精益改善十大原则
精益管理改善方案

精益管理改善方案精益管理(Lean Management)是一种致力于减少浪费、提高效率和质量的管理方法。
它起源于日本汽车制造行业,如今已经被广泛应用于各个行业和组织中。
本文将介绍精益管理的核心原则和一些常用的改善方案。
一、核心原则1. 增加价值、减少浪费:精益管理强调通过识别和消除各种形式的浪费,为客户提供更大的价值。
常见的浪费包括过产出、多余的库存、无效的运输等。
通过加强价值流程分析,精益管理鼓励组织对每个活动进行评估,并确保为客户创造最大价值。
2. 以顾客为导向:精益管理的目标是满足客户需求并提供超越其期望的价值。
它通过深入了解客户需求、强化质量控制,确保产品或服务符合客户期望,并建立良好的客户关系。
3. 持续改进:精益管理倡导持续改进的理念,鼓励组织不断地寻找和实施改进的机会。
它强调员工参与和持续学习,以推动组织的创新和进步。
二、改善方案1. 价值流程映射(Value Stream Mapping):价值流程映射是分析和改善价值流程的一种工具。
通过绘制从原材料到最终产品或服务交付的整个价值流,可以识别出浪费和瓶颈,并提供改进的机会。
组织可以借助价值流程映射来优化流程,并减少非价值添加的活动。
2. 5S方法:5S方法是一个用于改善和维护工作环境、提高效率和质量的实用工具。
它包括整理、整顿、清扫、标准化和自律五个步骤。
通过组织和标识工作场所,减少浪费和提高安全性,5S方法可以为组织创造一个更加高效和清洁的工作环境。
3. Kaizen活动:Kaizen是日语中“持续改进”的意思。
它是一种通过小步骤和持续努力来改善工作的方法。
组织可以组织Kaizen活动,鼓励员工提出改进意见,并实施小规模的改变。
这些积极的改变将有助于改进流程、提高效率和品质。
4. 启发式问题解决:启发式问题解决是一种基于经验和直觉的问题解决方法。
当面临问题时,员工可以利用已有的知识和经验,通过迅速分析和试验来找到解决方案。
这种方法注重快速反应和实验,以促进创新和改善。
精益改善十大原则精益生产专家们的十大改善工具
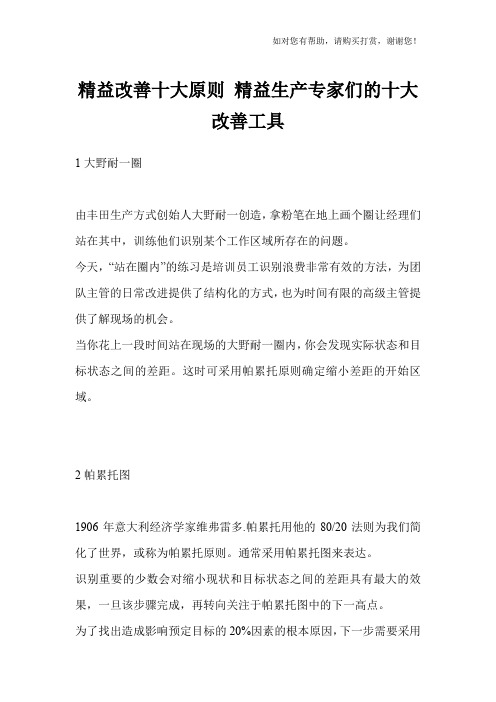
精益改善十大原则精益生产专家们的十大改善工具1大野耐一圈由丰田生产方式创始人大野耐一创造,拿粉笔在地上画个圈让经理们站在其中,训练他们识别某个工作区域所存在的问题。
今天,“站在圈内”的练习是培训员工识别浪费非常有效的方法,为团队主管的日常改进提供了结构化的方式,也为时间有限的高级主管提供了解现场的机会。
当你花上一段时间站在现场的大野耐一圈内,你会发现实际状态和目标状态之间的差距。
这时可采用帕累托原则确定缩小差距的开始区域。
