累积叠轧焊制备的Cu-Nb层状复合材料织构演变
纳米叠层金属基复合材料的力学行为
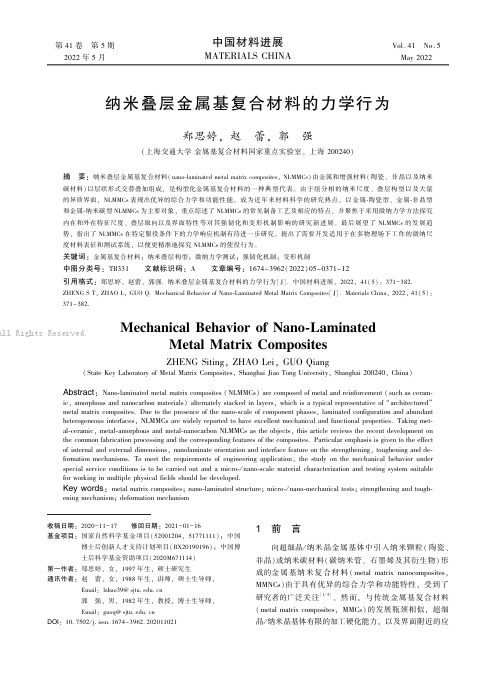
㊀第41卷㊀第5期2022年5月中国材料进展MATERIALS CHINAVol.41㊀No.5May 2022收稿日期:2020-11-17㊀㊀修回日期:2021-01-16基金项目:国家自然科学基金项目(52001204,51771111);中国博士后创新人才支持计划项目(BX20190196);中国博士后科学基金资助项目(2020M671114)第一作者:郑思婷,女,1997年生,硕士研究生通讯作者:赵㊀蕾,女,1988年生,讲师,硕士生导师,Email:lzhao39@郭㊀强,男,1982年生,教授,博士生导师,Email:guoq@DOI :10.7502/j.issn.1674-3962.202011021纳米叠层金属基复合材料的力学行为郑思婷,赵㊀蕾,郭㊀强(上海交通大学金属基复合材料国家重点实验室,上海200240)摘㊀要:纳米叠层金属基复合材料(nano-laminated metal matrix composites,NLMMCs)由金属和增强材料(陶瓷㊁非晶以及纳米碳材料)以层状形式交替叠加组成,是构型化金属基复合材料的一种典型代表㊂由于组分相的纳米尺度㊁叠层构型以及大量的异质界面,NLMMCs 表现出优异的综合力学和功能性能,成为近年来材料科学的研究热点㊂以金属-陶瓷型㊁金属-非晶型和金属-纳米碳型NLMMCs 为主要对象,重点综述了NLMMCs 的常见制备工艺及相应的特点,并聚焦于采用微纳力学方法探究内在和外在特征尺度㊁叠层取向以及界面特性等对其强韧化和变形机制影响的研究新进展㊂最后展望了NLMMCs 的发展趋势,指出了NLMMCs 在特定服役条件下的力学响应机制有待进一步研究,提出了需要开发适用于在多物理场下工作的微纳尺度材料表征和测试系统,以便更精准地探究NLMMCs 的使役行为㊂关键词:金属基复合材料;纳米叠层构型;微纳力学测试;强韧化机制;变形机制中图分类号:TB331㊀㊀文献标识码:A㊀㊀文章编号:1674-3962(2022)05-0371-12引用格式:郑思婷,赵蕾,郭强.纳米叠层金属基复合材料的力学行为[J].中国材料进展,2022,41(5):371-382.ZHENG S T,ZHAO L,GUO Q.Mechanical Behavior of Nano-Laminated Metal Matrix Composites[J].Materials China,2022,41(5):371-382.Mechanical Behavior of Nano-LaminatedMetal Matrix CompositesZHENG Siting,ZHAO Lei,GUO Qiang(State Key Laboratory of Metal Matrix Composites,Shanghai Jiao Tong University,Shanghai 200240,China)Abstract :Nano-laminated metal matrix composites (NLMMCs)are composed of metal and reinforcement (such as ceram-ic,amorphous and nanocarbon materials)alternately stacked in layers,which is a typical representative of architectured metal matrix composites.Due to the presence of the nano-scale of component phases,laminated configuration and abundant heterogeneous interfaces,NLMMCs are widely reported to have excellent mechanical and functional properties.Taking met-al-ceramic,metal-amorphous and metal-nanocarbon NLMMCs as the objects,this article reviews the recent development on the common fabrication processing and the corresponding features of the composites.Particular emphasis is given to the effect of internal and external dimensions,nanolaminate orientation and interface feature on the strengthening,toughening and de-formation mechanisms.To meet the requirements of engineering application,the study on the mechanical behavior under special service conditions is to be carried out and a micro-/nano-scale material characterization and testing system suitable for working in multiple physical fields should be developed.Key words :metal matrix composites;nano-laminated structure;micro-/nano-mechanical tests;strengthening and tough-ening mechanism;deformation mechanism1㊀前㊀言向超细晶/纳米晶金属基体中引入纳米颗粒(陶瓷㊁非晶)或纳米碳材料(碳纳米管㊁石墨烯及其衍生物)形成的金属基纳米复合材料(metal matrix nanocomposites,MMNCs)由于具有优异的综合力学和功能特性,受到了研究者的广泛关注[1-5]㊂然而,与传统金属基复合材料(metal matrix composites,MMCs)的发展瓶颈相似,超细晶/纳米晶基体有限的加工硬化能力,以及界面附近的应All Rights Reserved.