moldflow6.1中文教程第1章_注塑基础知识
《中文版Moldflow模流分析从入门到精通 2021版》读书笔记思维导图

3.2 网格的划 分
3 3.3
Autodesk Moldflo...
4 3.4
Autodesk Moldflo...
5 3.5
CADdoctor模 型修复医生
3.1.1 有限元 网格类型
3.1.2 认识网 格单元
3.2.2 生成网格
3.2.1 设置网格密 度
3.2.3 网格统计
3.3.1 网格诊 断技术
《 中 文 版 最新版读书笔记,下载可以直接修改 Moldflow模流分 析从入门到精通 2021版》
思维导图PPT模板
本书关键字分析思维导图
参数
文件
模流
模具
方法
浇口
解决
分析
工艺
成型 位置
气辅
案例
网格
缺陷
双色
创建
设计
教学
01 文前内容
目录
02 第1章 Autodesk Moldflo...
03 第2章 创建分析模型
2.1.1 创建节点
2.1.3 创建区域
1
2.2.1 平移实 体
2
2.2.2 旋转实 体
3
2.2.3 3点旋 转实体
4
2.2.4 缩放实 体
52.2Biblioteka 5 镜像实 体2.3.2 创建冷却系 统几何
2.3.1 创建浇注系 统几何
2.3.3 创建模具镶 件几何
第3章 网格规划与缺陷修复
1
3.1 有限元网 格概述
04
1.4.4 选 择分析类型
06
1.4.6 设 置工艺参数
05
1.4.5 选 择成型材料
1.4.7 设置注射 (进料口)位置
MOLDFLOW模具分析技术基础知识
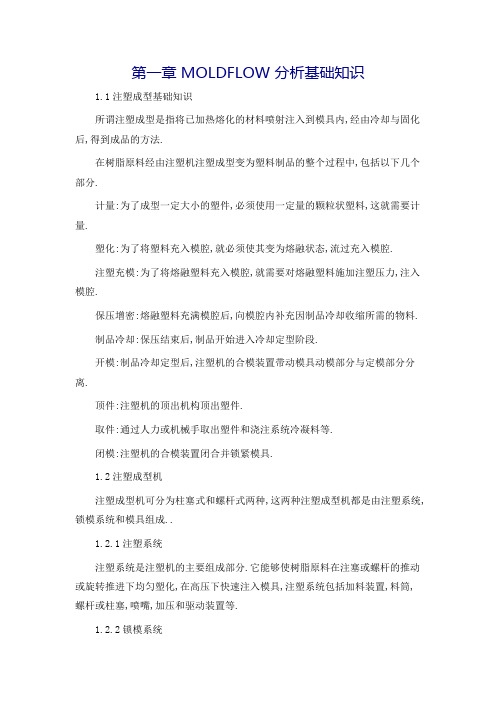
第一章 MOLDFLOW 分析基础知识1.1注塑成型基础知识所谓注塑成型是指将已加热熔化的材料喷射注入到模具内,经由冷却与固化后,得到成品的方法.在树脂原料经由注塑机注塑成型变为塑料制品的整个过程中,包括以下几个部分.计量:为了成型一定大小的塑件,必须使用一定量的颗粒状塑料,这就需要计量.塑化:为了将塑料充入模腔,就必须使其变为熔融状态,流过充入模腔.注塑充模:为了将熔融塑料充入模腔,就需要对熔融塑料施加注塑压力,注入模腔.保压增密:熔融塑料充满模腔后,向模腔内补充因制品冷却收缩所需的物料.制品冷却:保压结束后,制品开始进入冷却定型阶段.开模:制品冷却定型后,注塑机的合模装置带动模具动模部分与定模部分分离.顶件:注塑机的顶出机构顶出塑件.取件:通过人力或机械手取出塑件和浇注系统冷凝料等.闭模:注塑机的合模装置闭合并锁紧模具.1.2注塑成型机注塑成型机可分为柱塞式和螺杆式两种,这两种注塑成型机都是由注塑系统,锁模系统和模具组成..1.2.1注塑系统注塑系统是注塑机的主要组成部分.它能够使树脂原料在注塞或螺杆的推动或旋转推进下均匀塑化,在高压下快速注入模具,注塑系统包括加料装置,料筒,螺杆或柱塞,喷嘴,加压和驱动装置等.1.2.2锁模系统注塑机上实现锁合模具,启闭模具和顶出制件的机构称为锁模系统.