塑胶模具设计规范(参考Word)
塑胶件设计规范范文
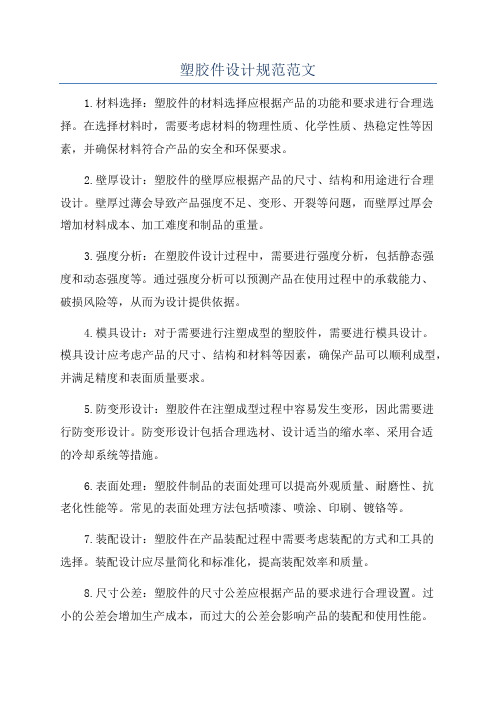
塑胶件设计规范范文1.材料选择:塑胶件的材料选择应根据产品的功能和要求进行合理选择。
在选择材料时,需要考虑材料的物理性质、化学性质、热稳定性等因素,并确保材料符合产品的安全和环保要求。
2.壁厚设计:塑胶件的壁厚应根据产品的尺寸、结构和用途进行合理设计。
壁厚过薄会导致产品强度不足、变形、开裂等问题,而壁厚过厚会增加材料成本、加工难度和制品的重量。
3.强度分析:在塑胶件设计过程中,需要进行强度分析,包括静态强度和动态强度等。
通过强度分析可以预测产品在使用过程中的承载能力、破损风险等,从而为设计提供依据。
4.模具设计:对于需要进行注塑成型的塑胶件,需要进行模具设计。
模具设计应考虑产品的尺寸、结构和材料等因素,确保产品可以顺利成型,并满足精度和表面质量要求。
5.防变形设计:塑胶件在注塑成型过程中容易发生变形,因此需要进行防变形设计。
防变形设计包括合理选材、设计适当的缩水率、采用合适的冷却系统等措施。
6.表面处理:塑胶件制品的表面处理可以提高外观质量、耐磨性、抗老化性能等。
常见的表面处理方法包括喷漆、喷涂、印刷、镀铬等。
7.装配设计:塑胶件在产品装配过程中需要考虑装配的方式和工具的选择。
装配设计应尽量简化和标准化,提高装配效率和质量。
8.尺寸公差:塑胶件的尺寸公差应根据产品的要求进行合理设置。
过小的公差会增加生产成本,而过大的公差会影响产品的装配和使用性能。
9.耐用性设计:塑胶件在使用过程中需要具有一定的耐用性。
耐用性设计包括选择合适的材料、优化结构、进行耐久性测试等。
10.产品标识:塑胶件在制造过程中需要进行产品标识,包括产品型号、批次号、生产厂家等信息。
产品标识有助于产品追溯和质量控制。
请注意,以上只是一些常见的塑胶件设计规范,具体的设计规范还需根据具体产品和行业的要求来确定。
在进行塑胶件设计时,还需充分考虑产品的使用环境、工艺要求和成本等因素,确保产品的质量和可生产性。
塑胶模具制作标准
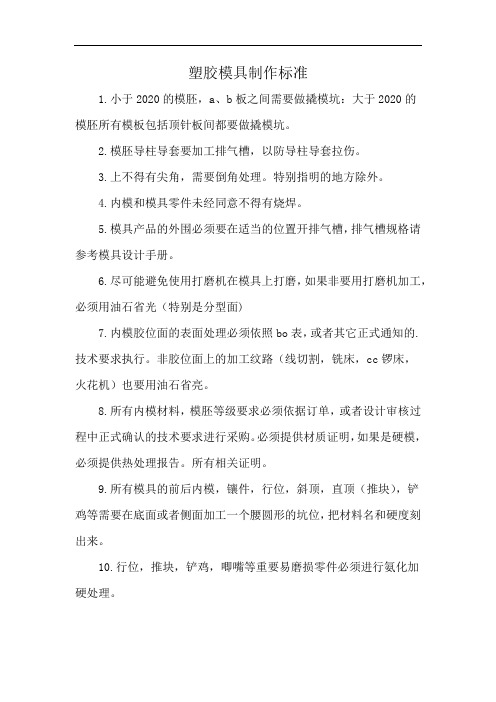
塑胶模具制作标准
1.小于2020的模胚,a、b板之间需要做撬模坑:大于2020的
模胚所有模板包括顶针板间都要做撬模坑。
2.模胚导柱导套要加工排气槽,以防导柱导套拉伤。
3.上不得有尖角,需要倒角处理。
特别指明的地方除外。
4.内模和模具零件未经同意不得有烧焊。
5.模具产品的外围必须要在适当的位置开排气槽,排气槽规格请参考模具设计手册。
6.尽可能避免使用打磨机在模具上打磨,如果非要用打磨机加工,必须用油石省光(特别是分型面)
7.内模胶位面的表面处理必须依照bo表,或者其它正式通知的.技术要求执行。
非胶位面上的加工纹路(线切割,铣床,cc锣床,
火花机)也要用油石省亮。
8.所有内模材料,模胚等级要求必须依据订单,或者设计审核过程中正式确认的技术要求进行采购。
必须提供材质证明,如果是硬模,必须提供热处理报告。
所有相关证明。
9.所有模具的前后内模,镶件,行位,斜顶,直顶(推块),铲
鸡等需要在底面或者侧面加工一个腰圆形的坑位,把材料名和硬度刻出来。
10.行位,推块,铲鸡,唧嘴等重要易磨损零件必须进行氨化加
硬处理。
注塑模具设计规范
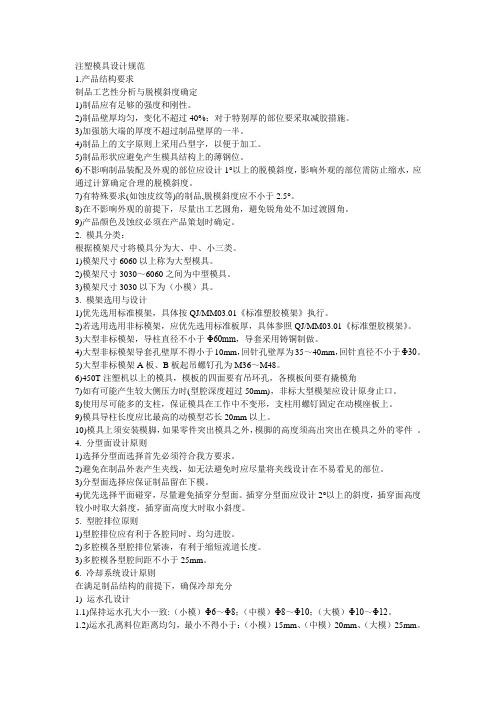
