鼠标盖注塑成型过程的Moldflow分析
基于Pro/E和MoldFlow的鼠标上盖注射模具优化设计

如 果把 浇 口设 在 此 位 置 ,型 腔 将 会按 图 3所 示布 置 ,不 仅增 加 了浇 口的 设 计 难 度 ,还 会 增 加 分 型 面 的 斜 率 ,加 大 凹凸模 的加 工 难 度 。通 过 观
察 ,发 现 塑 件 的 尾 部 虽 然 不 是 最 好 的浇 口位 置 ,
j l
. , . . . .
{ 、
返 回
∞Ⅵ 衍 商 一 赫
m “ 50 . ,w
¨州
3
r
;
}
c抖 褂 麓 { £
.
耐 j
£ 、 南
’
V
0 v O
图 1 发 火 电压 图 0
M
^
正 负 3 以 内,满足 系统指 标要求 。 ms
但 是 也 在 可 接 受 的 区域 范 围之 内 , 而且 按 照 图 4
所 示 布 置 型腔 ,较 之 前 的排 列 方 式 分 型 面斜 率会 小 很 多 ,所 以将浇 口位置 放在 尾部 。 22 冷却 分析 .
设 计 出 如 图 5所 示 的 冷 却 水 路 , 使 用
图 1 鼠 标 上 盖 三 维 图
05
1
l5
2
25
1 4 O1
+1
时 间 () s
l2 2 2 2l 5 1
l2 2 0 2l 7 l
. 2 + 2
图 8 电容 电压 变 化 图
28 86
28 89
3 4 4 2 4 7 5 0 5 0 0 3
+ 3
2 + 3 + 3
1 ~3 。 。。 塑 件 材 料 为 A S B ,成 型 收缩 率较 小 , 综 合 性 能 好 ,冲击 强 度 、力 学 强 度 较 高 ,尺 寸 稳 定 ,耐 化 学 性 ,电气 性 能 良好 ;但 吸 湿 性 强 ,必 须充 分 干 燥 ,要 求表 面 光 泽 的 塑 件 要 求 长时 间预 热 干燥 。
moldflow分析报告
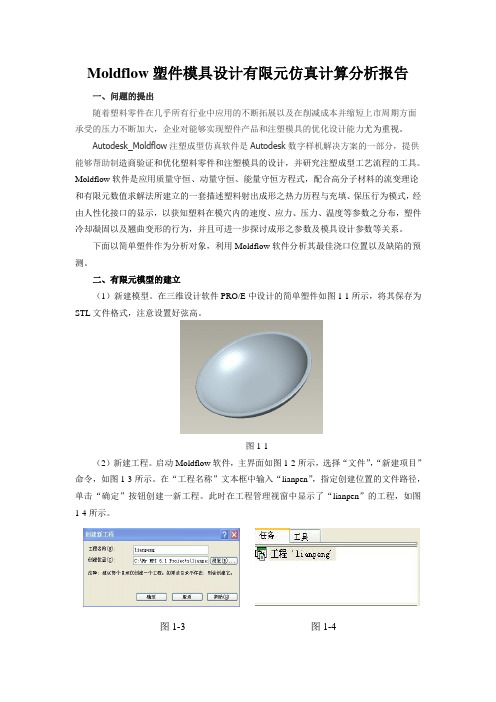
Moldflow塑件模具设计有限元仿真计算分析报告一、问题的提出随着塑料零件在几乎所有行业中应用的不断拓展以及在削减成本并缩短上市周期方面承受的压力不断加大,企业对能够实现塑件产品和注塑模具的优化设计能力尤为重视。
Autodesk_Moldflow注塑成型仿真软件是Autodesk数字样机解决方案的一部分,提供能够帮助制造商验证和优化塑料零件和注塑模具的设计,并研究注塑成型工艺流程的工具。
Moldflow软件是应用质量守恒、动量守恒、能量守恒方程式,配合高分子材料的流变理论和有限元数值求解法所建立的一套描述塑料射出成形之热力历程与充填、保压行为模式,经由人性化接口的显示,以获知塑料在模穴内的速度、应力、压力、温度等参数之分布,塑件冷却凝固以及翘曲变形的行为,并且可进一步探讨成形之参数及模具设计参数等关系。
下面以简单塑件作为分析对象,利用Moldflow软件分析其最佳浇口位置以及缺陷的预测。
二、有限元模型的建立(1)新建模型。
在三维设计软件PRO/E中设计的简单塑件如图1-1所示,将其保存为STL文件格式,注意设置好弦高。
图1-1(2)新建工程。
启动Moldflow软件,主界面如图1-2所示,选择“文件”,“新建项目”命令,如图1-3所示。
在“工程名称”文本框中输入“lianpen”,指定创建位置的文件路径,单击“确定”按钮创建一新工程。
此时在工程管理视窗中显示了“lianpen”的工程,如图1-4所示。
图1-3 图1-4图1-2(3)导入模型。
选择“文件”,“输入”命令,或者单击工具栏上的“输入模型”图标,进入模型导入对话框。
选择STL文件进行导入。
