1.粉末冶金工艺概述Overview of the PM process (Powder Compaction Sintering)
粉末冶金技术简介

工艺知识知识园地2010年第3期粉末冶金技术简介Brief Introduction of Po wderM etall urgy Technique粉末冶金技术就是以各种金属粉末(或金属粉末与非金属粉末的混合物)为原料通过压制成型、烧结和必要的后续处理制取金属材料和制品的一门制造科学。
粉末冶金技术出现于1870年的美国,它最初是压制铜铅合金轴承来实现轴承的自润滑。
粉末冶金法在很大程度上和陶瓷的加工方法相似,因此,很多粉末冶金新技术也能用来制造陶瓷材料。
此外,粉末冶金工艺可以将一些在其他工艺中难以融合或者不相融合的材料进行融合制成新型复合材料,这些新型复合材料具有各种特殊的使用性能。
图2 我国与发达国家冶金粉末应用情况比较粉末冶金工艺是一种无切削工艺,加工而成的产品化学组成独特,机械和物理性能也很特殊,具有许多其他工艺不能实现的特殊性能。
粉末冶金产品具有的性能不仅仅是其组成材料的简单融合,是普通的熔铸或者添加合金的方法无法实现的。
工艺中形成的材料多是半致密或全致密的,具有多孔性。
如轴承、磨具、润滑材料、导杆、刀具等。
用粉末冶金工艺制成的零件,多孔性是粉末冶金制品最主要的特性。
利用多孔性在制品内部加入润滑介质,形成微型自润滑系统,减轻零件磨损程度,提高使用寿命;加入催化剂,可以提高物质的接触面积,提高反应速度图1 粉末冶金加工流程示意图和催化效果;也可以利用多孔性制成多样过滤层。
另外,多孔性可以减轻产品重量,使用相同原料量制造更多满足要求的产品。
除此之外,利用粉末冶金工艺加工制造金属零件的特点有: 加工工艺流程短而简单,易于控制。
机械加工十几道工序才能完成的产品在粉末金属工艺中,有时候几道工序就能实现。
产品质量好,精度高。
随着粉末冶金技术水平的提高,其成型产品形状可以非常复杂,且尺寸误差和表面粗糙度也降低不少。
批量产品的精度也保持较高的一致性。
原料利用率高,加工效率高。
采用粉末冶金生产零件,其原料利用率在85%左右,批量生产甚至可达95%。
粉末冶金工艺简介

粉末冶金工艺简介粉末冶金工艺简介粉末冶金工艺是一种新型的金属制造工艺,它以粉末状的金属材料为原材料,利用热成型和冶金工艺,实现金属制品非切削加工的目的。
此类金属材料更具灵活性,也更加高效。
粉末冶金工艺属于加工性技术,主要是将金属粉末及其他填充物、胶结剂和外加剂制成规定形态的产品。