中国材料进展第41卷变局域化导致了MMNCs强度的提高通常伴随着均匀延伸率的下降,即存在强度-塑(韧)性倒置关系,很大程度上制约了其进一步的发展与应用[6-8]㊂复合构型化(即不改变基体和增强体成分,仅仅改变基体和增强体的尺寸和空间分布)是解决MMNCs强韧化矛盾㊁提升其综合性能的有效途径[9-12]㊂纳米叠层结构是自然界硬质生物材料广泛采用的复合构型㊂通过组分相的纳米尺度,叠层构型提供的几何约束效应,以及各种内在和外在韧化机制,能够破解强韧性倒置的难题[13,14]㊂受此启发,研究者们开发了具有优异力学性能的金属-陶瓷[15]㊁金属-非晶[16]㊁金属-纳米碳[17]等纳米叠层金属基复合材料(nano-laminated metal matrix composites,NLMMCs)㊂对于传统单一均匀的MMCs,研究者通常采用宏观的单轴拉伸[18]㊁压缩[19]和三点弯曲[20]等测试方法表征复合材料的力学性能,并结合断口的形貌来推测复合材料的强韧化机制[21]㊂然而,相比于传统的MMCs,NLM-MCs中复合界面占比显著增加,界面在其强化㊁变形和断裂过程中发挥了极为重要的作用,上述宏观力学测试方法很难准确地评价界面对NLMMCs强韧化机制的影响㊂另外,部分NLMMCs以薄膜的形式存在,宏观的力学测试方法难以对其性能开展研究㊂近年来发展起来的微纳力学测试方法(如纳米压痕[22]㊁微柱压缩与拉伸[23-25]㊁微悬臂梁弯曲[26])结合精确 定点 (site-specif-ic)的透射电子显微镜(transmission electron microscope, TEM)分析[27],为研究NLMMCs的力学性能㊁探索其强韧化机制提供了新思路和新方法,尤其是其满足了纳米叠层金属基复合薄膜材料力学行为研究的需求[28,29]㊂特别地,扫描电子显微镜(scanning electron microscope, SEM)和TEM中的原位微纳力学测试方法可以实时获得材料变形过程中的力学性能数据和显微结构变化,更加准确地阐释界面-结构-性能关系,为NLMMCs性能优化设计提供了强有力的支撑㊂因此,本文重点综述近年来NLMMCs的制备工艺,并聚焦于微纳力学方法探究NLMMCs的强韧化和变形机制的研究新进展,最后展望NLMMCs的发展趋势和其面临的挑战㊂2㊀纳米叠层金属基复合材料的制备方法2.1㊀磁控溅射法磁控溅射法是目前金属-陶瓷㊁金属-非晶型NLMMCs 最常使用的制备方法,其制备原理如图1a所示[29]:在电场作用下,工作气体氩气(Ar)发生电离,离子化气体进入暗空间鞘层(靠近靶材的较薄区域)时会因电压降而强烈加速,之后以很高的速度撞击目标靶材,使原子㊁分子或原子团簇从靶材表面溅射出来㊂这些溅射出的靶材粒子沉积在基板表面,形成薄膜㊂在制备过程中,通过调节电源功率㊁沉积速率和挡板闭合时间等工艺参数交替溅射2种不同材料,可以获得所需层厚和层厚比的金属-陶瓷和金属-非晶纳米叠层复合薄膜,如图1b和1c 中的Cu-非晶CuZr[30]和Al-SiC[31]纳米叠层复合薄膜所示㊂磁控溅射法具有沉积温度低㊁组元成分和厚度易控制㊁成膜质量好等优点,但溅射速率低的缺点限制了其在宏量化制备方面的应用,故常用于制备薄膜和模型材料㊂图1㊀磁控溅射法制备叠层薄膜的示意图(a)[29],Cu-非晶CuZr 纳米叠层薄膜(插图为Cu的选区电子衍射图谱)(b)[30]和Al-SiC纳米叠层薄膜(c)的TEM照片[31]Fig.1㊀Schematic diagram of the fabrication of one layer film using mag-netron sputtering(a)[29],TEM image of Cu-amorphous CuZrnanolaminates(the inset is selective area electron diffraction im-age of Cu)(b)[30]and Al-SiC nanolaminates(c)[31]2.2㊀逐层累积法Kim等[32]采用纳米级金属层和单层石墨烯逐层累积组装的方法制备了具有纳米叠层结构的石墨烯增强铜基和镍基复合材料薄膜,制备过程如图2所示㊂首先,采用化学气相沉积(CVD)方法在铜箔上生长出高质量的单层石墨烯,并通过湿法转移过程(聚甲基丙烯酸甲酯(PMMA)旋涂以及铜箔刻蚀等)将石墨烯转移到通过真空273All Rights Reserved.㊀第5期郑思婷等:纳米叠层金属基复合材料的力学行为蒸镀法沉积的金属(铜或镍)薄膜上;然后,通过多次循环金属纳米层沉积和石墨烯转移过程,制备出金属-石墨烯纳米叠层复合材料薄膜㊂在薄膜制备过程中,石墨烯的CVD生长和转移过程需要严格控制工艺参数,以免产生表面缺陷和残留有机污染物,降低复合材料的力学和物理性能㊂该制备方法通用性强,适合制备模型材料以研究石墨烯增强金属基复合材料中的界面效应㊁强化和变形机制㊁内外尺寸效应等基础性科学问题㊂图2㊀逐层累积法制备纳米叠层石墨烯增强铜基和镍基复合材料的制备路线图[32]Fig.2㊀Fabrication process of graphene reinforced Cu-and Ni-matrix nanolaminated composites based on the layer-by-layer approach[32]㊀㊀在此基础上,Yang等[33]采用辊间(roll-to-roll,R2R)CVD法累积多层Cu-石墨烯复合薄膜,并结合热等静压(hot isostatic pressing,HIP)技术(图3)制备了石墨烯层数可控且平行分布的石墨烯增强Cu基复合材料㊂这种方法的优点是易于实现NLMMCs中石墨烯大面积㊁高覆盖率和高度平行取向分布㊂同时,通过调整石墨烯生长参数可精确控制石墨烯的结晶度和层数㊂图3㊀辊间累积化学气相沉积法结合热等静压法制备石墨烯-Cu纳米叠层复合材料块体的示意图[33]Fig.3㊀Schematic diagram of the fabrication process of graphene-Cunano-laminated bulk composites via Roll-to-Roll CVD combinedwith hot isostatic pressing(HIP)[33]2.3㊀片状粉末冶金法启迪于自然界中贝壳珍珠层的 砖砌 结构,作者课题组开发了片状粉末冶金(flake powder metallurgy,FPM)工艺,制备了多壁碳纳米管(multi-walled carbon nano-tubes,MWCNTs)-Al砖砌结构纳米叠层复合材料块体,获得了优异的强韧性[34,35]㊂典型的片状粉末冶金工艺如图4所示:首先,通过球磨获得纳米厚度的片状Al粉末,并对其表面进行聚乙烯醇(PVA)溶液包覆,同时在分散剂的辅助下对MWCNTs团簇进行超声分散形成均匀的MWCNTs分散液;然后,将片状Al粉与MWCNTs分散液均匀混合,使得MWCNTs均匀吸附到Al片表面;最后通过冷压㊁烧结和热挤压等致密化过程,获得MWC-NTs-Al纳米叠层复合材料块体㊂在此基础上,作者课题组进一步改进了FPM工艺,制备了具有纳米叠层结构的石墨烯-Al[17,36-39]㊁石墨烯-Cu[40-42]㊁单壁碳纳米管(single-walled carbon nanotubes,SWCNTs)-Al复合材料[43]㊂该制备工艺过程中,纳米碳材料没有经过高能球磨,因此制备的复合材料可以保持纳米碳材料结构的完整性㊂另外,此方法通用性强,适合于大规模制备复合材料块体㊂2.4㊀共沉积法共沉积法是将纳米碳材料分散到金属材料中的有效方法,主要包括物理喷涂沉积法和电化学沉积法㊂例如,Meng等[44]通过把均匀分散的石墨烯溶液以一定的压力喷涂到酸洗的Mg箔片表面获得复合单元,然后将复合单元层层堆叠,通过后续的热压和热轧工艺制备了石墨373All Rights Reserved.