选择文件“lianpen.stl”。
单击“打开”按钮,系统弹出如图1-5所示的“导入”对话框,此时要求用户预先旋转网格划分类型(Fusion)即表面模型,尺寸单位默认为毫米。
图1-5单击“确定”按钮,脸盆模型被导入,如图1-6所示,工程管理视图出现“lp1_study”工程,如图1-7所示,方案任务视窗中列出了默认的分析任务和初始位置,如图1-8所示。
moldflow 案例

moldflow 案例Moldflow案例是指使用Moldflow软件进行塑料注塑成型分析的实例。
Moldflow是一款由Autodesk公司开发的塑料模具设计和分析软件,它可以帮助工程师在模具制造之前预测和优化塑料零件的成型过程。
以下是一个简单的Moldflow案例:1. 导入模型:首先,在Moldflow中导入一个三维塑料零件模型,该模型可以是自行设计的,也可以是从其他软件(如Autodesk Inventor、SolidWorks等)导入的。
2. 模型准备:对导入的模型进行必要的简化,以减少计算复杂度。
这包括删除不必要的特征、合并面、修整边等。
3. 材料选择:根据塑料零件的性能要求,选择合适的塑料材料。
Moldflow软件中包含了大量的塑料材料库,可以根据实际需求进行选择。
4. 模具设计:根据塑料零件的尺寸和成型要求,设计合适的模具结构。
这包括模具类型、腔数、冷却系统、顶出器等。
5. 网格划分:对模型进行网格划分,以便进行后续的分析。
Moldflow会自动进行网格划分,但用户可以根据需要对网格进行手动调整。
6. 分析设置:设置分析参数,包括成型条件(如注射速度、注射压力、模具温度等)、分析类型(如填充时间、冷却时间、保压时间等)以及结果输出选项。
7. 分析结果:运行分析后,Moldflow会生成一系列的分析结果,如填充曲线、压力分布图、翘曲变形图等。
这些结果可以帮助工程师评估塑料零件的成型性能,找出可能存在的问题,并进行相应的优化。
8. 结果分析与优化:根据分析结果,对模具设计和成型条件进行优化。
这可能包括修改模具结构、调整材料参数、改变成型条件等。
9. 报告生成:最后,根据分析结果和优化方案,生成相应的报告,以供后续的模具制造和生产过程参考。
这个案例仅供参考,实际的Moldflow案例可能会根据具体需求和行业领域有所不同。
总之,Moldflow案例旨在帮助工程师通过模拟塑料零件的成型过程,提高模具设计质量和生产效率。
鼠标上盖的模具设计毕业论文

毕业(设计)论文鼠标上盖的模具设计系(部)机电工程系专业模具设计与制造班级09模具设计与制造一班指导教师姓名学号课题研究的是鼠标上盖的模具设计。
本文在分析零件成型工艺的基础上,介绍了注塑加工工艺的前期准备工作。
采用UG设计方法进行了鼠标上盖的三维造型,计算了鼠标上盖的尺寸,对鼠标的材质进行分析,从鼠标的实用性上进行考虑,设计和研究利用软件进行初步模拟设计修改,做出立体图像进行测试,根据产品的实用性进行全面的修正,再对产品的用料和加工方法仔细考虑,选择塑料进行加工并且对塑料的种类进行了逐一测试,以便于更好的加工,根据材料选择更好的加工方法和制作工艺,对加工工具进行挑选,根据提前的计算值为参考对注射机进行调试,利用软件中的仿真功能对熔体流动进行仿真模拟分析,进一步的掌握了此类绘图仿真软件的应用,为以后的研究和学习打下了基础。
