精益概论
精益生产概论

1、异常停线:绝不传递次品,异常放大器;
推 动 改 善 不 断 升 级
问题 、培 育人 才 、建 立改 善创 新型 企业
自 动 化
品质保证 少人化
2、目视化异常管理:安装快速反应系统,异常看板、生产管 理板、标准作业书。
1、人机作业分离:自动检测、LCA一人减少; 2、防呆防错:5Why、三现主义消除异常、杜绝异常再发。
文化营
— 15 —
三、推进体系
3.2 JIT
序号
1
改善项目
物料与信息一体化
2
物流批量节拍
3
物流快速流动
4
物流空间最短化
5
物流流动准确化
改善方向
计划与物控指令合并 来料节拍与送料节拍,日计划来料 来料和送料裸件化、工装化、工具盒
物料到作业区最短,线边仓 看板来动、分拣单配送
(1)月计划指导供方采购 (2)周计划指导生产
供方库存不可查询
(1)供方平台报库存 (2)齐套查询
3
供应商送货
送货数量和时间不可控
(1)日计划指导送货数量和时间 (2)生产订单与供货物流合并、一致 (3)牛奶取货
4
库存过程
转运次数多、搬运次数多
线边仓建设、卸货工装车、来料裸件和工 装盒
— 25 —
五、方法体系
过渡页
11
精益生产目标体系
2 • 精益七个“零”目标体系结构 • 目标体系改善方向
— 11 —
二、目标体系
2.1 精益精益七个“零”目标体系结构
精益生产
JIT生 产计 划与 物流
追求7个“零”极限目标
一个 流
均衡 化与 同步 化系
统
自动 化
精益生产概论

精益生产的历史
Father of management管理 之父
Father of motion – time study动作/时间研究之父
Father of assembly line concept装配线概念之父
Industry quality transformation工业品质控制
Market Expectation …市场期望 • Faster Time to Market更快的产品开发周期 • Faster manufacturing lead times更短的制造 周期 • Lower costs更低的成本 • Open book policies开放式的订货政策 • High Mix/low volume competency多品种/少 批量生产竞争力 • Maximum flexibility最大的灵活度 • Rapid response time快速响应时间 • Operate as one company真正像一个公司一 样运作 • Stronger relationship更加强壮的关系
2) Right First Time quality improvement by 35%产品直通率提高35%
3) The distance your products moved around the factory to be reduced by 50%产品在厂内 搬运距离减少50% 4)80% reduction in machine change over 机器换线时间减少80% 5)How much space would be created if inventory were reduced by 50%库存减少50% 6)Lead time reduction by 50%交货周期缩短50% 7)Productivity improvement by 35%生产效率提升35%
班组建设之精益TWI概论

班组建设之精益TWI概论班组建设是指通过培养和发展工作团队的能力和效率,提升整个班组的绩效和效益。
精益TWI (Training Within Industry) 是一种经典的班组建设方法,旨在通过培训、工作指导和问题解决,提高班组成员的技能和素质,实现生产过程的优化和流程的持续改进。