金属粉末原料可用零件制造法和冶金合金技术来生产,包括合金粉末、精炼粉末和高纯度粉末等,胶结剂主要为各类塑料或助剂,外加剂一般是粉料及浮质料,为了满足不同的要求,开发出多种特殊的粉末冶金新型工艺,如压型粉末冶金(Powder Metallurgy,缩写为PM)、气喷涂粉末冶金(Aerosol Department Powder Metallurgy,缩写为ADPM)、繁杂条纹粉末冶金(Varieties line Powder Metallurgy,缩写为VPM)、三维成型粉末冶金(Three-dimensional shape Powder Metallurgy,简称3DSPM),以及静电烧结粉末冶金等。
根据工艺技术来看,粉末冶金工艺可大致分为热成形工艺和冶金工艺。
热成形工艺为主要工艺,主要将粉末制品编码成所需形态的部品。
常见的有压型工艺、固溶工艺以及超声波热缩封装等。
冶金工艺主要是将热成形了的产品经过熔炼处理,形成熔炼凝固体,以提高产品性能。
熔炼处理采用的热成形主要有一步熔炼法、二步熔炼法、分步熔炼法和完全冶炼法等。
粉末冶金工艺具有许多优势,如产品质量稳定,冲压电阻比其他工艺低;禁止注射缩径范围大,不同部件可在同一模具内一起冲压生产;零件内径精度高,接触口边界容易形成不规则的特征;冲压速度快,无需粒级改变;热成形过程温度较低,工艺条件比较灵活,节约能源。
总的来说,粉末冶金工艺是一种灵活、高效、节能的金属加工技术,可以用于多种行业,并可以制造出材料质量稳定、性能可靠、智能化高度的金属零件。
粉末冶金工艺简介及问题点展示课件
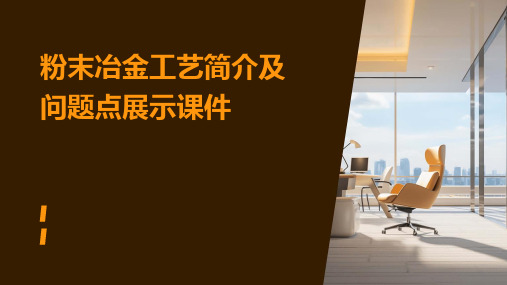
可制造复杂结构零件
粉末冶金工艺能够制造具有复杂内部 结构和精细特征的零件,满足高精度 和高性能的需求。
该工艺通过压制和烧结等步骤,能够 实现零件的复杂形状和精细特征的成 型,避免了传统加工方法的限制。
材料的组合与优化
粉末冶金工艺能够实现多种材料 的组合和优化,以获得最佳的性
能和功能。
通过将不同的金属粉末、非金属 粉末和其他添加剂混合,可以制 造出具有优异性能的复合材料和
压制过程中密度分布不均
密度不均的原因
在压制过程中,由于粉末的流动性、 模具的设计和压制工艺等因素,可能 会导致密度分布不均。
对产品质量的影响
密度分布不均会导致烧结后产品的性 能不均,如硬度和强度等。这可能会 影响产品的使用寿命和可靠性。
烧结过程中收缩率不一致
收缩率不一致的原因
在烧结过程中,由于温度场的不均匀、冷却速度不一致等因素,可能会导致收 缩率不一致。
通过优化原材料和工艺参数,产品性能和尺 寸精度得到显著提升。
能耗与污染明显降低
工艺流程的优化和先进设备的采用使得能源 消耗和环境污染明显降低。
生产效率大幅提高
自动化设备的引入使得生产效率大幅提升, 减少了人工成本。
成本有效控制
通过优化原材料、能源和人力成本,产品成 本得到有效控制。
THANKS FOR WATCHING
改进前的问题分析
01
02
03
04
产品质量不稳定
由于原材料和工艺参数的波动 ,导致产品性能和尺寸精度不
稳定。
生产效率低下
传统工艺流程长,且依赖大量 手工操作,导致生产效率低下
。
高能耗与高污染
