发电机并联负载分配
负载分配器LSM672使用说明书
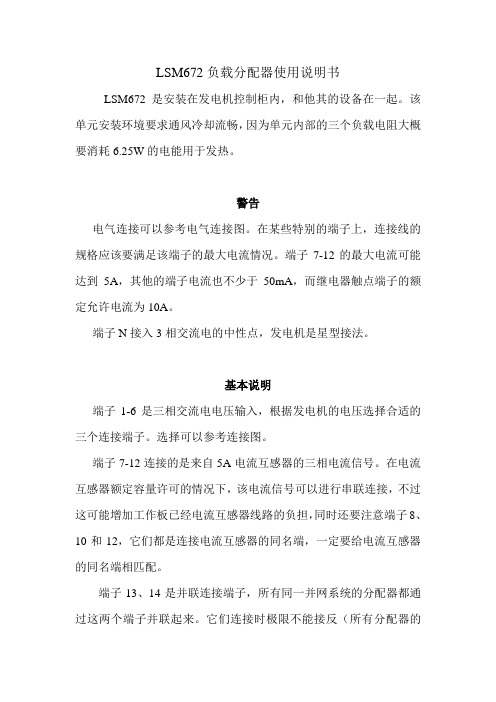
LSM672负载分配器使用说明书LSM672是安装在发电机控制柜内,和他其的设备在一起。
该单元安装环境要求通风冷却流畅,因为单元内部的三个负载电阻大概要消耗6.25W的电能用于发热。
警告电气连接可以参考电气连接图。
在某些特别的端子上,连接线的规格应该要满足该端子的最大电流情况。
端子7-12的最大电流可能达到5A,其他的端子电流也不少于50mA,而继电器触点端子的额定允许电流为10A。
端子N接入3相交流电的中性点,发电机是星型接法。
基本说明端子1-6是三相交流电电压输入,根据发电机的电压选择合适的三个连接端子。
选择可以参考连接图。
端子7-12连接的是来自5A电流互感器的三相电流信号。
在电流互感器额定容量许可的情况下,该电流信号可以进行串联连接,不过这可能增加工作板已经电流互感器线路的负担,同时还要注意端子8、10和12,它们都是连接电流互感器的同名端,一定要给电流互感器的同名端相匹配。
端子13、14是并联连接端子,所有同一并网系统的分配器都通过这两个端子并联起来。
它们连接时极限不能接反(所有分配器的13连在一块,14连在一块)。
如果并联线的长度超过1m,那么需要使用屏蔽线,并且把屏蔽线连接到端子23上。
继电器触点端子的连接必须要适用于低电流情况<1mA(干式触点)。
端子15是负载分配器的信号输出端,它连接发电机的速度控制单元,如果该控制线的长度超过1m,那么它也要使用屏蔽线,并且把屏蔽线连接到端子23上。
端子16是正功率复位端,使用一个常开的开关和发电机速度控制单元上的10VDC电源连接,当正功率继电器吸合后,通过点动连接开关,就可以把正功率继电器复位到正常的关闭状态。
通过端子16与电瓶的负极之间的不同连接方式,则可以通过端子16调节正功率监视器的范围。
例如在端子16与电源负极之间连接一个1MΩ的电阻,就可以把调节范围从100%是开启/40%时关闭调节成为85%开启/5%时关闭。
如果还有其他的特别调节需求,请和GAC的技术服务人员联系。
柴发并机运行要求
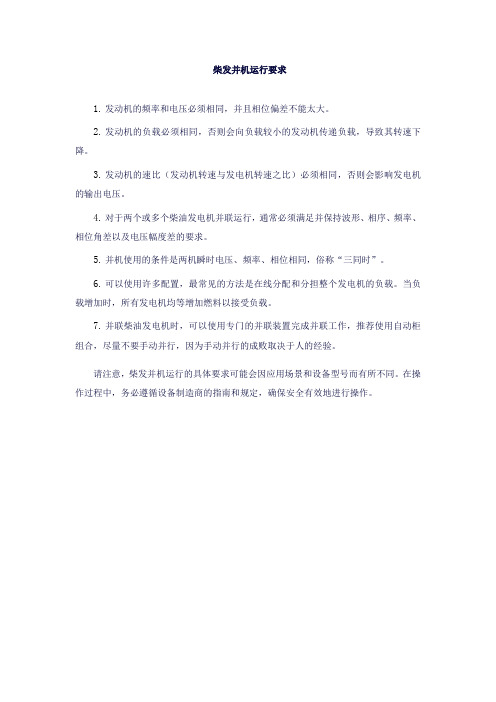
柴发并机运行要求
1.发动机的频率和电压必须相同,并且相位偏差不能太大。
2.发动机的负载必须相同,否则会向负载较小的发动机传递负载,导致其转速下降。
3.发动机的速比(发动机转速与发电机转速之比)必须相同,否则会影响发电机的输出电压。
4.对于两个或多个柴油发电机并联运行,通常必须满足并保持波形、相序、频率、相位角差以及电压幅度差的要求。
5.并机使用的条件是两机瞬时电压、频率、相位相同,俗称“三同时”。
6.可以使用许多配置,最常见的方法是在线分配和分担整个发电机的负载。
当负载增加时,所有发电机均等增加燃料以接受负载。
7.并联柴油发电机时,可以使用专门的并联装置完成并联工作,推荐使用自动柜组合,尽量不要手动并行,因为手动并行的成败取决于人的经验。
请注意,柴发并机运行的具体要求可能会因应用场景和设备型号而有所不同。
在操作过程中,务必遵循设备制造商的指南和规定,确保安全有效地进行操作。
发电机并联运行的条件
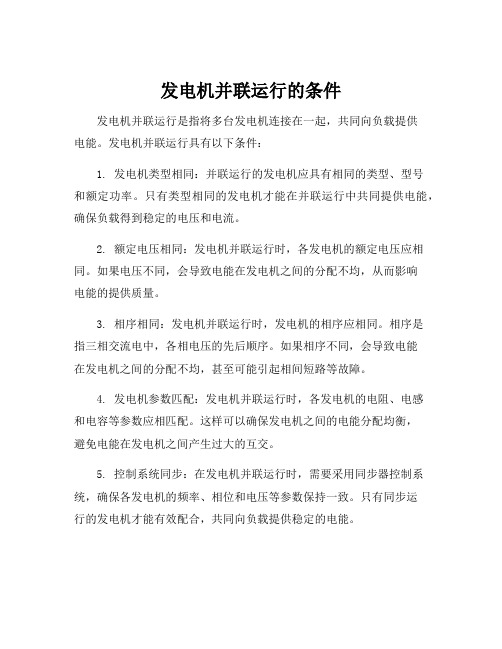
发电机并联运行的条件发电机并联运行是指将多台发电机连接在一起,共同向负载提供电能。
发电机并联运行具有以下条件:1. 发电机类型相同:并联运行的发电机应具有相同的类型、型号和额定功率。