熔料在高压下注入模具,必须施加足够大的锁模力才能保证模具严密闭合不溢料,锁模结构还应保证模具启闭灵活,准确,迅速和安全,并防止损坏模具和制件,避免机械受到强烈震动,达到安全运行以延长机器和模具的使用寿命.1.2.3模具模具是为了将树脂原料做成某种形状而用来承接射出树脂的部件.注塑模具主要由浇注系统,成型零件和结构零件组成.1.3注塑成型过程在注塑过程的塑化,填充,保压和冷却这四个主要阶段中,起主要作用的工艺参数也随着注塑过程的变化而变化.塑化塑化是指塑料在料筒内经加热达到良好可塑性的流动状态的全过程.塑化是注塑成型的准备阶段.熔体在进入模腔之前应达到规定的成型温度,并能在规定时间内达到足够数量,熔体温度应均匀一致,不发生或极少发生热分解以保证生产的连续进行.填充这一阶段从柱塞或螺杆开始向前移动起,直至模腔被塑料熔体充满为止.填充过程中包含的重要工艺参数有:熔体温度,注塑压力,填充时间.充模刚开始一段时间内模腔中没有压力,待模腔充满时,料流压力迅速上升达到最大值.充模的时间与模塑压力有关,充模时间长,先进入模内的塑料受到较多的冷却,粘度增大,后面的塑料就需要在较高的压力下才能进入模腔,反之,所需的压力则较小.在前一情况下,由于塑料受到较高的剪切应力,分子定向程度比较大.这种现象如果保留到料温降低至软化点以后,则制品中冻结的定向分子将使制品具有各向异性.这种制品在温度变化较大的使用过程中会出现裂纹,裂纹的方向与分子定向方向是一致的.而且,制品的热稳定性也较差,这是因为塑料的软化点随着分子定向程度增高而降低.高速充模时,塑料熔体通过喷嘴,主流道,分流道和浇口时产生较多的摩擦而使料温升高,这样当压力达到最大值时,塑料熔体的温度就能够保持较高的值,分子定向程度可减少,制品熔接强度也提高.充模过快时,在嵌件后部的熔接往往不好,致使制品强度变劣.保压这是指从熔体充满模腔时起,至柱塞或螺杆撤回时为止的一段时间.保压阶段包括的重要工艺参数有:保压压力,保压时间.保压阶段中,塑料熔体因受到冷却而发生收缩,但因塑料仍然处于柱塞或螺杆的稳压下,料筒内的熔料会被继续注入模腔内补足因收缩而留出的空隙,如果柱塞或螺杆停在原位不动,压力曲线就会略有衰减;如果柱塞或螺杆保持压力不变,也就是随着熔料入模的同时向前做少许移动,则在此段中模内压力维持不变.此时压力曲线与时间轴平行.压实阶段对于提高制品的密度,降低收缩和克服制品表面缺陷都有影响.此外,由于塑料还在流动,而且温度又在不断下降,定向分子容易被冻结,所以这一阶段是大分子定向形成的主要阶段.这一阶段拖延时间愈长,分子定向程度也将愈大.冷却这一阶段是指从浇口的塑料完全冻结时起,到制品从模腔中顶出时为止.冷却阶段包括的重要工艺参数是冷却时间冷却时模腔内压力迅速下降,模腔内塑料在这一阶段内主要是继续冷却,以便制品在脱模时具有足够的刚度而不致发生扭曲变形.在这一阶段内,虽无塑料从浇口流出或流入,但模内还可能有少量的塑料流动,因此到制品脱模时,模内压力不一定等于外界压力,模内压力与外界压力的差值成为残余压力.残余压力的大小与压实阶段的时间长短有密切关系.残余压力为正值时,脱模比较困难,制品容易被刮伤或破裂;残余压力为负值时,制品表面容易有陷痕或内部有真空泡.