瓦楞纸板常见纸病
瓦楞纸板常见纸病的解决方案

瓦楞纸板常见纸病的解决方案一、开胶、假粘1、里纸开胶原因分析:1.1胶质量不符生产要求或腐败变质;1.2上胶量太小;1.3车速过快,瓦楞辊、压力辊热量不足;1.4压力辊压力不足;1.5瓦楞辊、压力辊的中高严重磨损。
解决方法:1.1更换合格胶液;1.2适量调大涂胶量;1.3提高瓦楞辊、压力辊温度,保证180℃以上开机,同时根据温度情况调整车速;1.4适当调整压力辊压力,以里、瓦纸粘合良好,里纸不露楞、瓦纸不碎为宜;1.5打磨或更换新压力辊、瓦楞辊。
1、面纸开胶、夹芯开胶原因分析:2.1胶量过小、烘干机速度过慢;2.2胶液稀薄,涂胶辊挂胶不足;2.3烘干机热板温度不足,胶液未充分糊化;2.4烘干机车速过快,纸板烘干不足;2.5烘干机传输带上面的压载辊没完全落下。
解决方法:2.1适当加大涂胶量,并酌情提高车速;2.2更换胶液或在原胶液中加入适量乳化剂;2.3升高烘干机热板温度至180℃以上开机;2.4减慢车速;2. 5落下压载浮辊。
原因分析:3.1瓦楞辊温度不足;3.2胶量过小,温度过高;3.3车速缓慢造成萃胶;3.4胶液黏度不够。
解决方法:3.1提高单面机工作温度;3.2调整涂胶量,关闭热源,待温度下降至180℃以下,160℃以上开机;3.3提高单面机速度;3.4适当增加胶液黏度。
2、面纸假粘原因分析:4.1烘干机热板温度不足;4.2胶液沉淀变质;4.3纸板在烘干机内停留时间过长。
解决方法:4.1待温度达到胶液能糊化时开机;4.2更换新胶;4.3尽量减少停机时间,换单换纸和断纸再续时动作要果断迅速。
二、倒楞1、单面纸板倒楞原因分析:1.1瓦楞辊磨损;1.2上下瓦楞辊间隙过大;1.3瓦楞纸定量太高且厚度太厚;1.4瓦楞纸水分过大;1.5瓦楞纸未经预热器,可塑性差。
解决方法:1.1磨削或更换瓦楞辊;1.2调整瓦楞辊间隙至0.5mm;1.3更换瓦楞纸;1.4调大预热包角,增大预热面积;1.5将瓦楞纸穿过预热器。
瓦楞纸板不良原因分析

瓦楞纸板不良原因分析瓦楞纸板是由瓦楞纸板芯和面纸组成的一种多层结构材料。
它主要用于包装和运输行业,承载能力强,便于加工和加工。
然而,在实际生产和使用过程中,我们经常会遇到各种瓦楞纸板的不良问题,这直接影响了其使用效果和质量。
以下是对瓦楞纸板不良原因进行分析的一些常见问题。
1.压痕和划痕:瓦楞纸板在生产过程中可能会出现压痕和划痕的问题。
这可能是由于设备不当调整或操作不规范导致的。
例如,如果压痕辊的间距不正确,或者生产速度过快,纸板受到了太大的力,就会出现压痕。
而划痕则可能是由于切割工具不锋利或切割速度过快而导致的。
2.破裂和撕裂:瓦楞纸板在运输和使用过程中容易出现破裂和撕裂的问题。
这可能是由于纸板的强度不足造成的,可能是由于纸板芯的纸张质量不好,或者纸张的厚度不足。
此外,如果瓦楞纸板在存储或运输过程中受到了湿气或温度变化的影响,也会导致纸板的强度减小,容易发生破裂和撕裂。
3.潞水和水印:潞水是指瓦楞纸板表面出现水印痕迹,给纸板的外观质量带来影响。
潞水可能是由于纸张表面平整度不好,或者纸张吸水性能不佳导致的。
此外,如果生产过程中的湿度控制不当,或者纸板表面存在杂质或污染物,也会导致潞水问题的出现。
4.尺寸不一致:瓦楞纸板的尺寸一致性是其质量的重要指标之一、如果纸板的尺寸不一致,可能会导致包装箱的组合困难,影响使用效果。
尺寸不一致的原因可能是由于生产过程中的设备调整不准确或操作不规范,或者纸板芯的厚度不一致,造成纸板的尺寸差异。