注塑模具设计规范1.产品结构要求制品工艺性分析与脱模斜度确定1)制品应有足够的强度和刚性。
2)制品壁厚均匀,变化不超过40%;对于特别厚的部位要采取减胶措施。
3)加强筋大端的厚度不超过制品壁厚的一半。
4)制品上的文字原则上采用凸型字,以便于加工。
5)制品形状应避免产生模具结构上的薄钢位。
6)不影响制品装配及外观的部位应设计1°以上的脱模斜度,影响外观的部位需防止缩水,应通过计算确定合理的脱模斜度。
7)有特殊要求(如蚀皮纹等)的制品,脱模斜度应不小于2.5°。
8)在不影响外观的前提下,尽量出工艺圆角,避免锐角处不加过渡圆角。
9)产品颜色及蚀纹必须在产品策划时确定。
2. 模具分类:根据模架尺寸将模具分为大、中、小三类。
1)模架尺寸6060以上称为大型模具。
2)模架尺寸3030~6060之间为中型模具。
3)模架尺寸3030以下为(小模)具。
3. 模架选用与设计1)优先选用标准模架,具体按QJ/MM03.01《标准塑胶模架》执行。
2)若选用选用非标模架,应优先选用标准板厚,具体参照QJ/MM03.01《标准塑胶模架》。
3)大型非标模架,导柱直径不小于Φ60mm,导套采用铸铜制做。
4)大型非标模架导套孔壁厚不得小于10mm,回针孔壁厚为35~40mm,回针直径不小于Φ30。
5)大型非标模架A板、B板起吊螺钉孔为M36~M48。
6)450T注塑机以上的模具,模板的四面要有吊环孔,各模板间要有撬模角7)如有可能产生较大侧压力时(型腔深度超过50mm),非标大型模架应设计原身止口。
8)使用尽可能多的支柱,保证模具在工作中不变形,支柱用螺钉固定在动模座板上。
9)模具导柱长度应比最高的动模型芯长20mm以上。
10)模具上须安装模脚,如果零件突出模具之外,模脚的高度须高出突出在模具之外的零件。
4. 分型面设计原则1)选择分型面选择首先必须符合我方要求。
2)避免在制品外表产生夹线,如无法避免时应尽量将夹线设计在不易看见的部位。
塑胶模具设计手册
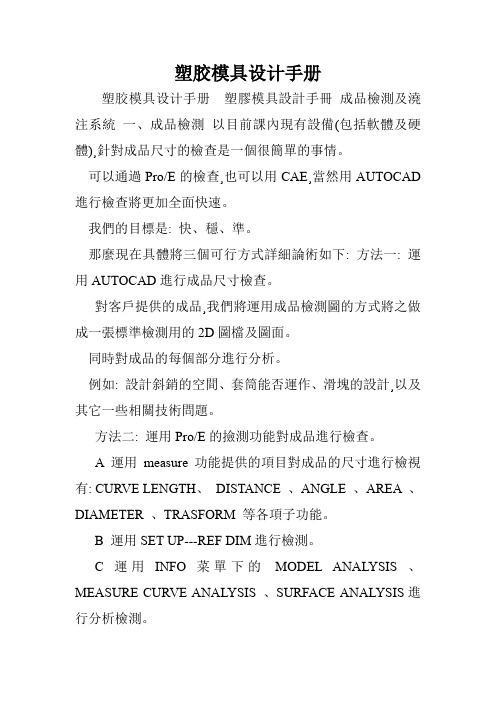
塑胶模具设计手册塑胶模具设计手册塑膠模具設計手冊成品檢測及澆注系統一、成品檢測以目前課內現有設備(包括軟體及硬體)¸針對成品尺寸的檢查是一個很簡單的事情。
可以通過Pro/E的檢查¸也可以用CAE¸當然用AUTOCAD 進行檢查將更加全面快速。
我們的目標是: 快、穩、準。
那麼現在具體將三個可行方式詳細論術如下: 方法一: 運用AUTOCAD進行成品尺寸檢查。
對客戶提供的成品¸我們將運用成品檢測圖的方式將之做成一張標準檢測用的2D圖檔及圖面。
同時對成品的每個部分進行分析。
例如: 設計斜銷的空間、套筒能否運作、滑塊的設計¸以及其它一些相關技術問題。
方法二: 運用Pro/E的撿測功能對成品進行檢查。
A運用measure功能提供的項目對成品的尺寸進行檢視有: CURVE LENGTH、DISTANCE 、ANGLE 、AREA 、DIAMETER 、TRASFORM 等各項子功能。
B 運用SET UP---REF DIM進行檢測。
C 運用INFO菜單下的MODEL ANALYSIS 、MEASURE CURVE ANALYSIS 、SURFACE ANALYSIS進行分析檢測。
方法三:運用CAE功能對成品進行檢測。
二、重量材質部分: 我們知道運用Pro/E的工程計算的功能可以很清楚地計算出成品的體積、重量。
我們運用CAE提供的資料庫將常用塑膠材料的特性進行匯編¸利用方便的塑膠特性選擇注塑成型機的大小。