中国材料进展第41卷图4㊀片状粉末冶金(FPM)法制备MWCNTs-Al纳米叠层复合材料示意图[34]Fig.4㊀Fabrication process for MWCNTs-Al nanolaminated composites by the flake powder metallurgy(FPM)method[34]烯-Mg叠层复合材料㊂该方法通过控制喷涂时间可以控制石墨烯的体积分数㊂电化学沉积工艺中,在阴极与阳极之间施加的电流(直流㊁脉冲或脉冲反向电流)作用下,通过电解液中金属离子(Cu2+㊁Ni2+等)的还原作用,将金属膜沉积在阴极(镀有纳米碳的金属箔)表面上,并形成叠层结构[45]㊂该方法操作简单,但纳米碳与金属是非共价键结合,界面结合强度较弱㊂此外,未经处理的CNTs具有疏水性,使得金属盐很难穿透CNTs之间的缝隙,从而会在沉积层内形成缺陷[12]㊂另外,Kang等[46]将选择性浸涂(selec-tive dip-coating)和电沉积技术相结合,制备了MWCNTs-Cu叠层复合材料㊂首先,采用阴离子表面活性剂(SDS)对MWCNTs进行表面官能团化,获得带负电的MWCNTs 溶液;然后把基体浸入MWCNTs溶液中后以3mm/min 的速度取出;最后,在酸性电解液中电沉积Cu层㊂由于电解液中的Cu2+与带负电荷的官能团化MWCNTs层之间的电荷吸引作用,Cu层电沉积在MWCNTs层表面,并填充了MWCNTs层的间隙;多次循环浸涂和电沉积过程,最终形成叠层结构Cu-MWCNTs复合材料㊂2.5㊀累积叠轧法累积叠轧(accumulative roll-bonding,ARB)法是将表面经过处理㊁尺寸相等的2块薄板材料在一定温度下叠轧并使其自动焊合,然后反复叠片㊁轧制获得叠层复合材料的工艺㊂ARB后材料微观结构细化,力学性能得到大幅度提升㊂例如,Yao等[47]以铜和石墨为原料,在室温下通过ARB工艺循环30次(每次循环厚度减少50%)制备Cu-石墨烯叠层复合材料,如图5所示㊂该研究表明,ARB能把原始的石墨转化为仅有5层的石墨烯,且在Cu基体中良好分散,从而获得了高的硬度和电导率㊂图5㊀累积叠轧法制备石墨烯-铜纳米叠层复合材料的示意图[47] Fig.5㊀Schematic diagram of the fabrication process for graphene-Cu nanolaminated composites via accumulative roll-bonding(ARB)process[47]3㊀纳米叠层金属基复合材料的强韧化机制3.1㊀纳米叠层金属基复合材料的强化机制3.1.1㊀界面结构特性及其对NLMMCs强化机制的影响纳米叠层结构的金属及其复合材料含有高密度的异质界面,这些界面通常作为位错形核源㊁位错湮灭阱㊁位错运动的障碍和位错存储和反应的择优位点[48],进而显著影响材料的力学行为㊂对于金属-金属纳米叠层材料,其界面结构包括共格界面㊁半共格界面和非共格界面[49],如图6所示㊂共格界面中界面上下的2种材料具有相同的晶体学结构和较小的晶格失配(通常为百分之几的量级)㊂由于较小的晶格失配导致界面具有高的共格应力,阻碍了位错穿过界面转移至相邻层,从而提高了材料强度㊂对于半共格界面,相邻两层之间存在较大的晶格失配,从而导致界面具有相对较低的抗剪强度㊂为了减少晶格畸变,在半共格界面上通常会产生失配位错[50]㊂界面通过剪切以响应失配位错的应力场,并吸引图6㊀金属-金属纳米叠层材料的3种界面结构示意图[49] Fig.6㊀Schematic illustration of the three kinds of interface structures in metal-metal nanolaminates[49]473All Rights Reserved.㊀第5期郑思婷等:纳米叠层金属基复合材料的力学行为位错至界面处㊂半共格界面成为位错滑移传输的障碍,从而实现材料的强化㊂而非共格界面是指相邻两层的界面由不同的晶体结构组成,其具有相对较大的晶格失配㊂在这种界面上,相邻层的滑移系统之间没有连续性,其具有较低的抗剪强度,使得位错核沿界面扩展,被界面吸收,阻碍了滑移传递至相邻层,从而使材料获得了高强度[51,52]㊂金属-金属纳米叠层材料界面结构对强化机制的影响详见综述论文[48,50,53,54]㊂金属-陶瓷(主要指晶体陶瓷)型NLMMCs的界面结构类似于金属-金属非共格界面,其界面强化机制也与之相似㊂对于金属-非晶(包括金属玻璃㊁非晶陶瓷和C或Si族元素玻璃)型NLMMCs,其金属-非晶界面(crystal-line-amorphous interfaces,CAIs)由基于位错调控塑性变形的金属层和基于剪切过渡区(shear transition zones,STZs)或剪切带(shear bands,SBs)调节塑性变形的非晶层组成[48]㊂CAIs中很容易形成剪切滑移,导致材料的屈服强度降低;此外,CAIs也是加载过程中位错形核和位错发射的择优位点[55]㊂对于金属-纳米碳型NLMMCs,其界面结构也类似于非共格界面,该类复合材料强度的提高主要来自于载荷从基体到纳米碳的跨界面传递㊁纳米碳抑制基体晶粒生长引起的细晶强化,以及纳米碳通过界面阻碍位错运动引起的位错强化和背应力强化[56,57]㊂结合强度大小合适的界面才能有效传递载荷并抑制材料发生破坏性变形[58]㊂然而,通常由于大的表面能差异和低润湿性,纳米碳材料与金属基体之间形成弱的范德华力或机械结合[59],使纳米碳层的承载强化未能充分发挥㊂研究者们通过形成强共价键[60,61]㊁表面金属化[62]和界面反应[63]等方法,解决界面不相容和润湿性差的问题,形成具有高结合强度的界面,从而显著提高界面强度,进一步提高材料强度㊂3.1.2㊀内在特征尺寸对NLMMCs强化机制的影响随着微纳力学测试方法的快速发展,纳米叠层金属及其复合材料的力学行为得以深入研究㊂除了各组分材料的本征强度以外,各组分的内在特征尺度也显著地影响纳米叠层金属及其复合材料的强度[64-68]㊂类似于金属-金属纳米叠层材料,NLMMCs的强度随软相金属层厚度的变化规律可以用以下3种强化机制来描述㊂当金属层厚度h相对较大(亚微米到微米尺度)时,NLMMCs的强度σ与金属层厚度h遵循Hall-Petch关系[31],即σɖh-0.5,此时,软相金属层中产生大量位错并在界面处塞积,引起材料强化㊂当金属层厚度h减小到某一临界尺寸(通常不大于200nm)时,材料强度仍然单调增加,但明显偏离Hall-Petch关系,此时NLMMCs的强度变化规律符合约束层滑移(confined layer slip,CLS)模型[31,68-70],这是因为层厚的减小使得单个金属层内难以形成位错塞积,而是以单个位错约束在金属层内滑移的形式来调节塑性变形进而影响材料强度㊂然而,对于金属-金属纳米叠层材料,当叠层厚度进一步降低至1~2nm时,位错源开动困难,界面不再具有阻碍位错运动的能力,单个位错能够穿过界面,此时材料强度达到饱和甚至有所降低,对应于界面势垒强度(interface barrier strength,IBS)模型[71]㊂特别地,对于非连续纳米碳增强的NLMMCs,除金属基体特征尺寸以外,纳米碳材料的横向尺寸也会通过影响纳米碳的承载强化和纳米碳阻碍位错运动影响复合材料的强度㊂例如,Zhao等[56]对Al基体层厚为200nm㊁石墨烯(reduced graphene