所以,只有大残余压力接近零时,脱模才比较顺利,并能够获得满意的制品.1.4注塑成型工艺条件注塑成型工艺条件主要包括温度,压力和时间等温度注塑成型过程中的温度主要有熔料温度和模具温度.熔料温度影响塑化和注塑充模,模具温度影响充模和冷却定型.熔料温度指塑化树脂的温度和从喷嘴射出的熔体温度,前者称为塑化温度,后都称为熔体温度.由此看来,熔料温度取决于料筒和喷嘴两部分的温度.熔料温度的高低决定熔体流动性能的好坏.熔料温度高,熔体的粘度小,流动性能好,需要的注塑压力小,成型后的制件表面光洁度好,出现熔接痕,缺料的可能性就小.反之熔料温度低,就会降低熔体的流动性能,会引起表面光洁度低,缺料,熔接痕明显缺陷.但是熔料温度过高会引起材料热降解,导致材料物理和化学性能降低.模具温度是指和制品接触的模腔表面温度.模具温度直接影响熔体的充模流动行为,制件的冷却速度和制件最终质量.提高模具温度可以改善熔体在模腔内的流动性,增强制件的密谋和结晶度以及减小充模压力和制件中的压力.但是,提高模具温度会增加制件的冷却时间,增大制件收缩率和脱模后的翘曲,制件成型周期也会因为冷却时间的增加而变长,降低了生产效率.降低模具温度,虽然能够缩短冷却时间,提高生产率,但是,会降低熔体在模腔内的流动能力,并导致制件产生较大的内应力或者形成明显的熔接痕等制件缺陷.压力注塑过程中的压力主要有注塑压力,保压压力和背压注塑压力是指螺杆或者柱塞沿轴向前移时,其头部向塑料熔体施加的压力.它主要用于克服熔体在成型过程中的流动阻力,还对熔体起一定程度的压实作用.注塑压力对熔体的流动,充模及制件质量都有很大影响.注塑压力的大小取决于制件成型树脂原料的品种,制件的复杂度,壁厚,喷嘴的结构形式,模具浇口的类型和尺寸以及注塑机类型等因素.保压压力是指对模腔内树脂熔体进行压实以及维护向模腔内进行补料流动所需要的压力.保压压力是重要的注塑工艺参数之一,保压压力和保压时间的选择直接影响注塑制品的质量,保压压力与注塑压力一样由液压系统决定.在保压初期,制品重量随保压时间而增加,达到一定时间不再增加.延长保压时间有助于减少制品的收缩率,但过长的保压时间会使制品两个方向上的收缩率程度出现差异.令制品各个方向上的内应力差异增大,造成制品翘曲,粘模.在保压压力及熔体温度一定时,保压时间的选择应取决于浇口凝固时间.背压是指螺杆顶部熔料在螺杆转动后退时对其施加的反向压力.增大背压可以排出原料中的空气,提高熔体密实程度,还会增大熔体内的压力,螺杆后退速度减小,塑化过程的剪切作用加强,摩擦热增多,熔体温度上升,塑化效果提高.但是背压增大后,如果不相应提高螺杆转速,那么,熔体在螺杆计量段螺槽中将会产生较大的逆流和漏流,从而使塑化能力下降.背压的大小与制件成型树脂原料品种,喷嘴种类以及加料方式有关.时间注塑成型周期主要由注塑时间Ti,保压时间Tp,冷却时间Tc,开模时间To组成.th为TP与TC之和.注塑时间是指注塑活塞在注塑油缸内开始向前运动直至模腔被全部充满为止所经历的时间.保压时间为从模腔充满后开始,到保压结束为止所经历的时间.