三、投影面積的大小: 投影面積的大小也可以通過Pro/E 計算¸當然CAE的計算也是可以完成的。
只不過是CAE中投影面積的計算費時太長。
這不是方法上的問題¸而是技巧性的問題。
四、模流分析的結果。
塑膠材料的特性及進膠方式。
一些常見的高份子材料列如下表: 結晶性非結晶性PP 聚丙烯PS(ATACTIC)聚苯乙烯HDPE高密度聚乙烯PV AC 聚酯酸乙烯LDPE低高密度聚乙烯PMMA聚甲基丙烯酸甲酯PA(NYLON) EV A乙烯--醋酸乙烯共聚合物POM聚縮醛A V PTFE EV PEO CHLORINATED PE氯化聚乙烯PETP(PET)聚對苯二甲二乙酯ABS HIPS PPO 賽璐璐(cellulose)纖維素塑膠PC 聚碳酸酯PBT 聚對丁烯二甲二乙酯對一些常見的¸我們公司及客戶們經常使用的塑膠特性做一些簡單的介紹: 一、PC塑料(POLYCARBONATE): PC 兼具有耐熱性、耐沖擊性和透明性。
塑胶模具设计规范
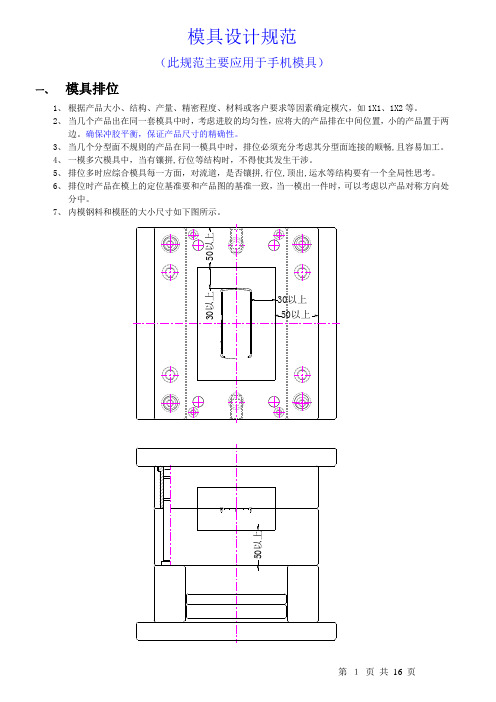
模具设计规范(此规范主要应用于手机模具)一、模具排位1、根据产品大小、结构、产量、精密程度、材料或客户要求等因素确定模穴,如1X1、1X2等。
2、当几个产品出在同一套模具中时,考虑进胶的均匀性,应将大的产品排在中间位置,小的产品置于两边。
确保冲胶平衡,保证产品尺寸的精确性。
3、当几个分型面不规则的产品在同一模具中时,排位必须充分考虑其分型面连接的顺畅,且容易加工。
4、一模多穴模具中,当有镶拼,行位等结构时,不得使其发生干涉。
5、排位多时应综合模具每一方面,对流道,是否镶拼,行位,顶出,运水等结构要有一个全局性思考。
6、排位时产品在模上的定位基准要和产品图的基准一致,当一模出一件时,可以考虑以产品对称方向处分中。
7、内模钢料和模胚的大小尺寸如下图所示。
8.产品大小和胶位厚度有较大相差时尽量不要出在同一套模具中。
9.模具方铁高度尽量订做标准高度。
10.模胚型号和中托司使用情况一定要写清楚(细水口需注明SP长度)11.必要时需注明模胚吊模孔移位情况12.考虑需不需开精框及内模料材料和规格(确定后模要不要镶大呵,如需要则一起订料,此为粗料.)二、模具系统设计一)、行位系统当塑胶产品确定前后模开模方向后,有下列情况时一般会采用行位或斜顶等结构:1)、相对出模方向塑胶产品上有倒扣或零度面;2)、产品的出模斜度不够蚀纹的角度;3)、保证特殊的外观面不能有夹线。
1、后模行位:1)、后模行位统一做镶件压块,行位压块用螺丝固定,行位压块材料为油钢淬火至HRC48-52°。
2)、所有与行位相对运动的零部件的滑动面(包括行位底耐磨片,压条,铲基斜面)须锣(磨)油坑,油坑可为平行四边行、V形或圆环形。
3)、行位铲机钢材整体采用738H,在铲机斜面上镶耐磨片,耐磨片可突出斜面0.5mm,耐磨片厚度为6mm(如下图),材料为油钢,淬硬至HRC48-52°。
康铨公司的铲基采用国产S136淬硬至HRC46-50°。
塑胶件设计规范

1. 目的:制订塑胶件设计规范,以利所有RD及PE人员在作塑胶件设计时能有所依循。
2.范围:本公司所有塑胶件的设计。
3.权责:.:RD或PE:图面的绘制。
.:模具课或供应商:塑胶模具的制作。
.:成型课:产品射出成型.4.定义:无。