只有类型相同的发电机才能在并联运行中共同提供电能,确保负载得到稳定的电压和电流。
2. 额定电压相同:发电机并联运行时,各发电机的额定电压应相同。
如果电压不同,会导致电能在发电机之间的分配不均,从而影响电能的提供质量。
3. 相序相同:发电机并联运行时,发电机的相序应相同。
相序是指三相交流电中,各相电压的先后顺序。
如果相序不同,会导致电能在发电机之间的分配不均,甚至可能引起相间短路等故障。
4. 发电机参数匹配:发电机并联运行时,各发电机的电阻、电感和电容等参数应相匹配。
这样可以确保发电机之间的电能分配均衡,避免电能在发电机之间产生过大的互交。
5. 控制系统同步:在发电机并联运行时,需要采用同步器控制系统,确保各发电机的频率、相位和电压等参数保持一致。
只有同步运行的发电机才能有效配合,共同向负载提供稳定的电能。
6. 负载均衡:发电机并联运行时,负载应均匀分配给各发电机。
负载不均衡会导致部分发电机过载或负载不足,影响发电机的运行稳定性和寿命。
7. 运行条件相同:发电机并联运行时,各发电机应处于相同的运行条件下,例如温度、湿度、海拔高度等。
不同的运行条件可能导致发电机之间的电能分配不均,甚至引起故障。
8. 保护系统完善:发电机并联运行时,应配置完善的保护系统,及时监测和保护各发电机的运行状态。
如果其中一台发电机出现故障,保护系统可以及时切除该发电机,确保系统的稳定和安全运行。
综上所述,发电机并联运行的条件包括发电机类型相同、额定电压相同、相序相同、发电机参数匹配、控制系统同步、负载均衡、运行条件相同和保护系统完善。
只有在满足这些条件的前提下,发电机并联运行才能有效实现,为负载提供稳定可靠的电能。
飞机电气系统:并联供电

控制 执 行 电路
触 发电 路
电网电压检测电路
检测电网上有无电压 当电网上无电压时,即没有其它发电机连
接在电网上,发电机可以立即投入电网 当电网上有电压时它不会输出合闸信号
自动并联检测电路
通过敏感发电机与电网之间的差值电压来 判断是否满足并联条件
当并联条件满足时,就会发出令发电机并 网的合闸信号
要求: △I=I1I2=0
负载均衡的概念
两台发电机并联,如 果两台发电机的输出电流相 等,各为负载电流的一半, 则称负载分配是均衡的。
5
负载均衡的条件
•两个调压器所保持的电压 相等,即U1=U2 •两台发电机的正线电阻相 等,即R+1=R+2
6
(二)提高负载分配均衡性的措施
• 两台发电机的转速不可能完全相同,引起U1与U2不可能完全相同
改变调节点的电压,提高负载分配的均衡性
2、发电机与蓄电池的并联运行
• 发电机投入已有蓄电池的飞机直流电网,需 满足的条件:
• 发电机极性必须与电网极性相同
• 发电机电压略高于电网电压(低于电网会有 反流,使发电机断开)
发电机蓄电池并联运行原理图
A
Ia
I
CJ
F
RL
G
B Ib
Eb
发电机与蓄电池电流分配图
交流发电机并联运行的优点
电压负载在供电的各发电机之间均匀分配; 多发电机系统中,一台发电机发生故障不会导致主系统
停止供电; 在某些使用条件下,安装容量在给定的时间-电压干扰特
性下,能满足更大的起动电流和尖峰负载的要求,同时 能更有效地利用发电机的安装容量; 并联系统可以使反延时的过流保护装置动作更迅速 。
• 各导线连接情况(拧紧、清洁状况等)不同,接触器电阻不同,引
发电机并联运行规程
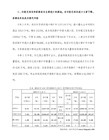
四、发电机是不能直接简单地并联运行的,涉及到两个发电机的频率和相位问题,主要是自同期与准同期问题.