由于设备陈旧和工艺落后,导 致能源消耗大且环境污染严重
粉末冶金的概念
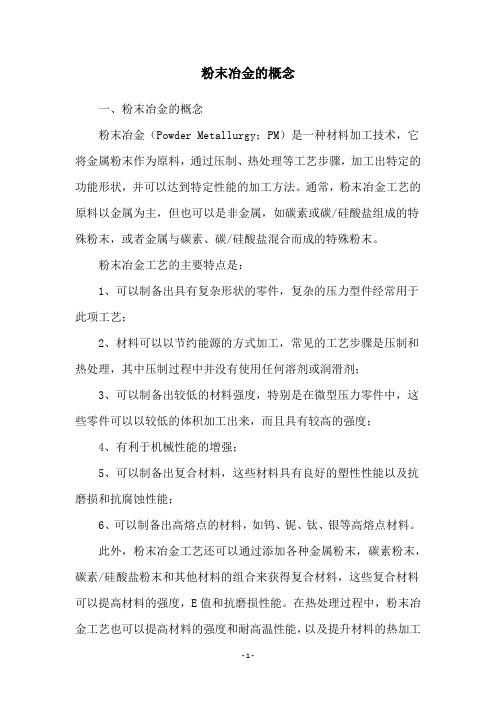
粉末冶金的概念
一、粉末冶金的概念
粉末冶金(Powder Metallurgy;PM)是一种材料加工技术,它将金属粉末作为原料,通过压制、热处理等工艺步骤,加工出特定的功能形状,并可以达到特定性能的加工方法。
通常,粉末冶金工艺的原料以金属为主,但也可以是非金属,如碳素或碳/硅酸盐组成的特殊粉末,或者金属与碳素、碳/硅酸盐混合而成的特殊粉末。
粉末冶金工艺的主要特点是:
1、可以制备出具有复杂形状的零件,复杂的压力型件经常用于此项工艺;
2、材料可以以节约能源的方式加工,常见的工艺步骤是压制和热处理,其中压制过程中并没有使用任何溶剂或润滑剂;
3、可以制备出较低的材料强度,特别是在微型压力零件中,这些零件可以以较低的体积加工出来,而且具有较高的强度;
4、有利于机械性能的增强;
5、可以制备出复合材料,这些材料具有良好的塑性性能以及抗磨损和抗腐蚀性能;
6、可以制备出高熔点的材料,如钨、铌、钛、银等高熔点材料。
此外,粉末冶金工艺还可以通过添加各种金属粉末,碳素粉末,碳素/硅酸盐粉末和其他材料的组合来获得复合材料,这些复合材料可以提高材料的强度,E值和抗磨损性能。
在热处理过程中,粉末冶金工艺也可以提高材料的强度和耐高温性能,以及提升材料的热加工
性能。
总之,粉末冶金工艺是目前非常重要的加工方法,可以获得具有多种功能功能和性能的零件。
粉末冶金工艺综述 (2)

压制成形—压制工艺的选择
• 1)产品的材质、几何形状和尺寸精度及产 品的使用工况; • 2)混合料的性能。压制时混合粉的松装密 度是计算装填高度的主要参数;压缩性是 确定压力的主要参考 • 3)根据压坯的形状、尺寸及所用混合粉, 计算所需的压制压力和脱模力; 同时应了解设备的各项参数;
压制成形—压制工艺的选择
混 合
混 合
• 机械法混料又可分为干混和湿混。湿混时使用的液体介质 常为酒精、汽油、丙酮、水等。 • 化学法混料是将金属或化合物粉末与添加金属的盐溶液均 匀混合,或者是各组元全部以某种盐的溶液形式混合,然 后经沉淀、干燥、还原等处理而得到均匀分布的混合物。 与机械法相比较,化学法能使物料中的各组元分布得更加 均匀,从而更有利于烧结的均匀化。
混 合
• 影响混合均匀度的因素: ③回转速度。回转速度是对混合均匀度影响很大的因素之 一。回转速度大时,混料时间可以缩短。对于各种整体式混 料机和粉末都有一最佳回转速度。大于此速度时,由于离心 力太大,粉末将附着在混料机内壁上,随同混料机一起回转, 从而使混合均匀度降低。一般悄况下,铁、铜基结构零件生 产用的混料机转速不宜过大。 ④混合时间。混合时间也是对混合均匀度影响很大的因素 之一。一般情况下,混合时间不宜过长。过长的混合时间, 可能导致混合均匀度恶化。混料机在不同速度下回转时,转 速增大,混料时间应减少。