5.外观缺陷:瓦楞纸板的外观缺陷可能是指纸板芯表面的起泡、蜂窝状,或者面纸的褶皱、异常颜色等问题。
这些缺陷可能是由于纸张质量不佳、生产过程中的设备故障或不良操作导致的。
例如,如果纸张含水量不均匀,或者设备温度过高,就会导致瓦楞纸板表面起泡或蜂窝状。
综上所述,瓦楞纸板的不良问题可能是由于生产过程中的设备故障、操作不良、纸张质量不佳等因素导致的。
为了解决这些问题,生产厂家应该加强对设备的维护和调整,确保操作人员的培训和规范。
瓦楞纸板生产线常见问题及维护方法

瓦楞纸板生产线常见问题及维护方法1起楞过程中的常见故障及排除方法1.1瓦楞的高度不够,原因可能是压力或温度过低,或者纸张含水分过高。
解决办法是调整压力或辊温,或降低车速,使纸张得以干燥。
1.2瓦楞高度不均一,压出的瓦楞纸两边长短不同呈扇形。
这是由于瓦楞辊平行度不好或两端压力不均匀所致。
如左边瓦楞纸比右边短,应适当将上瓦楞辊左边升高,否则逆向调整。
1.3瓦楞纸卷曲成筒状,主要原因是上下辊筒温度差过大。
应检查上、下辊筒内加热源工作情况,或许其中之一出现故障,可予以修理或更换。
1.4瓦楞纸粘在瓦楞辊面上。
辊面温度过高或原纸水分含量过大都会出现这种现象。
此时应调整辊面温度,使纸张干燥后再压楞,若刮刀与辊槽不贴合,应调整或更换。
2瓦楞辊的维护与保养方法2.1使用前要检查瓦楞辊的平行度和紧固情况,调整好辊间配合压力。
2.2使用时要注意对瓦楞辊进行充分的润滑。
生产中在瓦楞辊表面喷洒少量油雾或减摩剂,会使瓦楞辊间磨损减少,也可防止瓦楞纸断裂和起泡现象的发生。
2.3使用后要清除配合压力,清扫辊面。
切忌用水冲洗高温辊面,否则将会使辊变形,加速磨损。
2.4定期保养。
瓦楞辊正常情况下可生产2000万米左右的瓦楞纸板,如果每天生产5万米瓦楞纸板,大约一年后就要进行磨削加工修理,磨削后的瓦楞辊直径约减少1.0mm,瓦楞的系数增大,原纸与胶粘剂用量也增多。
3瓦楞纸箱在印刷中应注意的问题3.1避免满版印刷瓦楞纸箱满版或四周印刷图文时,除压印辊对瓦楞纸板有压皖的作用外,油墨对纸面还有浸润作用,这些将使瓦楞纸箱的抗压强度降低。
因此,瓦楞纸箱印刷图文越简单越好,并尽可能避免在整个箱面上到处印刷图文,更不要满版印色。
3.2避免带状(与瓦楞纸板机械方向相同)印刷有的装潢设计人员由于缺少印刷工艺知识,设计的纸箱印刷图案有一些横向的渐变线条。
当印刷时,印刷压力将瓦楞压溃。
纸箱的这一区域将发生应力集中,因而最易折断。
3.3油墨颜色要醒目由于瓦楞纸板本身的颜色相当暗,所以在选择印刷的颜色时必须考虑到尽量选用颜色饱和度大的,着色力强的油墨(如大红色),否则印出来的颜色与希望的颜色会有很大差距。
瓦楞纸板各种常见纸病的解决方案
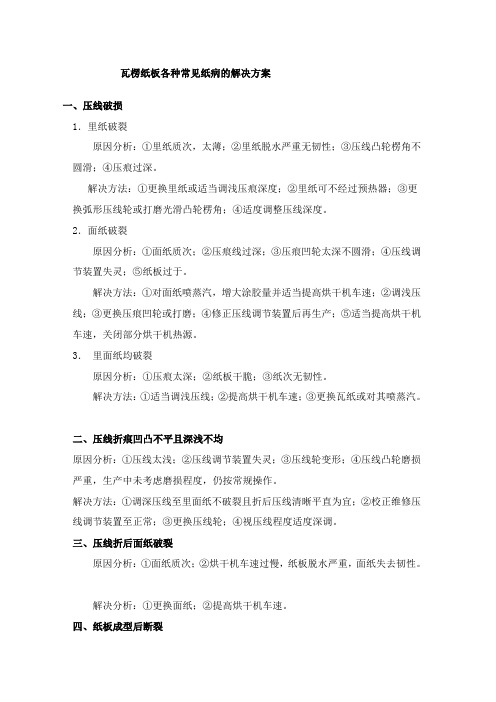
瓦楞纸板各种常见纸病的解决方案一、压线破损1.里纸破裂原因分析:①里纸质次,太薄;②里纸脱水严重无韧性;③压线凸轮楞角不圆滑;④压痕过深。
解决方法:①更换里纸或适当调浅压痕深度;②里纸可不经过预热器;③更换弧形压线轮或打磨光滑凸轮楞角;④适度调整压线深度。
2.面纸破裂原因分析:①面纸质次;②压痕线过深;③压痕凹轮太深不圆滑;④压线调节装置失灵;⑤纸板过于。
解决方法:①对面纸喷蒸汽,增大涂胶量并适当提高烘干机车速;②调浅压线;③更换压痕凹轮或打磨;④修正压线调节装置后再生产;⑤适当提高烘干机车速,关闭部分烘干机热源。