5.发电机并列后,应将控制屏上的同期开关、手动准同期开关及同期闭锁开关的操作把手恢复原位,然后接带负荷,使发电机按正常运行方式运行。
三、为防止不同期并列,在下列三种情况时不准合闸:
1.组合式三相同期表S的指针转动不平稳而且有跳动现象,不准合闸。因为这可能其内部的接点有卡阻现象。
2.若组合式三相同期表S的指针在接近同期点时出现停滞现象,不准合闸。因为此时虽然满足并列条件,但由于开关操作机构动作需要约0.2秒的时间,若在此时间内发电机与电网之间的电压、周波及相角差有变化,则会使开关的合闸在不同期点上。
2.待并发电机的周波ff应与电网的周波f相等,但允许相差±0.05~0.1周/秒以内。若两者周波不等,则会产生有功冲击电流,其结果使发电机转速增加或减小,导致发电机轴产生振动。如果周波相差超出允许值而且较大,将导致转子磁极和定子磁极间的相对速度过大,相互之间不易拉住,容易失步。因此,在待并发电机并列时,必须调整周波至允许范围内。通常是将待并发电机的周波略调高于电网的周波,这样发电机容易拉入同步,并列后可立即带上部分负荷。
3.将6KP的“手动准同期开关”1STK左转至“粗调”位置,6KP的组合式三相同期表S就有了电压和周波的指示。此时,通过调整发电机的电压及频率,使之与电网的电压及频率相近或基本一致。
4.当发电机周波与电网周波相差在1.0周/秒以内时,将“手动准同期开关”1STK右转至“细调”位置,则组合式三相同期表S的线圈得电,指针开始缓慢地顺时针方向转动。此时,应根据电压、频率的指示,更精细的调整待并发电机的频率。为了使待并发电机并列后可立即带上部分负荷,应使待并发电机的频率稍大于同期频率。同时,将待并开关(5KP的121或6KP的101)的操作把手置于“预备合闸”位置,做好并列合闸的准备,这时开关的绿色指示灯发出闪光。待指针快接近同期点时(考虑到开关操作机构有大约0.2秒的动作时间),迅速将待并开关(121或101)的操作把手右转至合闸位置,此时该开关的红色指示灯发平光,绿色指示灯熄灭,这表明待并发电机并列成功。
3.5并联运行发电机的有功功率分配和频率调节
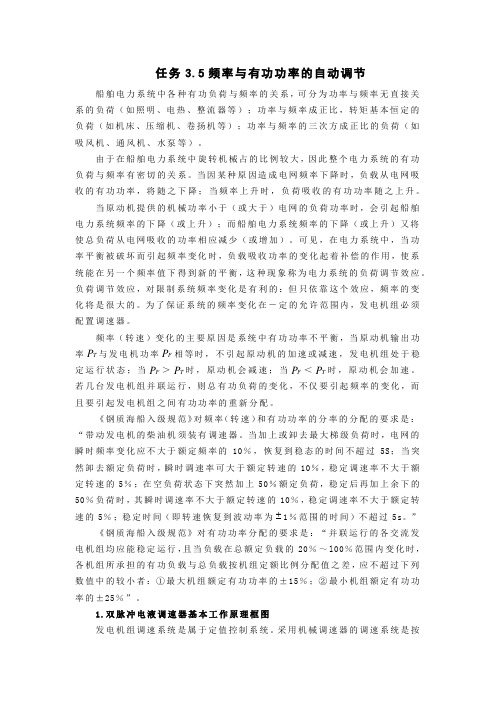
任务3.5频率与有功功率的自动调节船舶电力系统中各种有功负荷与频率的关系,可分为功率与频率无直接关系的负荷(如照明、电热、整流器等);功率与频率成正比,转矩基本恒定的负荷(如机床、压缩机、卷扬机等);功率与频率的三次方成正比的负荷(如吸风机、通风机、水泵等)。
由于在船舶电力系统中旋转机械占的比例较大,因此整个电力系统的有功负荷与频率有密切的关系。
当因某种原因造成电网频率下降时,负载从电网吸收的有功功率,将随之下降;当频率上升时,负荷吸收的有功功率随之上升。
当原动机提供的机械功率小于(或大于)电网的负荷功率时,会引起船舶电力系统频率的下降(或上升);而船舶电力系统频率的下降(或上升)又将使总负荷从电网吸收的功率相应减少(或增加)。
可见,在电力系统中,当功率平衡被破坏而引起频率变化时,负载吸收功率的变化起着补偿的作用,使系统能在另一个频率值下得到新的平衡,这种现象称为电力系统的负荷调节效应。
负荷调节效应,对限制系统频率变化是有利的:但只依靠这个效应,频率的变化将是很大的。
为了保证系统的频率变化在―定的允许范围内,发电机组必须配置调速器。
频率(转速)变化的主要原因是系统中有功功率不平衡,当原动机输出功P与发电机功率F P相等时,不引起原动机的加速或减速,发电机组处于稳率TP>T P时,原动机会减速;当F P<T P时,原动机会加速。
定运行状态;当F若几台发电机组并联运行,则总有功负荷的变化,不仅要引起频率的变化,而且要引起发电机组之间有功功率的重新分配。
《钢质海船入级规范》对频率(转速)和有功功率的分率的分配的要求是:“带动发电机的柴油机须装有调速器。
当加上或卸去最大梯级负荷时,电网的瞬时频率变化应不大于额定频率的10%,恢复到稳态的时间不超过5S;当突然卸去额定负荷时,瞬时调速率可大于额定转速的10%,稳定调速率不大于额定转速的5%;在空负荷状态下突然加上50%额定负荷,稳定后再加上余下的50%负荷时,其瞬时调速率不大于额定转速的10%,稳定调速率不大于额定转速的5%;稳定时间(即转速恢复到波动率为 1%范围的时间)不超过5s。
柴油发电机组运行论文
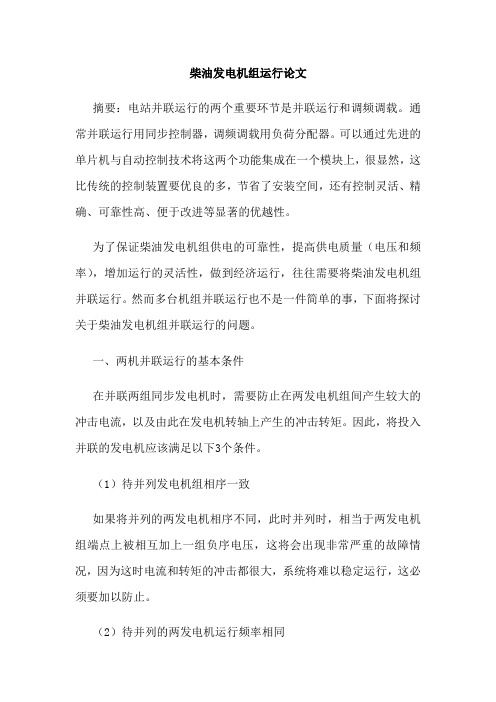
柴油发电机组运行论文摘要:电站并联运行的两个重要环节是并联运行和调频调载。
通常并联运行用同步控制器,调频调载用负荷分配器。
可以通过先进的单片机与自动控制技术将这两个功能集成在一个模块上,很显然,这比传统的控制装置要优良的多,节省了安装空间,还有控制灵活、精确、可靠性高、便于改进等显著的优越性。
为了保证柴油发电机组供电的可靠性,提高供电质量(电压和频率),增加运行的灵活性,做到经济运行,往往需要将柴油发电机组并联运行。
然而多台机组并联运行也不是一件简单的事,下面将探讨关于柴油发电机组并联运行的问题。
一、两机并联运行的基本条件在并联两组同步发电机时,需要防止在两发电机组间产生较大的冲击电流,以及由此在发电机转轴上产生的冲击转矩。
因此,将投入并联的发电机应该满足以下3个条件。
(1)待并列发电机组相序一致如果将并列的两发电机相序不同,此时并列时,相当于两发电机组端点上被相互加上一组负序电压,这将会出现非常严重的故障情况,因为这时电流和转矩的冲击都很大,系统将难以稳定运行,这必须要加以防止。
(2)待并列的两发电机运行频率相同假如发电机的频率不相同,则三相所对应的电压在大部分时候都不相等,以至于两边对应的相量间相位差将会在0°~360°之间不断变化,电压差值也不断地在0~2UN之间改变。
而且频率相差越大,这个变化的速度就会越快,若此时合闸,必然会产生冲击电流以及冲击转矩,这将使并列后两发电机组达到同步稳定的过程时间加长甚至难以达到稳定运行。
(3)待并列的两发电机端电压相等电压相等应该包括相位相同、频率一致和有效值三者相等,即相量相等。
通常大型同步发电机的转向和相序在出厂之前都已标定其相序。
对于没有明确标明转向和相序的发电机,可以使用相序指示器来确定。
而调节原动机的转速和发电机的励磁电流就可以调节频率的高低和电压的大小,在通过调节发电机的瞬时速度可以调整电压的相位。
此调节过程也称为整步过程,即为了将发电机投入电网并联所运行的调节和操作过程。
柴油发电机组并联运行.课件

优化负荷分配
根据负荷情况,可以自动或手动调 整并联运行机组的出力,使各机组 负荷分配更加合理,从而提高运行 效率。
提高设备利用率
当部分机组需要维修或保养时,可 以将其并联到其他机组,从而保持 整体供电能力不受影响。
并联运行的风险
相位差问题
多台柴油发电机组并联运行时, 如果各机组的相位差较大,可能 会导致电流波动和设备损坏。因 此,需要确保各机组相位一致。
设备备份
对于重要的工业设备,柴油发电机组并联运行可以提供备份电源,当主电源出现故障时, 可以迅速切换到备用电源,保证设备正常运行。
峰值负载
工业生产过程中会有一些峰值负载,柴油发电机组并联运行可以提供足够的电力来满足这 些峰值负载的需求。
家庭应用场景
1 2 3
家庭备用电源 在家庭中,柴油发电机组并联运行可以作为备用 电源,当主电源出现故障时,可以保证家庭的正 常供电。
并联运行需要满足一定的条件,例如各柴油发电机组的输出电压和频率必须保持一 致,输出相位差不能超过允许范围等。
并联运行的稳定性问题
并联运行的稳定性问题是指当系 统受到扰动或负载发生突变时, 各柴油发电机组之间的输出电流 分配可能会出现不均衡的情况。
当输出电流的不均衡程度超过一 定限制时,会导致某台柴油发电 机组过载或欠载,严重时甚至会
农村电力供应 在农村或偏远地区,柴油发电机组并联运行可以 作为主要的电力供应方式,满足居民的电力需求。
移动电源 柴油发电机组并联运行可以作为移动电源,为野 外作业、抢险救灾等提供可靠的电力供应。
总结与展望
并联运行的意义与价值
提高供电可靠性
01
通过并联运行,多台发电机组可以互为备用,当其中一台出现
- 1、下载文档前请自行甄别文档内容的完整性,平台不提供额外的编辑、内容补充、找答案等附加服务。
- 2、"仅部分预览"的文档,不可在线预览部分如存在完整性等问题,可反馈申请退款(可完整预览的文档不适用该条件!)。
- 3、如文档侵犯您的权益,请联系客服反馈,我们会尽快为您处理(人工客服工作时间:9:00-18:30)。
PARALLEL OPERATION WITH A NETWORK SYSTEMThe purpose of this discussion is to address the concerns of and the techniques required to successfully parallel synchronous generators to a network.A network consists of two or more buses connected together by one or more power lines whose impedance compared to the capacity of the network generating capacity cannot be neglected. Contrast this definition with that of a bus whose impedance is so low that it can be neglected. This difference makes analyzing the network's flow of current and the volt-age drop calculations much more difficult than the paralleled generators with loads all connected to a common bus. When we are able to neglect the bus resistance and reac-tance, the solution to current flow and voltage drops is very simple. Large electric power systems typical of our electric utility can only be analyzed by considering them to be net-work systems. It would not be economically feasible to transport power the way utilities currently do if the connections between loads and generators were required to have resis-tance and reactance negligible compared to the system capacity. With the capacity of computers to perform complex calculations very quickly, however, the analysis of power system load flow is greatly simplified compared to the slide rule days.Figure 1: Paralleled SystemsOne way to simplify the analysis of network operation is to adopt the concept of "infinite bus" for the network. This assumption can be used if the capacity of the network at a point of interconnection is at least 10 times greater than the capacity of equipment connecting to the network. The concept holds true when the network voltage and frequency are