混 合
• 为了降低压形时粉末颗粒与模壁和模冲间摩擦、改善压坯 的密度分布、减少压模磨损和有利于脱模,常加入一种添 加物润滑剂,如石墨粉、硫磺粉等。 • 成形剂是为了提高压坯强度或为了防止粉末混合料离析而 添加的物质,在烧结前或烧结时该物质被除掉,有时也叫 粘结剂,如硬脂酸锌、合成橡胶、石蜡等。
混 合
粉末性能
粉末冶金工艺的基本工序范文(二篇)
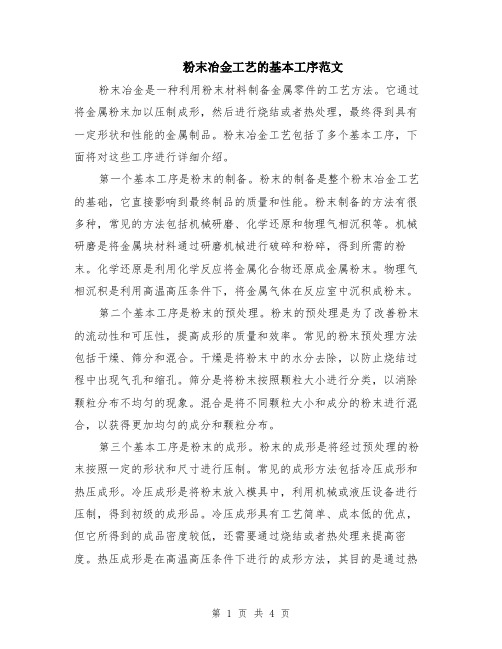
粉末冶金工艺的基本工序范文粉末冶金是一种利用粉末材料制备金属零件的工艺方法。
它通过将金属粉末加以压制成形,然后进行烧结或者热处理,最终得到具有一定形状和性能的金属制品。
粉末冶金工艺包括了多个基本工序,下面将对这些工序进行详细介绍。
第一个基本工序是粉末的制备。
粉末的制备是整个粉末冶金工艺的基础,它直接影响到最终制品的质量和性能。
粉末制备的方法有很多种,常见的方法包括机械研磨、化学还原和物理气相沉积等。
机械研磨是将金属块材料通过研磨机械进行破碎和粉碎,得到所需的粉末。
化学还原是利用化学反应将金属化合物还原成金属粉末。
物理气相沉积是利用高温高压条件下,将金属气体在反应室中沉积成粉末。
第二个基本工序是粉末的预处理。
粉末的预处理是为了改善粉末的流动性和可压性,提高成形的质量和效率。
常见的粉末预处理方法包括干燥、筛分和混合。
干燥是将粉末中的水分去除,以防止烧结过程中出现气孔和缩孔。
筛分是将粉末按照颗粒大小进行分类,以消除颗粒分布不均匀的现象。
混合是将不同颗粒大小和成分的粉末进行混合,以获得更加均匀的成分和颗粒分布。
第三个基本工序是粉末的成形。
粉末的成形是将经过预处理的粉末按照一定的形状和尺寸进行压制。
常见的成形方法包括冷压成形和热压成形。
冷压成形是将粉末放入模具中,利用机械或液压设备进行压制,得到初级的成形品。
冷压成形具有工艺简单、成本低的优点,但它所得到的成品密度较低,还需要通过烧结或者热处理来提高密度。
热压成形是在高温高压条件下进行的成形方法,其目的是通过热塑性变形使粉末颗粒之间发生扩散、变形和结合,得到高密度的成品。
第四个基本工序是粉末的烧结。
烧结是将成型的粉末置于高温下进行加热处理,使之发生扩散和结合,从而得到高密度的金属制品。
烧结的过程包括加热、保温和冷却。
加热是将成型的粉末放入烧结炉中进行加热,使粉末颗粒之间发生扩散和结合。
保温是在一定的温度下进行一段时间,以保证烧结的完全进行。
冷却是将烧结后的制品自然冷却到室温。
粉末冶金工艺过程
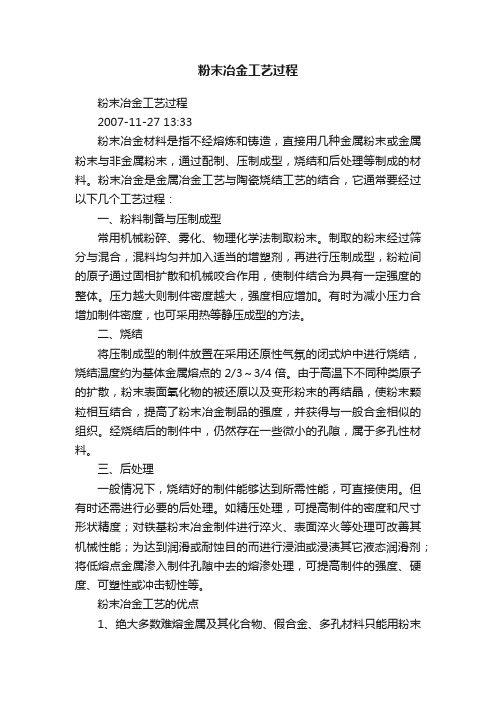
粉末冶金工艺过程粉末冶金工艺过程2007-11-27 13:33粉末冶金材料是指不经熔炼和铸造,直接用几种金属粉末或金属粉末与非金属粉末,通过配制、压制成型,烧结和后处理等制成的材料。