2帕累托图1906年意大利经济学家维弗雷多.帕累托用他的80/20法则为我们简化了世界,或称为帕累托原则。
通常采用帕累托图来表达。
识别重要的少数会对缩小现状和目标状态之间的差距具有最大的效果,一旦该步骤完成,再转向关注于帕累托图中的下一高点。
为了找出造成影响预定目标的20%因素的根本原因,下一步需要采用石川图深挖其中的根本原因。
3石川图石川图(又称鱼骨图或因果图)用以识别造成特定事件或情况的原因。
这是一种相当灵活的工具。
即可以采用4M(人,材料,设备,方法)或6M(加上环境和测量方法)为制造或生产型流程的进行根原因分析,又可用4P(价格,促销,地点,产品)进行市场和销售的改善。
到目前为止,你已经识别出问题的根原因,下一步准备实施相应的措施。
所以你需要一个行动计划。
4甘特图亨利.甘特在1910期间创造了闻名于世的项目管理工具甘特图。
任何使用微软项目管理软件或使用这个经典项目管理工具的人都需要感谢甘特先生。
随着甘特图在全球范围传播,带来管理大型,复杂项目的革命。
甘特先生算是早期具有精益思维的专家,他为后来的发展奠定了基础,例如标准作业合并表,安排每日工作和作业平衡。
行动计划不能仅局限于“计划和实施”,也要注重“检查和纠正”。
这是根据PDCA环原则,通称戴明环。
5戴明环戴明环又称为PDCA环。
爱德华.戴明以其在日本教授和传播PDCA 的质量改进方式而闻名。
更准确的说,应归功于Walter Shewhart,他是统计学的先驱者同时也是戴明的老师, PDCA即源自于他的构想。
11项精益制造原则
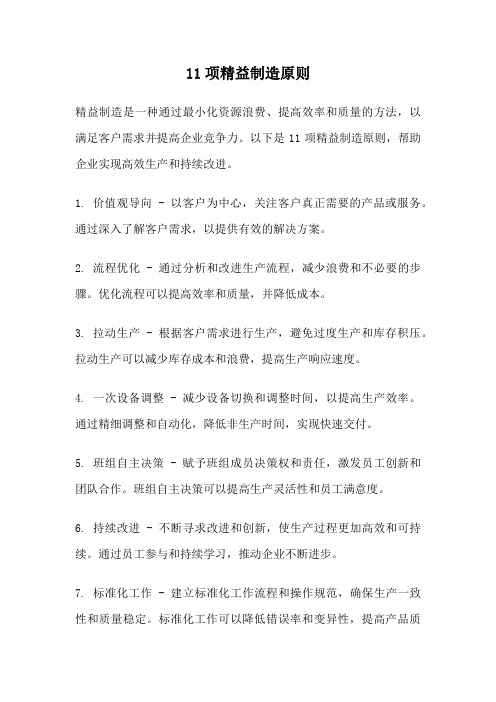
11项精益制造原则精益制造是一种通过最小化资源浪费、提高效率和质量的方法,以满足客户需求并提高企业竞争力。
以下是11项精益制造原则,帮助企业实现高效生产和持续改进。
1. 价值观导向 - 以客户为中心,关注客户真正需要的产品或服务。
通过深入了解客户需求,以提供有效的解决方案。
2. 流程优化 - 通过分析和改进生产流程,减少浪费和不必要的步骤。
优化流程可以提高效率和质量,并降低成本。
3. 拉动生产 - 根据客户需求进行生产,避免过度生产和库存积压。
拉动生产可以减少库存成本和浪费,提高生产响应速度。
4. 一次设备调整 - 减少设备切换和调整时间,以提高生产效率。
通过精细调整和自动化,降低非生产时间,实现快速交付。
5. 班组自主决策 - 赋予班组成员决策权和责任,激发员工创新和团队合作。
班组自主决策可以提高生产灵活性和员工满意度。
6. 持续改进 - 不断寻求改进和创新,使生产过程更加高效和可持续。
通过员工参与和持续学习,推动企业不断进步。
7. 标准化工作 - 建立标准化工作流程和操作规范,确保生产一致性和质量稳定。