not changed when real and reactive currents change at the point of connection. An example is a generator connected to a network, with generator size of 100kW and the connection point being an industrial plant served by a 10MVA transformer. With the transformer being fed from a line having a capacity of 150MVA, any changes in load flow caused by fuel or excitation changes at the 100kW generator will have no measurable effect on the voltage and frequency of the transformer secondary. This is also referred to as the stiffness of the grid.Figure 2: Typical Paralleled SystemT o control the real power flow from the 100kW generator, the problem has changed from the load sharing scheme needed for multiple generators serving an isolated load. Now the control scheme must regulate the real power load from the generator to the plant bus based on some other criteria than just load sharing. To perform this function, another block is added to the basic control loop of the speed governor establishing a desired kW load setpoint and adjusting fuel to the prime mover to maintain load at the setpoint value. Since this control loop is closed, stability of the control system must be provided for. The block diagram in Figure 3 illustrates a common way of providing the second control loop for regulating real power load. The setpoint may be a fixed value at or near full load, a control system designed to maintain steam pressure to a varying load while using the excess capacity of the prime mover to generate electricity, or to keep the utility power supply below some maximum demand limit. By regulating the generator load kW, any variation in frequency from the network will cause only momentary deviation in real load until the control loop senses the deviation in load and corrects by adjusting fuel.Figure 3: Alternative Control StrategyT o help explain this approach, let's review some basic governor controls.Parallel Operation Of The Governor And Real PowerIn paralleling multiple generators it is important to recognize that there are two fundamen-tal control loops: the governor control loop and the voltage regulator control loop. Thegovernor controls the real power portion of the generator, kW=EL-L *3*1*cosφ. 1000First, let's discuss the governor controls.DefinitionsBefore one can fully retain the information to be presented, it is imperative to recognize and understand the following terms.A: Droop: Refer to Figure 4. When a prime mover has a droop governor, the prime mover simply decreases in speed as load is applied. A droop governor will usually have between 3% to 10% droop. Figure 4 illustrates a governor with 3.3% droop. Notice the no load speed is set to 62 hz and at full load the prime mover’s speed has decreased to 60 hz.Figure 4: Droop Governor (3.3% droop)B: Isochronous: Refer to Figure 5. When an engine has an isochronous governor, the prime mover will maintain its set speed throughout its entire horsepower range. An isoch-ronous governor is said to have zero droop. Figure 5 illustrates a governor with zero droop. Notice the no load speed is set at 60 hz and at full load the prime mover’s speed remains at 60 hz.Figure 5: Isochronous GovernorC: Real Power is horsepower produced from the prime mover converted to kilowatts by the generator. KW=E L-L * 3*1*cos φ. In this formula, cos φ is the power factor. 1000D: Reactive Power is the power that is required by the inductive and capacitive loads. In a purely resistive load there is no reactive power. In a paralleled system the generators can produce reactive power which circulates among the generators called circulating current.Circulating currents are not desired and are controlled by the generator excitation.Paralleling Generators with Droop GovernorsSystems produced today seldom are designed with droop. This is because most loads require the generator frequency to remain constant and, as defined, droop governors decrease in speed with an increase in load.The operation of synchronizing requires that the generator’s voltage, frequency and phase have to be matched and a circuit breaker tying the generators together be closed. This magnetically locks the generators together, forcing them to operate at the same speed. All that has to be done now is to control the power distributed between the generators. The power required by the load is fixed.With the prime movers equipped with droop governors, it is important that both governors be set the same if the generators are expected to share load equally. This means each one has to be set to the same speed. Each one has to be calibrated with the same percentage of droop. With the speed and droop set the same, the prime movers will equally share the load. Refer to figure 6.With droopgovernors, theportion of loadsupplied by eachgenerator iscontrolled.Figure 6: Paralleling Generators with Droop GovernorsFigure 6 illustrates the droop curve and load of two paralleled generators. Notice the simi-larity between this figure and Figure 4. The difference is that we have added the second governor curve and the vertical axis is labeled both “speed” and “power”. The addition of power illustrates that when the speed setting is increased on one paralleled generator, that generator will assume a greater portion of load. The inverse occurs when the