oxide,RGO)横向尺寸分别为(186ʃ7)nm和(603ʃ58)nm的RGO-Al纳米叠层复合材料开展了基于单次和多次加载-卸载循环的微柱压缩实验,发现RGO尺寸较小的RGO-Al复合微柱具有更高的强度㊂通过对强化机制的分析发现,RGO尺寸较小的复合材料承载强化贡献小于RGO尺寸较大的复合材料;而RGO尺寸较小的复合材料中石墨烯与位错相互作用引起的各向同性硬化和动力学硬化的贡献远远大于RGO尺寸较大的复合材料㊂3.1.3㊀外在尺寸对NLMMCs强化机制的影响另一方面,除了内在尺寸效应以外,采用微纳力学方法研究NLMMCs力学行为所制备的微纳试样外在尺寸也会显著影响其力学行为[72-76]㊂例如,Zhang等[77]制备了调制比(非金属层与金属层厚度比η)相同,单层厚度h 从5nm变化到150nm的Cu-CuZr金属-非晶多层膜,采用聚焦离子束(focus ion beam,FIB)加工了直径D从350nm 变化到1425nm的微柱,并对其开展了单轴压缩实验㊂研究结果表明,当h或D发生单一变化时,微柱的强度符合 越小越强(smaller is stronger) 的规律㊂当h在10~ 150nm范围内时,位错活动主要受晶粒控制,微柱的强度仅依赖于内在特征尺度,而与外在直径无关,且强度与层厚的关系符合CLS模型;当hɤ10nm时,较小样品体积内包含位错的概率大大降低,样品外表面对位错行为的影响达到了与内界面相当的程度,导致样品强度受内在和外在尺寸共同影响㊂此外,Wang等[75]从不同调制比(η=0.1~3.0)的Cu-CuZr金属-非晶多层膜上切割不同直径(D=300~ 1500nm)的微柱开展单轴压缩测试,结果如图7所示㊂可以看出,在给定微柱直径时,微柱强度随着调制比的增加而增大;当调制比一定且小于0.5(η=0.1和0.3)时,微柱强度随直径的增大而降低,呈现 越小越强 的趋势;而当调制比大于0.5时,微柱强度随直径的增大而增大,呈现 越大越强 的趋势㊂这主要是由于复573All Rights Reserved.中国材料进展第41卷合薄膜在小的调制比(0.1)时,非晶的层厚小于剪切带形成需要的临界尺寸,剪切带(shear bands,SBs)难以形成,因此,更厚的软相金属层主导微柱的塑性变形㊂随着微柱直径的减小,金属层中位错源的数量减少,而且微柱中含有大晶粒的概率降低,因此,位错活动需要在较高的应力下进行,因此,微柱尺寸越小,其强度越高㊂当调制比大时(η=3.0),非晶层(<100nm)通常包含一定数量的内部缺陷,在这些缺陷处可以轻松激活剪切过渡区(shear transformation zones,STZs)并聚集形成SBs㊂随着直径减小,单个SBs 形成引起的软化更容易发生在较小的微柱中㊂图7㊀不同调制比η下Cu-CuZr 微柱2%流变应力与微柱直径的关系图[75]Fig.7㊀The flow stress at 2%strain offset of Cu-CuZr micro-pillars ob-tained from the true stress vs strain curves as a function of pillardiameter with different modulation ratio η[75]在纳米碳-金属型NLMMCs 中,Zhao 等[36]和Hu 等[76]分别研究了90ʎ(叠层方向垂直于加载方向)和0ʎ(叠层方向平行于加载方向)RGO-Al 纳米叠层复合微柱的外在尺寸效应㊂研究结果表明,直径大小对90ʎRGO-Al复合微柱的强度没有明显的影响㊂而对于0ʎRGO-Al 复合微柱,当微柱直径比铝层厚度(~200nm)大一个数量级时,微柱直径对其强度没有明显的影响,微纳米尺度下材料的力学性能能够反映宏观复合材料的力学性能㊂3.1.4㊀叠层取向对NLMMCs 强化机制的影响叠层取向与加载方向之间的相对角度会影响NLM-MCs 中的应力状态,进而影响其强度㊂例如,Mayer等[78]对0ʎ㊁45ʎ和90ʎ的Al-SiC 纳米叠层复合微柱开展单轴压缩实验,发现0ʎ微柱中增强相SiC 层处于承载方向,强度最高;45ʎ微柱由于协调剪切变形更容易,强度最低;90ʎ微柱中SiC 层出现的裂纹限制了其强度提高㊂另外,Fu 等[79]从RGO-Al 宏观块体材料中切割0ʎ和90ʎ纳米叠层RGO-Al 复合微柱,并对其开展了单轴微拉伸实验(图8a)㊂结果表明,0ʎRGO-Al 微柱的屈服强度显著高于90oRGO-Al 微柱,且都高于相应的纯铝微柱,如图8b 所示㊂经计算分析得知,90ʎRGO-Al 微柱强度的提高主要来自于RGO /Al 界面对位错的阻碍作用,而0ʎRGO-Al 复合微柱的强化来自于RGO 显著的承载强化以及RGO /Al 界面对位错的阻碍作用㊂3.2㊀纳米叠层金属基复合材料的韧化机制NLMMCs 由于纳米尺度㊁叠层构型以及大量异质界面的存在,被认为具有比传统单一均匀MMCs 更加优异的断裂韧性㊂特别是,近些年随着微纳力学技术的发展,NLMMCs 的韧化机制得到了更加深入的阐释㊂在金属-陶瓷型NLMMCs 领域,界面的存在使脆性陶瓷层中产生的裂纹发生偏转,改变了裂纹扩展的路径,并且陶瓷层中也有可能产生位错[80],实现与韧性金属层的塑性共变形,从而增加复合材料的韧性㊂Yang 等[81]采用微柱劈裂法(micro-pillar splitting,图9a)和缺口悬臂梁弯曲法(图9b)研究了叠层厚度和叠层取向对Al-SiC 纳米叠层复合薄膜断裂韧性的影响㊂结果发现,Al-SiC 纳米叠层复合薄膜在载荷平行于叠层时的断裂韧性高于其在图8㊀0ʎ和90ʎ纳米叠层RGO-Al 复合微拉伸试样示意图和SEM 照片,其中拉伸方向由黑色箭头标出(a);0ʎ和90ʎ纳米叠层RGO-Al 和纯Al 的屈服强度对比图(b)[79]Fig.8㊀Schematic illustration and SEM images of as-fabricated microtensile composite specimens with 90ʎand 0ʎRGO laminate orienta-tions (a);summaries of the 0.2%offset yield strength of 90ʎand 0ʎRGO-Al composite and pure Al samples (b)[79]673All Rights Reserved.