装配和入模:1、桩端板:A、端板、裙板组焊件,应按图纸要求检验合格,方可使用。
端板进厂卸车应有防止使端极及裙板变形的措施,严禁野蛮卸车。
B、端板及裙板变形应修整,特别裙口直径应大于桩径3 mm,避免漏浆。
2、装配:A、张拉板使用前要逐个清理干净,并在接触部位涂上废机油。
B、张拉螺栓使用前要逐根检查,螺纹磨损、损伤的不可使用,装配时螺纹部分要涂废机油,螺杆长度应要拧紧后长出1—2扣;张拉螺栓要对角均匀拧紧。
(注意:应先用手将张拉螺丝转三圈,然后用风炮打紧)C、桩端板、张拉板、钢筋笼组装位置要正确,不偏心,镦头不得突出端板平面,否则要磨平;为防止裙板变形,组装时端板下宜放垫板(也可在钢模内组装)。
组装后应检查模内张拉板及固定端张拉板凸台外园与端板外园是否偏心,否则应调整,以防合模不好,造成模口漏浆。
3、钢筋笼入模:A、钢筋笼入模前应作以下检查:a、钢模是否完好并清理干净。
b、脱模油应涂刷均匀,模底无沉积并累风干。
脱模油与水配比按要求调配。
B、操作要求:a、钢筋笼入模要多点悬吊、轻吊轻放。
b、入模的钢筋笼主筋不得扭斜,在两端检查同一根主筋距模口线的距离,其偏差小于10 mm。
c、检查端板裙口与钢模内壁不得有缝隙或凹陷,否则应修整,以免漏浆。
d、螺旋筋如有脱焊,应绑扎。
二、砼的制备和搅拌:1、制备:A、原材料的检验和复验:a、砂、石子应对级配、粒经、含泥量等检验,合格方可使用。
b、水泥按批次取样复验。
B、原材料的称量:a、搅拌站要按配料单正确操作,保证配料精度其允许偏差如表-4:表-4b、要保证称量精度,定期校正和保养,发现计时漂移不准,必须立即校称,不得继续生产。
c、砂、石子自然含水率,在实际工作中,应积累经验,即时调整砂、石子配料量,以保证配合比和桩壁厚。
试验室应对砂、石子自然含水率测定,出具当班配合比通知单,遇原材料变化即时调整。
如遇大雨导致含水率不易控制,应暂停生产。
d、砼坍落度应控制在5±2mm,夏季取大值。
e、冬季如遇砂、石料结冰,不得上料。
f、砼用水、冬季应不低于5度,否则应加热。
g、配料站砂、石料不得混仓。
h、不同规格管桩单根搅拌次数及每次配料量应合理确定,应做到在不超过搅拌机额定容量的前提下搅拌次数最少。
i、原材料变化应做试配并调整配合比。
砼配合比不经批准,不得随意变更。
2、砼的搅拌:A、搅拌制度:根据搅拌站结构,采用一次投料法。
搅拌时间定为90-120,以搅拌均匀为原则,减水剂在搅拌60秒后投入。
B、应做到先开机再投料,无特殊情况,禁止中间停机,否则要将料排出搅拌槽后才可开机。
C、出料的砼坍落度应控制在5±2cm。
D、班前应湿润搅拌槽,班后或中间停机时间长,均应将搅拌槽冲洗干净。
三、砼的喂料及合模:1、喂料:A、喂料前应检查钢模、钢筋笼、张拉板及张拉装置是否组装正确,并注意钢模温度不大于45度。
B、喂料顺序:先喂中间、后喂两端,两端1.5m范围内料保证足够饱满。
同时注意中间布料均匀。
C、喂料前应检查视砼坍落度,以5±2cm为宜,小于1㎝或大于12㎝的砼不可入模。
D、喂料操作中,要特别注意砼坍落度损失,尽量缩短作业时间,特别在夏季。
E、撒落的砼,不可再入模使用。
2、合模:A、合模前应清理模口结合面及密封槽内的杂物。
B、合模时,严禁人体各部位伸入钢模,上模要对准轻放。
C、合模螺丝应两侧同步均匀拧紧,不可遗漏。
合模丝未全部拧紧,不得张拉。
四、预应力张拉:1、预应力钢筋张拉控制应力及预应拉力:各种规格预应力筋的张拉控制应力及预应拉力,根据有关规定,见表-5:表-52、管桩张拉控制参数各种规格管桩张拉控制拉力、张拉长度及油压表压值,应根据《管桩张拉控制参数表》要求进行。
3、操作要求:A、必须按要求的表压值及拉伸量操作,不得随意变更。
具体操作时应以应控制(表压值)为主,应变控制(拉伸量)为辅,发现张拉异常,应即时检查汇报。
B、张拉操作时,应均匀加荷,达表压值时应即时停止加荷,并迅速拧紧螺母,再进行减压,以免回缩。
C、张拉千斤顶联接装置装配时,螺纹啮合长度,必须达到要求。
D、应看到中心张拉方式存在当张拉局部阻力不均或偏大时,易引起桩端板倾斜。