标准化工作可以降低错误率和变异性,提高产品质量。
8. 可视化管理 - 使用可视化工具和指标,跟踪生产状态和绩效。
可视化管理可以帮助员工了解生产情况,及时发现问题并采取措施。
9. 防错机制 - 引入防错机制和质量控制,减少错误和缺陷。
通过持续改进和培训,提高产品质量和客户满意度。
10. 合作伙伴关系 - 建立长期稳定的合作伙伴关系,共同追求卓越。
与供应商和客户紧密合作,实现共赢和共同成长。
11. 持续学习 - 鼓励员工不断学习和提升技能,适应市场变化和技术进步。
持续学习可以增强企业的创新能力和竞争力。
通过遵循这11项精益制造原则,企业可以实现高效生产、质量优先和持续改进。
精益制造不仅可以提高企业竞争力,还可以为客户提供更好的产品和服务。
在现代制造业中,精益制造已经成为企业提升效率和降低成本的重要方法,值得广泛应用和推广。
精益改善十大原则

粗益革新十大准则之阳早格格创做往日粗确的,当前一定粗确;当前粗确的,已去一定粗确.所谓“当局者迷,旁瞅者浑”,从本有的处事概念中跳出去,用旁瞅者的视线、站正在下处审视自己的处事观念战处事过程,也许便会创造分歧理之处,也便有了革新的切进面.有了革新的切进面后,交下去便是怎么样启展革新活动.正在自己里前也许有多种要收战观念,然而是通过周到分解以去要采用一条可止的路径,启展革新.“吾日三省吾身”,不人提修议,也要每日自省.如果有他人给自己提出了革新的修议,更要尽管交受,不要去辨别,要先审视自己处事观念、要收、过程,找出问题天圆,纵然不问题,对于自己搞一次周到查看也无害.料到了对于自己处事有利的革新面后便要坐时真施,哪怕真施后效验本去不那么完好,然而是惟有真施了,才知讲要收是可可止,才知讲背何圆革新.如果真真是自己处事观念、要收、过程出现了问题战过失,那便要赶快革新,延少一秒钟便要爆收一秒钟的浪费.革新的最后手段是缩小浪费、提下企业比赛力,毋庸置疑,革新要收自己也一定要“够节俭”,尽管不费钱,可则革新赢得的成果便会被革新要收的浪费无情天削减.“山贫火尽疑无路,柳暗花明又一村”,当咱们里前惟有二条路:牺牲大概者改变,无疑,智慧的人会毫无早疑天采用改变,果为改变了才有存正在下去的期视战大概.当咱们正在谷底时,无论往哪一个目标走,只消走,咱们的下度皆比谷底要下,只消改变了,往往便会赢得意念不到的支益.革新要坐时真施,也要探供问题的根根源基本果,正所谓“有的搁矢”,排除假果赢得真果,才搞够以最下的效用赢得革新预期的效验.那怎么样赢得真果呢?问案便是反复问自己五次为什么,每问一次,便背真果靠拢一面.“三个臭皮匠,顶个诸葛明.”革新是一个大众活动,革新面的创造、革新要收的收挖取真施,皆需要多人协同,也包罗收袖取职工的协同.有一句出名的广告语讲“不最佳,惟有更佳”.正在死产历程中,咱们需要随时闭注主瞅,谦脚以至超出主瞅的需要,而主瞅的需要是正在不竭删少的,果此,对于自己处事的革新也是无限的,咱们需要持绝不竭天“挨破固有概念”,“觅找可止的要收”,革新下去.。