speed setting is decreased on a paralleled generator. When the speed setting is changed in relationship to the speed setting of the other generator, the actual speed of the prime mover does not vary from the other generator. The torque from the prime mover is changed, thus changing the power output.The question may be asked: How are the mechanical governors capable of sharing the load? This can simply be determined by analyzing the performance (droop) characteristics of the mechanical governor. Refer to Figures 7 through 10.Figure 7 shows two generators, each with a droop governor. As load varies, the kW de-mand changes cause the generator speed to follow the droop curve, decreasing speed as load increases and increasing speed as load decreases.Passes above63Hz at 0%load, 60Hz at100%.Figure 7: Droop CurvesFigure 8: Loading of GeneratorsT o parallel the second generator with generator 1 operating at 100% load and 60Hz, the normal synchronizing method matches generator frequency (speed) to the bus (Gen 1). This adjustment of the speed setting causes the droop curve to be in the position shown in Figure 8 at the time of breaker closure, operating at 60Hz and no load.As the load on generator #2 is increased, the load on generator #1 decreases. As the load on #1 decreases, the speed increases. When generator #2 is at 25% load, generator #1 is loaded to 75% and the speed is at approximately 59.8Hz. As the loads are balanced to 50/50 each generator, the speed has increased to 61.5Hz. At this point both generators are at the same relative load and speed. An operator must then decrease both governor setpoints down to 60Hz.Figure 9: Balanced LoadAt this point, if the total load increases, the governors will share the increase proportion-ately. If generator #2 tries to take more of the load, its speed setting is raised.By raising its speed setting, generator #2 picks up some load from generator #1, due to the shift of the droop curve of generator #2 and the action of the droop curve of generator #1. With only two generators in parallel, the total kW demand of the load must come from the two generators, so the sum of the kW supplied by the two generators must equal the load kW. In addition, by the action of paralleling, the two generators must maintain exactly the same frequency. Any increase in power output from one of the generators results in a corresponding decrease in speed, based on the droop curve. The other unit will not allow the decrease in speed because its droop curve, seeing a decrease in load, attempts to increase the speed setting, keeping them in balance.As the total load increases from 50% to 100%, the paralleled generators will share the load equally but the system frequency will decrease along the droop curves as in Figure 10.Figure 10: Load ChangesThis is a dynamic system with power demand constantly changing on the system. The droop characteristics of the mechanical governors are a stabilizing mechanism in a parallel system. Simply put, as load attempts to change among the generators the droop governor stabilizes and proportions the load.Paralleling Generators with Isochronous GovernorIsochronous governing has became the governor of choice in today’s industry. The reason is the governor’s ability to maintain a constant set speed throughout the prime mover’s power range.Unlike droop governors, isochronous governors by themselves are not capable of control-ling paralleled generators. Isochronous governors require additional controls to be ca-pable of paralleling. These controls will be discussed later in this document. At this time it is important to understand why isochronous governors by themselves cannot be paral-leled.Figure 11 illustrates two generators running independently. The speed on generator #1 is set at 60Hz. The speed on generator #2 is set to 60.2Hz. Remember, isochronous gover-nors are designed to control at exactly their set speed. If these generators were paralleled, the generators would be forced to match speeds. Generator #1 would be pulled up to 60.1Hz and generator #2 would be pulled down to 60.1Hz. The governor on generator #1 would sense the actual speed to be too high and the governor on generator #2 would sense the actual speed to be too low. Governor 1 would respond by reducing fuel and governor 2 would respond by increasing fuel. The effect would be generator #2 taking all the load and motorizing generator #1.Figure 11: Generators Running IndependentlyIn order to parallel isochronous generators, it is necessary to add controls to each governor. These controls are designed to measure the real power out of each generator and com-pare the measured value with total load via the load lines. If the power levels are unbal-anced, the added controls send a power setting output to the speed input of the isochro-nous governor. The governor will increase or decrease the power of the prime mover to share the load properly between all paralleled generators. Refer to Figure 12 for a visual diagram of a typical load sharing system.Figure 12: Typical Load Sharing SystemParalleling Generators T o An Infinite BusWhen paralleling generators to an infinite bus there are two systems used. System 1 holds kW load of the generator bus constant and allows the utility to provide the remainder