5.作业内容:.产品材质的选用.根据不同的产品选用不同的材质.我司一般所用的塑胶料材质分为以下几类:5.1.1PC料其组成成为聚碳酸酯.材料特性为耐高温、耐腐蚀、耐磨性.尺寸稳定性高.且具有一定的刚性及韧性.其熔融状态下流动性较差.根据防火等级不一样又可分为PC94-V0(公司所用P4 478塑胶扣具旋转把手就选用此料)、PC94-V2(一般COVER与RM均选用此料).PC94-V0的防火等级要高於PC94-V2.另PC料可以用玻璃纤维来增强其刚性和力学强度.以达到受一定的压力而不变形.根据加玻纤的百分比不一样可以分PC+10%GF、PC+20%GF(P4塑胶扣具把手与主体选用料).PC料在设计时的肉厚最佳范围在~之间.PA66(俗称尼龙)其组成成分为聚胺.材料特性为具有良好的电气性能、热性能及力学综合性能,其力学强度随温度而异.在熔融状态下有很高的流动性.吸水性大.(与RM相配的黑白小豆豆选用料) .结构的设计.COVER结构设计所依规范.a.与风扇配合的螺丝孔中心距离.五公分的为40mm,六公分为50mm,七公分为,八公分为,且孔距公差要控制在±以内.b.Cover中间方孔要做到至少与风扇内框即出风口一样大,使cover不能挡住风扇风量.模具的设计模具设计首先根据产品的大小、材质、注塑机的规格决定模具的模穴数及模架的规格.(一般的模架的规格不能超过480*450MM)根据图纸的要求进行模具的设计(包括重点尺寸的控制、流道的设计、浇口的设计、顶针位置的设计以及脱模角度的控制等.设计时尽量要求好成型、好脱模、注塑时间短.根据所设计的模具在电脑上用Pro-E进行模流分析,看是否有注不满,有气泡等不良现象.模具设计的注意事项A.要考虑料流畅通填充型腔,尽量避免尖角、缺口.B.在不影响产口尺寸及功能的情况下尽量将脱模斜角取大.一般为~2度.C.设计浇口应考虑孔止填充不足,异向性变形,易产生熔接痕等因素.D.模具型芯、型腔应有足够刚性、强度及耐腐蚀性.E.顶出机构应均有力,便於换修.F.模具应设有排气斜槽,并宜设於易发生熔接痕部位.模具的制作.模具的制作需要严格按照模具图纸制作.模芯模腔加工要保证平面度、粗糙度.特别要注意重点尺寸的把握.模具试模.塑胶料的准备.根据产品的要求选用塑胶料.(我司通常所用的塑胶料有PC 料、PC加玻纤、尼龙NA66)PC料要试模前要经过洪干处理.120度连续四小进烘干使水份降在%以下.NA66料需要在成型前经过烘干处理.90度连续烘干五小时使水份降在%以下.注塑成型.A.试模前模具检查.a.外观检查.b.空运转检查.B.模具试模一般PC料的成型温度要控制在270~320度.NA66料的温度控制在260~275度之间.产品尺寸及功能检验.根据产品图检验注塑成型後的产品各尺寸是否合格.另实际组装是否有干涉.。
塑胶模具设计牛角进点设计规范
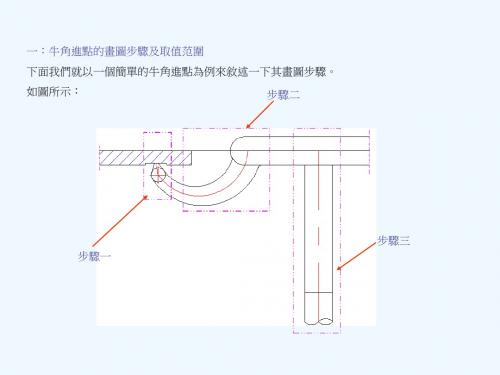
如為U形流道建議都要做此拆彎偷料。
步驟二: 1:按下圖所示找到牛角的另一個端點,畫出為R為值的牛角中心線。 防止流道漏膠和牛角 破膠位的情況出現 此數是為防止牛角超出 流道前端,如有超出此 值可相應加大
注:如R取值為L/2 畫出的圖,如左圖 所示為錯誤的,兩 紅線不可以相交。 所以R取值為>L/2 且不會出現兩線相 交的最接近的0.5一 間隔數值為宜。
2:畫圖形校核牛角的大端直徑D2值,確定后定出D3值,然后畫出兩條相切弧,完成步驟。