本文将从精益TWI的基本概念、原则和实施步骤等方面进行介绍。
精益TWI的基本概念是将工作简化为标准的连续动作,并将工作技能通过实践和教练来传授给班组成员。
它的核心原则是“工人是最佳的者”,即全员参与和班组自主决策。
同时,精益TWI强调问题的解决而不是责怪,鼓励班组成员积极主动地提出改进意见,并激发他们的自主创造力和责任心。
精益TWI的实施步骤主要包括三个阶段:设计阶段、实施阶段和掌握阶段。
设计阶段是指制定班组建设的整体目标和行动计划。
首先,明确需要进行班组建设的原因和目的,明确期望达到的效果和收益。
然后,根据工作特点和需求,设计出适应工作现场的培训内容和教材。
最后,确定班组成员接受培训和实践的时间和方式,以及评估和改进的方法。
掌握阶段是指班组成员逐步独立完成工作任务并持续改进的阶段。
班组成员通过实践操作和问题解决,逐渐提高工作效率和质量。
在这个阶段,班组成员应该积极主动地提出改进意见和建议,并及时反馈和分享工作经验。
班组领导需要持续支持和鼓励班组成员的改进行动,并及时给予认可和奖励,激发他们的进一步参与和创新动力。
总之,精益TWI是一种有效的班组建设方法,通过培训、工作指导和问题解决,提高班组成员的实际工作能力和自主创新能力,促进生产过程的优化和流程的持续改进。
它倡导全员参与、班组自主决策和问题解决,强调班组成员的积极主动性和责任心。
在实施过程中,需要设计合理的培训和实践计划,及时调整和改进,非常重要的是班组领导的支持和鼓励。
只有全员参与,班组建设才能取得实际效果,从而提升整个班组的绩效和效益。
3 精益概论 内部培训课程 含课后题

稳定且标准化的流程
目视管理
TPS理念
= 成本 + 利润
(2) 利润
= 售价 - 成本
成本主义 成本低減
(1) 成本主义
(2) 成本低減
利润
售价 成本
利润
成本
售价
增加利润的方法
1.提高售价… 需要>供給 2.降低成本… 需要≦供給
售价由客户決定
精益概论
成本低减 = 提高生产性 生 产 性 ≠ 劳动生产性 生产性:用生产要素,把有限的人、机、料适当的投入, 在规定的时间内生产出具有所需质量和低价格的产品。即 产出物(生产量)和为了生产此产品所投入的诸多因素( 总投入量)的比率为生产性。
精益概论
丰田——创造了世界制造业的奇迹
奇迹!美国人、德国人乃至全世界为 之惊呼并为它折服。 世界上最精益的制造企业。 继泰勒“科学工作法”、福特“批 量生产方 式”之后的又一划时代的里程碑。 世界工业史上的又一次革命。 官、产、军、商、学界埋首苦研追寻其长久不衰的奥秘。
谁能阻挡丰田?
精益概论
通用 860 1855 38
丰田 678 1290 101
福特 672 1642
5
戴—克 430 1600 6
大众 502 1050 13
精益概论
12
10 亿
丰田
美
10
元
8
同级别平均①
6
4
2
1997
1998
1999
2000
2001
2002
2003
2004
2005
图A-3 1997-2006年丰田与同级别公司在净收入上的比较
准时化(Just In Time) 在必要的时候
精益生产全讲义
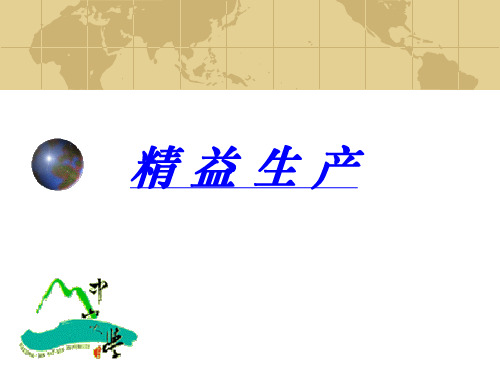
手工生产方式 完全按顾客要求 通用、灵活、便宜
粗略、丰富
懂设计制造 有较高操作技能
高 高 低 极少量需求
大批量生产方式
精益生产方式
标准化,品种单一 品种多样化、系列化
专用、高效、昂贵 柔性高、效率高
细致、简单、重复 不需要专业技能
较粗略、 多技能、丰富
待
8
管理的浪费
管理本身成为一种专 职的工作发生的浪费
事后管理的浪费
41
1、不良、修理的浪费
材料的损失; 设备、人员、工时的损失; 额外的修复、选别、追加检查; 额外的检查预防人员; 降价处理; 出货延误取消定单; 信誉下降; ……
42
2、加工的浪费
△
●