关键词:鼠标上盖,UG,模具设计,仿真模拟1 绪论 01.1课题研究背景 01.2塑料模设计发展现状 (1)1.3课题的主要内容和意义 (3)2 鼠标上盖设计及成型工艺分析 (4)2.1产品开发依据用途清单 (4)2.2制品结构和形状的设计 (4)2.3制品材料选择 (5)2.4注射工艺选择 (8)3 注射机的选择和校核 (10)3.1注射量计算 (10)3.2注射压力校核 (10)3.3锁模力校核 (10)3.4开模行程和模板安装尺寸校核 (11)4 模具设计 (13)4.1分型面位置和形状的设计 (13)4.2模具浇注系统设计 (14)4.3成型零部件结构设计 (16)4.4塑料模具力学设计 (19)4.5合模导向和定位机构设计 (20)4.6脱模机构设计 (20)4.7排气方式 (21)4.8模温调节系统 (21)4.9模具材料 (23)总结 (24)参考文献 (25)致谢 (26)1 绪论1.1课题研究背景模具工业是国民经济的基础工业,被称为“工业之母”。
在塑料制品生产过程中,模具的设计是相当重要的一环;因为模具的好坏直接影响到塑件质量,以及价格的高低。
注塑成型CAE报告(mlodflow分析报告)

材料成型CAE论文(Moldflow注塑工艺分析)在Moldflow Plastic Insight 6.0环境中,运用MPI的各项菜单及其基本操作,来实现对所选制件在注塑成型过程中的填充、流动、冷却以及翘曲分析,以此来确定制件的最佳成型工艺方案,为工程实际生产提供合理的工艺设置依据,减少因工艺引起的制件缺陷,有助于降低实际生产成本,提高生产效率。
一、导入零件导入文件guolingling.stp。
选择【Fusion】方式。
二、划分网格【网格】—【生成网格】—【立即划分】三、网格诊断【网格】—【网格诊断】,诊断结果如下:图1、网格诊断对诊断结果进行检查,发现连通区域为1,交叉边为0,最大纵横比为7.218616<8,均符合要求,网格划分合理。
四、选择分析类型1、浇口位置1)双击任务栏下的【充填】—【浇口位置】;2)选择材料:双击任务栏下的【材料……】—【搜索】—输入“ABS”—搜索—在结果中任选一种材料,点击【选择】即可;3)双击任务栏下的【立即分析】。
在分析结果中勾选:Best gate location,查看最佳浇口位置,如下图:图2、最佳浇口由最佳浇口位置分析结果可以知道,浇口设在零件上表面的中间部位,零件的注塑工艺效果好。
可采用直接浇口。
2、流动分析1)设置注射位置:设置之前,先将方案备份。
【文件】—【另存方案为】。
双击任务栏下的【设置注射位置】—鼠标变成一个十字光标和一漏斗形状,然后在上一步分析中的最佳浇口位置处单击,即可完成注射点的设置;2)选择分析类型:双击任务栏下【浇口位置】—【流动】;3)设置浇注系统:【建模】—【浇注系统向导】,设定直浇道、横浇道、内浇道的尺寸,各浇道尺寸均采取的默认值。
根据制件的形状特征以及最佳浇口位置,采用直接浇口。
4)双击任务栏下的【立即分析】。
查看分析结果中的“pressure at V/P swithover”项,发现出现了浇不足的现象,经分析是由于注射压力过小所引起的,只需增大注射压力即可。
Moldflow在气体辅助注塑成型中的应用分析

Moldflow在气体辅助注塑成型中的应用一.引言气体辅助注塑成型(简称气辅成型)是塑料加工领域的一种新方法,80年代开始用于生产实际,气体辅助注射成型比传统注射成型多一个气体注射阶段,由气体推动塑料熔体充满模具型腔,因此在气辅成型制品设计和模具设计时必须提供明确的气道来引导气体的走向。
气道几何尺寸的大小、截面形状的确定和位置的布置都会影响到气体的穿透和气体对熔体流动的干涉,从而最终影响到成型制品的质量。
根据气辅成型时射入型腔的熔融塑料的体积不同,气辅成型工艺大致可分为3种方式:a、中空成型,即熔体射入型腔充填到型腔体积的60-70%时,停止注射熔体,开始注入气体,直至保压冷却定型。