of the load demand. System 2 reverses this action, holding the utility bus kW load constant and forcing the generator bus to provide the remainder of the load demand.System 1Implementing system 1 requires addition of a load control module. To set the power level for system 1, a load control module is added to the load sharing controls that biases the communication lines which balance the load between generators. For example. if the voltage on the communication lines is 0 to 3 volts dc, adding a linear signal with 0 volts being no load and 3 volts being maximum rated load of the generator sets changes the load on all paralleled generators simultaneously. If one wants the generator system to produce 50% of rated load, a 1.5 volt dc signal is biased to the communication lines.System 1 is not desirable in all applications. A problem arises if the load’s power level drops below the generator bus set level. The generator bus will export power into the Utility network.Figure 13: System 1 (Generator Bus Constant)System 2System 2 control requires additional hardware compared to system 1. Controls are added to the utility to monitor the power level imported. These controls compare a set power level to an actual power level and adjust the bias to the load lines. The adjustment to the com-munication lines forces the generator bus to increase power out when load increases and decrease power out when load is decreased. This dynamic action controls the generator bus output while holding the utility at a constant power level. Unlike system 1 where power can be exported, system 2 prevents power from being exported into the utility.Figure 14: System 2 (Utility Bus Constant)Frequency variations in U.S. power networks are normally very small unless a lack of sufficient generating capacity occurs due to malfunctions of the system. If the frequency of the network should change significantly, the small generator has no choice but to follow, with tripping of protective relays disconnecting it very quickly to avoid damage to the machine when frequency exceeds normal operating conditions.If the generator is a large utility plant, the real power load is dispatched or controlled by an operator to keep the network frequency at 60 Hz and to share the load between plants. The utility practices good economy by taking the power demand from those plants able to supply the power at lowest cost per kWh (Kilowatt hour). On large systems, the solution to providing power at lowest production cost requires a sizable computer with a model of the network to continually evaluate the load demand and its location on the network in order to shift the generation of the power among the plants. When the solution to the needs is calculated, the dispatcher calls for power to be supplied from the plants, either by remote control to each plant or by sending dispatch requirements to the plant operators. Load profiles are well established for normal workdays, weekends, etc. so the problem can be solved for a given profile, and each plant can follow the profile until some deviation re-quires a change in operating instructions. In large utility plants the network voltage and frequency are affected by changes in the plant load levels, making it necessary to solve the load flow of the network in order to keep the network operation within acceptable power quality limits.Parallel Operation of the Excitation SystemT o control the reactive power from the 100kW generator, a similar control loop to the speed governor kW regulator is used to measure one of two parameters of the generator; the first is reactive power flow, measured by current and voltage transformers connected in quadrature exactly like the arrangement in the droop circuit. By comparing the measured kvar load with the setpoint, adjustable for leading or lagging reactive load, the generator will supply a constant reactive current to the bus regardless of load demand and variation in bus voltage.T o help understand what we are discussing, the power triangle is a good tool to use. Across the bottom axis is the real power expressed in Watts or Kilowatts (W or kW). Along the hypotenuse of the triangle is the apparent power expressed in Volt Amp or Kilovolt Amp (VA or kVA). The reactive power is the third leg of the triangle and is expressed as Volt Amperes reactive or Kilovolt Amperes Reactive (VArs or kVArs).The cosine of the angle is referred to as a Power Factor, a measure of the ratio of reactive power to resistive power. For power factor of 1.00, the current is in phase with the voltage, and the reactive load is zero. Power factor of 0.8 is the rating of most small to medium size generators, indicating that it is designed to deliver 80% of rated current as resistive load, and 60% of load current as inductive reactive load current (0.8 is cosine of 36.9 degrees, sine of 36.9 degrees is 0.6). This rating of the machine indicates the thermal capability of the stator windings on a continuous basis at maximum ambient temperature. This rating also indicates the thermal capability of the rotor windings on a continuous basis at maxi-mum ambient temperature. The machine voltage and frequency rating give the thermal rating of the core of the machine at maximum voltage and nominal speed.Figure 15: Power TriangleT