○
自动 插件
●
焊接 组装1 组装2 检测
○
◎
◎
●
包装 ●
徐小凤 ●
○
◎
○
◎
○
△
多技能员工 金 庸 ○
△
●
△
◎
◎
韦小宝 ◎
○
○
●
F4
○
◎
●
○
◎
拉登 ◎
●
△
●
○
萨达姆 △
●
◎
●
○
◎
吕不韦 ●
○
△
○
●
备注:△—计划学习,○—基本掌握,◎—完全掌握,●精通
27
案例
QC小组活动
Q C C uality ontrol ycle
多技能
高
低 高 物资缺乏、供不应 求
低 更低 更高 买方市场
精益生产之JIT生产方式概论

精益生产之JIT生产方式概论简介在现代生产管理中,精益生产是一种高效的生产管理方法,旨在消除浪费,提高生产效率。
其中的JIT(Just-in-Time)生产方式更是精益生产中的重要组成部分,它通过在生产过程中仅在需要时提供所需的物料、零件和信息,避免库存积压,实现生产的高效、灵活和快速。
JIT生产的特点1.零库存: JIT生产方式下,通过供应链管理和精准计划,避免了过多的库存积压。
2.按需生产:生产根据客户订单实时生产,减少了等待时间和生产周期。
3.连续改进: JIT生产鼓励连续改善生产流程和质量控制,不断提高效率和质量水平。
JIT生产的优势1.降低成本:去除库存、减少废品和减少生产周期等措施可以显著降低成本。
2.提高生产效率: JIT生产方式可以减少等待时间、缩短生产周期,提高生产效率。
3.增强市场竞争力:更快速、更灵活地响应客户需求,提升企业在市场上的竞争力。
JIT生产的挑战1.供应链管理难度: JIT生产对供应链管理要求严格,一旦出现供应链中断可能影响整个生产。
2.生产规模限制: JIT生产适用于需求较为稳定的产品,对于波动大的产品需求可能无法满足要求。
3.技术和培训要求:JIT生产需要生产工人具备高效、高质的生产技能,需要企业加大技术培训投入。
JIT生产的应用JIT生产方式是多种企业中常用的生产管理方法,尤其适用于汽车制造、电子产品制造等行业。
在全球范围内,许多知名企业如丰田、索尼都采用了JIT生产方式,取得了显著的效益。
总结JIT生产方式作为精益生产的重要组成部分,通过精准计划、供应链协同和质量控制等手段,实现了高效、灵活和快速的生产管理。
虽然面临着一些挑战,但随着生产管理理念的不断进步和完善,JIT生产方式仍然是现代企业提升生产效率、降低成本的重要方法之一。
精益知识ABC系列之一——精益概论

化(也称之为带人字旁的“自働化”); 3) “一大基础”是指持续改善。改善是丰田生产方式(TPS)的基础,
可以说没有改善就没有丰田生产方式(TPS)。
中化化肥精益知识 ABC 系列
8、丰田生产方式(TPS)的创始人?
中化化肥精益知识 ABC 系列
2)精益的核心理念及原则,如价值确定、流动、拉动等,均来自于 丰田生产系统; 3)所谓精益,就是基于 TPS 上的管理总结与扩展。 6、丰田汽车的发展和成就? 答:二十世纪 50 年代,丰田公司决心发展汽车工业。公司派出丰田 喜一郎等人去美国学习,但是发现美国的大量生产方式不适合日本。 丰田只能走小批量多品种的道路。以大野耐一为代表的丰田员工发展 了很好的管理哲学和管理方法, 在小批多种的环境下,一心一意与浪 费作斗争,三十年流程效率提高了近 100 倍。这样,当整个市场都开 始往多批少量方向转变时,丰田早已成竹在胸了。丰田获利丰厚,2003 年全球汽车领域利润第一,2004 年仍然是第一。 7、什么是丰田生产方式(TPS)? 答:丰田生产方式(TPS)的理论框架包含“一个目标”、“两大支 柱”和“一大基础”。 1) “一个目标”是低成本、高效率、高质量地进行生产,最大限度
中化化肥精益知识 ABC 系列
基础,另建一套管理体系;精益管理不是高不可攀,也不高深,就是 把身边的事情做好。
精益,从心开始; 改善,从我做起!