精益生产10个原则
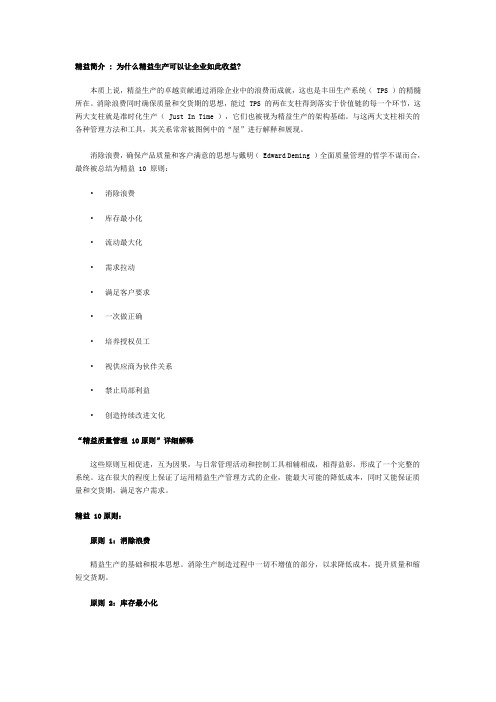
精益简介 : 为什么精益生产可以让企业如此收益?本质上说,精益生产的卓越贡献通过消除企业中的浪费而成就,这也是丰田生产系统( TPS )的精髓所在。
消除浪费同时确保质量和交货期的思想,能过 TPS 的两在支柱得到落实于价值链的每一个环节,这两大支柱就是准时化生产( Just In Time ),它们也被视为精益生产的架构基础。
与这两大支柱相关的各种管理方法和工具,其关系常常被图例中的“屋”进行解释和展现。
消除浪费,确保产品质量和客户满意的思想与戴明( Edward Deming )全面质量管理的哲学不谋而合,最终被总结为精益 10 原则:•消除浪费•库存最小化•流动最大化•需求拉动•满足客户要求•一次做正确•培养授权员工•视供应商为伙伴关系•禁止局部利益•创造持续改进文化“精益质量管理 10原则”详细解释这些原则互相促进,互为因果,与日常管理活动和控制工具相辅相成,相得益彰,形成了一个完整的系统。
这在很大的程度上保证了运用精益生产管理方式的企业,能最大可能的降低成本,同时又能保证质量和交货期,满足客户需求。
精益 10原则:原则 1:消除浪费精益生产的基础和根本思想。
消除生产制造过程中一切不增值的部分,以求降低成本,提升质量和缩短交货期。
原则 2:库存最小化库存是 7 大浪费之一。
库存占用资金和场地,并掩盖了企业经营管理中的大量问题,精益生通过不断降低库存,暴露问题,解决问题后再降低库存的循环不断降低库存量。
原则 3:流动最大化让物流和加工过程快速流动起来,以最短的生产周期应对市场变化。
原则 4:需求拉动不再依靠预测来生产,而根据客户的需求来生产,尽可能最迟将客户的需求导入生产环节以提升准确性。
当客户需求的时候才生产。
原则 5:满足客户要求了解客户的正真需求,满足顾客在质量、交货、服务、价格等方面的需求。
原则 6:一次做正确生产的每个环节确保提供的都是合格品,每一步骤都作工确,而不是最后校正。
在制造过程中坚持“不制造、不传递、不接受”不合格品的“三不”原则。
现场改善的基本原则
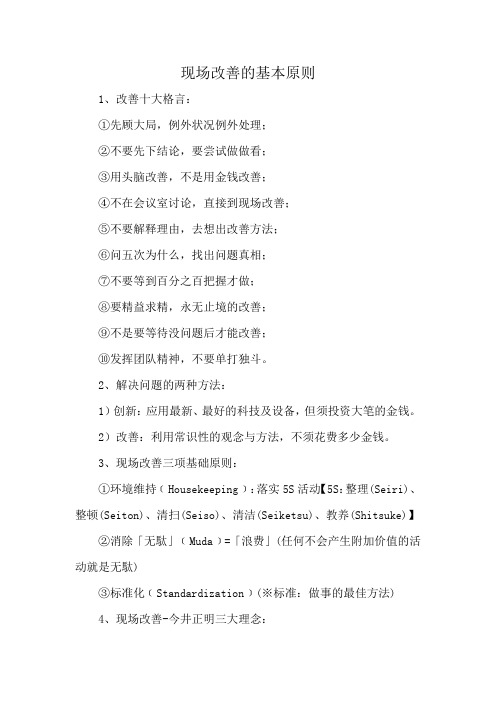
现场改善的基本原则1、改善十大格言:①先顾大局,例外状况例外处理;②不要先下结论,要尝试做做看;③用头脑改善,不是用金钱改善;④不在会议室讨论,直接到现场改善;⑤不要解释理由,去想出改善方法;⑥问五次为什么,找出问题真相;⑦不要等到百分之百把握才做;⑧要精益求精,永无止境的改善;⑨不是要等待没问题后才能改善;⑩发挥团队精神,不要单打独斗。