c取值3度以上 D3=(D1+D2)/2 如果:(a) D4>=2xR1,D2=D4。 (b) D4<2xR1 =< 1.3xD4,D2= 2xR1 。 (D2值取以0.5為間隔的數值) (c) 2xR1 >= 1.3xD4,D2= 2xR1 。 (D2值取以0.5為間隔的數值,且此時應 考慮將D3即流道的直徑加大) 最后以上述畫圓的方法將牛角的外圈線畫出 此圓位置位于牛角中心 弧的中點
一:牛角進點的畫圖步驟及取值范圍 下面我們就以一個簡單的牛角進點為例來敘述一下其畫圖步驟。 如圖所示: 步驟二
步驟三 步驟一
步驟一: 首先我們找到產品上進點位置,采用點澆口的方式將頭部形狀畫出,然后旋轉一個角度“b”。
此為近似值,為0.4~0.6之間
D的取值為DFM報告提供 a=50度 D1的取值為先畫一個三切圓,然后 取0.5一間隔的近似值,如1.5、2等, 再以相切、相切、半徑的方式畫圓。 b=10~20度
步驟三: 按下圖所示找到牛角的另一個端點,畫出為R為值的牛角中心線。 倒R角,防止銳 角刮出料屑
L4=(1.5~2)xD4
L3>=L1+L2
如L3值大于模仁或接近模仁厚度 時,采用右圖的方式做插入式拉 料頂針。
塑胶模具设计标准

塑胶模具设计标准随着现代工业的不断发展,塑胶模具的使用越来越广泛,它不仅可以满足工业生产的精度要求,而且体积小、形状复杂的产品多采用塑胶模具生产,塑胶模具的设计也逐渐成为工业界的一个热门话题。
为保证塑胶模具的质量和生产效率,设计标准非常重要,因此本文旨在介绍塑胶模具设计的标准。
一、设计要求1. 精度和可靠性:塑胶模具的设计必须具有高精度和可靠性,以保证产品质量。
在模具的设计中,应当注意各个部位之间的配合精度,并加强模具的稳定性和刚度,避免在生产过程中产生振动或变形等问题。
2. 生产效率:塑胶模具的设计应该根据生产要求,尽可能地提高模具的生产效率,确保每个生产周期内的生产数量越多越好,大大提高生产效率。
3. 可维护性:塑胶模具是高精度的工具,在生产中如果发生异常操作或意外,那么就需要保障维修的方便性和及时性,因此,设计模具时还需要考虑方便的维护性,方便人员进行内部维修。
4. 安全性:生产过程中要保证安全,所以塑胶模具的设计需要考虑人员安全。
例如,模具密封性能良好,垂直度保持一致性并且设计的外部结构可靠性高。
二、设计原则1. 客户需求原则:模具的设计要满足客户的要求和需求,达到客户的满意度。
在产品的设计和原材料选择方面,应尽量满足客户的工艺要求和性能要求,并根据客户的特殊需要做出特殊处理,以解决客户面临的问题。
2. 高密度模具原则:高密度模具可以提高生产效率,产量大。
因此,在设计模具时,需要选择材料的密度越高越好。
例如,当铝合金材料的密度大于等于2g/cm3时,该材料的热传导、硬度和强度都较高。
3. 标准化设计原则:标准化是模具设计的重要原则,有利于产品的质量控制,提高生产效率。
在模具的设计中,应该考虑标准化设计和生产,例如,标准结构部位的设计、标准板件的设计、标准件的选用,从而降低模具制造成本,提高生产效率。
4. 多模式选择原则:在设计模具时,需要根据客户的生产需求,确定是按批量生产还是按单件生产。
- 1、下载文档前请自行甄别文档内容的完整性,平台不提供额外的编辑、内容补充、找答案等附加服务。
- 2、"仅部分预览"的文档,不可在线预览部分如存在完整性等问题,可反馈申请退款(可完整预览的文档不适用该条件!)。
- 3、如文档侵犯您的权益,请联系客服反馈,我们会尽快为您处理(人工客服工作时间:9:00-18:30)。