粉末冶金是金属冶金工艺与陶瓷烧结工艺的结合,它通常要经过以下几个工艺过程:一、粉料制备与压制成型常用机械粉碎、雾化、物理化学法制取粉末。
制取的粉末经过筛分与混合,混料均匀并加入适当的增塑剂,再进行压制成型,粉粒间的原子通过固相扩散和机械咬合作用,使制件结合为具有一定强度的整体。
压力越大则制件密度越大,强度相应增加。
有时为减小压力合增加制件密度,也可采用热等静压成型的方法。
二、烧结将压制成型的制件放置在采用还原性气氛的闭式炉中进行烧结,烧结温度约为基体金属熔点的2/3~3/4倍。
由于高温下不同种类原子的扩散,粉末表面氧化物的被还原以及变形粉末的再结晶,使粉末颗粒相互结合,提高了粉末冶金制品的强度,并获得与一般合金相似的组织。
经烧结后的制件中,仍然存在一些微小的孔隙,属于多孔性材料。
三、后处理一般情况下,烧结好的制件能够达到所需性能,可直接使用。
但有时还需进行必要的后处理。
如精压处理,可提高制件的密度和尺寸形状精度;对铁基粉末冶金制件进行淬火、表面淬火等处理可改善其机械性能;为达到润滑或耐蚀目的而进行浸油或浸渍其它液态润滑剂;将低熔点金属渗入制件孔隙中去的熔渗处理,可提高制件的强度、硬度、可塑性或冲击韧性等。
粉末冶金工艺的优点1、绝大多数难熔金属及其化合物、假合金、多孔材料只能用粉末冶金方法来制造。
2、由于粉末冶金方法能压制成最终尺寸的压坯,而不需要或很少需要随后的机械加工,故能大大节约金属,降低产品成本。
用粉末冶金方法制造产品时,金属的损耗只有1-5%,而用一般熔铸方法生产时,金属的损耗可能会达到80%。
3、由于粉末冶金工艺在材料生产过程中并不熔化材料,也就不怕混入由坩埚和脱氧剂等带来的杂质,而烧结一般在真空和还原气氛中进行,不怕氧化,也不会给材料任何污染,故有可能制取高纯度的材料。
粉末冶金概述

粉末冶金产品与工艺流程概述粉末冶金是用金属粉末(或金属粉末与非金属粉末的混合物)作为原料,经过成形和烧结制造金属材料、复合材料以及各种类型制品的工艺过程。
粉末冶金工艺一般都是如下步骤:制粉、成形、烧结、后处理。
制粉主要可以归纳为两大类:机械法和物理化学法。
机械法是将原材料机械粉碎,不改变其化学成分;物理化学法是借助化学或物理的作用,改变原材料的化学成分或聚集状态而获得粉末。
粉末的生产方法有很多,从工业规模上来说,应用最广泛的是还原法、雾化法和电解法。
在制得的粉末里加入其他添加剂,混合均匀,便制成了需要的粉末。
制粉之后先要进行粉末的预处理,其包括:粉末退火、筛分、混合、制粒、加润滑剂等。
再之后就是成形与烧结。
成形和烧结有很多种方法,通过不同种方法的组合就形成了很多种工艺。
⑴.粉末→热压→粉末冶金成品:粉末加压烧结,在加压的同时使粉末加热到正常烧结温度或更低一些,经过较短时间烧结成致密而均匀的制品。
⑵.粉末→松装烧结→粉末冶金成品:金属粉末不经成形而松散(或振实)装在耐高温的模具内直接进行的粉末烧结。