中化化肥精益知识 ABC 系列
中化化肥精益知识ABC
系列之一—精益概论
1、精益管理的起源? 答:精益管理源于精益生产。 二次世界大战后,日本丰田公司发展了独特的丰田生产方式(Toyoto Production System,简称 TPS),从一个日本的小公司一跃成为世 界汽车业巨头。美国麻省理工学院的三位教授在上个世纪九十年代共 同出版了一本具有里程碑意义的书《改变世界的机器》(THE MACHINE THAT CHANGED THE WORLD),总结了以丰田生产方式为原型的制造模 式,第一次提出了“精益生产”的概念。1996 年 Womack、P. James 和 Daniel T. Jones 发表的《精益思想》(《Lean Think-ing》)一 书奠定了精益制造的基础。 2、什么是精益生产? 答: 精益生产(Lean Production,简称 LP)是美国麻省理工学院数 位国际汽车计划组织(IMVP)的专家对日本“丰田 JIT(Just In Time) 生产方式”的赞誉之称,精,即少而精,不投入多余的生产要素,只 是在适当的时间生产必要数量的市场急需产品(或下道工序急需的产 品);益,即所有经营活动都要有益有效,具有经济性。精益生产是 当前工业界最佳的一种生产组织体系和方式。 精益生产:通过消除企业所有环节上的不增值活动,来达到降低成本、 缩短生产周期和改善质量的目的。
精益生产概论(流程化生产)

; 3、缩短内部作业时间; 4、缩短外部作业时间;
缩短作业切换时间
• 快速切换的技巧: 1.采用并行作业; 2.消除调节环节,把内部作业调整到外部作业,
事先做好准备,不要拆除整个,标准化,消除 测量的仪器,用模块代替; 3.减少人体走动; 4.使用专用的工装; 5.使用快速连接装置; 6.做好事前准备工作; 7.程序化和标准化工具和工装;
缩短作业切换时间
实现均衡生产,可以实现的切换次数是关键,决定了生产批量的 大小。
缩短作业切换时间
S 单个 M 分钟 E 变换 D 模具
模具的更换要少于10分钟
(原始定义)
快速换模是一种由丰田集团新乡重夫开发、大 野耐一完
善在产品系列更换时,被用于分析和改善损失时间的 方法。
缩短作业切换时间
S步te骤p 65
• 优点: 1、最短的生产周期。 2、发现问题及时,品质成本低。 3、搬运最小化,创造安全的生产条件。 4、减少存货和在制品。
流程式生产的U型布局
精益生产线布局可以有效降低中间在制品,缩 短制造周期。
也可以有效的暴露制造过程中的问题
连续流布局为解决生产制造过程中的问题提供 了有效途径。
例如:不良品低减、制造周期缩短、劳动效率提 高、减少生产空间、减少库存等。
设备布置和设计
3、一笔画的整体布置实现厂房整体流程化,工厂流程像 一笔化下去一样,连续不中断,对于工厂货厂房内生 产线不止一条并且具有前后流程上的关联,要考虑工 厂或厂房的整体流程化。步骤:1、集群式布置改为流 程式布置。2、采用U型生产线。3、将长屋形改为大通 铺形。整体上呈现一笔画布置。
4、设备的不合理布置:鸟笼形布置,三角形、四角形。 孤岛形布置,单元之间相互隔离的布置。直线形布置 。
- 1、下载文档前请自行甄别文档内容的完整性,平台不提供额外的编辑、内容补充、找答案等附加服务。
- 2、"仅部分预览"的文档,不可在线预览部分如存在完整性等问题,可反馈申请退款(可完整预览的文档不适用该条件!)。
- 3、如文档侵犯您的权益,请联系客服反馈,我们会尽快为您处理(人工客服工作时间:9:00-18:30)。
Lean production
精益思想与认识
Just In Time
适品 · 适量 · 适时
JIT的基本思想是:只在需要的时候、按需要 的量、 生产所需的产品,故又被称为准时制生产、适时生产 方式、看板生产方式。 JIT的核心是:零库存和快速应对市场变化。 精益生产不断消除所有不增加产品价值的工作, 所以,精益是一种减少浪费的经营哲学。
2、价值流
3、流动 4、拉动 5、尽善尽美
识别出每种产品的价值流; 使价值不间断地流动;
让客户从生产者方面拉动价值; 永远追求尽善尽美。
Lean production
Lean production