注塑时间与保压时间由制件成型树脂原料的流动性能,制件几何形状,制件尺寸大小,模具浇注系统的形式,成型所用的注塑方式和其他工艺条件等到因素决定.冷却时间指保压结束到开启模具所经历的时间.冷却时间的长短受熔体温度,模具温度,脱模温度和冷却剂温度等因素的影响.在保证取得较好制件质量的前提下,应当尽量缩短冷却时间的大小,否则,会延长制件成型周期,降低生产效率,还可能造成具有复杂几何形状的制件脱模困难.开模时间为模具开启取出制件到下个成型周期开始的时间.注塑机自动化程度高,模具复杂度低,则开模时间短;否则,开模时间较长.1.5常见制品缺陷及产生原因1.5.1短射短射是指由于模具模腔填充不完全造成制品不完整的质量缺陷,即熔体在完成填充之前就已凝结。
MOLDFLOW详细操作手册
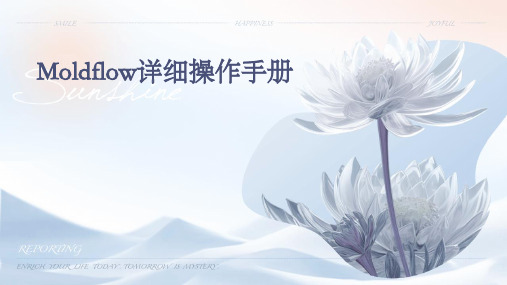
VS
4. 在必要情况下,采用多级注射工艺 来改善填充效果。
05
Moldflow案例分析
案例一:手机壳模具设计优化
总结词
通过Moldflow对手机壳模具进行模拟分析, 优化模具设计,提高生产效率和产品质量。
1. 导入3D模型
将手机壳的3D模型导入Moldflow软件中,并 进行适当的单位和网格划分设置。
冷却介质
根据模具结构和生产条件,选择合适的冷却介质,如水、油等, 以提高冷却效果和减小冷却时间。
模具热平衡分析
温度场分布
通过热平衡分析,了解模具温度场分布情况,为优化模具设计和减 小热误差提供依据。
热传导与对流
分析模具材料、冷却介质和塑料之间的热传导与对流情况,以提高 冷却效果和减小成型周期。
热膨胀与收缩
多模腔模拟
模腔耦合分析
通过多模腔模拟,分析各模腔之间的耦合效应, 以优化模具设计和减小成型误差。
充型平衡
通过多模腔模拟,分析各模腔的充型情况,以实 现各模腔的充型平衡和减小缺陷。
冷却平衡
通过多模腔模拟,分析各模腔的冷却情况,以实 现各模腔的冷却平衡和减小成型周期。
04
Moldflow常见问题与解决 方案
浇注材料等。
03
4. 设计调整
根据模拟分析结果,对模具设计方案进行调 整,如优化浇注系统、改进模具结构等。
05
04
3. 模拟分析
对模具进行充填、流动、保压和冷却 等模拟分析,观察分析结果,评估模 具设计方案的有效性和可行性。
06
5. 验证调整效果
通过再次模拟分析验证调整后的模具设计方案 效果,确保方案的有效性和可行性得到提高。
4. 尝试增加模拟迭代次数或采用更高级的求解算法以提高模 拟精度。
Moldflow课件--第一章概述

CAE应用情况 CAE应用情况
• 全球应用CAE技术的比例仅15%左右,仍有 广大的发展空间。 • 影响CAE技术推广的原因:分析的准确性;相 关技术人员的养成;技术使用的简易性。 • CAE模拟分析主要误差来源:理论模式(物 理现象、材料物性);数值解法(numerical Solver);几何模型(geometry model);错误 的输入数据
材料成形CAE基础 二、材料成形CAE基础