wo parameters, reactive power and power factor, are the ones that the excitation system can control. The question is then raised as to how this is done. One approach is to treat the infinite source as another generator to be paralleled to and connect the voltage regula-tor in the droop mode.Figure 16: Typical Droop ConnectionIn this method, the droop adjustment is made just as if the generator were paralleled with another generator. If there is also a step up transformer between the generator and the grid, this approach works even better due to the impedance of the transformer. Adding droop to the voltage regulator is, in a sense, like adding impedance to the line, so a large transformer helps in this type of paralleling. If the grid is not very stiff, then paralleling in the droop mode may be satisfactory. This way, an operator can monitor and make adjust-ments as required to maintain bus voltage and reactive load sharing.Now the question is asked that if generators can be paralleled with the regulators in the droop mode, can I parallel with the regulators connected in reactive differential or cross current. The answer to this is that it is not recommended. If we review what a cross current loop looks like to the voltage regulators, we can see why. Since the regulators connected in cross current expect that a change in its compensation circuit will cause a change in the other circuits, there will not be a change in the infinite grid no matter what the regulator does.Figure 17: Cross Current CompensationSince many generator power systems must support load in a mode not paralleled to the grid and at some point will also parallel with the grid, how can the systems be connected in cross current? The answer is that the cross current connections may be disabled when the main tie breaker is closed. Breaking the loop in any one spot will disable the cross current compensation. An example is as follows:Figure 18: Scheme to Disable Cross CurrentIt may seem that connecting the regulators in droop to parallel to the grid is the best way to operate. However, compared to the frequency, bus voltage is subject to much greater variation, and the source of the variation may be local changes in load or network voltage variations which occur because of line losses changing with load or changes in network operating voltage from daytime to nighttime levels. Regardless of the cause, the effect on a droop compensated generator would be changing reactive load levels. Most regulators have a maximum 6-8% droop setting. If the grid voltage goes higher than the droop set-ting, the regulator decreases its output and a generator is paralleled and must start import-ing VArs to operate at the high bus voltage level. This could cause the generator to be-come underexcited, start slipping poles, and become damaged.Conversely, if the voltage on the grid decreases, the regulator tries to drive the voltage back to its setpoint. Since by definition the grid is infinite, the generator cannot restore the voltage. As the excitation increases the generator starts exporting VArs into the grid. This situation can cause excess heating of the generator rotor windings as well as the distribu-tion transformer. This is a potentially damaging situation for the generator.Automatic VAr/Power Factor RegulationAdding a var regulator to the excitation system and operating in the var regulation mode allows maximum utilization of the generator reactive load capability independent of real power load. Alternatively, the var regulator may be set to maintain the generator reactive load at zero, if the vars are not bringing in revenue, to keep the generator as cool as pos-sible while supplying the revenue-producing real power to the load. With VAr regulation, the changes in bus voltage which can cause VAr load variations are compensated by adjustment to the avr setpoint voltage. The result is a constant VAr load on the generator without any operating intervention.Figure 19: Alternative Control StrategyThe second type of control loop measures the power factor or the angle of generator current with relation to the voltage. In this control mode, the reactive load is regulated as a percentage of the real power load, tracking any changes in real power to keep the percent-age constant. This form of control is often preferred by operating personnel trained to keep the power factor constant in their manual control practices. Many generators are equipped with a power factor meter and a kW meter in addition to volts, amps and frequency. In this configuration, a var regulator can produce some readings on a pf meter which will alarm some operators trained to keep power factor to 0.8 or higher. However, use of var regula-tion does not add any risk to the generator if operating at rated kvar and 10% of rated kW. The power factor of this load is 0.54 pf at 84% of rated generator current. The generator is able to operate safely under at this condition. Power factor regulation may be selected as a control option if desired, but by replacing the traditional power factor meter with a var meter and regulating the reactive load, better use of machine capacity may result.There are three basic ways to add VAr/power factor regulation to an excitation system. They are:1)Add additional component