3.里面纸均破裂原因分析:①压痕太深;②纸板干脆;③纸次无韧性。
解决方法:①适当调浅压线;②提高烘干机车速;③更换瓦纸或对其喷蒸汽。
二、压线折痕凹凸不平且深浅不均原因分析:①压线太浅;②压线调节装置失灵;③压线轮变形;④压线凸轮磨损严重,生产中未考虑磨损程度,仍按常规操作。
解决方法:①调深压线至里面纸不破裂且折后压线清晰平直为宜;②校正维修压线调节装置至正常;③更换压线轮;④视压线程度适度深调。
三、压线折后面纸破裂原因分析:①面纸质次;②烘干机车速过慢,纸板脱水严重,面纸失去韧性。
解决分析:①更换面纸;②提高烘干机车速。
四、纸板成型后断裂原因分析:①瓦纸质次;②纸板过分干燥;③成型工序设备调节不当;④压线太浅,瓦楞未压扁或成型后折叠摇盖时高强瓦楞将面纸撑破,瓦楞随之断裂。
解决方法:①更换瓦纸;②保证纸板含水量在10±3左右;③注意成形各工序的设备调节并调至最佳状态;④烘干机加速并加大涂胶量,压线调深。
五、纵切毛边原因分析:①分纸刀已钝或刀刃有缺口;②上下刀咬合过深;③上下刀之间有间隙。
解决方法:①打磨或更换新刀;②调节上下刀重合至最佳状态;③将上下两刀靠紧,用手转动刀轮,灵活不伤刀为宜。
六、横切纸板拖尾原因分析:①横刀已钝;②横切刀上下两片咬合不正,纸板切不断的部位在机械力作用下带起撕裂的面瓦纸;③横切机瞬时加速调节不当,引起阻纸。
瓦楞纸板常见质量问题和产生原因及解决办法

修正瓦楞辊的贴合间隙 清理瓦楞表面异物
瓦楞辊贴合间隙大
• 修正瓦楞辊的贴合间隙
瓦画辊贴合间隙不平衡 •
导纸板位置不正、磨损或带
脏
瓦楞原纸含水水均衡
•
瓦楞原纸的张力太小
•
检查并修正或更换导纸 板
加大予热包角 适当调整张力控制
瓦楞纸板常见质量问题和产生原因及 解决办法
质量问题
平行度
• 瓦楞辊表面带脏
• 清理瓦楞辊,保持干净
• 导纸板位置不正,、带脏或磨损 • 检查、修正、清理或更换导
纸板
• 涂胶辊、浮动辊间隙不当
• 调整二者的贴合间隙
• 粘合剂质量不好
• 检查并重新制作粘合剂
• 瓦楞原纸含水不均衡张力小 • 适当予热并加大张力控制
• 过纸天桥张力不均衡
瓦楞纸板常见质量问题和产生原因及 解决办法
1. 面纸予热包角太大 2. 里纸予热包角太小 3. 过纸天桥堆积过多 4. 单面机涂胶量过大
5.涂胶仙涂胶量偏少
6.车速太低
7.双面机热板温度高
8.重量辊施加压力过大
解决办法
• 减少包角、降低予热 • 增大包角、加强予热 • 减少过纸天桥的堆积 • 适当控制单面机的着胶
量 • 适当增大涂胶机的着胶
7.双面机热板温度高 8.重量辊施加压力过大
解决办法
• 减少包角、降低予热
• 增大包角、加强予热 • 减少过纸天桥的堆积 • 适当控制单面机的着胶
量 • 适当增大涂胶机的着胶
量 • 根据实际运行质量,适
当提高车速
• 提高车速或人为降低热 板
• 适当投放重量辊
PPT文档演模板
瓦楞纸板常见质量问题和产生原因及 解决办法
瓦楞纸板各种常见纸病的解决方案ppt课件
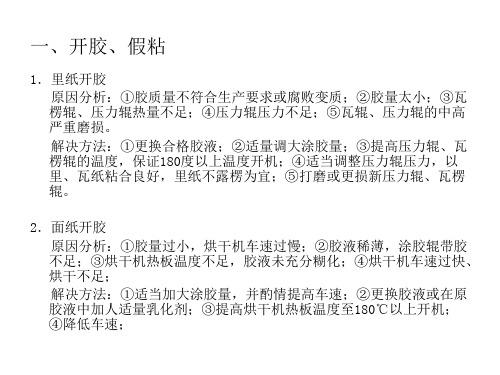
原因分析:①天桥单面纸板堆积过多所致;②单面纸板张力太小;③纵 切机后的托纸架高低位置不当。 解决方法:①尽量减少单面纸板在天桥上的堆积,避免因过量挤压造成 韵折痕;②调整天桥上单面纸板张力至折痕消失为宜;③对纵切机后托 纸架高低的调整,视纵切纸板送人横切机的角度而定,只要在托纸架部 分不出现纸板折痕为准。