材料成形CAE是通过数值模拟的方法, 是通过 的方法, 材料成形 速度场、 计算材料成形问题中工件和模具的速度场、 温度场、应力场、应变场等,并将计算结 温度场、应力场、 以计算机图形的方式直观地显示出来, 果以计算机图形的方式直观地显示出来, 供材料成形工艺及模具设计时参考。 供材料成形工艺及模具设计时参考。
MPA可以理解为 简易的快速的” MPI。 MPA可以理解为 “简易的快速的” MPI。 MPA分析内容少 算法进行了简化,分析速度快。 分析内容少, MPA分析内容少,算法进行了简化,分析速度快。MPA 的结果准确性还可以, MPI基本上一致 基本上一致, 的结果准确性还可以,与MPI基本上一致,只是少一点而 已。 MPA可提供如下分析。 可提供如下分析。 可提供如下分析 产品结构是否合理 怎样选择合适的注塑材料 怎样确定合理的浇口位置 浇口位置自动优化 预测熔接痕位置 模具型腔是否充满 最终制品的质量如何 怎样选择合适的注塑机 缩痕分析 成本顾问 等分析项。 等分析项。由于没有冷却的支持部分分析结果和实际有较 大出入。 大出入。
Moldflow系列产品 Moldflow系列产品
Moldflow Plastics Advisers(快速试模分 快速试模分 析):最快最便捷的测试产品工艺性以及优 : 化模具设计的工具。 化模具设计的工具。
Moldflow培训大纲
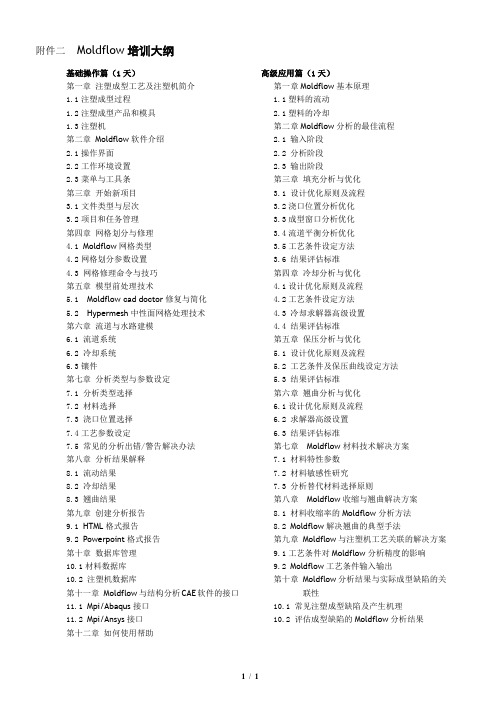
附件二Moldflow培训大纲基础操作篇(1天)第一章注塑成型工艺及注塑机简介1.1注塑成型过程1.2注塑成型产品和模具1.3注塑机第二章Moldflow软件介绍2.1操作界面2.2工作环境设置2.3菜单与工具条第三章开始新项目3.1文件类型与层次3.2项目和任务管理第四章网格划分与修理4.1 Moldflow网格类型4.2网格划分参数设置4.3 网格修理命令与技巧第五章模型前处理技术5.1 Moldflow cad doctor修复与简化5.2 Hypermesh中性面网格处理技术第六章流道与水路建模6.1 流道系统6.2 冷却系统6.3镶件第七章分析类型与参数设定7.1 分析类型选择7.2 材料选择7.3 浇口位置选择7.4工艺参数设定7.5 常见的分析出错/警告解决办法第八章分析结果解释8.1 流动结果8.2 冷却结果8.3 翘曲结果第九章创建分析报告9.1 HTML格式报告9.2 Powerpoint格式报告第十章数据库管理10.1材料数据库10.2 注塑机数据库第十一章Moldflow与结构分析CAE软件的接口11.1 Mpi/Abaqus接口11.2 Mpi/Ansys接口第十二章如何使用帮助高级应用篇(1天)第一章Moldflow基本原理1.1塑料的流动2.1塑料的冷却第二章Moldflow分析的最佳流程2.1 输入阶段2.2 分析阶段2.3 输出阶段第三章填充分析与优化3.1 设计优化原则及流程3.2浇口位置分析优化3.3成型窗口分析优化3.4流道平衡分析优化3.5工艺条件设定方法3.6 结果评估标准第四章冷却分析与优化4.1设计优化原则及流程4.2工艺条件设定方法4.3 