模具设计规范(此规范主要应用于手机模具)一、模具排位1、根据产品大小、结构、产量、精密程度、材料或客户要求等因素确定模穴,如1X1、1X2等。
2、当几个产品出在同一套模具中时,考虑进胶的均匀性,应将大的产品排在中间位置,小的产品置于两边。
确保冲胶平衡,保证产品尺寸的精确性。
3、当几个分型面不规则的产品在同一模具中时,排位必须充分考虑其分型面连接的顺畅,且容易加工。
4、一模多穴模具中,当有镶拼,行位等结构时,不得使其发生干涉。
5、排位多时应综合模具每一方面,对流道,是否镶拼,行位,顶出,运水等结构要有一个全局性思考。
6、排位时产品在模上的定位基准要和产品图的基准一致,当一模出一件时,可以考虑以产品对称方向处分中。
7、内模钢料和模胚的大小尺寸如下图所示。
8.产品大小和胶位厚度有较大相差时尽量不要出在同一套模具中。
9.模具方铁高度尽量订做标准高度。
10.模胚型号和中托司使用情况一定要写清楚(细水口需注明SP长度)11.必要时需注明模胚吊模孔移位情况12.考虑需不需开精框及内模料材料和规格(确定后模要不要镶大呵,如需要则一起订料,此为粗料.)二、模具系统设计一)、行位系统当塑胶产品确定前后模开模方向后,有下列情况时一般会采用行位或斜顶等结构:1)、相对出模方向塑胶产品上有倒扣或零度面;2)、产品的出模斜度不够蚀纹的角度;3)、保证特殊的外观面不能有夹线。
1、后模行位:1)、后模行位统一做镶件压块,行位压块用螺丝固定,行位压块材料为油钢淬火至HRC48-52°。
2)、所有与行位相对运动的零部件的滑动面(包括行位底耐磨片,压条,铲基斜面)须锣(磨)油坑,油坑可为平行四边行、V形或圆环形。
3)、行位铲机钢材整体采用738H,在铲机斜面上镶耐磨片,耐磨片可突出斜面0.5mm,耐磨片厚度为6mm(如下图),材料为油钢,淬硬至HRC48-52°。
康铨公司的铲基采用国产S136淬硬至HRC46-50°。
4)、行位沉深B板25mm以上,行位压块沉深B板15mm以上。
5)、行位开模采用斜导柱。
斜导柱的大小及数量视行位大小而定,角度要比行位斜面小2-3°。
6)、行位定位必须准确,行位行程小的尽量采用弹弓加螺丝头的方式定位,行位行程大且不方便加装弹弓时,可采用多个行位波仔的方式定位,所有行位需加装定位螺丝,以防行位掉落,用油缸开合的行位及抽芯结构,要加装合理的行程开关。
7)、行位斜导柱的斜度通常为15°;长度不能与B板相干涉。
模胚上导柱长度要足够长,合模时导柱与导套先合,然后斜导柱才能套入行位。
8)、行位高度与长度理想比例为1:2,实际视具体情况而定,但尽量不大于1:1,否则会造成行位不够稳定。
9)、铲机与行位的配合面要求超过行位高度的2/3以上,大面积封胶的行位,铲机必须加反铲,模板上钢料宽度至少有15mm以上,如下图所示。
10)、不论行位的侧面是否封胶,其两侧均要做斜度,一般为单边1-3°。
类似手机底壳行位四面包夹线时,一般尽量在四R角中间以45度方向出行位夹线。
如图所示:11)、 行位行程的计算(以两板合模为例):为保证制品顺利脱模,行位移动的距离一定要充分,一般以制品可以脱模的最小距离加上3mm 为最小行程:22= R - r +3AB=AC+3所有手机软胶类产品须做行位时,因为行位开模会将产品扣位略拉长,所以行位行软胶时退开的行程比行硬胶须更长一些。
12)、 行位在分型面上行小针需做成隧道含针的形式或做“T ”型槽形式。