□改正的浪费 是指在生产中发生不良品,需返工所用的时间、人力、物力 上的浪费
◆任何的不良品产生,皆造成材料、机器、人工等的浪费。 ◆损失的工时及延误交期 ◆要想生产一个合格的零件,在生产的源头就杜绝不合格零部件、原材 料流入生产后道工序
Lean production
□加工作业的浪费
Lean production
制造过多(过早)的浪费 Overproduction 库存的浪费 Inventory 搬运的浪费 Material Movement 等待的浪费 Waiting 改正的浪费 Correction
七大浪费
加工作业的浪费 Processing 动作的浪费 Motion
Lean production
消耗了资源,而不 能创造价值的一切 人类活动
Lean production
七大浪费定义的由来 大野耐一先生将杜绝浪费视为是丰田生产方式的基本思想,并在现场 总结出了七种浪费,由此产生了七大浪费。并将其分成了四个层次:
第一层次:过剩的生产能力存在
第二层次:制造过剩的浪费
第三层次:过剩库存的浪费
第四层次:为消除以上三个层次产生浪费的浪费
是指在制造过程中,进行不必要的检验、加工或指实际 加工精度比工艺要求精度要高
◆有一些加工程序是可以省略、替代、重组或合并
也被称为改善四原则!
◆将我们实际生产中可以省略的,产生不了直接效益 的工序或步骤尽可能的进行
Lean production
□动作的浪费
是指在生产操作不合理导致的时间浪费(操作员所做 的没有增值的动作)。
Lean production
Inventory Covers All Problem 库存掩盖所有问题
库存水平
Lean production
Low Down Inventory To Expose Problem 通过降库存暴露问题
库存水平
Lean production
□搬运的浪费
是指在生产中的搬运. 因为搬运产生不了直接价值, 所以应 该尽可能减少搬运作业
大规模流水线引起了一场工业变革
Lean production
精益的起源 第3阶段——精益生产
*多样化 *小批量 *六西格玛质量
现在
Lean production
精益的起源
• 准时化 • 自动化 • 七大浪费
大野耐一
• 防错法(pork-yoke) • 快速换模(SMED)
Lean production
Lean production
精益的起源 第2阶段——大规模生产
*劳动分工 *零件互换性 *科学管理 *流水线装配
1900-1925
Lean production
• 1863年-1947年 福特出生后第二年,平炉炼钢法问世,现代钢铁时代 拉开序幕。 • 1903年创立福特汽车公司 • 1913年,首次使用流水线制造T型车。
制造过多(过早)的浪费 Overproduction
•生产多于下游客户所需 Making More Than Needed •生产快于下游客户所求 Making Faster Than Needed
劳模?
Lean production
□库存浪费 为满足生产或顾客的需求,而超过最必要的库存数量
◆常见的库存浪费 –产生不必要的搬运、堆积、放臵、防护处理、寻找等浪费 –使先进先出的作业困难 –损失利息及管理费用 –隐藏不良品损失 –隐藏产能不平衡与过剩损失 –隐藏机器故障损失…
等待工件
十二种动作浪费 ◆两手空闲 ◆单手空闲 ◆不连贯停顿 ◆幅度太大 ◆左右手交换 ◆步 行 多 ◆转身角度大 ◆移动中变换状态 ◆不明技巧 ◆伸背动作 ◆弯腰动作 ◆重复不必要动作 拿的动作交替 转身角度太 Lean 大 production
动作太大
精益的五个原则: 1、价值
精确地定义特定产品的价值;
◆搬运是一种无效的动作,但有些时候搬运也是必须的 ◆搬运浪费又包含放臵、堆积、移动、整理等动作的浪费
Lean production
□等待的浪费 就是闲着没事,等着下一个动作的来临,这种浪费是无 庸臵疑的。
◆工作量少时,员工便无所事事
◆生产线工序不平衡
◆有劳逸不均的现象 ◆下达生产命令不及时
◆开会占用太多时间
戴姆勒 430 1600 6
丰田 678 1290 101
Lean production
4、丰田生产方式的特征是什么?