冷却求解器高级设置4.4 结果评估标准第五章保压分析与优化5.1 设计优化原则及流程5.2 工艺条件及保压曲线设定方法5.3 结果评估标准第六章翘曲分析与优化6.1设计优化原则及流程6.2 求解器高级设置6.3 结果评估标准第七章Moldflow材料技术解决方案7.1 材料特性参数7.2 材料敏感性研究7.3 分析替代材料选择原则第八章Moldflow收缩与翘曲解决方案8.1 材料收缩率的Moldflow分析方法8.2 Moldflow解决翘曲的典型手法第九章Moldflow与注塑机工艺关联的解决方案9.1工艺条件对Moldflow分析精度的影响9.2 Moldflow工艺条件输入输出第十章Moldflow分析结果与实际成型缺陷的关联性10.1 常见注塑成型缺陷及产生机理10.2 评估成型缺陷的Moldflow分析结果1 / 1。
Moldflow6_1中文版案例实战视频教程解析教案
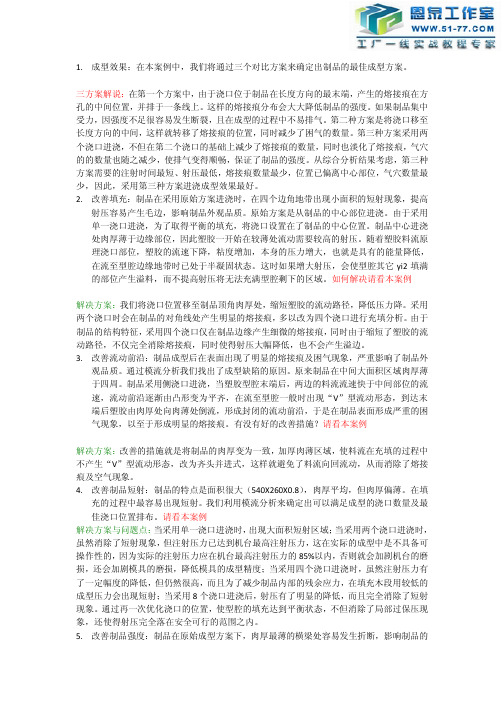
1.成型效果:在本案例中,我们将通过三个对比方案来确定出制品的最佳成型方案。
三方案解说:在第一个方案中,由于浇口位于制品在长度方向的最末端,产生的熔接痕在方孔的中间位置,并排于一条线上。
这样的熔接痕分布会大大降低制品的强度。
如果制品集中受力,因强度不足很容易发生断裂,且在成型的过程中不易排气。
第二种方案是将浇口移至长度方向的中间,这样就转移了熔接痕的位置,同时减少了困气的数量。
第三种方案采用两个浇口进浇,不但在第二个浇口的基础上减少了熔接痕的数量,同时也淡化了熔接痕,气穴的的数量也随之减少,使排气变得顺畅,保证了制品的强度。
从综合分析结果考虑,第三种方案需要的注射时间最短、射压最低,熔接痕数量最少,位置已偏离中心部位,气穴数量最少,因此,采用第三种方案进浇成型效果最好。
2.改善填充:制品在采用原始方案进浇时,在四个边角地带出现小面积的短射现象,提高射压容易产生毛边,影响制品外观品质。
原始方案是从制品的中心部位进浇。
由于采用单一浇口进浇,为了取得平衡的填充,将浇口设置在了制品的中心位置。
制品中心进浇处肉厚薄于边缘部位,因此塑胶一开始在较薄处流动需要较高的射压。
随着塑胶料流原理浇口部位,塑胶的流速下降,粘度增加,本身的压力增大,也就是具有的能量降低,在流至型腔边缘地带时已处于半凝固状态。
这时如果增大射压,会使型腔其它yi2填满的部位产生溢料,而不提高射压将无法充满型腔剩下的区域。
如何解决请看本案例解决方案:我们将浇口位置移至制品顶角肉厚处,缩短塑胶的流动路径,降低压力降。
采用两个浇口时会在制品的对角线处产生明显的熔接痕,多以改为四个浇口进行充填分析。
由于制品的结构特征,采用四个浇口仅在制品边缘产生细微的熔接痕,同时由于缩短了塑胶的流动路径,不仅完全消除熔接痕,同时使得射压大幅降低,也不会产生溢边。
3.改善流动前沿:制品成型后在表面出现了明显的熔接痕及困气现象,严重影响了制品外观品质。
通过模流分析我们找出了成型缺陷的原因。
MOLDFLOW模具分析技术基础知识