㊀第5期郑思婷等:纳米叠层金属基复合材料的力学行为垂直于叠层时的断裂韧性㊂当载荷平行于叠层时,裂纹扩展沿着金属/陶瓷界面发生,并且由于Al 层塑性变形的作用,断裂韧性随层厚的增加而增加,在层厚为100nm时达到最大㊂当载荷垂直于叠层时,裂纹扩展到界面处出现了偏转,断裂韧性随着层厚的减小而增加,在层厚为25nm 时达到最大,这归因于层厚减小导致了更高的界面密度㊂图9㊀微柱劈裂法(a)和缺口悬臂梁弯曲法(b)研究Al-SiC 纳米叠层复合材料断裂韧性的加载示意图[81]Fig.9㊀Schematic diagrams of the load directions for the fracture tough-ness testing of Al-SiC nanolaminates via micro-splitting (a)andnotched cantilevers bending methods (b)[81]在金属-非晶型NLMMCs 领域,非晶层具有力学不稳定性,而叠层结构限制了非晶层中裂纹和剪切带的形成和扩展,并且在一定条件下可以实现非晶层和金属层之间产生塑性共变形,提高复合材料的塑韧性[48]㊂为了揭示金属-非晶纳米叠层复合薄膜的韧化机制和潜在的破坏机理,Wang 等[82]制备了层厚为50nm㊁宽度B 为500~3500nm 的Ag-CuZr 和Mo-CuZr 多层膜悬臂梁(图10a),并通过SEM 中的原位弯曲实验研究多层膜组分和悬臂梁外在尺寸对断裂行为的影响㊂结果如图10b 所示,当悬臂梁宽度在500~3500nm 范围内变化时,Ag-CuZr 多层膜的断裂韧性总是高于Mo-CuZr 多层膜㊂另外,Ag-CuZr 多层膜的断裂韧性随悬臂梁宽度的增加而增加;而Mo-CuZr 多层膜的断裂韧性随悬臂梁宽度的增加而减小,当悬臂梁宽度超过~1500nm 时保持不变㊂对其断裂机理的分析发现,Ag-CuZr 悬臂梁中非晶CuZr 层中开动的微裂纹在多层结构中出现了互连(图10c),而Mo-CuZr 悬臂梁中的裂纹破坏性地穿过多层薄膜扩展(图10d),导致了Ag-CuZr 悬臂梁表现为韧性断裂,而Mo-CuZr 悬臂梁表现为脆性断裂,且Ag-CuZr 断裂韧性高于Mo-CuZr 多层薄膜㊂非晶纳米叠层复合薄膜的断裂韧性随成分和悬臂梁尺寸的变化主要归因于韧性相的塑性能耗散,裂纹尖端钝化㊁裂纹桥接以及塑性区应变梯度对裂纹扩展的影响等韧化机制㊂图10㊀金属-非晶纳米叠层复合薄膜的断裂韧性及断裂机制[82]:(a)典型的多层膜悬臂梁的SEM 照片,(b)Ag-CuZr 和Mo-CuZr 悬臂梁的断裂韧性随宽度B 的变化规律,(c,d)Ag-CuZr(c)和Mo-CuZr(d)悬臂梁的断裂机制示意图Fig.10㊀Fracture toughness and fracture mechanisms of metal-amorphous nanolaminated composite films [82]:(a)typical SEM image ofthe Ag-CuZr micro-cantilevers,(b)cantilever width B -dependent fracture toughness K Q in Ag-CuZr and Mo-CuZr nanolami-nates,(c,d)schematic diagrams of fracture mechanisms in Mo-CuZr (c)and Ag-CuZr (d)micro-cantilevers773All Rights Reserved.。
铸轧法制备铜_铝_铜复合板的界面组织与性能_张衡

第36卷第3期2015年6月河南科技大学学报:自然科学版Journal of Henan University of Science and Technology :Natural ScienceVol.36No.3Jun.2015基金项目:河南省重大科技专项基金项目(102105000007)作者简介:张衡(1989-),男,河南商丘人,硕士生;谢敬佩(1957-),男,河南安阳人,教授,博士,博士生导师,主要从事金属复合材料的研究.收稿日期:2014-10-28文章编号:1672-6871(2015)03-0001-05铸轧法制备铜-铝-铜复合板的界面组织与性能张衡1,谢敬佩1,尚郑平2,李继文1,孙浩亮1(1.河南科技大学材料科学与工程学院,河南洛阳471023;2洛阳铜一金属材料发展有限公司,河南洛阳471100)摘要:采用铸轧法制备了不同厚度的铜-铝-铜复合板,并分别采用拉伸试验、剥离试验、X 射线衍射仪、能谱点分析(EDS )、扫描电镜(SEM )和能谱线扫描分析(EPMA )等对复合板力学性能、形貌和组成进行了检测。
检测结果表明:界面层的主要组成物为α(Al )、CuAl 2、Cu 9Al 4。
板厚从6mm 增大到14mm 时,界面层厚度和Cu 、Al 原子扩散程度均逐渐增加。
抗拉强度从115MPa 增大到135MPa ,延伸率从25%增加至31%,剥离强度从30N /mm 增大至35N /mm ,剥离强度即为界面层结合强度。
关键词:铜-铝-铜复合板;水平连铸;界面层;剥离强度中图分类号:TB331;TG146.1;TG146.2文献标志码:A0引言中国铜资源紧缺,而铝资源相对丰富,为了节省铜资源,开发了铜包铝电缆、铜-铝-铜复合排、铜-铝-铜复合箔等种类繁多的铜铝复合材料[1-5]。
铜-铝-铜复合板是一种铜铝双金属复合材料,充分发挥了铜的高导电、高导热率和铝的密度低、抗腐蚀、价格便宜等优点,既经济又满足了使用性能,在导电、导热和装饰等行业得到广泛应用[6-7]。
累积叠轧技术的基本原理及其在金属层状复合板材制备中的应用

工业技术科技创新导报 Science and Technology Innovation Herald69①基金项目:湖南省自然科学基金科教联合基金资助项目(项目编号:2017JJ5022)。
作者简介:赖春明(1989—),男,汉族,湖南茶陵人,硕士,讲师,研究方向:金属材料加工过程中的组织和性能控制。
DOI:10.16660/ki.1674-098X.2018.31.069累积叠轧技术的基本原理及其在金属层状复合板材制备中的应用①赖春明 张麦秋(湖南化工职业技术学院 湖南株洲 412011)摘 要:金属层状复合材料将性能不同的金属牢固地结合在一起以综合不同金属材料的优点与特性,在工业各个领域都展现出极为广阔的发展前景。
累积叠轧(Accumulative Roll Bonding,ARB)工艺作为一种细化金属晶粒提高金属性能的可靠方法,也为制备金属层状复合材料提供了一个新的途径。
本文围绕金属层状复合材料和ARB工艺技术的发展,以及ARB 工艺在金属层状复合材料制备中的应用进行了总结,并指出了存在的主要问题。
关键词:金属层状复合材料 累积叠轧 微观组织 力学性能中图分类号:TG335 文献标识码:A 文章编号:1674-098X(2018)11(a)-0069-03金属层状复合板材由于同时具有不同金属材料的优异性能,已成为当今材料科学领域中的研究热点之一,并且在实际工业上的应用也愈加广泛。
在大部分的金属层状复合板材中,基体材料及包覆层材料之间的结合强度以及包覆率等对于该复合材料的力学性能以及包括耐蚀性、钎焊性等在内的其他特殊性能均有较大的影响,是决定其能否达到使用要求的关键因素。
而已有的复合板材制备方法在产品性能、成材率或生产效率等方面很难满足实际生产需求。
累积叠轧技术由于工艺简单,设备投资小,且能获得剧烈变形来细化晶粒、提升材料的强度性能,最早被广泛应用于加工生产超细晶高性能金属材料,在其本身技术的不断发展过程中,也逐渐成为制备金属层状复合材料的重要发展方向。
Ni-Al活性复合材料累积叠轧的研究进展
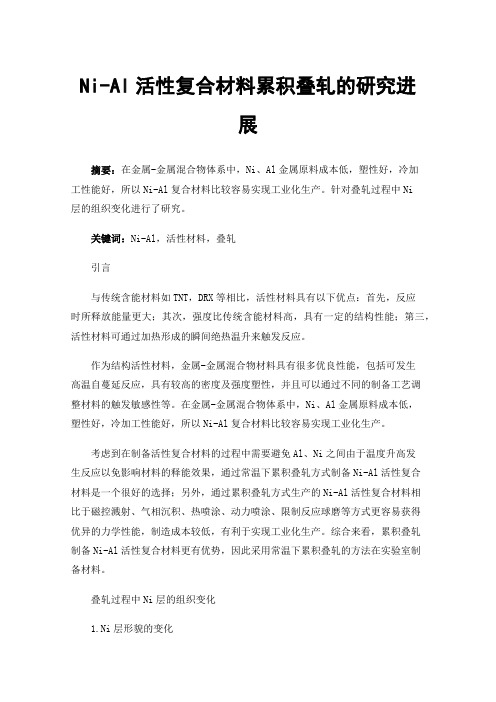
Ni-Al活性复合材料累积叠轧的研究进展摘要:在金属-金属混合物体系中,Ni、Al金属原料成本低,塑性好,冷加工性能好,所以Ni-Al复合材料比较容易实现工业化生产。
针对叠轧过程中Ni层的组织变化进行了研究。
关键词:Ni-Al,活性材料,叠轧引言与传统含能材料如TNT,DRX等相比,活性材料具有以下优点:首先,反应时所释放能量更大;其次,强度比传统含能材料高,具有一定的结构性能;第三,活性材料可通过加热形成的瞬间绝热温升来触发反应。