这种工艺主要适用于类似把手、手柄之类的大壁厚塑料制品,应用效果最理想。
b、短射,即熔体充填到型腔体积的90-98%时,开始进气。
该方法主要用于较大平面的厚壁或偏壁制品。
c、满射,即熔体充填至完全充满型腔时才注入气体,由气体填充因熔体体积收缩而产生的空间,并将气体保压和熔体保压配合使用,使制品翘曲变形大大降低,用于较大平面的薄壁制品成型,其工艺控制较复杂。
前两种方法也称为缺料气辅注射法,后者称为满料气辅注射法。
气辅工艺原理第一阶段:塑料注射:熔体进入型腔遇到温度低的模壁,形成一个较薄的凝固层。
第二阶段:气体注射:惰性气体进入熔融的塑料,推动中心未凝固的塑料进入尚未充满的型腔。
第三阶段:气体入射结束:气体继续推动塑料熔体流动直到熔体充满整个型腔。
第四阶段:气体保压结束:在保压状态下,气道中的气体压缩熔体,进行补料确保制件的外观。
二.气辅注射成型技术的特性(1)可保证壁厚差异较大制品的成型质量采用气辅技术可将制品壁厚处“挖空”设计成气道,从而保证壁厚差异较大制品的成型质量。
可简化制品的形状,可将原来因壁厚差异较大需分成几个零件成型然后组合的制品,实现一体成型。
如图1所示。
(2)注射压力低所需注射压力为普通注射成型注射压力的10%~75%,相应成型同样投影面积制品的锁模力也只需普通注射成型锁模力的10%~75%,图2为普通注射与气辅技术成型过程中熔融树脂的压力行为。
基于Moldflow的电机盖注塑成型分析
基于Moldflow的电机盖注塑成型分析王乾【摘要】运用Moldflow软件进行电机盖的注塑成型设计.通过最佳浇口位置分析确定了浇口的形式和进入型腔的位置,并对其进行流动和翘曲的模拟分析,预测可能存在的熔接痕位置、翘曲变形量和气穴分布等缺陷.根据结果有针对性地优化模具设计方案,解决了实际生产中会出现的制品缺陷问题,从而可以提高制品质量,缩短模具设计制造和产品开发周期.%The molding process of motor cover was designed with Moldflow software. The gates into the cavity of the form and position were determined through the best gate location analysis, and the process of flowing and warping were simulately analyzed to predict the possible defects, such as weld lines, warpage and distribution of air traps. The design of the injection mold was optimized according to the analyzing results and the problems of product defects during practical production were solved, thus could improve the product quality and shorten the designing and product developing cycle. [Ch.,11 fig. 1 tab. l0ref. ]【期刊名称】《轻工机械》【年(卷),期】2012(030)003【总页数】4页(P9-12)【关键词】模具设计;计算机辅助工程;模流分析;优化设计【作者】王乾【作者单位】常州轻工职业技术学院模具系,江苏常州213164【正文语种】中文【中图分类】TQ320.66随着塑料工业的迅速发展,产品对模具的要求越来越高,传统的模具设计方法已无法适应产品更新换代和提高质量的要求。