第一章MOLDFLOW分析基础知识1.1注塑成型基础知识所谓注塑成型是指将已加热熔化的材料喷射注入到模具内,经由冷却与固化后,得到成品的方法. 在树脂原料经由注塑机注塑成型变为塑料制品的整个过程中,包括以下几个部分.1.计量:为了成型一定大小的塑件,必须使用一定量的颗粒状塑料,这就需要计量.2.塑化:为了将塑料充入模腔,就必须使其变为熔融状态,流过充入模腔.3.注塑充模:为了将熔融塑料充入模腔,就需要对熔融塑料施加注塑压力,注入模腔.4.保压增密:熔融塑料充满模腔后,向模腔内补充因制品冷却收缩所需的物料.5.制品冷却:保压结束后,制品开始进入冷却定型阶段.6.开模:制品冷却定型后,注塑机的合模装置带动模具动模部分与定模部分分离.7.顶件:注塑机的顶出机构顶出塑件.8.取件:通过人力或机械手取出塑件和浇注系统冷凝料等.9.闭模:注塑机的合模装置闭合并锁紧模具.1.2注塑成型机注塑成型机可分为柱塞式和螺杆式两种,这两种注塑成型机都是由注塑系统,锁模系统和模具组成..1.2.1注塑系统注塑系统是注塑机的主要组成部分.它能够使树脂原料在注塞或螺杆的推动或旋转推进下均匀塑化,在高压下快速注入模具,注塑系统包括加料装置,料筒,螺杆或柱塞,喷嘴,加压和驱动装置等.1.2.2锁模系统注塑机上实现锁合模具,启闭模具和顶出制件的机构称为锁模系统.熔料在高压下注入模具,必须施加足够大的锁模力才能保证模具严密闭合不溢料,锁模结构还应保证模具启闭灵活,准确,迅速和安全,并防止损坏模具和制件,避免机械受到强烈震动,达到安全运行以延长机器和模具的使用寿命.1.2.3模具模具是为了将树脂原料做成某种形状而用来承接射出树脂的部件.注塑模具主要由浇注系统,成型零件和结构零件组成.1.3注塑成型过程在注塑过程的塑化,填充,保压和冷却这四个主要阶段中,起主要作用的工艺参数也随着注塑过程的变化而变化.1.塑化塑化是指塑料在料筒内经加热达到良好可塑性的流动状态的全过程.塑化是注塑成型的准备阶段.熔体在进入模腔之前应达到规定的成型温度,并能在规定时间内达到足够数量,熔体温度应均匀一致,不发生或极少发生热分解以保证生产的连续进行.2.填充这一阶段从柱塞或螺杆开始向前移动起,直至模腔被塑料熔体充满为止.填充过程中包含的重要工艺参数有:熔体温度,注塑压力,填充时间.。
Moldflow 注塑机参数的输入

Moldflow 注塑机参数的输入
在moldflow 的注塑机数据库里找不到我们所要的注塑机型号。
这就得我们自己输入注塑机的参数。
现在基于moldflow 6.1 将BOY 公司的BOY12A 微型注塑机参数输入。
BOY12A的参数如下:
第一步:打开6.1,点击菜单栏里的工具中新建个人数据库,找到注塑机。
点击确定,新建
第二步:输入第一栏。
第一栏里都是注塑机的基本信息,如型号、生产厂家等:
第三步:输入第二栏。
第二栏是注塑机注射单元的信息:
第四步:输入第三栏。
第五步:输入第四栏。
完成,点击确定保存。
第六步:调用我们所保存的注塑机参数文档。
点击打开按键选择我们所保存的文件即可。