to the system,2)Integrate VAr/Power factor control into the regulator itself, and3)Programmable Logic Controller.No matter which approach is used, the technique is doing one of the following:As angle changes, the power factor changes.Figure 20: Constant kVAR LevelAs the kW changes, the angle stays the same, the kVAR level changes. Since we are regulating the angle, the cosine of the angle stays the same.Figure 21: Constant Power factor LoadAdding an additional component to the excitation system is relatively easy. A basic block diagram is shown in Figure 22.Figure 22: VAR/PF Controller with Static ExciterFigure 23 shows the faceplate of the Basler Electric SCP-250. Setting on the SCP-250 is from .6 power factor leading to .6 power factor lagging when in the power factor control mode.Figure 23: SCP-250 FaceplateIn the VAr control mode the adjustment is either to produce or absorb VArs. The VAr range adjustment sets up the limits at either end of the potentiometer travel.Figure 24 illustrates a generator that is equipped with a solid state voltage regulator having reactive voltage droop compensation. The graph illustrates the effect of bus voltage changes on the reactive/ampere load on the generator. If the bus voltage drops by 6%, the reactive/ampere generator load will change from 0 - 75%. A further decrease in bus voltage exceeding 4% would overload the generator, causing excessive heating in the field wind-ing as well as the power semiconductors of the automatic voltage regulator. The VAr/PF controller regulates at a programmed operating point and is insensitive to changes in the bus voltage. Field heating increases (higher excitation current) as lagging reactive load increases. Keeping the lagging VAr load under control protects the generator field from overheating. This function can be performed by an operator, or the VAr/PF controller auto-mates the control function.Figure 24: Voltage Regulator Droop versus Var/PF Control RegulationFigure 24 also illustrates the condition where the bus voltage may increase, causing a leading power factor condition on the generator. Here, the voltage regulator will decrease excitation following the characteristic slope of the reactive compensation circuit. This will keep the system in synchronism. If the bus voltage rises excessively, however, leading VAr load will increase, leading to a reduction in the field excitation and causing possible loss of machine synchronism.The other two techniques used to regulate VArs or power factor follow the same basic connections of the voltage and current sensing as well as control. There is a voltage input and a current input at some phase angle difference as well as a means to turn the control on/off. As with the SCP-250, this is typically a 52b control off the main tie breaker.In PLC (Programmable Logic Controller) control, the excitation is sometimes controlled by a DC input into the regulator similar to the SCP-250. However, sometimes the PLC will have output contacts to control a motor operated potentiometer or reference adjuster to change the regulator's setpoint to change excitation. The only potential drawbacks to this ap-proach are the coordination of the overall control loop so stability is achieved and the wear and tear of a constantly moving M.O.P. or reference adjuster.There are other uses for VAr/power factor regulation. One is kVA control.kVA ControlIn some industrial applications such as paper mills, large induction motor loads may exist. Precious VArs are robbed from the system resulting in low power factor. Cost penalties are also often realized because of this low power factor. T o improve the plant power factor, capacitors are often utilized across the line to restore kVArs. This method is very effective, but also very expensive. For paper companies where power plant generation is available, it may be desirable for these generators to restore kVArs in the system by forcing them to operate overexcited along the kVA limit of the generator. The method enables maximum utilization of the generator, especially when available kilowatts are minimum.A kVA controller is connected so the sensed voltage is shifted 30 degrees leading from the normal quadrature connection. Referencing Figure 25, an advantageous locus of operat-ing points is obtained. As kW load decreases, the vector 0-D moves to 0-C, O-B, and finally 0-A approximately following the kVA limit of the generator. Armature and field current at0-A is slightly greater than 0-B. The lagging kVAr has increased almost 50%, providing greater utilization of the machine. The capability curve suggests that rotor field heating may occur at minimum kilowatts. Therefore, the use of a maximum excitation limiter is suggested to override the kVA controller at exceedingly low values of kW to help ensure safe rotor field heating. The system offers a benefit in improved power factor because of the 50% increase in lagging kVAr. The percent improvement in power factor is determined by the amount of kilowatt load on the generator. The more kilowatt load, the less kVA for var improving.The VAr/Power Factor Controller regulates at a programmed quantity of VAr or power factor to assure sufficient excitation on the field under all types of load.Figure 25: Generator Capability Curve。