二十、面纸划痕
原因分析:①原纸制造时的划痕;②预热器有毛刺所致;③烘干机热 板上面有胶渣纸屑等异物,便磨擦划伤面纸;④烘干机后的各纸板托 架宥毛刺或硬物划伤;⑤堆码机转送带接扣部分开裂。 解决方法:①更换瓦纸;②打磨预热器;③清除热板异物;④清除异 物打磨毛刺;⑤更换皮带扣或将翘起带扣敲平。
二十一、白卡纸板泛黄
原因分析:烘干机车速过慢,热板温度过高,白卡面纸被过分烘烤所 致,胶液碱量过重。 解决方法:提高烘干机车速,减少白卡板在烘干机内的停留时间,适 当减少胶液用碱量。
二十二、纸板里纸布满皱痕
原因分析:里纸定量低于150g,经烘干机传输带压迫即出现米粒大小 的凸凹小坑。 解决方法:更换大克重的里纸,若不影响产品质量也可不必更换。
2. 面纸破裂 原因分析:①面纸质次;②压痕线过深;③压痕凹轮太深不圆滑;④ 压线调节装置失灵;⑤纸板过于。 解决方法:①对面纸喷蒸汽,增大涂胶量并适当提高烘干机车速;② 调浅压线;③更换压痕凹轮或打磨;④修正压线调节装置后再生产; ⑤适当提高烘干机车速,关闭部分烘干机热源。
3.里面纸均破裂 原因分析:①压痕太深;②纸板干脆;③纸次无韧性。 解决方法:①适当调浅压线;②提高烘干机车速;③更换瓦纸或对其 喷蒸汽。
2.面纸起皱 原因分析:①导纸辊不平行;②烘干机进纸口偏斜;③瓦纸水分不平 衡;④瓦纸两端张力不平衡。 解决方法:①校正导纸辊;②纠正烘干机进纸口;③增大瓦纸预热面 积;④更换瓦纸。
瓦楞纸板生产线故障与对策

瓦楞纸板生产线故障与对策在制造瓦楞纸板时会产生很多故障,其中有原材料问题,粘合剂问题,机械本身问题,操作技术问题及熟练程度的问题,在当今市场需求尤其在生产过程控制特别要求尽量尽快减少。
由上述故障引出的质量问题造成的报废数量和频率是重中之重。
经公司研究决定,由技术部编写本对策以解决生产急需达到降低控制成本之目的。
一、瓦楞纸断裂这是鉴别瓦楞纸适应性的重要指标。
其形原因:1、单面机预热张力2、瓦楞纸刹车器3、在进入上下瓦楞辊时受到的弯曲与剪切力产生原因解决办法①瓦楞原纸质量不好①更换瓦楞原纸②瓦楞辊磨损②进行简易修复或更换瓦楞辊③瓦楞辊间隙太小③修正和调整瓦楞辊的贴合间隙④运行中机械性损坏④检查并修复机械性不当造成的损伤⑤刹车过紧⑤降低气刹压力减少刹车紧力⑥预热包角过大⑥减少预热包角二、瓦楞折皱产生原因解决办法①瓦楞原纸在抄造或抄宽方向上有湿斑或料斑①增大预热器包角②瓦楞原纸的制动力不强②加大制动力平衡张力③瓦楞辊的平行度不好③修正或调整瓦楞辊的平行度④瓦楞原纸含水平不均衡④适当预热或喷蒸气使其保持平衡的含水三、瓦楞的变形表现为:没有达到规定的瓦楞高度,瓦楞变形,瓦楞形不整齐的现象。
这样的瓦楞成形的纸板本身比较软,平面强度低,刚性也低,做成的纸箱抗压强度也低,戳穿强度也小。
此种原因在流水线上有发生,在制箱过程中也有发生。
产生原因解决办法①使用了低强度的瓦楞原纸本身抗压强度不够①更换高强度瓦楞纸②瓦楞原纸水分过低或过高易变形②加大预热包角或喷雾均衡水分③上、下瓦辊间压力不足时瓦楞成型不好③调整合适压力④瓦楞辊磨损,降低了瓦楞高度④更换瓦辊和压力辊可解决⑤双面机上涂胶辊和压载辊的间隙调节不当⑤调节合适间隙达到正常合适⑥加热部和冷却部的加重辊压力不适当导致压溃⑥调整加大压辊间隙高度⑦瓦楞纸板水分高或热板温度不够不能使其定型⑦加大蒸气压力使温度升高到合适温度,或检查导致温度不好的原因以解决⑧横切机压辊调节太重,导致压溃瓦楞⑧调节重辊铊的间隙距离可解决四、瓦楞的倾斜表现为:瓦楞向纸板运动方向倾斜,但还没倒塌。