2、解决问题的两种方法:1)创新:应用最新、最好的科技及设备,但须投资大笔的金钱。
2)改善:利用常识性的观念与方法,不须花费多少金钱。
3、现场改善三项基础原则:①环境维持﹝Housekeeping﹞:落实5S活动【5S:整理(Seiri)、整顿(Seiton)、清扫(Seiso)、清洁(Seiketsu)、教养(Shitsuke)】②消除「无駄」﹝Muda﹞=「浪费」(任何不会产生附加价值的活动就是无駄)③标准化﹝Standardization﹞(※标准:做事的最佳方法)4、现场改善-今井正明三大理念:①重视现场:任何问题都要到现场去了解,当场用最简单、最不花钱的方式来寻求「改善」,而非以投入资金,从外界购买最新的科技设备来提升工厂的水平。
②最简单的「改善」方式:日本式的TQM、TPM、JIT、5S、QCC及提案建议...等。
③高阶层的承诺﹝Commitment﹞:所谓承诺不是指应允某一件事,而是说从事这些改善活动必需要长久、持续地做下去,这不是一年、二年之事,而是一辈子的事。
5、日本式改善活动-「五心」:①信心:相信这些改善活动会带给你好处;②决心:下定决心赶快去做,不要犹豫不决;③耐心:要永远持续做下去,成果自然呈现;④关心:对员工表示出你的关怀及重视之意;⑤爱心:多用鼓励的方式来鼓舞员工士气。
6、主要的改善观念:①改善与管理;②过程与结果;③遵循PDCA循环/SDCA循环;④品质第一;⑤用数据说话;⑥下一工序就是顾客。
精益思维“十大”原则
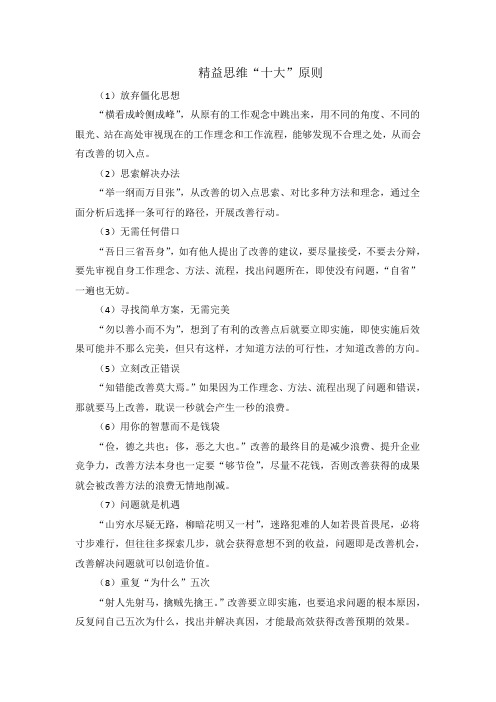
精益思维“十大”原则(1)放弃僵化思想“横看成岭侧成峰”,从原有的工作观念中跳出来,用不同的角度、不同的眼光、站在高处审视现在的工作理念和工作流程,能够发现不合理之处,从而会有改善的切入点。
(2)思索解决办法“举一纲而万目张”,从改善的切入点思索、对比多种方法和理念,通过全面分析后选择一条可行的路径,开展改善行动。
(3)无需任何借口“吾日三省吾身”,如有他人提出了改善的建议,要尽量接受,不要去分辩,要先审视自身工作理念、方法、流程,找出问题所在,即使没有问题,“自省”一遍也无妨。
(4)寻找简单方案,无需完美“勿以善小而不为”,想到了有利的改善点后就要立即实施,即使实施后效果可能并不那么完美,但只有这样,才知道方法的可行性,才知道改善的方向。
(5)立刻改正错误“知错能改善莫大焉。
”如果因为工作理念、方法、流程出现了问题和错误,那就要马上改善,耽误一秒就会产生一秒的浪费。
(6)用你的智慧而不是钱袋“俭,德之共也;侈,恶之大也。