7材料成型过程的计算机模拟——MOLDFLOW
7材料成型过程的计算机模拟——MOLDFLOW MOLDFLOW是一种用于模拟材料成型过程的计算机软件。
它通过计算机模拟,可以预测和优化塑料制品成型过程中的缺陷和问题,如短流、气泡、收缩和变形等。
本文将详细介绍MOLDFLOW的工作原理、应用和优势。
MOLDFLOW的工作原理主要基于有限元分析(FEA)方法。
它将整个成型过程分为多个时间和空间步骤,并对每个步骤中的物理过程进行数值模拟。
通过对塑料的熔融、流动、冷却和固化等过程的模拟,MOLDFLOW能够提供详细的信息,如温度分布、流动速度、塑料填充和压力分布等。
同时,MOLDFLOW还可以通过计算机模拟来预测和优化成型过程中的缺陷和问题,如短流、气泡、收缩和变形等。
MOLDFLOW的应用范围非常广泛。
它可以用于注塑成型、吹塑成型、压缩成型、挤出成型等各种材料成型过程的模拟和优化。
在注塑成型中,MOLDFLOW可以帮助优化模具设计、材料选择和加工参数,从而提高产品质量和生产效率。
在吹塑成型中,MOLDFLOW可以预测和优化瓶嘴的形状和位置,从而改善瓶子的气密性和外观。
在挤出成型中,MOLDFLOW可以模拟材料的流动和变形,从而改善挤出产品的尺寸精度和表面质量。
MOLDFLOW的优势主要体现在以下几个方面。
首先,它能够通过计算机模拟来预测和优化成型过程的缺陷和问题,从而节省了传统试验方法所需的时间和成本。
其次,MOLDFLOW可以提供详细的信息,如温度分布、流动速度、塑料填充和压力分布等,从而帮助工程师更好地理解材料的行为和成型过程的变化。
此外,MOLDFLOW还可以进行多场耦合分析,如热-流体耦合分析、应力-应变耦合分析和热-机械耦合分析等,从而更全面地研究材料成型的多种物理过程。
总之,MOLDFLOW是一种用于模拟材料成型过程的计算机软件。
它通过计算机模拟,可以预测和优化塑料制品成型过程中的缺陷和问题,如短流、气泡、收缩和变形等。
MOLDFLOW的工作原理基于有限元分析方法,它能够模拟塑料的熔融、流动、冷却和固化等过程,并提供详细的信息。
moldflow注塑常见问题分析与解决
常见制品缺陷及产生原因
短射(short shot) 翘曲(Warp) 气穴(air trap ) 熔接痕和熔接线(weld line ) 喷射流(Jetting) 凹陷(Sink Marks) 飞边(Flash) 水波纹 滞流(Hesitation) 流动不平衡 ……
流痕 (Flow marks)
流痕(flow marks)是塑件在浇口附近之涟波状的表面瑕 疵。其产生原因是塑件温度分布不均匀或塑料太快凝固,
熔胶在浇口附近产生乱流、在浇口附近产生冷塑料或是保
压阶段没有补偿足够的塑料。
原因: 低熔胶温度、低 模具温度、低射 出速度、低射出 压力或者流道和 浇口太狭小。
1. 改变塑件设计:设法使射出熔体容易流动,如
增加壁厚,减少过多拐角等
2. 改变模具设计:增加浇口尺寸和数目;增大浇
注系统尺寸;改变浇口位置等
3. 调整成形工艺参数:增加注射体积;增加注射
速度、压力;提高温度等
翘曲(Warp)
翘曲:是指塑件发生扭曲而未能达到设计 形状要求。
产生翘曲主要原因: 1. 冷却不均匀:凸凹模面冷却速 率不同
水波纹(ripples)
• 波纹(ripples)是指接近流动长度末諯的指纹般的小涟波 。波纹缺陷的产生是由于熔胶流动波前部份在模穴壁面冷 却,并且与后到熔胶的持续翻滚冷却之效应.