为此,除认真做好各工序操作外,张拉操作时,如必要可采用二次张拉工艺,即一次张拉至要求值,立即排油回缩到60—70%表压值,再二次加压至要求值,可改善桩端板倾斜缺陷。
E、张拉操作时,发生断筋、镦头拉脱、表压值及拉伸量失常等异常情况,应立即汇报处理。
F、张拉操作时,桩轴线(特别是张拉端)禁止站人,同时旋锁紧螺母人员的手不要过早插入锁紧螺母手孔,以防张拉中发生断筋、断张拉杆、连接件破损等异常情况时,机具等弹出伤人。
G、张拉装置定期标定。
五、离心成型:1、离心参数的选择:要取得高强密实的砼,影响因素诸多,结合原材料品质、桩径、壁厚等因素,应根据《管桩离心制度》规定参数进行离心,生产过程中,尚应结合实际情况,必要时再作适当调整。
2、操作要求:A、严格执行离心制度和设备操作要求,离心机托轮面不得有油污。
B、钢模吊运要轻吊轻放,吊点要适当,距两端2—2.5m左右,成型后不允许二次吊运和剧烈振动,入养护池应跑轮压跑轮不错位。
C、要注意砼初凝时间,从搅拌至成型结束,应在45分钟内完成。
同时,禁止前段工序完成较长时间等待离心现象。
六、常压蒸养1、养护制度《管桩常压养护制度》进行。
2、静放时间应不小于1h。
3、升温梯度为20℃/h,应注意季节变化、桩体温度、环境温差等情况调节升温时间。
4、降温剃度不得大于30℃/h,出池桩身温度与环境温差应小于40℃。
A、恒温温度当采用硅酸盐水泥和普硅水泥时为75℃;掺用矿碴或其它辅助胶凝材料时为85℃。
B、做到蒸养池内温度均匀,池盖要加湿沙密封。
池内不得积水,更不可浸桩。
C、严格控制蒸养制度,如实作出记录,常压蒸养后的桩身砼强度应大于40Mpa。
七、二次养护(蒸压养护或洒水养护):常压蒸养后并脱模的桩,桩身砼尚未达到设计强度,还要根据工艺技术要求,继续做二次养护:1、对PC型桩,实施洒水养护,即在桩身冷却后洒水养护7天(保持桩身湿润),再自然养护7天,总养护期14天,并经检验合格,方可出厂。
2、对PHC型桩,实施蒸压养护,应按《管桩高压养护制度》进行:A、常压蒸养护脱模后,应尽快压蒸,以节省热能。
B、按养护制度操作,与锅炉司炉工密切配合,多釜运行时应妥善安排,避免蒸汽母管汽压过大波动。
C、开釜门应待釜内汽压充分降至零位后进行,降压速度不宜过大。
D、管桩降温出釜应视气温、温差及气候条件等,必要时应延长通风降温时间,一般温差不宜大于60—70度,特别是冬季。
E、釜内不应积水。
F、釜内废汽应尽量综合利用,以节省热能。
八、脱模、清模:1、脱模时,因桩身砼强度尚未达到设计强度,故起吊装车要轻吊轻放,避免碰撞。
翻模时桩下应按两支点要求垫缓冲材料(如废轮胎等)。
2、拆模时,应先拆除中心张拉杆锁紧螺母,张拉螺丝要对称拆除,合模螺丝要两侧同时拧松。
3、脱模后,质检人员应逐根对桩进行外观和尺寸检查,对存在缺陷按规定作修补处理,并检查合格。
4、脱模后,钢模应清理干净,并均匀涂刷脱模油。
脱模油浓度要按规定调制,不可过浓和过稀。
5、产品标志在桩端1—1.5米处,脱模后进行。
九、产品检验:分桩身砼强度、外观质量、尺寸偏差及力学性能等检验环节。
在桩身砼强度和力学性能检验合格的基础上,再按外观质量及尺寸偏差检验结果,评定其产品相应等级(优等、一等、合格三个等级)。
1、砼抗压强度:每100盘或一个班当班拌制的同配比砼随机取样,制作三组试块,与管桩同条件养护,分别检验脱模、28d及出厂强度。
脱模强度应大于40Mpa、28d强度应大于60 MPa(PC.PTC桩)及80 MPa(PHC桩)。
2、外观质量及尺寸偏差:在脱模后进行,逐根检验,待产品质量稳定后,再实施批量抽检。
3、力学性能检验:下列情况之一时,应进行检验:A、同一品种、规格、型号的管桩连续生产30000 m或达4个月时:B、当材料、工艺有较大改变时;C、合同要求时。
十一、产品堆放和发运:1、产品桩要按质量等级、规格、长度等分类堆放。
堆放层数不宜超过表-6规定:表-62、堆放场地应坚实平整,上面发两支点支承布置,下层桩下各支点垫1.5m宽,0.3m高的细石粉,并在同一水平面上。
3、多层堆放,最外侧桩应设防滑落设施。
4、产品装卸应轻吊轻放,严禁抛掷、碰撞、滚落。
5、不合格产品或养护期不到的产品,不经批准,不得出厂。