Lean production
• 后序拉动前序 • 缩小批量,直至单件 流。 • 依照节拍整体同步
丰田屋
• 快速反应 • 防错机制
Lean production
准时化( JIT)
用精益的眼光看浪费
• 我们要做的事就是关注一个时间段:从客户发给我们订单到回 款的时间,通过消除不增值的浪费来减少这个时间段。 -------大野耐一
订 单 处 理 采 购 下 单 供 应 商 备 料 来 料 检 验 原 料 存 储 搬 运 和 等 待 检 验 及 返 工
识别价值, 制造周期 消除浪费
精益生产概论
一、精益的起源 二、精益思想与认识 三、精益的实施
Lean production
一、精益的起源
• 1、手工艺阶段 • 2、大规模生产阶段 • 3、精益生产阶段
Lean production
精益的起源 第1阶段——手工艺阶段
*只根据客户规定生产 *单件生产,产品唯一 *成本高
1876年前
Lean production 3
精益的起源
亚当· 斯密——劳动专业分工 • 1776年,亚当· 斯密发表了《国富论》。
提出了劳动专业分工
• 分配理论
F.W.泰勒——时间研究 • 19世纪末20世纪创建了“泰勒制” • 1911年 发表《科学管理原理》 • 科学管理之父 吉尔布雷斯夫妇——动作研究 • 吉尔布雷斯夫妇两人,改进了泰勒的方 法,我们称为“动作研究”。 • 吉尔布雷斯夫妇发明了一个“动素”的 概念,把人的所有动作归纳成17个动素, 对每个动素做定量研究。
交付周期
增值时间(Value added time)
运 输
加 工
成 品 存 储
成 品 发 运
货 款 回 收
增值比率
=
制造周期(Manufacturing cycle time)
X 100%
Lean production
浪费 MUDA
这是一个日语词汇,意思是浪费。
《现代汉语词典》定义
精益术语定义
对人力、财物、时间 等用得不当或没有节 制
Lean production
精益思想与认识
2、精益生产的目标是什么?
7个“
零
”
目标
☆ 零切换浪费 ☆ 零库存 ☆ 零浪费 ☆ 零不良 ☆ 零故障 ☆ 零停滞 ☆ 零事故
Lean production
精益思想与认识
3、企业为什么推行精益生产管理?
意外和明天不知道哪个先来, 没有危机才是最大的危机!
二、精益思想与认识
• • • • 1、什么是精益生产? 2、精益生产的目标是什么? 3、企业为什么推行精益生产管理? 4、丰田生产方式的特征是什么?
Lean production
精益思想与认识
1、什么是精益生产?
Lean Production
精益生产
1960年代开始,以丰田为代表的日本汽车制造业 通过实施JIT生产模式,以低成本、高质量的突出优 势迅速占领美国汽车市场,引发了美日之间长达十年 的汽车贸易战。 JIT——因其经营效率极限化被美国学者赞誉为 “精益生产”,并对人类的生产革命产生了长远影响。
• 拉动生产
Lean production
自働化(jidoka) • 自働化是指在制造过程出现异常时生产线自动停止 或作业员使之停止的能力,以防止不良流转。 自働化与自动化? *自働化的主要工具:ANDON
Lean production
1996年
1990年
1978年
1978年以前
Lean production
JIT即“just in time”,表示只在客户需要时提供给客户需要的产品的需要的 数量。 JIT三要素: ﹡节拍
* 单件流
* 拉动生产
Lean production
• T.T 节拍时间(Takt Time): 指制造一个零件所需要的时间,它随着顾客的需求不断变化,反应 整个制造的过程。
每日有效工作时间
计算公式:=
每日顾客需求数量
例:每日上班时间为8小时,顾客平均日需求为5000件,每日休息时间 为10分钟,维护时间为20分钟,节拍为多少?
THale Waihona Puke T==54秒Lean production
• 单件流(OPF) 单件流指的是当产品以顾客需要的速率通过整个生产流程时的一种状况
如何实现单件流?
Lean production
• 产品销量总是保持原地踏步怎么办? • 辛辛苦苦生产出来的产品卖到市场上没有利润或 者赔钱怎么办? • 假如明天的市场让你的产品降价50%怎么办?