调整方法
1. 改良塑件设计:增加塑件厚度。
2. 变更模具设计:确定塑件有合适的流道系统, 包括竖浇道、流道和浇口。在整个模具安排适 当的排气系统,特别是流动路径的末端。 3. 调整成形条件:提高模具温度,提高熔胶温度
处理方法
1. 改变浇口位置,按冲击型浇口设计
注塑模具的模流分析
注塑模具的模流分析注塑模具的模流分析是指在注塑模具设计阶段,通过模具的数值模拟计算和分析,得出注塑成型过程中的流动状态。
模流分析可以帮助制造商预测并优化注塑成型过程,以确保产品质量和生产效率。
下面将介绍注塑模具的模流分析的重要性、分析内容及步骤,并分享一些模流分析的实际应用案例。
一、注塑模具模流分析的重要性1.预测成型缺陷通过模流分析,可以预测成型缺陷,如短射、气泡、翘曲等,帮助制造商在实际生产前就能够发现潜在的问题并加以改进,减少不良品率。
2.优化模具结构模具结构对注塑成型过程的影响很大,通过模流分析可以确定最佳的模具结构,如冷却系统的设计、料斗和浇口的位置等,从而提高成型效率和产品质量。
3.提高产品质量模流分析能够帮助设计师预测和优化填充过程,从而避免成型缺陷,提高产品质量。
4.节约成本通过模流分析可以调整注塑工艺参数,如注射速度、注射压力等,达到最佳注塑效果,减少成本。
二、注塑模具模流分析的内容1.塑料材料流动模拟模流分析可预测塑料在模腔内部的流动速度、温度分布和填充情况,以及预测和防止可能出现的缺陷,如短射、气泡、翘曲等。
2.模具温度分析通过模流分析,可以优化模具的冷却系统设计,确保模具在注塑过程中能够保持合适的温度,提高成型效率和产品质量。
3.油压分析注塑模具中的油压对模具的开合速度和稳定度影响很大,模流分析可以帮助设计师优化油压系统,确保模具运行平稳。
三、注塑模具模流分析的步骤1.准备模具CAD模型和相关参数首先需要准备注塑模具的CAD模型及相关参数,如材料特性、注射机参数等。
2.进行模型网格划分将模具CAD模型划分成网格,以便进行计算和分析。
3.设置材料和物理参数设置塑料材料的流变性能和热物理参数。
4.设定模具填充流动条件设定注塑过程中的注射速度、压力、温度等参数。
5.进行模流计算和分析通过计算机软件进行模流计算和分析,得出注塑成型过程中的填充情况、温度分布、压力分布等信息。
6.优化设计和参数调整根据模流分析结果,对模具结构和工艺参数进行优化和调整,以改进产品质量和生产效率。
- 1、下载文档前请自行甄别文档内容的完整性,平台不提供额外的编辑、内容补充、找答案等附加服务。
- 2、"仅部分预览"的文档,不可在线预览部分如存在完整性等问题,可反馈申请退款(可完整预览的文档不适用该条件!)。
- 3、如文档侵犯您的权益,请联系客服反馈,我们会尽快为您处理(人工客服工作时间:9:00-18:30)。
鼠标盖注塑成型过程的Moldflow分析严志云北京化工大学机电工程学院,北京(100029)Email:yzy2006test@一、建立模型鼠标是电脑的一个重要外部设备,如图1,其外壳大都是由塑料注塑成型,本文中将对常用的鼠标其上盖的注塑成型进行Moldflow分析,模拟其注塑成型过程,为注塑工艺参数优化提供指导。
图1 鼠标和注塑机通过三维软件PRO/E对鼠标上盖进行建模,如图2。
然后将模型导入分析软件Moldflow中进行网格划分,如图3。
图2 鼠标上盖三维建模图3 鼠标盖的网格划分鼠标盖的材料选用Moldflow软件材料库中的ABS,牌号为Lustran ABS Elite HH 1891:Bayer USA,然后选用注塑机为Moldflow中默认的注塑机,工艺参数也为Moldflow中的默认值,然后对鼠标盖进行最佳浇口位置的分析,结果如图4,蓝色区域为最佳浇口位置。
图4 最佳浇口位置确定浇口位置以后开始建立流道系统。
为了提高生产率,鼠标盖的注塑成型方式设计为一模两腔。
为了不影响其外观,浇口形式选用潜伏式浇口,潜伏式浇口形式示意图如图5,本例中选用普通潜伏式浇口。
确定浇口形式以后,进行浇注系统的设计,如图6,具体尺寸为:主流道长度为50mm,形状为锥形,小口直径为4mm,大口直径为5mm;分流道直径为5mm,浇口中心线起点处直径为1.1mm,浇口中心线终点处直径为3mm。
冷却系统按照Moldflow软件中的默认值进行设计,冷却管道直径为10mm,结构如图7。