作为结构活性材料,金属-金属混合物材料具有很多优良性能,包括可发生高温自蔓延反应,具有较高的密度及强度塑性,并且可以通过不同的制备工艺调整材料的触发敏感性等。
在金属-金属混合物体系中,Ni、Al金属原料成本低,塑性好,冷加工性能好,所以Ni-Al复合材料比较容易实现工业化生产。
考虑到在制备活性复合材料的过程中需要避免Al、Ni之间由于温度升高发生反应以免影响材料的释能效果,通过常温下累积叠轧方式制备Ni-Al活性复合材料是一个很好的选择;另外,通过累积叠轧方式生产的Ni-Al活性复合材料相比于磁控溅射、气相沉积、热喷涂、动力喷涂、限制反应球磨等方式更容易获得优异的力学性能,制造成本较低,有利于实现工业化生产。
综合来看,累积叠轧制备Ni-Al活性复合材料更有优势,因此采用常温下累积叠轧的方法在实验室制备材料。
叠轧过程中Ni层的组织变化1.Ni层形貌的变化图1是Ni-Al复合材料经过累积叠轧后的金相组织(a、b、c、d分别是4、7、9、11道次的金相组织示意图)。
图1 不同道次累积叠轧后Ni-Al复合材料金相组织Fig.x Metallographic structure of Ni/Al composite after differentpasses by accumulative roll bonding在累积叠轧过程中,由于Ni层质地比较硬,所以在两种不同材料的共变形中,由于相组成的流动特性的差异和塑性不稳定性的出现,Ni层会随着变形首先发生颈缩和断裂(图中扁条状的为金属Ni)。
ARB工艺和HIP工艺
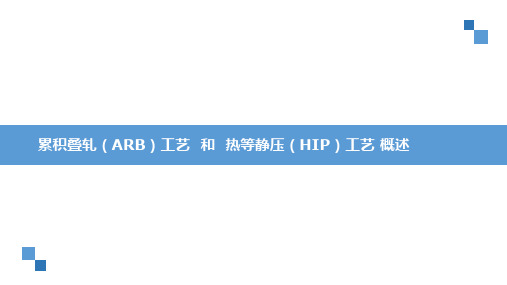
累积叠轧(ARB)工艺
累积叠轧工艺是将表面进行脱脂、加
工硬化等处理后尺寸相等的P两A块R薄T 板TWO
材料在一定温度下叠轧并使其自动焊 合,然后重复进行相同的工艺反复叠 片、轧制焊接,从而使材料的组织得 到细化,夹杂物均匀分布,大幅度提 高材料的力学性能。
累积叠轧工艺示意图
累积叠轧(ARB)工艺特点
热等静压(HIP)工艺背景
热等静压技术(HIP)起源于20世纪50年代,由美国Battelle研究所开发,最早用 于原子能反应过程中燃料元素的扩散黏结。 热等静压技术的出现,打破了合金原有的铸造、锻造的技术路线,进一步提高了合 金材料的力学性能,提高了材料利用率并加快了产品生产周期。随后热等静压技术 的应用逐渐地延伸到金属基复合材料的成型;随着热等静压技术日益广泛地应用, 有研究者将热等静压技术用于石墨、陶瓷等无机非金属材料的成型及致密化领域。
Байду номын сангаас热等静压工艺原理图
热等静压(HIP)扩散连接
热等静压复合扩散连接是将2种或2种以上的不同材料,在高温 高压作用下进行扩散连接的一种新技术,涉及到的材料可以是 金属-金属、金属-非金属、非金属-非金属,它是近几年发展起 来的,特别是在民用方面值得应用推广的一项较好技术。
HIP 扩散连接是在高温、高压的作用下,被连接材料的原子快速 移动、相互扩散,最终材料在表面紧密接触,在固态下连接在一 起的焊接工艺。
1.目前,关于同种或异种金属固相扩散连接和轧制复合的界面结合机制, 主要有机械啮合理论、薄膜理论、金属键理论、位错理论、再结晶理论、 能量理论、原子扩散理论、三阶段理论等。
2.对金属轧制复合过程中微观组织演变规律的研究还是初步阶段,现阶 段研究主要集中在两方面:一是组元金属内晶粒形貌与微观组织和结构 变化,二是复合层界面处原子扩散与金属间化合物的形成。
累积叠轧和电沉积工艺制备Al-Cu复合材料及其组织和力学性能研究

累积叠轧和电沉积工艺制备Al-Cu复合材料及其组织和力学性能研究累积叠轧和电沉积工艺制备Al/Cu复合材料及其组织和力学性能研究摘要:Al/Cu复合材料在航空航天、电子器件和汽车工业等领域具有广泛应用。
本文采用累积叠轧和电沉积工艺制备了Al/Cu复合材料,并研究了其组织和力学性能。
结果表明,通过调整累积叠轧过程中的压下轧制比,可以控制复合材料中Al和Cu层的厚度和界面结合强度。
同时,电沉积工艺可以在界面处形成纳米晶结构,增强了界面的强固性。
通过扫描电子显微镜(SEM)、透射电子显微镜(TEM)和X射线衍射(XRD)等手段对制备的Al/Cu复合材料进行了显微结构和相组成的分析。
力学性能测试表明,复合材料具有较高的硬度和强度,且具有优异的耐腐蚀性能。
本研究为Al/Cu复合材料的制备工艺和性能提供了重要的参考。
引言Al/Cu复合材料由于其独特的性能,在各个领域得到了广泛的应用。
其中,Al和Cu材料的厂界结合强度对于复合材料的性能至关重要。
为了达到优异的厂界结合强度,我们引入了累积叠轧和电沉积工艺。
累积叠轧是一种通过多次循环叠轧的方式,使两种材料之间产生冷变形,从而增强层间结合的工艺。
电沉积则是通过电化学方法,在界面处形成纳米晶结构,增强界面结合的工艺。
本研究旨在通过这两种工艺制备Al/Cu复合材料,并研究其组织和力学性能。
实验方法首先,我们选择纯度为99.99%的Al和Cu片材作为原材料。
在累积叠轧过程中,通过调节压下轧制比控制Al和Cu层的厚度比。
同时,在电沉积工艺中,我们采用了适当的电沉积条件,使得在Al/Cu界面处形成纳米晶结构。
通过SEM、TEM和XRD等手段对制备的Al/Cu复合材料进行了显微结构和相组成的分析。
同时,使用硬度测试仪和力学测试仪对复合材料的力学性能进行了测试。
结果与讨论通过调节累积叠轧过程中的压下轧制比,我们成功地控制了复合材料中Al和Cu层的厚度比。
同时,电沉积工艺在界面处形成了纳米晶结构,增强了界面的强固性。
Al-Zn-Mg-Cu系铝合金厚板冷轧过程中的织构演变
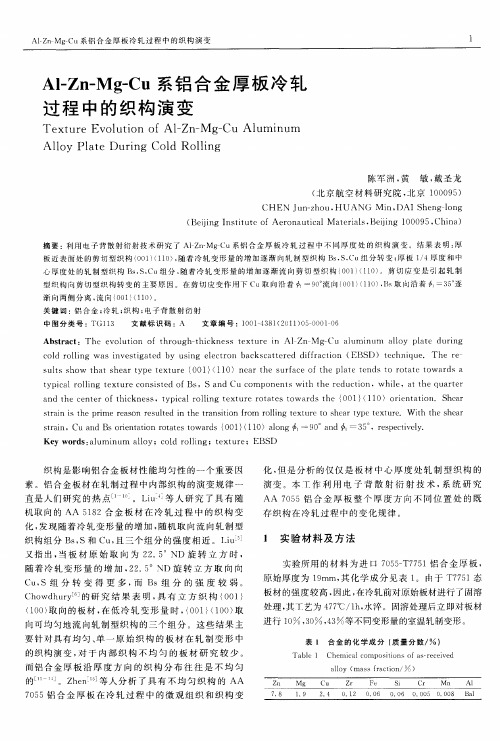
心厚 度 处 的 轧制 型 织 构 B , , u组 分 . 着 冷 轧变 形 量 的 增 加逐 渐 流 向剪 切 型织 构 { 0 } 1 0 。剪 切 应 变 是 引 起 轧 制 ss C 随 0 1 ( 1) 型织 构 向剪切 型织 构 转 变 的 主要 原 因 。在剪 切 应 变 作 用下 C u取 向沿 着 ≠ 一9 。 向 { 0 l 1 0 . s 向 沿着 一3 0流 0 1 ( 1) B 取 5逐
s i h w h ts e rt p e t r { 0 } 1 0 e rt es ra eo h lt e d O r tt o r sa u t s o t a h a y etx u e 0 1 ( 1 >n a h u fc ft ep aet n st o aet wad s
a d t ec n e ft ik e s y ia ol g tx u er ttst wa d h { 0 } 1 0 n h e t ro hc n s ,t p c l l n e t r o ae o r st e 0 1 ( >o in a in S e r r i 1 re tt . h a o
( ej g I si t fAe o a t a Ma eil。 ejn 0 0 5, ia B in n t u eo r n u i l i t c tras B i g 1 0 9 Ch n ) i