瓦楞纸板常见故障原因分析与排除
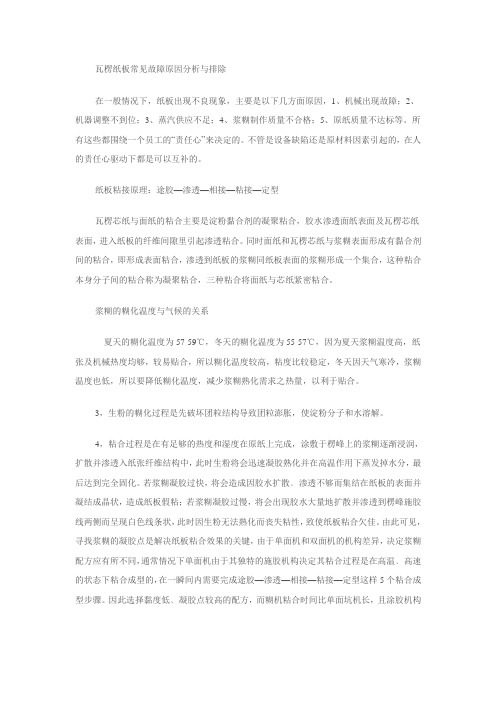
瓦楞纸板常见故障原因分析与排除在一般情况下,纸板出现不良现象,主要是以下几方面原因,1、机械出现故障;2、机器调整不到位;3、蒸汽供应不足;4、浆糊制作质量不合格;5、原纸质量不达标等。
所有这些都围绕一个员工的“责任心”来决定的。
不管是设备缺陷还是原材料因素引起的,在人的责任心驱动下都是可以互补的。
纸板粘接原理:途胶—渗透—相接—粘接—定型瓦楞芯纸与面纸的粘合主要是淀粉黏合剂的凝聚粘合,胶水渗透面纸表面及瓦楞芯纸表面,进入纸板的纤维间隙里引起渗透粘合。
同时面纸和瓦楞芯纸与浆糊表面形成有黏合剂间的粘合,即形成表面粘合,渗透到纸板的浆糊同纸板表面的浆糊形成一个集合,这种粘合本身分子间的粘合称为凝聚粘合,三种粘合将面纸与芯纸紧密粘合。
浆糊的糊化温度与气候的关系夏天的糊化温度为57-59℃,冬天的糊化温度为55-57℃,因为夏天浆糊温度高,纸张及机械热度均够,较易贴合,所以糊化温度较高,粘度比较稳定,冬天因天气寒冷,浆糊温度也低,所以要降低糊化温度,减少浆糊熟化需求之热量,以利于贴合。
3,生粉的糊化过程是先破坏团粒结构导致团粒澎胀,使淀粉分子和水溶解。
4,粘合过程是在有足够的热度和湿度在原纸上完成,涂敷于楞峰上的浆糊逐渐浸润,扩散并渗透入纸张纤维结构中,此时生粉将会迅速凝胶熟化并在高温作用下蒸发掉水分,最后达到完全固化。
若浆糊凝胶过快,将会造成因胶水扩散﹑渗透不够而集结在纸板的表面并凝结成晶状,造成纸板假粘;若浆糊凝胶过慢,将会出现胶水大量地扩散并渗透到楞峰施胶线两侧而呈现白色线条状,此时因生粉无法熟化而丧失粘性,致使纸板粘合欠佳。
由此可见,寻找浆糊的凝胶点是解决纸板粘合效果的关键,由于单面机和双面机的机构差异,决定浆糊配方应有所不同,通常情况下单面机由于其独特的施胶机构决定其粘合过程是在高温﹑高速的状态下粘合成型的,在一瞬间内需要完成途胶—渗透—相接—粘接—定型这样5个粘合成型步骤。
因此选择黏度低﹑凝胶点较高的配方,而糊机粘合时间比单面坑机长,且涂胶机构为冷态施胶,它的粘合过程是在常温下完成粘合成型,这就要求选择黏度高﹑凝胶点较低的配方,以满足纸板粘合成型的需要。
- 1、下载文档前请自行甄别文档内容的完整性,平台不提供额外的编辑、内容补充、找答案等附加服务。
- 2、"仅部分预览"的文档,不可在线预览部分如存在完整性等问题,可反馈申请退款(可完整预览的文档不适用该条件!)。
- 3、如文档侵犯您的权益,请联系客服反馈,我们会尽快为您处理(人工客服工作时间:9:00-18:30)。
瓦楞纸板常见纸病的解决方案一、开胶、假胶1、里纸开胶原因分析:(1)胶质量不符合生产要求或腐败变质;(2)胶量太小;(3)瓦楞辊、压力辊热量不足;(4)压力辊压力不足;(5)瓦辊、压力辊的中高严重磨损。
解决方法:(1)更换合格胶液;(2)适量调大涂胶量;(3)提高压力辊、瓦楞辊的温度,保证在180℃左右温度开机;(4)适当调整压力辊压力,以里、瓦纸粘合良好,里纸不露楞为宜;(5)打磨或更换新压力辊、瓦楞辊。
2、面纸开胶原因分析:(1)胶量过小,烘干机车速过慢;(2)胶液稀薄,涂胶辊带胶不足;(3)烘干机热板温度不足,胶液未充分糊化;(4)烘干机车速过快、烘干不足;(5)烘干机和传输带上面的压载辊没完成落下。