图5 潜伏式浇口图6 鼠标盖浇注系统图7 冷却系统二、成型工艺窗口分析上述工作完成以后首先进行制品的成型工艺窗口分析(Molding Window),得到的结果给出了推荐的模具温度、熔体温度和注塑时间,如图8。
图8 成型工艺窗口分析的推荐值成型工艺窗口分析得到工艺参数的推荐值为:模具温度71℃,熔体温度271℃,注塑时间0.5423s。
另外还可以得到模具温度、熔体温度和注塑时间三个参数的范围,如图9。
图9 模具温度、熔体温度和注塑时间三个参数的范围从图中可以得出三个参数的范围为:模具温度49~71℃,熔体温度249~271℃,注塑时间0.1s~3.7s。
如果成型工艺条件位于这个范围之内,那么就可以生产出好质量的制品。
有了成型工艺窗口之后,就可以在这个范围内对成型条件做出适当修改以期获得最好的制品质量。
三、填充分析分析完成型工艺窗口,接下来进行填充分析(Fill分析)获得最佳浇口系统设计,选择最佳浇口位置、浇口数目、最佳浇注系统布局。
工艺参数设置时将成型工艺窗口分析的推荐值代入。
具体分析结果如下:(1)填充时间(Fill time)结果:(2)压力(Pressure)结果:(3)气穴(Air traps)结果:(4)熔接线(Weld line)结果:反复观察fill time的动画显示中制品填充的过程,判断两边型腔填充是否平衡。
观察制品的fill time结果和pressure结果发现两个型腔的充填是平衡的,接下来分析熔接线和气穴,熔接线一共有10条,气穴在制品边缘,能够释放气体,可以通过改变浇口位置来改变熔接线位置,尽量使熔接线数量减少。
(5)注射点的压力时间曲线(Pressure at injection location: XY Plot)结果:(6)剪切应力(Shear stress at wall)结果:(7)剪切速率(Shear rate, bulk)结果:此制品材料允许的最大剪切速率和剪切应力在材料参数中可以查到,最大剪切速率为12000 1/s,最大剪切应力为0.28Mpa。
观察发现潜伏浇口部位剪切速率和应力超过允许值,制品上有的部位也超过允许值,应改变浇口尺寸和形状,将潜伏浇口的尺寸改为:浇口中心线起点处直径为1.5mm,浇口中心线终点处直径为4mm。
重新进行分析,将剪切速率和剪切应力的分析结果与上面的分析结果比较。
剪切速率结果比较:第一次分析的结果第二次分析的结果剪切应力结果比较:第一次分析的结果第二次分析的结果注射点的压力结果比较:第一次分析的结果第二次分析的结果观察结果发现浇口尺寸增大后,剪切速率和剪切应力明显减小,由于浇口位置没变,因此熔接线位置没变,但此制品的熔接线可以满足要求,故对浇口位置不做改变。
分析注射点压力时间曲线发现,浇口尺寸改变后,注射点压力上升过程为单峰值,而没改变尺寸之前,注射点压力有两个峰值,波动较大。
另外由于浇口尺寸增大,注射点压力下降。
四、cool+flow+warp分析进行完填充分析得到优化的浇注系统,然后在Moldflow中进行cool+flow+warp分析,分析结果如下:1.Flow分析结果(1)体收缩率(V olumetric shrinkage)结果:(2)顶出时的收缩率(V olumetric shrinkage at ejection)结果:从结果中可以看出,顶出时体收缩率很不均匀,制品末端收缩较大。
(3)冷凝层因子(Frozen layer fraction)结果:通过动态的观察冷凝层的变化,找出浇口冷凝的时间,如果直到压力释放之后浇口或制品都没有冷凝,那么修改Pack Time为更长的值然后重新分析:从结果中可以看出浇口冷凝的时间为8.8s,压力释放时间如下面所示为11.11s浇口在压力释放之前冷凝。
(4)压力(Pressure)结果:(5)流动前沿温度(Temperature at flow front)结果:从图中可以看出温差为仅1.1℃,满足要求。
(6)注射点压力(Pressure at injection location: XY Plot)结果:(7)Sink index结果从图中可以看出制品末端收缩较大,考虑提高保压压力和延长保压时间。
2.Cool分析结果(1)制品平均温度(Average temperature, part)结果:制品平均温度温差为11℃,满足要求。