摘 要 : 用 电子 背散 射 衍 射 技 术研 究 了 Al n MgC 利 — — u系铝 合 金 厚 板 冷 轧 过 程 中不 厚 度 处 的织 构 演 变 。结 果 表 明 : Z 厚
异步累积叠轧纯铜材的取向变化过程与力学性能

异步累积叠轧纯铜材的取向变化过程与力学性能周蕾;史庆南;王军丽;米辉;刘润【摘要】Pure copper sheets were prepared by Asymmetrical Accumulative Rolling Bonding(AARB) at room temperature. By optical microscopy, scanning electron microscopy(SEM) with electron back-scattered diffraction(EBSD) , X-ray diffractometer(XRD) with texture accessories and stretch mechanics performance tests, the microstructure,texture and mechanical properties of pure copper sheets by AARB were discussed. The results show that after six times of AARB, the grains of copper is refined by compression deformation and shearing deformation ,and the average grain size is refined to 5μm. Texture of sample main composed of {112}<111>, {123 } <634> , {011} <211 > and {011}<100>. Yield strength and tensile strength of sample incre ase obviously. σ0.2 and σb got to 348MPa and 452MPa separately. The elongation of sample decreases to 2. 3% after the second pass, and then it decreases a little with the rise of the equivalent strain.%室温下对纯铜薄板进行一到六道次的异步累积叠轧变形加工.采用金相显微镜、扫描电镜附带背散射电子衍射、X射线衍射仪附带织构附件及拉伸试验机进行组织、取向观察及力学性能测试,获得铜材异步叠轧过程的显微组织、轧制织构变化过程和力学性能.结果表明:经过六道次的异步累积叠轧变形,由于压缩变形与剪切变形作用,使晶粒细化,铜材晶粒尺寸由30~50μm细化到5μm.异步叠轧过程中出现:{112}<111>,{123}<634〉,{011}<211>和{011}<100>几种主要组分轧制织构.材料的屈服强度与抗拉强度明显提高,六道次后分别达到348MPa和452MPa.材料的伸长率在二道次后显著下降到2.3%,然后随等效应变的增加略微下降.【期刊名称】《材料工程》【年(卷),期】2013(000)003【总页数】5页(P38-41,50)【关键词】纯铜;异步叠轧;显微组织;织构;力学性能【作者】周蕾;史庆南;王军丽;米辉;刘润【作者单位】昆明理工大学材料科学与工程学院,昆明650093【正文语种】中文【中图分类】TG335.5;TG339叠轧法很早以前应用在工业生产中,目的是为了获得薄板,而在研究超细晶体材料制备的方法中,叠轧法通过对板的叠合克服了因轧机弹性变形而造成的“最小轧制厚度”问题,使得板材可以获得很大的累积应变,同时获得超细晶晶粒。
- 1、下载文档前请自行甄别文档内容的完整性,平台不提供额外的编辑、内容补充、找答案等附加服务。
- 2、"仅部分预览"的文档,不可在线预览部分如存在完整性等问题,可反馈申请退款(可完整预览的文档不适用该条件!)。
- 3、如文档侵犯您的权益,请联系客服反馈,我们会尽快为您处理(人工客服工作时间:9:00-18:30)。
第36卷第6期 2017年12月电子显微学报Journal o! Chinese Electron Microscopy SocietyVol. 36,No. 62017-12文章编号= 1000-6281(2017)06-0556-08累积叠轧焊制备的Cu-Nb层状复合材料织构演变赵晓然\毛圣成〃,蔡吉祥\秦斌\张泽u,韩晓东1(1.北京工业大学固体微结构与性能研究所,北京100124;2.浙江大学电子显微镜中心材料科学与工程学院,浙江抗州310027)摘要层状复合材料的高强度、高硬度、高热机械稳定性以及抗辐照损伤等优良的热力学性能都与材料中的异相界面及其织构密不可分。
研究层状复合材料的异相界面结构及织构的演化是目前的研究热点之一。
本文利用累积叠轧焊技术制备了单层厚度在微米到亚微米的Cu-Nb层状复合材料。
利用电子背散射衍射(EBSD)技术分析了 C u和N b的织构随轧制道次的演化规律,为更好的理解和设计异相界面,发展高力学性能材料提供了实验依据。
关键词累积叠轧焊;C u-N b;织构演变;EBSD中图分类号:TB331;TG111. 7;TG115. 21+5. 3 文献标识码:A doi:10. 3969/j. issn. 1000-6281. 2017. 06. 007复合材料是通过机械或化学复合的方法将两相 复合到一起,使材料兼具两相的优异性能[1_3]。
复 合材料在能源、国防领域有着重要的应用,例如,Cu-Nb层状复合材料是制备核发电场电力传输导线的 潜在材料。
这是由于其具有比块体Cu更高的抗损 伤性[4]。
对于C u导线,其在核辐照条件下容易形 成孔洞,并相互合并从而演化为裂纹,导致C u导线 失效[5]。
而Cu-Nb中的异质界面,可以有效的煙灭 孔洞,避免了孔洞导致的材料断裂,提高了导线在辐 射的极端条件下的服役寿命。
层状复合材料,由于 其丰富、可控的微观结构特征,例如,组元材料的晶 体结构、调制结构参数、界面属性以及界面结构/特 性[6_7]等,而成为研究复合材料特别是微纳米尺度 复合材料塑性变形行为的理想模型材料。
发展高性 能复合材料,必须在微观尺度研究其塑性变形行为, 揭示其塑性变形机理。
研究者基于Hall-Petch效 应,实现了通过降低双层周期来增加强度的目的,例 如,Cu-Cr层状复合材料的强度在层厚降至2.5 nm 时,可达到其理论强度极限的1/3〜1/2[8]。
层状复 合材料可以通过自上而下的制备方法制得,如磁控 滅射、物理气相沉积(PVD)或其它沉积方法;也可 以通过累积叠轧的方法制得。
Misra等通过物理气 相沉积(PVD)方法制备了 Cu-Nb层状复合材料[9]。
其力学性能相比于纯元素体材料得到了极大的提 升,且表现出明显的尺寸效应,例如,当层厚为5 nm 时其屈服强度高达2 GPa[9]、硬度高达7 GPa[l0]。
Misra等将材料的高性能归因于随层厚的减小Cu 和Nb两相所具有的强烈择优取向,以及所形成的 K-S(Kurdjumov-Sachs )界面取向关系,即:丨l l l l C u l I丨l l〇lNb[7]。
通过自上而下方法制备的 层状复合材料,其优点在于可以精确控制层厚。