解决方法:(1)适当加大胶量,并提高车速;(2)更换胶液或在原胶液中加适量乳化剂;(3)提高烘干机热板温度到180℃左右再开机;(4)降低车速;(5)落下压载浮辊。
3、里纸假粘原因分析:(1)瓦楞辊温度不足;(2)胶量过小,温度过高;(3)车速慢造成粹胶;(4)胶液粘度不够。
解决方法:(1)提高单面机温度;(2)调整涂胶量,关闭热源待温度降至于180℃以下,160℃以上开机;(3)提高单面机速度;(4)适当增加胶液粘度。
4、面纸假粘原因分析:(1)烘干机热板温度不足;(2)胶液沉淀变质;(3)纸板在烘干机内停留时间过长。
解决方法:(1)待温度达到胶液能糊化时开机;(2)更换新胶(3)降底面纸无轴支架的张力后仍出现面纸断裂,可更换拉力好的纸筒。
估计断纸重续时间可能超过两分钟,立即割断单面瓦楞纸板,将烘干机内的纸板开出后再续纸,尽量减少纸板在烘干机内的停留时间。
二、倒楞1、单面纸板倒楞原因分析:(1)瓦楞辊磨损;(2)上下瓦辊间隙过大;(3)瓦纸克重太大太厚;(4)瓦纸水分过大;(5)瓦纸未经预热器可塑性差。
解决方法:(1)更换瓦辊或磨削;(2)调整两瓦辊间隙至0.5mm;(3)更换瓦纸;(4)调大瓦纸预热包角;(5)将瓦纸穿过预热器。
2、双瓦倒楞原因分析:(1)经双面机涂胶后倒楞,属涂胶辊与压载辊间隙过小所致;(2)经烘干机后倒楞,传输带上面的浮动压载辊不能上下自由活动而压迫瓦楞变形;(3)涂胶量过大,瓦楞纸吸收胶液中的大量水分变软,随烘干机运动方向一边倒;(4)瓦纸品质次。
解决方法:(1)调整双面机、压载辊与涂胶辊之间的间隙至略小单面纸板车0.2 mm即可,以单面纸板向塞入压载辊与涂胶辊之间,能自由插入且带动压载辊转动瓦楞无变形为佳;(2)调整烘干机传输带上的浮辊自由活动;(3)减少涂胶量至均匀分布瓦楞楞峰,而不流入瓦沟内为宜;(4)更换瓦纸。
三、塌楞、高低楞1、塌楞、高低楞原因分析:(1)单面机、瓦楞辊不平;(2)瓦楞辊严重磨损;(3)瓦楞辊两端热量不足;(4)瓦纸张力不足;(5)瓦纸两端张力不均匀。
(6)真空吸附封闭不严或风孔堵塞或真空板内有纸屑尘埃等杂物。
解决方法:(1)调整两瓦辊至平等;(2)更换瓦楞辊;(3)调节升高瓦辊平衡温度;(4)涨紧瓦纸制动闸阀;(5)更换瓦纸;(6)检查真空吸附封闭情况,更换密封、垫片,紧固螺钉,清理堵塞孔或真空板内纸屑等杂物。
2、高低楞原因分析:(1)瓦纸张力过大;(2)纸张可塑性差;(3)瓦纸两端制动不一致;(4)瓦纸水分不平衡;(5)导纸辊不平行。
解决方法:(1)适当减少张力;(2)视纸质适量喷蒸汽或增大预热面积;(3)改用小克重瓦纸;(4)调节至适宜的吸风量。
四、打皱1、里纸折皱原因分析:(1)瓦纸辊厚薄不匀;(2)未经预热直接输入瓦楞机(3)瓦纸两端制动不一致;(4)瓦纸水分不平衡;(5)导纸辊不平行。
解决方法:(1)更换瓦纸;(2)将瓦纸穿过预热器;(3)调整瓦纸制动平衡;(4)增大瓦纸预热面积或更换瓦纸;(5)校正导纸辊。
2、里纸起皱原因分析:(1)导纸辊不平行;(2)烘干机进纸口偏斜;(3)瓦纸两边张力不平衡。
解决方法:(1)校正导纸辊;(2)纠正烘干机进纸口(3)增大瓦纸预热面积;(4)更换瓦纸。
3、瓦纸打皱原因分析:瓦纸两端强力、水分、厚薄不均、制动不足。
解决方法:调整预热面积,涨紧制动闸阀或将瓦纸翻转使用,如还出现打皱现象,可更换瓦纸。