(2)冷却剂温度(Circuit coolant temperature)结果:冷却剂的入口和出口温度差为0.26℃,满足要求。
(3)冷却管道管壁温度(Circuit metal temperature)结果,冷却管道管壁温度与模壁温度的差值应当控制在5℃以内,结果满足要求。
(4)制品温度差(Temperature profile, part)结果,制品的温度差异是引起翘曲的主要原因,因此该值应尽量减小,一般应控制在20℃以内:从图中看出温度差为18.65℃,满足要求。
(5)制品的最高温度(Maximum temperature, part)结果:制品的最高温度要低于材料的顶出温度,材料的顶出温度在软件中的材料明细表中为85℃,从下图中可以看出制品的最高温度为51.96℃,满足要求。
(6)制品凝固时间(Time to freeze, part)结果:从图中可以看出制品的冷却很均匀,制品在10.51s凝固。
(7)流道冷却时间(Time to freeze, cold runner)结果:3.Warp分析结果(1)综合因素引起的总体偏差(Deflection, all effects: Deflection)结果:果:(3)综合因素引起的Y方向上的偏差(Deflection, all effects: Y Component)结果:果:从结果中可以看出制品末端的翘曲较大,下面将浇点的位置改变,并增加保压时间和增大保压压力,保压时间设为15s,保压压力设为填充压力的85%,然后重新进行cool+flow+warp分析,将分析结果与上次分析结果对比,查看几个关键因素结果的变化。
(a)体收缩率结果比较:第一次分析结果第二次分析结果第二次分析时制品体收缩率有少量增加,由4.18%增大到4.3%,但是制品收缩更均匀。
(b) 顶出时的收缩率结果比较:第一次分析结果第二次分析结果第二次分析时制品顶出时的收缩率最大值下降。
(c)冷凝层因子结果比较:第一次分析结果第二次分析结果第二次分析制品冷凝更均匀。
(d) 流动前沿温度结果比较:第一次分析结果第二次分析结果第二次分析时制品流动前沿温度为271℃~271.9℃,最高温度略有下降,更均匀一些(e)Sink Index结果比较:第一次分析结果第二次分析结果从图中可以看出Sink由4.3%下降到3.8%。
(f)注射点压力结果比较:第一次分析结果第二次分析结果比较两个曲线发现注塑点压力略有下降,由曲线峰值可以确定该制品成型用注塑机最小注塑压力为53Mpa。
(g)综合因素引起的总体偏差(Deflection, all effects: Deflection)结果:第一次分析结果第二次分析结果比较结果,翘曲最大值由0.3857下降到0.3688,且制品最大翘曲区域减小。
比较两次分析结果的几个关键因素表明,经过修改的工艺参数可以提高制品的质量。
五、确定工艺参数下面先确定翘曲产生的原因,导致收缩变化过大的原因有三条:收缩不均匀、取向不均匀和冷却不均匀。
下面分析各个因素引起的翘曲,确定引起翘曲的主要原因。
1.冷却不均匀导致的翘曲(Deflection, differential cooling: Deflection)结果:2.收缩不均匀导致的翘曲(Deflection, differential shrinkage: Deflection)结果:3.取向不均匀导致的翘曲(Deflection, orientation effects: Deflection)结果:由上面三个图结果显示可知,翘曲的主要原因是收缩不均匀引起的,不是冷却不均匀引起的,因此不用修改冷却管道,考虑制品的收缩可以满足要求,因此不再做工艺参数修改,确定工艺参数如下:材料:Lustran ABS Elite HH 1891:Bayer USA浇注系统尺寸:主流道长度为50mm,形状为锥形,小口直径为4mm,大口直径为5mm;分流道直径为5mm,浇口中心线起点处直径为1.5mm,浇口中心线终点处直径为4mm。
冷却管道直径为10mm。
工艺窗口:模具温度49~71℃,熔体温度249~271℃,注塑时间0.1s~3.7s。
注塑机最小注塑压力为53Mpa。
保压时间为15s,保压压力为填充压力的85%。