小针尾部需做到4mm 以上:高起分型面做隧道行位13)、 行位座材料采用718H,行位镶件采用S136淬火加硬至HRC48-52°。
康铨公司的行位座采用国产8407加硬至HRC46-50°。
2、 前模行位:1)、 前模行位一般采用GC 或FC 型模胚,行位做在A 板上,铲机做在前模固定板上,A 板与水口板用4支自制的标准小拉杆限位,小拉杆直径为16mm 。
(附录1) A 板和B 板之间必须安装机械扣机或拉杆上部加弹簧(也可在水口板上加强力胶)。
结构优先考虑图a,其次考虑图b.图 a 图b2)、 前模行位的铲机采用油钢,行位座采用718H ,(康铨公司的行位座采用国产8407加硬至HRC46-50度)。
行位镶件采用S136淬火加硬至HRC48-52°。
3、 斜顶:1)、 斜顶结构首选图a ,其次图b ,再次图c 。
斜顶在斜顶座里滑动,斜顶座以螺丝固定在顶针板里面。
斜顶座升入B 板内,以青铜片导向(如图d ),并将四角倒成C2X45°的C 角。
斜顶材料一般用国产8407(康荃公司的斜顶材料为8407淬硬至HRC46-50度),斜顶座用油钢淬硬至HRC48-52度;斜顶能够做到全包胶的一定要做成全包胶形式(但不能影响外观),以防有披锋产生。
图 A图BC图D2)、 当分型面上有斜顶时,需在回程杆下加做弹弓胶。
(如下图)3)、 斜顶有位置做大时尽量做大,以便增加强度。
多个斜顶共用一个斜顶座时,斜顶座可以劈开,方便配模。
二)、 浇注系统:1、 流道:流道应根据成品形状、塑胶特性、啤机调试、型腔的布置、入水位置及形式而进行设计,而且保证塑料能迅速而均匀地充满型腔。
常用流道为圆形或梯形和“U ”形。
1)、 主流道尽可能短,软胶类的产品的主流道长度应尽量小于50MM 。
2)、 分流道原则上为圆形,有如下几种情况流道需开成梯形:a)、 后模为推板时,前模分流道为梯形。
b)、 采用点胶口入水时,前模A 板底部开梯形流道。
c)、 电镀产品的辅助流道一般为梯形,都开设在后模。
d)、 小产品可在后模一側开梯形流道。
e)、 梯形流道的尺寸:围流道及分流道主流道电镀小件流道四大件流道主流道3)、 主流道和分流道的末端及拐角处均须做冷料井及排气槽,如图。
分流道末端须开排气槽4)、 需电镀的产品需采用辅助流道,并在流道上做镶针和胶柱,方便胶件叠放。
A-A SECTIONH 大于产品高度 2mm5)、6)、 当同一模具上有多级分流道时,上一级分流道大约是下一级分流道直径的1.4倍左右。
7)、 PC 和PMMA 等透明材料须采用“S ”形分流道。
8)、 所有流道必须抛光,以免影响注塑流动性及啤塑外观。
9)、 电镀件需考虑做挂位和防呆设计。
10)、 叠放孔不宜太深,防止有残余电镀液;流道底尽量倒R 角,利于导电。
2、 浇口:浇口的形式及大小需根据成品大小和形状,流道长短,成品塑料特性,客户要求等因素而定,入水位置通常设在成品最大壁厚处。
常用入水形式如下: 1)、 直接浇口:制品在外观和功能均允许的情况下才可使用直接浇口。
2)、 侧浇口:侧浇口设置于制品分型面处,制品允许有浇口痕迹才可以使用,侧浇口包括边缘浇口和搭接浇口,其浇口尺寸与壁厚、大小、材料等许多因素有关,一般规格如图。