五、起泡1、里纸起泡原因分析:(1)瓦纸水分不均衡;(2)卷筒制动不足;(3)瓦楞辊、压力辊热量不足;(4)压力辊磨损或不平行;(5)胶辊磨损局部带胶困难或有导物夹入涂胶辊与调量辊中间;(6)瓦楞辊部分吸风槽堵塞,导纸板磨损。
解决方法:(1)增大瓦纸预热面积;(2)涨紧制动闸阀;(3)待温度升到180℃左右时,再续纸开机;(4)更换磨削压力辊或校正至平行;(5)更换涂胶辊,清除涂胶辊与调胶辊的杂物;(6)清理瓦楞辊吸风槽,更换导纸片。
2、面纸起泡原因分析:(1)瓦纸水分不平衡;(2)面纸未经预热器直接输入烘干机;(3)胶液粘度不够;(4)涂胶辊与调量辊间夹有纸屑、胶块;(5)涂胶辊不平衡或磨损。
解决方法:(1)更换瓦纸;(2)将面纸经过预热器并适当调整预热面积;(3)增加液粘度;(4)清除涂胶辊与调胶辊的杂物及胶块;(5)校正涂胶辊或更换。
六、瓦楞破碎1、单面纸板瓦楞破碎原因分析:(1)压力辊加压过大;(2)瓦纸纤维短,无韧性,质量差;(3)上下两瓦辊间隙过小;(4)预热面积过大,纸张严重失水;(5)瓦楞辊温度过高;(6)瓦楞辊中高严重磨损,压力辊抬升后,瓦纸受力不平衡,导致单面瓦楞两端压力过大造成瓦楞破损。
解决方法:(1)适当减少压力辊压力;(2)更换瓦纸;(3)校正瓦楞辊间隙;(4)减少预热面积;(5)降低瓦楞辊温度到150℃后再开机;(6)更换或磨削瓦楞辊。
2、经双面机后瓦楞破碎原因分析:(1)天桥各导纸辊或多重预热器缸面有毛刺造面机械划伤;(2)天桥至单面机的传输带接扣扎破。
解决方法:(1)检查到有导纸瓦楞破碎的毛刺,用砂纸或砂板打磨光;(2)更换扣带,重新接好。
七、压线破损1、里纸破裂原因分析:(1)里纸质次,太薄;(2)里脱水严重无韧性;(3)压钱凸轮楞角不圆滑;(4)压痕过深。
解决方法:(1)更换里纸或适当调浅压痕深度;(2)里纸可不经过预热器;(3)更换弧形压线轮或打磨光滑凸轮楞角;(4)适当调整压线深度。
2、面纸破裂原因分析:(1)面纸质次;(2)压痕线过深;(3)压痕凹轮太深不圆滑;(4)压线调节装置失灵;(5)纸板过干。
解决方法:(1)对面纸喷蒸汽,增大涂胶量并适当提高烘干机车速;(2)调浅压痕线;(3)更换压痕凹轮或打磨;(4)修正压线调节装置后再生产;(5)适当提高烘干机车速,关闭部分烘干机热源。
3、里面纸均破裂原因分析:(1)压痕太深;(2)纸板干脆;(3)纸次无韧性。
解决方法:(1)适当调浅压线;(2)提高烘干机车速;(3)更换瓦纸或对其喷蒸汽。
八、压线折痕凹凸不平且深浅不均原因分析:(1)压线太浅;(2)压线调节装置失灵;(3)压线轮变形;(4)压线凸轮磨损严重,生产中未考虑磨损程度,仍按常规操作。
解决方法:(1)调节压线至里面纸不破裂且折后压线清晰平直为宜;(2)校正维修压线调节装置至正常;(3)更换压线轮;(4)视压线程度深调。
九、压线折后面破裂原因分析:(1)面纸质次;(2)烘干机车速度过慢,纸板脱水严重,面纸失去韧性。
解决方法:(1)更换面纸(2)提高烘干机车速。
十、纸板成型后断裂原因分析:(1)瓦纸质差;(2)纸板过分干燥;(3)成型工序设备调节不当;(4)压线太浅,瓦楞未压扁或成型后折叠摇盖时高强瓦楞将面纸撑破,瓦楞随之断裂。
解决方法:(1)更换瓦纸;(2)保证纸板含水量在10±3左右;(3)注意成型各工序的设备调节并调至最佳状态;(4)哄干机加速并加大涂胶量,压线调深.十一、纵切毛边原因分析:(1)分纸刀已钝或刀刃有缺口;(2)上下刀咬合过深;(3)上下之间有间隙。