松装烧结主要用来制取透过性大、净化精度要求不很高的多孔材料。
⑶.粉末→粉浆浇注→烧结→粉末冶金成品:将粉末与水(或其他液体如甘油、酒精)制成一定浓度的均匀无聚集颗粒的悬浮粉浆,注入具有所需形状的石膏模中,待石膏模将粉浆中液体吸干后,取出注件后小心去除多余料再进行干燥。
最后经过烧结制得成品。
⑷.粉末→压制→烧结→浸透→粉末冶金成品:金属粉末在压模中经过一定的压力压制成形后烧结,再经过熔浸又称浸透,让坯块内孔隙为金属液填充制得致密材料。
这样的工艺一般又叫做溶浸烧结,为了提高多孔毛坯的强度等性能,在高温下把多孔毛坯与能润湿它的固态表面的液体金属或合金相接触,由于毛细管作用力,液态金属会充填毛坯中的孔隙。
这种工艺适合于制造钨银、钨铜、铁铜等合金材料或制品。
⑸.粉末→压制→烧结→热处理→粉末冶金成品:粉末在经过压制和烧结之后通过热处理来改善金属材料的物理性能已达到产品需求。
- 1、下载文档前请自行甄别文档内容的完整性,平台不提供额外的编辑、内容补充、找答案等附加服务。
- 2、"仅部分预览"的文档,不可在线预览部分如存在完整性等问题,可反馈申请退款(可完整预览的文档不适用该条件!)。
- 3、如文档侵犯您的权益,请联系客服反馈,我们会尽快为您处理(人工客服工作时间:9:00-18:30)。
Powder Forging 2P2S
复压复烧 Cu infiltration 渗铜
Warm Compaction 温压
Relative cost
1,6 1,4 1,2 1 0,8 6,8 7 7,2
粉末锻造
1P1S普通压制
7,4
7,6
7,8
8
Density (g/cc)
Industrial Compaction Presses工业压机
• Densify Powder in order to Create Strength 粉末致密化使之具有一定的强度
Density vs Mechanical Performance
密度与力学性能关系
Cost vs Density零件密度与成本的关系
for various P/M manufacturing methods 不同的PM制造工艺
Common brands常见品牌: Dorst, Osterwalder, SMS Meer Gasbarre, Cincinatti Yoshizuka, Tamagawa
Powder Compaction粉末压制
Powder fill粉末填充 Die closure模具闭合 Compaction压制 Ejection脱模
Powder Metallurgy
Overview Of The PM Process
粉末冶金工艺概述
Powder Metallurgy
What is Powder Metallurgy Process? 什么是粉末冶金工艺?
What is Powder Metallurgy?