但 这类方法沉积速率较低,难以实现大批量、大块体材 料的制备,限制了其应用。
累积叠轧焊技术(ARB)由Saito等[11]首次开 发,通过大塑性变形,将两种金属材料进行机械复 合,属于自上而下的制备方法。
基于ARB技术已成 功制备了多种不同金属层状复合材料,例如,Cu-Nb[12]。
ARB技术是在传统轧制的基础上,增加了 堆叠、分割、表面处理和轧制等工序,并重复上述过 程直至所需层厚。
AR B技术能够同时精确控制材 料的晶粒尺寸和层厚,并通过变形量调控两相界面 的取向关系,适合于大批量的制备大尺寸材料。
随 着层厚的降低,层状复合材料的力学性能表现出2 个典型的特点。
特点一是其材料的强度/硬度随层 厚的降低而逐渐增加,例如,Beyerlein等[13]用ARB 制备了 Cu-Nb层状复合材料,发现当层厚从700 nm收稿日期:2017 -05 -02;修订日期=2017 -05 -30基金项目:国家自然科学基金面上项目(No.51471008);国家自然科学基金重点基金项目(No.51231008);北京市科技新星资助项目(No.Z141103001814108).作者简介:赵晓然(1992 -),女(汉族),河南人,硕士.E-m ail:yiduanlu2010@*通讯作者:毛圣成(1980 -),男(汉族),山东人,副研究员.E-m ail:scmao@第6期赵晓然等:累积叠轧焊制备的Cu -Nb 层状复合材料织构演变557降低至7 nm 时,复合材料的硬度从1. 8 GPa 增加到 4.5 GPa 。
特点二在于其力学性能具有良好的热稳 定性,如Zheng 等[14]研究中发现当层厚为10 nm 时,Cu -Nb 层状复合材料的硬度可达4. 13 GPa ,并且 在500丈退火1 h 后仍能保持4. 07 GPa 的硬度;这 种稳定性被认为与织构分布和PVD Cu -N b 相似的 稳定的界面结构:j112}Cul I j 112}Nb ,〈110〉Cul I 〈111〉Nb 相关。
研究表明这种稳定界面的形成与两相织构的演 变密切相关[15],尤其采用ARB 技术制备的复合材 料。
Liu 等[7]发现当Cu -A g 层状复合材料的厚度减 小80%时,C u 层表面主要织构为Copper 彳112丨 〈111〉织构,靠近两相界面处的主要织构为Brass |011}〈211〉。
Beyerlein 等[15]发现 ARBCu-Nb 层状 复合材料在单层厚为200 nm 时,C u 层有很强的 |44 11}〈11 11 8〉和 Copper j 112}〈111〉织构,Brass j 110丨〈112〉和S 彳213丨〈364〉织构较弱;Nb 相中以 a 织构中的j 112 }〈 110〉和j 001 }〈 110〉织构为主;单 层厚为10 nm 时,C u 层织构发生改变,具有很强的 Goss j 110 }〈001〉织构和Brass 织构;N b 相演变为 j 111 }〈 110〉织构。
Lee 等[16]和 Carpenter 等[17]发现 ARB Cu -Nb 层状复合材料的层厚从600 nm 减小到 80 nm 时,Cu 的织构由 j 112}〈111〉变为 j 4 4 11 } 〈11 11 8〉织构,N b 相的织构由j 112}〈110〉变为 j 225 }〈 110〉。
Carpenter 等[18]对 ARB Zr-Nb 层状复合材料织构研究发现,在单层厚为92 nm 时,Nb 相 有强的j 001 }〈110〉织构,Z r 相有很强的j 33017} 〈1120〉和j12112}〈1010〉。
本文利用累积叠乳焊工艺制备了不同层厚的 Cu -Nb 层状复合材料。
本文利用电子背散射衍射 (EBSD )技术,研究了 ARB 制备的Cu -Nb 层状复合材 料的织构及界面关系随乳制变形量的演化规律。
将 对精确调控层状复合材料的显微结构提供实验依据。
1实验方法1.1样品制备ARB 制备层状复合材料的过程如图1所示。
Cu 和Nb 设计的体积比为50/50,两种板材的初始 厚度为0.5 mm ,长度为100 mm , 宽度为50 mm ;两 层的纯度分别为99. 99%c C u 和99. 95%c Nb 。
乳制 前,对两种板材分别用砂纸进行机械打磨直至完全 去掉表面氧化皮。
将打磨好的板材在丙酮中超声波 清洗10 min 以上,以完全去除样品表面的有机物和 其它污染。
将处理过后的板材按照Cu -Nb-Cu -… C u 的顺序依次堆叠,并用包套固定。
采用双辊异步 机对固定包套中的样品进行乳制,单道次变形量为 90%,切割、热处理和去包套,并重复上述过程,直至 将样品的单层厚度乳制到300 nm 左右。
每道次切 割尺寸为3 mm 长、0. 5 mm 宽的截面样品用于 EBSD 实验。
图1 ARB 制备Cu-Nb 层状复合材料的工艺流程示意图。
Fig. 1 Schematic diagram of the ARB fabricating processes of Cu-Nb layeredcomposites.558电子显微学报 J.Chin.Electr.Micros.Soc.第36卷1.2电子背散射衍射(EBSD)测量EBSD实验的样品通过机械抛光制得。
将每道 次样品的截面依次用800 #、1200 #、2000 #、5000 #的金相砂纸进行打磨,然后用0.05 的氧化铝抛光液和0.02p m的二氧化硅抛光液进行振动抛光。
EBSD实验在JSM 6500F型扫描电镜(SEM)上进 行,加速电压为30 kV;数据处理和分析通过TSL OIM Analysis6.0 软件进行。
2实验结果和讨论2.1 ARB Cu-Nb微观结构的表征图2是1〜3道次的Cu-Nl)层状复合材料的截 面SEM像。
图中深色衬度的为Cu,浅色衬度的为 N l。
单层平均层厚由第1道次的〜36 ^m逐渐减少 为〜3叫(2道次),〜300 nm(3道次)。
由图2可 以看出,3个道次的样品都没有剪切带的产生,说明 每道次结束后的热处理消除了轧制过程产生的内应 力。
Cu-Nb界面在3个道次中都为连续界面,但随 着轧制道次的增加,逐渐变得不平直;这是由于在轧 制过程中,单层材料内发生了非均匀塑性变形。
该 现象同样在其他研究组制备的Cu-N l、Zr-N l、Cu-Zn 和Cu/Zn/A l等体系[|7,|9-2|]中发现,与有限元分析 预测结果一致[22-23]。
图3(a〜c)是1〜3道次Cu-N l层状复合材料 轧向的EBSD三色图,在图中用不同颜色代表不同 的取向,如图3d反极图所示。
图3(e〜g)是3个道 次对应的物相图,绿色代表Cu,红色代表N b如图 3h所示。
从图中可看出,1道次轧制并经热处理后 (图3a) ,Cu和N b晶粒相对较大,晶粒沿轧制方向 没有明显延展,尚有部分晶粒是等轴晶,不存在明显 的织构。
经2道次和3道次轧制并热处理后(图3 b,c) ,C u和N b中的晶粒明显沿轧向延长,单层厚 度方向仅有1〜2个晶粒,且两相都具有[111]和 [101]的轧向择优取向。
2.2 ARB Cu-Nb的织构演变分析图4是1〜3道次轧制后Cu-Nb层状复合材料 中Cu层的取向分布图(ODF)。
从图4a中可以看 出,在第1道次轧制后,C u层中晶粒取向分布比较 分散。