解决方法:(1)打磨或更换新刀;(2)调节上下刀重合至最佳状态;(3)将上下两刀靠紧,用手转动刀轮,灵活不伤刀为宜。
十二、横切纸板拖尾原因分析:(1)横刀已钝;(2)横切刀上下两刀咬合不正,纸板不断的部位在机械刀作用下带起撕裂的面瓦纸;(3)横切刀瞬时加速调节不当,引起阻纸。
解决方法:(1)换刀,答案磨;(2)校正上下两刀的位置;(3)根据纸板长短,正确调节瞬时加速。
十三、纸板回软原因分析:(1)胶中碱含量过大;(2)下线纸板堆码重叠过高,纸板内蒸汽未得到充分散发;(3)纸板存放环境湿度过高;(4)哄干机温度太低而车速又过快,低温环境又造成干燥假象,堆码后瓦楞变堆码,纸板因之降低强度。
解决方法:(1)适当调整胶的用碱量;(2)采用井字形堆码,堆码高度不超过1.5米为宜,必要时可用鼓风机强制驱散纸板内的手汽;(3)对存放纸板的库房开窗通风降温,到场地撒石灰粉吸潮;(4)根据涂胶量、纸质、哄干机温度,在确保纸板质量的情况下灵活掌握车速。
十四、纸板边部开胶1、里纸边部开胶原因分析:(1)涂胶辊带胶不到位;(2)胶盘振动游离;(3)单面机瓦楞两端温度不足或过高,瓦楞瞬间涂胶后低温使胶液未糊化,水分迅速渗透到瓦纸中留下淀粉印,高温后胶失去粘性。
解决方法:(1)将胶阀适当开大,加大胶液流量;(2)校正固定胶盘;(3)升高瓦楞辊温度,以手指蘸水弹到瓦楞辊上,水珠2-3秒蒸发掉为宜,温度过高可用毛刷蘸机油抹瓦楞两端,蒸发的油烟即带走部分瓦楞热量,即可达到降低温度之目的。
2、面纸边部开胶原因分析:(1)涂胶辊带胶不到位;(2)哄干机传输带跑偏,纸板边缘受压不到位;(3)哄干机两边热温度不足。
解决方法:(1)将胶糟内补足胶液,使涂胶辊全部浸到胶液;(2)及时纠偏,使传输带正确到位;(3)待哄干机热板温度平衡稳定后再开机。
十五、缺材露瓦1、里纸露瓦原因分析:(1)里纸未对齐;(2)里纸预热缩水;(3)里纸宽幅不足;(4)飞边过少。
解决方法:(1)点动无轴支架左右移动,直到纸板对齐为止;(2)(3)(4)更换瓦纸。
2、里纸露楞原因分析:(1)里纸宽幅不够;(2)瓦纸含水量过高,预热后缩水过多;(3)里纸与各层单面瓦楞纸板未对齐。
解决方法:同里纸露瓦方法。
3、瓦纸缺材原因分析:(1)瓦纸窄于里面纸;(2)天桥上夹纸器将单面纸板边刮掉;(3)瓦纸边缘缺不齐。
解决方法:(1)更换瓦纸;(2)适当调整夹纸器,以单面纸板不左右摆动,又能顺利通过为宜;(3)调节夹纸挡板,将单面纸板与面纸对齐。
十六、切断长度不稳定原因分析:(1)哄干机转速不稳定;(2)横切刀齿轮间有纸毛或齿轮、轴承损坏;(3)天桥单面纸板运行阻力过大;(4)面纸制动张力过大;(5)哄干机传输带打滑;(6)横切机无级变速齿轮啮合间隙过大或转动链条老化、松弛;(7)横切控制程序混乱,受强磁场干扰。
解决方法:(1)检查哄干机主电动机是否缺相,电压是否稳定,轴承是否损坏;(2)清除根切刀转动齿轮间的纸屑,更换齿轮轴承;(3)对天桥各导纸辊转动不灵活的加润滑油或更换轴承,并适当调节控制单面纸板张力的真空吸附风量;(4)减少面纸制动力;(5)常清理哄干机传输带,并保持哄干机热板清洁,生产中出现传输带打滑现象可在其上面喷少量水即可缓解,注意尽量避免未输纸让哄干机空转,从而减少传输带与热板的直接摩擦,否则传输带的糙面磨平,极易造成打滑现象;(6)纠正无级变速齿轮间隙,更换新链条或适当调整链条,整固装置;(7)排除强磁场干扰。