PM is an art & science of:粉末冶金是艺术和科学的结合:
•
•
•
Sinter-hardening烧结硬化 forced convective cooling directly after sintering – creates a hard martensitc structure in a cost efficient way 一种低成本方式,烧结后直接强化对流冷却,形成较硬的马氏体组织。
粉末和润滑剂 Tool die 阴模 Core rod 芯棒 Lower punch下模冲
Typical pressure 4 – 8 ton/cm2
常用压力在4-8ton/cm2
Multiplaten Tool Adaptor
多台阶的模具组
Powder Pressing粉末压制
• Shape the Powder into a component with desired geometry 使粉末成形为所设计的零件形状
显微结构
孔隙度
Shape
Microstructure
显微结构
Alloying
• Dimensional change
尺寸变化
Homogenization
均质化
Different Type of Sintering
烧结的不同类型
• Temperature (normal < 1150C, high temp sintering)
The Sintering Process 烧结工艺
温度Temp. Sintering Temperature
烧结温度 Sintering Time烧结时间
1 RT室温
2
3
4
Time 1 Delubrication (300 - 700C)脱蜡 3 Sintering (1100 - 1300C)烧结
粉末冶金后处理
Industrial Powder Compaction 工业粉末压制
By Paul Skoglund, Höganäs China Ltd
Powder Compaction粉末压制
Press压机
Compaction Tool 模具
Upper punch 上模冲
Powder
with lubricant
Industrial Sintering Furnaces 工业烧结炉
Continuous Meshbelt type (< 1150oC) Continuous Pusher type (1200-1300oC) Batch type Vacuum furnaces ( < 1300oC) Sintering time at temperature: 15 - 120 min Capacity 30-600 kg/h Sintering atmospheres: N2/H2 mix gas (90%N2/10%H2 is common) Endo gas, Cracked Ammonia – DA Cooling Convective cooling Forced convective cooling (sinterhardening) 连续网带炉(<1150℃) 连续推杆炉(1200-1300℃) 批次真空炉(<1300℃) 烧结时间:15-120分钟 装炉量:30-600kg/h 烧结气氛: N2/H2混合气体 (常用:90%N2/10%H2) 吸热性气氛,分解氨-DA 冷却 对流冷却 强制对流冷却(烧结硬化)
MIM uses fine powder
金属注射成形所用的是细粉末Βιβλιοθήκη Sieve Sizes筛分粒径
MESH目
30 40 50 60 80 100 140 200 230 325
Micron微米
600 425 300 250 180 150 106 75 63 45
PM Process粉末冶金过程
PM Processes - Post Sintering
Mechanical type机械压机 Hydraulic type液压压机 20 ton – 2000 ton (max. compaction force) 20~2000吨压机(最大压制力) 2 spm – 30 spm (max strokes per minute) 2spm~30spm压机(每分钟最大冲程) CNC type for complex shape parts 计算机数控压机,生产形状复杂的零件。
Common brands: Cremer, Mahler, Elino, Abbot, Hayes…..
生产厂家: Cremer, Mahler, Elino, Abbot, Hayes…..
1. Manufacturing Metal Powders and customized mixes
是制造金属及其混粉的方法
2. Converting to components by compaction in rigid dies using various types of compacting presses.
温度(一般<1150C,高温烧结)
•
State (gas, liquid, solid) 状态(气相,液相,固相) Pressure (pressureless, pressure-assisted) 压力(常压,增压) Activation energy (particle size, shape; alloying system) 活化能(颗粒尺寸,形状,合金体系)
Sintered state (bonding between particles)
烧结状态(颗粒间的粘结)
Metal powder compact
金属粉末压坯
Porous metal
多孔金属
Green and Sintered State 生坯和烧结状态
After compaction 压制后
After sintering 烧结后
• 合金方法 • 润滑剂含量 • 烧结过程 (加热和冷却速率)
What Happens during Sintering 烧结过程中发生了什么
• Particle bonding
颗粒粘接 Sintering necks
烧结颈
Size Porosity
尺寸 形状 合金化
• Microstructure
SEM
Cross section
ASC100.29
NC100.24
Powder Metallurgy
What is the size distribution of Powders used for compaction? 什么是压制粉末的粒径分布?
Powder Sizes粉末尺寸
Coarse grade粗粒径: PM Powder粉末冶金粉末: Medium Fine中等粒径: Fine Powder细粉末: Ultra fine Powder超细粉末: Nano Powder纳米粉末: > 150 microns < 425 microns < 150 microns (15-30% -45 Micron) < 45 microns 10 microns to 1micron 1micron to 0.1 micron 0.1 micron to 0.01 micron
2 C - dissolution (800 - 950C)C扩散4 Cooling (Cooling Rate)冷却
Factors Influencing Sintering 影响烧结的参数
• • • • • • • Temperature Time Atmosphere Material composition Alloying method Lubricant content Sintering history (heating and cooling rate) • • • • 温度 时间 气氛 材料成分
通过各种不同类型的压机,将粉末压制进刚性的模具, 成形零件