”改善的最终目的是减少浪费、提升企业竞争力,改善方法本身也一定要“够节俭”,尽量不花钱,否则改善获得的成果就会被改善方法的浪费无情地削减。
(7)问题就是机遇“山穷水尽疑无路,柳暗花明又一村”,迷路犯难的人如若畏首畏尾,必将寸步难行,但往往多探索几步,就会获得意想不到的收益,问题即是改善机会,改善解决问题就可以创造价值。
(8)重复“为什么”五次“射人先射马,擒贼先擒王。
”改善要立即实施,也要追求问题的根本原因,反复问自己五次为什么,找出并解决真因,才能最高效获得改善预期的效果。
(9)让每个员工寻找答案“三个臭皮匠,顶个诸葛亮。
”改善周是团体活动,改善点的发现、改善方法的发掘与实施,都需要多人配合,也包括领导与员工的配合。
(10)改进无止境“没有最好,只有更好”。
工作的改善亦是无限的,只有持续不断地“打破固有观念”,“寻找可行的方法”,一直改善实施下去,才能最终满足客户不断上升的需求。
精益生产管理的十个重点
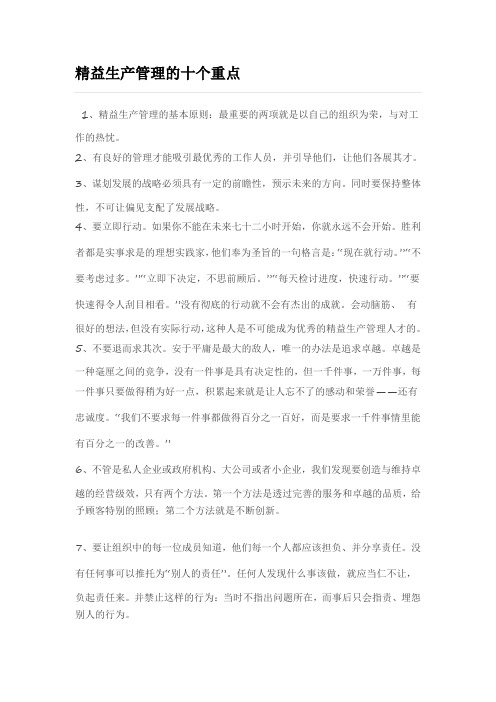
精益生产管理的十个重点1、精益生产管理的基本原则:最重要的两项就是以自己的组织为荣,与对工作的热忱。
2、有良好的管理才能吸引最优秀的工作人员,并引导他们,让他们各展其才。
3、谋划发展的战略必须具有一定的前瞻性,预示未来的方向。
同时要保持整体性,不可让偏见支配了发展战略。
4、要立即行动。
如果你不能在未来七十二小时开始,你就永远不会开始。
胜利者都是实事求是的理想实践家,他们奉为圣旨的一句格言是:“现在就行动。
”“不要考虑过多。
”“立即下决定,不思前顾后。
”“每天检讨进度,快速行动。
”“要快速得令人刮目相看。
”没有彻底的行动就不会有杰出的成就。
会动脑筋、有很好的想法,但没有实际行动,这种人是不可能成为优秀的精益生产管理人才的。
5、不要退而求其次。
安于平庸是最大的敌人,唯一的办法是追求卓越。
卓越是一种毫厘之间的竞争,没有一件事是具有决定性的,但一千件事,一万件事,每一件事只要做得稍为好一点,积累起来就是让人忘不了的感动和荣誉——还有忠诚度。
“我们不要求每一件事都做得百分之一百好,而是要求一千件事情里能有百分之一的改善。
”6、不管是私人企业或政府机构、大公司或者小企业,我们发现要创造与维持卓越的经营级效,只有两个方法。
第一个方法是透过完善的服务和卓越的品质,给予顾客特别的照顾;第二个方法就是不断创新。
7、要让组织中的每一位成员知道,他们每一个人都应该担负、并分享责任。
没有任何事可以推托为“别人的责任”。
任何人发现什么事该做,就应当仁不让,负起责任来。
并禁止这样的行为:当时不指出问题所在,而事后只会指责、埋怨别人的行为。
8、情况许可的话,就设法引发内部竞争和比较。
从纸上作业看,内部竞争不仅不需要,而且十分浪费,但在真实世界及长期眼光看,内部竞争是保持继续成功的动。