1.0-2.5 2.0B 0.6T0.35-1.01.5常用值一般值代号 1.0-2.0L A、边缘浇口1.0-2.5 1.5B 0.3T0.2-0.51.2常用值一般值代号 1.0-2.0L B、软胶类边缘浇口1.0-1.5 1.0B 1.0T 0.8-1.2 1.5常用值一般值代号 1.0-2.0L C、搭接浇口H0.2-0.50.33.0-5.04.0B 0.8T2.0常用值一般值代号 1.5-2.5L D、透明件边缘浇口开成扇形注:浇口截面积不能大于流道截面积0.6-1.5E、边缘浇口与搭接浇口的选择见图顺流(良)喷流(差)ba喷流(差)顺流(良)3)、 点胶口:4)、 潜伏式浇口:潜伏式浇口有潜顶针、潜薄片、潜产品和潜牛角等几种,手机模的潜水首选潜牛角(注意牛角不易太弯,不利顶出)。
a)、潜顶针:潜顶针的位置空间上不能太窄,要能方便下剪钳。
常取:b)、潜牛角:3、唧嘴:1)、三板模尽量套用自制的标准大唧嘴(附录2)。
2)、两板模使用自制的标准小唧嘴(附录3),软胶模孔径ф2.5,硬胶模孔径ф3.0。
(如下图)3)、唧嘴R的大小需根据注塑机型号和客户的要求来定,一般 R=15.5mm或R=21mm。
(如上图)4)、唧嘴底距离A板框底做到8—10mm4、定位圈:1)、每套模具必须装有定位圈(即定位法兰),以便装模定位。
2)、定位圈直径一般为ф100(公差-0.2~-0.4mm)。
凸出模面板高度10mm,5、自动脱水口装置:1)、细水口模(三板模)均采用自制标准小拉杆带动水口板移动使水口自动脱落。
小拉杆直径为16mm(附录1)2)、一般采用B板(动模板)面上装有4粒尼龙胶塞的结构,当有前模行位时,一定要采用机械扣机的形式。
3)、水口针以ф5mm顶针磨成如下图形式:三)、冷却系统1、所有模具冷却水出口必须打“OUT”,入口必须打“IN”,并有数字编号,如“IN 1”、“OUT 1”等等2、运水排布均匀,直径做ф6mm。
大产品做到ф8mm--ф10mm3、运水孔边至胶位的距离为6mm以上。
4、运水孔边与螺丝、顶针、斜顶、镶件至少相距4mm。
5、所有防水圈均采用耐高温胶圈,胶圈型号为ф12*2.5。
6、 为方便安装运水接头,运水每个进、出口之间的距离至少保证有30mm 以上。
7、 模胚上运水进、出口螺牙采用管螺纹1/8”BSP 牙。
8、 运水的排布尽量从左右侧进出,并且进出口尽量对准基准一侧。
四)、 顶出系统制品在模具中冷却固化之后,需切实可靠将其从模具中推顶出来,这一机构称之为顶出系统。
同时必须保证,当模具闭合时,它不会与模具其它零部件发生干涉,并回到初始位置,准备进行下一个周期的动作顶出系统要保证除软胶模外所有模具在注塑时都能全自动啤塑。
1、 顶出行程:一般要求制品完全脱离钢料至少10mm ,如下图所示,以上2、 正确的顶出位置,应设在制品脱模困难的地方,如骨位、柱位及有包紧力的地方,同时顶出痕迹不能影响制品外观,并且顶出机构不能和其它零件(如撑头、螺丝等)干涉。
3、 常用的顶出方式如下 1)、 顶针:a ) 许可的情况下,尽量使用3mm 以上的顶针,顶针小于或等于2mm 时需带托。
3mm 以下的顶针都在盘起或在MISUMI 订购(视项目而定),托针须注明托位的大小和长度,并使用相应的编号。
b ) 当顶针位于圆弧面或顶针和司筒受胶位方向限制时,必须要设计定位装置,定位方式如下图,c ) 所有顶针必须高出模面0.05mm 。
d ) 所有顶针和镶针为1.5mm 及1.5mm 以下时,钢料上顶针和镶针孔采用慢走丝线割,1.5mm 以上顶针孔采用慢走丝线割,当啤塑材料为PA 、POM 、软胶系列等一些容易走批峰的塑胶时,所有顶针孔也需要慢走丝线割。
2)、 司筒:a ) 所有司筒孔采用慢走丝线割。