9、别太相信自己的记性,假如你不把事情写下来,即使你最想做的事,你可能都会迟迟无所行动。
要养成这样一个习惯:将全天中值得注意的事情以及发生的问题,采用笔记本式的连续记载方式一一作好记录,这将给你的工作带来埤益。
- 1、下载文档前请自行甄别文档内容的完整性,平台不提供额外的编辑、内容补充、找答案等附加服务。
- 2、"仅部分预览"的文档,不可在线预览部分如存在完整性等问题,可反馈申请退款(可完整预览的文档不适用该条件!)。
- 3、如文档侵犯您的权益,请联系客服反馈,我们会尽快为您处理(人工客服工作时间:9:00-18:30)。
精益改善十大原则之袁州冬雪创作
以前正确的,现在未必正确;现在正确的,未来未必正确.所谓“当局者迷,傍观者清”,从原有的工作观念中跳出来,用傍观者的眼光、站在高处审视自己的工作理念和工作流程,也许就会发现分歧理之处,也就有了改善的切入点.
有了改善的切入点后,接下来就是如何展开改善活动.在自己眼前也许有多种方法和理念,但是通过全面分析以后要选择一条可行的途径,展开改善.
“吾日三省吾身”,没有人提建议,也要逐日自省.如果有他人给自己提出了改善的建议,更要尽能够承受,不要去分辨,要先审视自身工作理念、方法、流程,找出问题所在,即使没有问题,对自己做一次全面检查也无害.
想到了对自身工作有利的改善点后就要当即实施,哪怕实施后效果其实不那末完美,但是只有实施了,才知道方法是否可行,才知道向何方改善.
如果确实是自身工作理念、方法、流程出现了问题和错误,那就要顿时改善,耽误一秒钟就要发生一秒钟的华侈.改善的最终目标是减少华侈、提升企业竞争力,毋庸置疑,改善方法自己也一定要“够俭仆”,尽能够不花钱,否则改善获得的成果就会被改善方法的华侈无情地削减.“山穷水尽疑无路,山穷水尽又一村”,当我们眼前只有两条路:死亡或者改变,无疑,聪明的人会毫无迟疑地选
择改变,因为改变了才有生存下去的希望和能够.当我们在谷底时,无论往哪个方向走,只要走,我们的高度都比谷底要高,只要改变了,往往就会获得意想不到的收益.
改善要当即实施,也要追求问题的根来历根基因,正所谓“有的放矢”,解除假因获得真因,才干够以最高的效率获得改善预期的效果.那如何获得真因呢?答案就是反复问自己五次为什么,每问一次,就向真因接近一点.
“三个臭皮匠,顶个诸葛亮.”改善是一个团体活动,改善点的发现、改善方法的发掘与实施,都需要多人配合,也包含带领与员工的配合.
有一句著名的广告语道“没有最好,只有更好”.在生产过程中,我们需要随时关注顾客,知足甚至超出顾客的需求,而顾客的需求是在不竭增长的,因此,对自身工作的改善也是无限的,我们需要持续不竭地“打破固有观念”,“寻找可行的方法”,改善下去.。